[computational Fabrication] Specifying CAM Toolpaths for a Ring Box in Fusion360
by soniahashim in Workshop > CNC
442 Views, 4 Favorites, 0 Comments
[computational Fabrication] Specifying CAM Toolpaths for a Ring Box in Fusion360
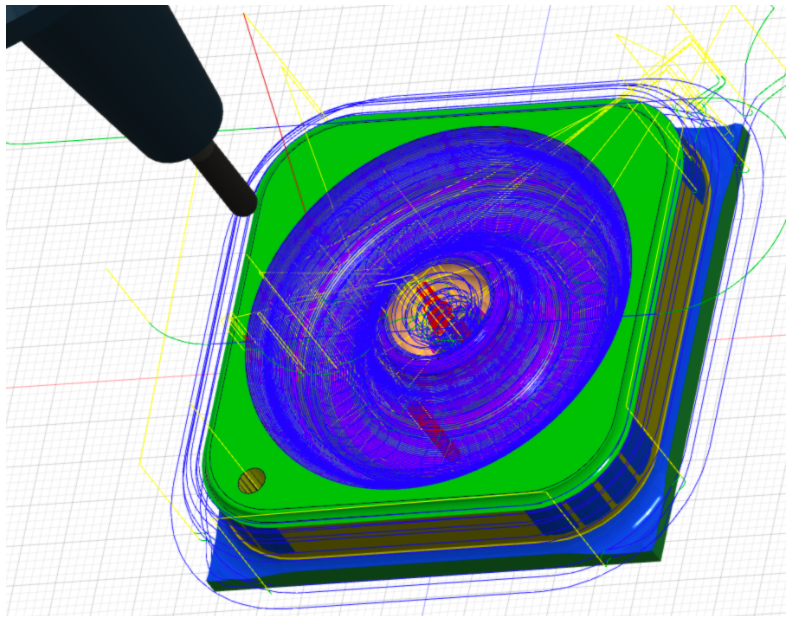
OVERVIEW
The goal of this project is to get familiar with specifying tool paths to explore CAM* programming in Fusion360. I’ll try to convert the geometry of some simple designs so that the objects can be CNC** milled.
This is the sixth assignment for a course I’m taking this quarter (Spring 2020) on computational fabrication taught by Prof. Jennifer Jacobs at the Media, Arts & Technology program at the University of California Santa Barbara. The idea behind the course is that digital fabrication can be combined with computational design to create complex and functional physical forms.
Tools I used for this work include
- Fusion360, CAD/CAM software by Autodesk
* CAM = Computer Aided Machinery, specifies movements and tool configurations.
** CNC = Computer Numerical Control, for computationally based mills as opposed to hand mills.
STEP 0 [Explorations]
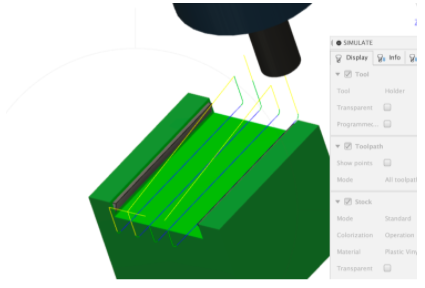
I experimented with old designs but ran into some issues. My designs were very deep and resulted in calculated toolpaths with many collisions. There were also gradual curves which were not cleared precisely and overhangs (I tried to mill the model from its side) that were taken out by the tool by naively specifying toolpaths. I decided to start with a new design that was more flat and shallow.
STEP ONE [Designing a Ring Box]
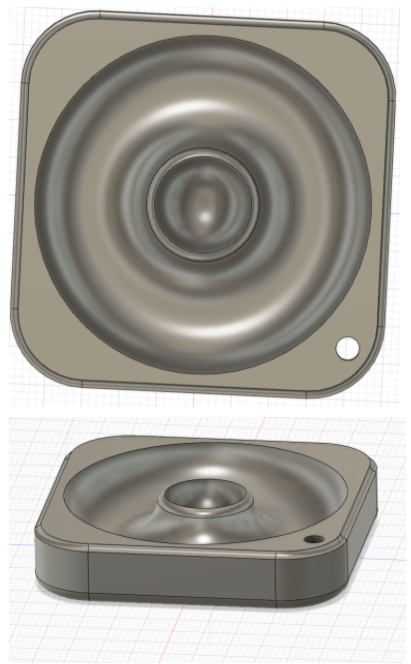
The first step was to create a design that can be CNC milled. I created a small ring box inspired by the macbook body aluminum casing that is CNC milled. I also created a hole as I want to try out this toolpath. Two copies of the design can be attached with one flipped and connected using a dowel to create a box that swivels to open. Some details are pretty fine-grained (like the pipe exterior to provide a pinch point to open the box). It will be interesting to see how well these are handled. I rounded the outer corners of the outside of the box. If time remains, I’ll add an SVG to etch on the exterior.
STEP TWO [Specifying the Stock and Setting Up the Tool Library]
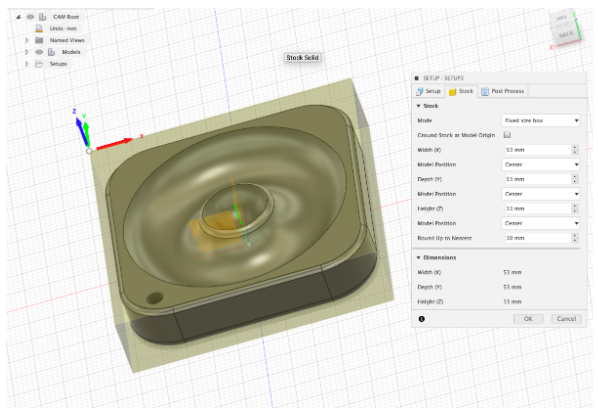
Using the manufacturing ribbon, I created a set-up and specified a fixed stock size with 1.5mm give on each edge. The result is shown. I also oriented the work coordinate system (WCS).
We are using the P9_HaasMill_Aug2017 tool library.
STEP THREE [Setting Up Paths]
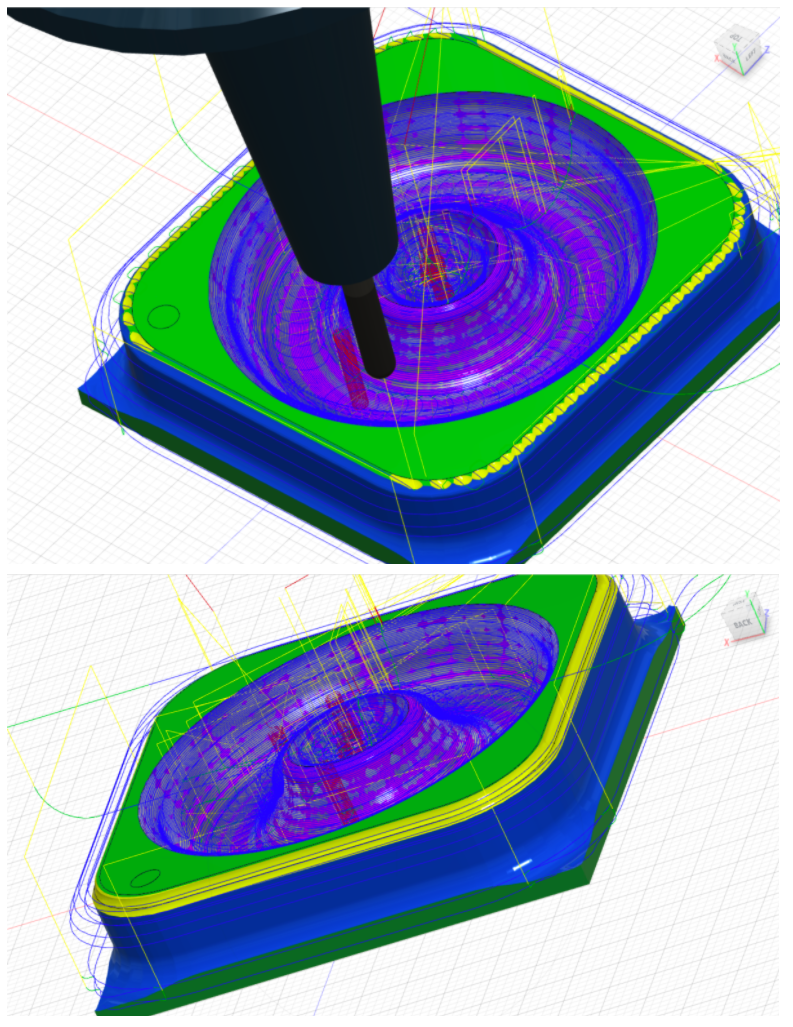
I simulated the tool paths after every step with the stock visualized.
- Facing. The first path is a facing tool path using a facing mill. I’m realizing my part is a bit small.
- Roughing. Next, I used a 3d adaptive clearing path to clear out the depressions. I wasn’t sure what chains to select to get the intended result and found selecting all three interior chains worked well. I revised this to include the piped edge . I used tool 117 (1/4’’ ball).
- Finishing. Next I used 3d pocket clearing, a steep and shallow command, followed by a ramp command with a smaller tool tip (1/8" Ball EM Long) to clear out the depressions. I wonder if the final result will be striated. The pipe depression along the edge is not as deep as it is in my model (looking at the simulation). There was trial and error in figuring out the right commands to use (a parallel pass for the edge gave a very uneven and unintended result).
- Drilling. I used a spot drill to make a starter hole (depth = diameter / 2). The drilling strategy was determined by measuring and calculating the depth / diameter ratio. Diameter = 3.175mm, depth = 10mm. Since the ratio is less than 3, I used a default drilling cycle (rapid out as opposed to peck drilling). Since the hole was so small I used tool 1010 (a 1/8'’ spot drill). I changed the depth to stock bottom so that the hole would be drilled past the depth of the model hole.
- Flip!
- Roughing. I added an Adaptive Clearing path to determine the silhouette and remove excess material with the 1/2" Rough EM Short tool.
- Face. I cleared the bottom face using a face command using the 1/4" EM Short tool.
- Finishing. I created the rounded edge using a Scallop command with the 1/8'’ ball tool used above.
- Drilling. I copied the drill command from above just for the sake of the simulation.
STEP FOUR [Simulation & Export]
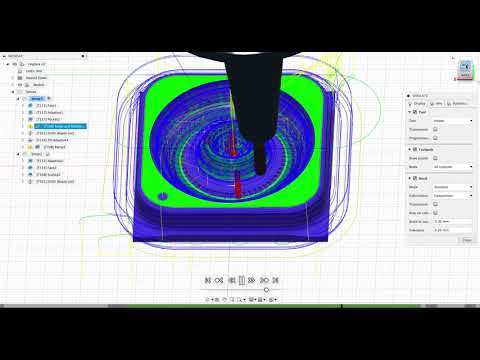
I’ve shared a video of the simulation that shows some leftover material (in simulate I selected Comparison for the color mode). In particular, I think the striations would be a cool addition to the design to create some texture. I’m not sure if the edges would be very sharp. I’ve also attached the set up sheet from the set-ups described above.
The set-up sheet and STL file corresponding to the ring box can be found here:
https://github.com/SoniaHashim/compfab/tree/master/week6