Upcycled Gradient Leather Dress
by kinkybutcute in Craft > Leather
476 Views, 3 Favorites, 0 Comments
Upcycled Gradient Leather Dress


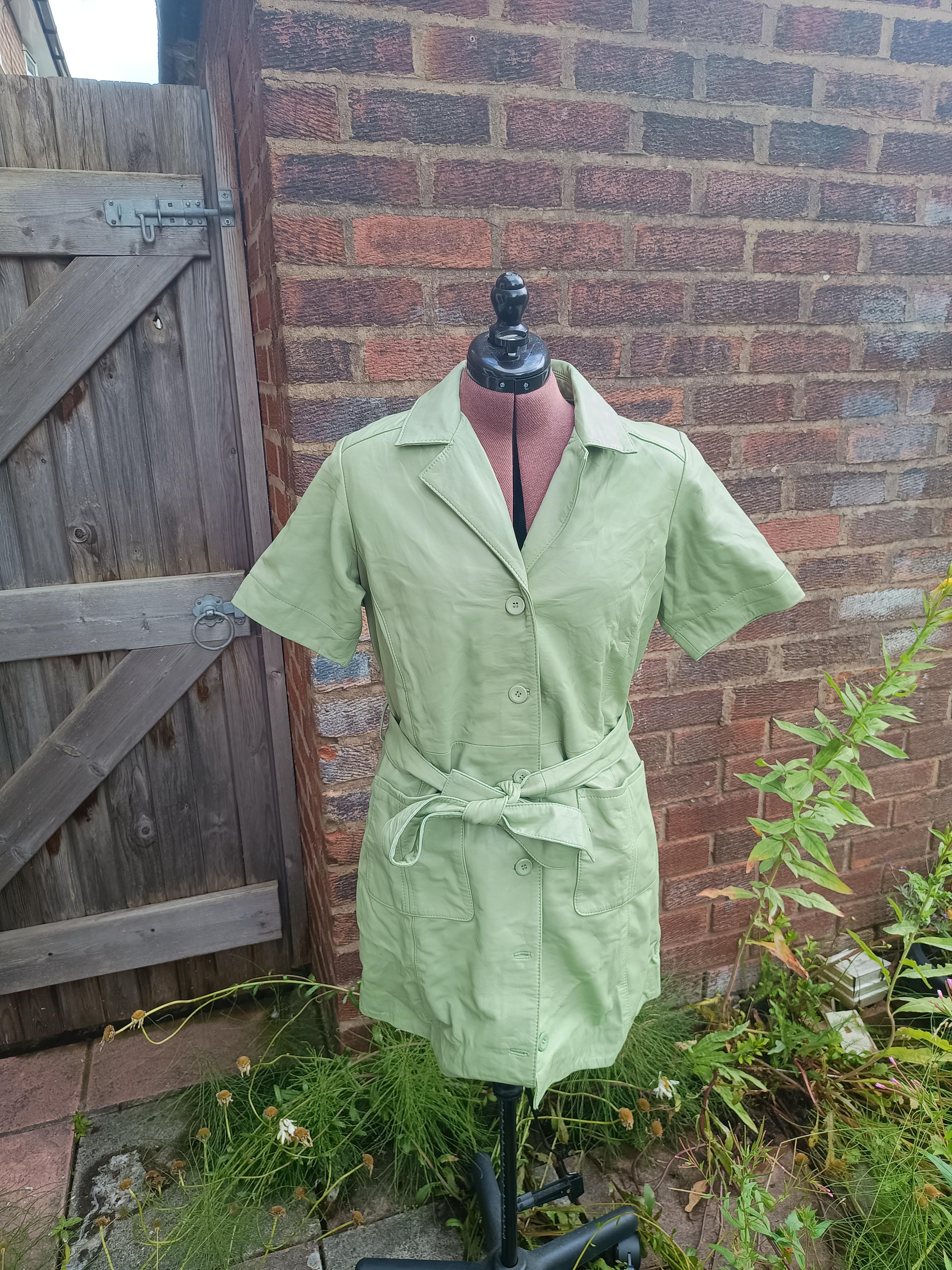
I found a truly hideous green and slightly stained leather dress on Vinted for £3 (the photo doesn't do it justice, it's a dress not even a mother could love) and decided that for £3 it was worth trying to salvage. So here's the process I used to improve it!
Supplies
- unloved real leather dress (must be a dyeable colour, e.g. white can dye any colour, yellow could go green etc.)
- leather deglazer (I used a full bottle of Angelus brand deglazer)
- rubbing alcohol
- wool daubers/other applicators
- protective gloves
- masking tape
- bin bags
- dress form if you've got it
- leather dyes (I used a range of Fiebings: yellow, turquoise, kelly green and USMC black)
- dye reducer
- leather finish/top coat (I used snow proof mink oil)
If you're casting new buttons:
- epoxy silicone casting kit and mixing supplies (I wanted to try out my shiny new resin mixer, but a plastic cup and wooden stir stick would work just fine)
- acrylic sheet/other smooth surface
- double sided sticky tape or other adhesive
- large plastic cup
- plasticine
- resin colourants (I used chameleon flakes, nail art powder in black, and black and silver resin pigment)
- epoxy casting resin
- needle and thread
Snip Off Those Buttons!

Nice and easy step - if your garment has buttons you can either leave them in place and dye around them or, if they're a nasty wrong-sort-of-pistachio colour, just snip them off and put them aside. My dress had small inner buttons that were sewn to the outer ones, forming a shank, so I made sure to put those aside safely.
Protect the Lining

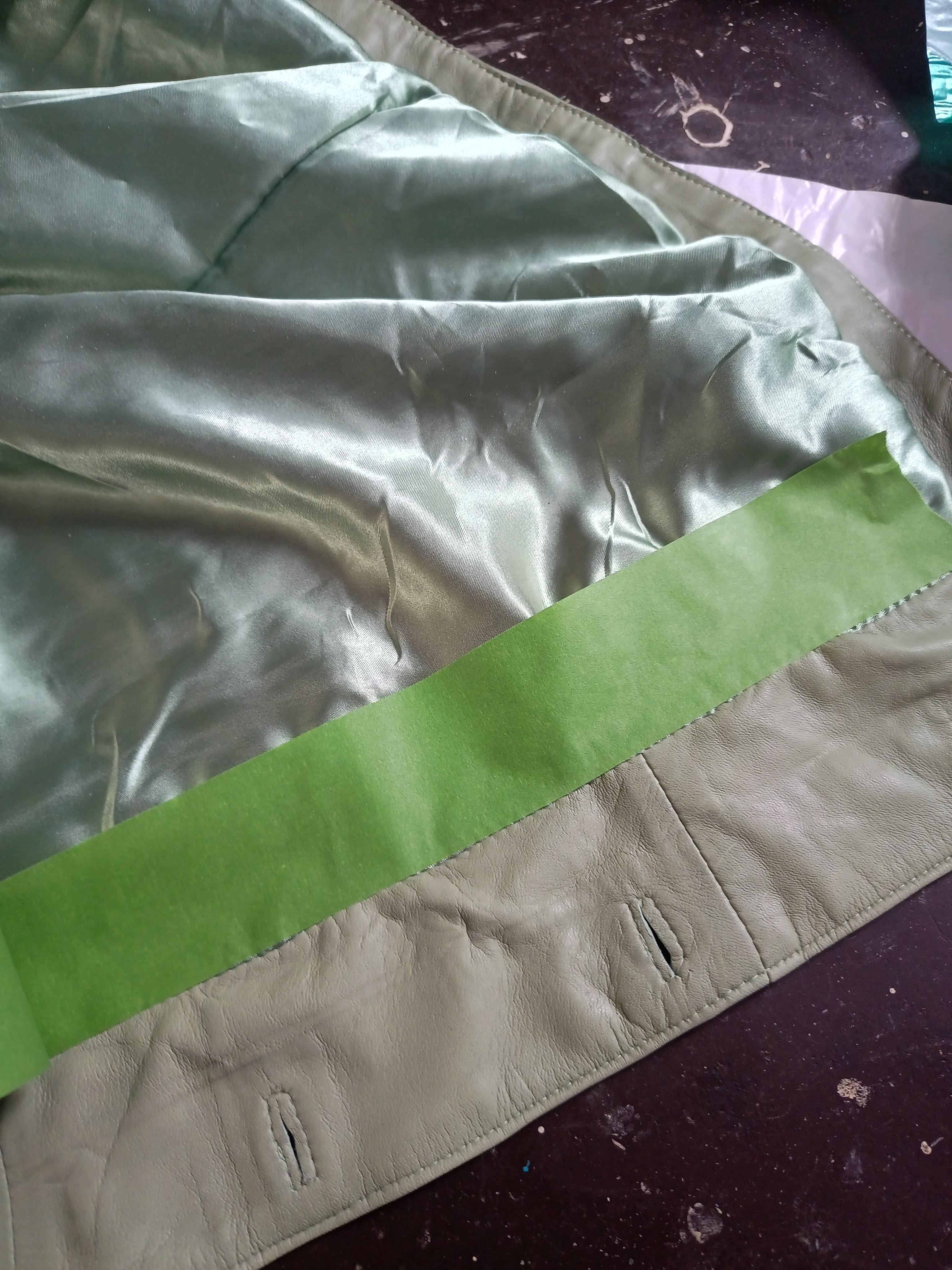

I taped all the edges where the lining met the leather - I decided a millimetre either way wouldn't matter too much, but I wanted to try and get a clean line between the redyed leather and the lining.
I then cut open some plastic bin bags and attached them to the masking tape with more tape (if you're feeling clever, you could combine the two steps and use less tape, but that sounded too fiddly to me).
Deglaze Leather

I used a wool dauber (not pictured, I switched from the less effective J cloth) to apply the deglazer, working it into the leather in a circular motion. I recommend doing this outside, as it has a pretty strong smell. And definitely wear gloves, deglazer has some fairly nasty chemicals in.
After applying to the whole dress the leather looked a little patchy - as I was going for a darker overdye this wasn't really an issue for me, but I went ahead and did a second go over the whole dress but with rubbing alcohol this time (giving a quick wipe with rubbing alcohol is good practice any time you plan to dye some leather).
Make Mould

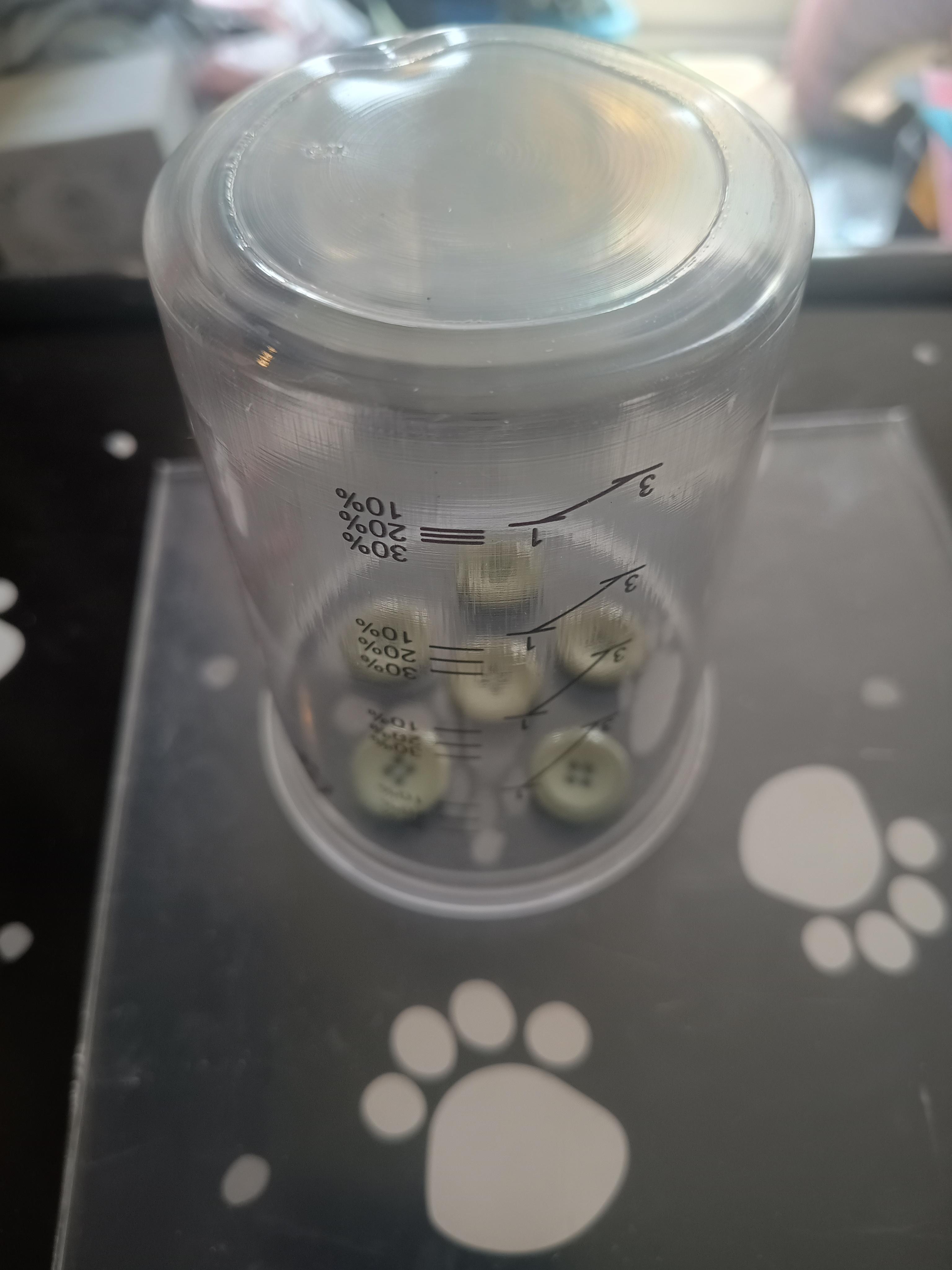






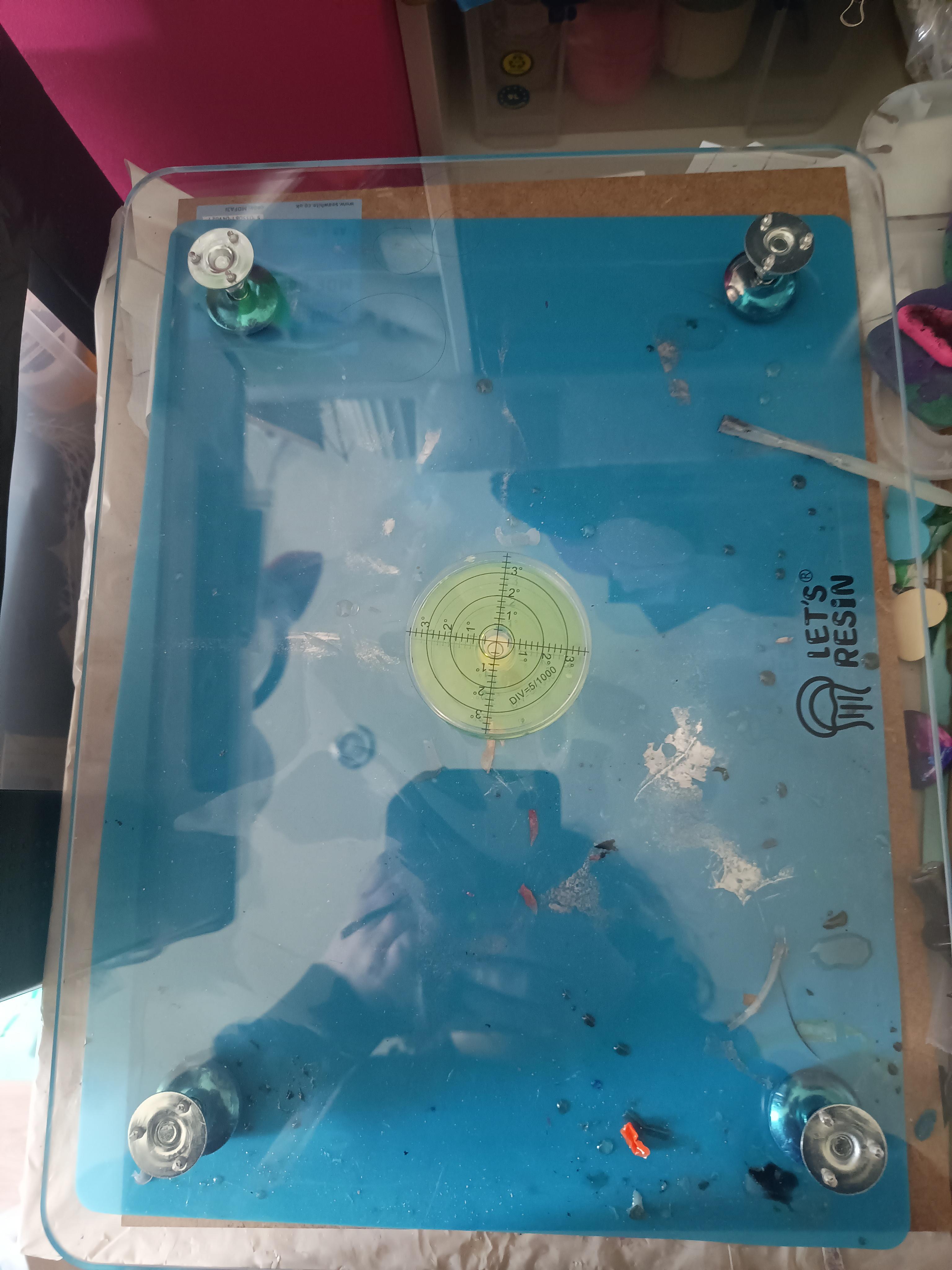





I really wanted to get on with dyeing that dress, but the weather conspired against me. So I went ahead and cast the buttons in silicone.
First I grabbed a large plastic cup, and checked it would fit the six buttons comfortably. Then I used double sided sticky tape to attach the buttons to the acrylic sheet, and cut a ring from the lip of the cup. I then squished plasticine all around the rim, attaching it to the acrylic sheet.
I then checked I had a level surface to cast on (enter the circular spirit level), and mixed up my silicone. My kit was 1:1 by weight, and my mixing cup was about the same diameter as the mould cup, so I weighed out the first part to around half the height I wanted the mould, and then did part B to the same weight (27g each time). I then used my very exciting new resin mixer to mix up the silicone, gave the sides a scrape, and mixed it again.
I was a bit worried about getting air bubbles in the button holes, so I took a cocktail stick and deposited mixed silicone into each hole. I then poured the rest of the silicone from a height of 30cm, and left it to cure.
In the end it turned out pretty good!
Cast Resin Buttons






With the weather still conspiring, I painted my button mould and cast the resin.
First I used chameleon flakes to paint a bit of colour into the button mould. Chameleon flakes are very static-y, so be prepared for them to fly in all directions!
Then I used black nail powder to cover the rest of each button cavity. I mixed up some epoxy casting resin, coloured it with black and silver pigment (the silver isn't necessary, I just felt like making the backs of things pretty!) and filled my mould up. As you can see, I had some extra moulds on hand to use up the excess resin. I don't tend to mix less than 30ml of casting resin at a time, as less would be both fiddly and also liable to not cause the necessary chemical reaction for hardening it.
Finally Dyeing the Dress!!







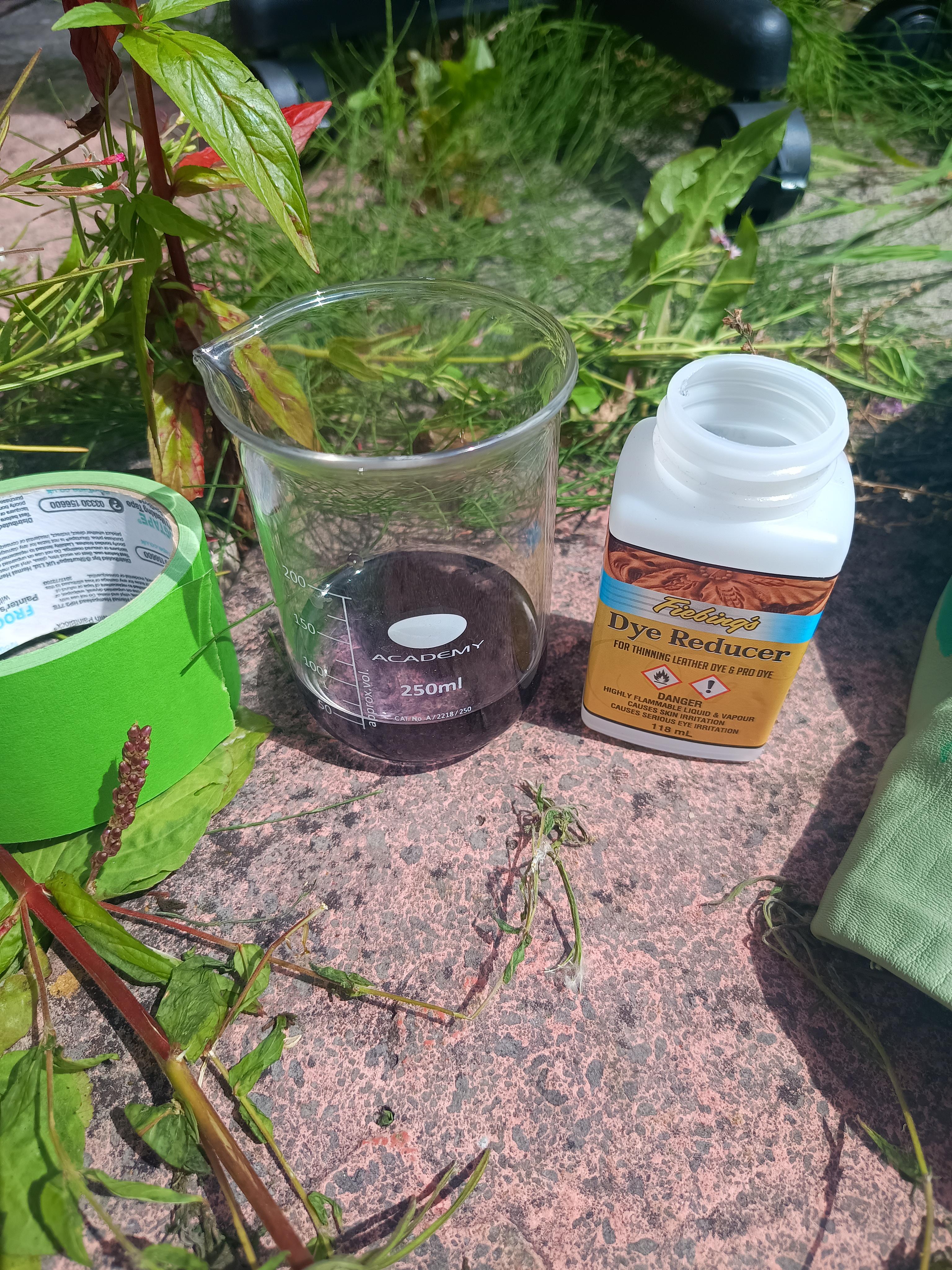





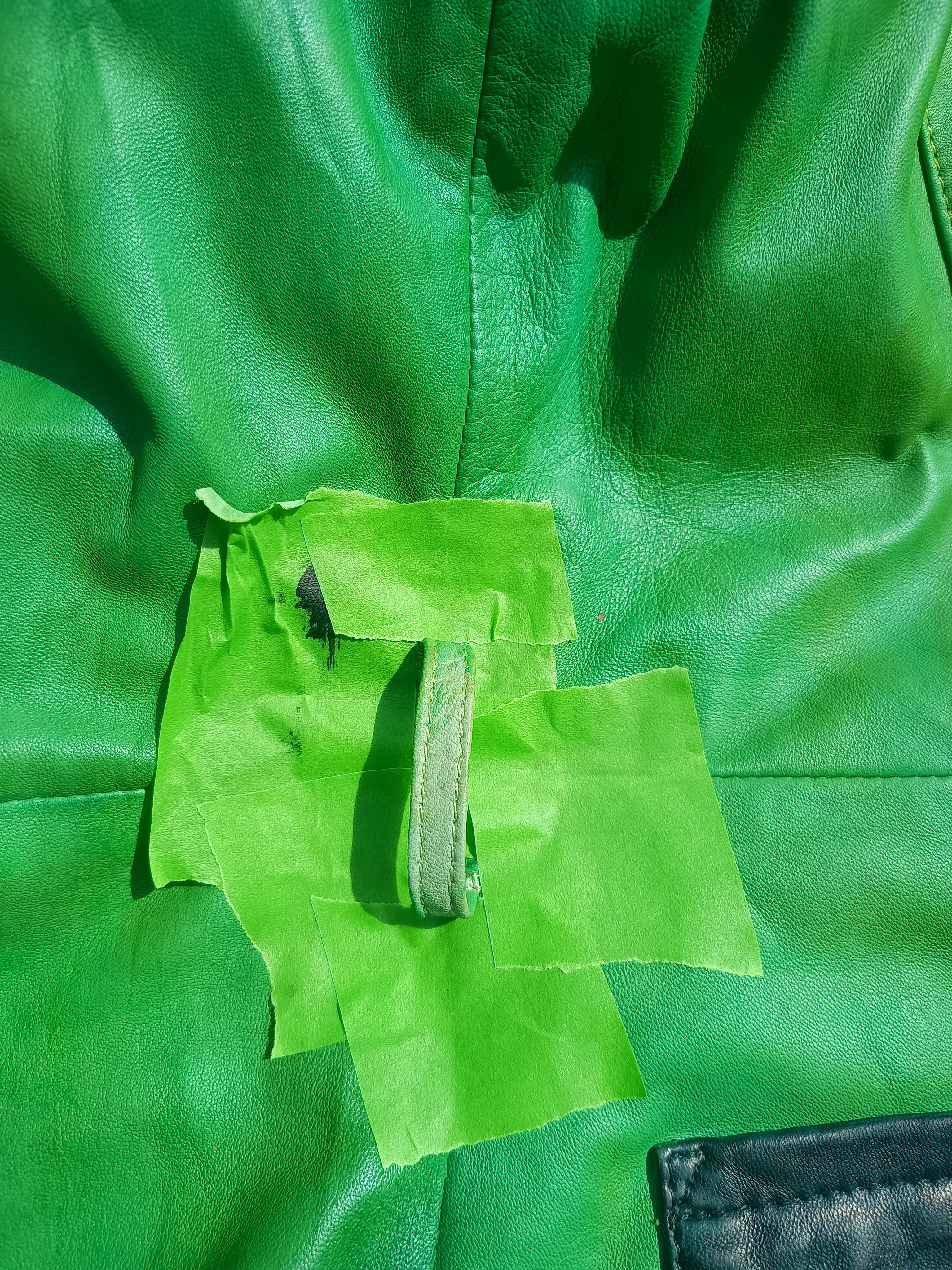





At last the weather and my energy levels cooperated! I took my tailor's dummy outside, and stuffed the dress with a cushion and some old bubble wrap to make a sort of scarecrow.
I started off spray dyeing with plastic spray bottles, but I didn't like how it was going (Future Me is getting an airbrush...), so I switched to my trusty wool daubers. I used a lot of yellow at the top with a little turquoise (Fiebings turquoise is very weak compared to its other colours, so it made for a bright yellowy green), transitioning to kelly green for the main body.
For the fade to black at the bottom, I used a lot of dye reducer in a pot, with a tiny pipette quantity of black. I worked my way down, adding another squirt of black at a time, until the very bottom was undiluted black. I also masked off around the pockets and belt loops with frog tape, and painted those solid black too, along with the entirety of the belt.
Once the outer dress was all done, I turned it inside out, and dyed the inner edges and collar black too. I used a makeup applicator to do the very edges black as well.
Top Coat
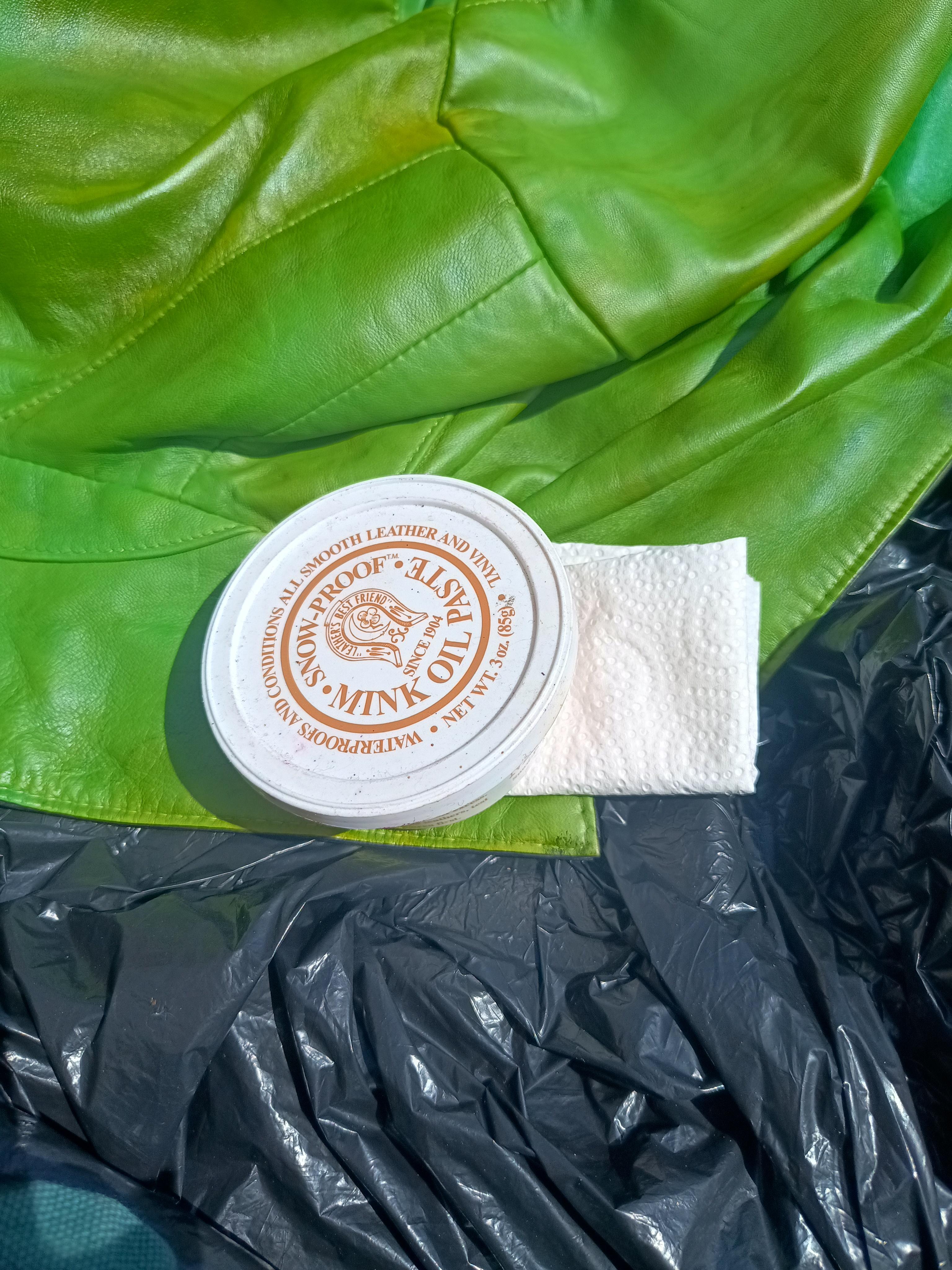

After the dye had dried, I put a top coat on. Because I thought the deglazer might have been quite harsh on the leather, I chose to use an oilier more nourishing finish, in this case snow proof mink oil. I used paper towels to apply it all over the leather, and more paper towels to wipe the excess off. Some excess dye also came off at this stage, so I just kept applying and rubbing until I'd got most of it off.
I then removed all the tape I'd been using to mask with.
Sew on Buttons




I then used linen thread to sew my new buttons on. I took the original backing buttons and the new resin buttons, and sandwiched through the original holes in the leather, making a shank out of the thread. I first sewed through the pairs of holes in the front button twice, going through the leather and back button each time, then I wound the working thread tightly around the thread shank behind both buttons front and back, tied off, and sewed each other button in the same way.
Done!




The dress turned out gloriously garish, and I'm really happy with the result. My advice to someone taking on this type of project would be: start out with an item you're not too invested in (i.e. something ugly/damaged you wouldn't use as is) before taking on anything you really love or was expensive. And go with the flow - my original dye application method just wasn't working, so I switched to daubing. It's a different result to my original plan, but I love the trashy chaos result anyway!