Under Desk Tool Drawer [Modeller's Delight]
by Hey Jude in Workshop > Organizing
80877 Views, 1313 Favorites, 0 Comments
Under Desk Tool Drawer [Modeller's Delight]
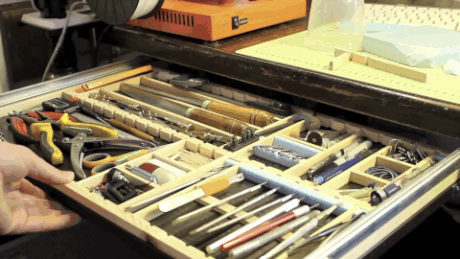
![Under Desk Tool Drawer [Modeller's Delight]](/proxy/?url=https://content.instructables.com/FF2/ULUZ/HWRC29PL/FF2ULUZHWRC29PL.jpg&filename=Under Desk Tool Drawer [Modeller's Delight])
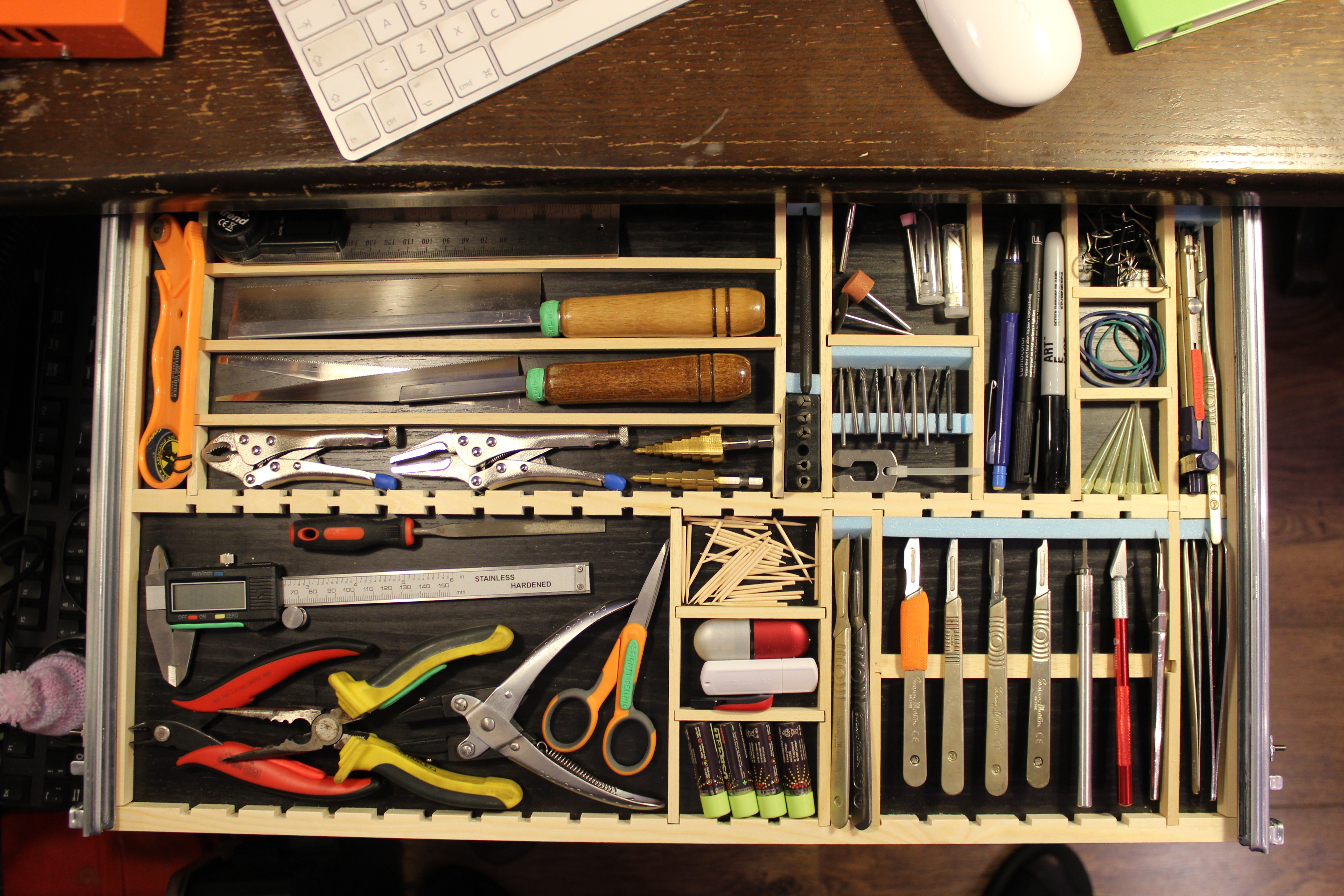
The perfect way to store your sharp tools under your desk. Made from re-purposed kitchen cabinet runners and some scrap wood. This Instructable also expands on how to do this with no specialist power-tools for low cost.
WHY I MADE THIS: I just moved to London (to start working at sugru). London is clearly more expensive than Bristol, so my 'workshop' is now in one corner of the kitchen. Space is a premium and I needed not to leave my sharp tools all over the place when not in use. I looked around for ready-made solutions to store tools under my desk, but they were either around $40 (and not deep enough) - and certainly not reconfigurable.
SCAVENGE: The solution came when I was at IKEA's Bargain Bin and saw two (really smooth) kitchen cabinet runners going for 50p each. I grabbed a bit of scrap wood and knew this was going to save the day!
NO POWER TOOLS REQUIRED: I appreciate this is not 'hard-core innovation', but I thought I should share it with people as firstly, it seemed to impress some of my friends - and secondly, it surprised them that I didn't use any heavy machinery to modify the runners. THIS is the focus of this Instructable, and I will show you how to cut metal with Nibblers (yes, really they are called that) and how to chisel out a slot with a screwdriver (if you don't have a circular saw). [Zona Saw is optional, as Junior Hacksaw will do too.]
SHARE THE LOVE: If you are familiar with my website Design Modelling, you'll know that although I often have access to fabulous workshops and facilities as a Design Engineer - I get kick out of being able to do things cheaply, safely and well... so please let me know how you get on with this Instructible - and of course share any pro tips of a similar nature!
Tools, Materials & Diagrams
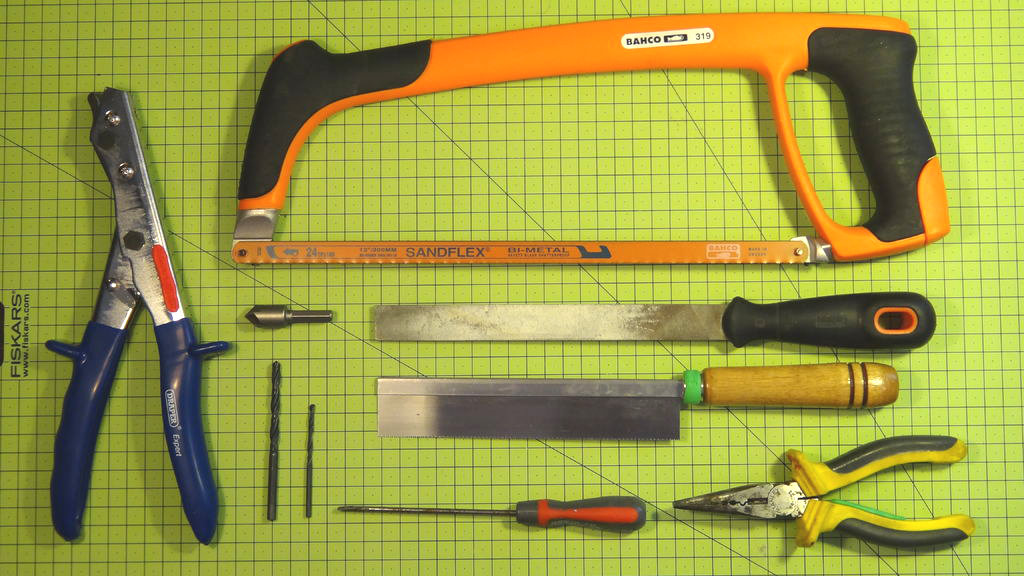
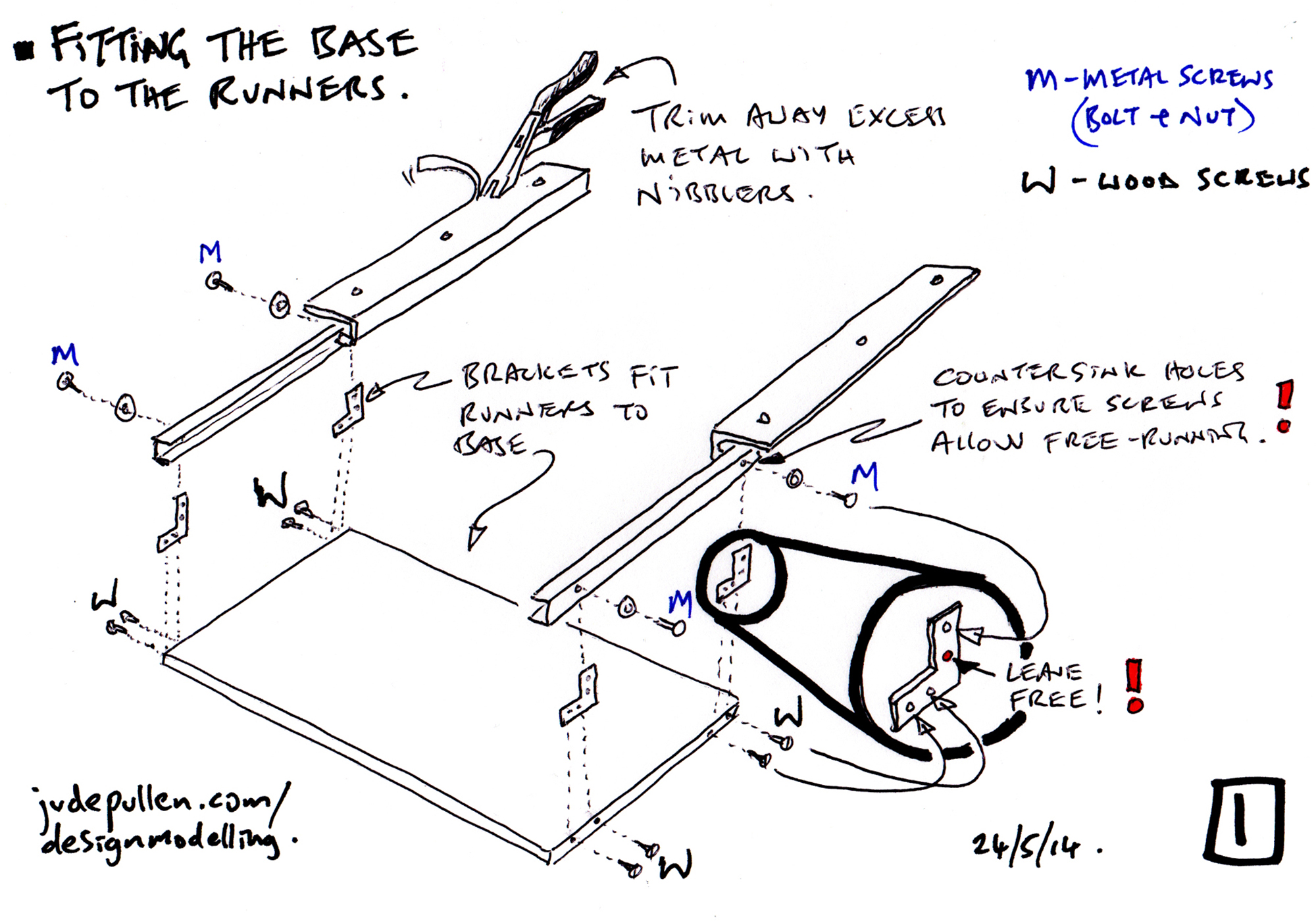
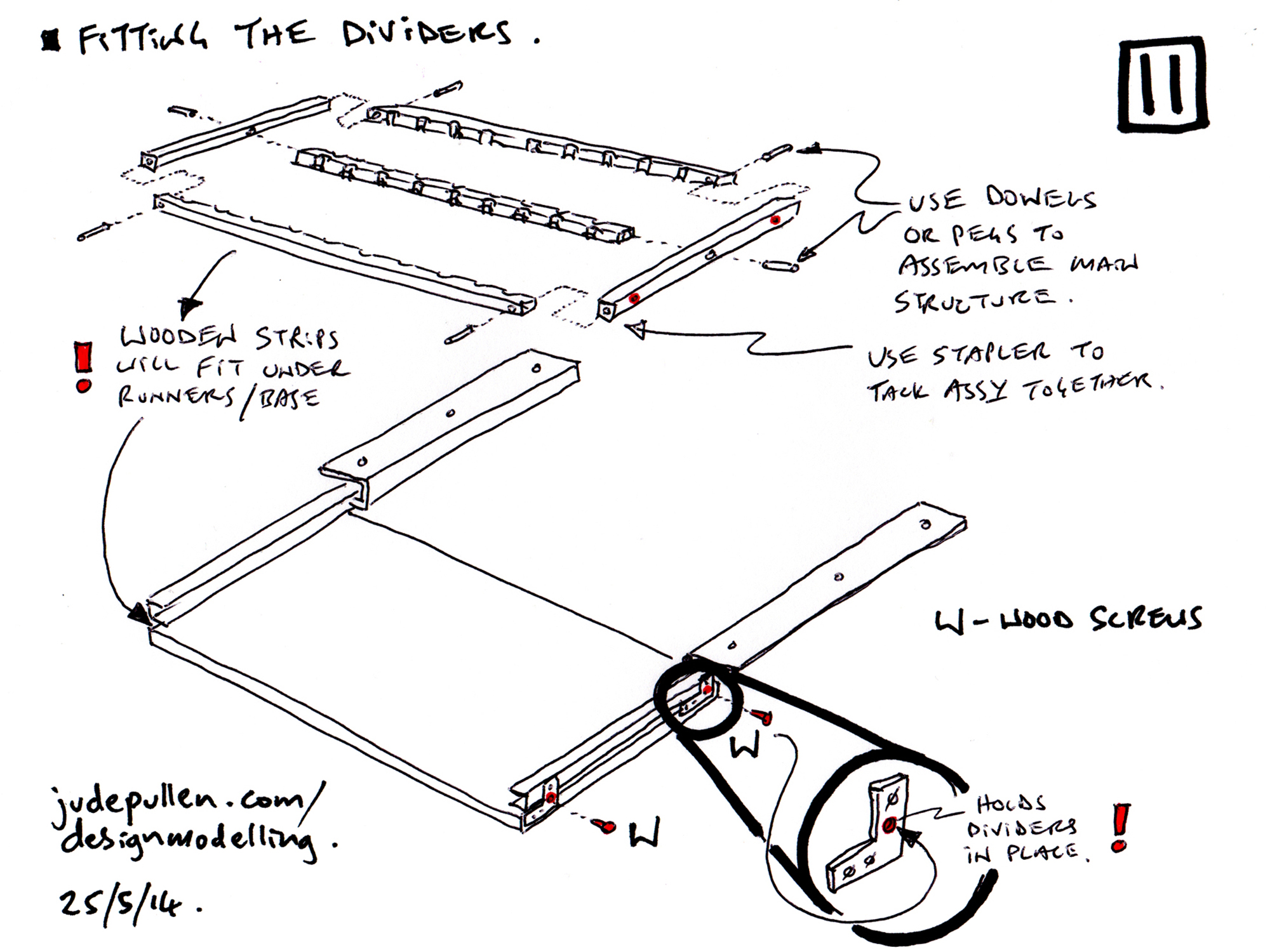
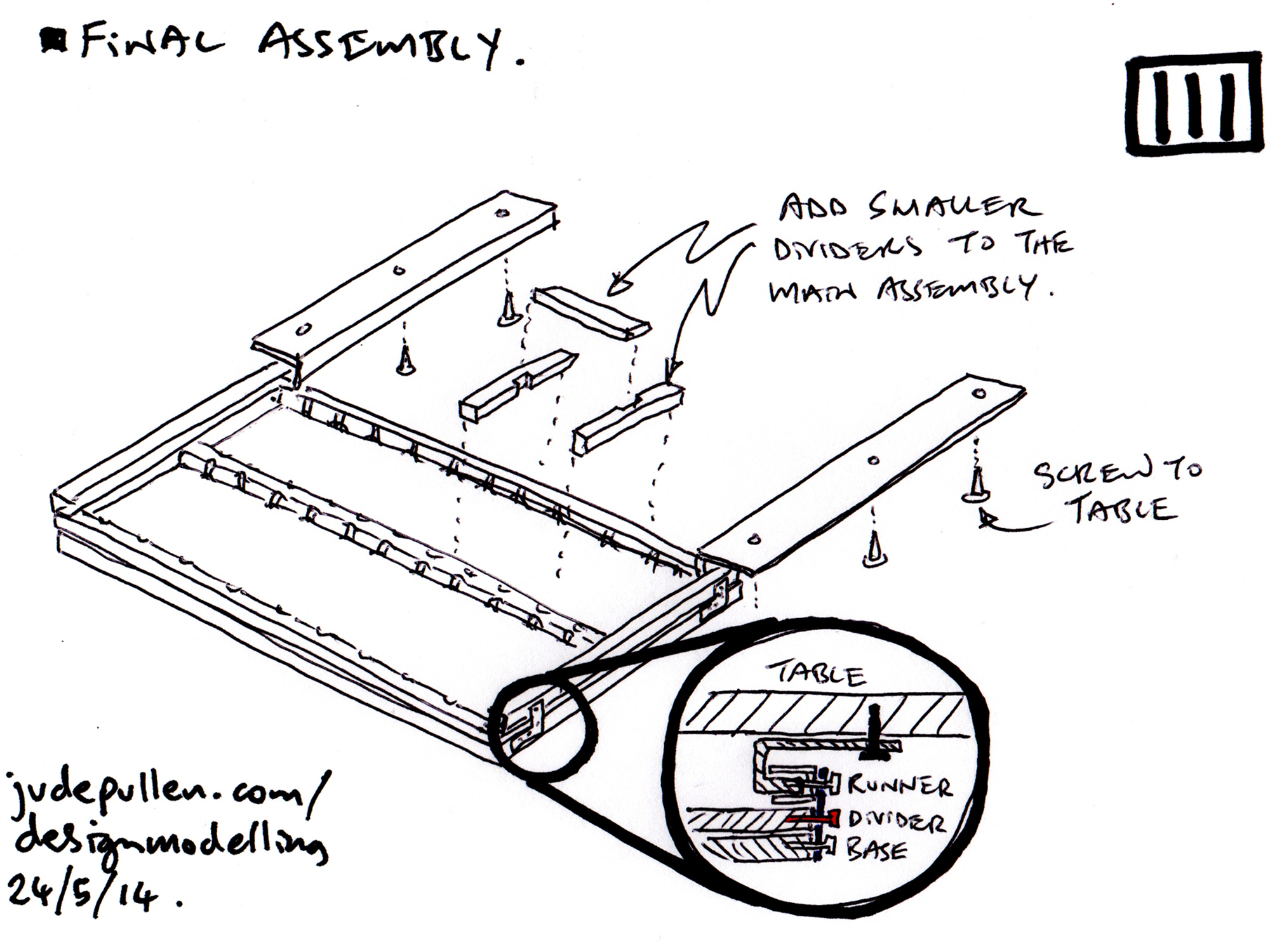
TOOLS: I'm expecting most viewers of Instructables have many of these tools, but here they are for completeness:
Nibblers* | Hacksaw | Drill Bits & Countersink | File | Razor Saw* | Flathead Screwdriver | Pliers.
*More on these later. The only one not shown is a Power Drill.
MATERIALS: Other than the scavenged stuff, like Runners, the 'strip-wood' was 12mm square section and 12x5mm section: I bought about 2 each of 2m length. I used M3 countersunk (CSK) Bolts (15mm long) with nuts and washers, and 12mm and 25mm Wood Screws.
DIAGRAMS: So... I had deliberated over whether this in fact was and Instructable, owing to the fact that the kitchen cabinet runners (and integral part) are not exactly 'off the shelf'. Consequently, I felt it was only right that I sketched out the overarching process, so that regardless of what runners and bits of wood you do scavenge, you get the general idea and can easily have a go at it.
Hopefully this is neither totally confusing, or patronisingly obvious. Although, even if it is obvious, I recon there will be a few pro tips that are worth knowing anyway, so read on...
Modifying Metal Runners: Using Nibblers
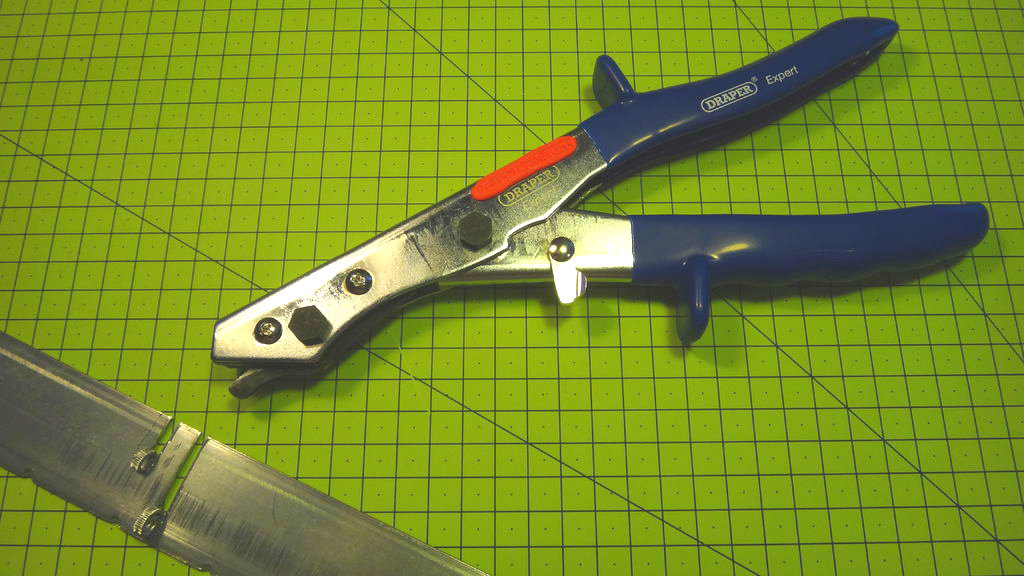
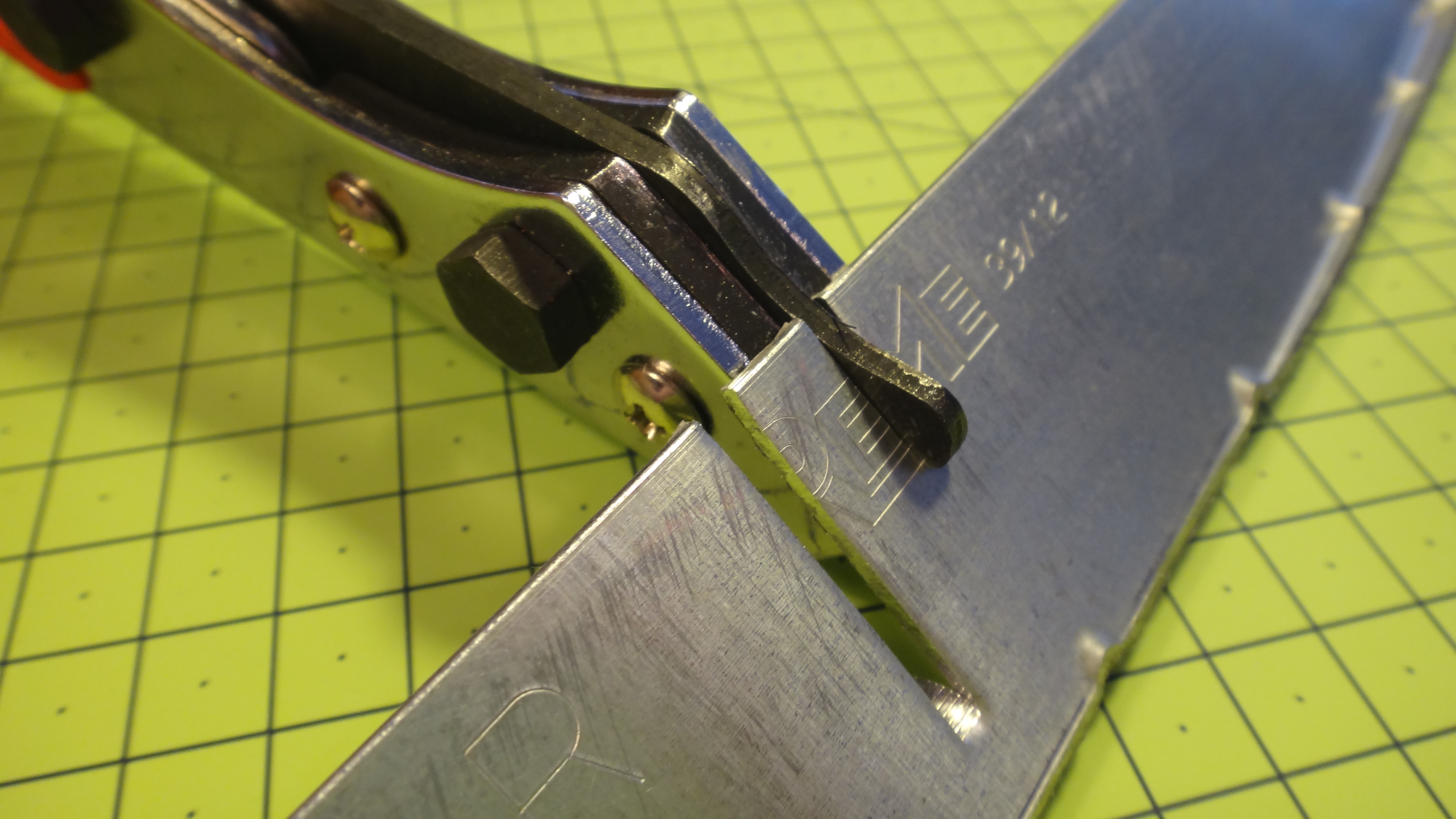
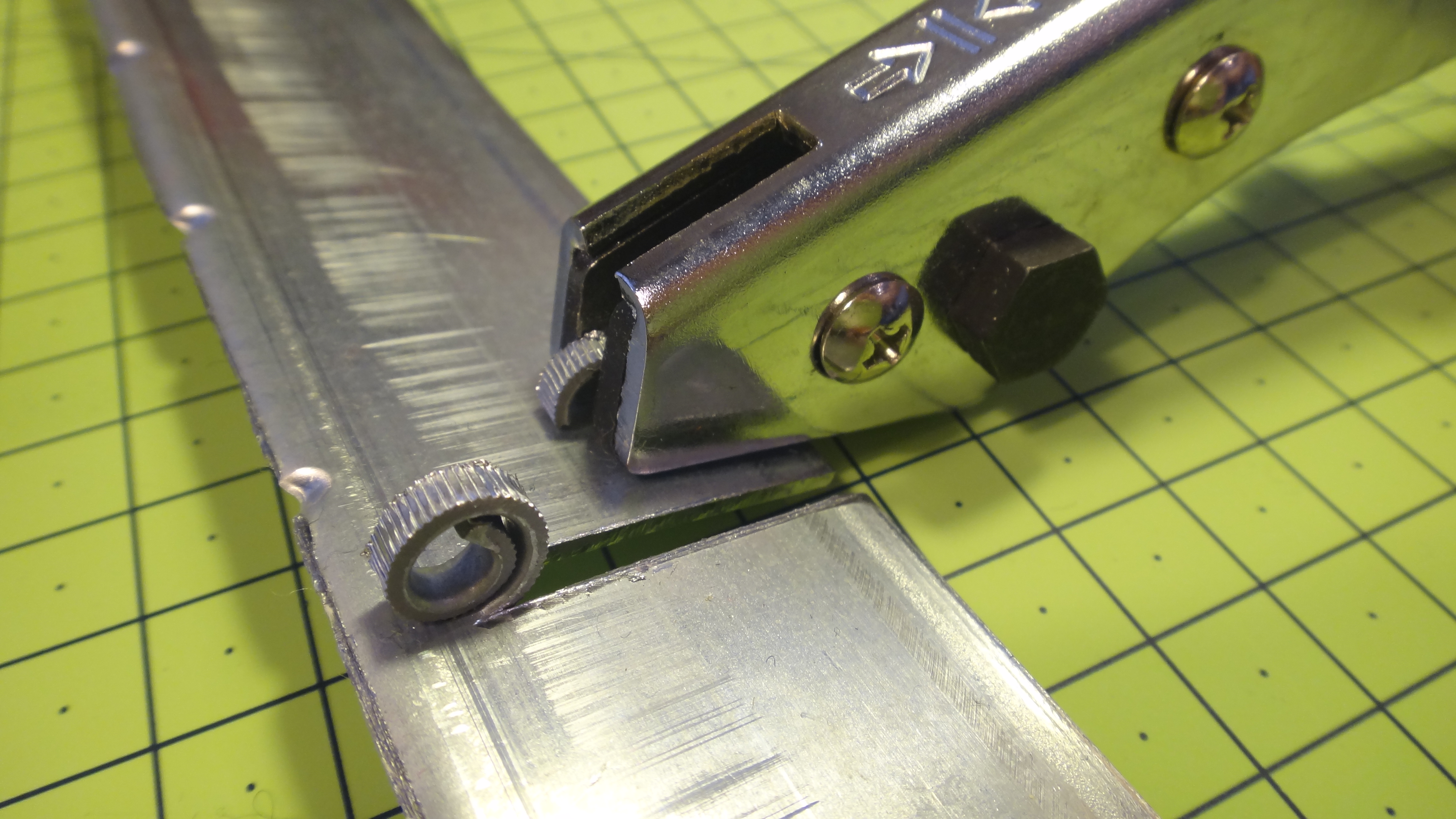
As mentioned, there is an emphasis on simple tools for the job. Nibblers have been a game-changer for me.
Nibblers - from Amazon - allow you to hand-cut sheet metal up to 2mm thick, for around $15-$25. Aside from being very safe to use, they also allow you to get into small corners or even make a round hole square. Even if you have power tools that do the same job, arguably these give great control.
As you can see they cut a 3mm channel out, so bear this in mind when cutting away work. However, unlike shears or tin-snips, they do not buckle or twist the metal and you are left with a 'flat' cut every time. Granted it requires some force, but less than you'd expect all things considered.
Joining Brackets to the Runners (+Countersinking)
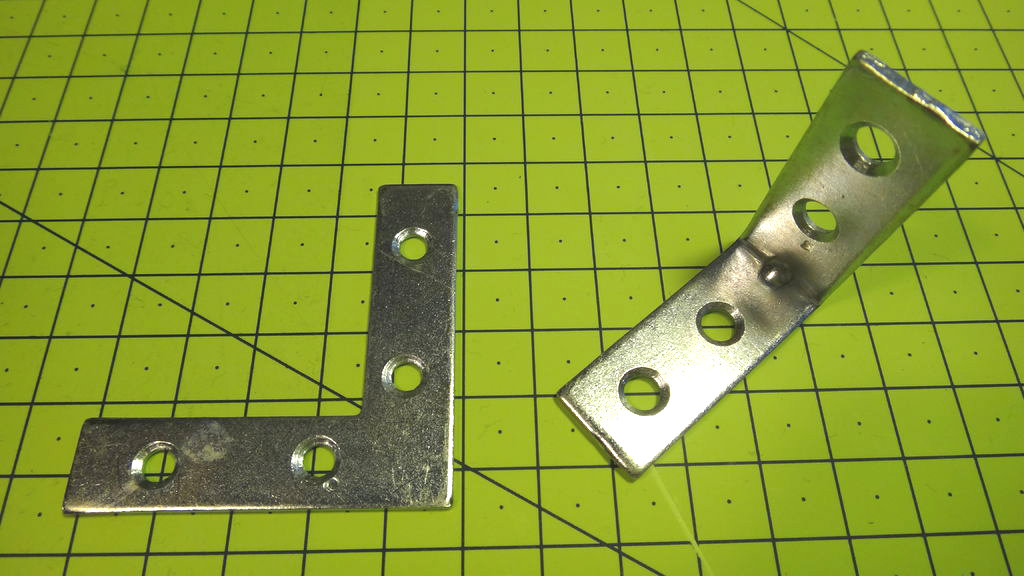
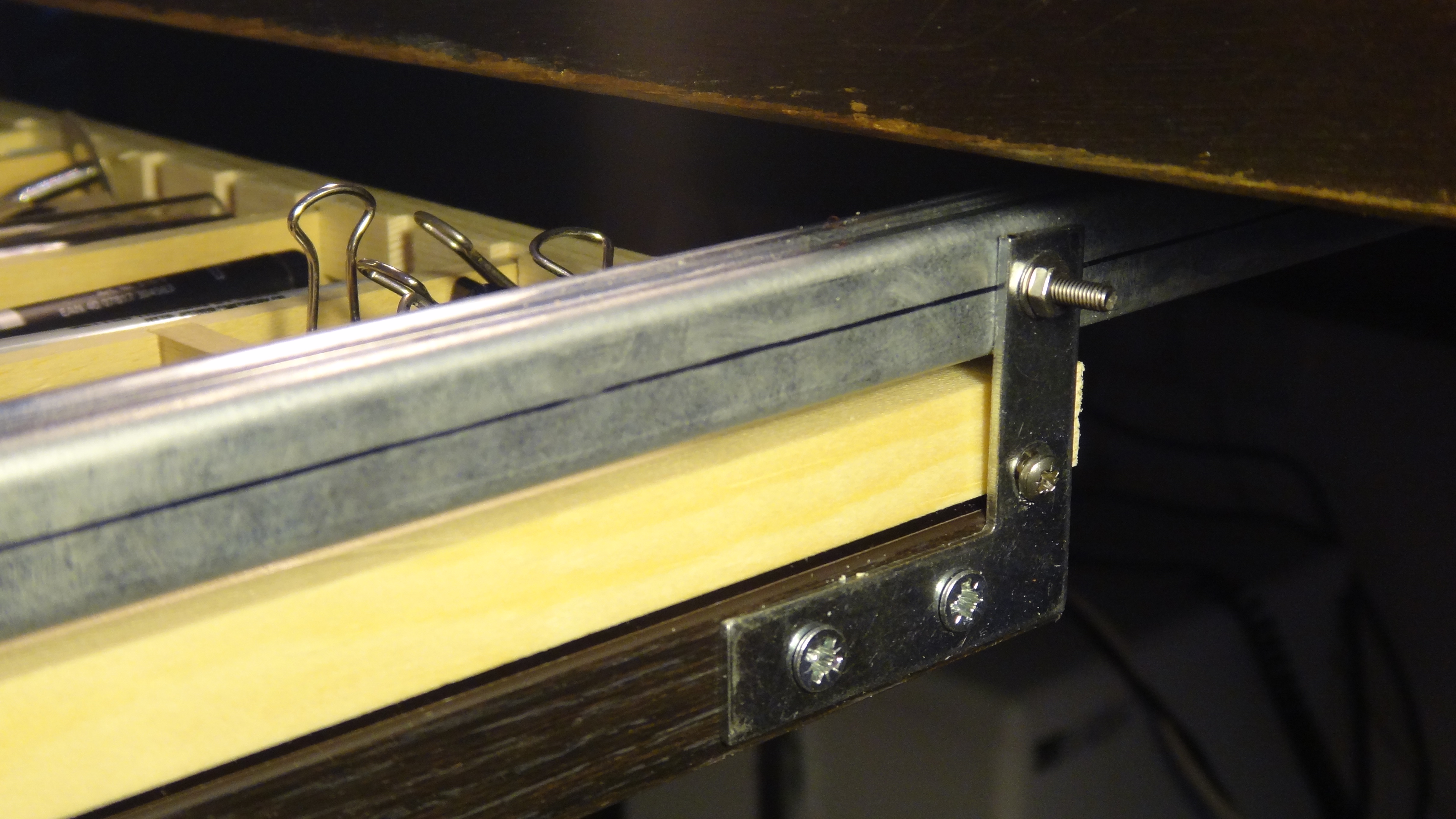
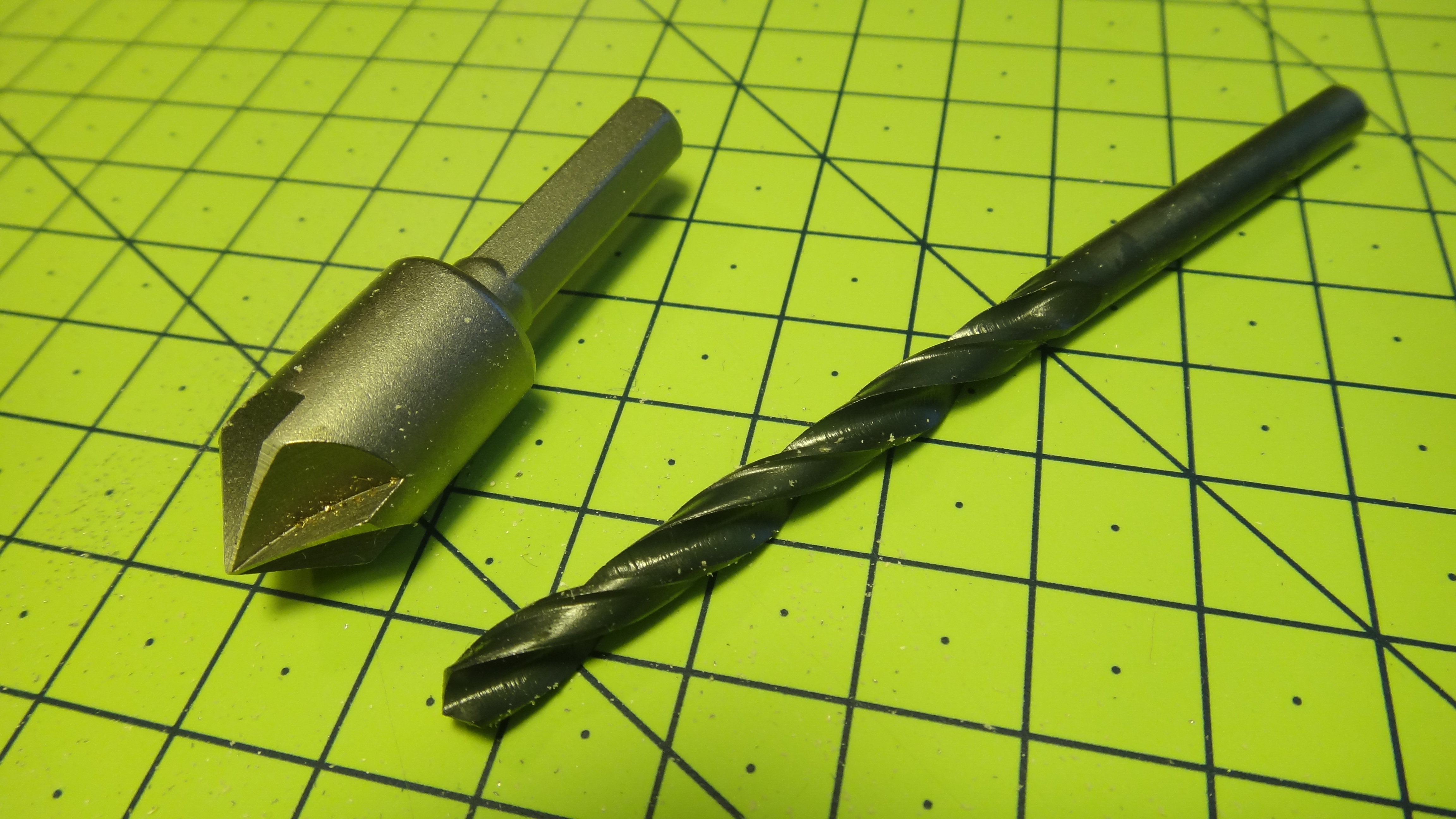
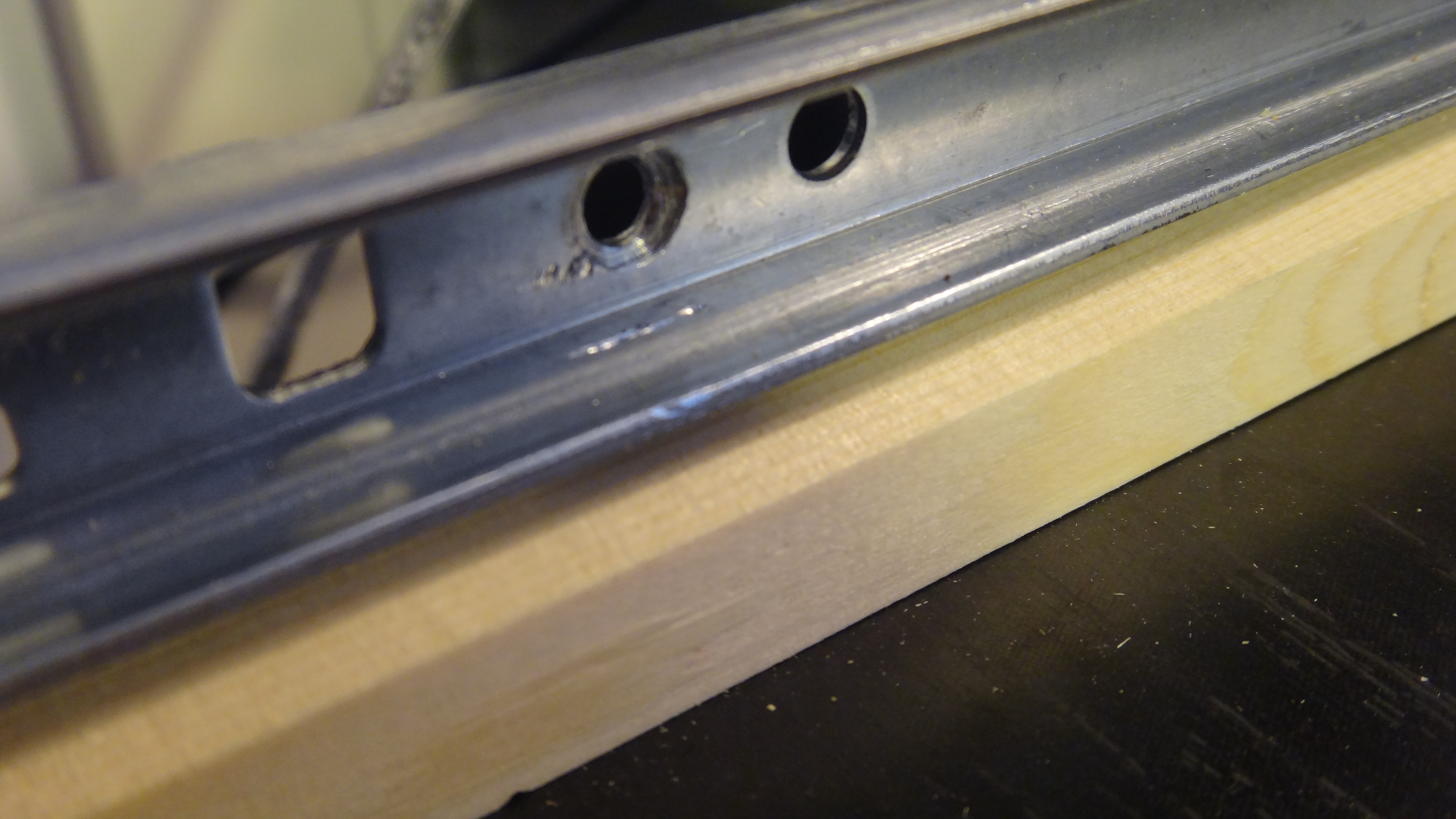
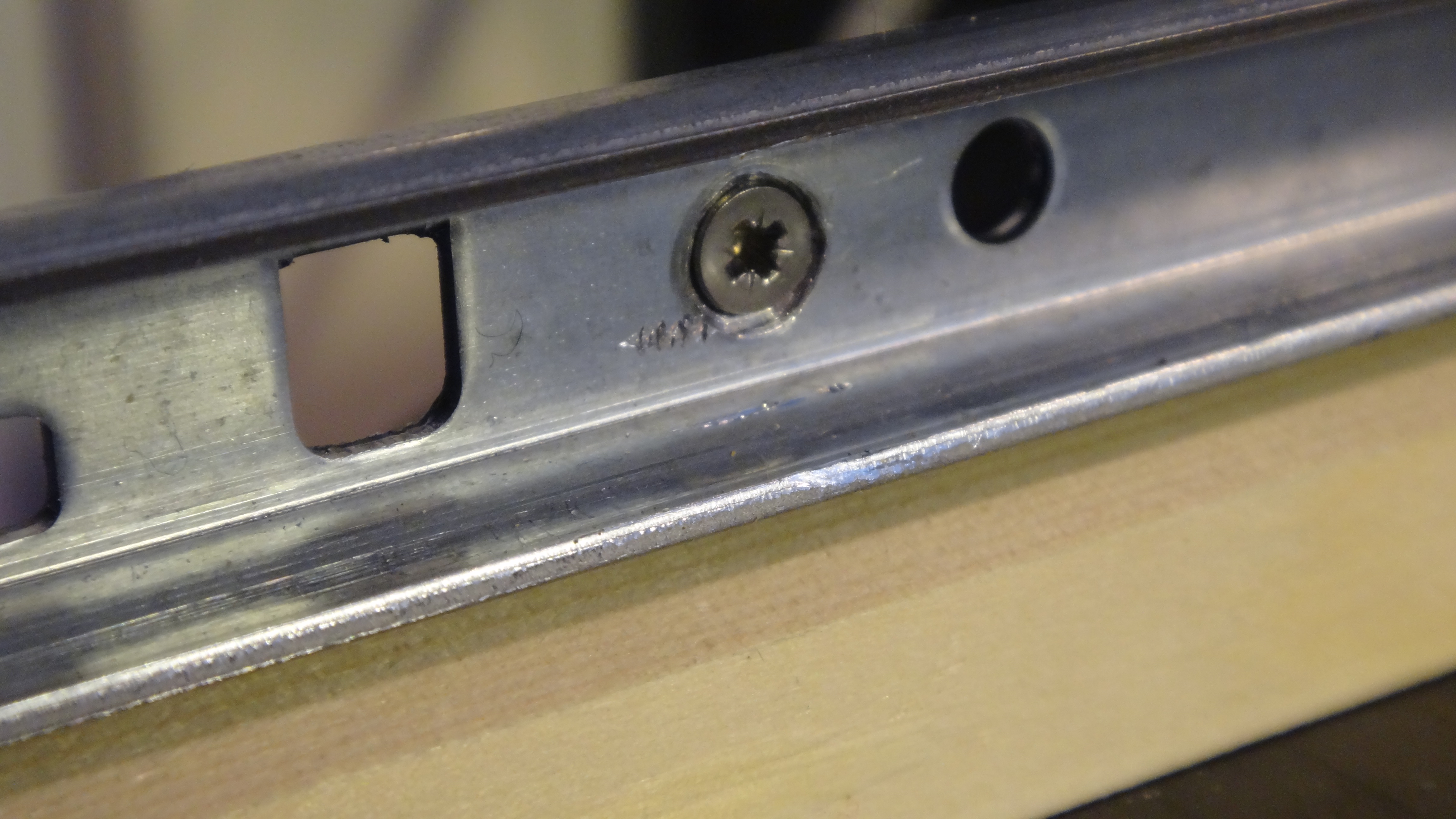
The first pictures show the bracket and how it'll end up like. The following mages show you how to do it...
This will be different depending on what Runners you have scavenged, but chances are, you may end up needing to fix the bolts from the 'runner-side'. In other words, if you used a screw which protrudes, it will get in the way of your runners and stop them extending fully. The solution is to countersink them.
What if you don't have a Countersink? Don't worry, you can use a larger drill-bit to make something that works pretty much the same as shown. It may even be the case (like with my runners) that a countersink did not fit, so this was my only option!
Once you get the hang of this, attach the rest of the brackets - allowing enough space for your wood 'dividers' to fit in, in some orientation. Again, this will vary with what you have to hand, but you get the idea...
Joining Brackets to the Base. (+How to Trim a Bolt to Size)
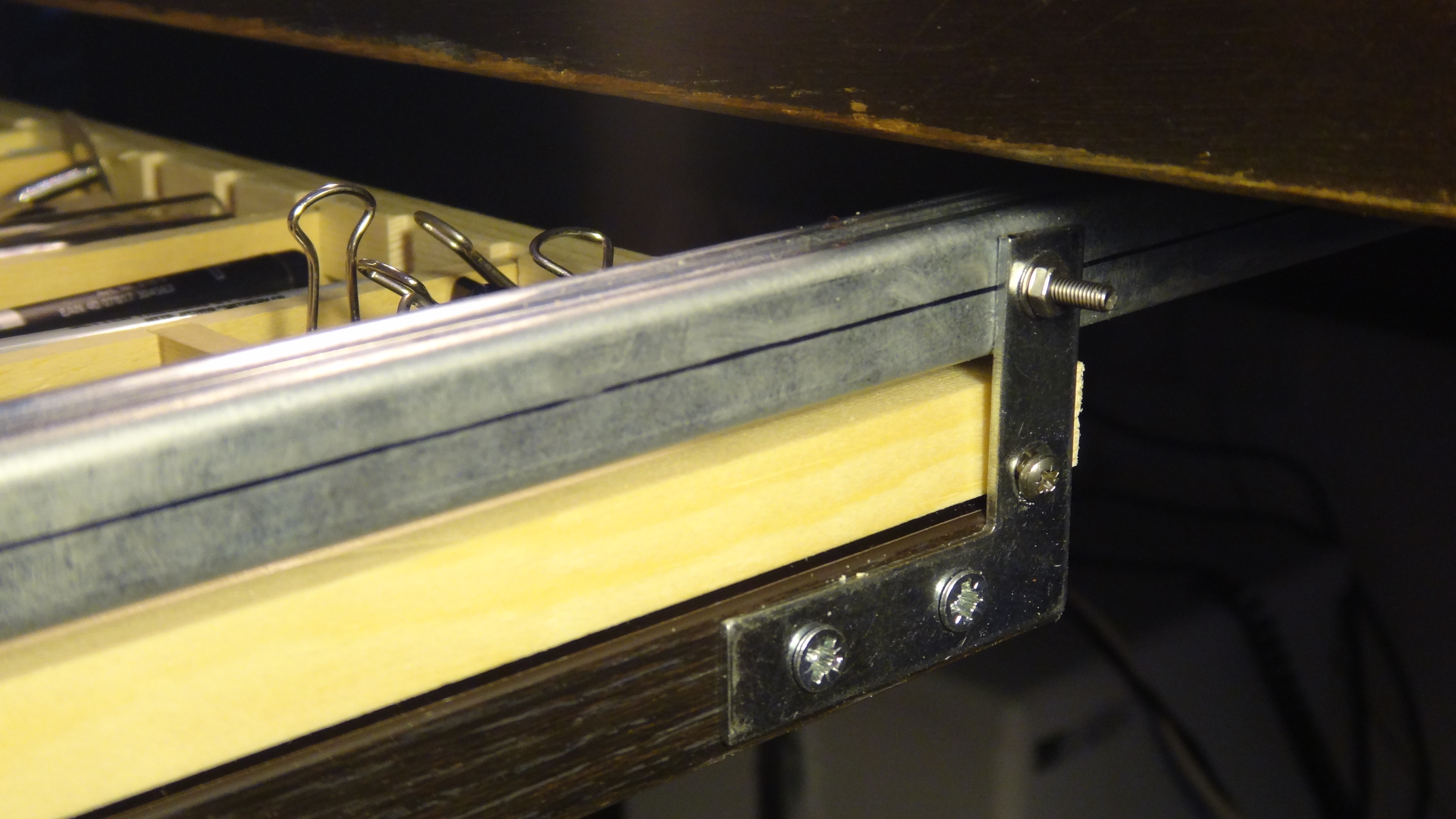
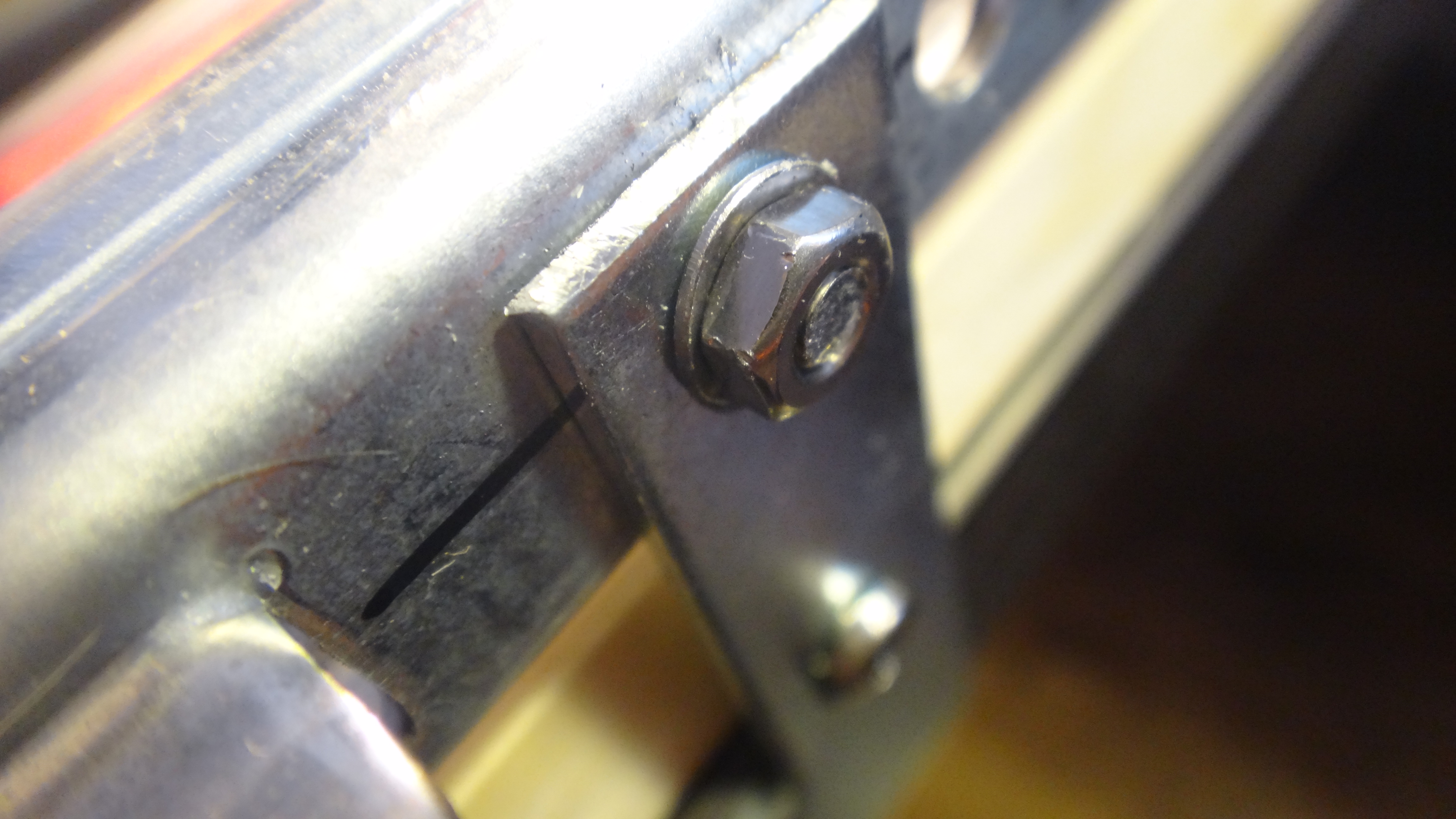
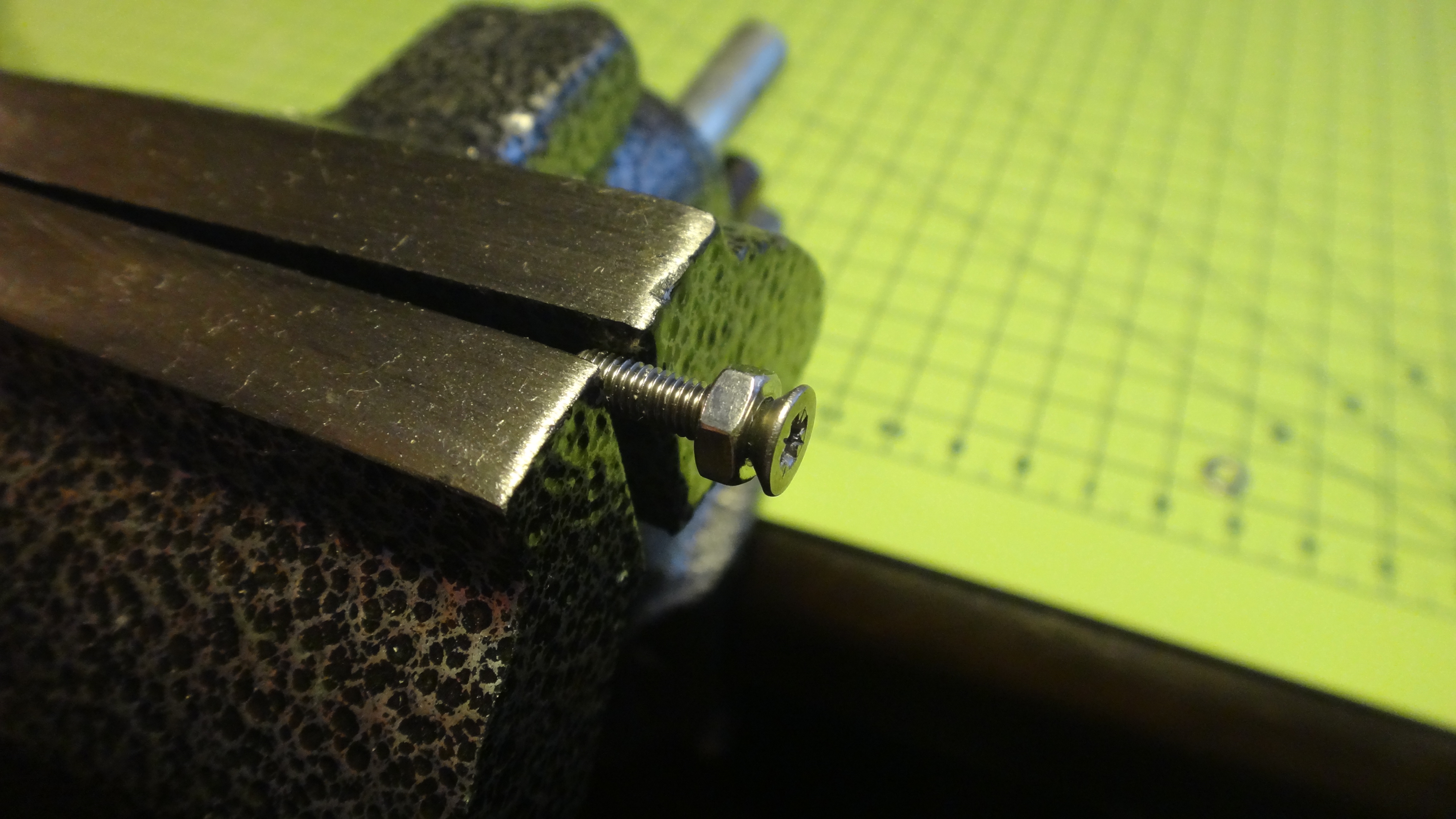
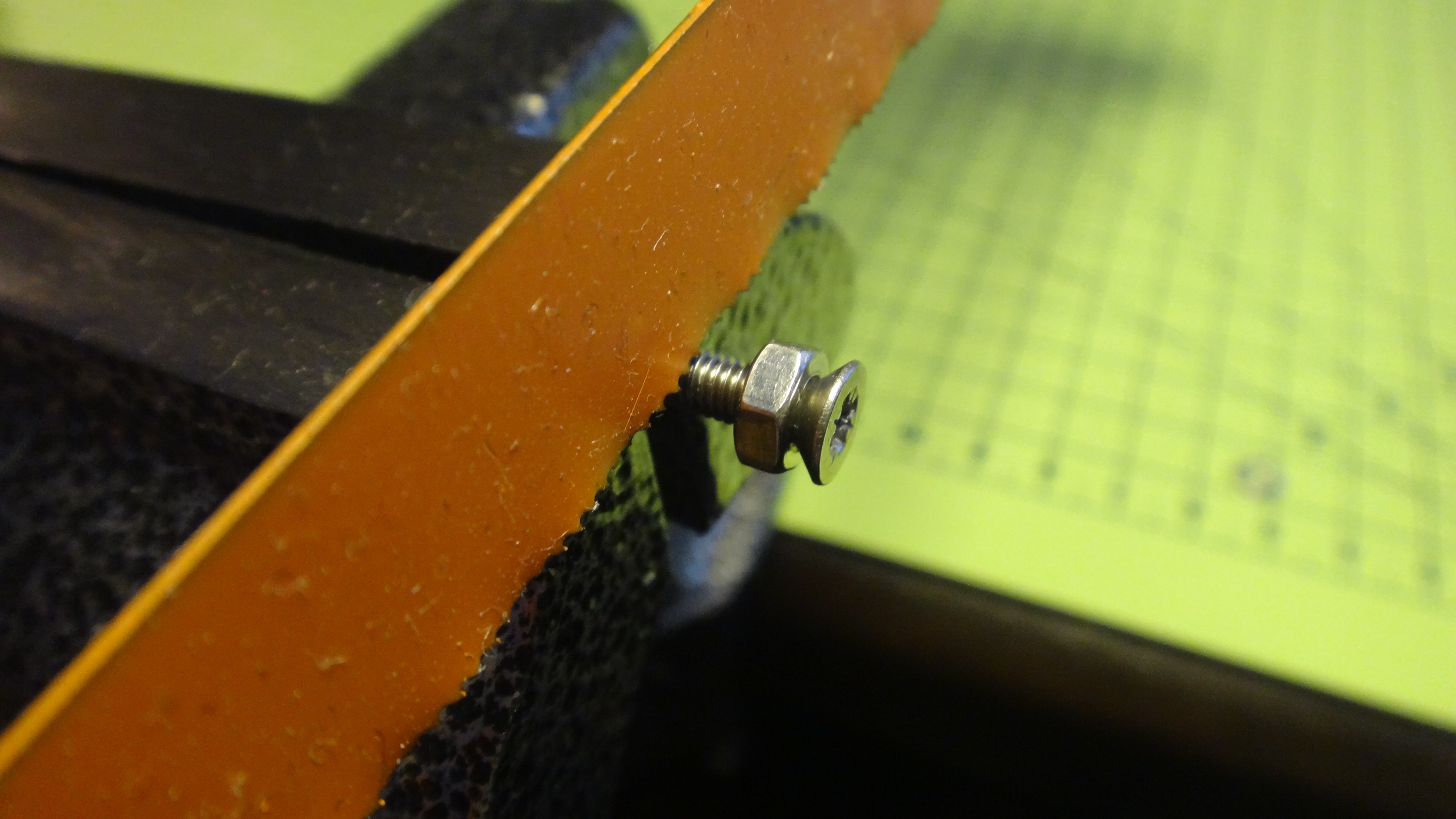
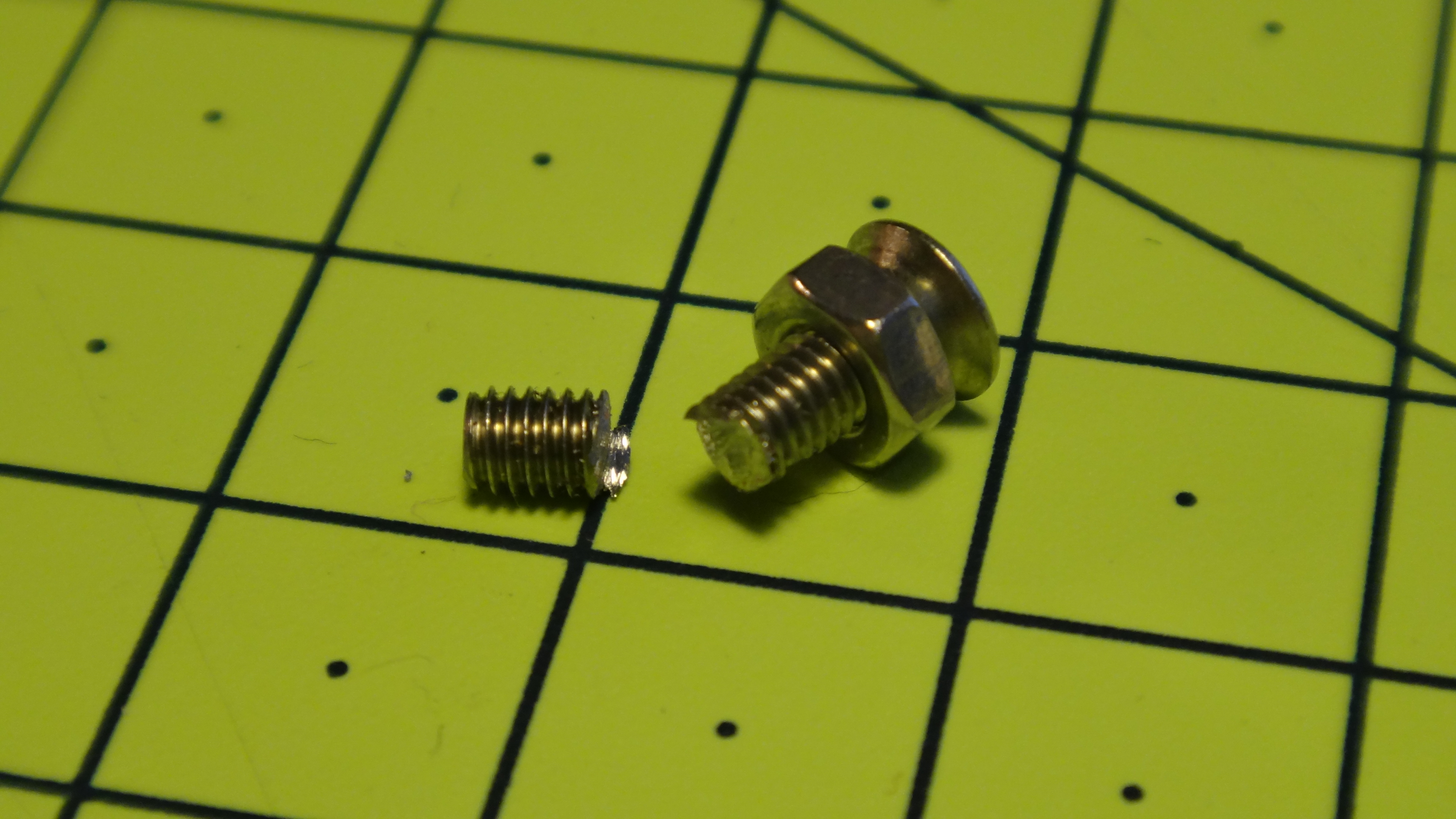
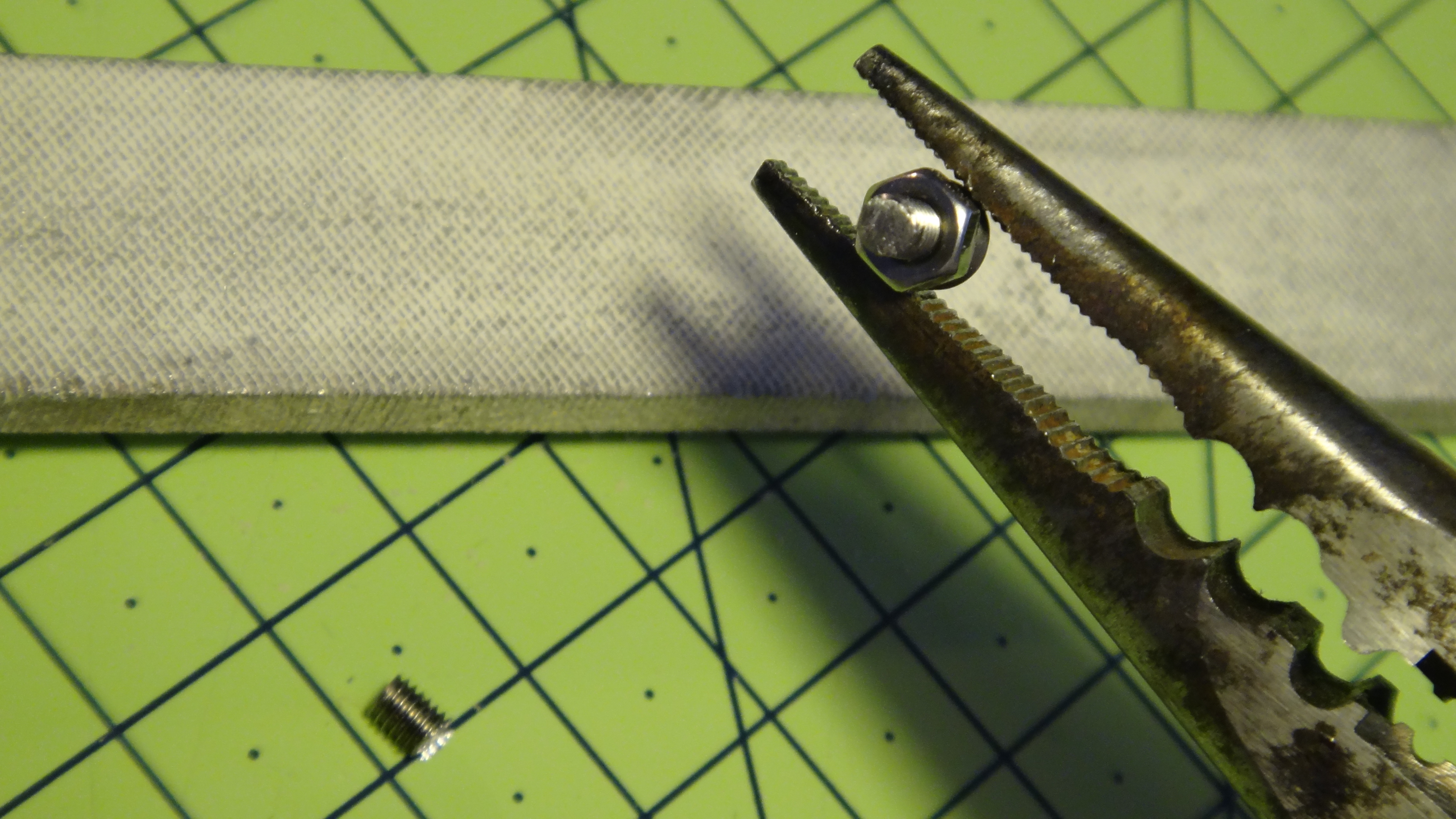
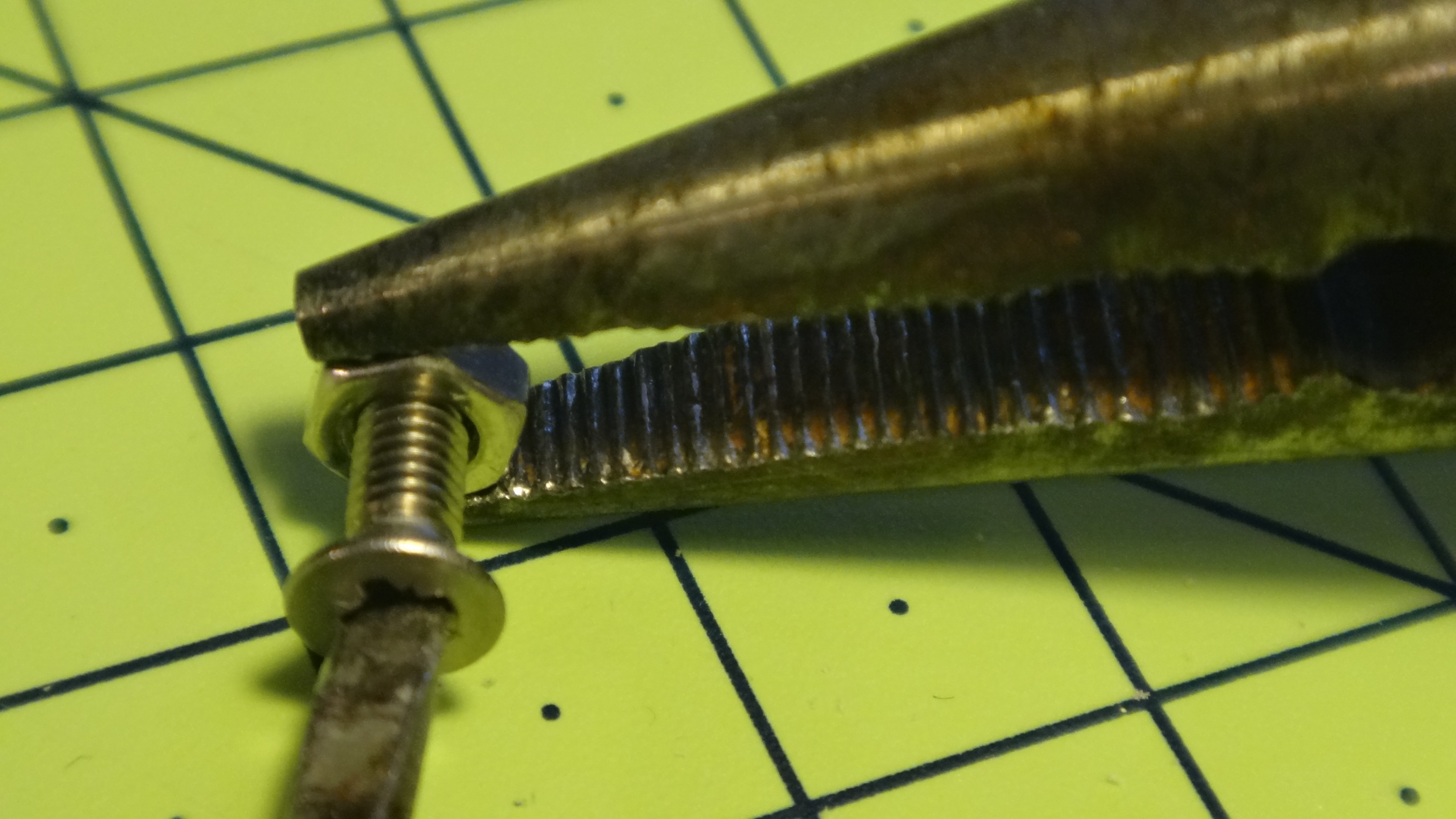
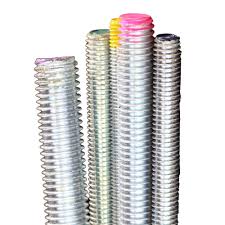
The first picture shows that the bolt sticks out too far. Now you could get one the right size, but that's not always possible. The next image shows the bolt trimmed to size.
Do not simply saw the bolt, follow these instructions to keep a smooth running thread:
1. Put the Nut on the bolt. Screw it all the way to the head.
2. Clamp the 'unwanted' end in a vice - hard!
3. [Measure the length you require]. Saw. Using a Hacksaw or Junior Hacksaw. Use your fingernail as a rest for the blade to begin and saw gently towards you until you have a cut about 1mm deep - then you can saw back and forth. If you try to saw forwards straight away, the blade will simply 'jump' and you'll mess up the thread.
4. Take the bolt with pliers and file the rough edge off. WHen flat, work in a circular motion to get a slightly rounded edge all the way round.
5. Unscrew the nut off the bolt.
Now if you has done up to step 4 without the nut being on, you would now have messed-up the thread on the bolt. The nut, as it unscrews, actually 're-cuts' the thread as it leaves - making it easy to screw back on. FOr good measure un/screw it back and forth at the bask bit to even it out.
EXTRA: This principle of 're-cutting' the thread is essential on other things like 'studding'.
Making the Dividers (Wood-working on the Cheap)
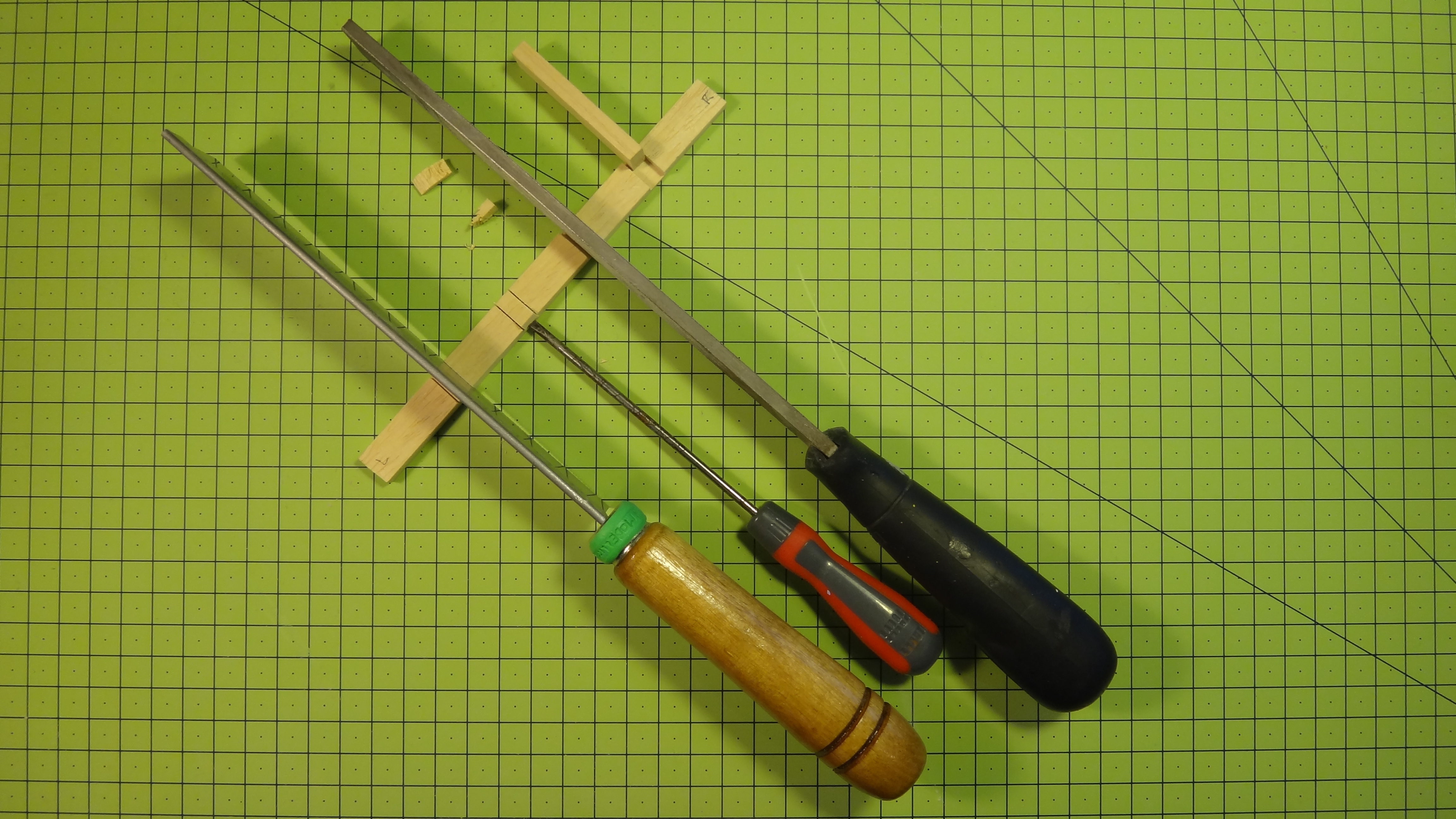
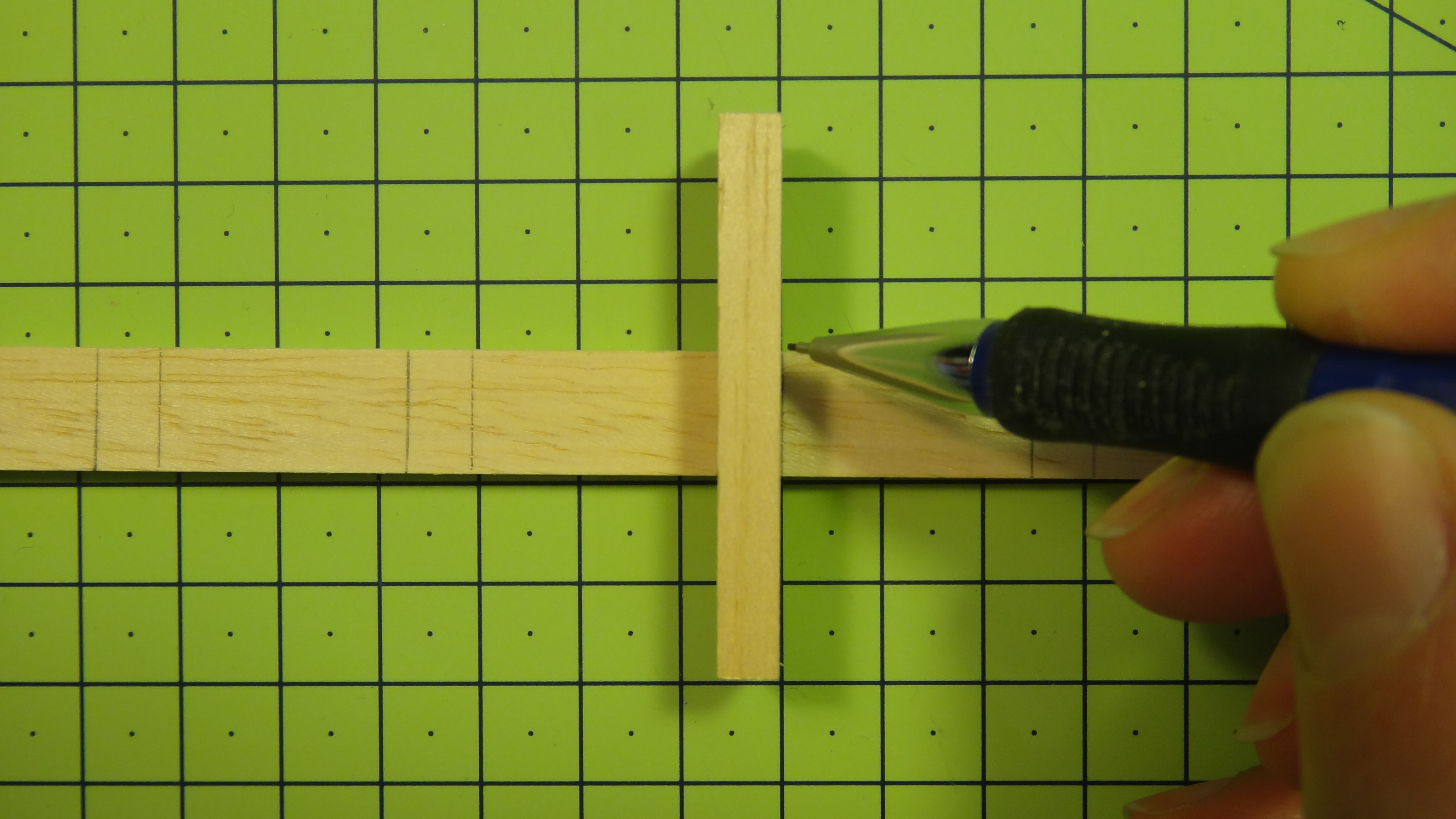
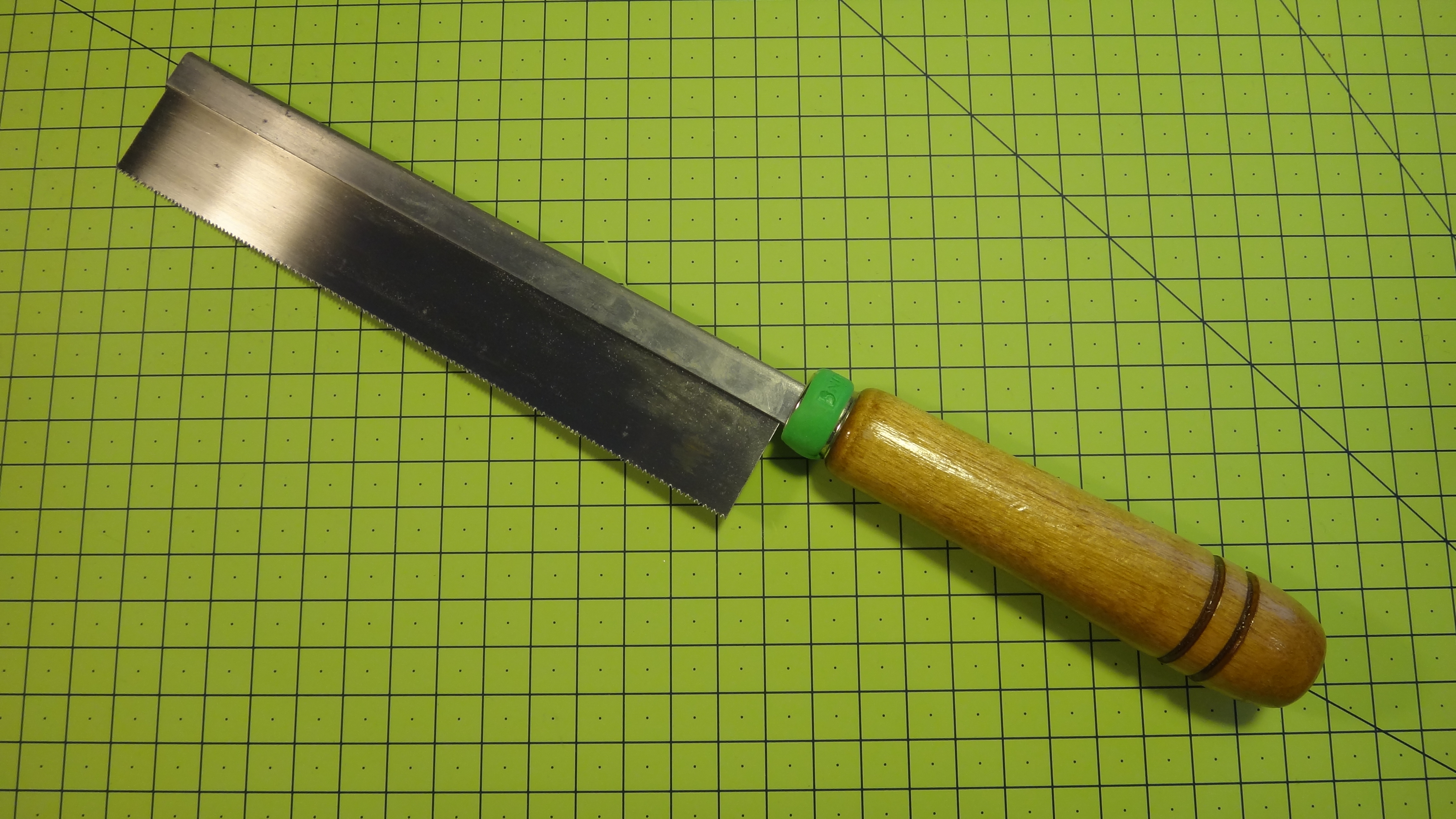
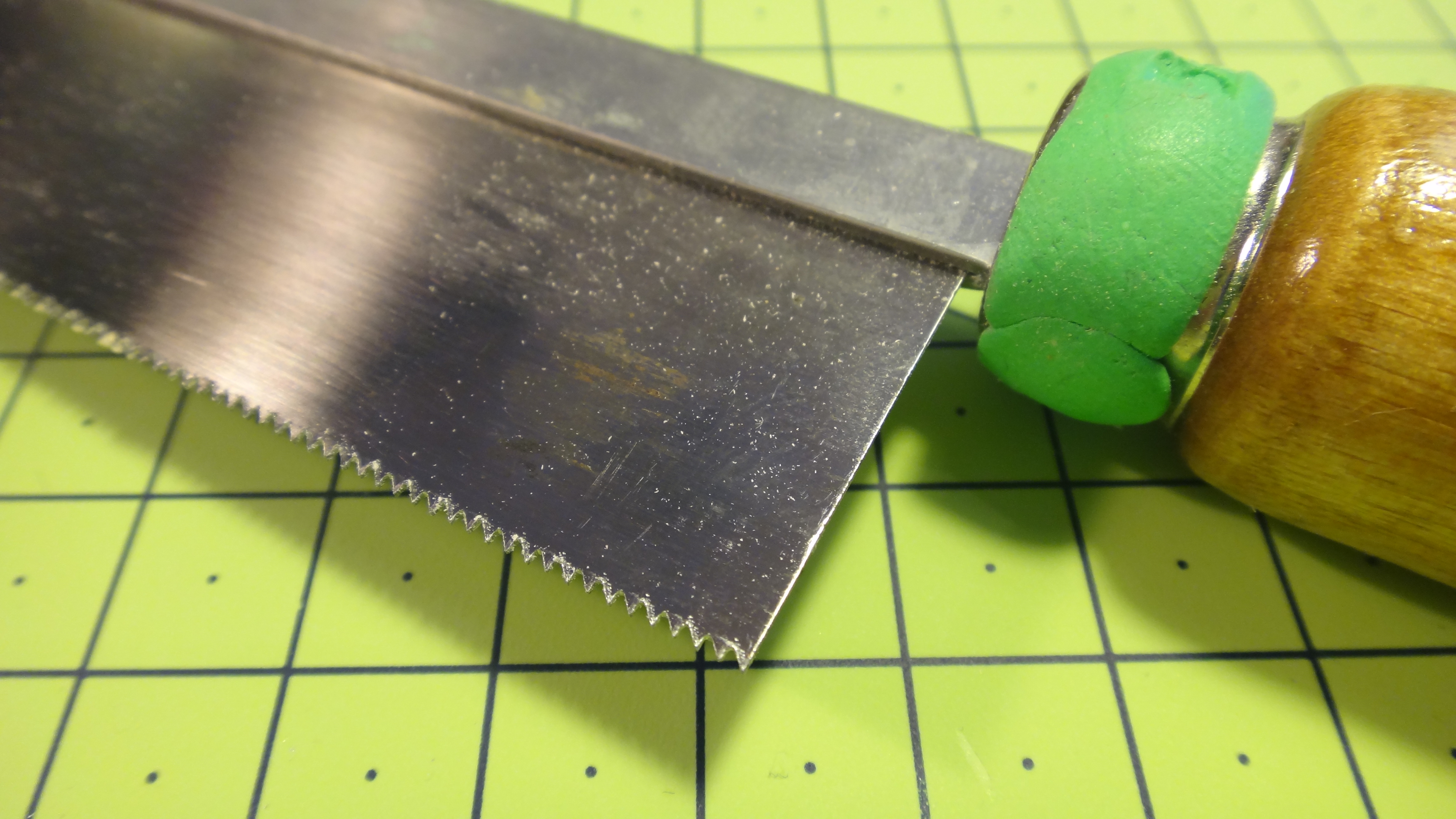
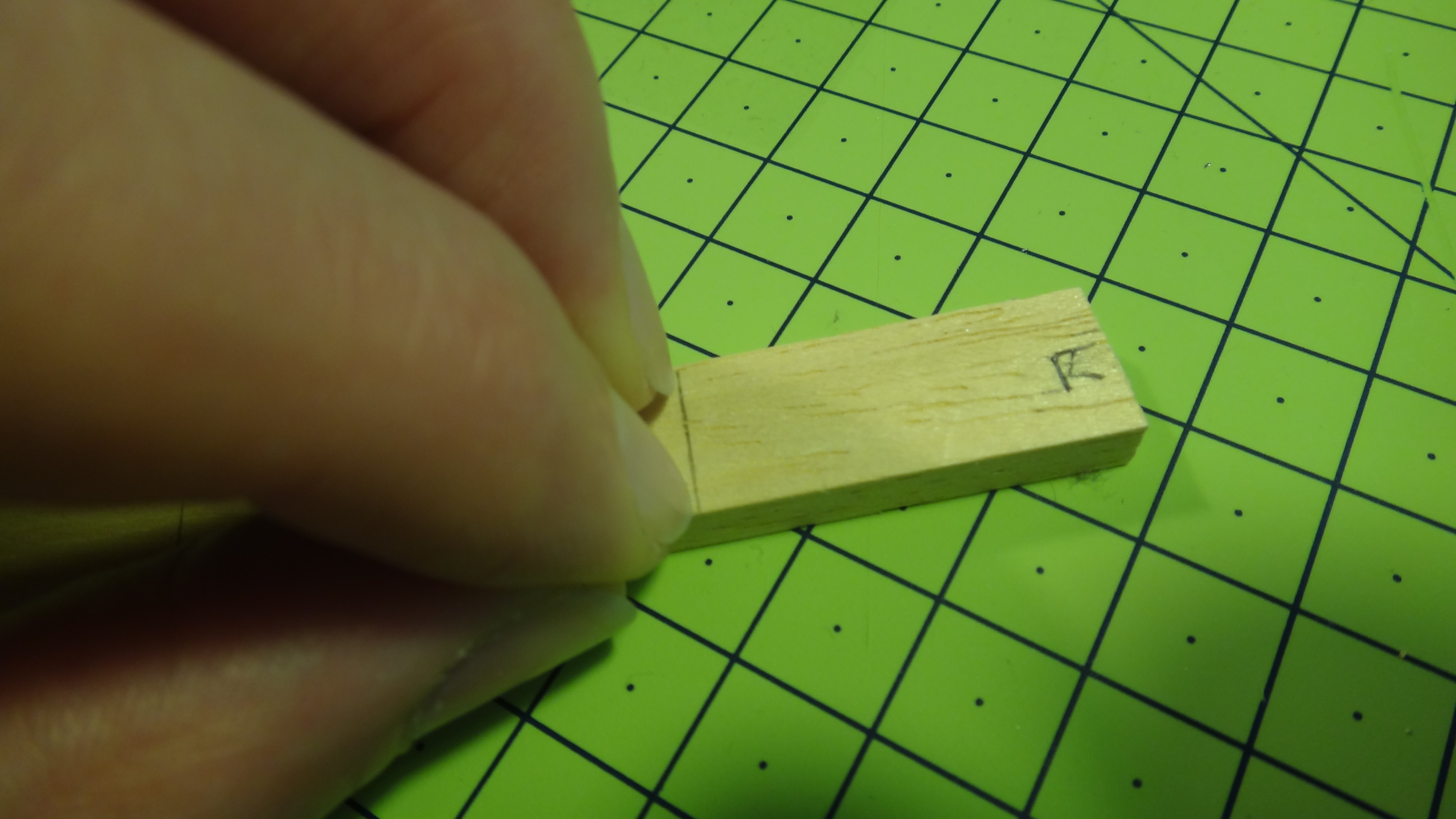
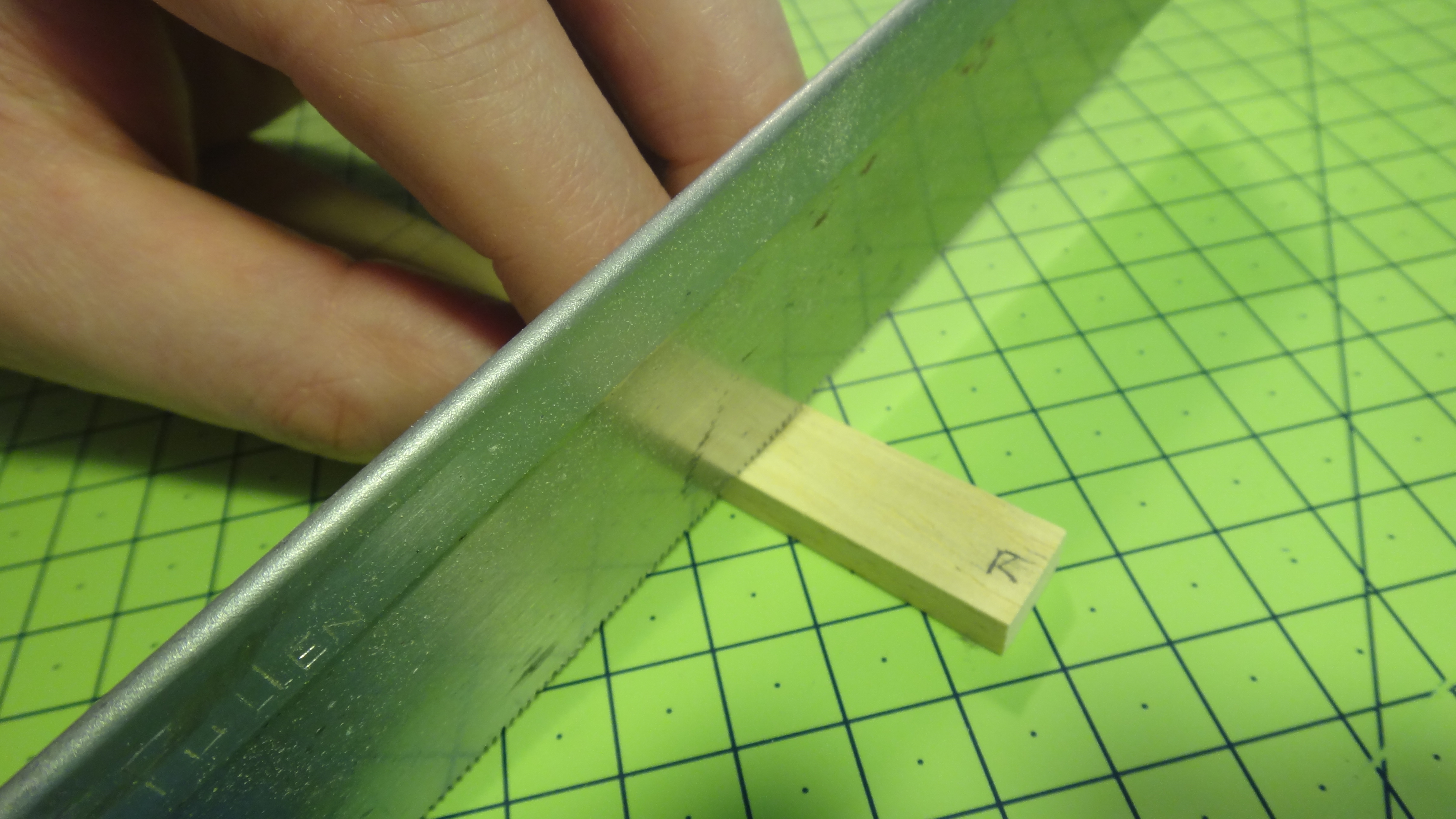
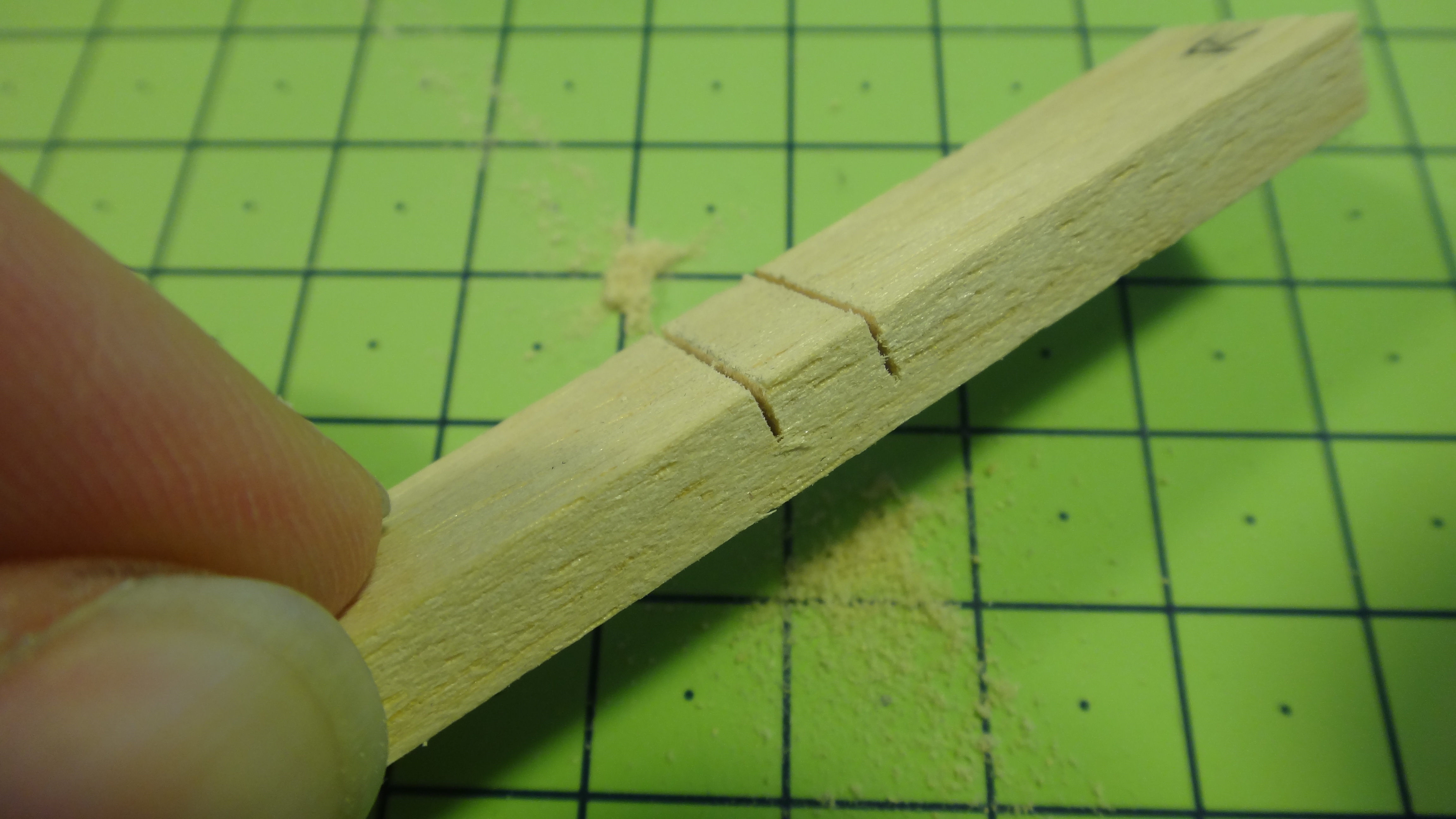
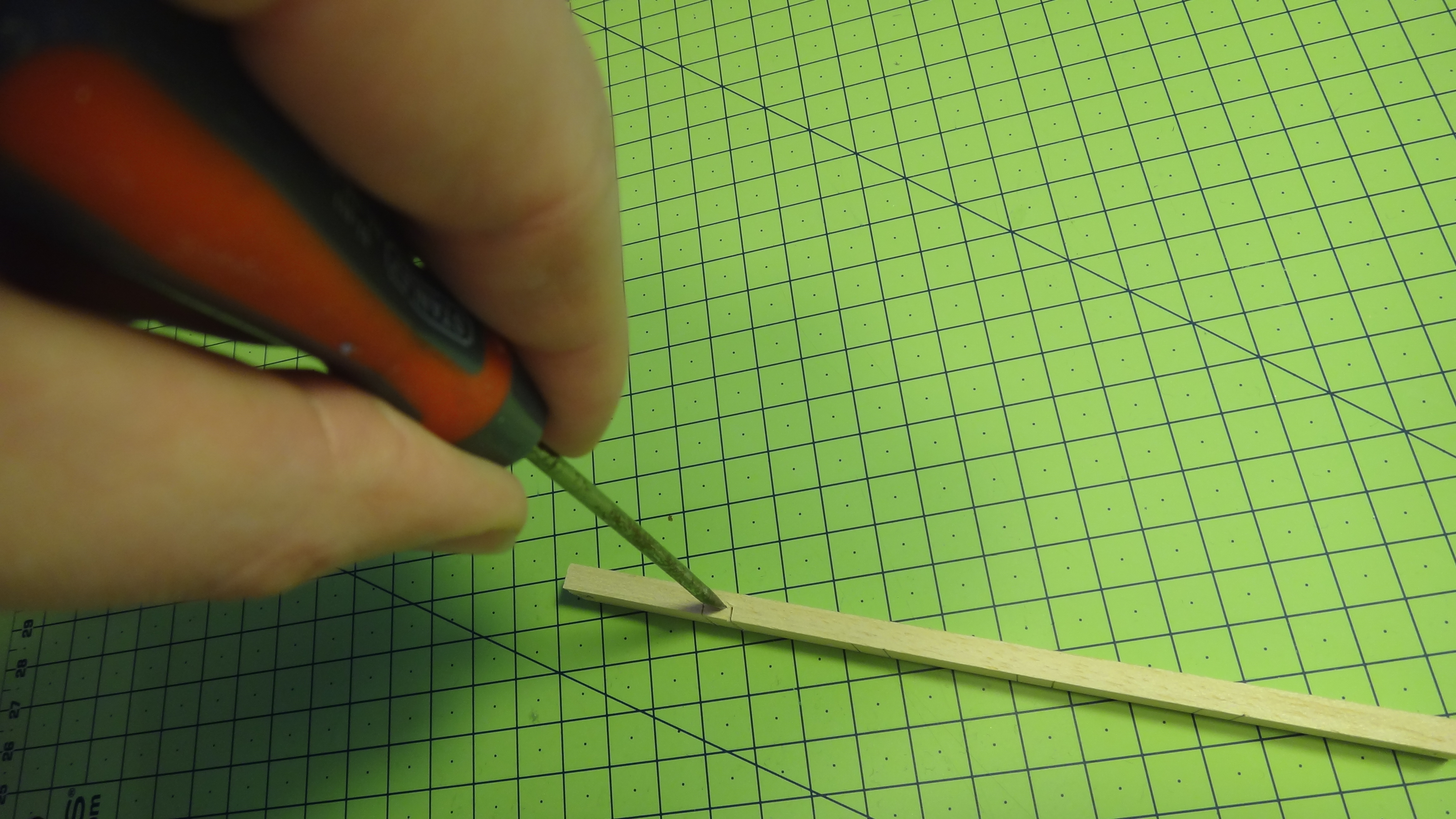
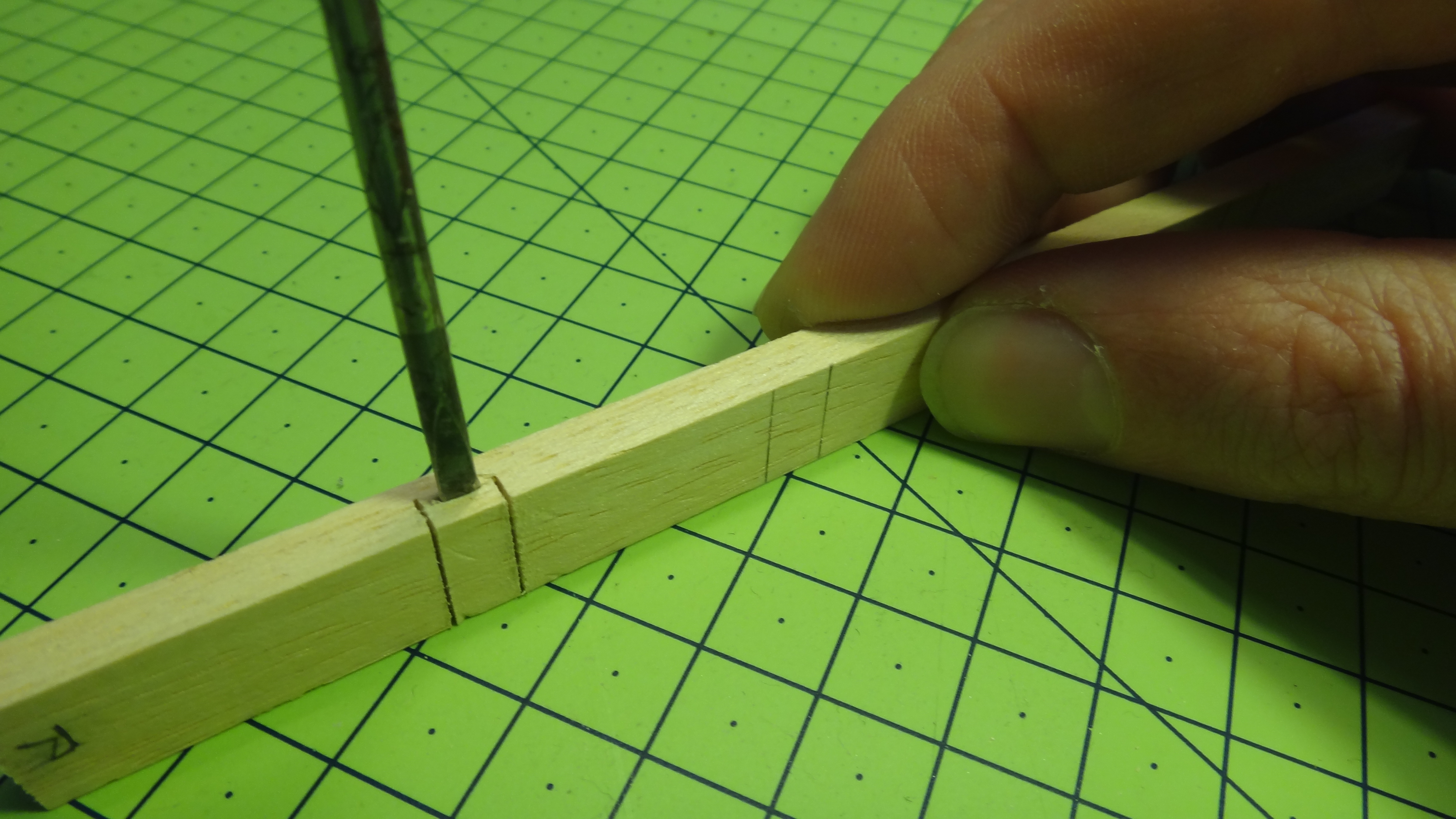
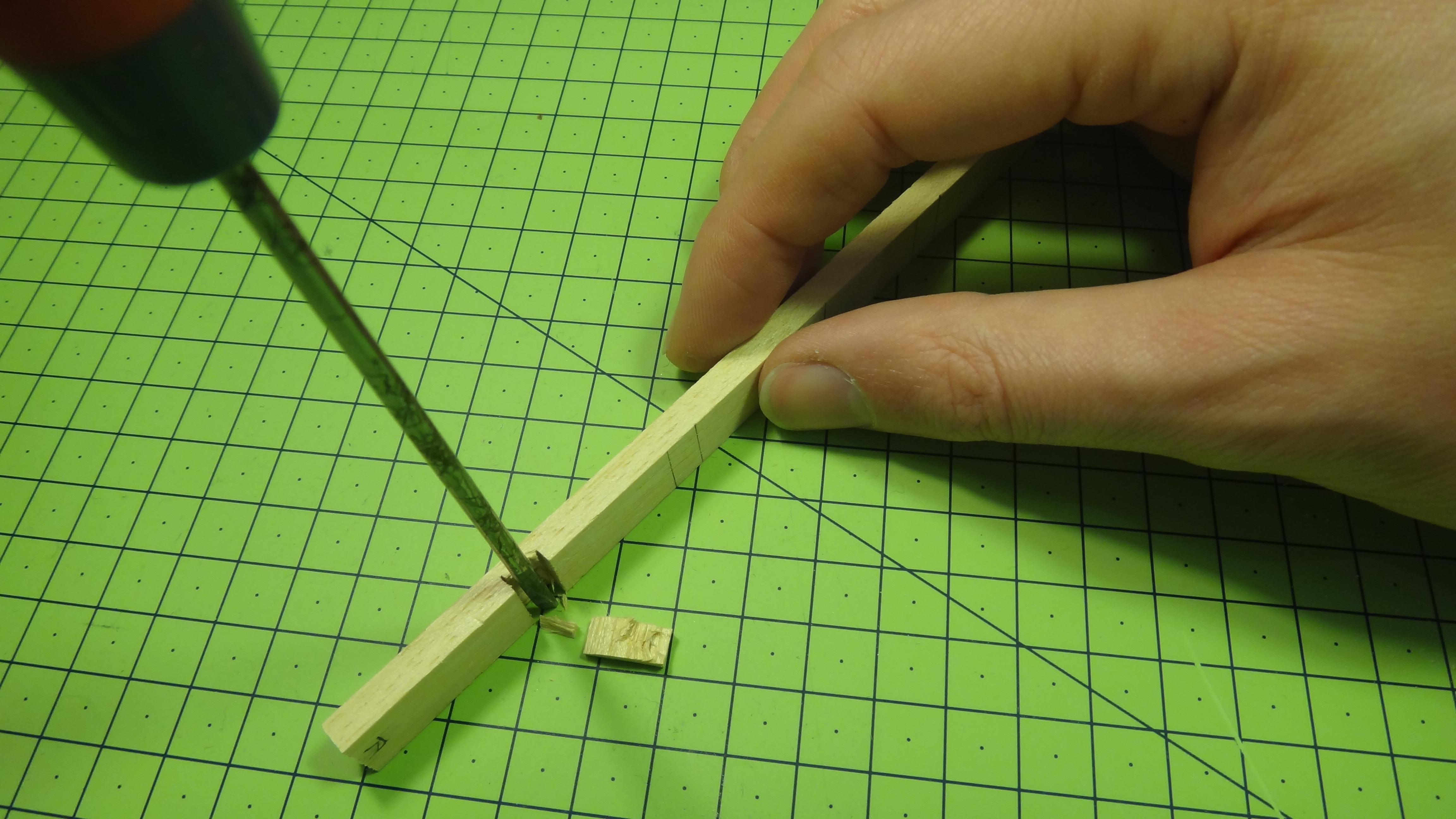
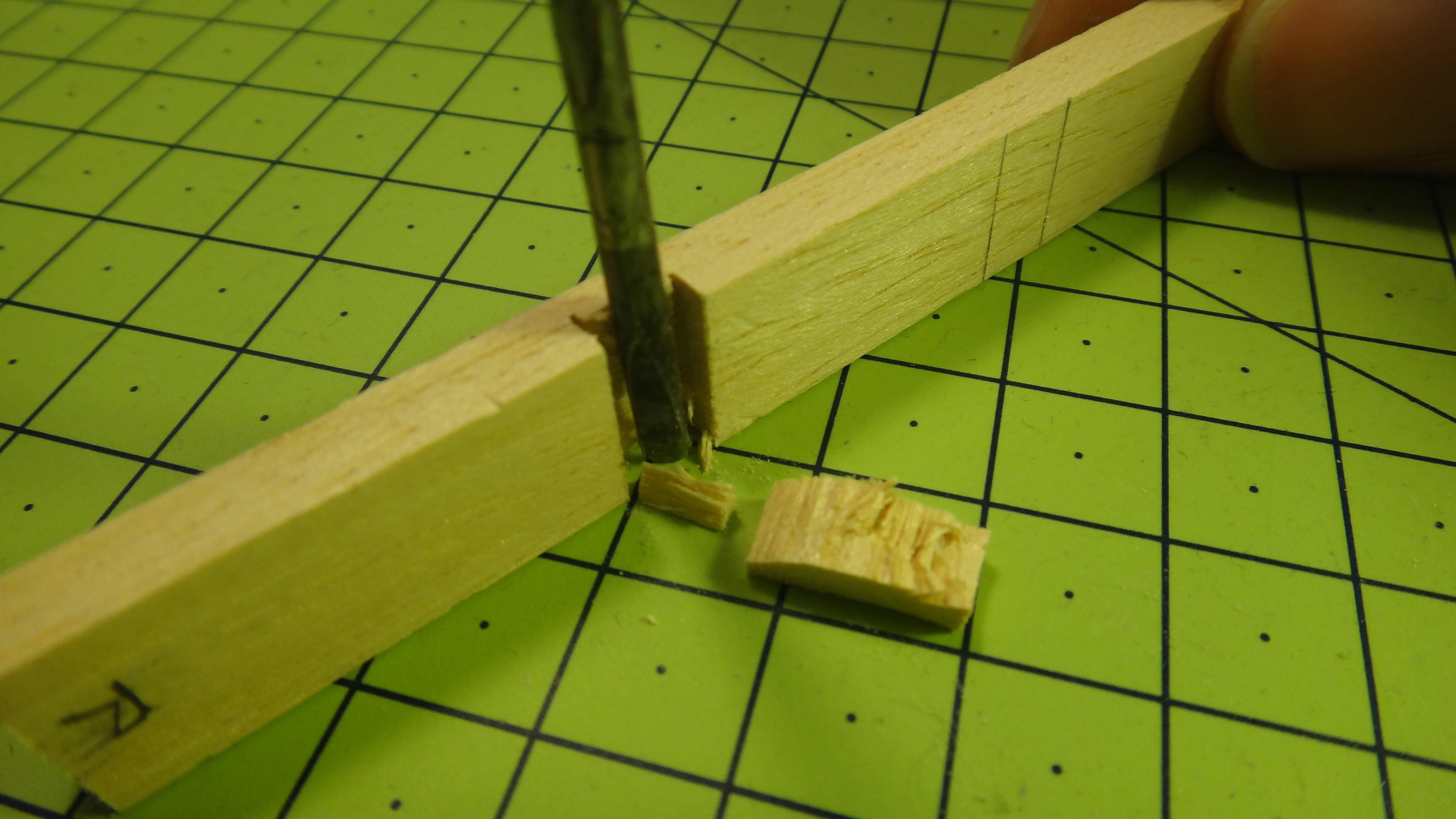
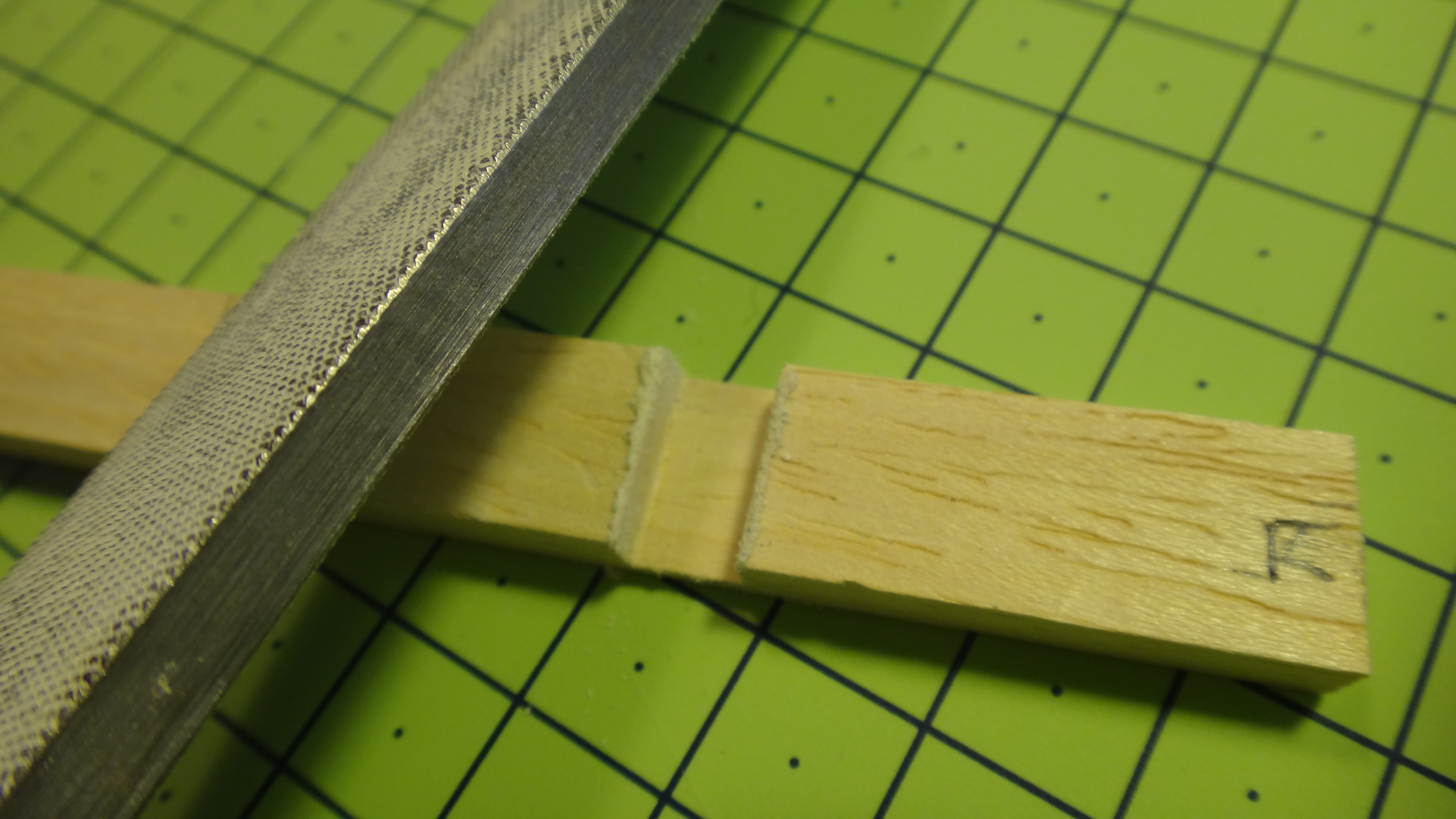
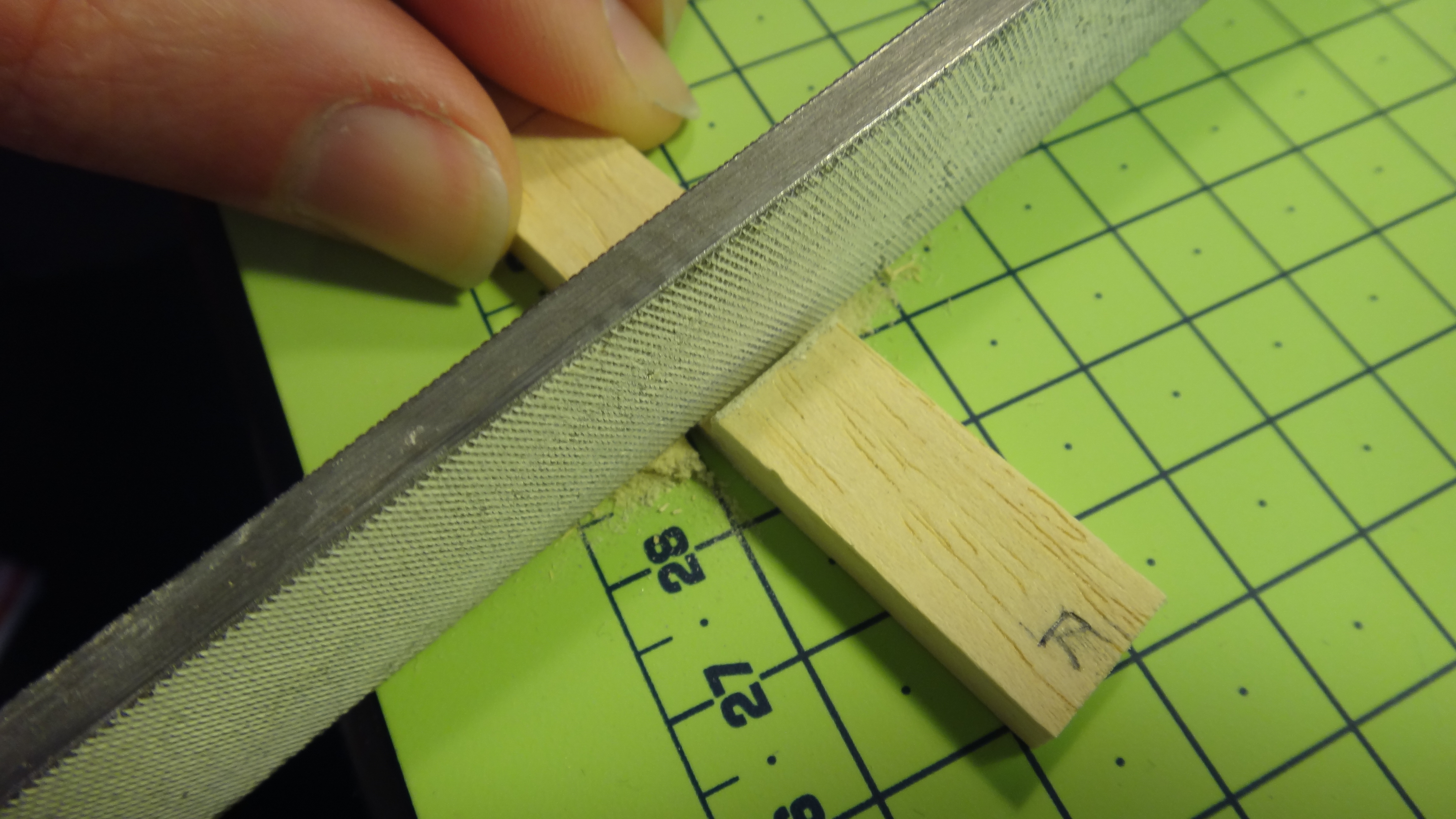
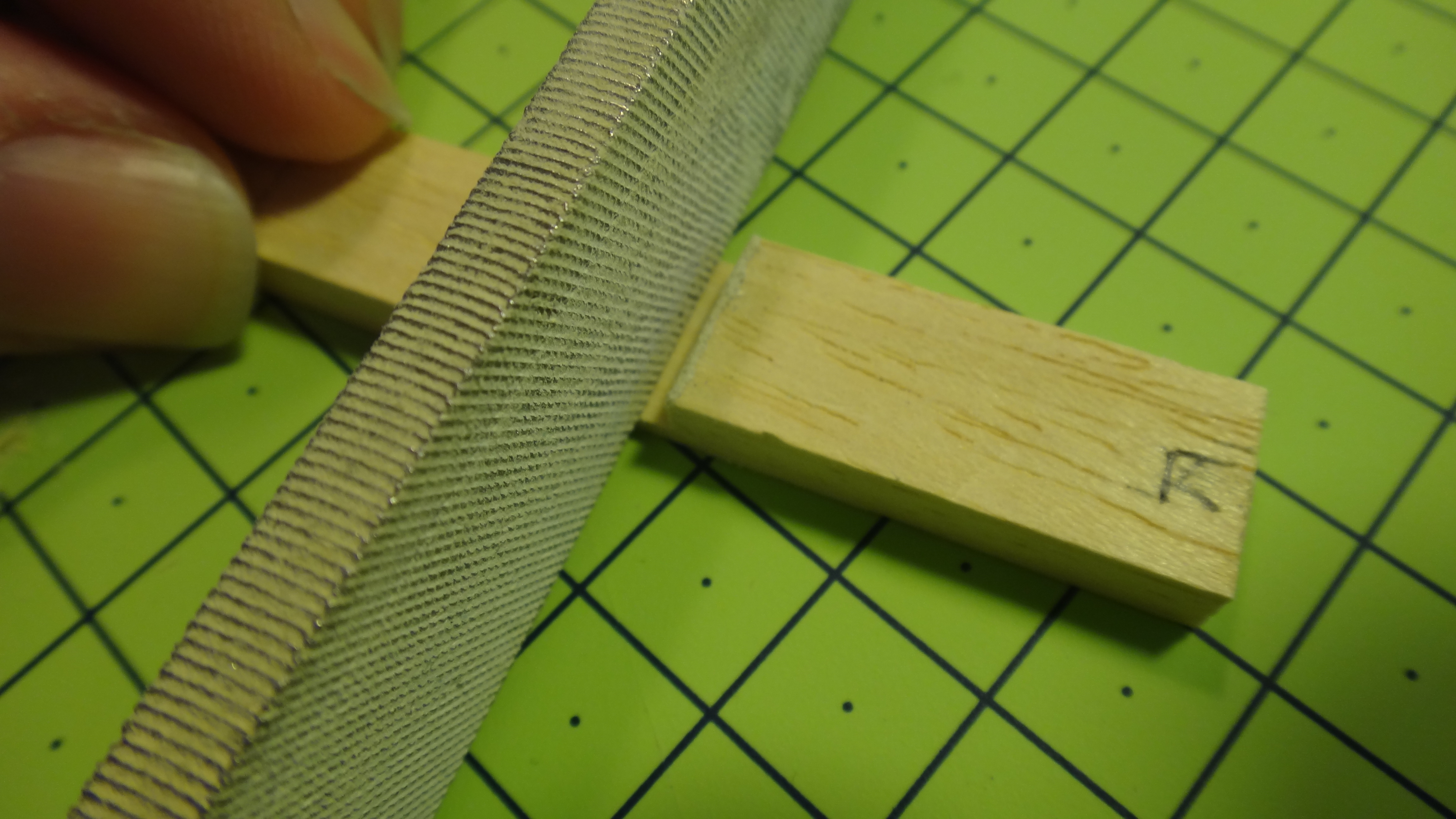
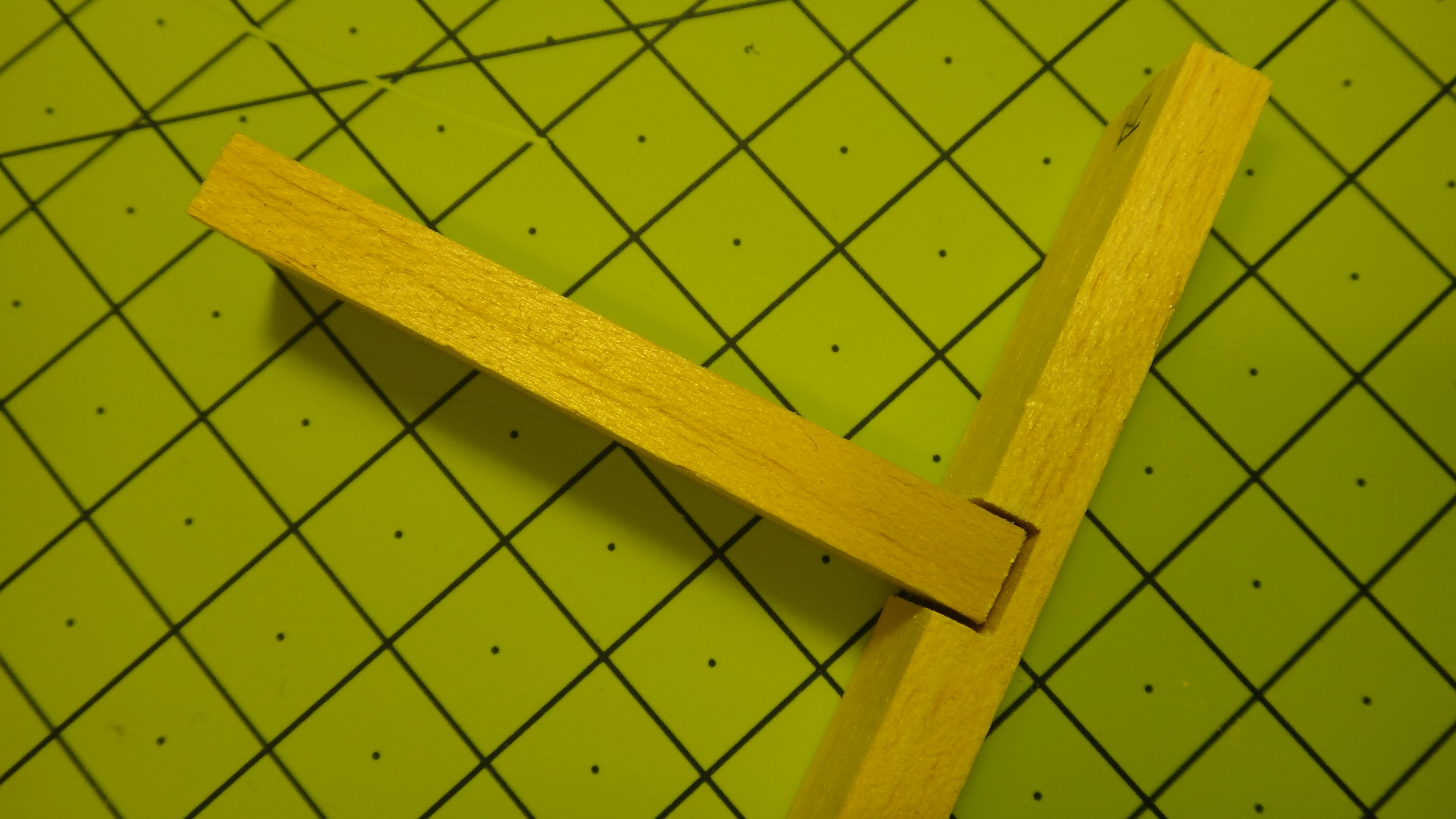
0. Overview of how the process.
1. Mark-out the slots. Sounds obvious, but you can waste a lot of time measuring things carefully, when what you are looking for is 'fit'. Also, when making a first prototype, the aesthetic/functional preference will guide you, rather than choosing an arbitrary measurement and feeling like you must stick to it.
2. Zona-Saw. Now it does not matter if you don't have one of these saws (though they are fantastic to use and only around $10), but they key thing is that the teeth face backwards; you cut on the 'pull-stroke' towards you. (You can reverse a Junior Hacksaw blade too).
3. Use your fingernail as a guide (as for the metal work) and start sawing gently until you have an established groove. Arguably you can clamp the wood for a more stable cut, though the Zona is so sharp I didn't need to. Roughly cut 1/4 to 1/3 of the way through one side. (Don't cut too much, as this will be double-sided!)
4. Now take a flat-headed screw-driver a little smaller than the thickness of your groove to be cut. Place it on the top, and tap the handle by hand. The would will splinter out quick easily. Put a scrap of wood underneath to protect your table. It is surprising how quick this process is, but do practice on a scrap first!
5. Take a file and even out the groove.
A NOTE ON FILES: Ever noticed how only 3 sides of a file are rough? This is because it can be handy to file one side and not leave a mark on the other. On this instance, I filed the depth first and then flipped over to do the sides of the groove - but this allowed me not to risk making it any deeper when pressing on the sides.
6. Now is the laborious part of making numerous cuts for as many 'sections' and you need for you tools.
Try laying your tools out beforehand to get a rough idea of where divisions are needed.
Installation
![Under Desk Tool Drawer [Modeller's Delight]](/proxy/?url=https://content.instructables.com/F13/DJJV/HVM5EFIZ/F13DJJVHVM5EFIZ.jpg&filename=Under Desk Tool Drawer [Modeller's Delight])
Screw the brackets to the underside of you table. It is usually a good idea to drill holes for the screws (smaller than the screws) to make installation easier. Also, you should put the screws in one either side at a time, so as the runners are not bent/bias to one side.
Please let me know how you get on. Do upload any pictures of your own variations. And check out more stuff like this at Design Modelling.
Thanks,
Jude
PS - please share the I'ble / Video if you like it.