Tahoe Glow
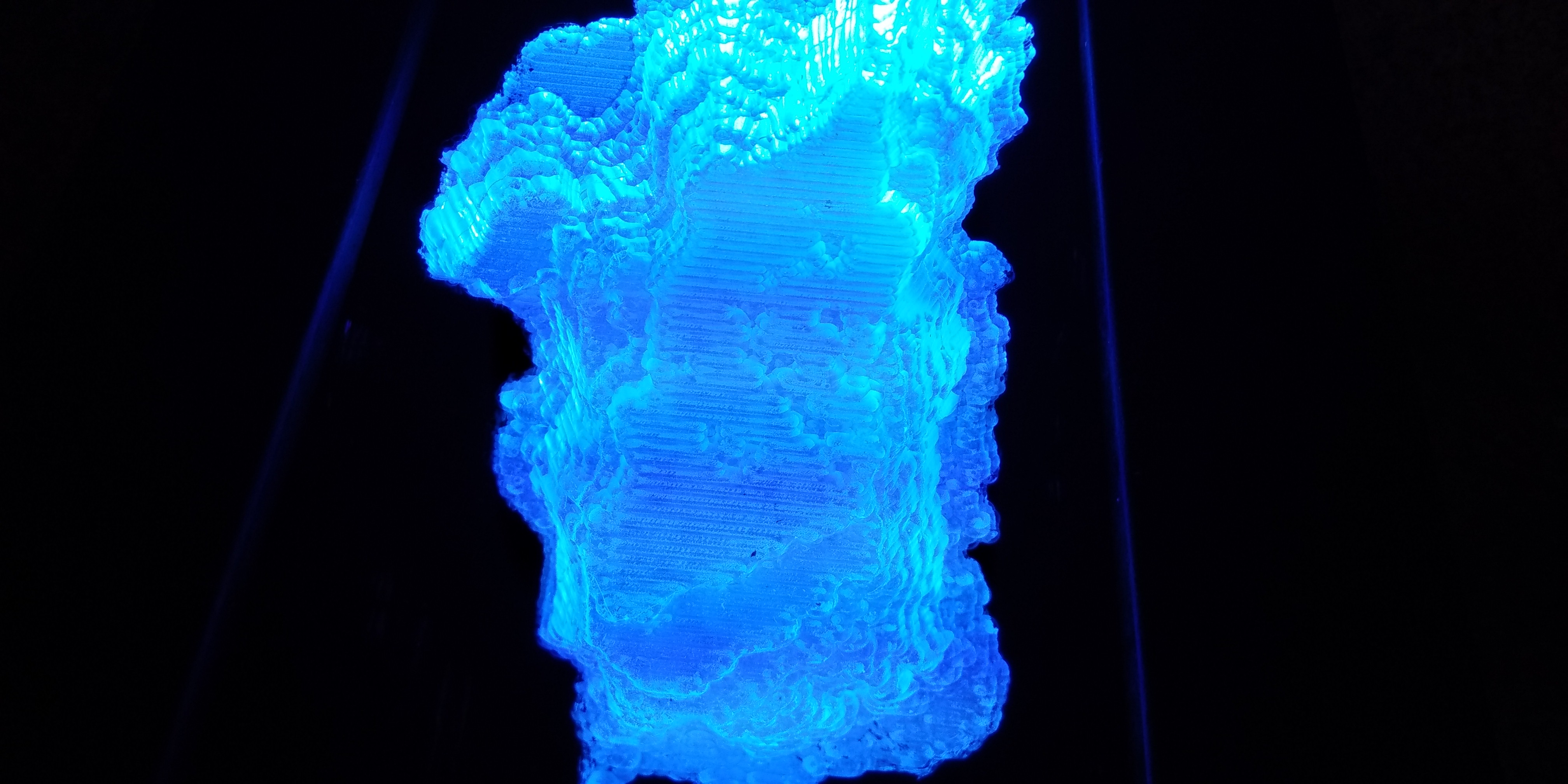
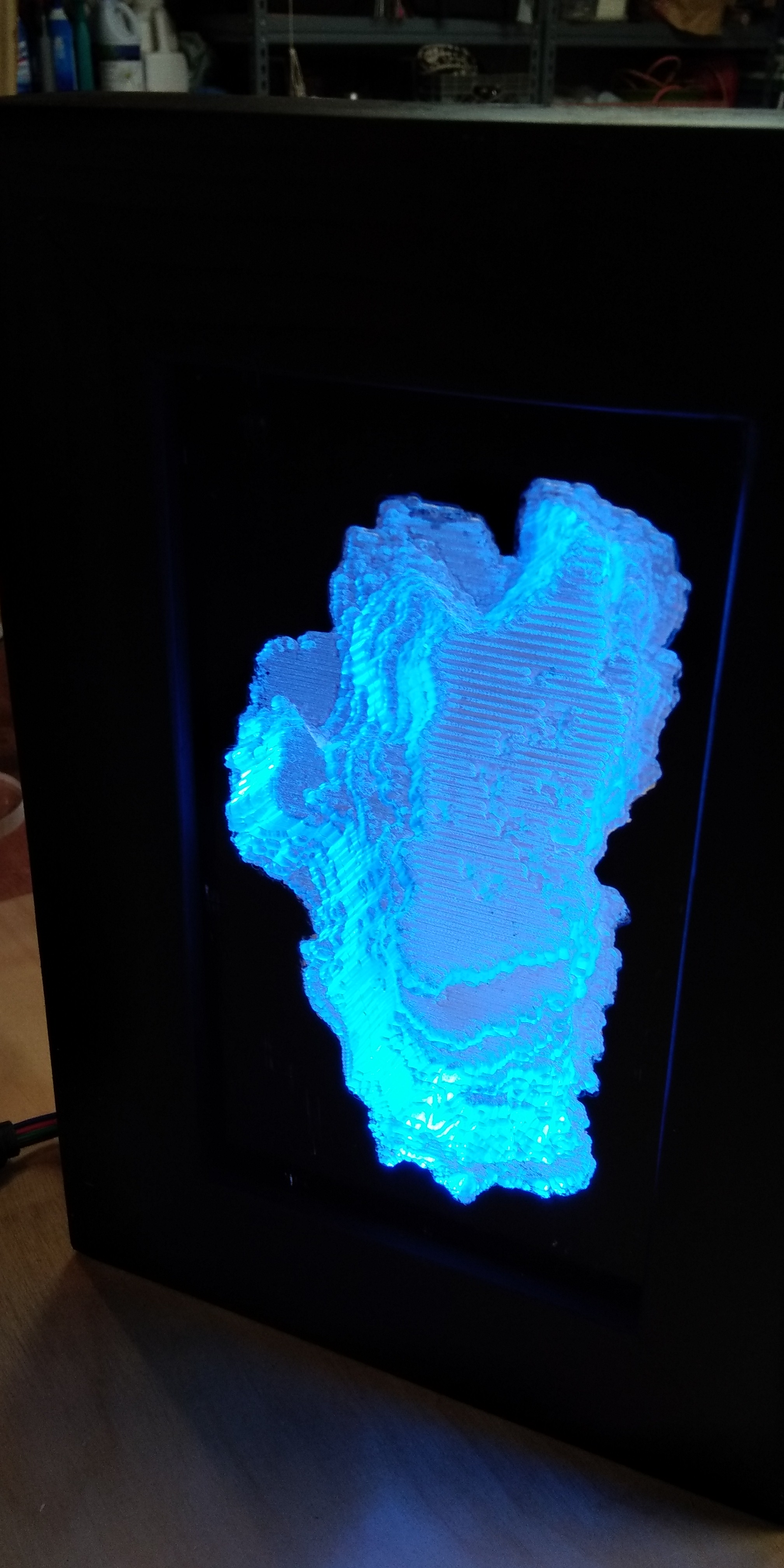
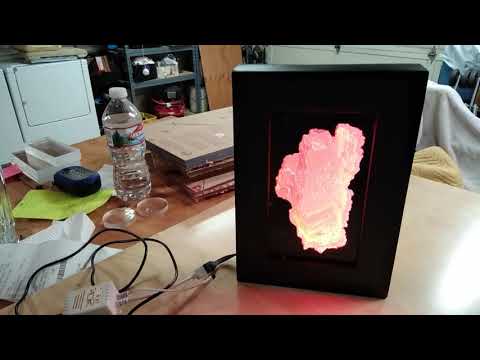
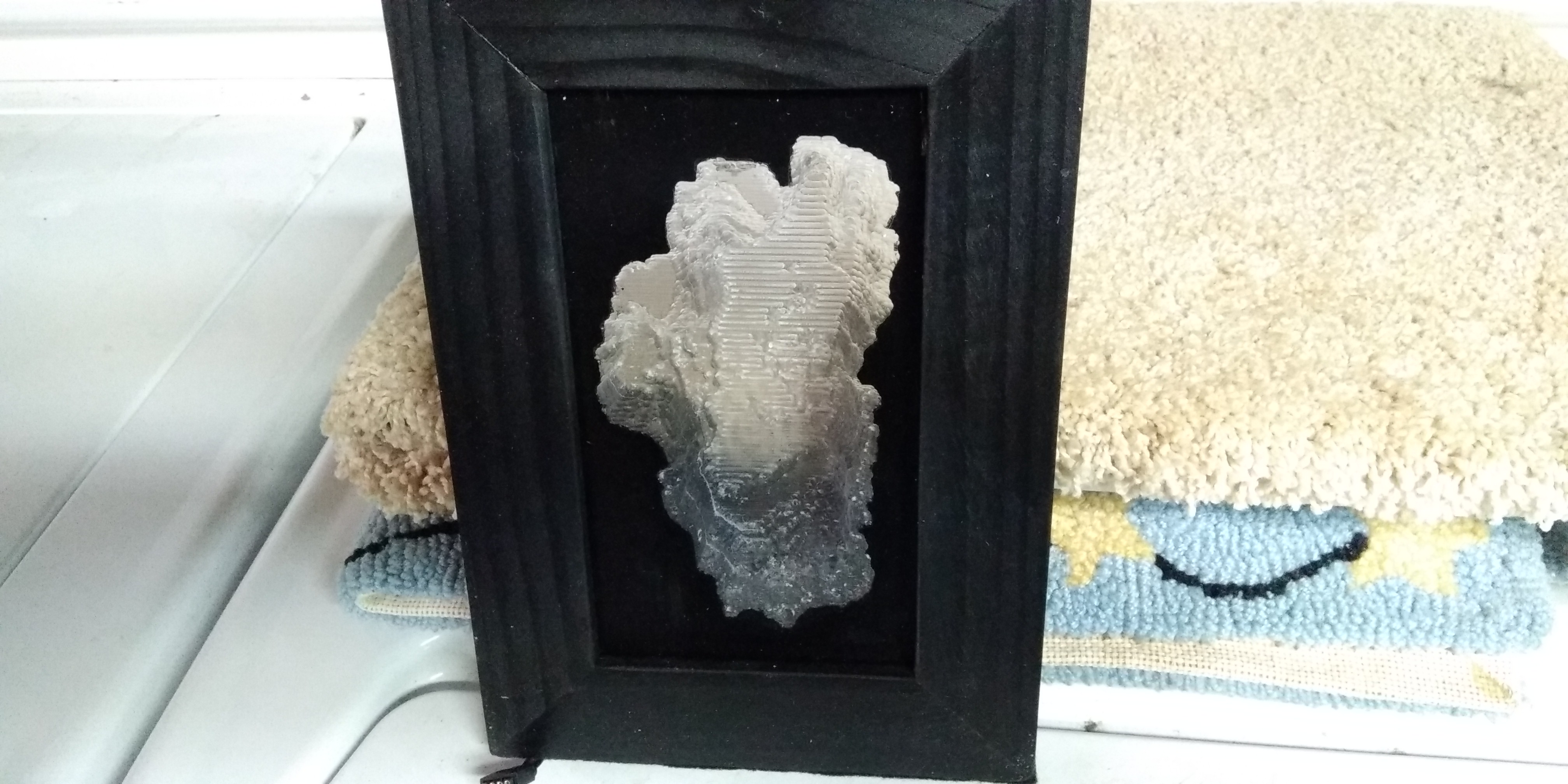
I built myself a CNC machine and wanted to try it out. The first project was a simple cut out from acrylic and it came out great. Flushed with success, I now wanted to try a 3d carving project, again in acrylic. I looked online for ready-to-carve grayscale images but didn’t see anything I liked. Our family goes to Lake Tahoe periodically so I got the notion of a carved version of the lake depicting the various depths (bathymetric). The third try came out well so I added LEDs on the sides and a frame to hide LEDs. This Instructable assumes access to a CNC machine and other woodshop tools including a table saw (for the wooden frame). You’d also have to buy a controllable LED strip.
Software
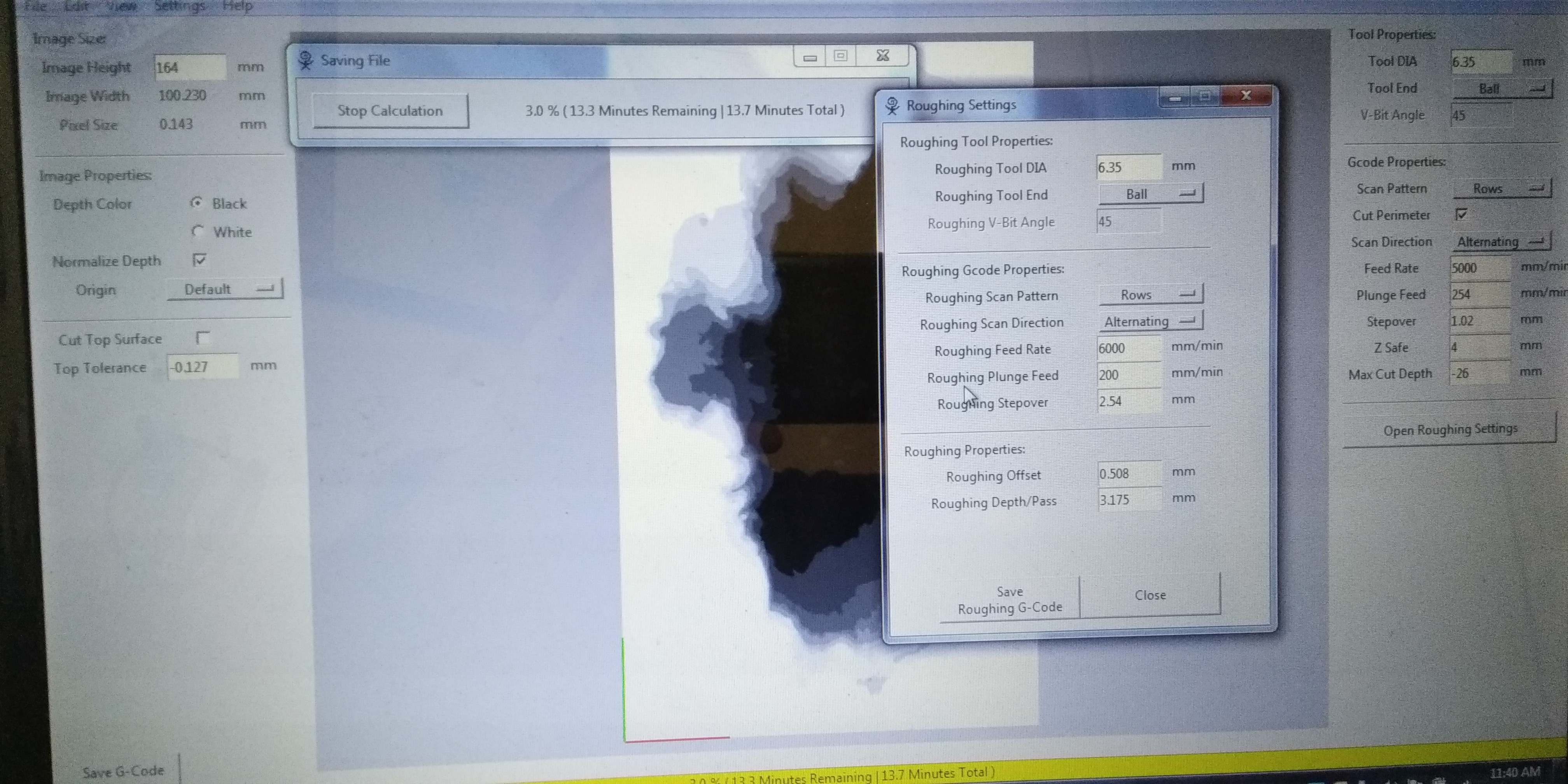
To run the CNC machine one needs Gcode. Usually it’s a CAM program (Computer Assisted Manufacturing) that takes in a 3d model (produced by a CAD program) and generates the Gcode. I could have gone that way, but I found a simpler approach.
I found a software package online called Scorchworks Dmap2gcode. It’s free, relatively simple to use, and does a good job producing Gcode. It reads in a grayscale image that you provide and generates G-code for the CNC machine. Now, where was I to get a grayscale bathymetric map of Tahoe?
Grayscale Image
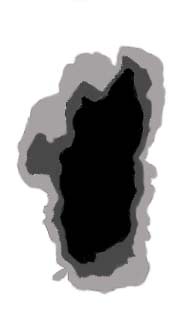



Google Images is a great place to start but I didn’t find anything that was grayscale and ready to go. I did find a very simple one that had about three depth levels – not satisfactory. I settled on one that had depth lines at 50 meter intervals covering the actual depth of 500 meters. But it was far from grayscale. So I used Photoshop, first to clear out all the words and symbols I didn’t want in the carving, and then to assign levels of gray to different levels in the lake.
I used black to represent the deepest level cut, and white to represent the top of the material just above the lake surface. There were ten levels before you reach the surface, so each one got an increasingly lighter shade of gray using the Photoshop Paint bucket tool. The result is grayscale, but with dark lines between the levels. I had to remove these manually, using the Paintbrush tool – very tedious work. Finishing that, there were still odd specs and blobs, so I used the Blur tool to smooth it all over. Maybe Blur would have worked to get rid of the black lines too, but I didn’t think of it till I was done. So now I had an image.
Carving
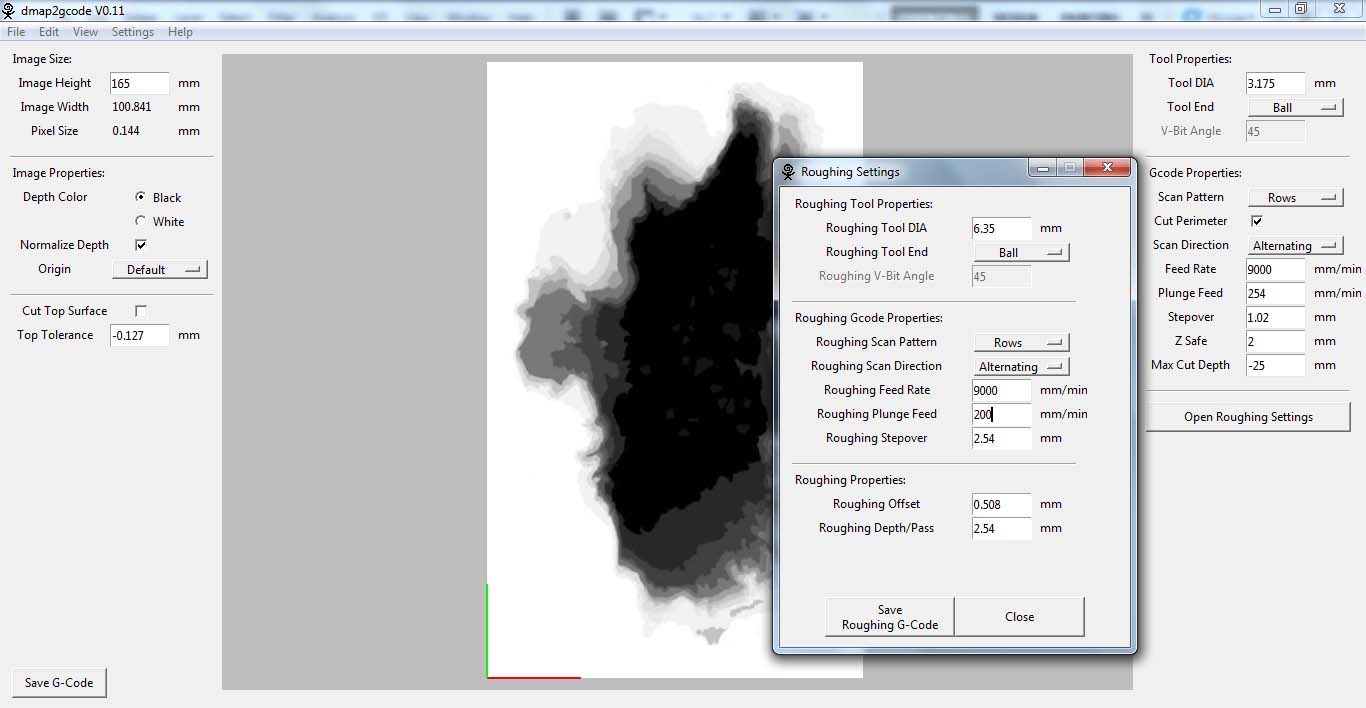
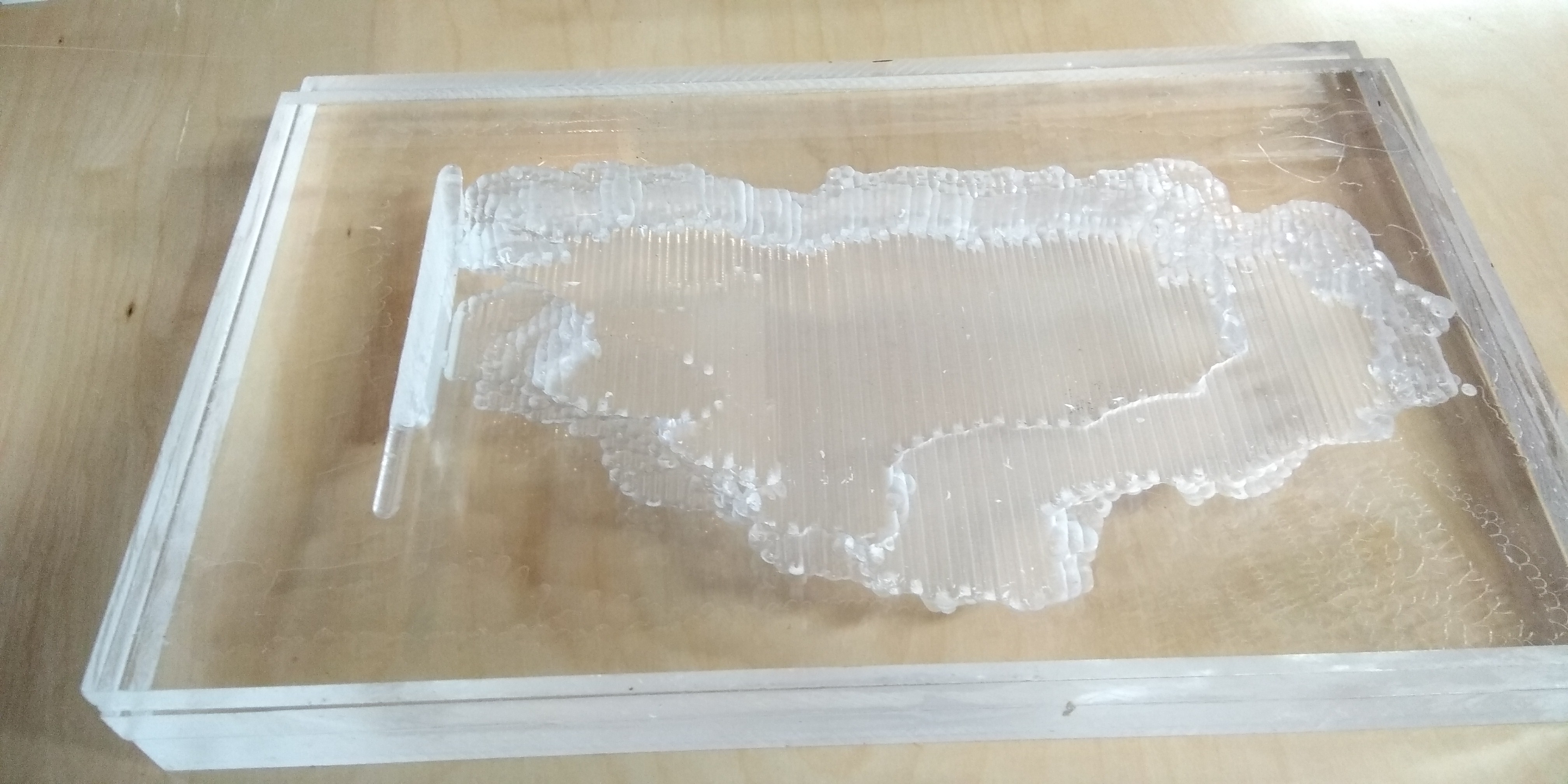
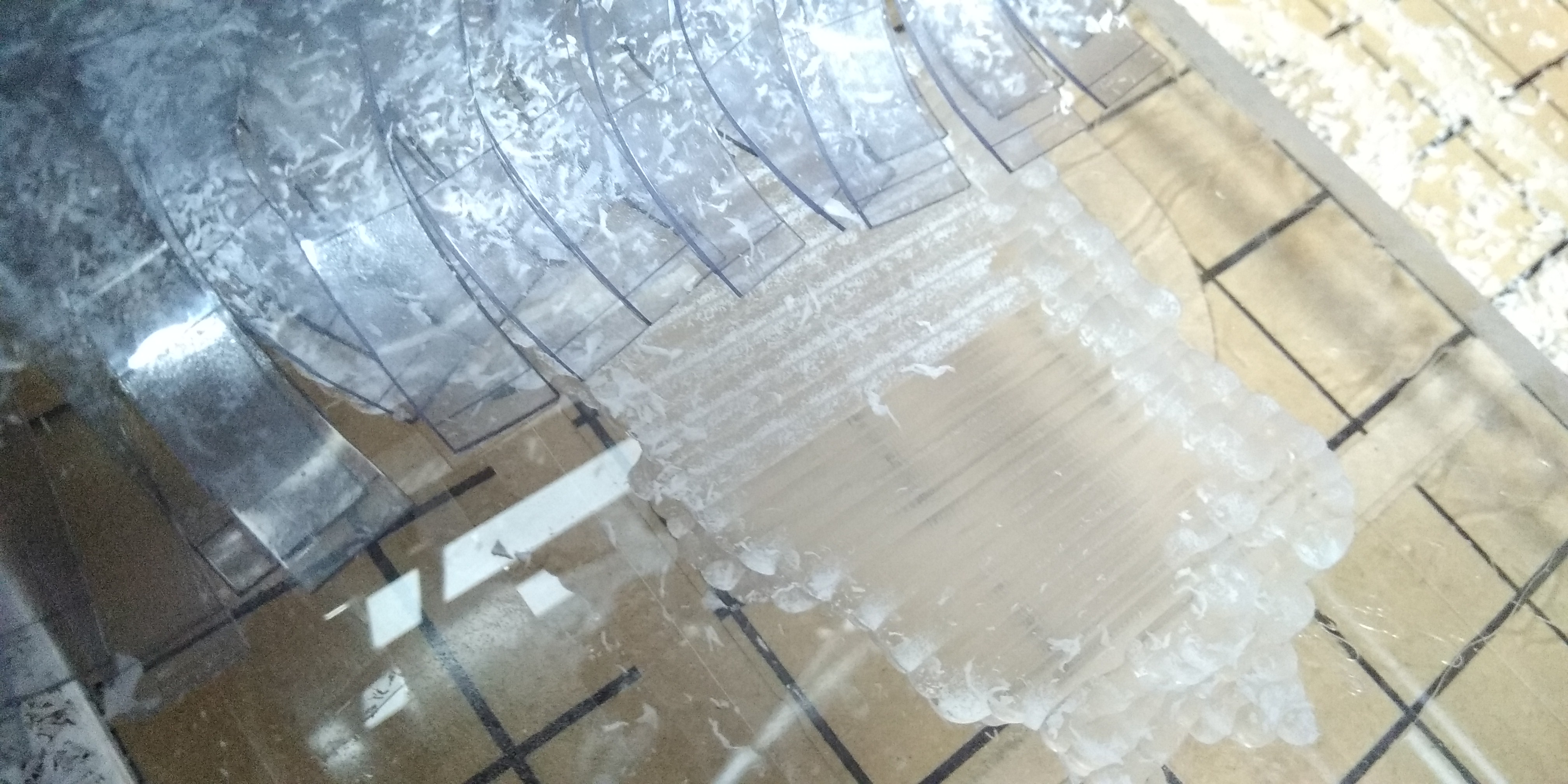
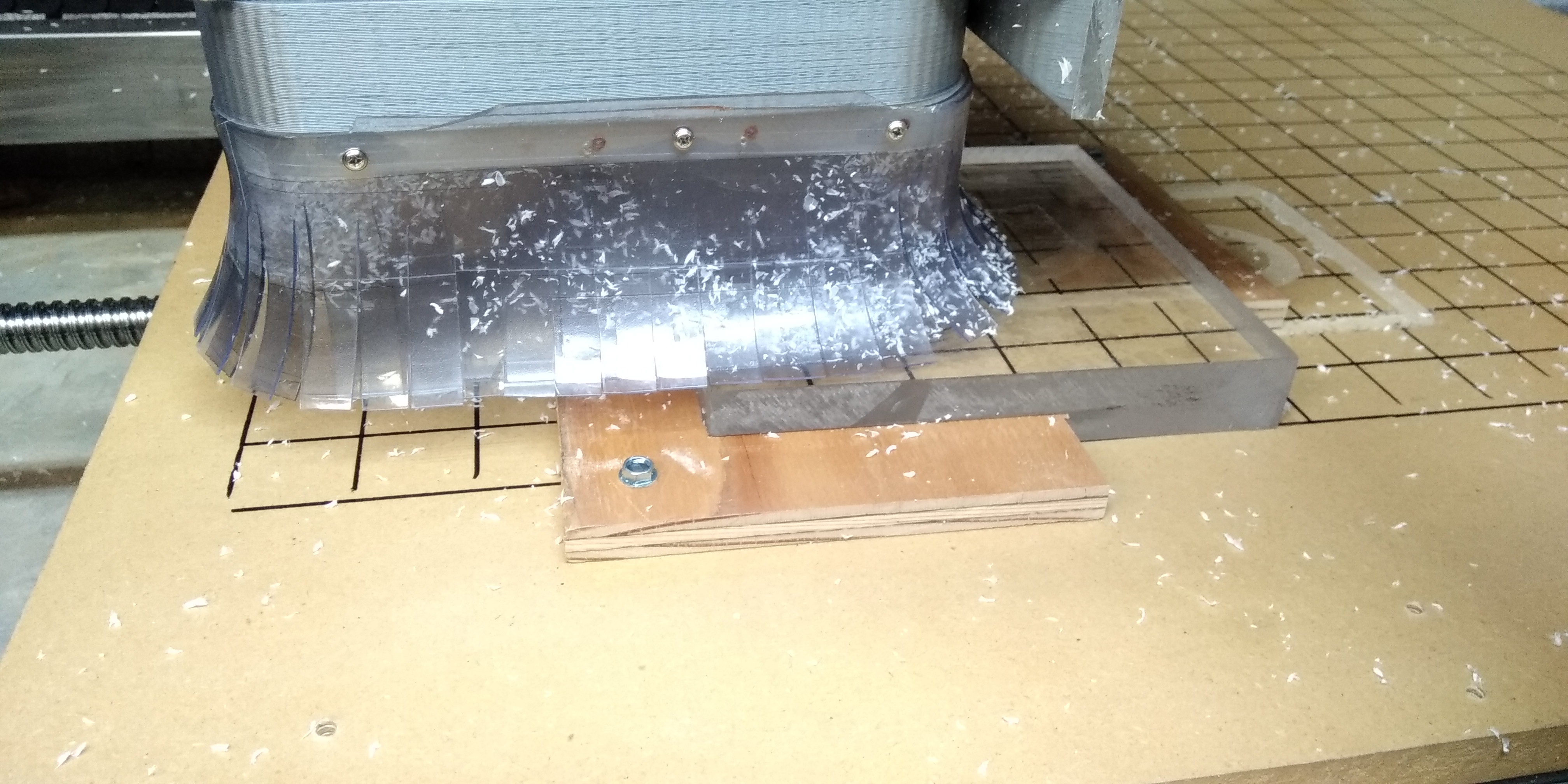
My source for acrylic is the scrap table at TAP plastics and they usually have cheap pieces of clear cast acrylic up to about 3/8 or ½ inch thick. For carving a lake we need to go deep. But a thick piece of acrylic is pretty expensive, so I cemented three layers together. I haven’t figured out a way to do this and have the cement run evenly between the layers, wetting the entire surface so it looks continuous. Instead it’s blotchy and you can easily see when the cement has run, and where it hasn’t. It turns out with my lighting scheme it didn’t matter anyway.
I’m still figuring out the CNC machine so I started with smaller scale carving. It came out well but I learned things about where to put the zero point for X and Y. Then I went for a larger scale and was going gangbusters until the X axis motor coupling broke and the machine spent a lot of time carving an ugly trench in my fancy acrylic.
After fixing the machine, I went for a medium sized product and it came out fine. The depth scale is exaggerated, but it does give the idea of great depth.
The carving is done in two passes and the software generates two separate Gcode files. The first is the roughing pass, where a larger bit is used and most of the material is removed. I used a ¼ inch ball end, two flute bit. Then the finish pass with a smaller bit to clean up after the roughing and bring it to the specified dimensions. For that I used a 1/8 inch ball end, two flute bit. In both runs, the spindle rpm was about 30,000 and the feed rate was 375 inches per minute. Depth of cut was at one tool diameter.
Lighting
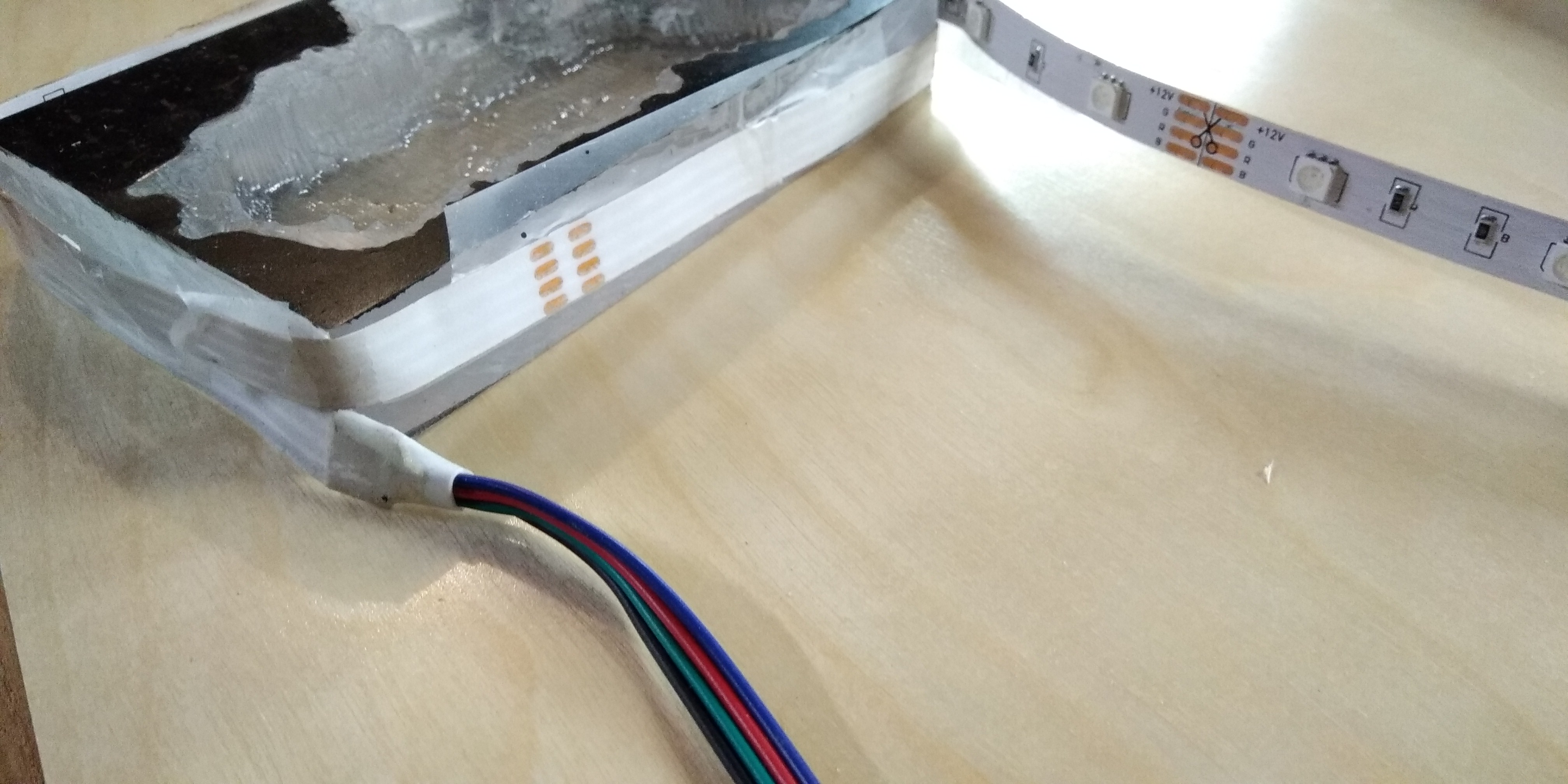
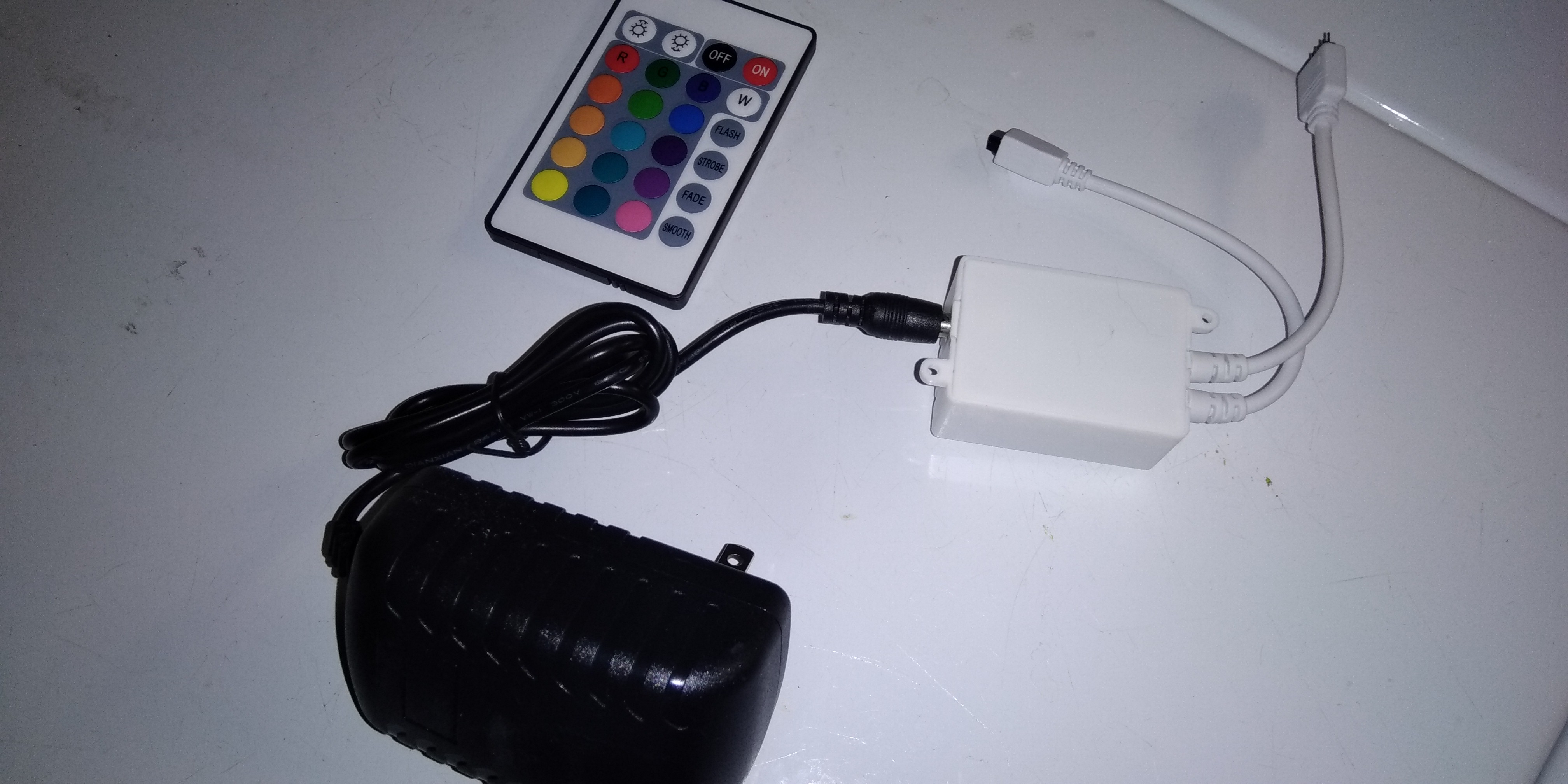
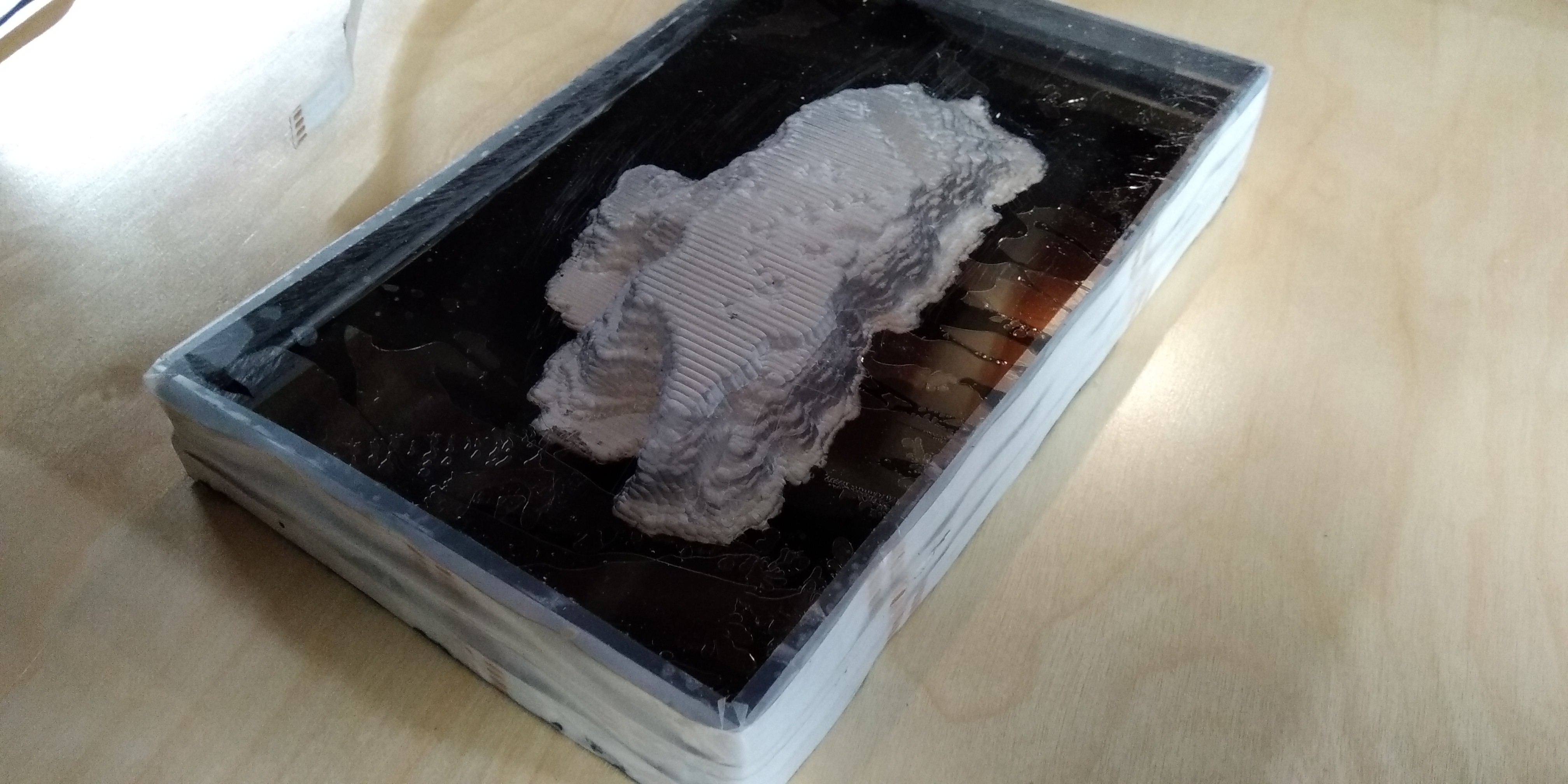
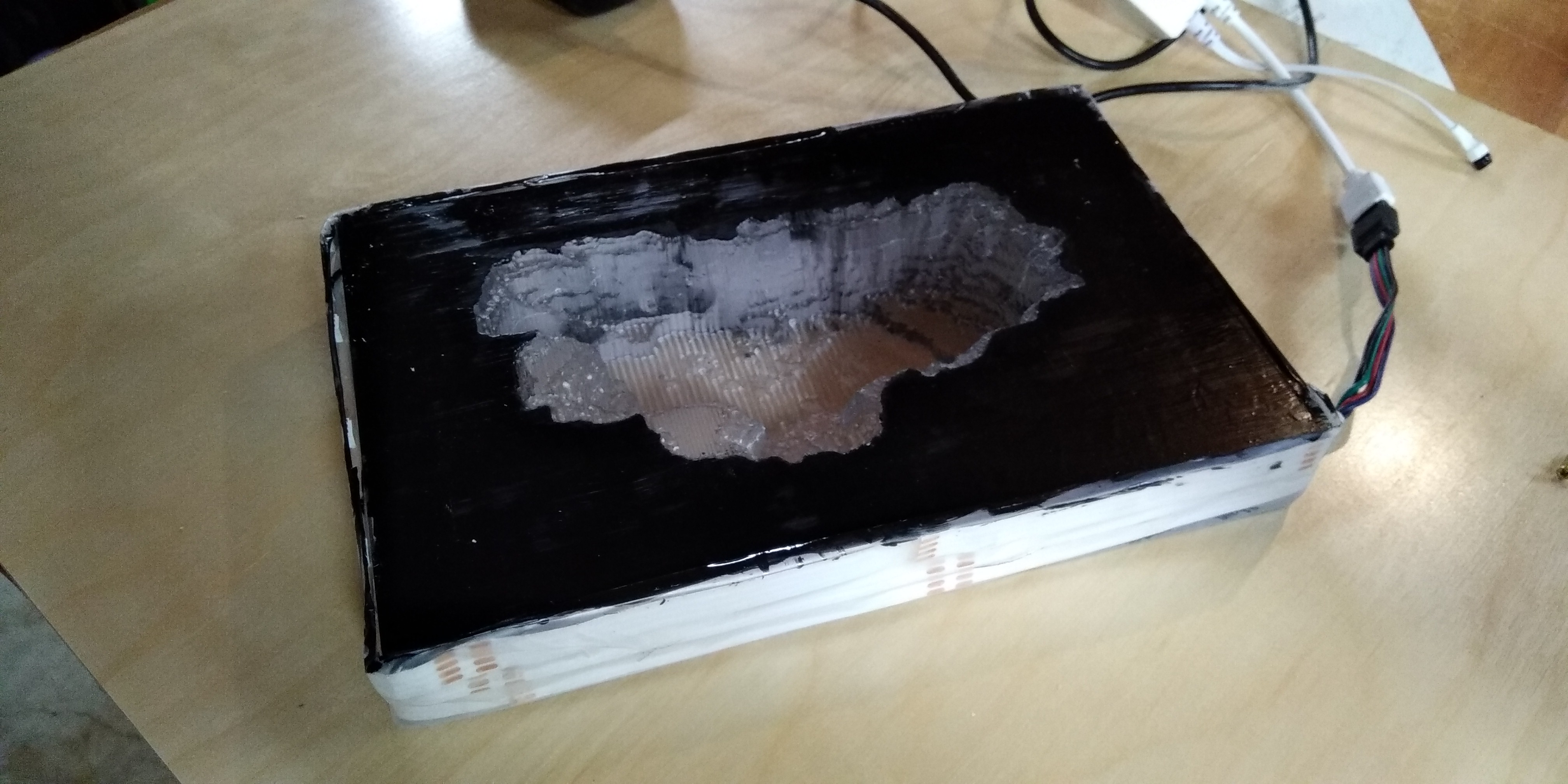
The LEDs are the ones that come on an adhesive strip, and with a remote, a control box, and a 12 volt wall wart. The adhesive is on the wrong side for my purpose so I used transparent tape (Scotch tape) to stick the LED strip onto the sides of the carving and cover the sticky part. I wrapped the strip around the sides a total of three times. This gives plenty of light. I think one could do fine with only one wrap around.
The carving lit up, but something wasn’t right. I tried putting mirrored aluminized Mylar (mirror) on the bottom. That made it brighter but too shiny and still not right. I tried painting the bottom of the carving black, but that wasn’t great either. Then, rather obvious now, I painted the top surface black – everything but the carved out lake. Much better, since it hid all the irregular cementing between acrylic layers, and it made the glowing lake pop out visually. Now all I needed was a frame so you wouldn’t see the LEDs at the sides.
The Frame
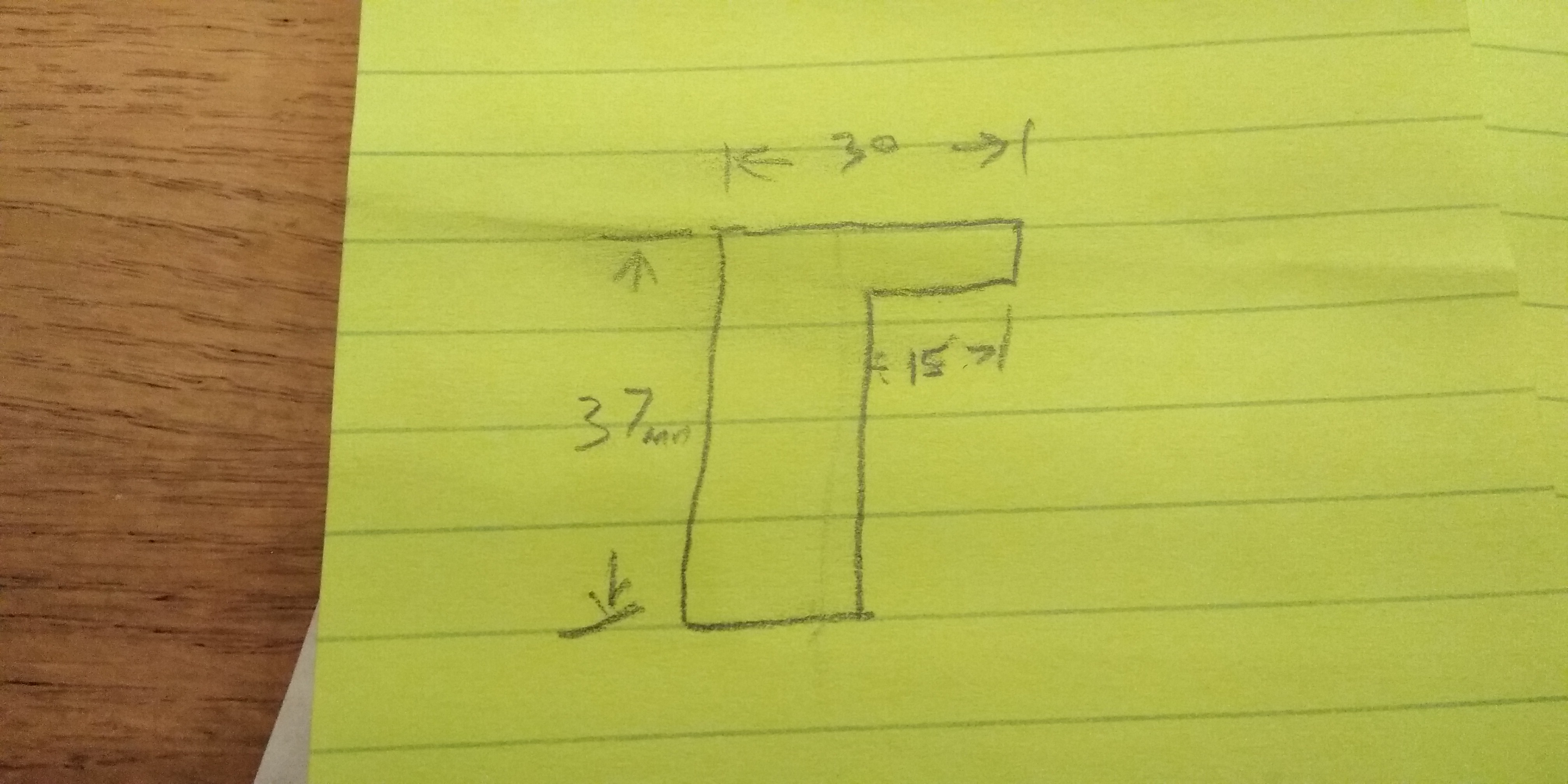
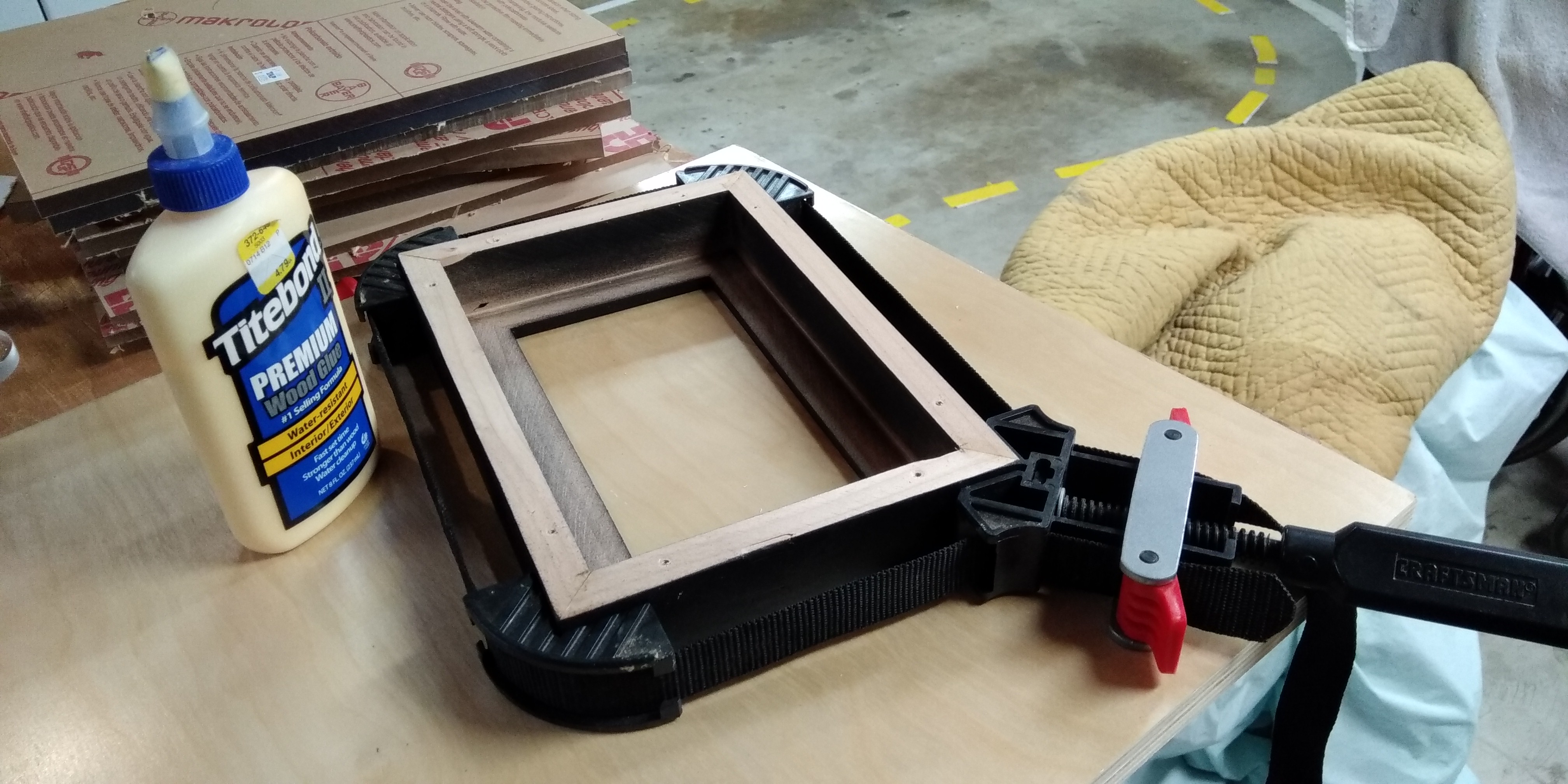
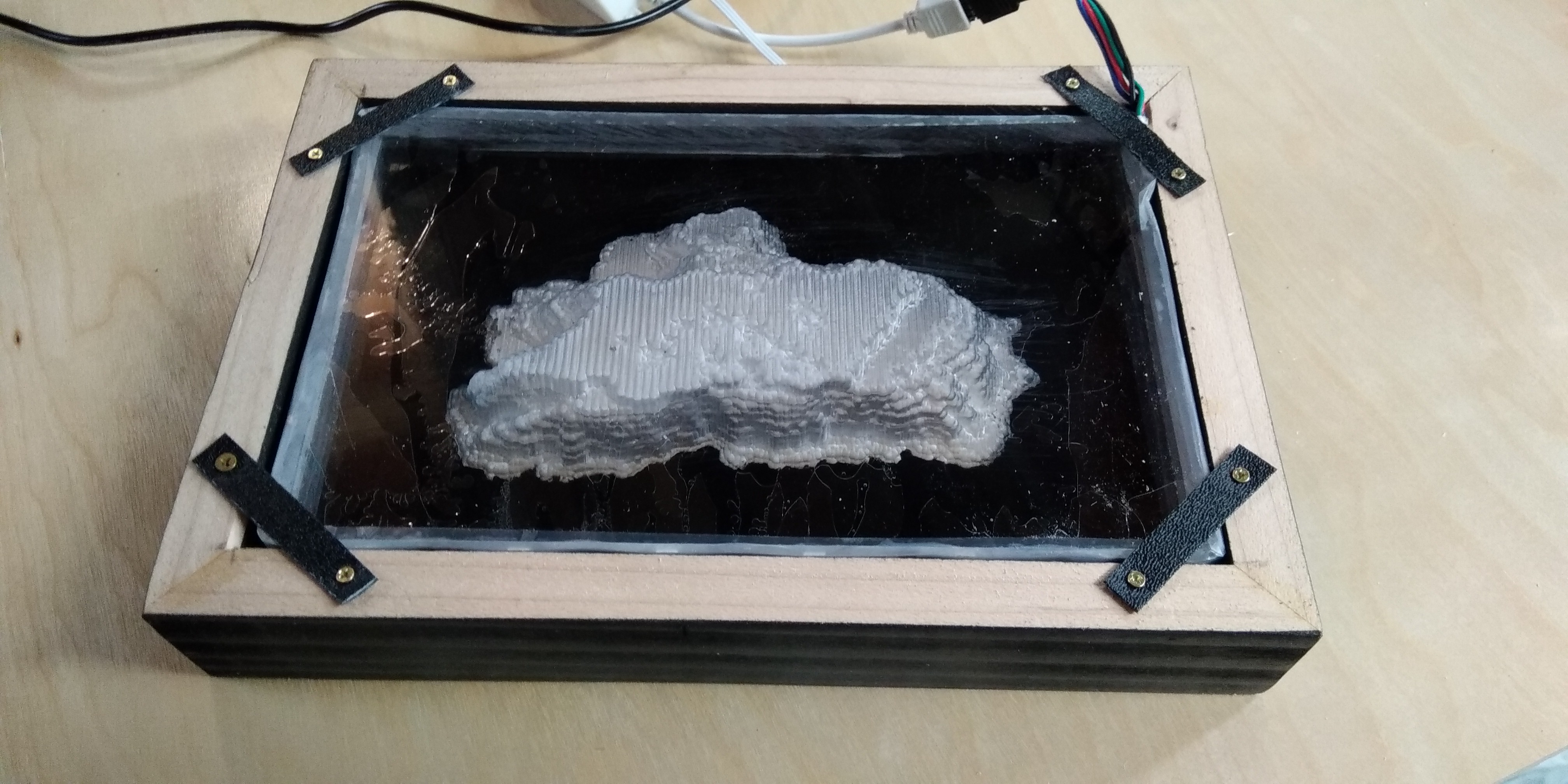
I came back from Home Depot with a nice piece of pine 2” by 2” (37mm square). I used the table saw to rip it to an L shape, so the foot of the L hung over the acrylic by about 15mm to hide the lights. It was already just the right height to cover the sides. I mitered it to size and glued it, using a clamping rig that squeezes all the pieces together. I sprayed it black, and after a couple of coats it looked fine. The acrylic piece fit inside snugly, and I secured it into the frame with little plastic strips.
Postscript
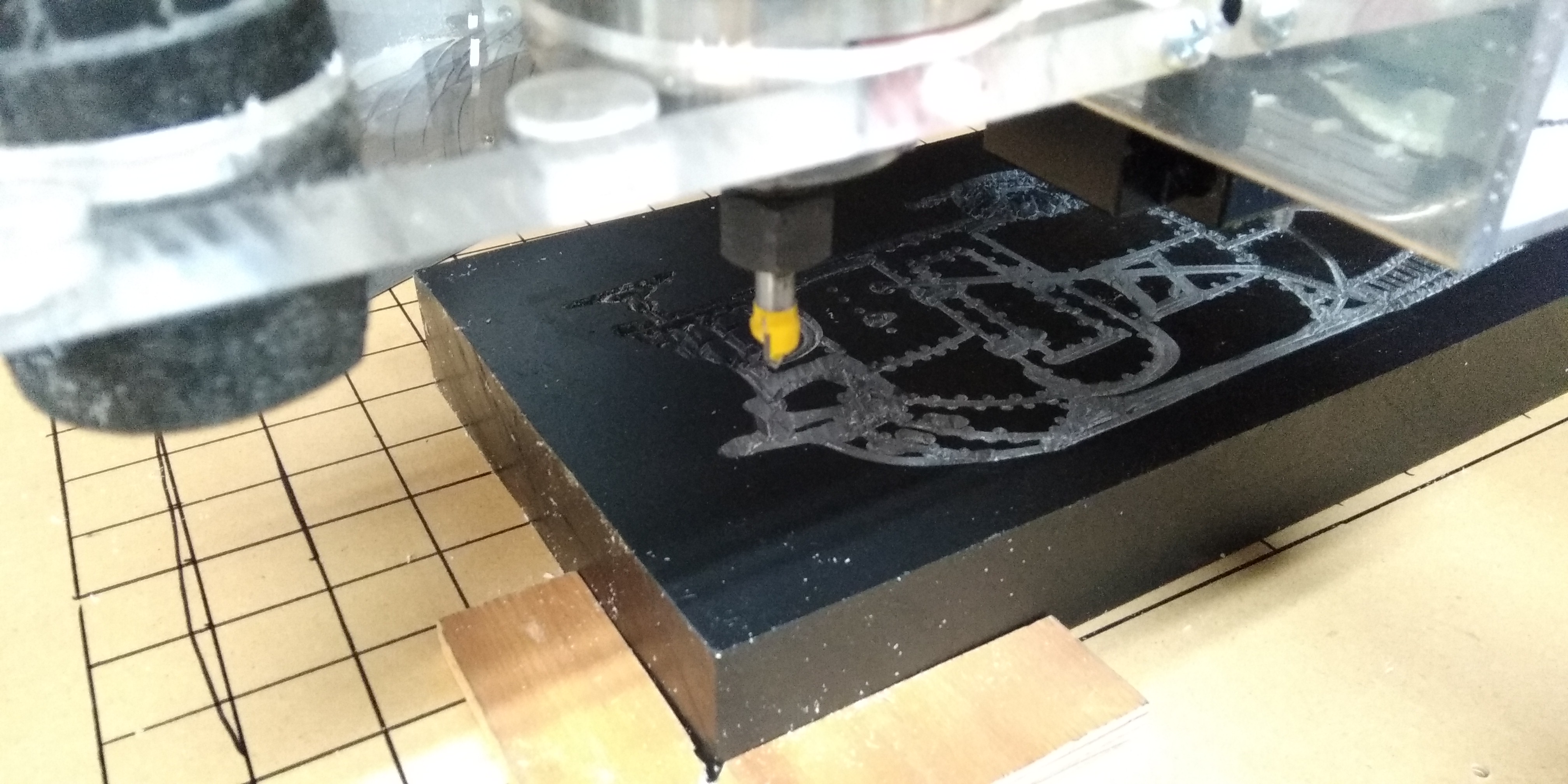
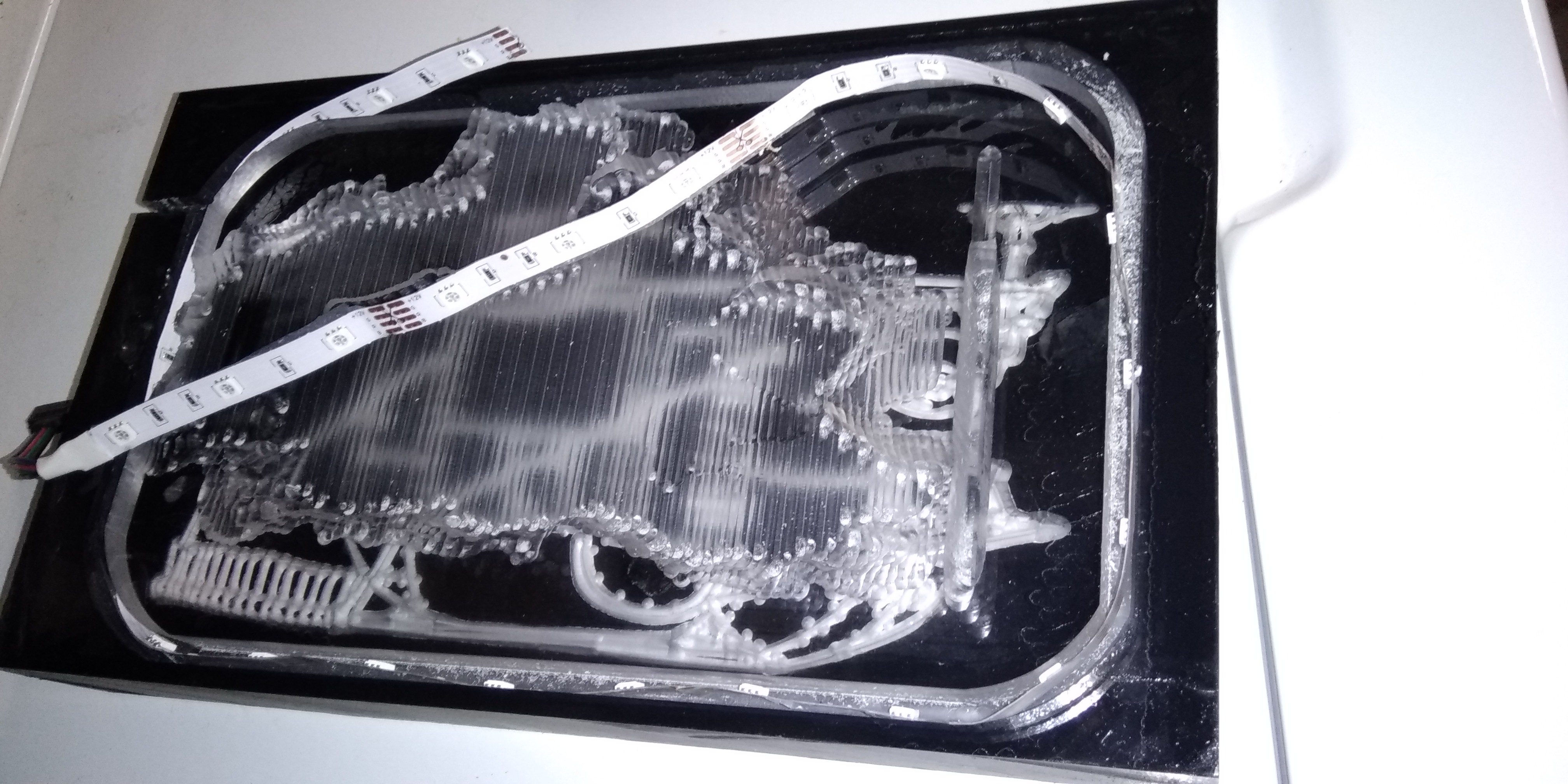
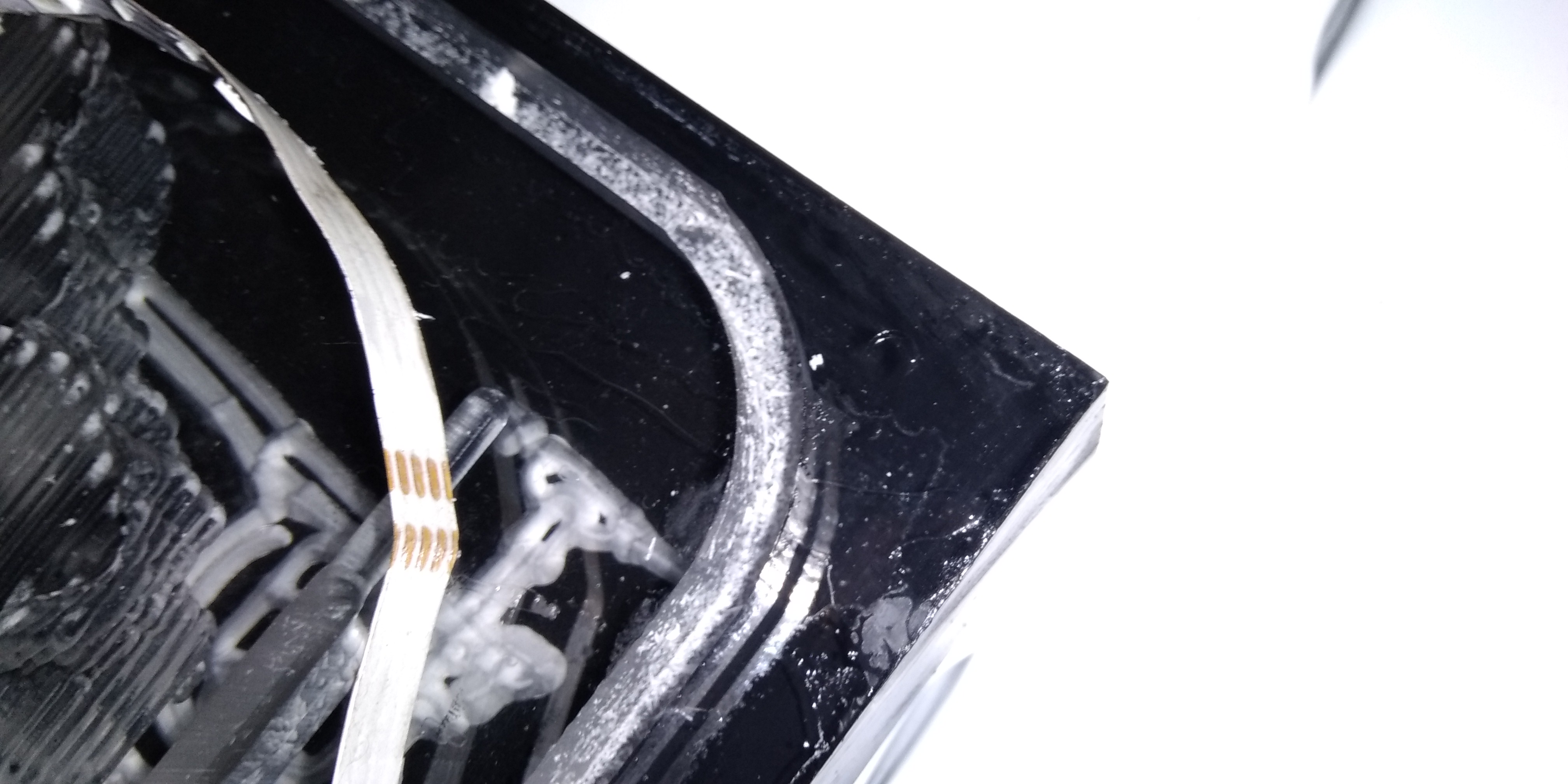
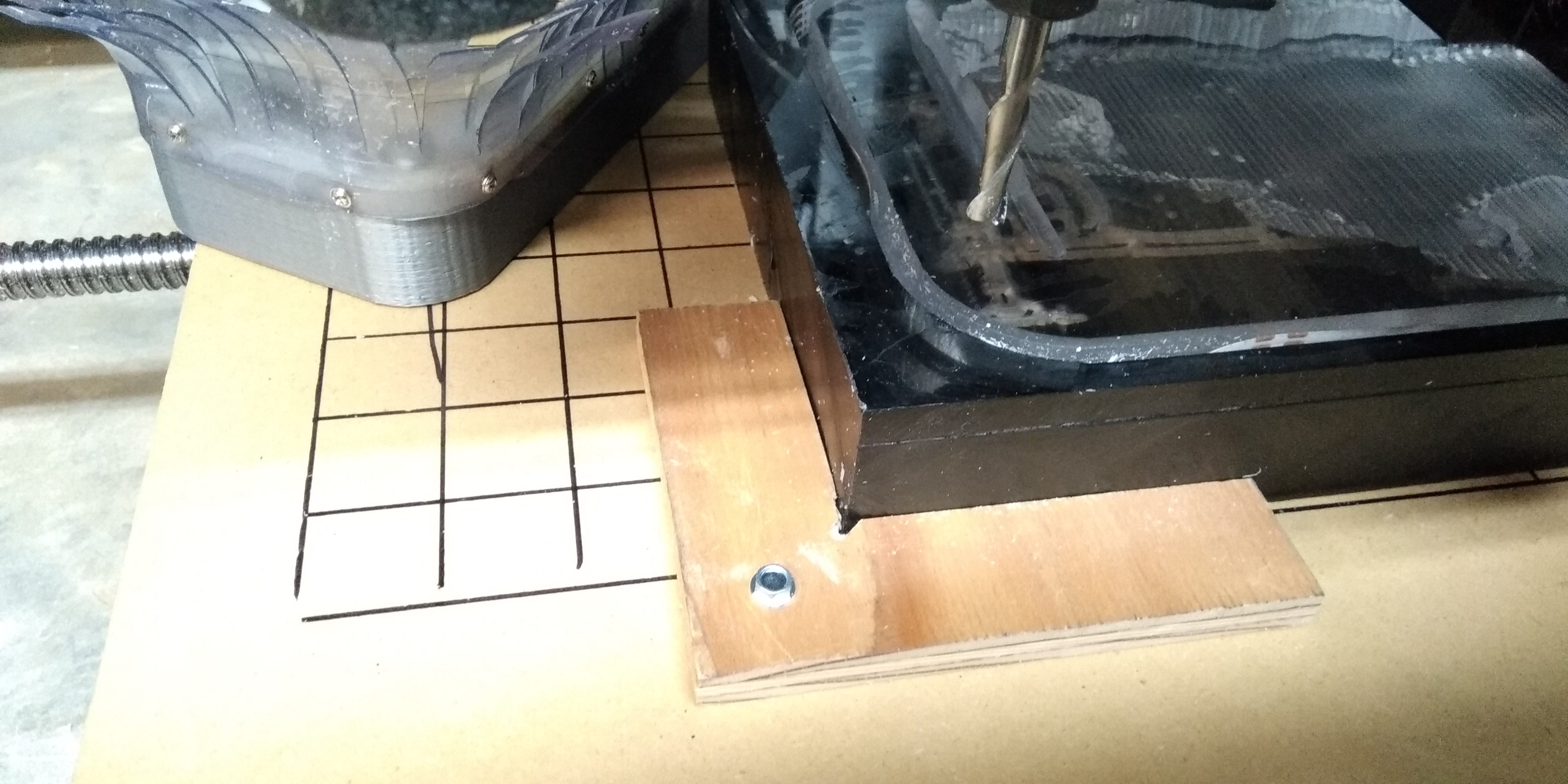
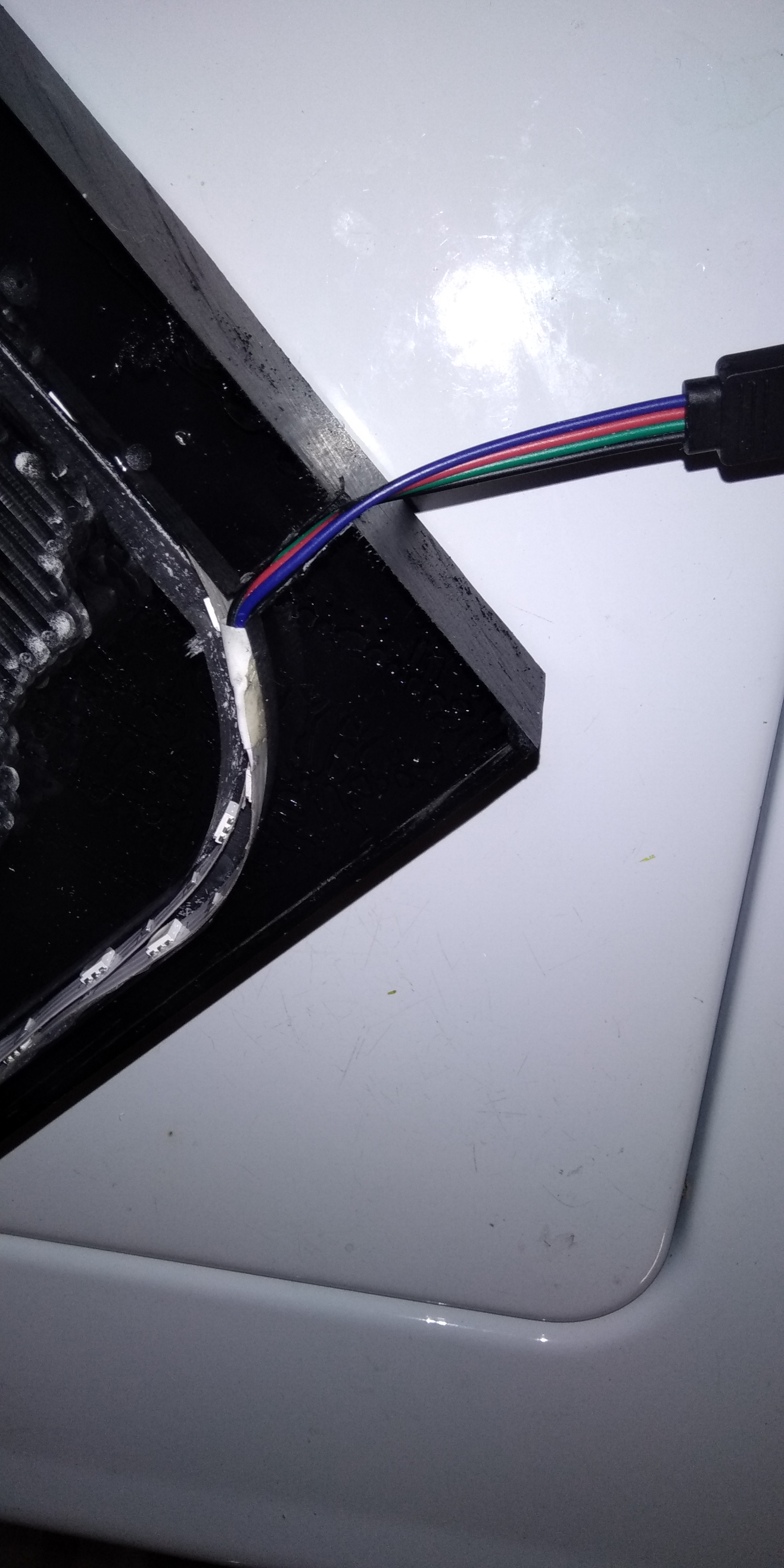
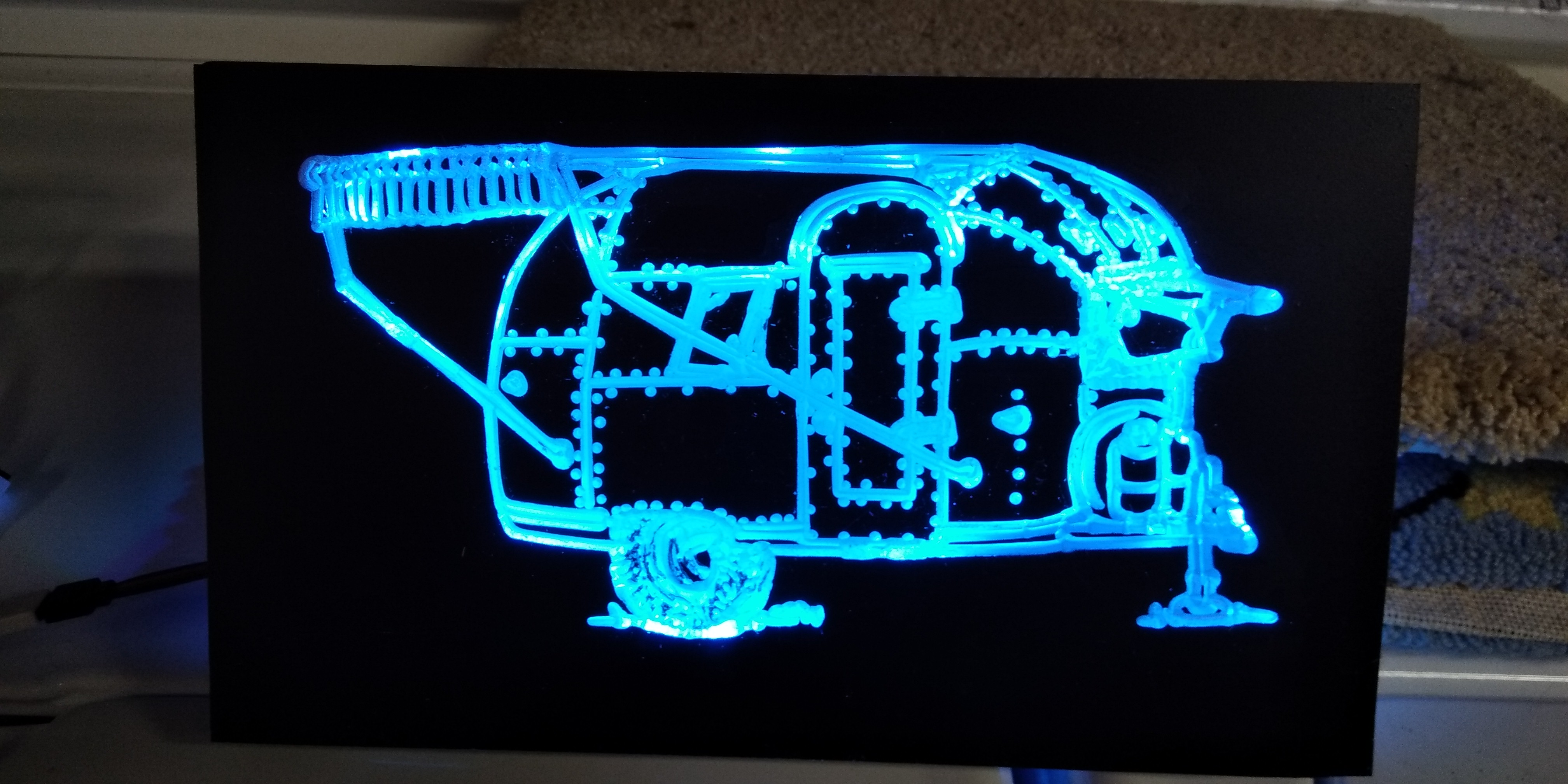

After doing several “bathymetric” carvings (more of Tahoe and one of the Pacific Ocean) I started doing V carved images on the CNC machine. The software I used for V carving was also free, Scorchworks Fengrave and quite easy to use. The first bunch of carvings were in wood (Poplar) where the carved out portion was painted black and the wood face was sanded to white. But I had this big chunk of acrylic left over from the spoiled large Tahoe effort. The oldest daughter loves Airstream trailers so I decided to V carve an Airstream image on the back side of the spoiled acrylic. With black paint on the face, only the V carved part would show and it could be lit up with LEDs.
By the way, a great source for v-carvable drawings is Google Images looking for “coloring pages”. They’re black & white, mostly with bold lines and fairly simple. Looking for “line drawings” is not great because you get artistic but intricate images – not carvable.
I painted the face black before doing the V carving so I wouldn’t have to “paint between the lines” later. This is worth doing, but isn’t magic because the CNC dust shoe rubs against the paint and makes little scratches on the black surface. It required some touch-up after carving. Maybe next time I’ll do the V carving without the dust shoe and clean up afterward.
Instead of a wooden frame to hide the LED strip, I used the CNC machine to rout out a deep slot on the back. This allowed the LEDs to be contained within the acrylic block. I was pleased with this improvement.