Stainless Steel Damascus Rings
by GoldenFabrications in Workshop > Metalworking
3574 Views, 61 Favorites, 0 Comments
Stainless Steel Damascus Rings
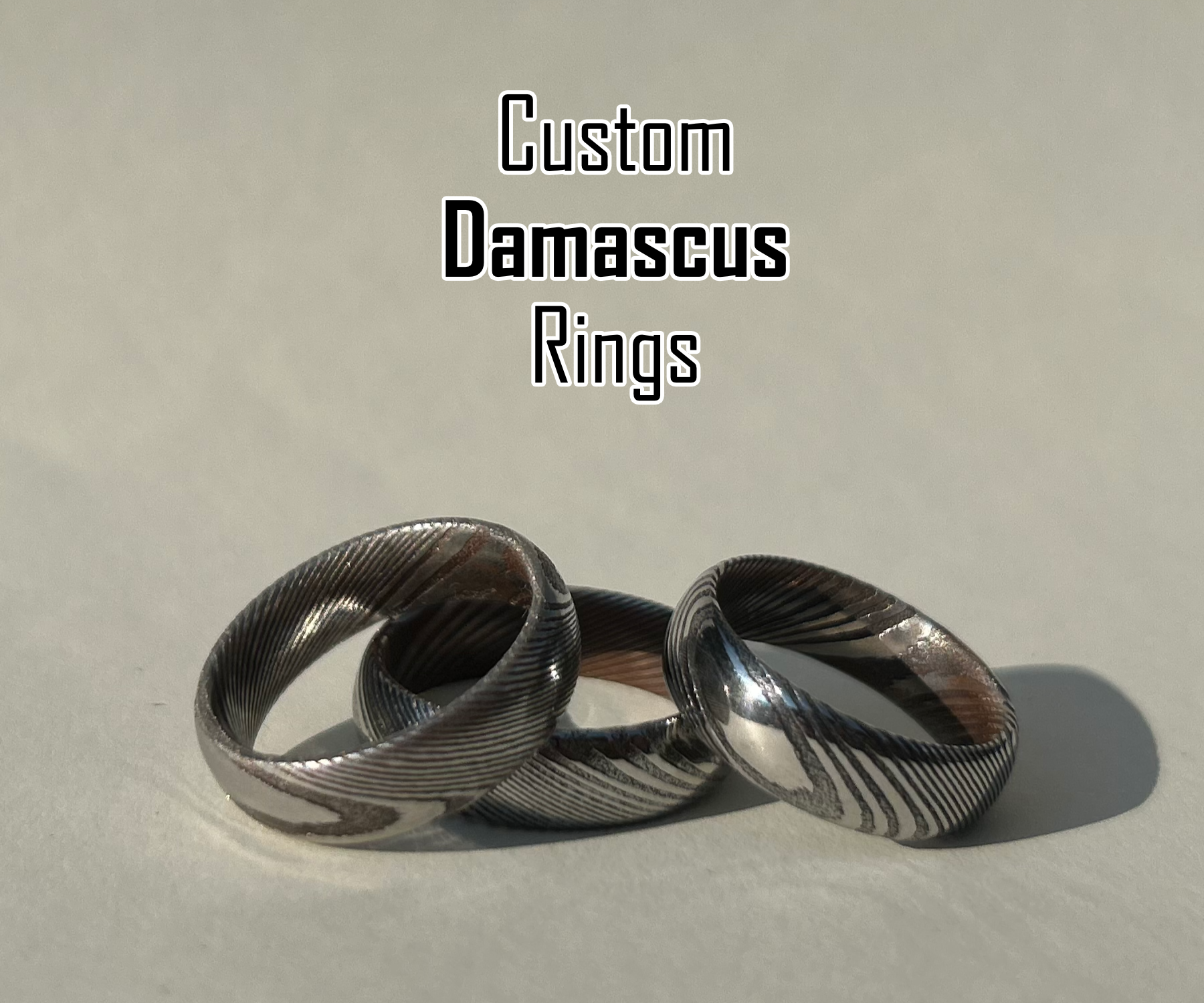
I've always loved the rich and captivating patterns within Damascus steels. The twist and patterns within them always reminded me of how two different things can create one beautiful image. I thought this would be a perfect representation of marriage. I created my first ring for my wedding and now am making them for other people! I wanted to share my process so you too can create a beautiful ring.
What is Damascus steel, you might ask? Originating from ancient sword-making techniques, Damascus steel boasts a mesmerizing, distinctive pattern, characterized by its swirling and flowing waves. Traditionally, this technique was applied to create formidable swords and knives with beautiful patterns. However, I will be employing modern stainless steel with its enhanced rust resistance to craft elegant rings that embody the essence of this time-honored art form.
Throughout this guide, we'll share with you the essential tools, materials, and techniques required to create your very own stainless steel Damascus rings.
Supplies
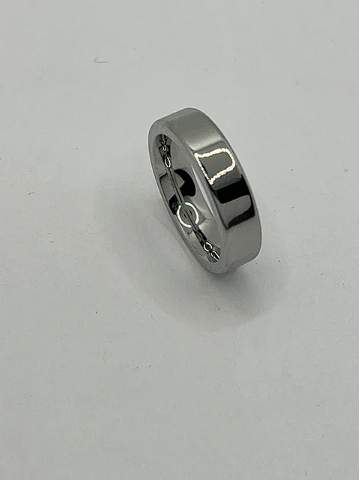
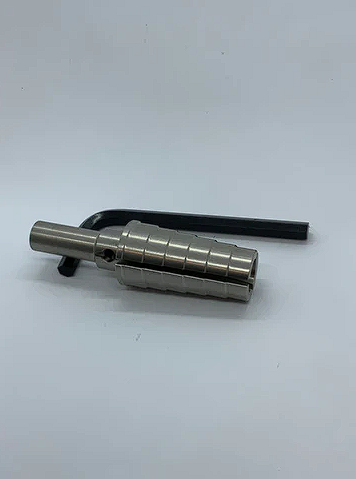
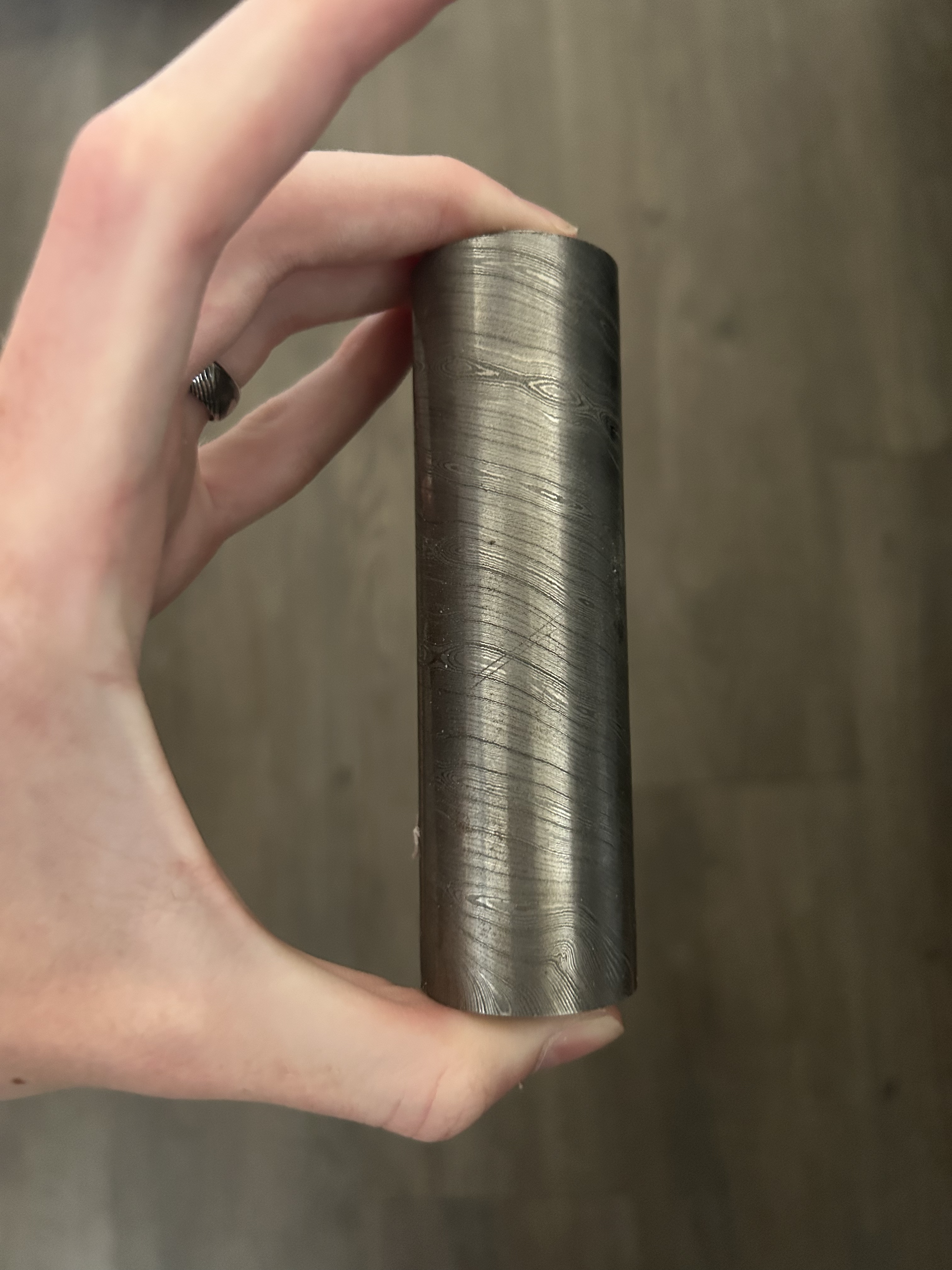
A great website for sourcing your materials: https://ringsupplies.com
Ring Blanks (Option 1)
Damascus Round Stock (Option 2)
Glass Jars (Small Mason Jars)
Dremel (Or Other Rotary Tool)
Designing Your Ring
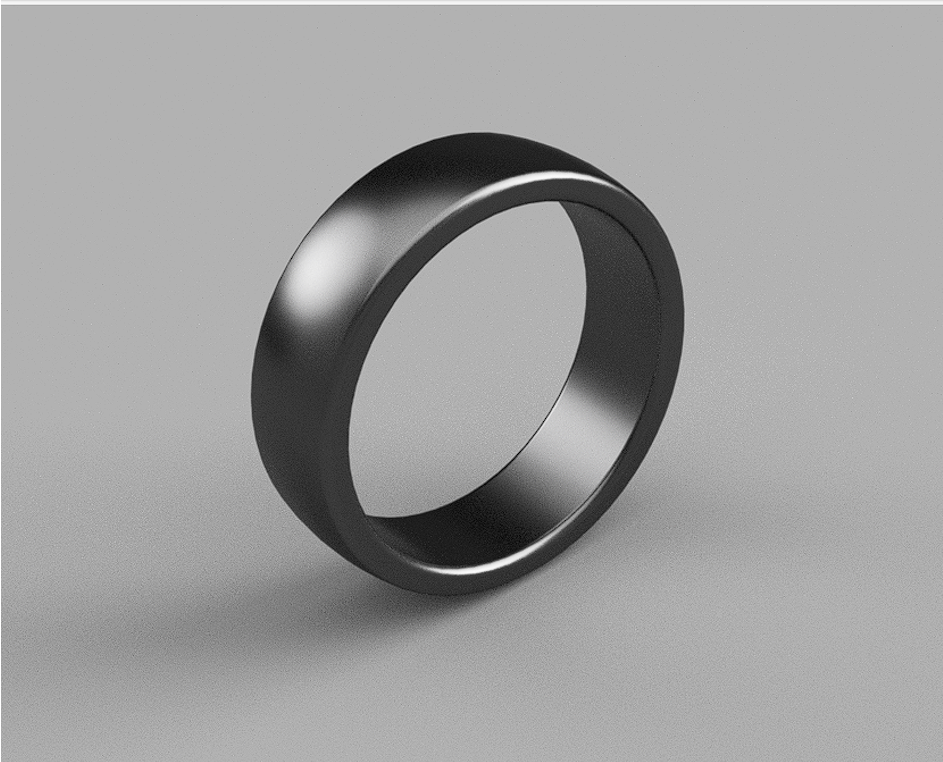
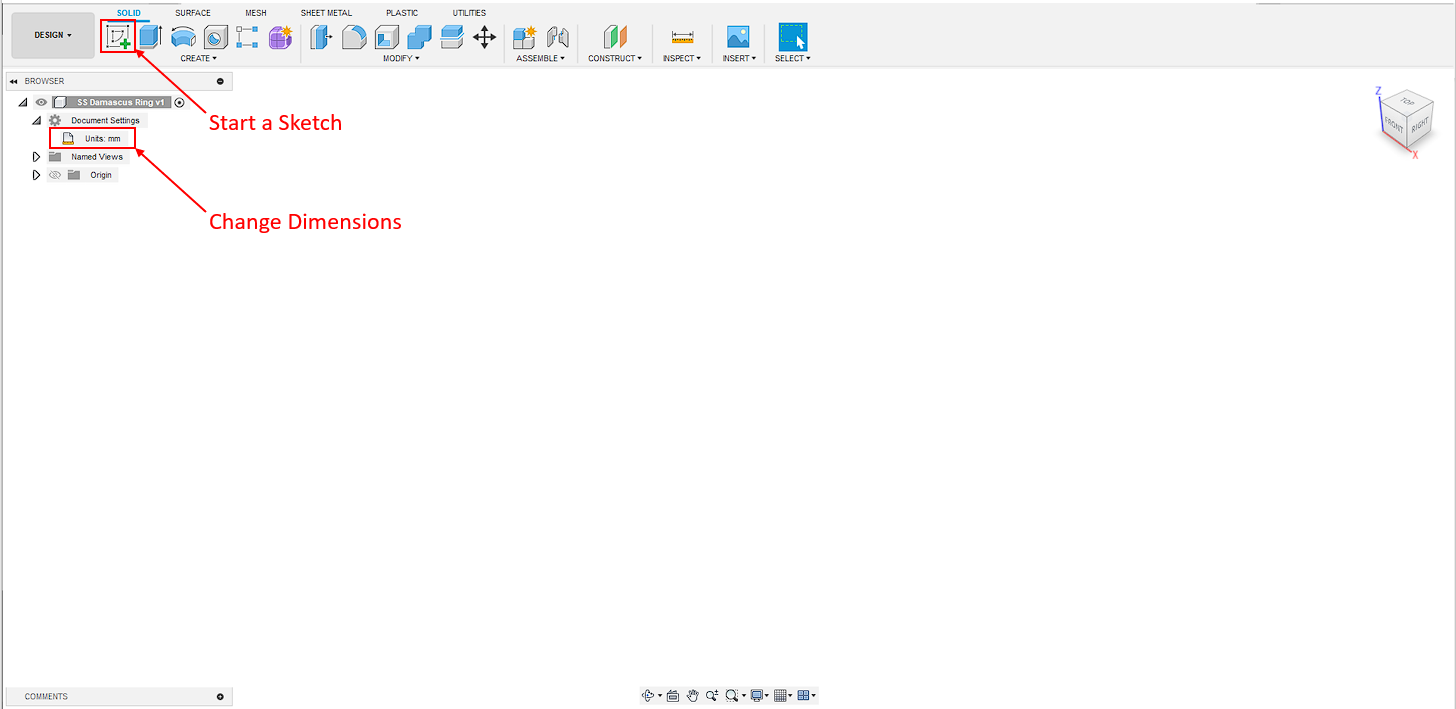
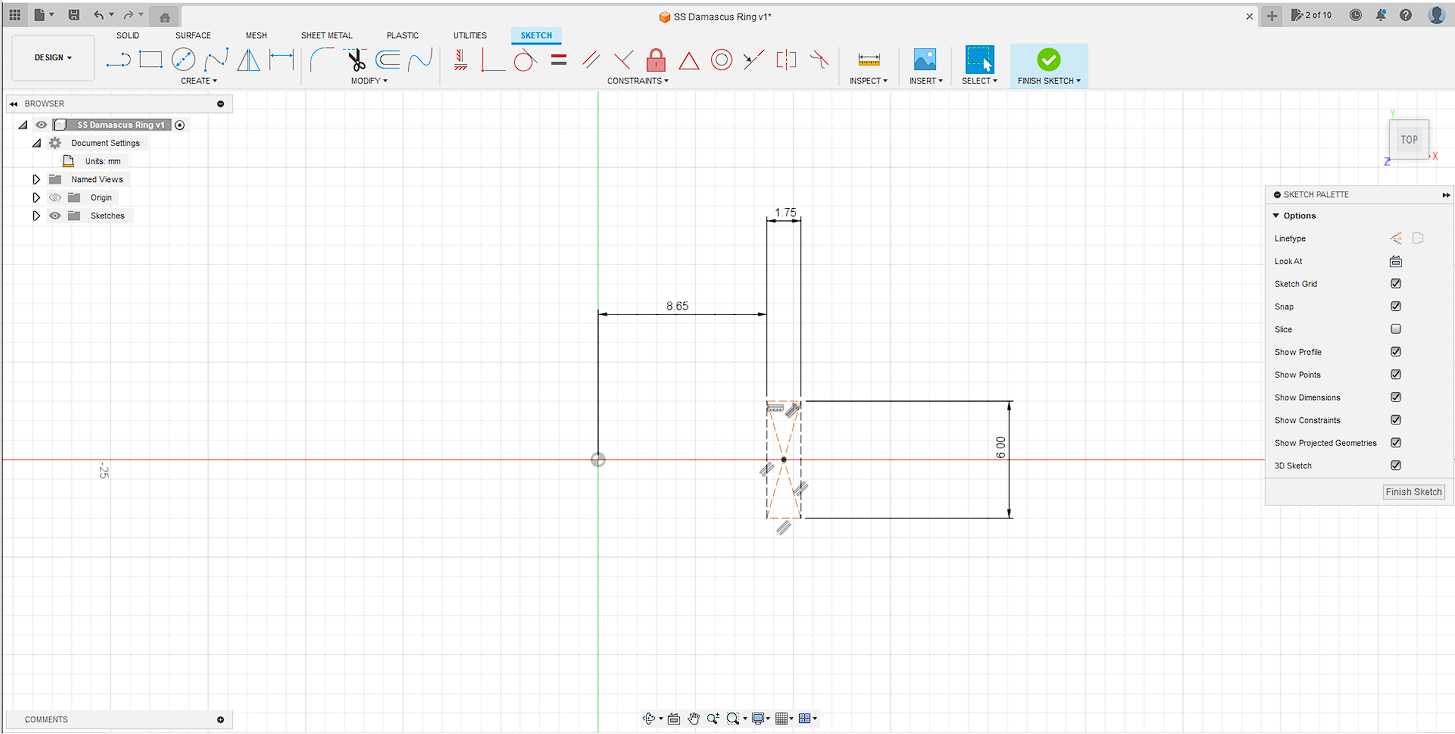
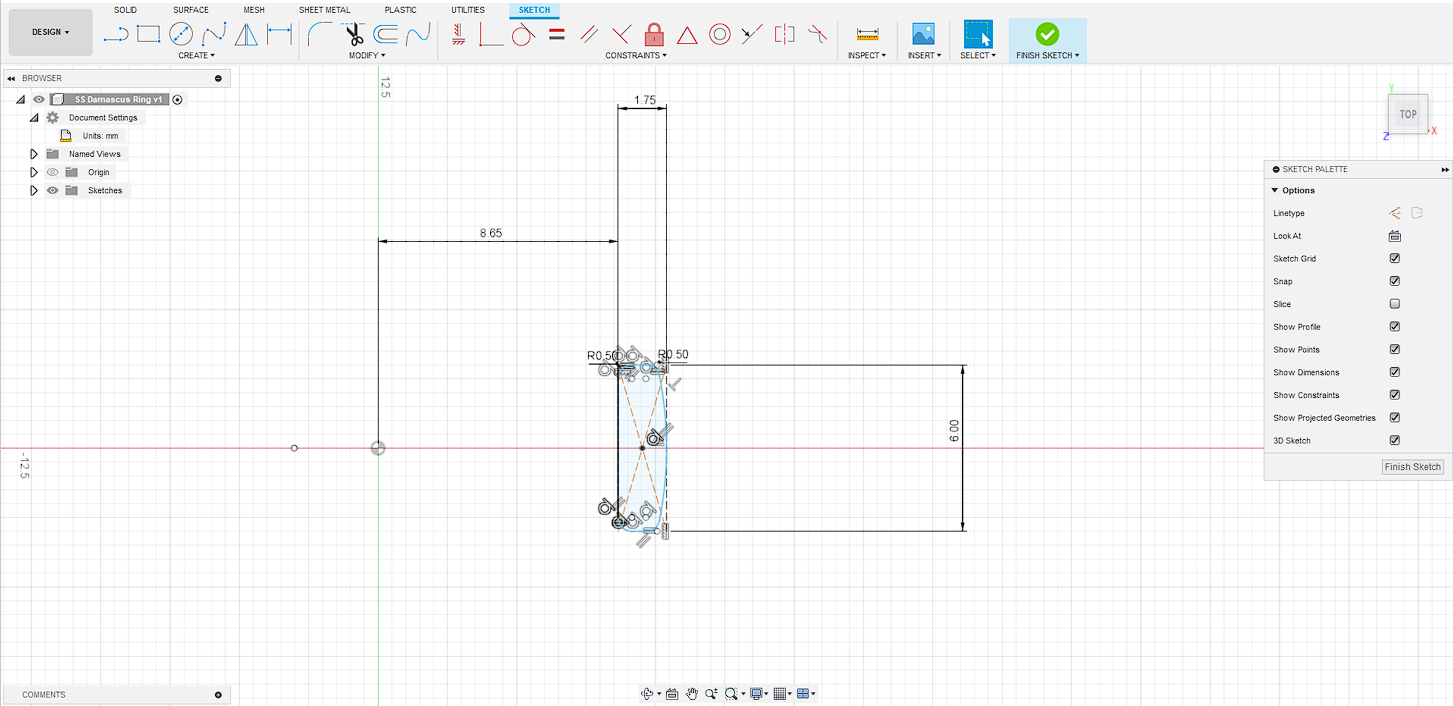
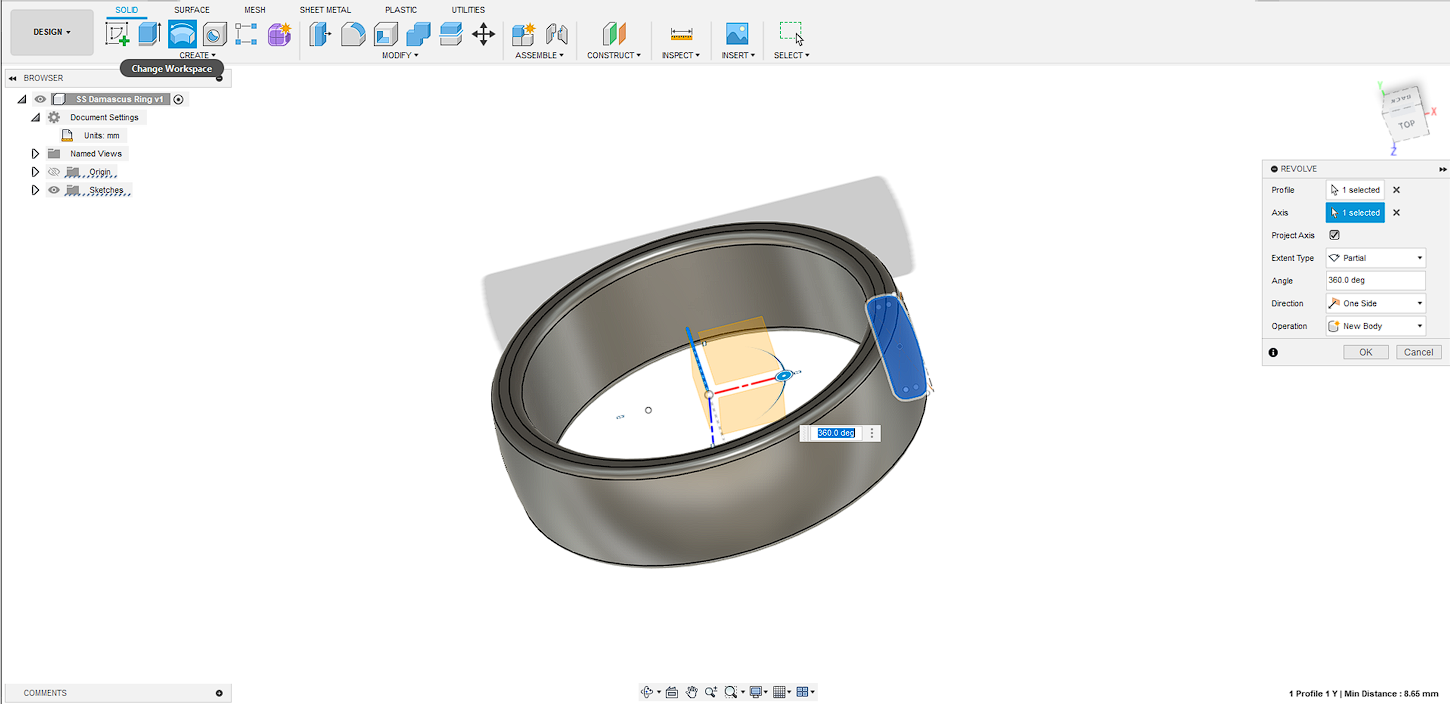
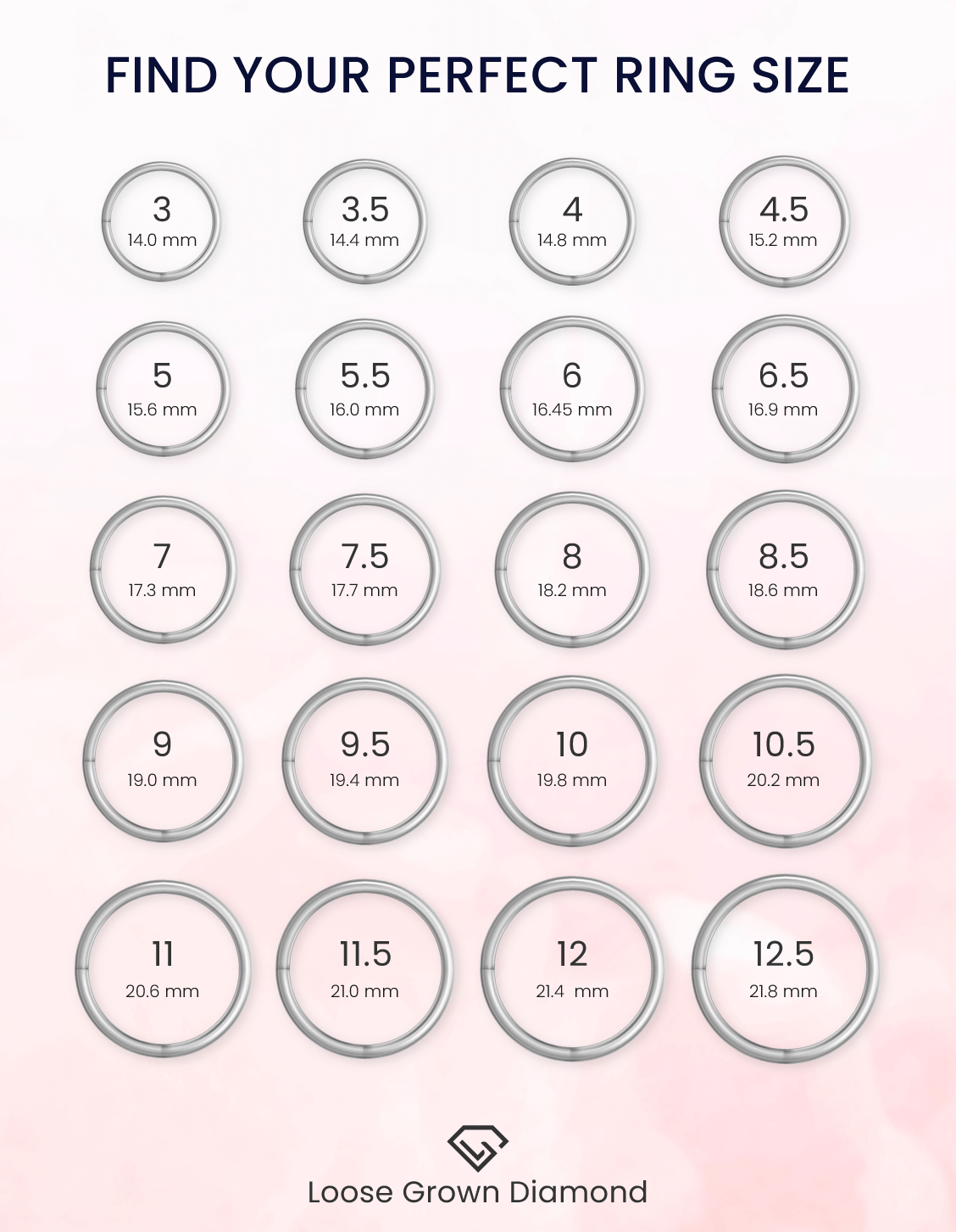
When designing custom rings, having a plan is a crucial step into create a ring you'll love. In order to make a ring design I loved, without wasting time iterating on expensive material, I decided to use Fusion 360. Fusion 360 is an easy-to-use CAD software used to quickly prototype designs. It is great for getting ideas from your head into the physical world.
Step 1: Launch Fusion 360
Open Fusion 360 on your computer and create a new design file to start working on your ring design. Fusion 360 is free to use for makers!
Step 2: Set Up the Design Environment
Rings are measured by sizes (6.5,7,8, etc.) these sizes correspond to inner diameters in mm shown on the chart above. Because of this, I like to work in millimeters when designing.
Step 3: Sketch the Ring Profile
Using the Sketch tools, draw the 2D profile of your ring on the XY plane. Consider the ring's width, thickness, and overall shape. You can experiment with different profiles to find the one that suits your vision best. Keep in mind this sketch will be rotated around the y-axis, so when spacing your profile away from the y-axis use the radius of your desired ring size instead of the diameter.
Step 4: Revolve the Profile
With the sketch selected, use the "Revolve" command to give your 2D profile some thickness and turn it into a 3D shape.
Step 6: Apply Materials
Assign appropriate materials to different components of the ring to visualize how it will look in real life. For the stainless steel part, choose a suitable metal material to give it a realistic appearance.
Step 9: Review and Refine
Take some time to review your 3D model from different angles and perspectives. Make any final refinements or tweaks to perfect your design.
Step 10: Save and Export
Once you're satisfied with your ring design, save the Fusion 360 project file and consider exporting it to other formats like STL if you plan to 3D print the ring or share it with others. 3D printing can be a great way to get the feel of the ring and see how it fits you. Use calipers to double-check the ring size measurements, because 3D-prints can create out-of-dimension parts.
Repeat these steps until you find a ring design that you love!
Choosing Your Material
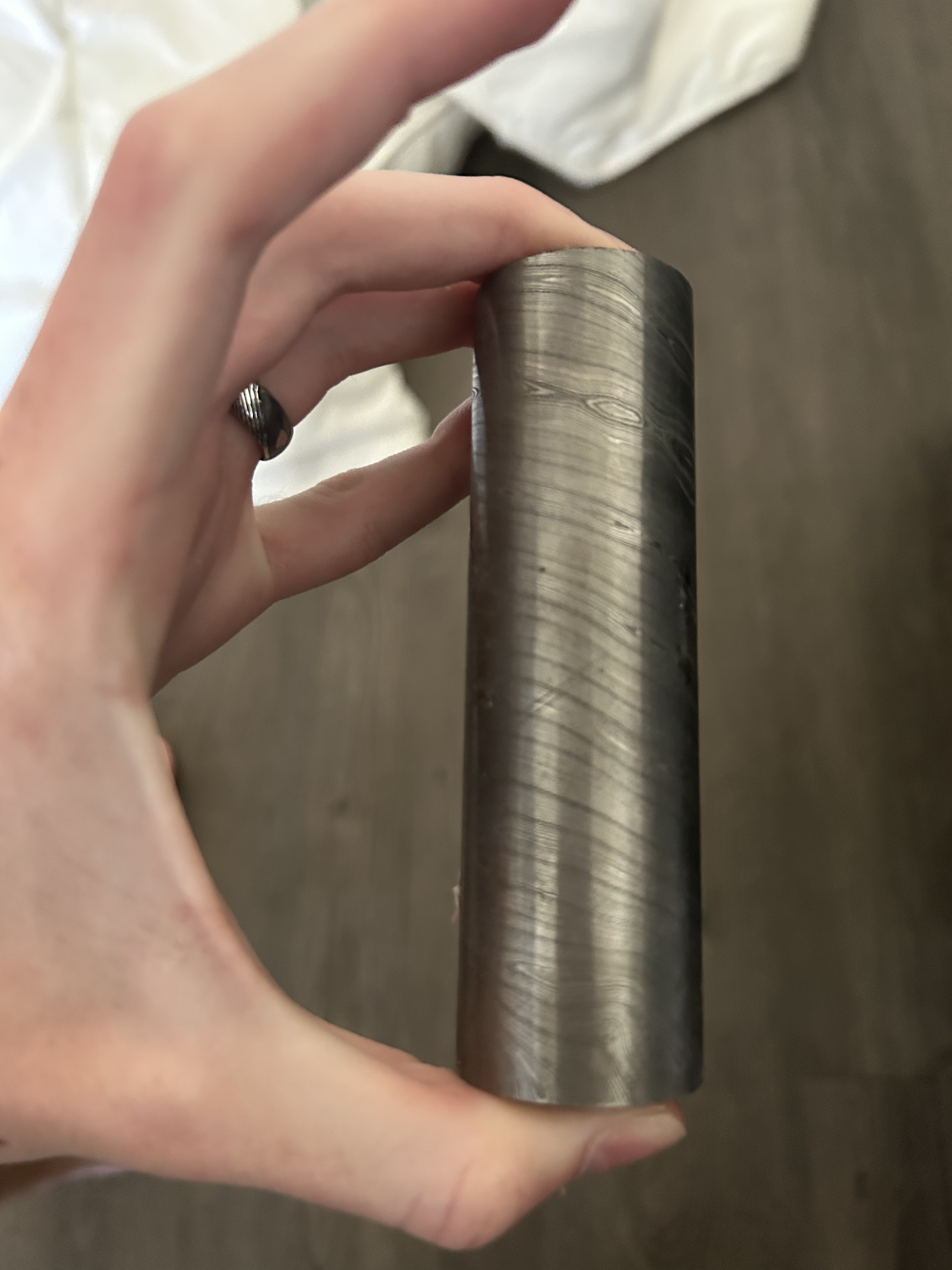
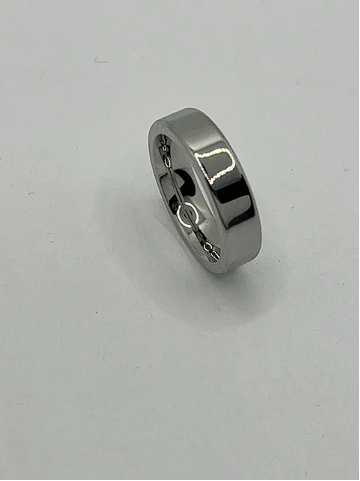
There are two types of Damascus steel you can use.
- Carbon Steel Damascus:
- Appearance: Carbon steel Damascus is known for its striking contrast and dark patterns. The high carbon content allows for deeper etching during the acid etching process, resulting in prominent and bold patterns.
- Maintenance: Carbon steel requires more care and maintenance compared to stainless steel. It is susceptible to rust and corrosion, so regular cleaning, drying, and oiling are necessary to prevent tarnishing.
- Hardness: Carbon steel Damascus tends to be harder than stainless steel Damascus, making it an excellent choice for sharp-edged tools like knives. However, for rings, this hardness can lead to increased brittleness and the potential for chipping or cracking under certain conditions.
- Cost: The cost of carbon steel damascus is a lot cheaper than stainless steel.
- Stainless Steel Damascus:
- Appearance: Stainless steel damascus exhibits more subtle and refined patterns compared to carbon steel. The etching process may not produce as deep contrasts, but it can still result in beautiful and elegant designs.
- Maintenance: Stainless steel is highly resistant to rust and corrosion, making it low maintenance and ideal for everyday wear. It won't require as much care and can withstand exposure to moisture without significant issues.
- Hardness: While stainless steel is generally less hard than carbon steel, it still provides sufficient durability for a ring. It strikes a good balance between hardness and toughness, making it less prone to cracking or chipping compared to high-carbon steel.
- Cost: The cost of stainless damascus is significantly higher than carbon damascus.
- This is my personal choice due to its ability to resist rust and low maintenance.
The choice between carbon steel damascus and stainless steel damascus for your ring depends on your preferences and budget. If you desire a bold and dramatic pattern with a unique appearance, carbon steel might be more suitable. On the other hand, if you prioritize low maintenance, corrosion resistance, and everyday wear, stainless steel damascus would be a better option.
The first ring I created was out of carbon steel, after a few months it began to rust on the inner diameter. However, I was not being super careful with it. I would take it in the shower with me and wash my hands with it on, which allowed for rust to form easier. Because of this, I made a new one out of stainless steel which has been holding up great!
Turning Your Ring
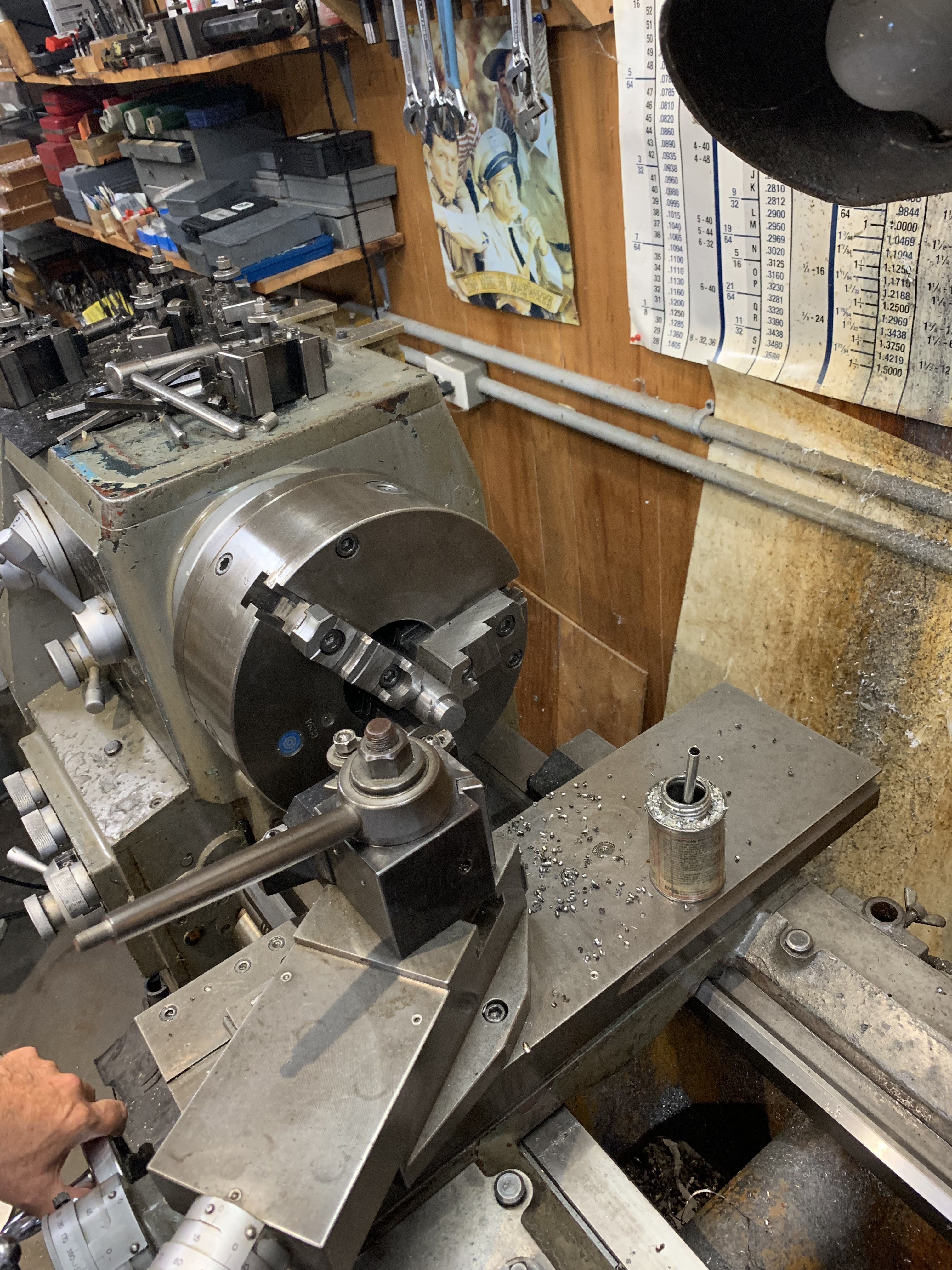
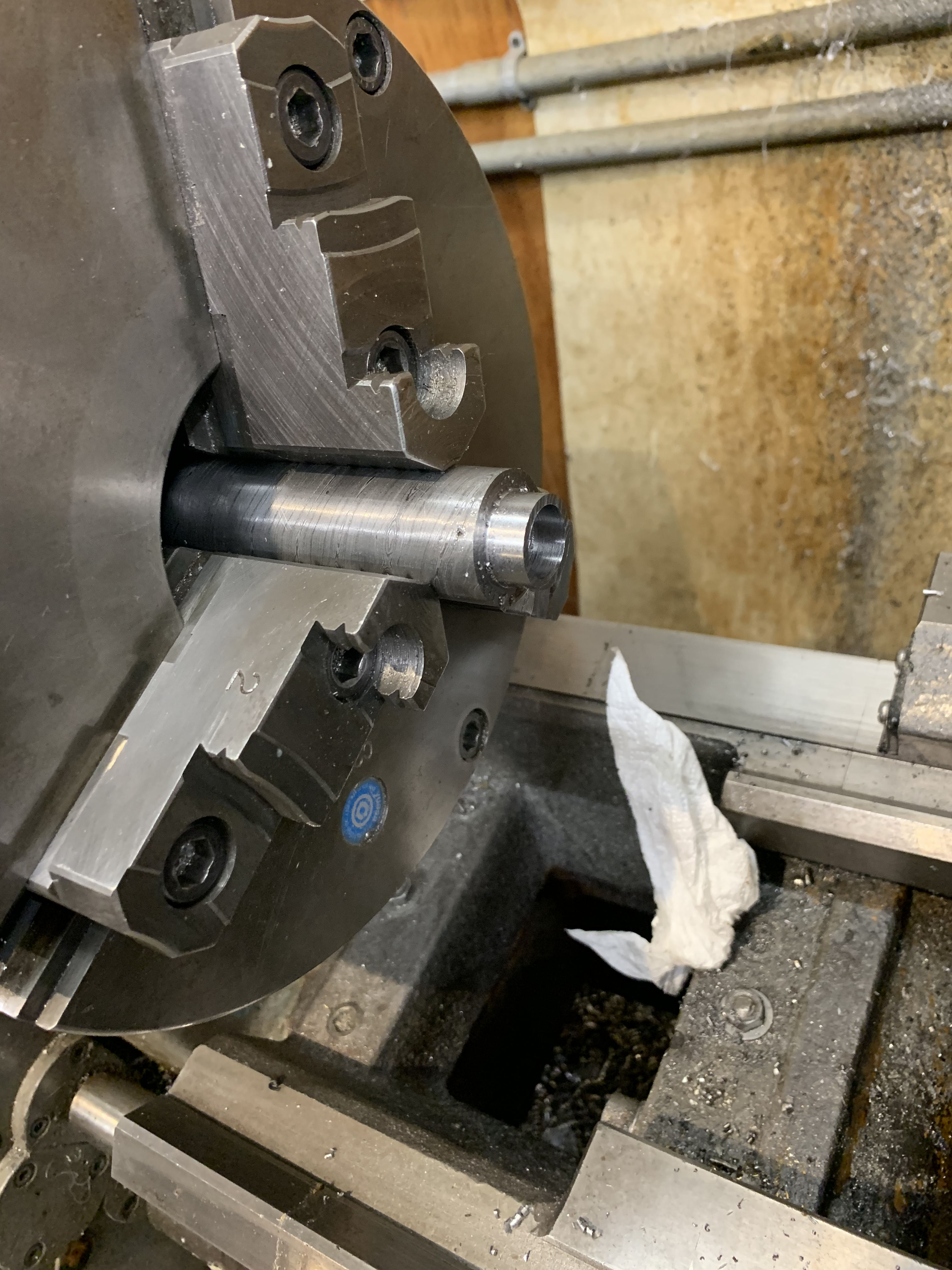
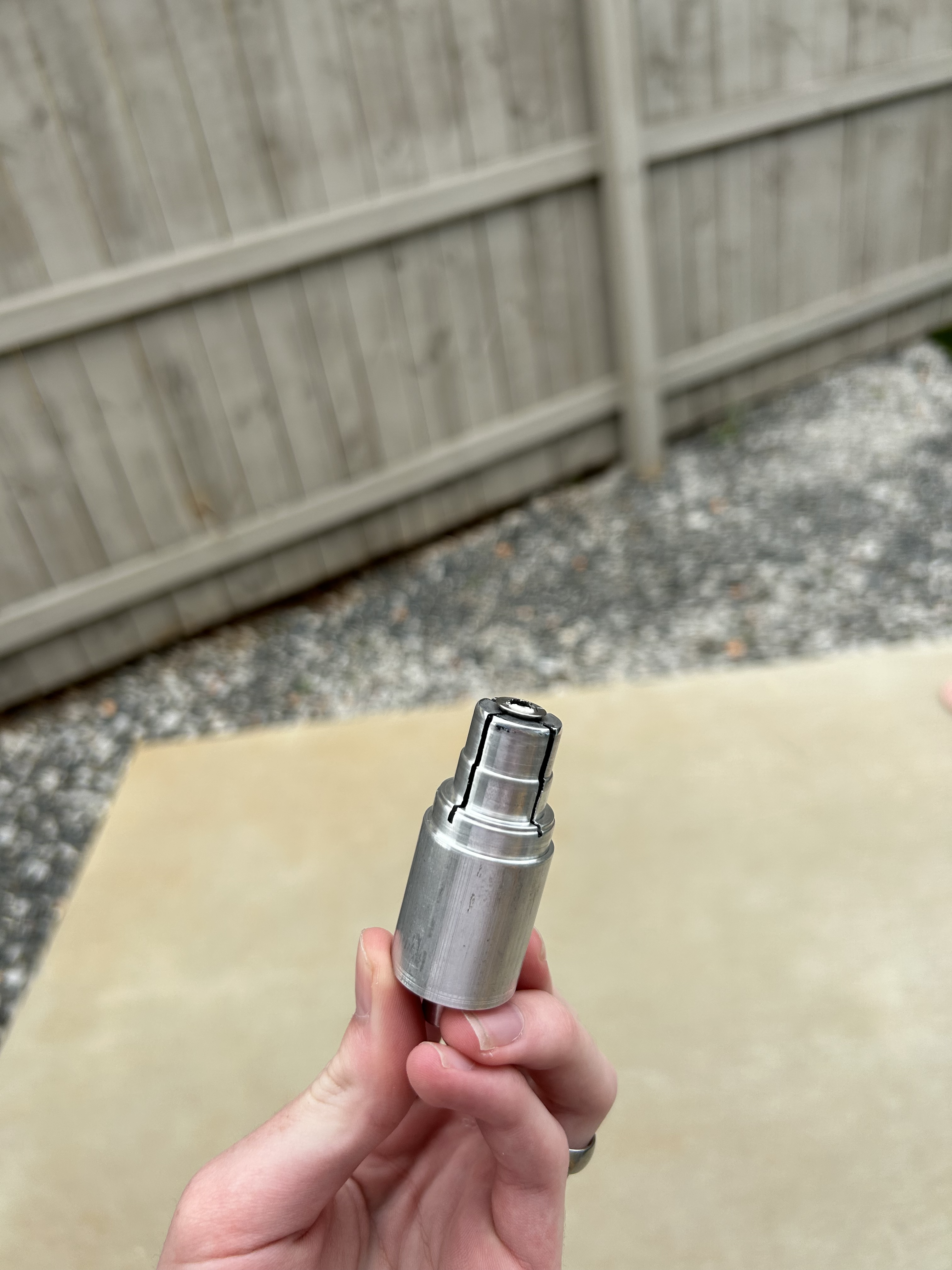
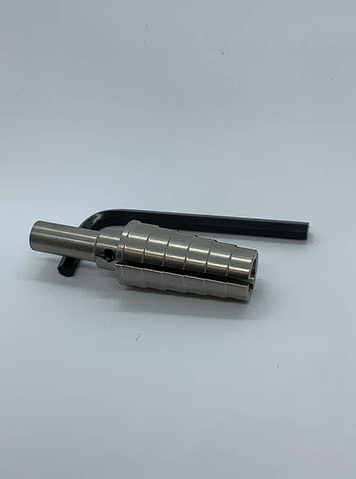
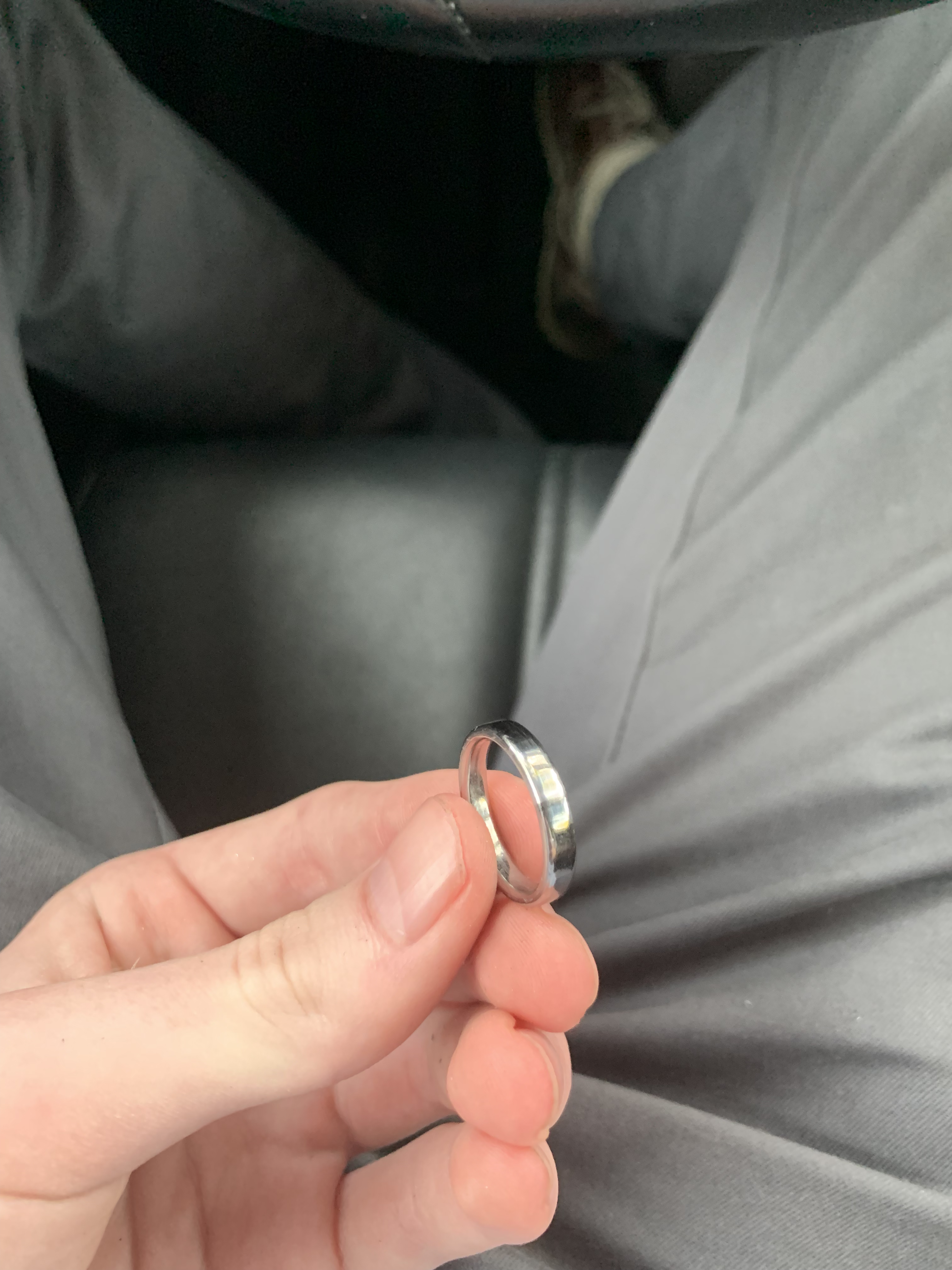
Step 1: Secure the Ring Blank/Stock:
- If you are using a ring blank it is really helpful to use a ring mandrel to secure it to the lathe's chuck. They have ring mandrels in stock on the website list in the supplies section. I however did not want to purchase one, because I was not sure how many rings I wanted to make so I created my own out of scrap aluminium. I created it by cutting a cross shape with a bandsaw and tapping the center of the cross with an M5 screw. I then machined the aluminum to have the right outer diameter to hold onto the ring sizes that I needed. Place the ring over the mandrel and then tighten it in.
Step 2: Select the Lathe Tools:
- I went simple by using a piece of high-speed steel that had a sharp edge ground into it, but a carbide tip would do just fine.
Step 3: Set the Lathe Speed:
- Adjust the lathe's speed according to the size and material of your ring blank. If you are using carbon steel and a HSS cutter I recommend a speed of around 220 FPM. For stainless, I recommend 120 FPM (Feet per Minute).
Step 4: Start Turning the Outer Profile:
- With ring blanks, the inner diameter will already be bored out to your desired size with a nice comfortable fit on it. This means all you have to machine is the outer profile. Start by cutting down the outer diameter to the highest point of your ring. You can get this dimension by referencing your Fusion 360 model/drawing and using the measure tool. Next, use a file on the edges of the ring to slowly bring down the edges to your desired outer profile. This step takes patience and a sharp file!
- If you are using a round stock of steel I recommend boring out the inner diameter before doing the outer diameter.
Step 5: Refine the Outer Surface:
- Once you have the desired outer diameter use 400 grit sandpaper to smooth out the outer profile. Do not use any grit higher than 400, a rougher surface helps with the etching process.
Etch the Ring
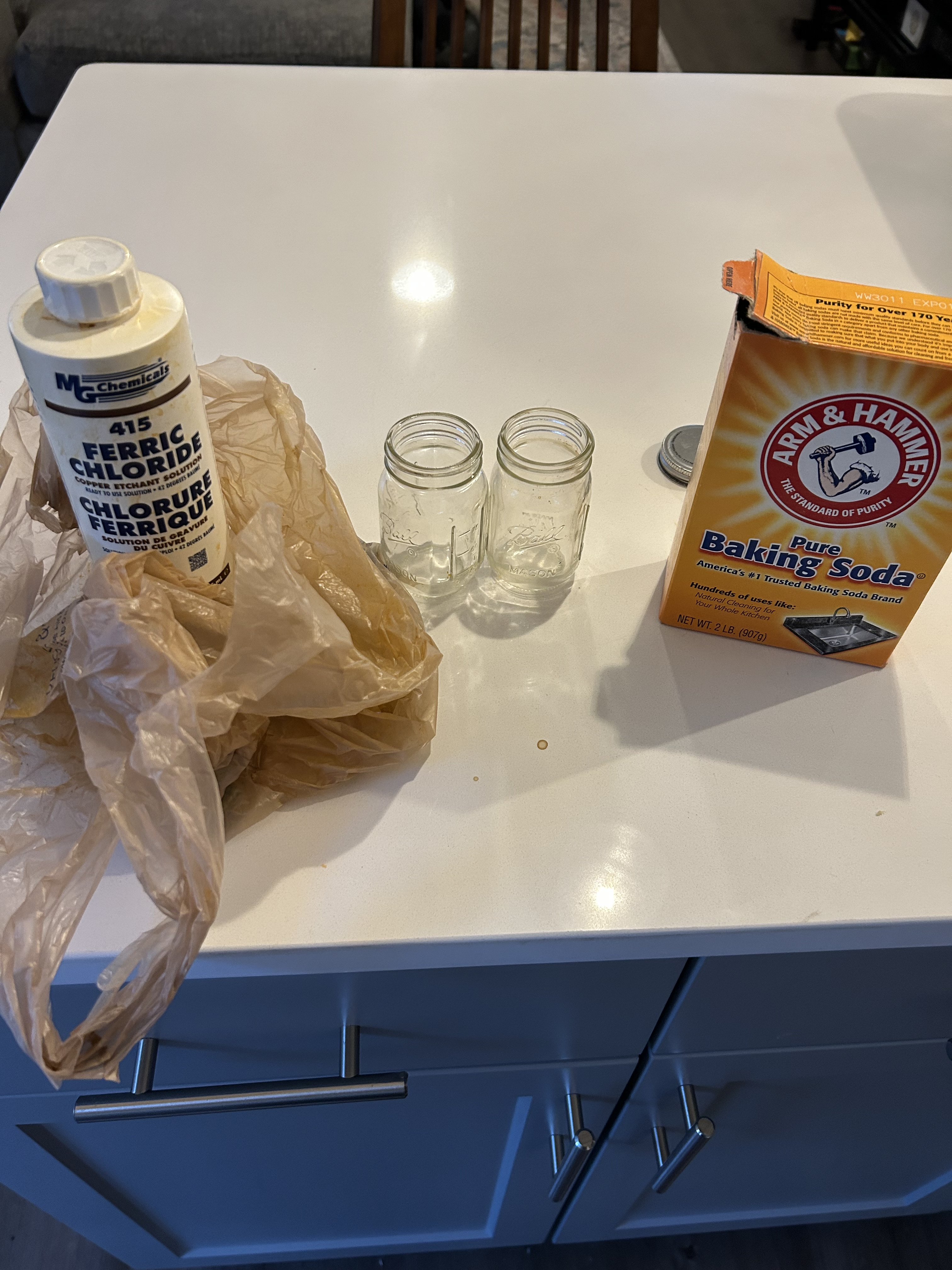
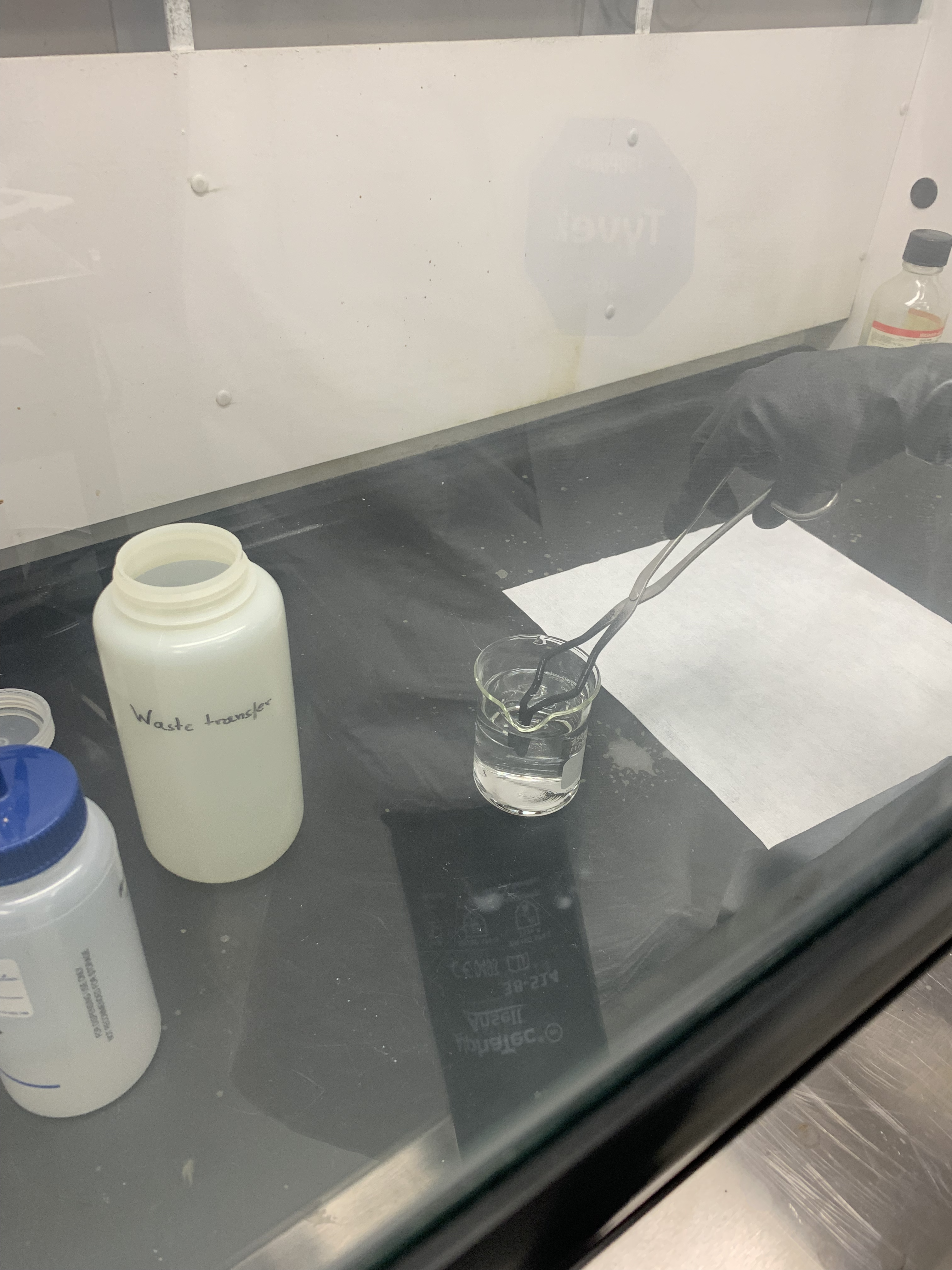
In order to bring out the beautiful patterns of the ring, we need to etch them. The patterns formed in the damascus are from two different types of steel. One steel has a higher carbon content than the other. When the ring is emerged into the acid, the acid eats away the carbon content in one steel while leaving the other relatively unscathed.
Take caution while doing this step and make sure you are in a well-ventilated area and wearing latex gloves.
Step 1: Prepare the Etching Solution:
- Create the etching solution by mixing ferric chloride acid with distilled water using a 50/50 ratio. Always add the acid after you add the water.
- You also want to create a mixture of baking soda and water to help get rid of the acid after the etch.
Step 3: Clean the Ring Surface:
- Thoroughly clean the surface of the stainless steel Damascus ring to remove any dust, oils, or residues that might interfere with the etching process. I used isopropyl alcohol for cleaning.
Step 5: Immerse the Ring in the Etching Solution:
- Carefully lower the ring into the prepared etching solution. Make sure the ring is fully submerged and that the solution covers the entire surface that you want to etch. I dangled the ring with a steel wire to keep it evenly surrounded by the acid.
Step 6: Monitor the Etching Process:
- Keep a close eye on the ring as it etches. Shake the ring around to try to remove any bubbles that may form on the ring. I kept the ring in for 15 minutes at a time.
Step 7: Remove the Ring and Neutralize the Acid:
- Once the desired level of etching is achieved, carefully remove the ring from the etching solution. Immediately rinse the ring with water to stop the etching action. After rinsing, neutralize any residual acid by soaking the ring in the baking soda solution.
Step 8: Repeat!
- If the etch does not look deep enough or you can't feel the etch with your fingernail, I would repeat steps 5-7.
- I ended up repeating the etches 2-3 times.
Polish
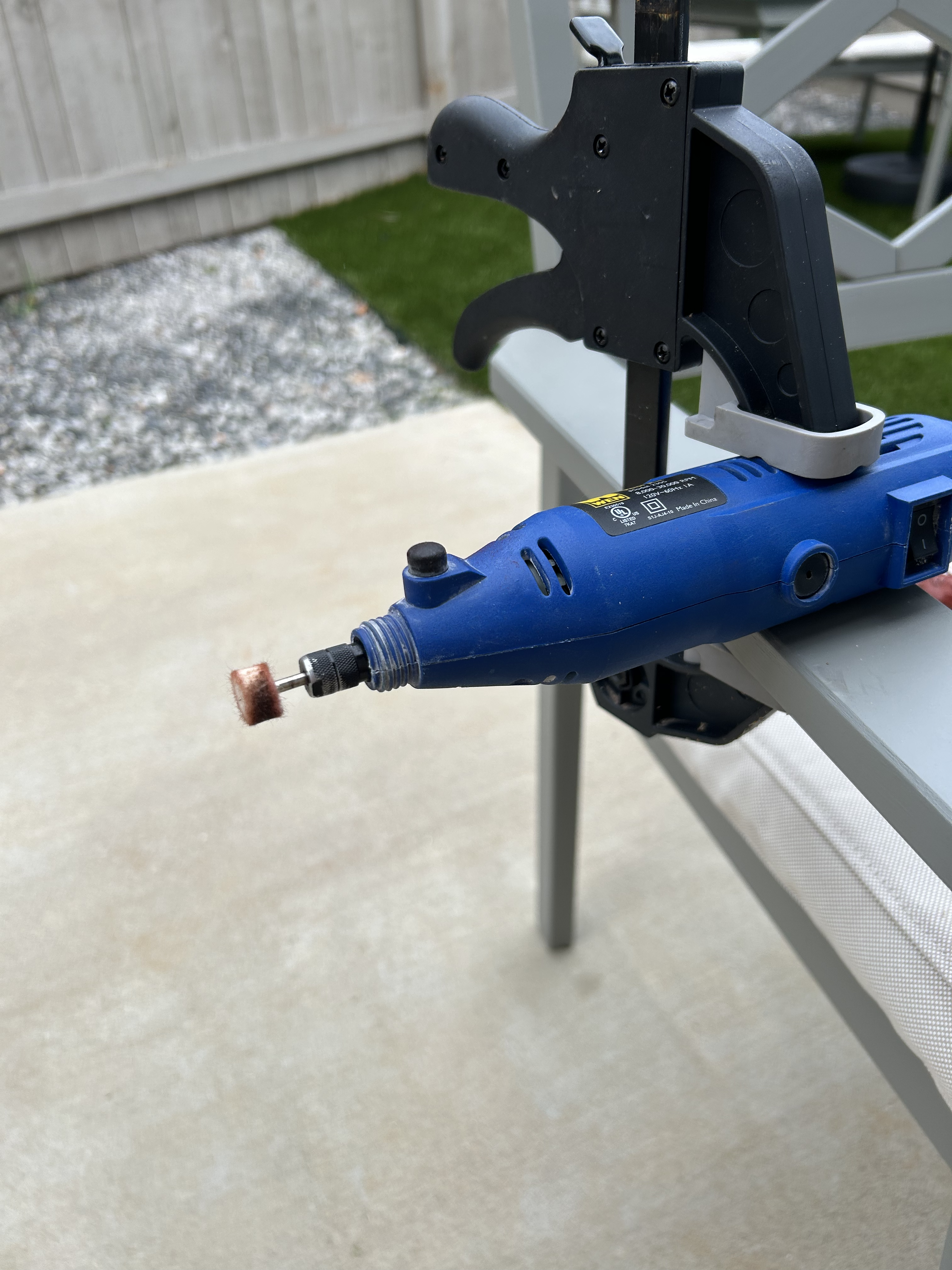
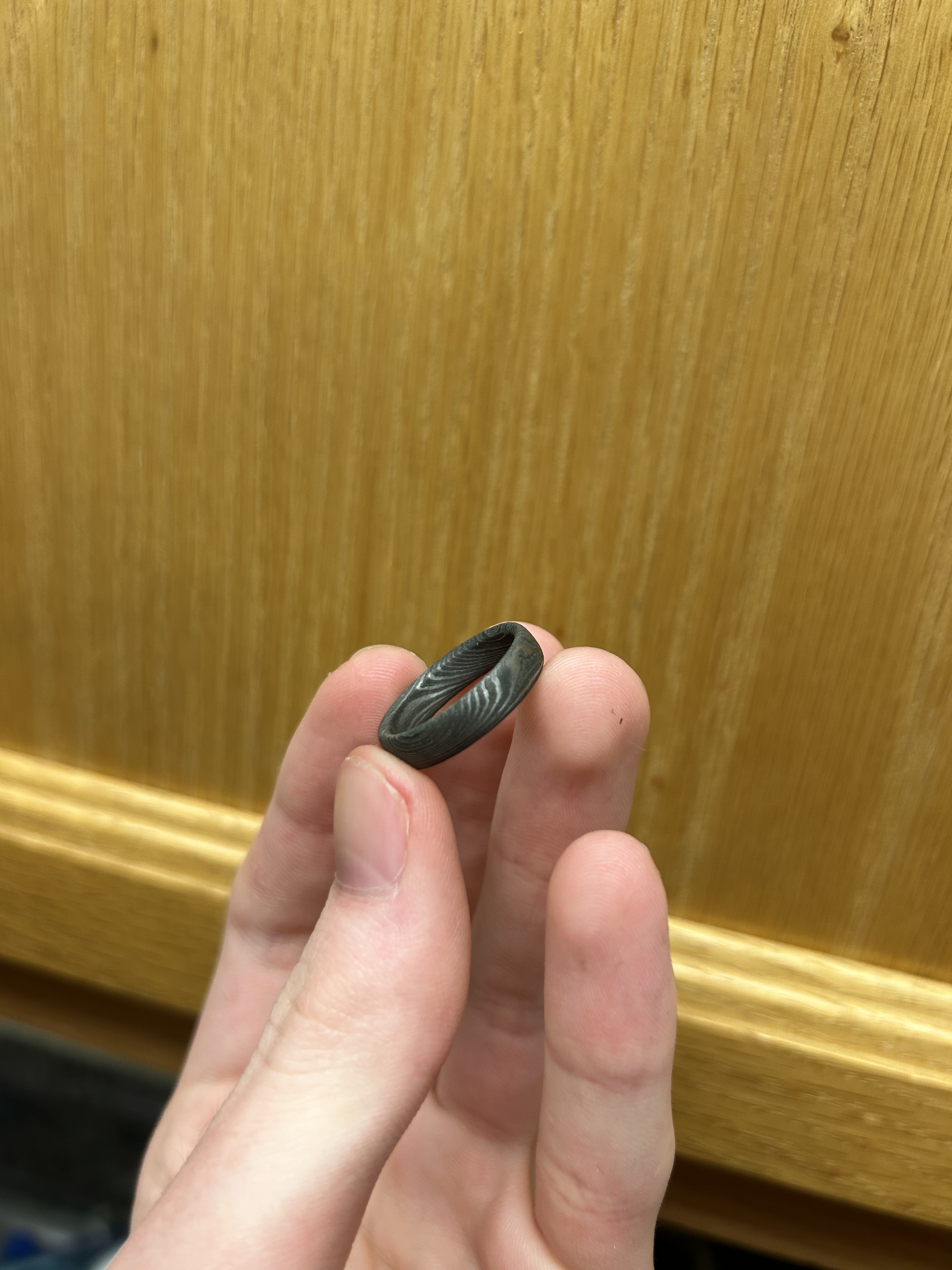
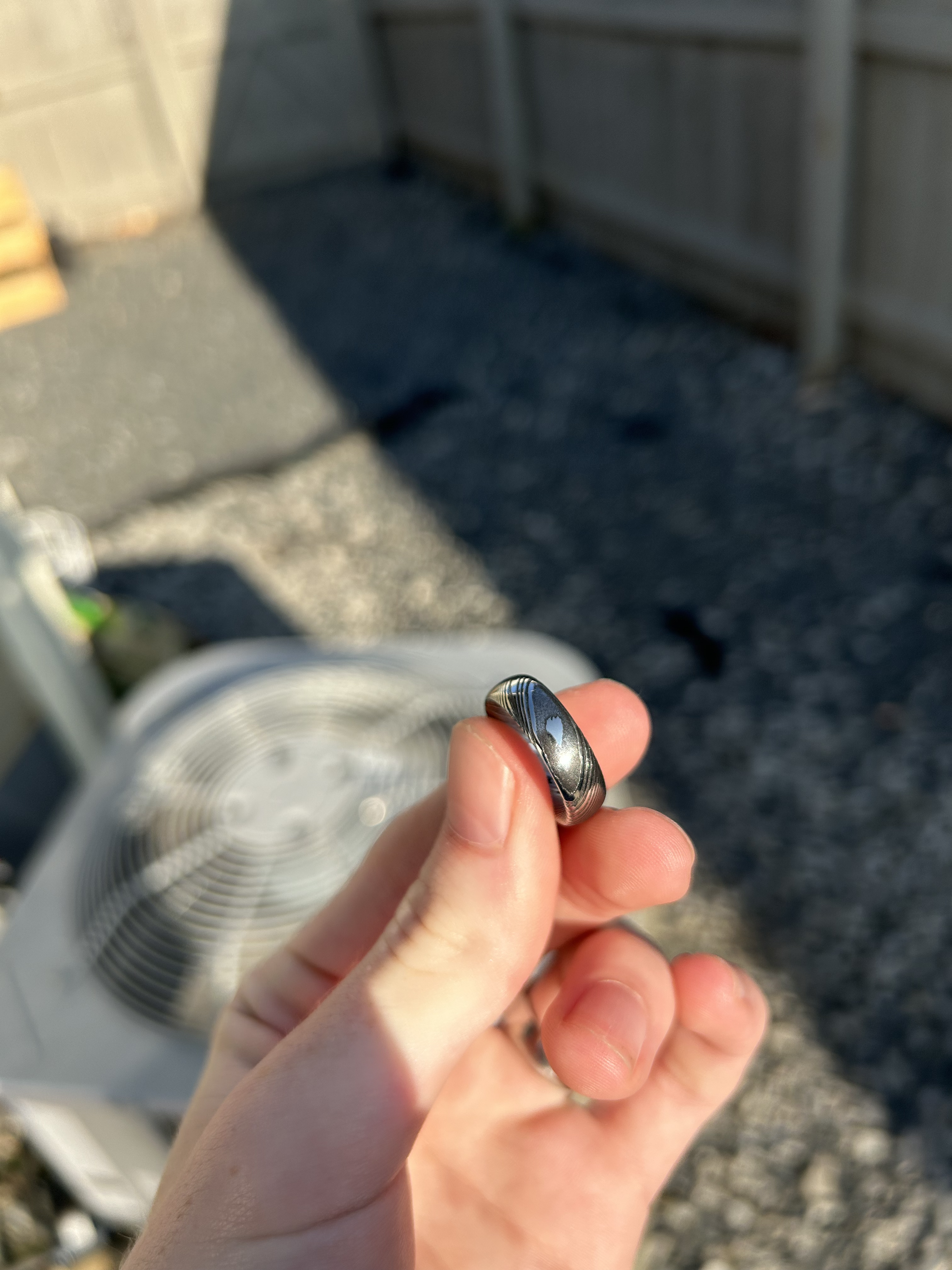
Polish is a great way to take your piece to the next level. The finish after the etch feels like sandpaper and may not be comfortable to wear. Polishing the ring brings it to a beautiful smooth and shiny finish. The finished product looks like a museum piece!
Step 1: Gather Polishing Supplies:
- Before you begin polishing, gather the necessary supplies. You'll need a cloth, polishing compounds, and a rotary tool with appropriate polishing attachments.
- Mounting the rotary tool to a surface will give you better control of your polish.
Step 2: Clean the Ring:
- Ensure the ring is clean and free from any dust or debris. If needed, wash the ring with mild soap and water, and dry it thoroughly before proceeding with polishing.
Step 3: Select the Polishing Compound:
- Choose a suitable polishing compound for stainless steel. Polishing compounds come in various grits, so start with a medium or fine-grit compound for initial polishing.
Step 4: Apply Polishing Compound:
- Turn on the rotary tool and then dab a small amount of the polishing compound onto the polishing wheel.
Step 5: Begin Polishing:
- Set the tool to a low or medium speed to avoid overheating the metal. Carefully polish the ring's surface, applying light pressure and moving the ring in a circular motion around the polishing head.
Step 6: Regularly Check Progress:
- As you polish, periodically stop and check the ring's progress. The stainless steel Damascus should start to reveal its shine and patterns more prominently as you continue polishing.
Step 7: Remove Excess Polish:
- After polishing, wipe off any excess polishing compound from the ring's surface using a clean and dry section of the polishing cloth.
Apply Protective Finish (Optional)
If you are using a carbon steel damascus ring you may want to protect the ring better from rust. You can do this by spraying a clear coat of enamel, lacquer, or a metal protective film. I don't have much experience with using a film, but it could be a great way to protect your jewelry!