Sketchup Tricks for 3D Printed Parts
by Downunder35m in Workshop > 3D Printing
6301 Views, 119 Favorites, 0 Comments
Sketchup Tricks for 3D Printed Parts
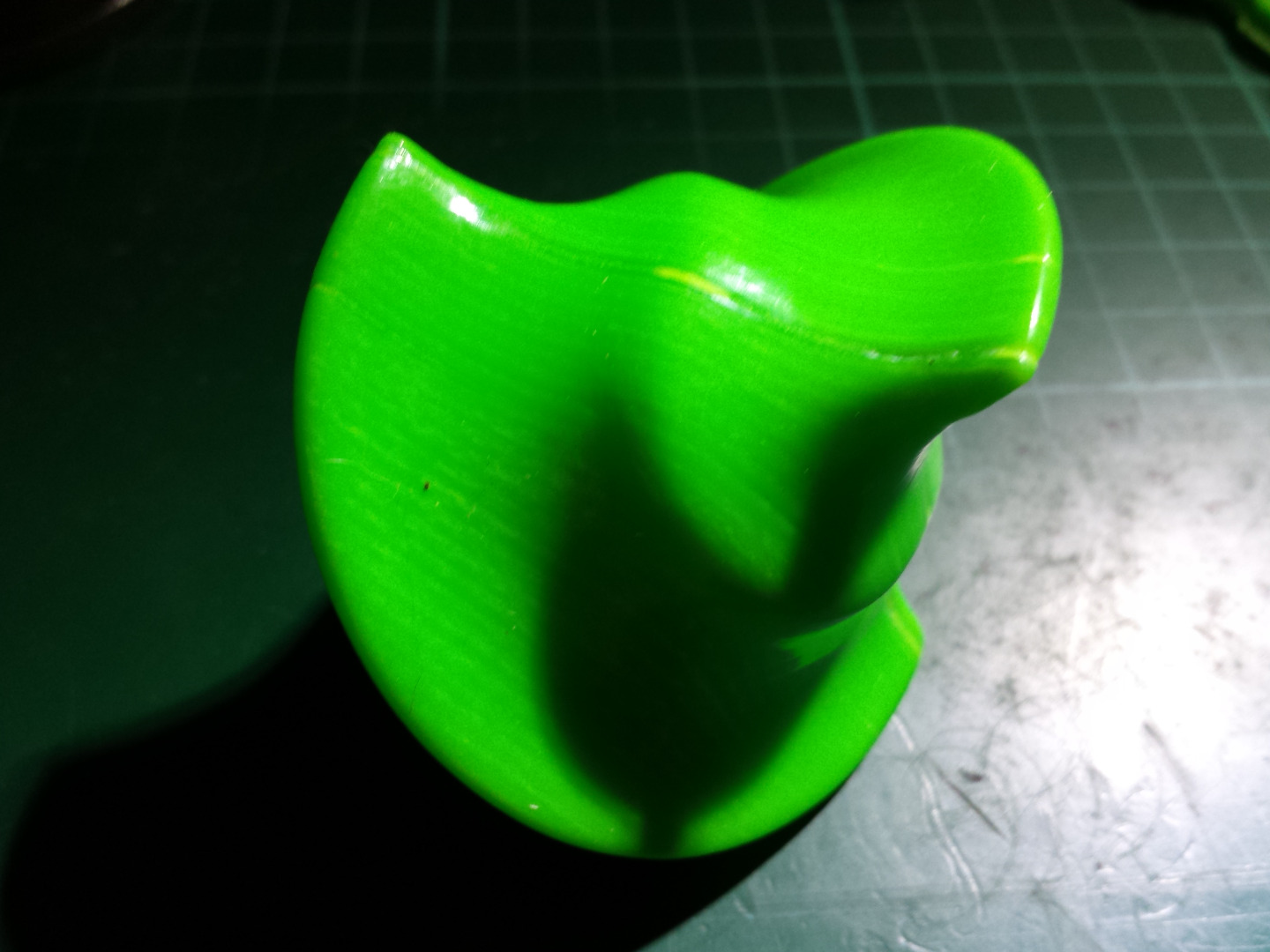
Update 27/06/2015: New video for cutting holes and removing bits.
Update 26/06/2015: Added some videos, one on the Align tool, the other for creating a mould from a 3D part.
Update 24/06/2015: Due to the massive interest in this Instructable I will add more tipps in the future as I find them.
For today I added a step that shows how to design or change your models to prevent lift off from the print bed.
There are several good programs to create your 3D models, some prefer Blender, others use more professional tools from the Autodesk range or even just 123D Design.
They all, including Sketchup have their good and bad features and today I will try you to overcome some of the following problems when using Sketchup:
* Objects created to be solids when finnished so there are no holes, twisted surfaces and so on.
* Creating proper half sections or cut parts for prints.
* Using the Follow Me Tool properly.
* Making use of the Scale function to get better looking objects.
* Using some good and free plugins to make life so much easier.
I will use the Sphericon I already posted in the Instructable of one of the contest entries.
3D-Printing-a-Transparent-Sphericon
Creating one like this seems to be easy enough until you encounter the stubborn problems within Sketchup.
So it is time to share how do something like this the "easy way".
Skill level is for anybody familiar with the basic use of Sketchup.
"Tools" You Will Need for This Instructable
1. Sketchup, I use the Pro version but the standard should do as well.
2. Some plugins:
Align Plugin for Sketchup
Solid Inspector
STL import export
3. Patience ;)
Let's Do It!
We start Sketchup (SU) with a blank page.
Settings should be in mm.
Warning note:
Whenever possible use the scroll wheel on your mouse to zoom into the object when placing something.
Whenever working in a single pane switch the cam to that view, like in our case the front view, and use only the hand tool and zoom to move around but do not tilt or pan around.
Most wrong alignments result in the user not using fixed cam views ;)
Also not how the color of points and lines change when you match something - this is extremely helpful.
As we want to create a Sphericon, there are several ways of doing so.
But I will try to do in a way that can be used for other models as well, so you can learn how to create complicated objects without having them partially destroyed while trying to fix the STL file.
The thoughts behind it:
When creating a 3D model in SU you will encounter certain limits with the tools sooner or later.
One of the worst is the Follow Me Tool when using it on relatively small objects with a lot of rounded shapes.
In many cases you end up with something that is incomplete, has not followed the set path properly or came out totally unexpeted.
I did spent quiete a few hours close to operator meltdown until I found a way out.
Same problem when you need to match an object onto another.
Not only do you fight with 3 dimensions during the placement but further more it is next to impossible to get a part exactly where you want it - that is where the align plugin comes in handy.
Last but not least we all created nice looking models that contained thausands of errors, most of the time an online service or Netfabb can repair them, but sometimes they still refuse to print.
And if you ever tried to create two halfs from one object so it can be printed better you know how hard it can be to really match the parts.
What is a Spericon and why do we make one now?
I won't go into the details, check Wiki or the nice Instructable linked on the first page for it.
We make one as it a nice toy and to show how to use the tools I mentioned.
Starting with a sqare...
As we need an extruded shape and don't want to spend hours creating it we start with a square.
Change to front view and create a box of 30 by 30mm.
You can use the mouse to get the sie right but I find it easier to type 30;30 into the littly box in bottom right corner ;)
Start from the coordinate center and create the box to the right
It should look like this now:
Next we create two guide points on the red X axis for later use.
Start from the coordinate center and move with the measuring tool to the right,
enter 75 into the little box.
Do the same to the left and it looks like this:
(notice the two "dots" on the red line!)
Now we start to create our cut out parts so we get a nice looking Sphericon.
First some lines and half circles, the half circles are set to 3mm long and 1.5mm for the diameter.
Next we draw two circles, one of 5mm radius, the other of 3mm radius as shown.
The big one start from the center, the small one where the diagonal line meets the big circle.
Next step is to create an arch.
For this we create two guidelines at an angle of 25° away from the center diagonal line.
Where the guidelines meet the small circle is our first point of attachment, the second where the circle in the corner meets the other diagonal line.
Not in the above pic how the color for the arch changed!
This indicates it is tangient to to the circles, meaning you have no bumps or corners.
Repeat the process on the other side of the small circle to connect the circle in the bottom right the same way.
As we only need the outer, rounded shape it is time to remove all lines we don't need.
When done it should look like this and gives us the extrusion profile:
Of course being a Sphericon we need this profile twice so we can create the right sphere.
So first we copy our shape, then we use the align tool to get them together in the right place.
First order of action is to select the center point of the movement on the part we want to move.
Notice the green dot?
We use the copy part as we want to keep the original in the center of the coordinate system.
Next step is select the orientation.
X and Y.
For X we use the lower edge of our copied part, for Y the one going up on the Y axis.
As you can see the orientation for the remaining axis is done automatically.
To place our part correctly we must now define the same points in the original part to the left.
And we use the same points, so starting in the bottom left corner for the origin and along the X-axis of the part for the X axis direction.
But as we want out part to be mirrored the Z-Axis doe not go up on the part but down on the coordinate system - note the littly dot!
Ok, what have we done with this tool?
We marked to orientation and position of what we want to move and where we want to move it to :)
You can pa around and check but the parts should be sitting perfectly on the red line with no gap.
If there is a wrong alignment undo and start over, it is quite easy to miss the correct spot on the axis when using a tilted view.
Now we can remove the line on the X axis to get a single object - note that we still have not grouped anything !
Notice that the bottom part has a grey color? This means the surface is flipped, the back is the front.
We correct that by a right click on the selected surface and filp it with the menu function.
It can happen that the surface disappears when you delete the center line, if so simply undo and draw a little line vertically across the existing ones where they meet the center line.
After that you can delete the center line and still have a solid surface.
Next I will show you the limits of the follow me tool.
The easiest would now to draw a half circle and to extrude the shape we have along the half circle.
If we do this is the result:
As you can see it does not look round like a church bell as you might have expexted and the top seems to be missing too.
But if we use the measuring tool to scale our model up from 30mm to 3000mm the follow me tool gives a much better result:
Problem is that complicated shapes can't be simplyfied enough for the tool, so upscaling helps.
It might look like the program is frozen, that is normal as it takes some time to calculate all.
We no do the same with the bottom half to get what we need.
Tipp:
Delete the surface of the path you want to follow and mark the line before using the Follow me tool.
That way you only need to click on the surface you want to extrude and don't need to delete the resulting surface of the half circle when the extrusion is done.
It might be necessary to some repairs before we finally flip the part over for printing.
For example check the inside if there is a surface left from the half circle, sometimes Sketchup still draws the extruded part as a solid.
Also the top and bottom cones will need some attention.
But before you now jump at it calm down as the entire part we created is useless for 3D printing.
Just another hickup caused by the limits of the follow me tool :(
If you check the below sideview pic carefully you will notice we did not create a true half circle with the extruded part.
Exporting and printing like this would mean the flat surface is not flat at all and our part would be useless.
But not all is lost, simply undo till you are back to the mirrored part we had before we started with the half circle.
Now we draw a full circle instead!
Be aware that the fake freezing of Sketchup might be longer now ;)
And make sure to delete the surface of the circle before using the follow me tool.
In return we get a nice "flying saucer" that does not even have the top and bottom imperfections we had when using the half circle.
Nice, but now you will wonder how we can slice that in half to get the part we can print out...
Remember the two guide points we created earlier and that are still visible?
In the pic you can see the model is grey again, so we select it and flip the surface to make it white before proceeding.
We now select the entire model and group it before we draw a big box using our guide points, or two boxes to be precise that will be combined into one.
But just to be sure our model is really a solid we use the Solid Inspector on the selected model.
That is what we expect to see here, if you see something with a lot of errors or it takes forever to finnish you had flipped surfaces or did not group the model.
Now we use our guide points to create a box that covers exactly one half of your object:
Group this box so we can use it as our cutting tool.
To do so we select both groups (hold CRTL and click on the second).
Now select the intersect tool from the menu or use the icon.
After quite some calculating you have now three objects.
The box with the missing piece and two halfs of our Sphericon.
As we used the guide points we created on the X axis we can be sure to have a perfect cut where we want it.
On the block in the background you can see how it is now a mold formed by the part we cut out.
We remove all parts but the one in the center of the coordinate system and flip it so it sits flat on the X and Y axis.
Again w use the align tool as before but this time select the coordinate axis for the second reference instead using them on a part.
Of course if you have access to a DLP printer and want the entire thing in one pice you turn and join them with the align tool and after that combine them into a group.
That's it ;)
Prints Lifting From the Bed...
If there is one thing we all hate then it would be a big print being wasted once the part starts to lift off the build platform....
Even users with hated beds complain that certain structures almost always lift more or less.
Especially long and thin parts and those printed fast with thick layers are problematic.
So why not include "lif-off-support" at the design stage?
What?
Yes, I know, sounds terrible and sounds even more complicated - but it is not :)
First I will try to explain:
When you already know that corners or thin areas (in x-y) tend to lift off and you know how to use Sketchup (or any other 3D modeller) you can fix that.
Slicers offer a brim option that is meant to help with the lift off, we do the same but a bit thicker and with more attention to details.
We design our testobject so we can be almost certain there won't be too much lift off anymore and I will show you how.
For the ease of following the next bit:
All measurements are in mm but it does not really matter once you got the pic ;)
Let's start with a simple cross, 100 x 100 and 20 high:
Could be a connector, measuring tool or whatever.
But if you print this like it is (especially using ABS) there is a big chance the outer ends will lift off and the print starts to peel.
So we create a few little boxes around our corners that are just 1mm high, or for bigger parts go higher if you don't mind the extra work.
You want to have a good balance between the thickness of these extra squares and your top / bottom solid fills.
Perfect would be to match the thickness to the sum of both.
Eg.: Printing with 0.1mm layer height and 3 bottom, 5 top layers.
If the first layer also has 0.1mm this makes 9 layers at 0.9mm all up.
So use 0.9mm for the height of the extra squares ;)
For better looks and a bit more holding power a round shape can be used as well, I will do that to show you how it should look.
Quite easy to do too:
Using the bottom view select the center of the short line with the circle tool, I used the section tool.
Now go along one of the long lines until you get a radius of about 20mm - does not have to be a perfect measurement but you have to select a point on the line.
Drag around the the top to the other line and connect the end of the circle.
Pull it up 0.9mm and done ;)
If you don't want to "ruin" your existing models that way simply save the finnished model with a meaningful filename.
Like instead of "100mm cross" as the original name it 100mm cross liftoff".
When editing existing files for this always make sure to ungroup your model first as otherwise you might just create a nested entity.
For the ease of cleaning the part you can add a gap around the object down to just 2 layers, but if done correctly you will only have a solid structure attached that should be quite easy to cut off clean.
But it is important to check that the extra liftoff pads will be printed as a solid, otherwise the outer perimeter of your part will be interrupted by an infill which leaves open bits on your part.
Cutting Holes Through Objects When Push/pull Refuses to Work
If you ever tried to create some more complex structures you will have encountered the problem of creating holes thorugh areas that also have a void in the path.
One of the big limits the push pull tool has is cutting through voids or intersecting surfaces.
There is no way to tell the tool you actually want a hole everywhere.
So a hole is cut into a surface but a solid will continue in a void.
In some case this does not matter too much as you can substitute guidlines to create the same shape on both sides of your object.
You then simply push the hole from both side indepently.
But if there is another wall at a different angle in the path it will require some cleanup work.
For parts created within Sketchup this is usually not too bad but doing so on imported STL files will be quite frustrating.
We can substitude here by using the Volume tools and creating an object that will be removed from our part - similar to the mold making exercise.
In the video I will again show some possible hurdles and how to avoid them for a better and easier result.
Please always pay attention to the editing mode!
There are three ways you are able to create and work on objects.
1. Nothing is selected - it is like drawing on a blank sheet.
It does not matter what or where you draw it will not interact with an existing part on the screen.
This mode is good to create new objects, group objects by double clicking, selecting things and so on.
You can identify this mode as there will be no boxes drawn around your objects and nothing is highlighted in blue.
2. Object highlighted blue.
In this mode you work with the entire object for cutting operations (volume tools), moving it, rotating, aligning and so on.
In most cases you will not do any editing on the object in this mode.
3. Object in not highlighted in blue but with a dotted balc box around it.
In this mode you work on the object for editing.
Changes on a surface or line will include the entire object, so push/ pull, deleting of lines and surfaces and so on are all done in this mode!
Again for the volume tools you want mode 2 instead.
4. Object highlighted in blue AND with a blue box around it.
In this mode you also see the outer dimensions of an object through the blue box.
It also includes guidelines included in the object, which sometimes can make the box bigger than the actual object.
In this mode you can do the same as in mode 2 but it also the mode for exporting an object as a STL file.
If you export without this selecting your object can be messed up or include all other objects still in the scene.
Please watch the video and play some of the exercises through to get a better understandig.
Additional Tips and Infos
The method I used with the scaling and box cutting is a woraround for problems that should not exists.
There are other plugins available that can do more but at a price of money.
If you work with simple shapes you won't need to upscale but be aware that if something does not work as accrate as you like or not all, upscaling can help in many cases where detail is required.
The Follow Me Tool is powerful but also temperamental.
Pre-selecting the path and deleting the surface within it usually makes life much easier.
Also I prefer to select a line, like the circle, instead of using a surface for the path as the results can be surprising to say the least.
Solid Inspector is a tool you should not need if the parts are designed correctly.
Before using it make sure you checked the model from all sides for flipped surfaces (grey instead of white), holes or unwanted lines.
Do not trust the tool to do all the work for if you require perfect results!
You can circle through errors found to manually inspect and correct them - make use of it before asking the tool to do it for you.
Endless lists of errors here mean you did something seriously wrong with your part - again check for holes and flipped surfaces!
If you are unable to find the errors manually save your work before using the tool to fix it.
Sometimes the program crashes and without autosave you might loose your progress.
Netfabb offers a great online fixing for STL files with really good results but it should be the last way out.
It is always best to have a good model to work with instead of a bad one with a STL export that was repaired.
When creating molds with the volume tools it is easier to include all vents and risers and to group them with the part before creating seperate parts.
Especially future wax molds benefit from having these things included at a fine detail level instead of adding them manually to the wax once finninshed.
Please use the scaling functions when casting in aluminium to get the part 1 or 2% bigger than designed to allow for shrinking and sanding / cleanup.
For time and CPU consuming task it can be helpful to have the Windows Task manager up and running.
As long as you can see either the CPU or memory usage slightly fluctuating you can be certain Sketchup has not crashed.
Some operations with rounded parts take a long time and use a lot of ressources, so if in doubt make a coffee and be patient ;)
Whenever possible with upscaled parts you need to work with, try to scale them back to the original size.
For example when cutting out one part from another size does matter if one or both parts have a lot of curved surfaces.
In some cases it might best to use Netfabb ot Meshlab to reduce the face count on a model.
Unless you need highly precise parts it does not matter if a 3mm circle is made up from 24 or 96 lines - but it does matter for calculations on the parts.
Update 23/08/2015: Volume operations
With my Repulsine project I noticed a massive flaw in Sketchup.
If you try to use the volume tools on too complicated objects it will fail and often the program crashes.
I am not talking about basic geometric shapes that you combined to some sort of sculpture, I am talking about objects with a lot of curved surfaces here.
There are some settings that can ruin this prcess too, for example the auto save - if it tries to save your file during such volume opreations Sketchup often crashes. So disable it and save manually if you encounter this.
Also Sketchup loves to do automatic checks of your files, the so called validation check.
This goes so as ruining an entire model when you try to save it.
What happens is that after you save the file the screen version will be updated to this saved version.
If you see that you model changed in terms of getting spikes or having missing surfaces you have to use the undo function to get your model back.
In some cases the only way to save the model sucessfully is to complete all outstanding repair works with the Solid Inspector first. If Solid Inspector gives the all clear the object will not be ruined during the saving operation.
Quite often, after designing a complex part Solid Inspector claims it is all shiny but the volume tools still claim you don't have a solid.
This is usually caused by another group within your group or component!
Easiest way to fix is to explode the model, check again for other groups within it and explode them too.
If there is no other group you can group the object again and in most cases it will be recognised as a solid now.
For complex operations never assume Sketchup has crashed!
Check the task manager and you will see it is still working.
Long delays when using the volume tools are normal with curved shapes and the more complex the part is the longer it will take.
Last but not least, repair works....
After using the volume tools, especially the subtract function, you have to check the model for errors and fix them.
You will be tempted sometimes to use external tools on the exported STL file - DO NOT DO THIS!
Sketchup will not handle complex STL files well and in many cases the resulting file is not longer a perfect match to parts that require a perfect fit.
Although it can be very time consuming doing the repair fully within Sketchup is the best option.
Everything else results in files that might be still perfect for printing but useless for further volume tool operations.
And again: If the tools only produce useless results try to upscale your model by a factor of 100 or even 1000.
Video Tutorials
My intention is not create the perfect tutorial, so will see all my errors, wrong ways of doing things and so on.
Most of the things you see are on purpose to show common downfalls as I experienced them while learning how to use the program.
You might also find a typo or two in the explaining text.
If do find one feel free to keep it for private use, using it to make money from the typo would make me ask for a fair share ;)
First up the Align Tool and rotating objects:
The next about making a mold, at least the basic steps required.
You still have to make some guide holes vents and so on, but for the actual creation of the negative in two blocks it fine.
All else is normal Sketchup work anyway;)
The second part can be skipped as it mainly shows problem when you forget to ungroup an object for editing.
But if some things never work for it might be fun to watch so you can avoid these mistakes that only cause frustration ;)
Here is the video to step 4.
It should show the most important steps for proper cuttings and pus / pull operations.