Power Drill to Belt Sander Conversion
by 24Eng in Workshop > 3D Printing
29094 Views, 391 Favorites, 0 Comments
Power Drill to Belt Sander Conversion




Some people spend a lot of money on a 3D printer then don't have money for other tools. I did that. I wanted a 1" (25mm) wide belt sander but it wasn't in the budget. Instead of admitting defeat, I decided to make parts for my own belt sander.
Creating the project with only 3D printed parts would have been possible but the filament would have gotten expensive. Instead, I wanted to combine the benefits of inexpensive steel hardware store parts with a printable design. Everything was printed in regular ABS so it's not necessary to track down a rare filament.
Here's what you'll need.
Materials:
- Two angle brackets at least 2" (50mm) long
- 6' of 5/16" threaded rod
OR
- 2m of 8mm threaded rod
- Steel spacers to match threaded rod
- Washers to match threaded rod
- Nuts to match threaded rod
- All-metal lock nuts to match threaded rod
- Six 608ZZ bearings, these are the kind used in skate equipment
- Wing nuts to match threaded rod (optional but nice)
Of course, you'll need a hand tools, a power drill and a 3D printer, or access to one. Your power drill won't need any modifications so you'll still be able to use it as a drill tomorrow.
3D Printing Files



That first image is animated if you want to see what the parts look like all around.
All the STL files can be downloaded right here. If you have a large print bed, download the file "Belt Sander All Parts.stl" otherwise download the other two STL files. In fact, you could download just "Belt Sander Parts Half1.stl" print it, then print the mirror image and you'd have all the parts you need. Neat huh?
Please print the pieces with high infill. The third picture shows the hazard of printing with only 10% infill, the pieces are too weak to withstand a tripping accident.
Advanced users. You may also notice that there is a text file called "Belt Sander.scad" This is the OpenSCAD file I used to model the parts. If you want to make changes, you're welcome to my source code.
Pulley Assembly




There are three pulleys in the project. Two of them have sockets for bearings and they should be paired with the pieces that attach perpendicular threaded rods. The first picture shows the pulleys with the perpendicular pieces but there should be steel spacers between the pieces and the bearings.
The third pulley accepts a threaded rod should be held firmly in place with all-metal lock nuts. It may be necessary to use a long socket to tighten these together. One side of the threaded rod should be long enough for a spacer, bearing and a lock nut. The other side should be that long plus another 6" (15cm) or more. This is where the drill will attach. This pulley should also be given rubber bands. It is not vital to find the exact bands shown in the picture, doubling up an ordinary rubber band should suffice.
Drive Plate Assembly



Four threaded rod segments should be cut to 12" (30cm) each.
The angle braces should have their outermost holes drilled to 5/16" or 8mm.
Follow the example in the second and third pictures to see how the threaded rods and angle braces should be arranged in the printed drive plate. The nuts touching the angle braces should be tightened down as much as possible.
Now is also a good time to insert the bearings into the drive plate.
Final Assembly



It is time to put it all together.
The drive shaft should be assembled first. Spacers go on the threaded rod, one touching each of the nuts. From there the drive plates can be affixed by pushing the threaded rods through the bearings. The idea is that when the drive shaft is spun everything touching it should be stationary to the shaft.
Loop the belt around each pulley before placing them on the threaded rod and have nuts in place to keep the pulleys stationary. This is where wing nuts come in handy.
Operating





Attach a power drill to the drive shaft that sticks out.
It's possible to operate the sander without a bench, just hold something that's not moving and engage the drill with your other hand.
If you plan to use it as a desktop sander, it may be necessary to insert some of the threaded rods into a drilled piece of wood. This just props up one end so the belt doesn't wreck your work surface. It doesn't hurt to clamp this to your work surface.
Check out the video to see it running.
Use a clamp to hold the drill in place. Depending on the type of drill, it may be necessary to prop up the sander on a piece of scrap wood.
It's that simple.
About Me
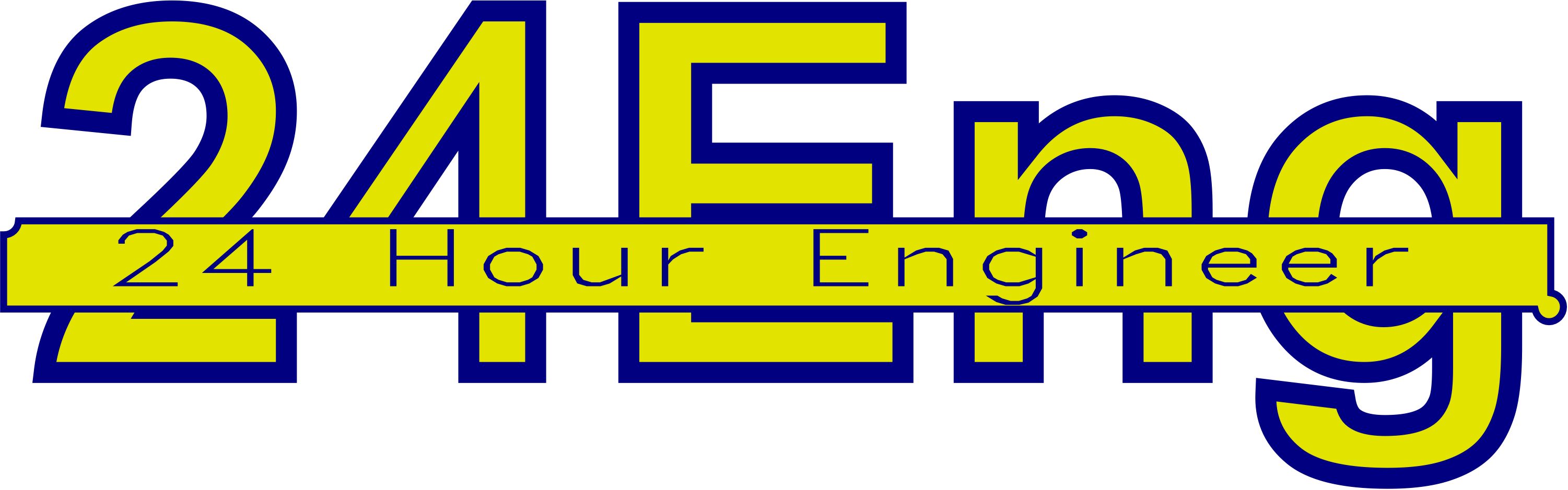
Thank you for reading. I write incessantly at my blog, 24HourEngineer.com
You can find this project there including the times I messed up. Remember those metal spacers? I didn't have them for the first run and accidentally friction welded a pulley to the drive plate. There are some projects with 3D printers and some without. There are some projects with programming and some without. There are some projects with only simple tools and some without. All of them have lots of pictures, even the parts I mess up.