Nerf Modding 101: Alpha Trooper CS-18
by SnakesOfDeath in Outside > Launchers
110463 Views, 33 Favorites, 0 Comments
Nerf Modding 101: Alpha Trooper CS-18

Today I am going the show you how to do basic all-around beginner--intermediate modifications in the Nerf Alpha Trooper CS-18
Warning: If performed incorrectly, modifications can reduce performance or render the blaster inoperable. When performing even basic mods, there is always a risk of losing parts, cracking plastic, or not being able to re-assemble the blaster. Some of the more common blasters' internal pictures can be found online, and it is worthwhile to use these as references.
When performing cosmetic mods, care must be taken in order to not lock up any moving parts. Without a few layers of a hard clear coat, paint can gum up areas where plastic slides on plastic. For more complex mods like barrel replacement and fabrication of sealed breech, you must take into consideration the volume of the plunger tube in relation to the barrel length, and spring power must also be increased. So make sure you know what you are getting yourself into before you start a mod.
Credit for and information in this 'ible was originally created, published, and copyrighted by Orange Mod Works™
Warning: If performed incorrectly, modifications can reduce performance or render the blaster inoperable. When performing even basic mods, there is always a risk of losing parts, cracking plastic, or not being able to re-assemble the blaster. Some of the more common blasters' internal pictures can be found online, and it is worthwhile to use these as references.
When performing cosmetic mods, care must be taken in order to not lock up any moving parts. Without a few layers of a hard clear coat, paint can gum up areas where plastic slides on plastic. For more complex mods like barrel replacement and fabrication of sealed breech, you must take into consideration the volume of the plunger tube in relation to the barrel length, and spring power must also be increased. So make sure you know what you are getting yourself into before you start a mod.
Credit for and information in this 'ible was originally created, published, and copyrighted by Orange Mod Works™
In the first part of this 'ible I will show you how to do some mods for beginner modders, people who are doing something like this for the first time.
What is a Mod?
A modification or “mod” is anything you do to your blaster that changes its looks, form, or functionality. Doing a custom paint job, adding your own accessories and parts, and working on the internals to increase power are all considered mods.
Why Mod?
There are a plethora of reasons to mod a blaster:
• A modded blaster is a great addition to a costume.
• A blaster that you mod becomes your own work of art.
• A modded blaster can shoot further and with more intensity compared to FOF (fresh out of factory) blasters. It can give you the upper hand in your next battle.
• Cosmetic modding, when done right, yields stunning results. A humble foam blaster can become anything from a dystopian “steampunk” gun to a clean cut weapon right out of science fiction. They can even mimic weapons out of video games and movies.
Regardless of the reason, modding is an incredibly fun hobby that creates custom works of art out of average foam blasters.
What is a Mod?
A modification or “mod” is anything you do to your blaster that changes its looks, form, or functionality. Doing a custom paint job, adding your own accessories and parts, and working on the internals to increase power are all considered mods.
Why Mod?
There are a plethora of reasons to mod a blaster:
• A modded blaster is a great addition to a costume.
• A blaster that you mod becomes your own work of art.
• A modded blaster can shoot further and with more intensity compared to FOF (fresh out of factory) blasters. It can give you the upper hand in your next battle.
• Cosmetic modding, when done right, yields stunning results. A humble foam blaster can become anything from a dystopian “steampunk” gun to a clean cut weapon right out of science fiction. They can even mimic weapons out of video games and movies.
Regardless of the reason, modding is an incredibly fun hobby that creates custom works of art out of average foam blasters.
Chapter 1: Opening the Blaster







It is important to be familiar with your blaster’s internal structure in order to carry out any performance-related mods. Be sure to remember that there is often a variety of screw sizes in your blaster, so keep track of which screws go where. Make sure no small springs shoot out when the blaster is opened. The blaster should be unloaded with the mainspring relaxed. Try to avoid opening the blaster when it is in the cocked position, as it can shoot out the back of the blaster and cause injury.
Supplies Needed:
• #1 Phillips Head Screwdriver
• Small Flat Head Screwdriver
Step 1: Set Blaster on a clear workspace with the screws facing you. (Pic. 1)
Step 2: Remove screws. Be sure to make note of each screw's placement, because sizes differ. It is helpful to place the screws on the table in their original positions relevant to an outline of the blaster. Refer to the above picture for visible screw locations; hidden screws are shown below.
Note that there are four screws hidden under the slide of the blaster, and must be removed after removing the handle. There are a total of 23 screws. (Pic. 2)
Step 3: Gently remove the rear cap of the blaster. Be sure you do not accidentally leave your blaster in cocked position, because the spring could shoot out and cause injury. (Pic. 3-4)
Step 4: At this point, the blaster should easily separate into two halves. If it appears to be sticking, double check to make sure that all the screws have been removed. If the issue continues, use a flat head screwdriver and gently pry around the seam until the blaster separates. (Pic. 5)
Step 5: Set the top half aside, and you should have something that looks like this (note: this AT has tape on the plunger tube and a lock removed already, stock can be seen in the close-up): (Pic. 6-7)
Supplies Needed:
• #1 Phillips Head Screwdriver
• Small Flat Head Screwdriver
Step 1: Set Blaster on a clear workspace with the screws facing you. (Pic. 1)
Step 2: Remove screws. Be sure to make note of each screw's placement, because sizes differ. It is helpful to place the screws on the table in their original positions relevant to an outline of the blaster. Refer to the above picture for visible screw locations; hidden screws are shown below.
Note that there are four screws hidden under the slide of the blaster, and must be removed after removing the handle. There are a total of 23 screws. (Pic. 2)
Step 3: Gently remove the rear cap of the blaster. Be sure you do not accidentally leave your blaster in cocked position, because the spring could shoot out and cause injury. (Pic. 3-4)
Step 4: At this point, the blaster should easily separate into two halves. If it appears to be sticking, double check to make sure that all the screws have been removed. If the issue continues, use a flat head screwdriver and gently pry around the seam until the blaster separates. (Pic. 5)
Step 5: Set the top half aside, and you should have something that looks like this (note: this AT has tape on the plunger tube and a lock removed already, stock can be seen in the close-up): (Pic. 6-7)
Chapter 2: Removing the Locks









Locks allow you to half-cock your blaster, and are there to ensure that the slide is racked to the most rearward position before trigger is pulled. The magazine lock prevents the magazine from being removed unless the slide is pulled all the way back Many modders prefer to remove these locks in order to control blaster function precisely to their liking. Locks are geared towards the safety of younger users, and may be left in if desired.
Supplies Needed:
• #1 Philips head screwdriver
• Knife/box cutter/Dremel (optional)
Step 1: Locate the trigger and magazine locks utilizing the close-up photo of the internals located in the previous step.
Step 2: Remove the screw holding in the trigger catch activator and remove the activator.
Step 3: Remove the trigger lock. Take care to keep the spring from shooting out during removal.
Step 4: To remove the magazine lock, the bolt sled and plunger/breach must be removed as well. Pull the mainspring out through the back of the gun, then remove the trigger catch. Then gently work the bolt sled and plunger assembly out of the blaster, maneuvering the bar connecting the bolt sled to the cocking handle through the internals of the blaster. The magazine lock can be removed from the assembly without disassembling the whole thing. Follow the pictures above to see how to do this. (Pic. 1-6)
Step 5 (optional): If you would like to keep the magazine lock in order to preserve the functionality of the jam door, but still remove your magazine whenever you like, a small bit of plastic at the bottom of the magazine lock must be removed. This can be done with a sharp knife, a box cutter, or it can be ground off with a Dremel or similar tool. Before and after: (Pic. 7)
Supplies Needed:
• #1 Philips head screwdriver
• Knife/box cutter/Dremel (optional)
Step 1: Locate the trigger and magazine locks utilizing the close-up photo of the internals located in the previous step.
Step 2: Remove the screw holding in the trigger catch activator and remove the activator.
Step 3: Remove the trigger lock. Take care to keep the spring from shooting out during removal.
Step 4: To remove the magazine lock, the bolt sled and plunger/breach must be removed as well. Pull the mainspring out through the back of the gun, then remove the trigger catch. Then gently work the bolt sled and plunger assembly out of the blaster, maneuvering the bar connecting the bolt sled to the cocking handle through the internals of the blaster. The magazine lock can be removed from the assembly without disassembling the whole thing. Follow the pictures above to see how to do this. (Pic. 1-6)
Step 5 (optional): If you would like to keep the magazine lock in order to preserve the functionality of the jam door, but still remove your magazine whenever you like, a small bit of plastic at the bottom of the magazine lock must be removed. This can be done with a sharp knife, a box cutter, or it can be ground off with a Dremel or similar tool. Before and after: (Pic. 7)
Chapter 3: Air Restrictor Removal (Part 1)




The air restrictor slows down the flow of air from the plunger to the dart. This device serves to reduce the blaster's power and prevent the plunger from slamming into the plunger tubing at full speed, drastically reducing the noise generated during firing.
Note: Some of the plunger tubing pictured below has been cut out of the plunger for demonstration purposes.
Supplies Needed:
• Hammer
• Nail or small screwdriver or punch
• Pliers (optional)
Step 1: Remove the bolt sled and plunger from the blaster. Unpin the plunger assembly from the bolt sled using a nail, small screwdriver, or punch. You can do this by inserting the nail, screwdriver, or punch into the hole that houses the retention pin and apply pressure. We prefer to use a hammer and nail for this step. When the pin is partially removed as shown, pliers can be used to pull the rest of it out. (Pic. 1)
Step 2: Once the retention pin is removed, separate the plunger and bolt sled, putting the plunger tube, bolt sled, and retention pin to the side, as they are not needed for this process. (Pic. 2)
The inside of your breech should look like this: (Pic. 3)
TIP: Before we move on, it's important to understand which parts of the tubing assembly are ok to hit with the drill and which are not. If you shake the plunger tube, you should hear some parts rattling around. The follow picture shows exactly what's inside the plunger tube: (Pic. 4)
In the next section, I've listed 2 different methods for air restrictor removal. Please review the supplies required for each, and pick one that's most convenient for you. If done correctly, all of these methods will work.
Note: Step 1 is the same for each method and must be completed prior to starting on the next part.
Note: Some of the plunger tubing pictured below has been cut out of the plunger for demonstration purposes.
Supplies Needed:
• Hammer
• Nail or small screwdriver or punch
• Pliers (optional)
Step 1: Remove the bolt sled and plunger from the blaster. Unpin the plunger assembly from the bolt sled using a nail, small screwdriver, or punch. You can do this by inserting the nail, screwdriver, or punch into the hole that houses the retention pin and apply pressure. We prefer to use a hammer and nail for this step. When the pin is partially removed as shown, pliers can be used to pull the rest of it out. (Pic. 1)
Step 2: Once the retention pin is removed, separate the plunger and bolt sled, putting the plunger tube, bolt sled, and retention pin to the side, as they are not needed for this process. (Pic. 2)
The inside of your breech should look like this: (Pic. 3)
TIP: Before we move on, it's important to understand which parts of the tubing assembly are ok to hit with the drill and which are not. If you shake the plunger tube, you should hear some parts rattling around. The follow picture shows exactly what's inside the plunger tube: (Pic. 4)
In the next section, I've listed 2 different methods for air restrictor removal. Please review the supplies required for each, and pick one that's most convenient for you. If done correctly, all of these methods will work.
Note: Step 1 is the same for each method and must be completed prior to starting on the next part.
Air Restrictor Removal (Part 2)




Method 1:
Supplies Needed:
• Dremel tool or drill
• Long Dremel bit or drill bit
• Flat head screwdriver
• Rat tail file
Step 1: With the long Dremel or drill bit, drill a series of holes through the three posts holding the air restrictor in place, shown below. Again, be careful not to drill through the sides of the plunger tube. (Pic. 1)
Step 2: Using the flat head screwdriver, punch out the air restrictor.
Step 3 (optional, but recommended): Use the rat tail file to grind down any leftover bits of plastic inside the plunger tube. The goal is to have the inside of the plunger tube as smooth as possible. (Pic. 2)
Tip: Be careful not to break the two pieces of plastic holding the post in place.
Method 2:
Supplies Needed:
• Wire coat hanger or metal dowel or long screwdriver
• Fire (lighter, torch, etc.)
• Gloves or oven mitt
• Needle nose pliers
• Rat tail file
• Flat head screwdriver
Step 1: This method involves creating a series of holes like method 1. But instead of drilling, we are going to use a heated metal rod to melt the holes. This should be done in a well- ventilated area due to the creation of plastic fumes.
Hold the metal poker of choice with a glove or oven mitt, and heat the other end with a lighter or torch. (Pic. 3)
Step 2: Stick it down the plunger tubing and start melting the holes. The poker will have to be reheated after each hole. (Pic. 4)
Step 3: Using the flat head screwdriver, punch out the air restrictor.
Step 4 (optional, but recommended): Use the rat tail file to grind down any leftover bits of plastic inside the plunger tube. The goal is to have the inside of the plunger tube as smooth as possible. (Pic. 2)
Supplies Needed:
• Dremel tool or drill
• Long Dremel bit or drill bit
• Flat head screwdriver
• Rat tail file
Step 1: With the long Dremel or drill bit, drill a series of holes through the three posts holding the air restrictor in place, shown below. Again, be careful not to drill through the sides of the plunger tube. (Pic. 1)
Step 2: Using the flat head screwdriver, punch out the air restrictor.
Step 3 (optional, but recommended): Use the rat tail file to grind down any leftover bits of plastic inside the plunger tube. The goal is to have the inside of the plunger tube as smooth as possible. (Pic. 2)
Tip: Be careful not to break the two pieces of plastic holding the post in place.
Method 2:
Supplies Needed:
• Wire coat hanger or metal dowel or long screwdriver
• Fire (lighter, torch, etc.)
• Gloves or oven mitt
• Needle nose pliers
• Rat tail file
• Flat head screwdriver
Step 1: This method involves creating a series of holes like method 1. But instead of drilling, we are going to use a heated metal rod to melt the holes. This should be done in a well- ventilated area due to the creation of plastic fumes.
Hold the metal poker of choice with a glove or oven mitt, and heat the other end with a lighter or torch. (Pic. 3)
Step 2: Stick it down the plunger tubing and start melting the holes. The poker will have to be reheated after each hole. (Pic. 4)
Step 3: Using the flat head screwdriver, punch out the air restrictor.
Step 4 (optional, but recommended): Use the rat tail file to grind down any leftover bits of plastic inside the plunger tube. The goal is to have the inside of the plunger tube as smooth as possible. (Pic. 2)
Chapter 4: Air Release Hole Mod


Supplies needed:
• Tape (recommended) or glue
Step 1: Locate the air release hold on the plunger tubing. (Pic. 1)
Step 2:Tape around the plunger tubing to seal the holes. If you're using glue, make sure no excess glue drips into the plunger, as this may cause the blaster to not fire properly. (Pic. 2)
Step 3: Now re-pin the plunger to the bolt sled and you’re done with this step!
• Tape (recommended) or glue
Step 1: Locate the air release hold on the plunger tubing. (Pic. 1)
Step 2:Tape around the plunger tubing to seal the holes. If you're using glue, make sure no excess glue drips into the plunger, as this may cause the blaster to not fire properly. (Pic. 2)
Step 3: Now re-pin the plunger to the bolt sled and you’re done with this step!
Chapter 5: Modifying the Plunger O-Ring
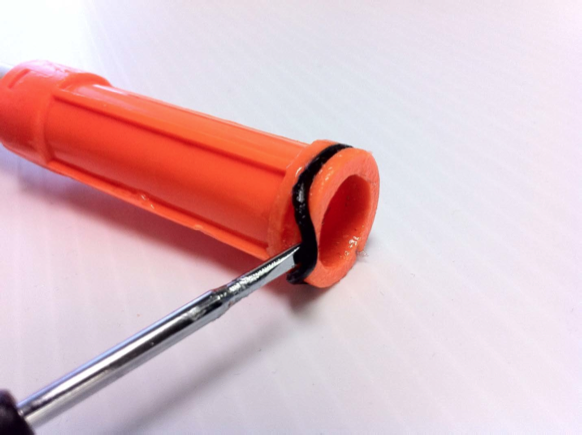

The O-ring seal on the plunger tubing makes sure the air compressed by the plunger assembly and spring does not leak out during compression. Some blasters come with an excellent O-ring seal while some come with undersized or loose O-rings. Improving this seal is an easy mod that can add a few extra feet to your shots. It is worth noting that the Alpha Trooper comes with a superb stock O-ring, and does not really need modification.
Supplies needed:
• Small flat head screwdriver
• Teflon tape
• O-ring safe lubricant such as petroleum jelly or silicon based lubricant
Caution: Make sure whatever lubricant you use is safe for rubber O-rings. Lubricants like WD-40 will melt the rubber over time and destroy the O-ring. Lubricants like gun oil can penetrate the O-ring causing it to swell. This will cause the plunger to lock up inside of the plunger tubing rendering the blaster inoperable until the O-ring is replaced.
Step 1: Remove the bolt sled and plunger from the blaster (see Step 4 on page 11 for details)
Step 2: Remove the plunger from the plunger tube and gently pry the O-ring out of its groove with a flat head screwdriver. Be careful not to damage the O-ring if you plan on reusing it. (Pic. 1)
Step 3: This method involves wrapping a thin layer of tape around the O-ring lip in order to create a better air seal. You must take care not to use too much tape because it will create more pressure between the O-ring and the wall of the plunger resulting in greater resistance against the spring. When done correctly the plunger tubing should slide easily back into the plunger. Electrical tape is not recommended for the Alpha Trooper, as it is too thick. It is also recommended to wrap the Teflon tape around the plunger only once. Make sure to wash off any factory lubrication before applying the tape because it will not stick otherwise. When finished, it should look something like this: (Pic. 2)
Supplies needed:
• Small flat head screwdriver
• Teflon tape
• O-ring safe lubricant such as petroleum jelly or silicon based lubricant
Caution: Make sure whatever lubricant you use is safe for rubber O-rings. Lubricants like WD-40 will melt the rubber over time and destroy the O-ring. Lubricants like gun oil can penetrate the O-ring causing it to swell. This will cause the plunger to lock up inside of the plunger tubing rendering the blaster inoperable until the O-ring is replaced.
Step 1: Remove the bolt sled and plunger from the blaster (see Step 4 on page 11 for details)
Step 2: Remove the plunger from the plunger tube and gently pry the O-ring out of its groove with a flat head screwdriver. Be careful not to damage the O-ring if you plan on reusing it. (Pic. 1)
Step 3: This method involves wrapping a thin layer of tape around the O-ring lip in order to create a better air seal. You must take care not to use too much tape because it will create more pressure between the O-ring and the wall of the plunger resulting in greater resistance against the spring. When done correctly the plunger tubing should slide easily back into the plunger. Electrical tape is not recommended for the Alpha Trooper, as it is too thick. It is also recommended to wrap the Teflon tape around the plunger only once. Make sure to wash off any factory lubrication before applying the tape because it will not stick otherwise. When finished, it should look something like this: (Pic. 2)
Chapter 6: Modifying Spring



Increasing the tension of the mainspring will give your blaster a small power boost by taking up the slack that is normally present. By swapping the mainspring with a more powerful one you can easily double the power of your blaster but over time powerful springs will increase the wear on the blaster.
Supplies Needed:
• Method 1:
• Aftermarket spring
• Method 2:
• Duct tape or electrical tape
Step 1: Remove bolt sled, spring, and plunger from the blaster.
Step 2, Method 1: Install aftermarket spring by pulling the original spring off the plunger and replacing it with the aftermarket spring. (Pic. 1)
The aftermarket spring picture above is made out of slightly thicker wire. The stock spring was measured at around 2.5 kg and the aftermarket spring was measured at over 6kg. The spring swap alone will allow the Alpha Trooper to fire an angled shot up to 70 feet and can be found in the Orange Mod Works Stage 1 performance kit. You can also just bye the spring by itself (click here). (Pic. 2)
Step 2, Method 2: Create a 1 cm wide buffer out of tape by wrapping it around the outside of the plunger where the spring would rest normally. (Pic. 3)
Make the tape layer thick enough to hold the spring in place but not thicker than the plunger lip. Be careful not to make the strip of tape too wide because you will not be able to cock the plunger back if it is. This mod gives you a boost in spring tension without having to stretch out the spring. Stretching the spring causes irreversible damage to the spring and will decrease its performance after only a few shots.
Supplies Needed:
• Method 1:
• Aftermarket spring
• Method 2:
• Duct tape or electrical tape
Step 1: Remove bolt sled, spring, and plunger from the blaster.
Step 2, Method 1: Install aftermarket spring by pulling the original spring off the plunger and replacing it with the aftermarket spring. (Pic. 1)
The aftermarket spring picture above is made out of slightly thicker wire. The stock spring was measured at around 2.5 kg and the aftermarket spring was measured at over 6kg. The spring swap alone will allow the Alpha Trooper to fire an angled shot up to 70 feet and can be found in the Orange Mod Works Stage 1 performance kit. You can also just bye the spring by itself (click here). (Pic. 2)
Step 2, Method 2: Create a 1 cm wide buffer out of tape by wrapping it around the outside of the plunger where the spring would rest normally. (Pic. 3)
Make the tape layer thick enough to hold the spring in place but not thicker than the plunger lip. Be careful not to make the strip of tape too wide because you will not be able to cock the plunger back if it is. This mod gives you a boost in spring tension without having to stretch out the spring. Stretching the spring causes irreversible damage to the spring and will decrease its performance after only a few shots.
Chapter 7: Brass Breech Mod





This modification gives you the advantage of utilizing precision brass parts while preserving the blaster's original function. This mod is more advanced and requires you to destroy some of the original stock parts. Once you start this mod there is no going back to the original pieces.
Supplies Needed:
• 9/16 brass tubing
• 17/32 brass tubing
• Dremel Tool
• Conical grinding bit
• Reinforced cutting wheel
• Metal file
• Sand paper
• Hack saw
• Permanent marker
• Epoxy
• Glue
Step 1: Using the reinforced cutting wheel for the Dremel tool, cut a 13.5cm long piece of the 9/16” brass tubing and a 11cm piece of the 17/32” brass tubing. The larger outer tubing will help strip the dart from the magazine and guide it into the airtight 17/32” tubing. After you make the cuts, clean the rough edges with sandpaper or a metal file. The ends should be flat with no jagged pieces of metal.
Step 2: Grind the inner edge of one end of the 17/32” tubing you cut. The idea is to make a cone shaped grind that will help funnel the dart into the tube. Take your time here and get a nice clean looking feed ramp. (Pic. 1)
Step 3: Make a dot with your marker on either side of the mouth of the 9/16” tubing, dividing it in half. Next, measure 1.7 centimeters down from the lip of the 9/16” piece of tubing and make a dot in between the two dots you made earlier. Finally, connect the dots and color the area in between them; this is the material you are going to remove. (Pic. 2)
Step 4: Cut the part marked, and clean the area up with a conical grinder bit, file, or sandpaper.
The purpose of this cut angle is to prevent the tubing from catching on the magazine and not loading the last dart in the magazine. (Pic. 3)
Step 5: Now take your stock plunger tubing and cut it off of the plunger with your hack saw. Also cut off the front part that connects the plunger assembly to the bolt sled. This piece will be connected to the tubing with epoxy later. (Pic. 4)
Step 6: Grind out the plunger so the 9/16” tubing can fit inside the hole. (Pic. 5)
Supplies Needed:
• 9/16 brass tubing
• 17/32 brass tubing
• Dremel Tool
• Conical grinding bit
• Reinforced cutting wheel
• Metal file
• Sand paper
• Hack saw
• Permanent marker
• Epoxy
• Glue
Step 1: Using the reinforced cutting wheel for the Dremel tool, cut a 13.5cm long piece of the 9/16” brass tubing and a 11cm piece of the 17/32” brass tubing. The larger outer tubing will help strip the dart from the magazine and guide it into the airtight 17/32” tubing. After you make the cuts, clean the rough edges with sandpaper or a metal file. The ends should be flat with no jagged pieces of metal.
Step 2: Grind the inner edge of one end of the 17/32” tubing you cut. The idea is to make a cone shaped grind that will help funnel the dart into the tube. Take your time here and get a nice clean looking feed ramp. (Pic. 1)
Step 3: Make a dot with your marker on either side of the mouth of the 9/16” tubing, dividing it in half. Next, measure 1.7 centimeters down from the lip of the 9/16” piece of tubing and make a dot in between the two dots you made earlier. Finally, connect the dots and color the area in between them; this is the material you are going to remove. (Pic. 2)
Step 4: Cut the part marked, and clean the area up with a conical grinder bit, file, or sandpaper.
The purpose of this cut angle is to prevent the tubing from catching on the magazine and not loading the last dart in the magazine. (Pic. 3)
Step 5: Now take your stock plunger tubing and cut it off of the plunger with your hack saw. Also cut off the front part that connects the plunger assembly to the bolt sled. This piece will be connected to the tubing with epoxy later. (Pic. 4)
Step 6: Grind out the plunger so the 9/16” tubing can fit inside the hole. (Pic. 5)
Brass Breech Mod (Part 2)





Step 7: Sand down the underside tip of the plunger tubing you cut off so it fits over the 9/16 brass tube, and epoxy it in place as shown here: (Pic. 1-2)
Step 8: After attaching the front of the plunger tubing to the brass as seen in picture 2, there will be a small amount of brass that needs to be cut flush with the piece of plunger tubing. (Pic. 3)
Step 9: When the epoxy is dry, test fit the 9/16” tubing into the plunger. The distance from the top of the plunger where the tube is inserted to the tip of the plastic piece you epoxied on should be 15 centimeters. Refer back to pictures 1-2.
BEFORE you glue the tube into the plunger, test fit the whole assembly in the blaster to MAKE SURE it will cock back. If the tube is inserted too far into the plunger, the plunger assembly will not travel back far enough to engage the trigger lock. If it is sticks out too far from the plunger, it will hinder dart feeding. IT IS IMPERATIVE TO DOUBLE AND TRIPLE CHECK THIS FIT. If glued incorrectly, the blaster will be ruined.
Step 10: Insert the 17/32” tube into the 9/16” tube with the funnel ground end facing out. (Pic. 4)
This piece should be recessed slighted from the lower edge of the 9/16” brass tubing. Once you are satisfied with the fit you can slide it out and add a dab of glue to hold it in place. You do not need to add glue down the whole length of the piece; just a little bit toward the top is good enough. Too much glue will prevent the tubes from sliding together because the space between them is almost airtight as it is.
Step 11: After the epoxy dries, you can now reattach the breech to the bolt sled and reinsert the assembly into your blaster as normal. When finished, you should have something that looks like this: (Pic. 5)
Step 8: After attaching the front of the plunger tubing to the brass as seen in picture 2, there will be a small amount of brass that needs to be cut flush with the piece of plunger tubing. (Pic. 3)
Step 9: When the epoxy is dry, test fit the 9/16” tubing into the plunger. The distance from the top of the plunger where the tube is inserted to the tip of the plastic piece you epoxied on should be 15 centimeters. Refer back to pictures 1-2.
BEFORE you glue the tube into the plunger, test fit the whole assembly in the blaster to MAKE SURE it will cock back. If the tube is inserted too far into the plunger, the plunger assembly will not travel back far enough to engage the trigger lock. If it is sticks out too far from the plunger, it will hinder dart feeding. IT IS IMPERATIVE TO DOUBLE AND TRIPLE CHECK THIS FIT. If glued incorrectly, the blaster will be ruined.
Step 10: Insert the 17/32” tube into the 9/16” tube with the funnel ground end facing out. (Pic. 4)
This piece should be recessed slighted from the lower edge of the 9/16” brass tubing. Once you are satisfied with the fit you can slide it out and add a dab of glue to hold it in place. You do not need to add glue down the whole length of the piece; just a little bit toward the top is good enough. Too much glue will prevent the tubes from sliding together because the space between them is almost airtight as it is.
Step 11: After the epoxy dries, you can now reattach the breech to the bolt sled and reinsert the assembly into your blaster as normal. When finished, you should have something that looks like this: (Pic. 5)
Chapter 8: Problems With Creating a Sealed Breech
With direct plunger magazine fed foam blasters such as the “Longshot”, a sealed breach similar to that of a firearm can be made out of tubing. This breech feeds each dart into a sealed chamber before firing. Because the blaster is firing from a closed breech it is able to achieve near perfect air seals plus the advantage of a long tight bore barrel. With the reverse plunger system found in this blaster the volume of compressed air needed to use a sealed breech to its full potential is not present and the size of the blaster is not ideal for adding a barrel.