Multi-layer CNC Cut Sign
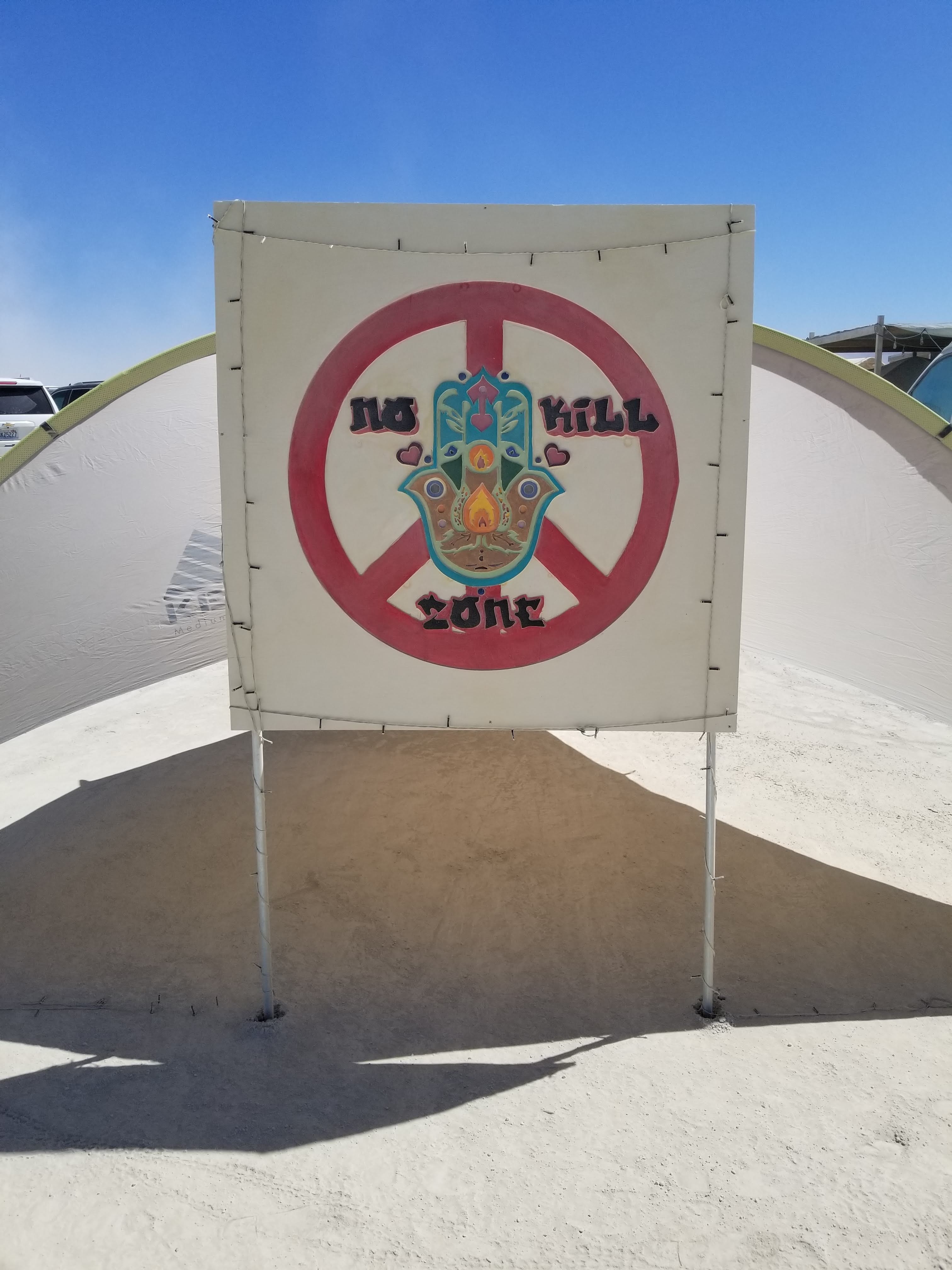
A wooden carved and painted sign is a fun project to do on your CNC machine.
When finished and installed, it becomes a focal point for whatever it signifies, in this case a Burning Man camp.
With CNC, you need to work in several disciplines and with several pieces of software, hardware and tools and even paint.
It is fun to experiment and come up with a workflow that guides you through design, CAM coding, carving and finish work. This instructable will give you a brief overview of my workflow. There are many different options for design, Cam, carving, etc. It helps to practice and try out different approaches and tools.
Supplies
- One 4'x4' sheet of 15/32 Exterior rated plywood
- White primer, outdoor rated
- Poly Urethane Varnish
- Palette of Acrylic paints
- Large Brush
- Maslow CNC machine
- 4 1" wood screws
- 1" Endmill
- 1/8" Endmill
- 2x 5' EMT Conduit 3/4 Diam.
- 4x EMT Conduit clamps 3/4"
- 4 1/2" Panhead Screws
- Philips screw driver or impact driver
- Computer
- Inkscape vector graphic software
- Fusion 360 Software
Design Your Sign in Inkscape
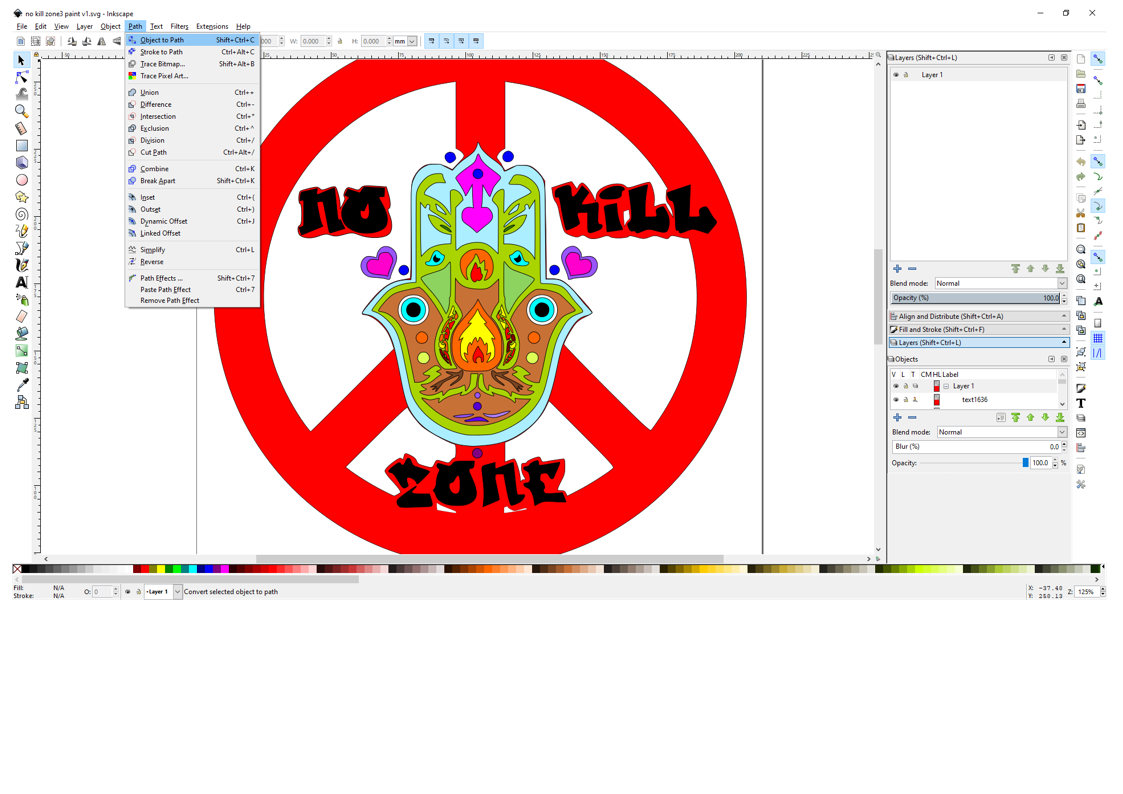
- Set the rough dimensions, by drawing a box to size in Inkscape in mm (i.e. 1210 mm x 1219 mm)
- Get inspired by the theme (in my case "No Kill Zone") and take inspiration from looking at related sources on the web, I.e. Pinterest or google image search
- 3-Axis CNC carvings are basically a robot following a specific path at a specific depth in the wood. This CNC machine, or robot, can only follow a path that you first lay out as a vector graphic (.svg or .dxf formats) and then turn that vector graphic into so-called G-Code, a programming language that tells the "robot" exactly where to go and how deep to cut, etc.)
Design the sign in Inkscape by starting with simple shapes and refining the vectors from there- If needed, convert any JPGs to vector format in Inkscape with the trace functionality
- Choose a font and if you don't already have it, there are thousands of free fonts you can download from the web
- When you're done with the line drawing and fonts, try different color schemes to help think about details and painting
- When the design is final, convert all objects to "path" (I.e. fonts) and create a "union" of all the paths. This is important for import to your CAM program Fusion 360. Fusion otherwise will see line breaks in objects and not recognize closed circles, ovals and other shapes as such
- Export the file as type DXF using roboline, make sure to use 'mm' as base unit and leave LWPolyline unchecked.
Computer Aided Manufacturing (CAM - or How to Turn the Vector Graphic Into Carvable Code)
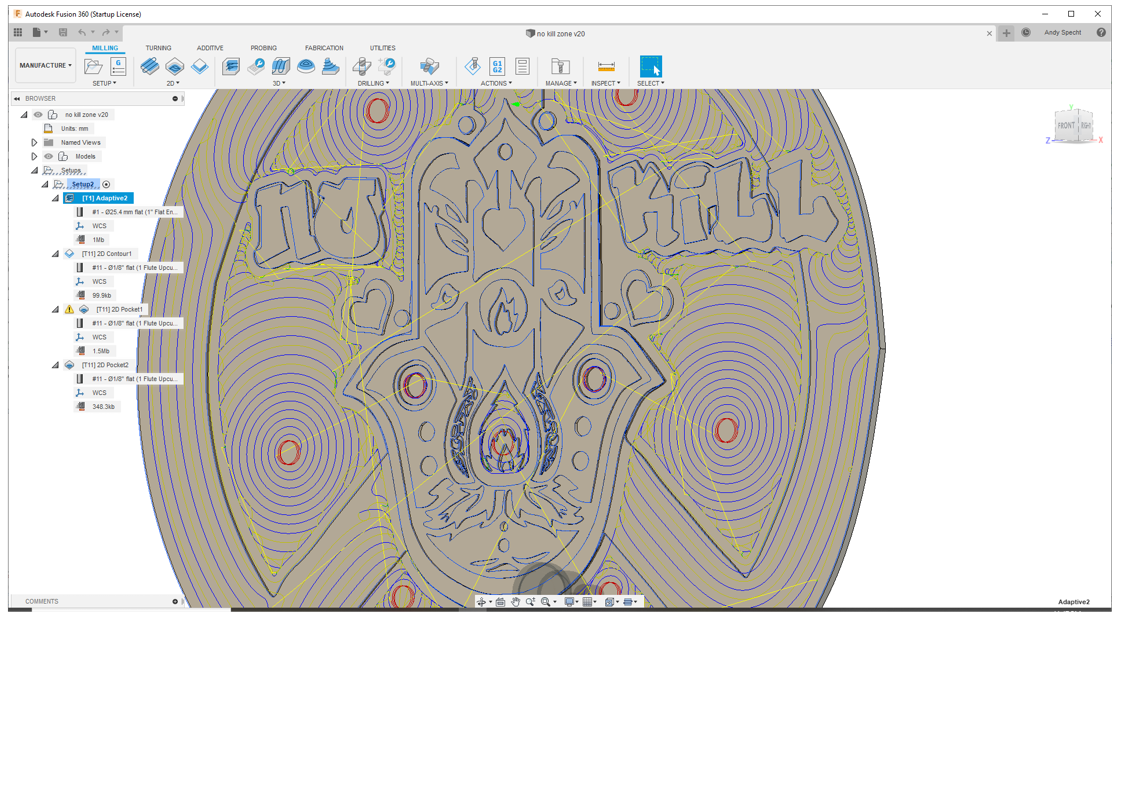
The second step in my workflow is the CAM set up in Fusion 360:
Here I import the 2D design, turn it into a 3D relief and tell the computer what tools I want to use for carving.
Even more so then Inkscape, Fusion takes some learning to use well. There are great you tube videos out there and some online courses, books and webinars.
Start simple, you'll learn lots with each project!
I won't go into too much detail of the cam set up in this instructable and just point out some specifics:
- Import file in Fusion 360 by creating a new drawing and importing DXF
- Check that all shapes are actually recognized by Fusion by holding your mouse over them and see them turn blue
- Measure wood sheet thickness with calipers and "extrude" sign features:
- For this sign I chose 3 different levels of depth in addition the top surface. Each level is two mm apart, so -2mm, -4mm, -6mm. I chose to emphasize certain features, like the font by bringing it more forward and contrast it against the background by dropping it in a few mm.
- In the manufacturing set up I defined the wood piece and tools used to carve out the sign. The sign is pretty big, so the finer details come out by using a 1/8” end mill. Of course, I don’t want to carve out all the surfaces with a small 1/8” bit. To save time, I am using a 1” end mill to rough out most of the bigger spaces. The 3D adaptive clearing strategy allows to just set the outside boundary and then let Fusion figure out all the details without me having to define each and every one of them
- With the 1/8” bit, I then do a 2D pocket rest machining strategy, so that it only clears away the corners that the 1” bit could not get into.
Overall on the Maslow, being a pretty slow machine, it still took 6+ h to carve all the details.
Carving on the Maslow CNC
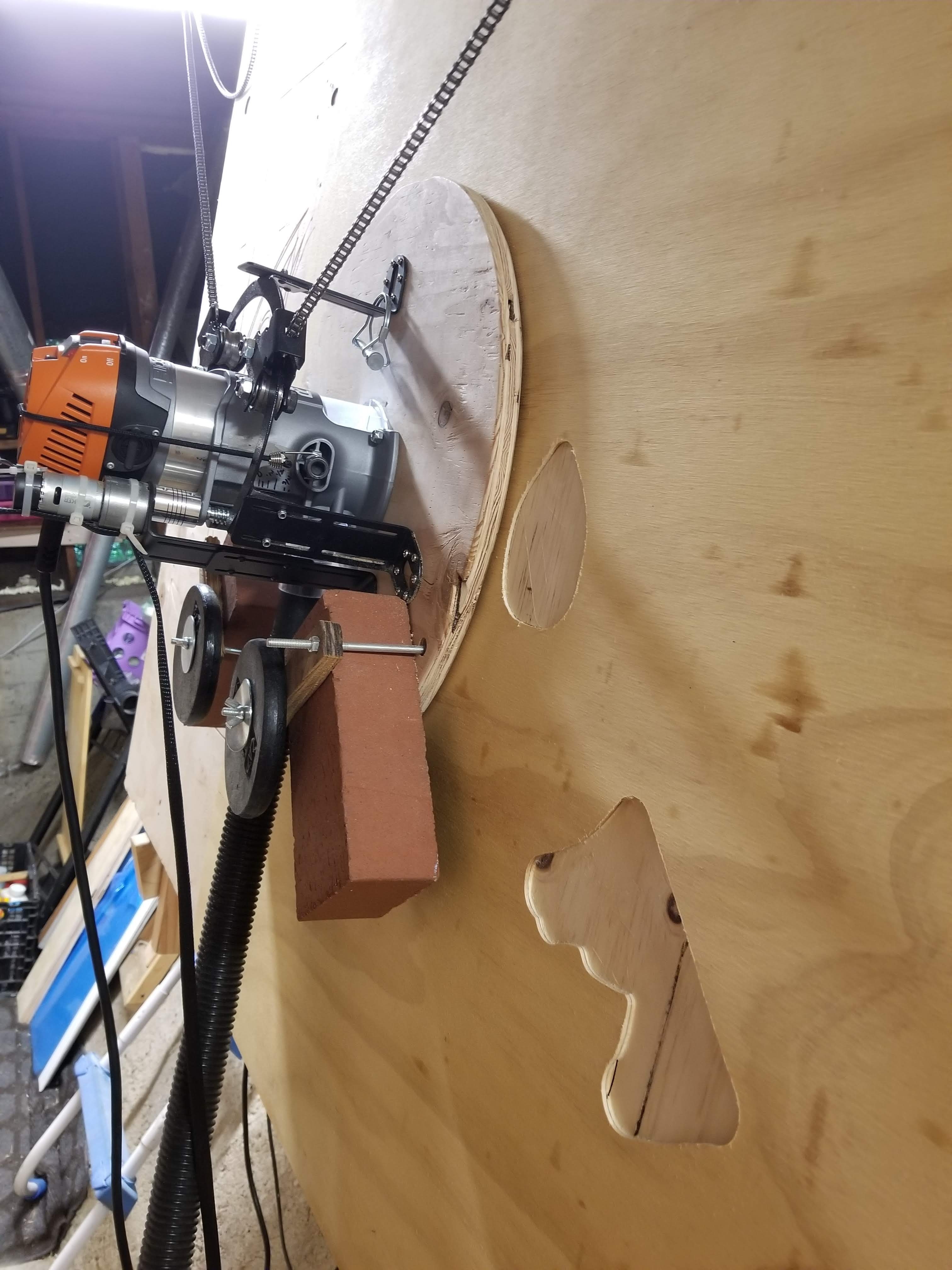
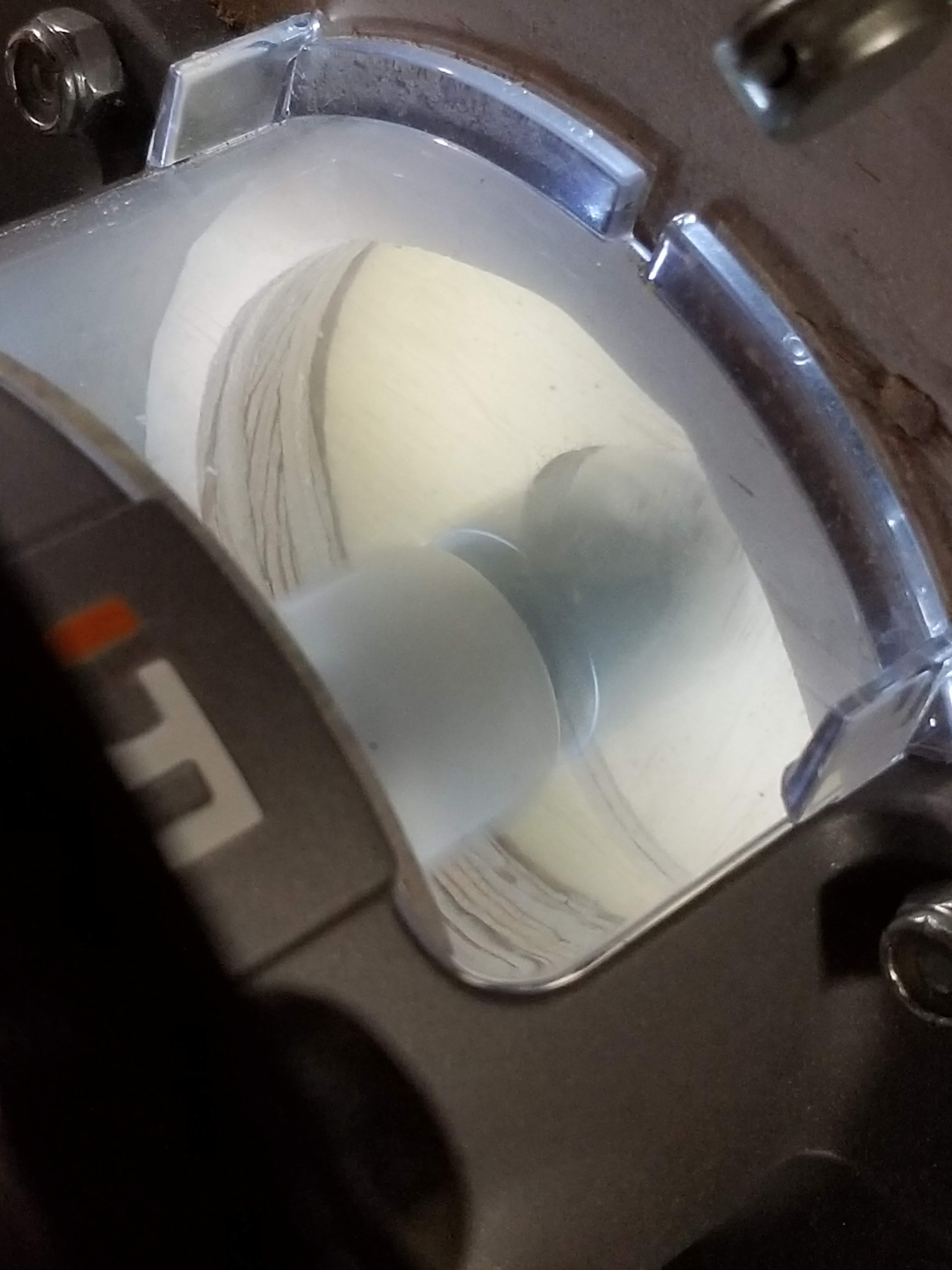
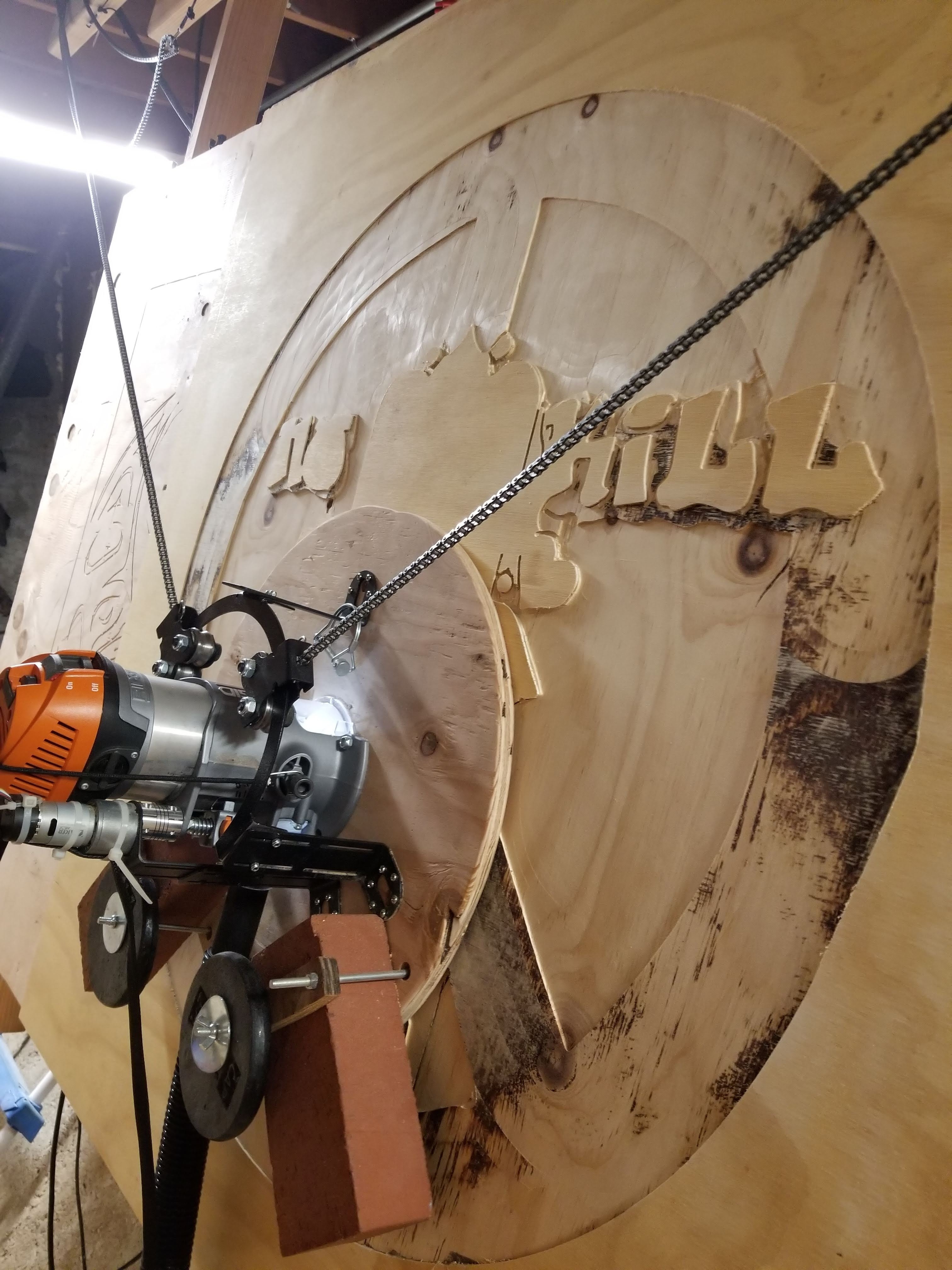
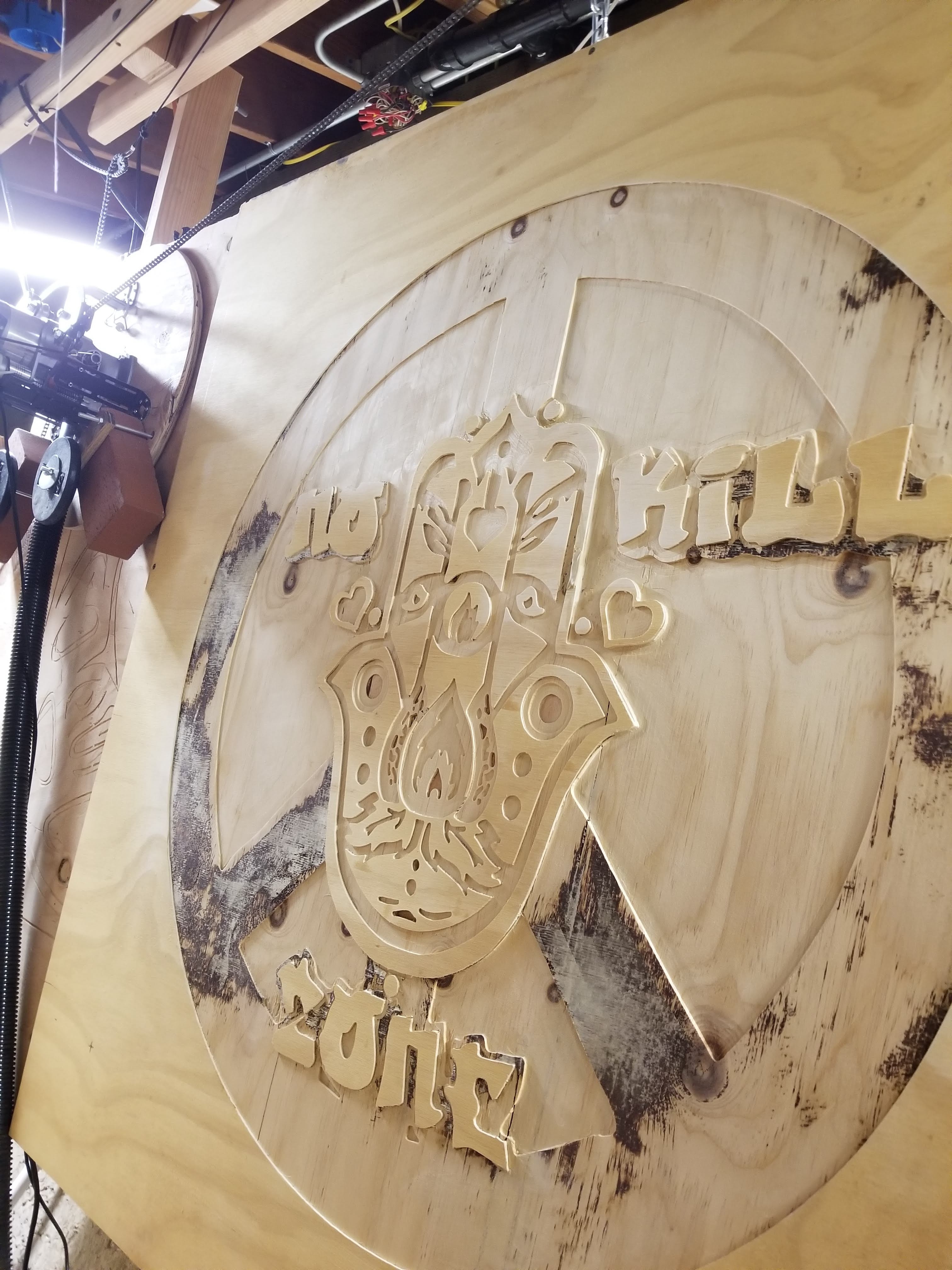
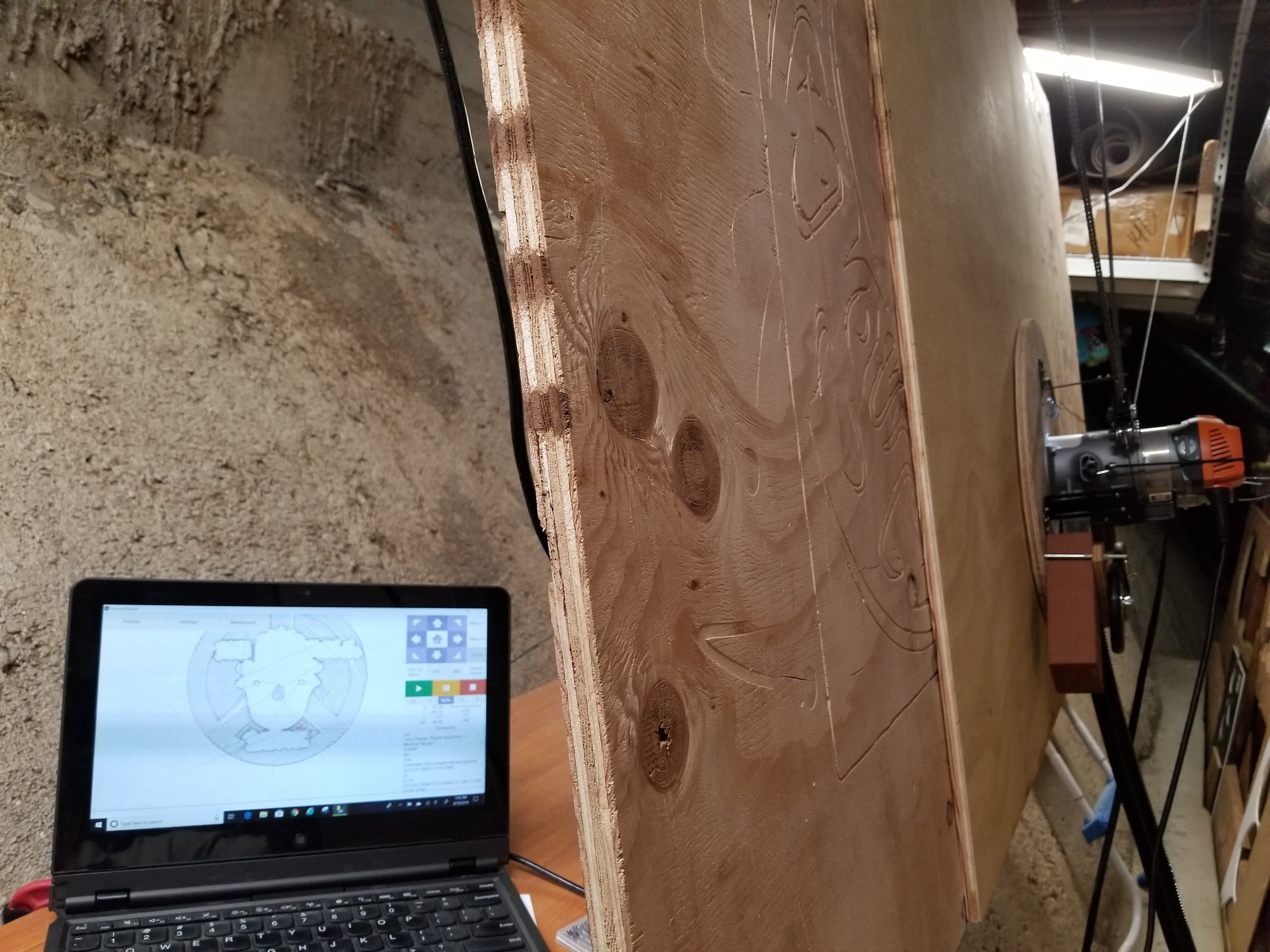
After creating the code, it is now time to actually feed the code to the CNC machine, set the workpiece on the table and set up a tool on the router. It's fun to watch the machine move the router over the work piece and see the carving happening.
For a 4'x4' sign you need a large. full sheet capable router. I got the Maslow CNC, it not only can it do full sheets, it also can do them almost vertically, which saves a lot of space in my work area.
The Maslow CNC is an unusual CNC in that the router that carves the wood, actually sits on a sled that sits right on the work piece. This is great in many ways, because I don’t have to ensure that the work piece is 100% flat on the table, the sled glides over it and it will always cut relative to the surface.
Where it does become a problem, is when the surface gets cut over a space bigger than the 18” diameter sled, so the sled tilts into the carving. This sign was just on the edge of that, so I had to babysit some of the cut and make sure the sled does not get stuck.
In general you want to be really close when carving wood with a CNC machine, just to be able to quickly stop the machine, if something goes wrong.
Cleanup
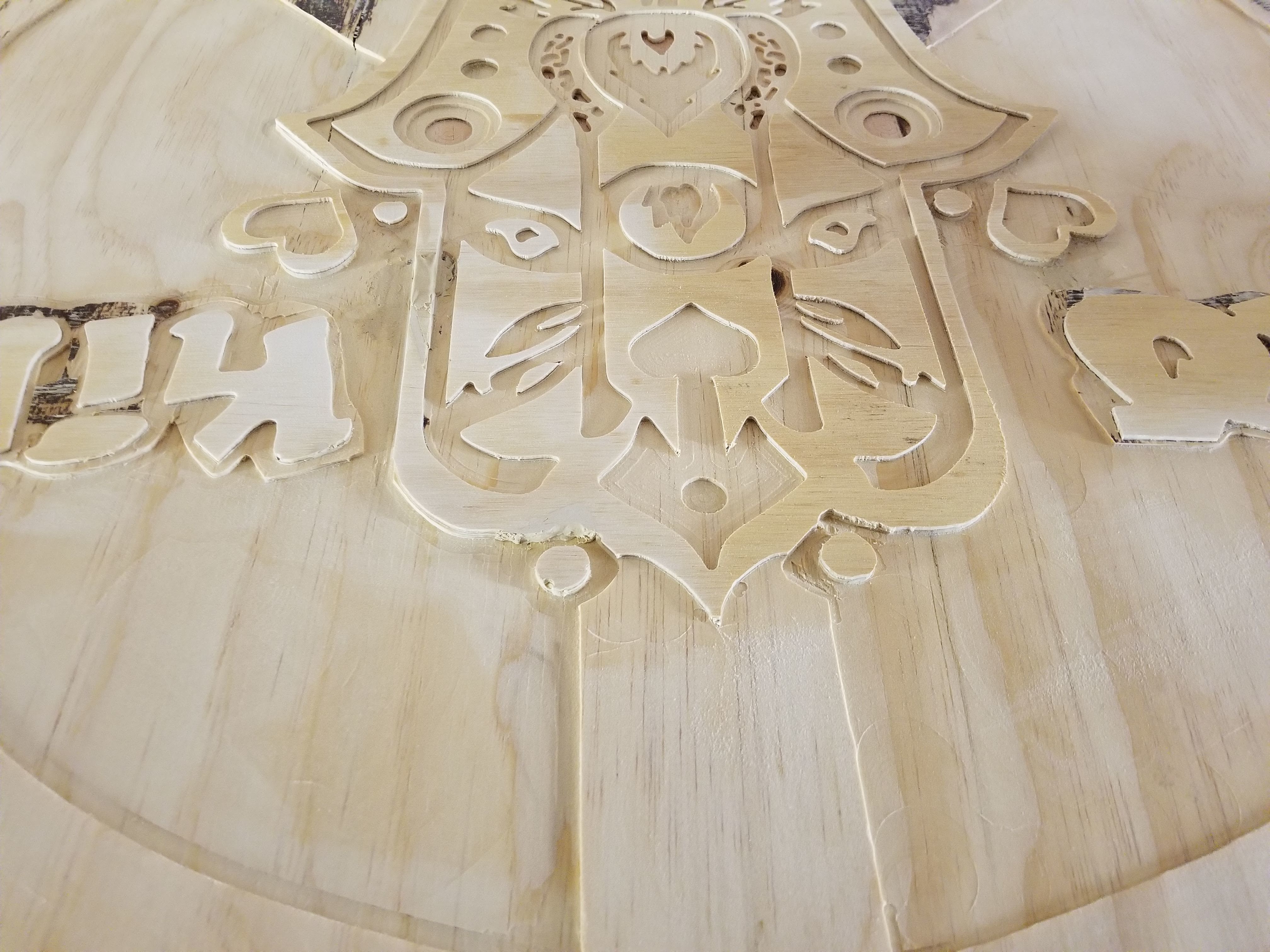
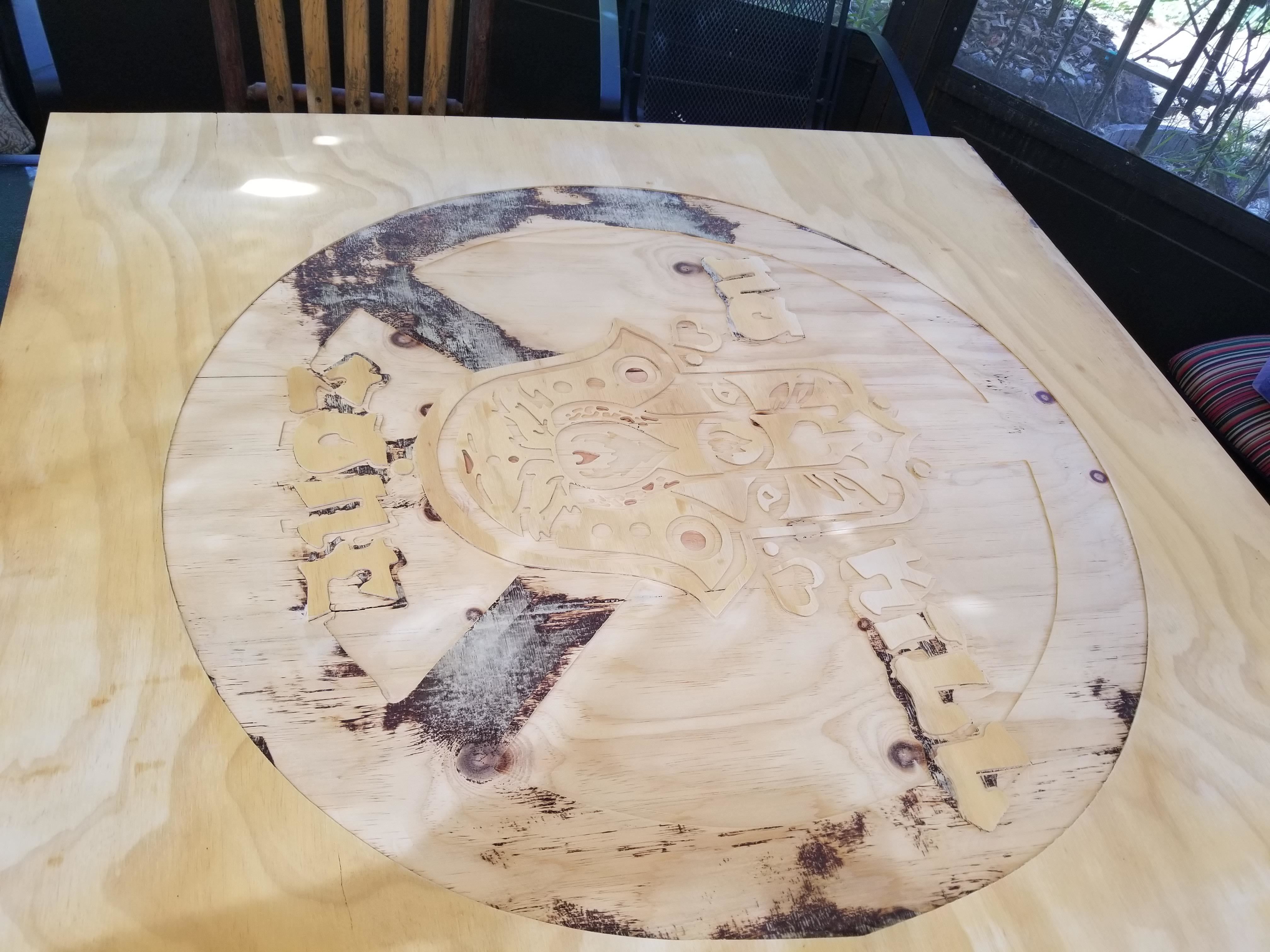
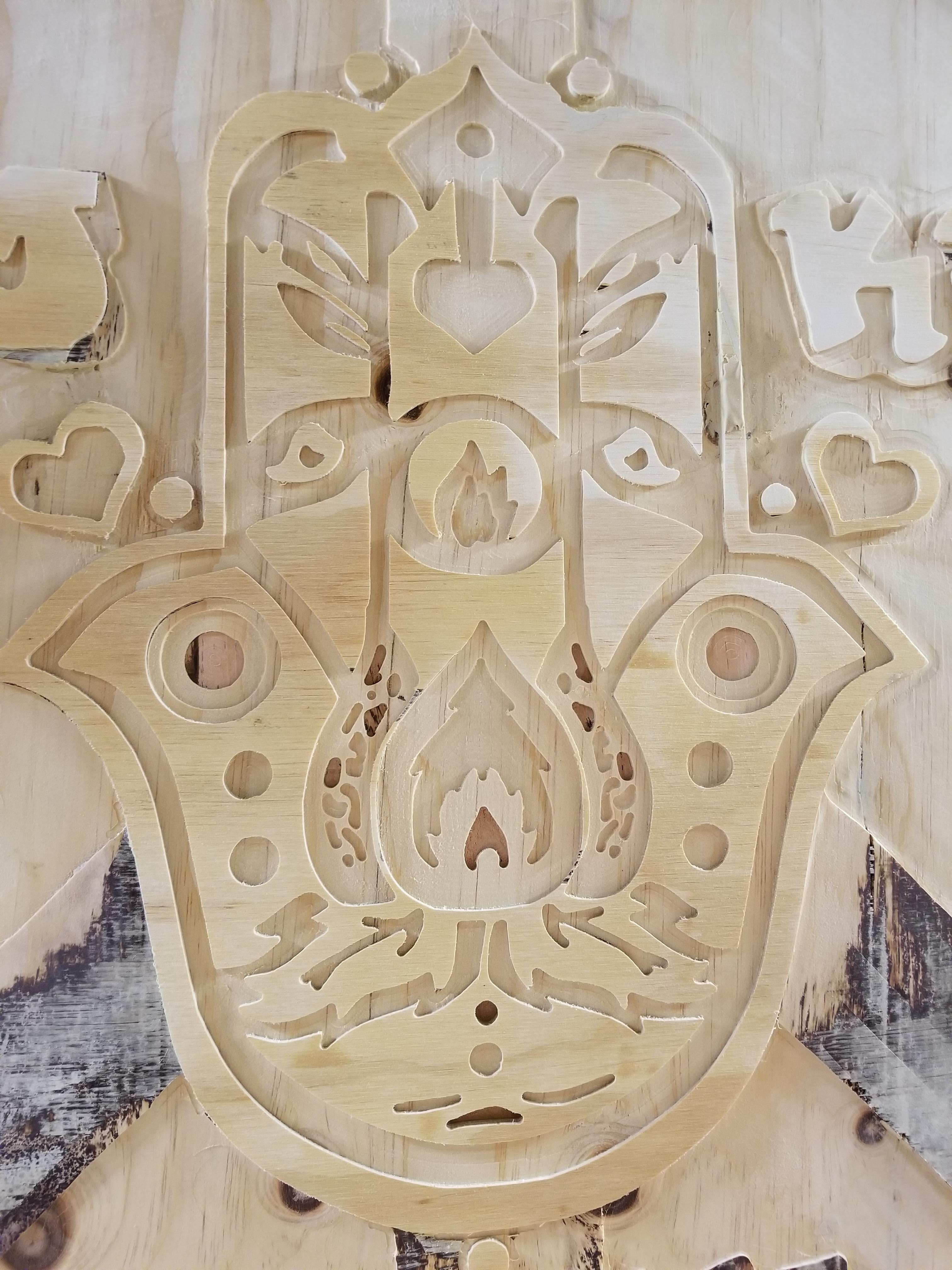
After the carving I need to clean up any issues. There is sanding needed, where the bit leaves ‘witness marks’, shallow grooves that are not part of the design.
Also, I made a couple of mistakes when stopping and restarting the machine and accidentally cut into the design. Wood putty is great for fixing these problems:
I fill in the area with wood putty, wait for it to fully dry and then sand it flat and smooth.
Painting, Varnish and Mounting
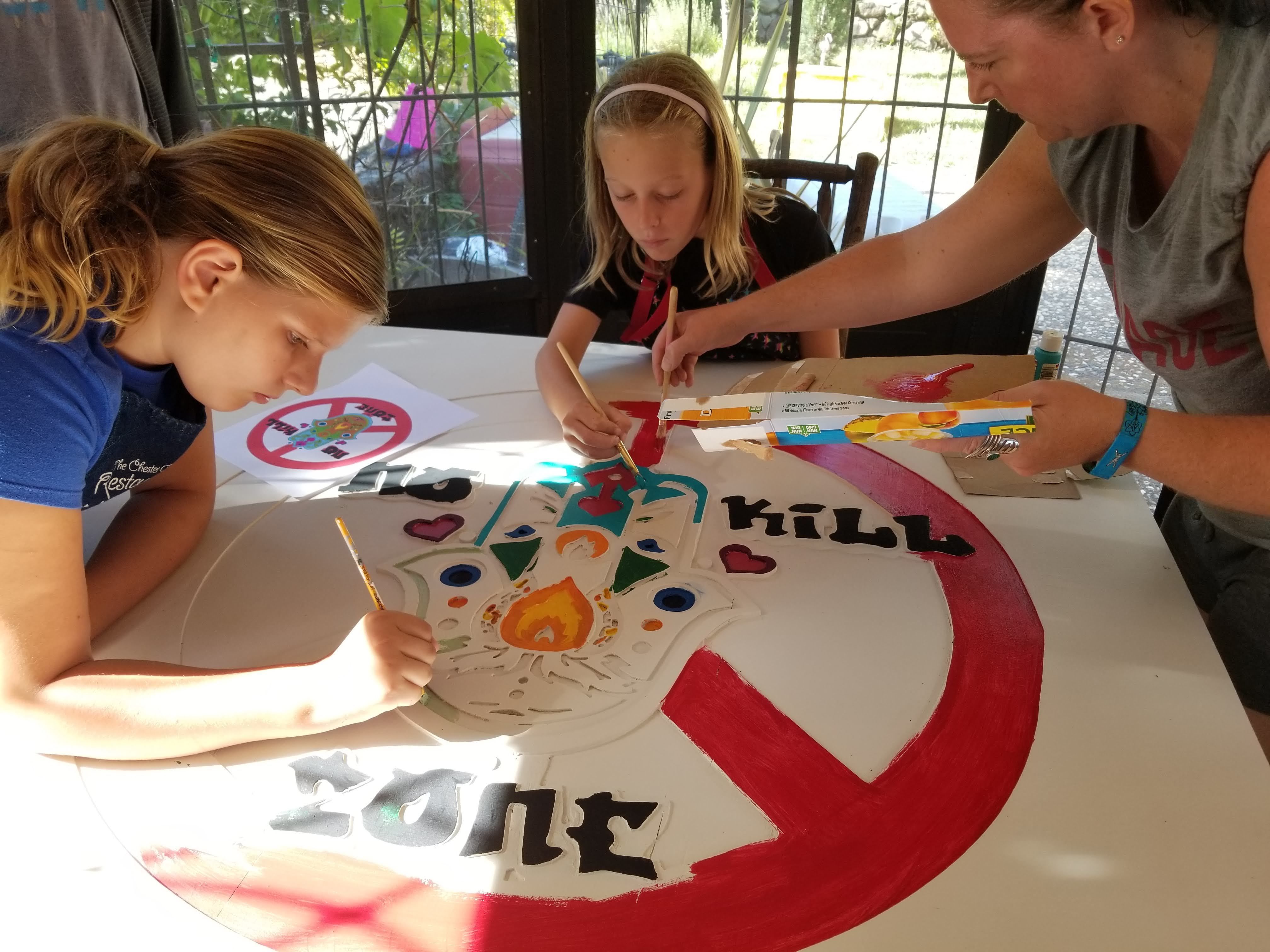
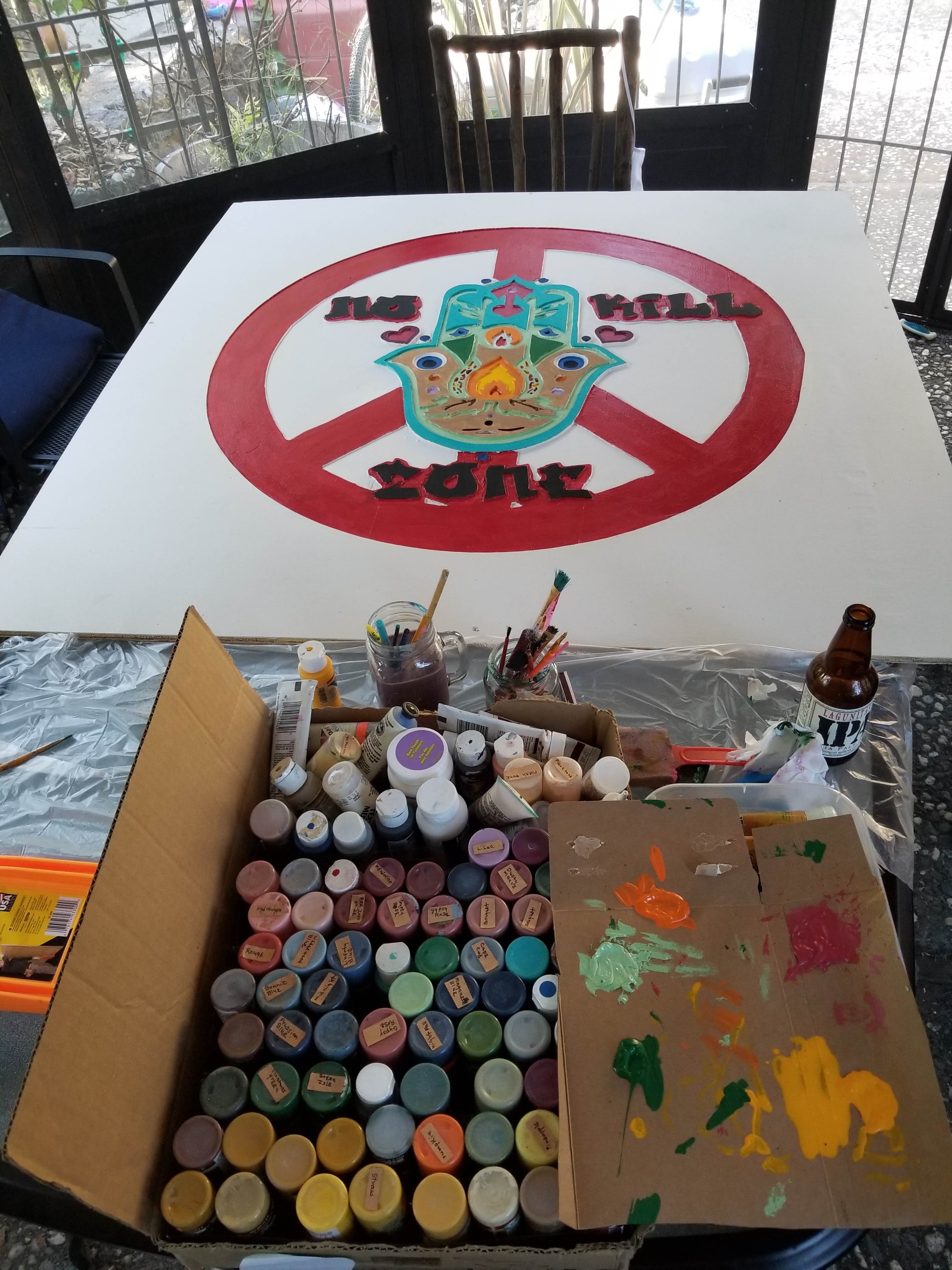
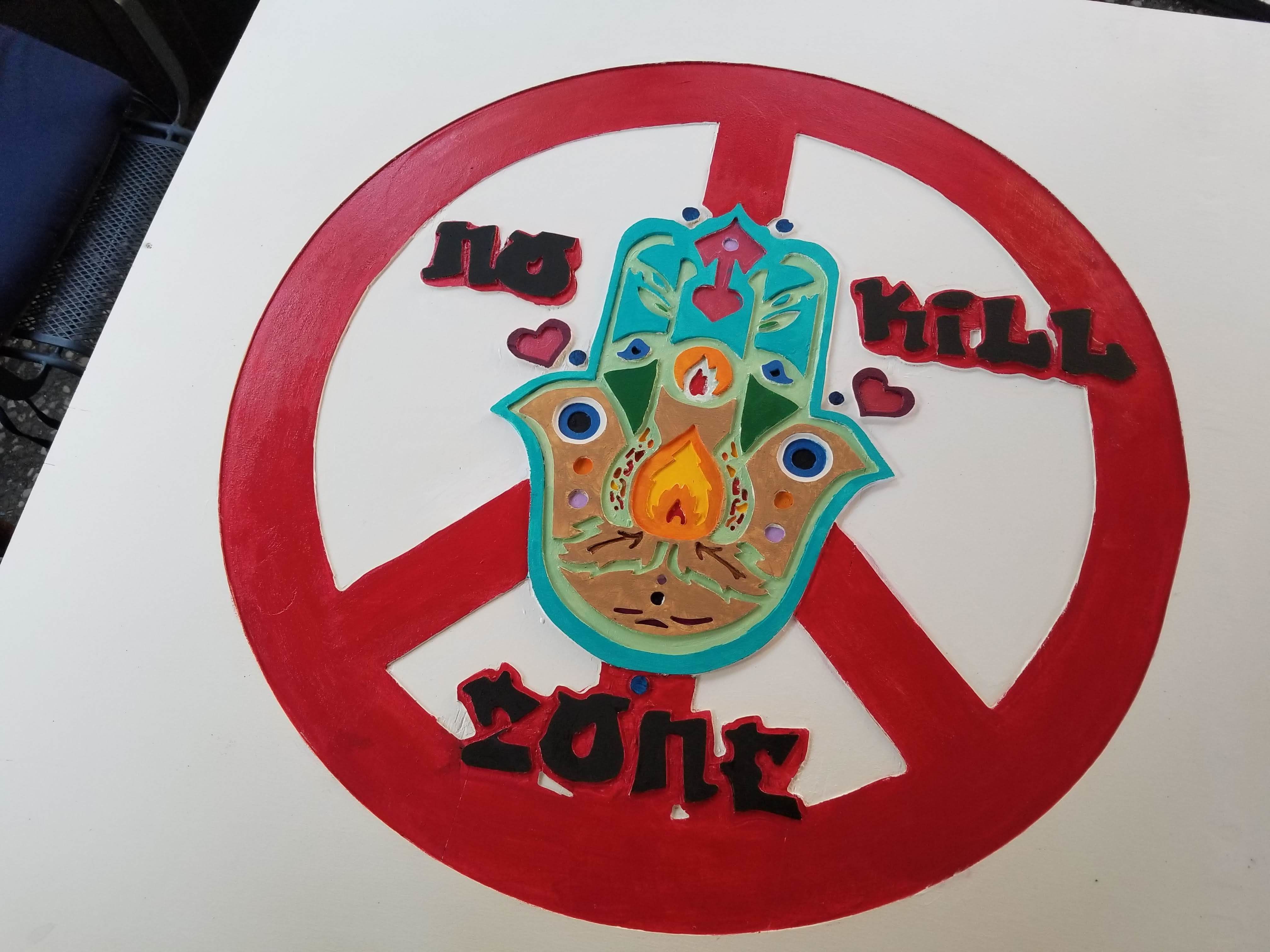
After carving and sanding:
- Take the board off the cnc table,
- blow off the rest of the wood shavings with compressed air and
- prime the sign in white with an outdoor primer.
- When the primer is dry, the sign becomes a fun family project to paint with acrylic paints.
- After allowing for the acrylic paint to dry, I apply a coat of polyurethane varnish
- The sign is supported by 2x 5’ 3/4 EMT pipes, attached with 4x 3/4 EMT clips