Millow: 3D Milling a T-spline Body With Inventor HSM and Haas CNC Mill
by tinkertinker in Workshop > CNC
2533 Views, 14 Favorites, 0 Comments
Millow: 3D Milling a T-spline Body With Inventor HSM and Haas CNC Mill
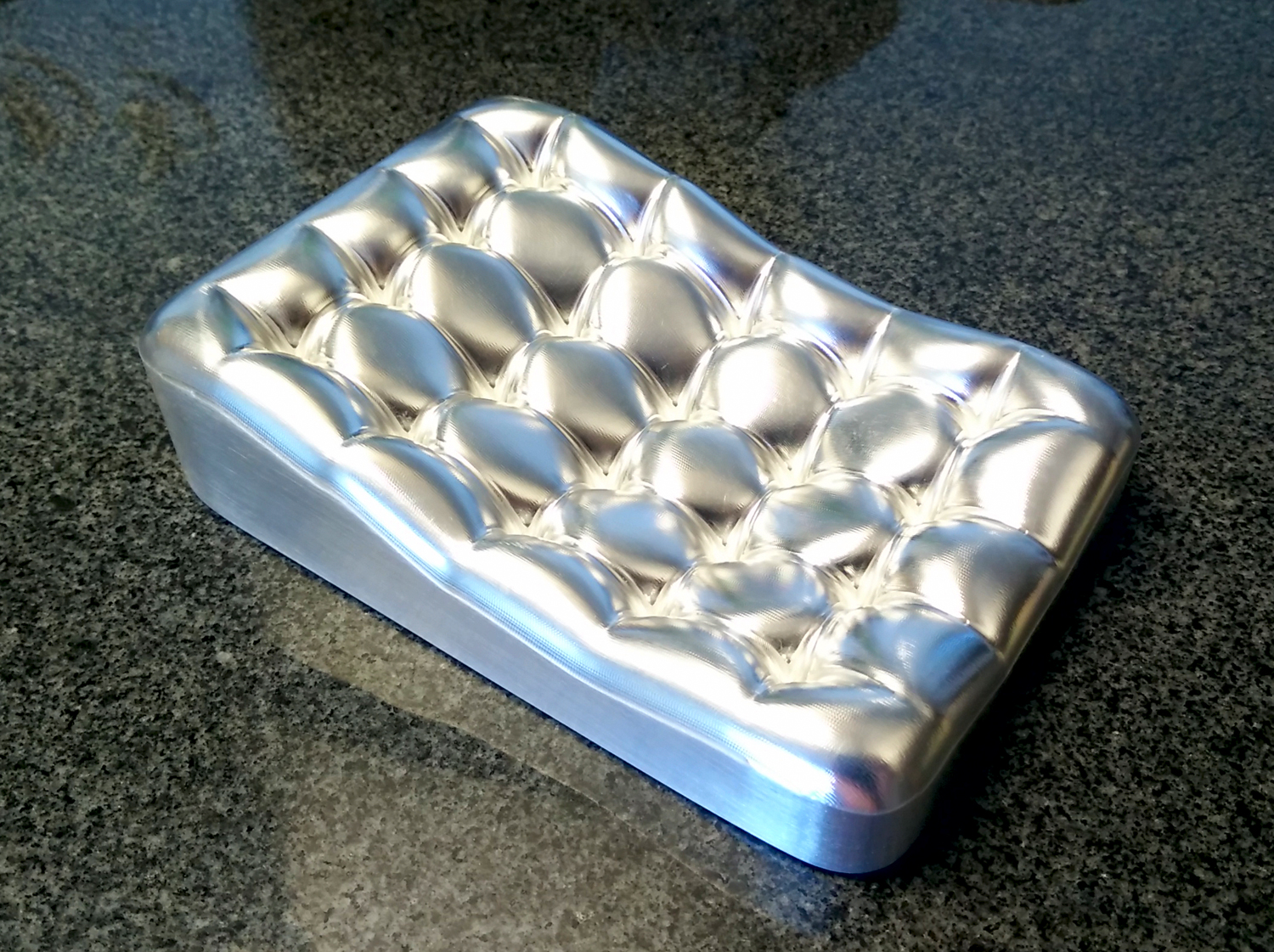
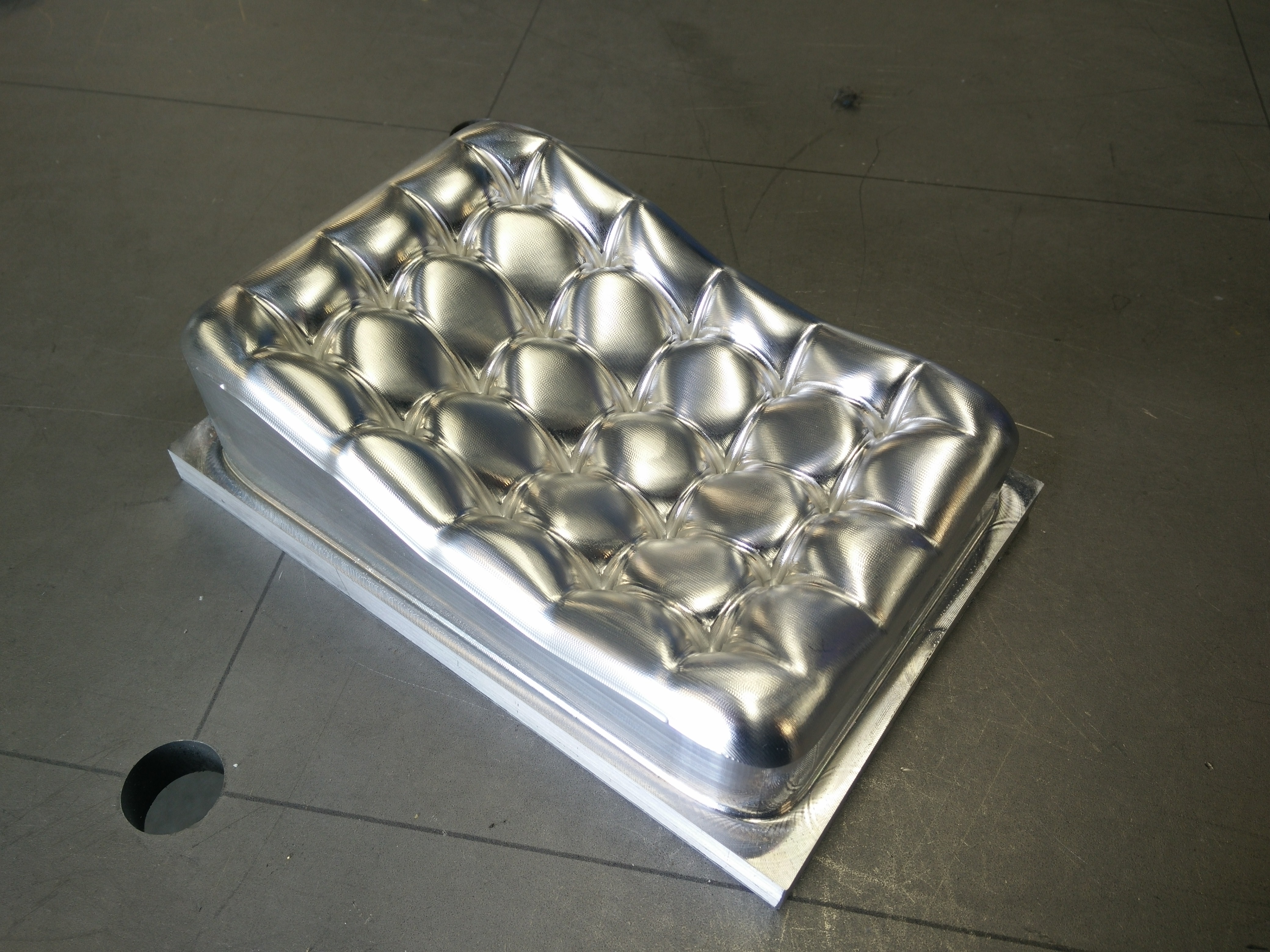
I made this project to practice working with the following skills:
- Using T-splines in Inventor
- Creating toolpaths in Inventor HSM CAM
- 3D Milling on the Haas CNC Mill
This Instructable is written assuming you have basic knowledge of the tools being used, and that you are seeking to expand your skills the same way I am: with a little help and a lot of hands-on time.
Modelling With T-Splines in Inventor

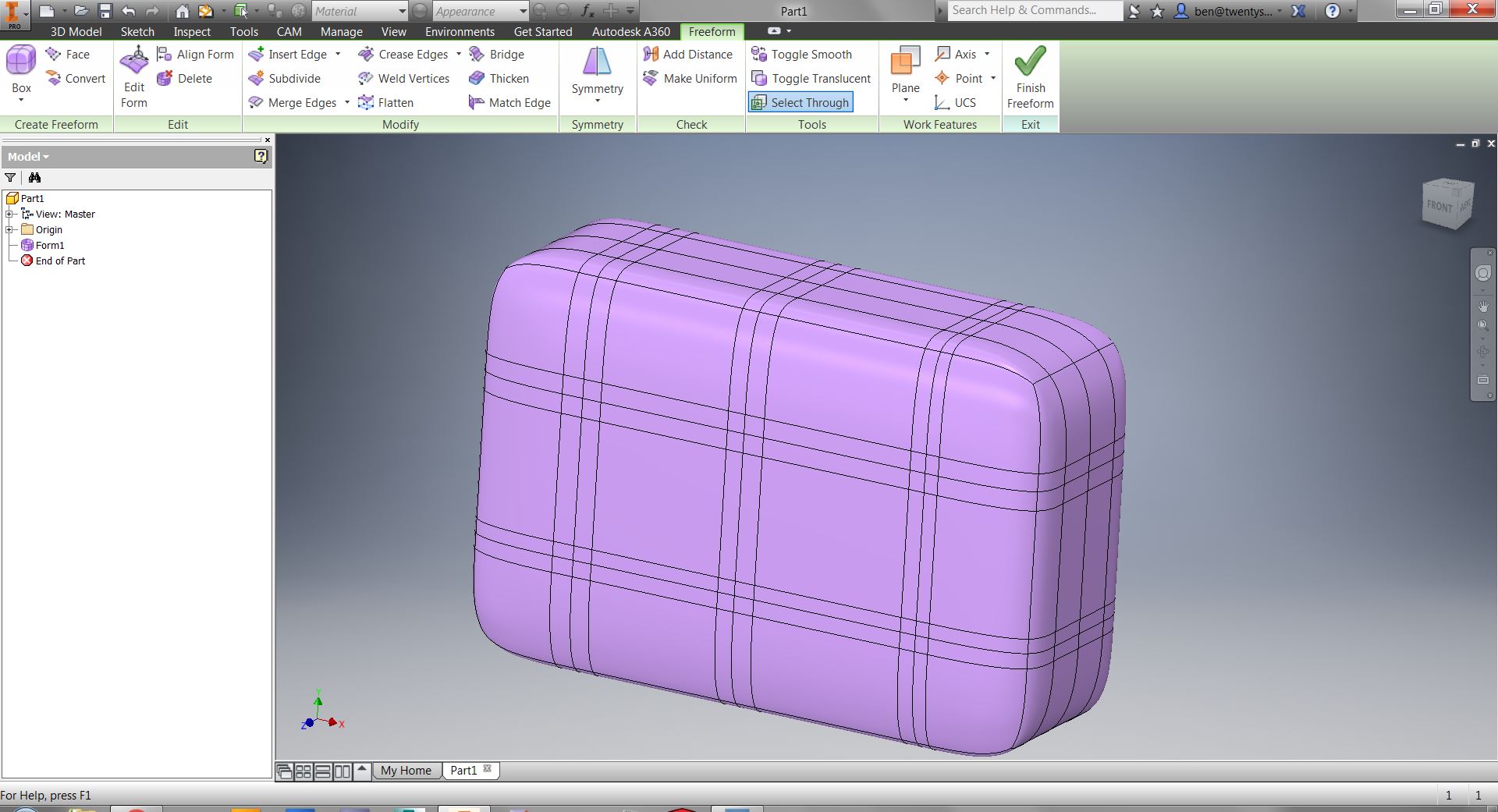
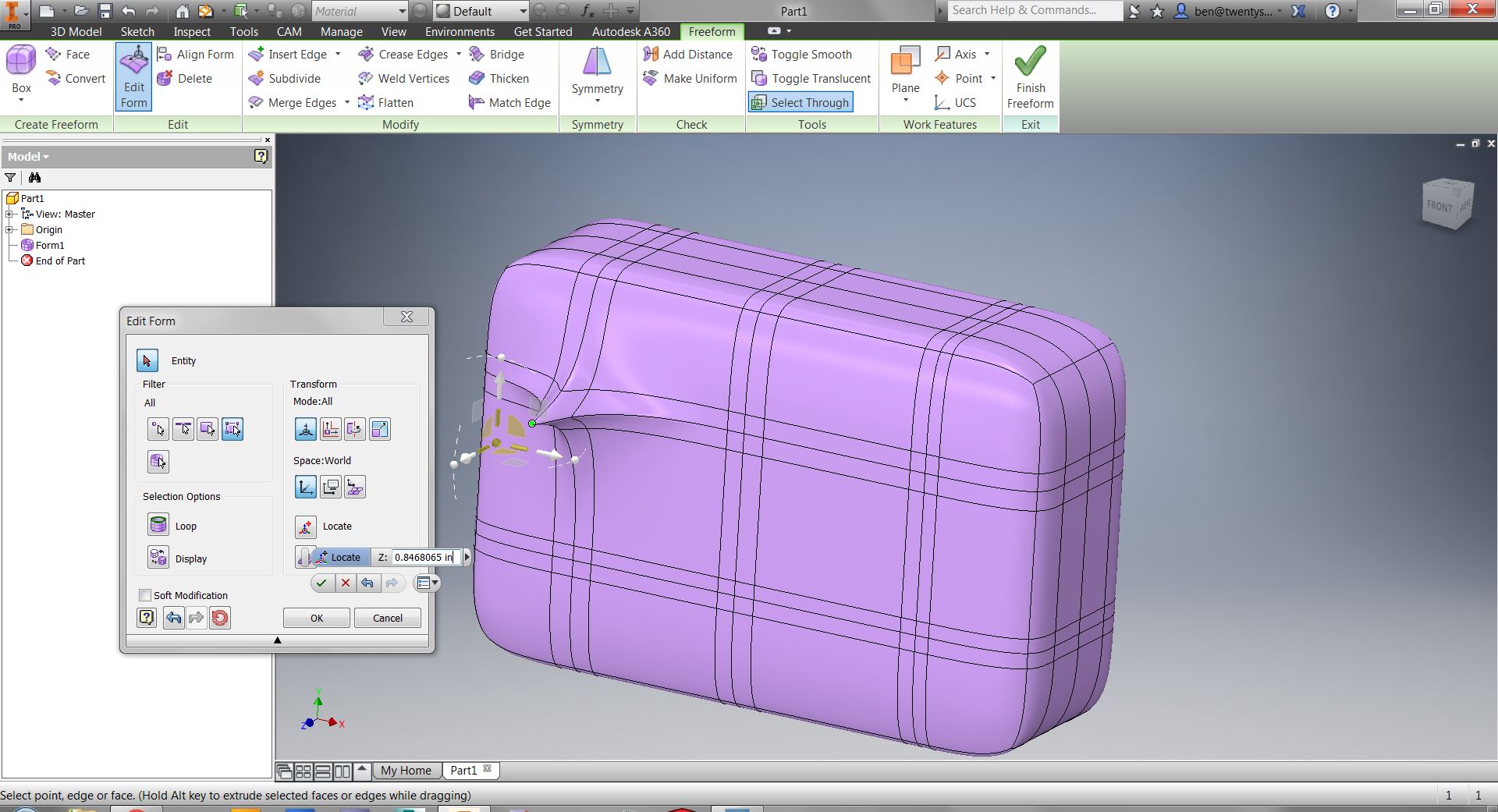
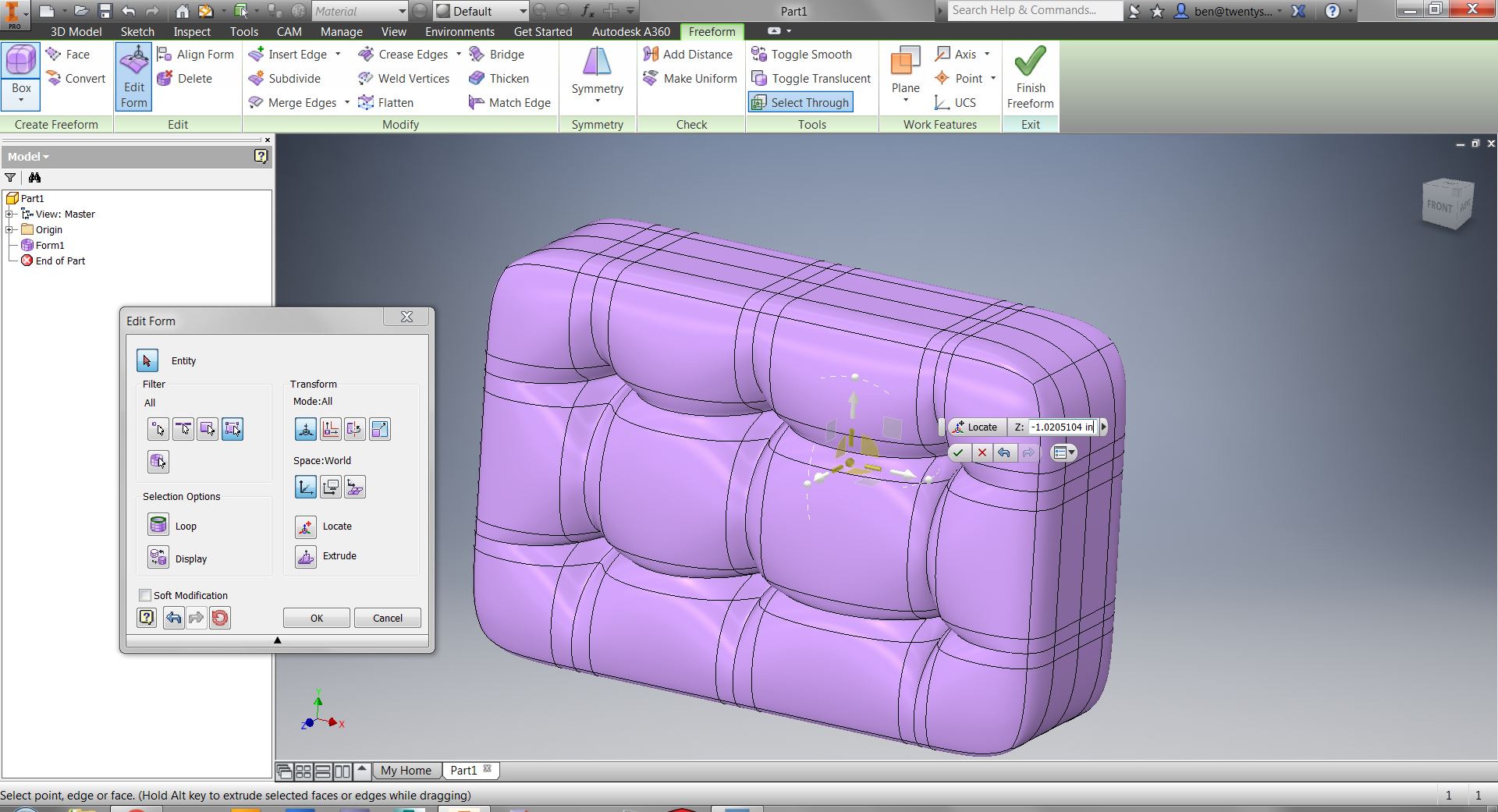
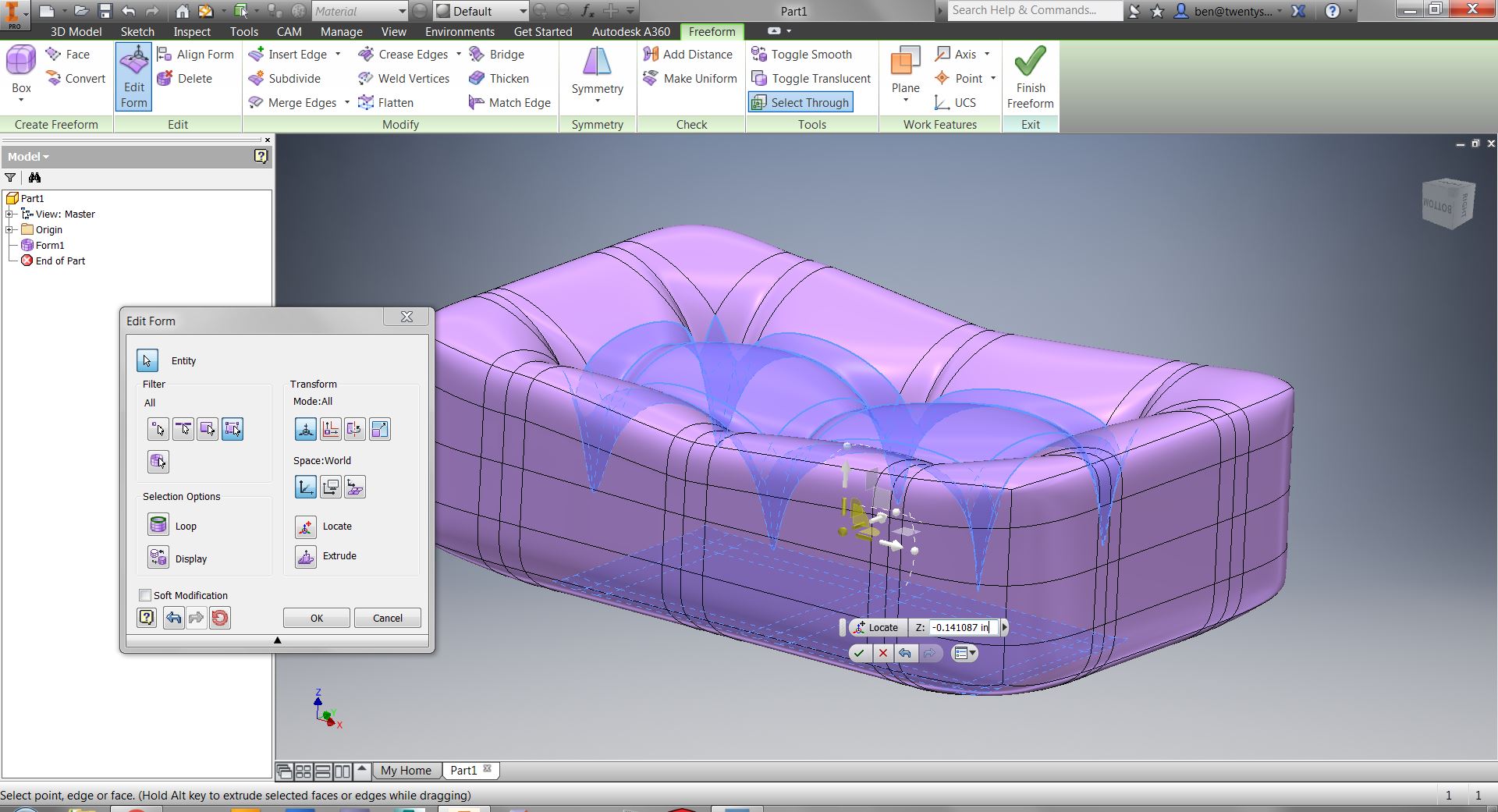
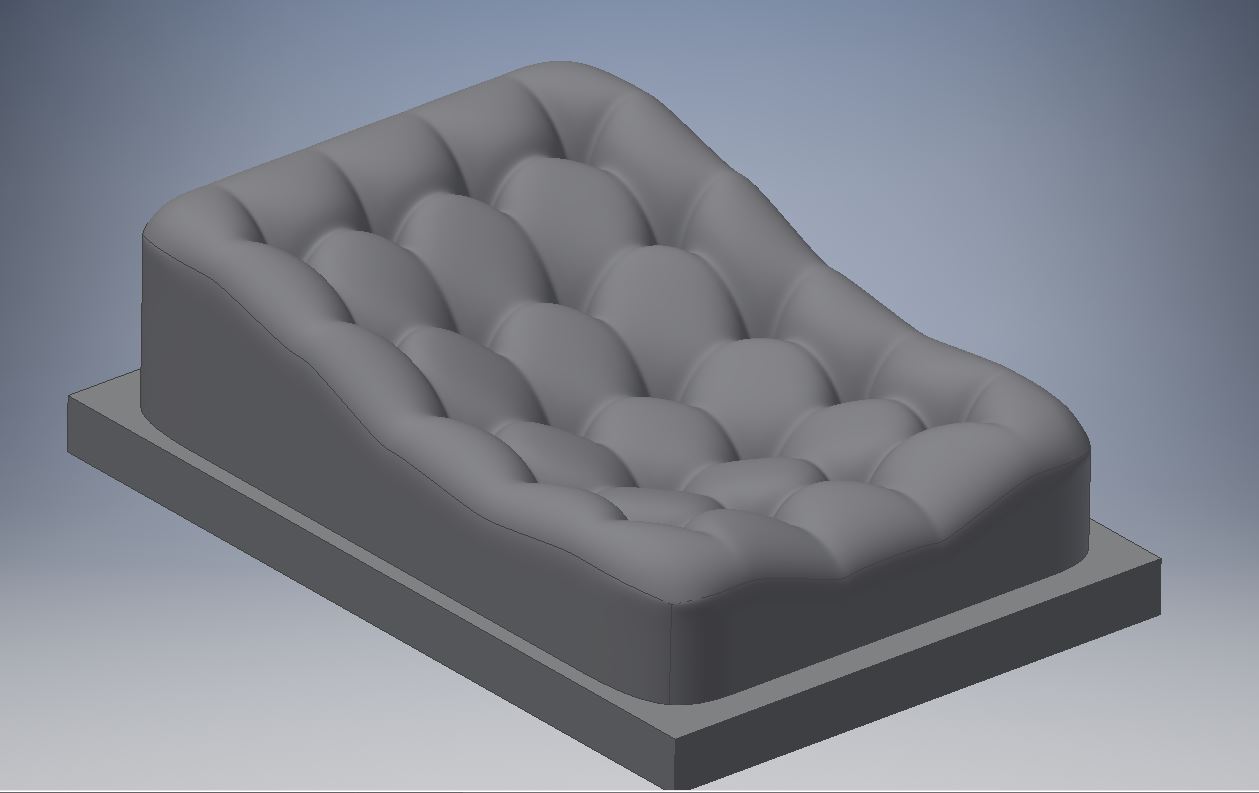
The ability to model with T-splines in a solid-modeling program like Inventor is a big advantage. The hard part is that the T-splines themselves are not really "precise" in any way, and they move around in somewhat unpredictable ways.
In order to get the "pillowtop" look, I began by creating a T-spline box with a ton of control edges. Once you set the size and divisions of your box, AFAIK there isn't a way to go back and edit. I knew I was working with a 6" L x 4" W x 2" H block of aluminum, so I set the size to 5.5" x 3.5" x 2".
I then deleted most of the edges so that I ended up with a grid of t-splines in groups of 3 tightly spaces parallel edges (double-click the edge, then [delete]).
By selecting and pulling on the vertex at the center of each 3 x 3 intersection, the 4-pointed pillow indent is created (select vertex, then [edit form]).
I selected all of the center vertices and pulled all of them down far into the pillow.
I then selected and pushed some of the faces to distort the whole pilowtop. I used a selection box to select an area of faces, which had the side-effect of through-selecting the bottom of the box as well, but I didn't worry about that, since I knew I was going to lop off the bottom and add a solid block there.
I finished the T-spline box and went back to solid mode, where I sliced off the bottom and added a base that measured 6" x 4" x 3/8" (essentially the exact stock I wanted left over at the end of the milling process).
Toolpath in Inventor HSM CAM
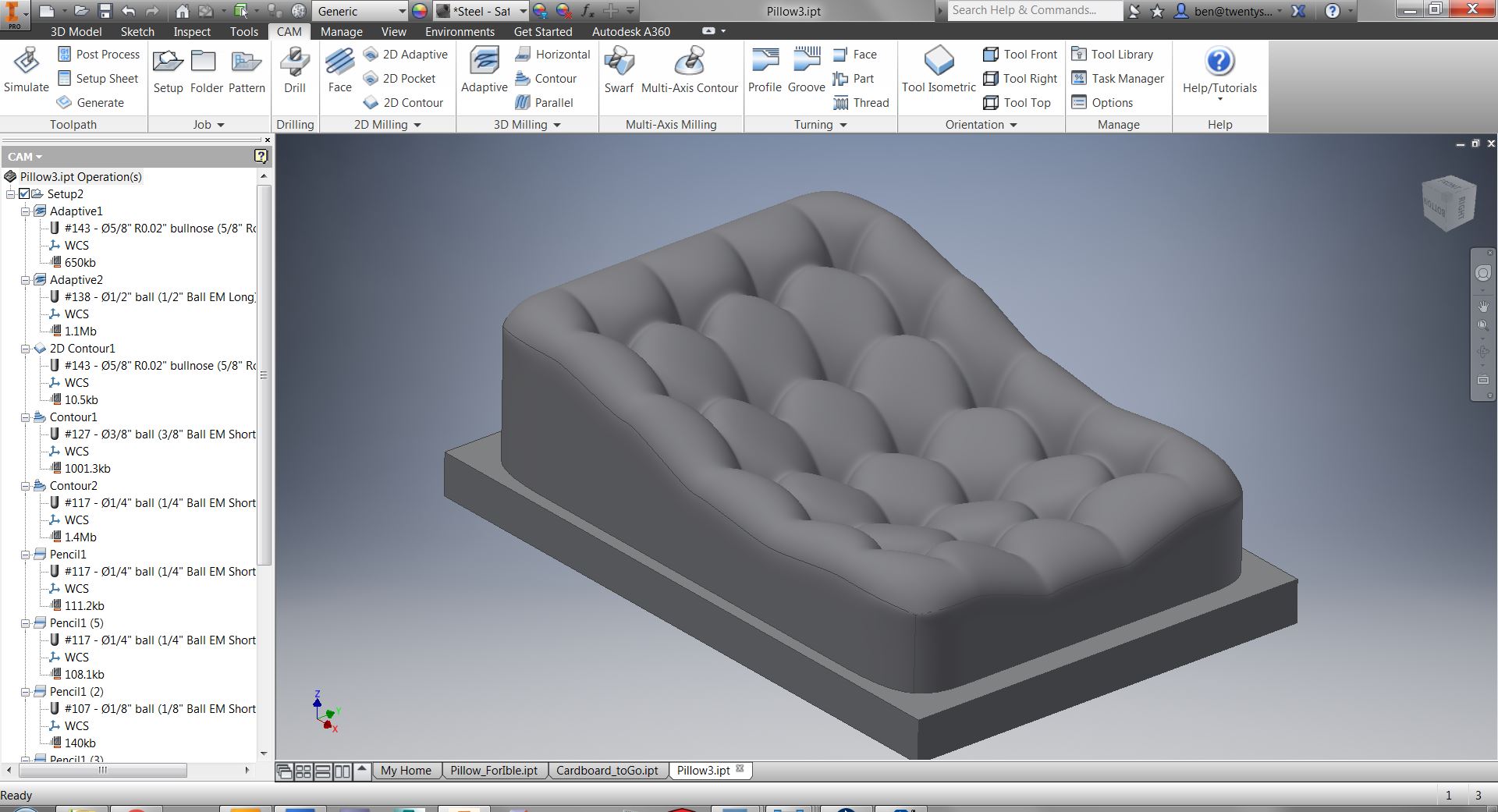
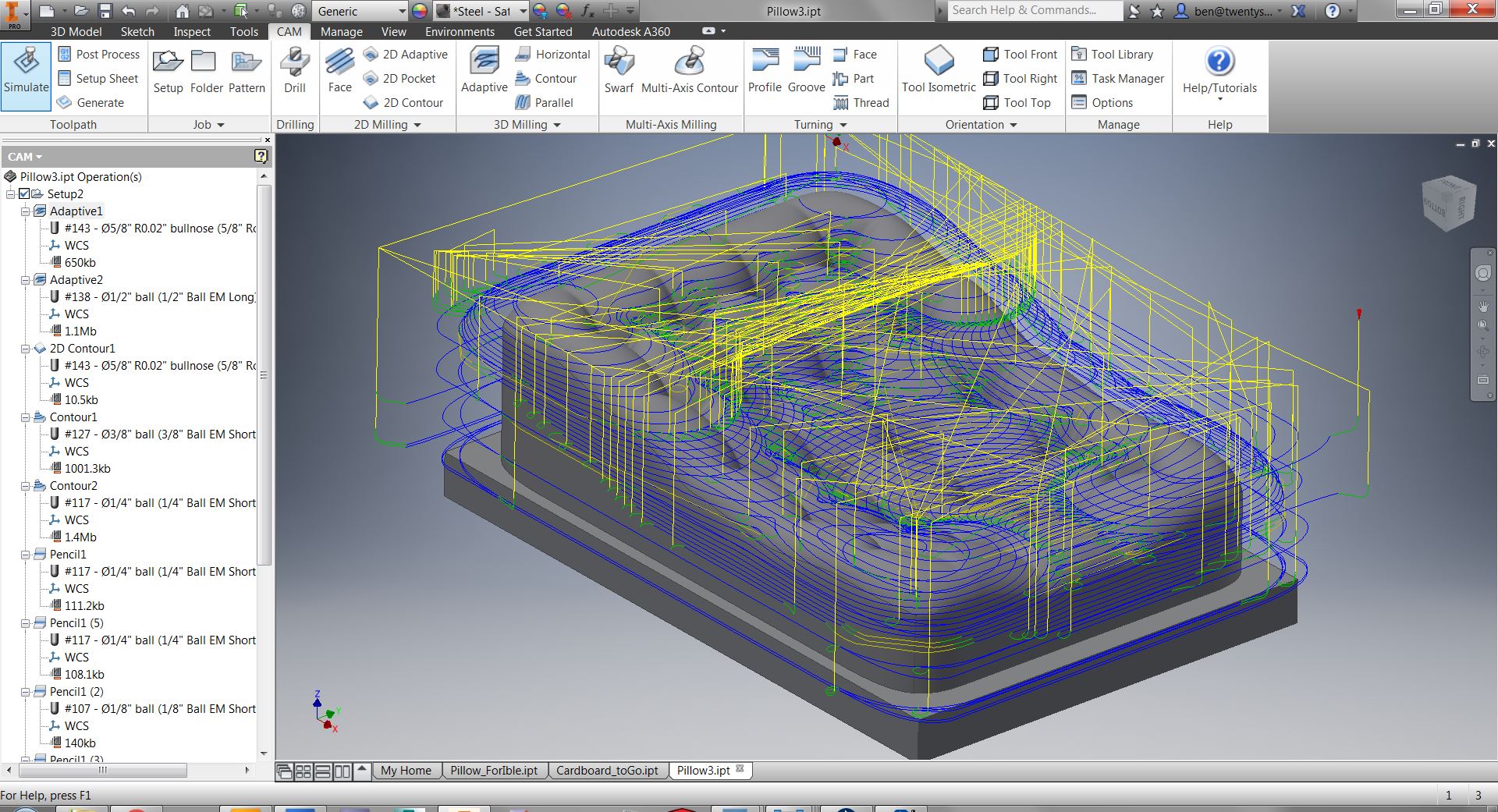
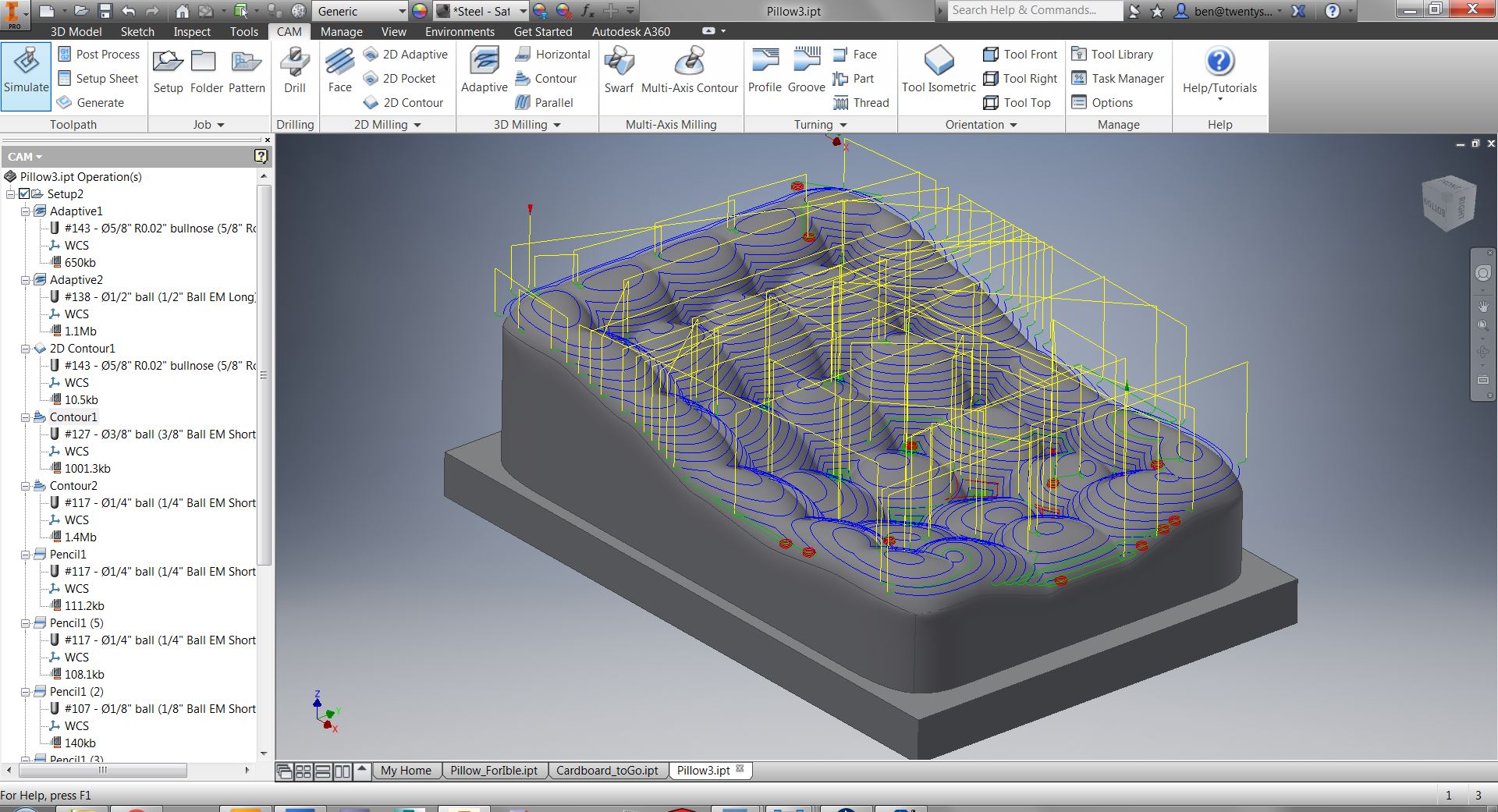
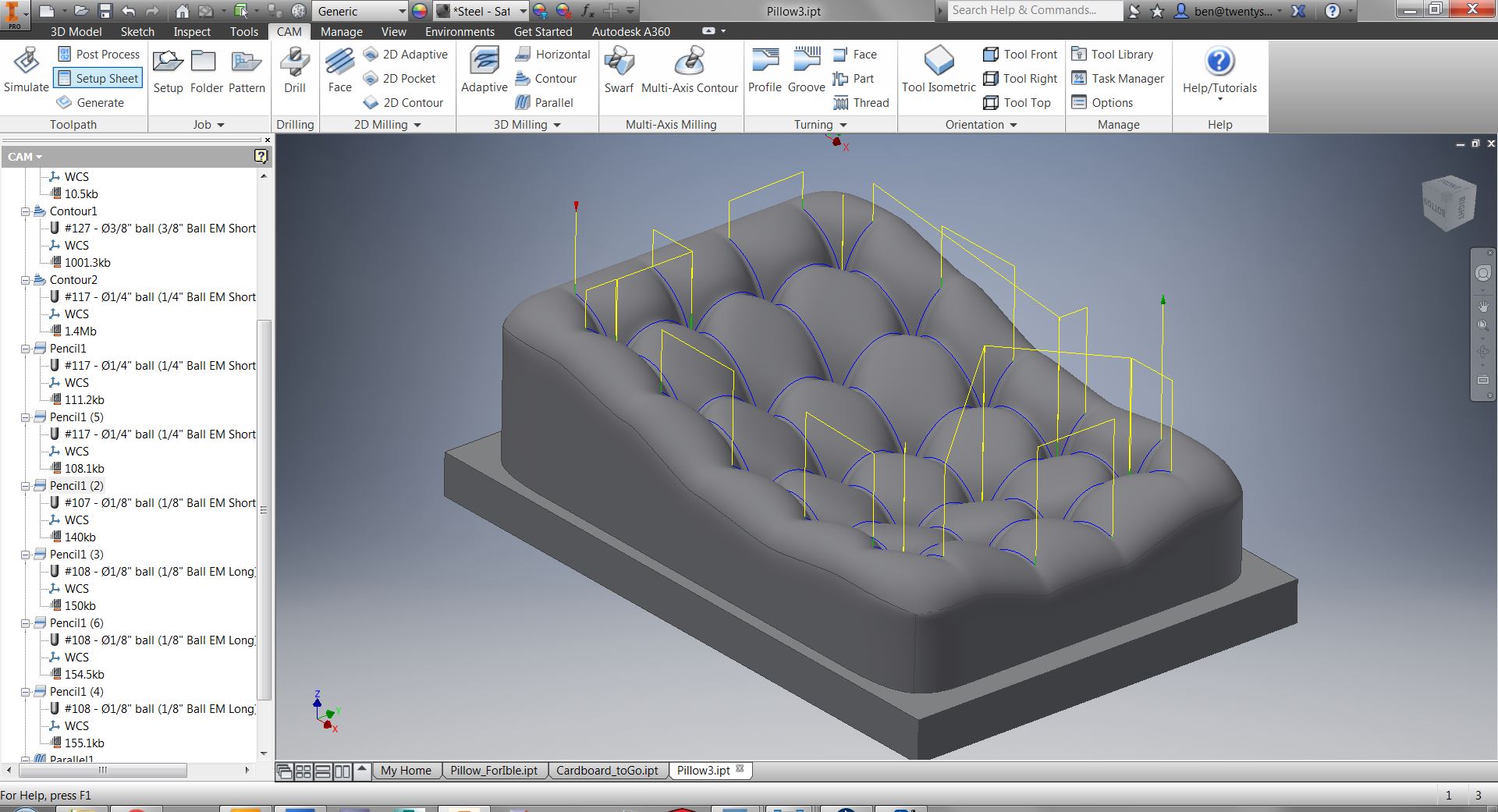
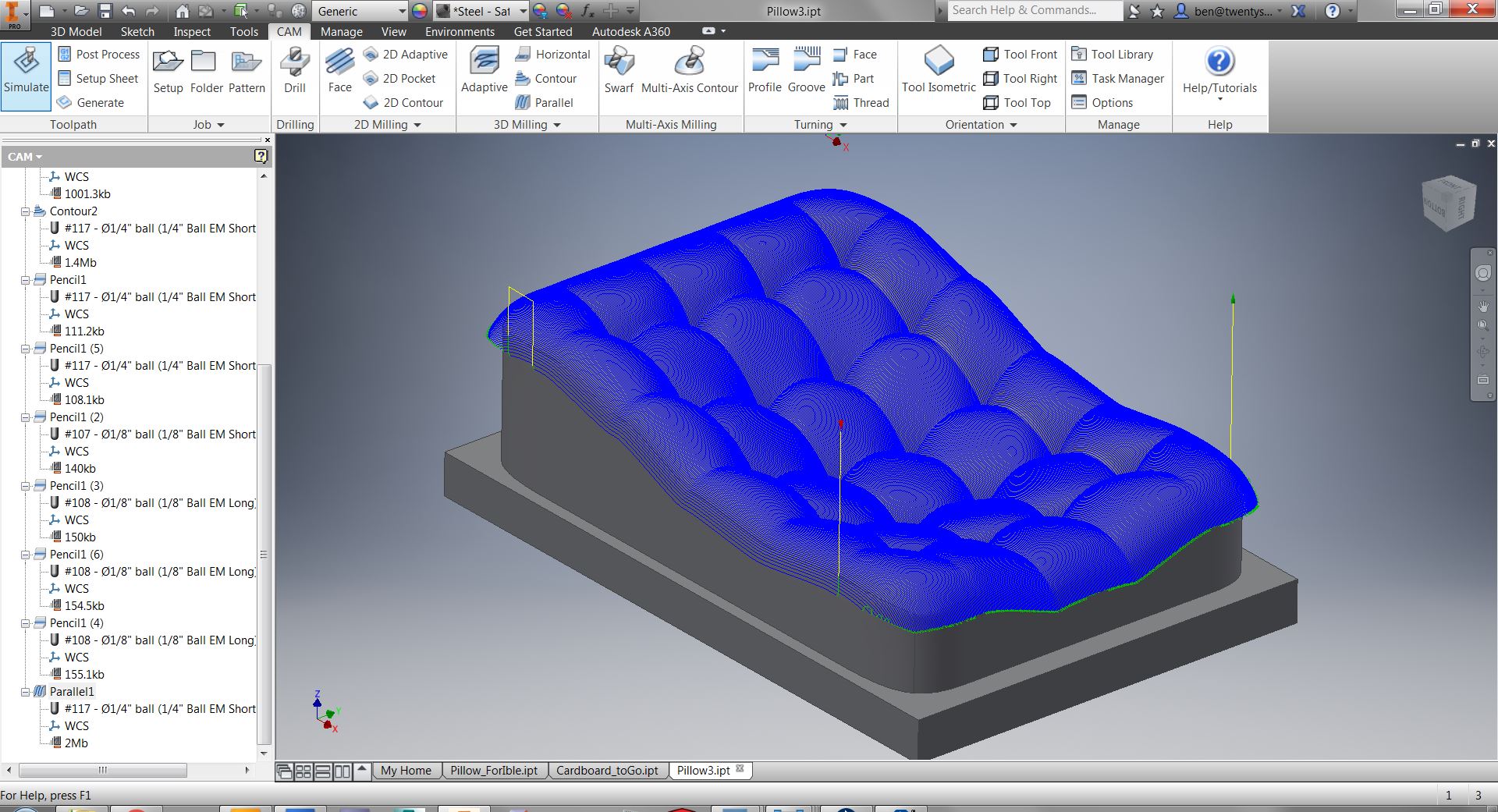
Since this was a learning project, I wanted to be conservative with my toolpaths, i.e.: play it safe.
To that end, I began with two separate Adaptive paths to rough out the shape. I then cleaned up the outside of the pillow, followed by contour passes, and then a series of 6 Pencil paths to hit the creases in the pillowtop, followed by a parallel path. That ended up looking like this:
- Adaptive roughing pass with 5/8" bullnose bit, leaving 0.020" stock
- Adaptive roughing pass with 1/2" ball-end bit, leaving 0.020" stock
- Contour pass with 5/8" bullnose bit, restricted to outer base edge
- Contour pass with 3/8" ball-end bit, restricted to the top of the model, leaving 0.005" stock
- Contour pass with 1/4" ball-end bit, restricted to top of model, leaving 0.002" stock
- Pencil pass with 1/4" ball-end, leaving 0.003" stock
- Pencil pass with 1/4" ball-end, leaving no stock
- Pencil pass with short 1/8" ball-end, leaving 0.015" stock
- Pencil pass with long 1/8" ball-end, leaving 0.005" stock
- Pencil pass with long 1/8" ball-end, leaving 0.002" stock
- Pencil path with long 1/8" ball-end, leaving no stock
- Parallel finishing path with 1/4" ball-end, restricted to top of model (with 0.1245" offset), 0.010" stepover.
You might have the following questions:
Why two roughing passes??
In the future, I would probably eliminate the second roughing pass. I was concerned that the bullnose bit would leave lots of material, and that it would strain the contouring bits to clear it away. In retrospect, it added a lot of machining time for very little benefit.
Why so many Pencil paths??
The dips in the pillowtop are deep, so there was actually quite a difference made by each pass, and slowly easing into those deep recesses ensured that no tools were broken. (Shout-out to Julie at Pier 9 for recommending multiple pencil paths to safely highlight those crease lines!)
What's up with the offset on the last step?
With 3D toolpaths, the tool wants to go over the entire model. With a T-spline-based part, there is not much geometry to select to restrict the tool, so you've got two basic options: restrict using Heights, or using Bounding Box. I needed a bounding box because of the varying heights of my model, and luckily I was able to select the outside border of the pillowtop. Within the Bounding Box dialog, you can choose from 3 options:
- Tool stays inside box
- Tool centerline can move to edge of box
- Tool can move outside box (but no further)
If I selected #3, the tool would plunge to the base of the model and crash. #2 got close, but would leave an unfinished border around the edge. Luckily you can add an offset, so I used #2, but offset the boundary by 0.0005" from the radius of the tool, thus allowing it the just almost exit the boundary. You can see in the last photo that it stays on top of the model, but dips over the edge quite nicely.
Machining on the Haas VF2ss CNC Mill
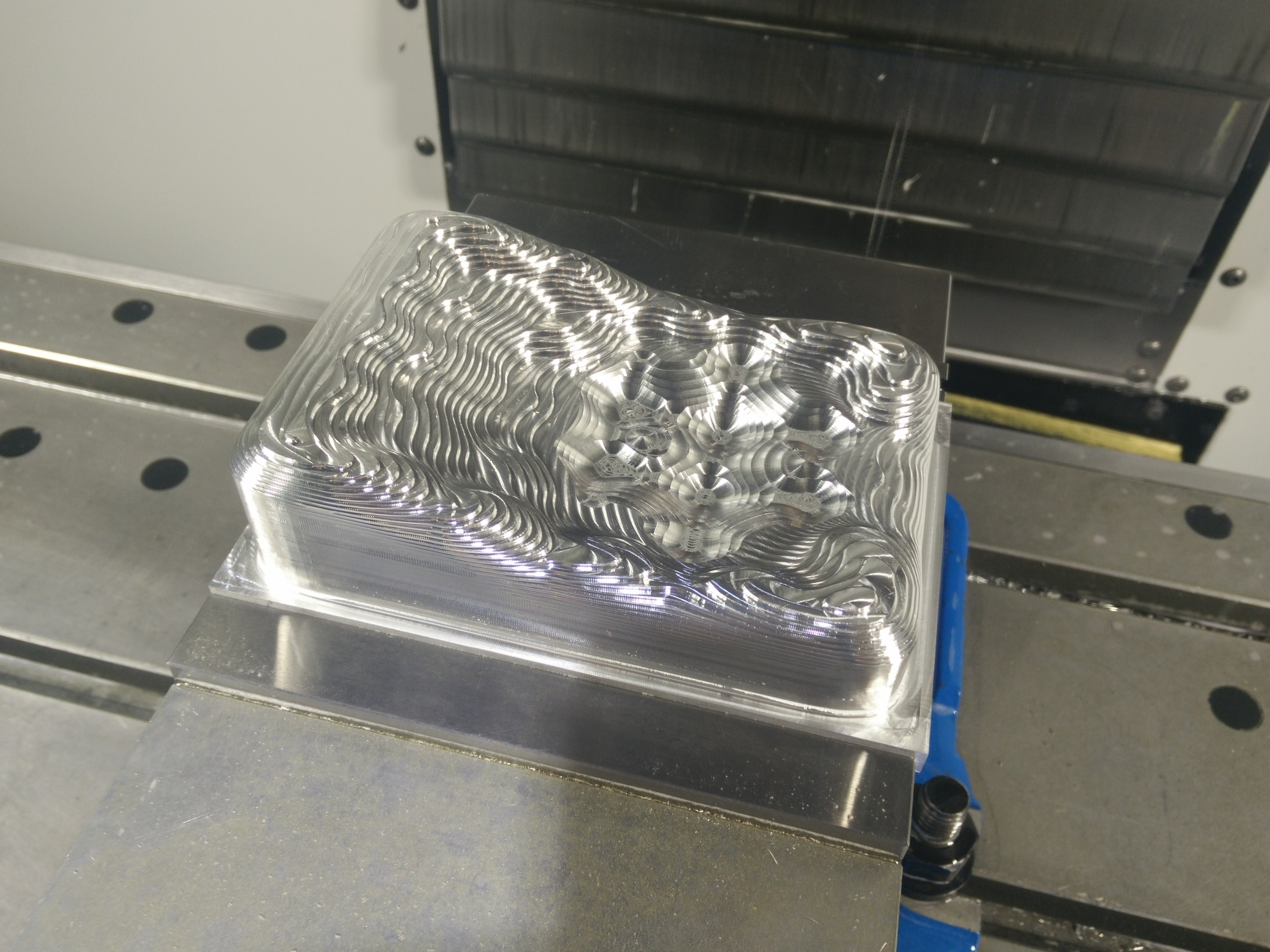
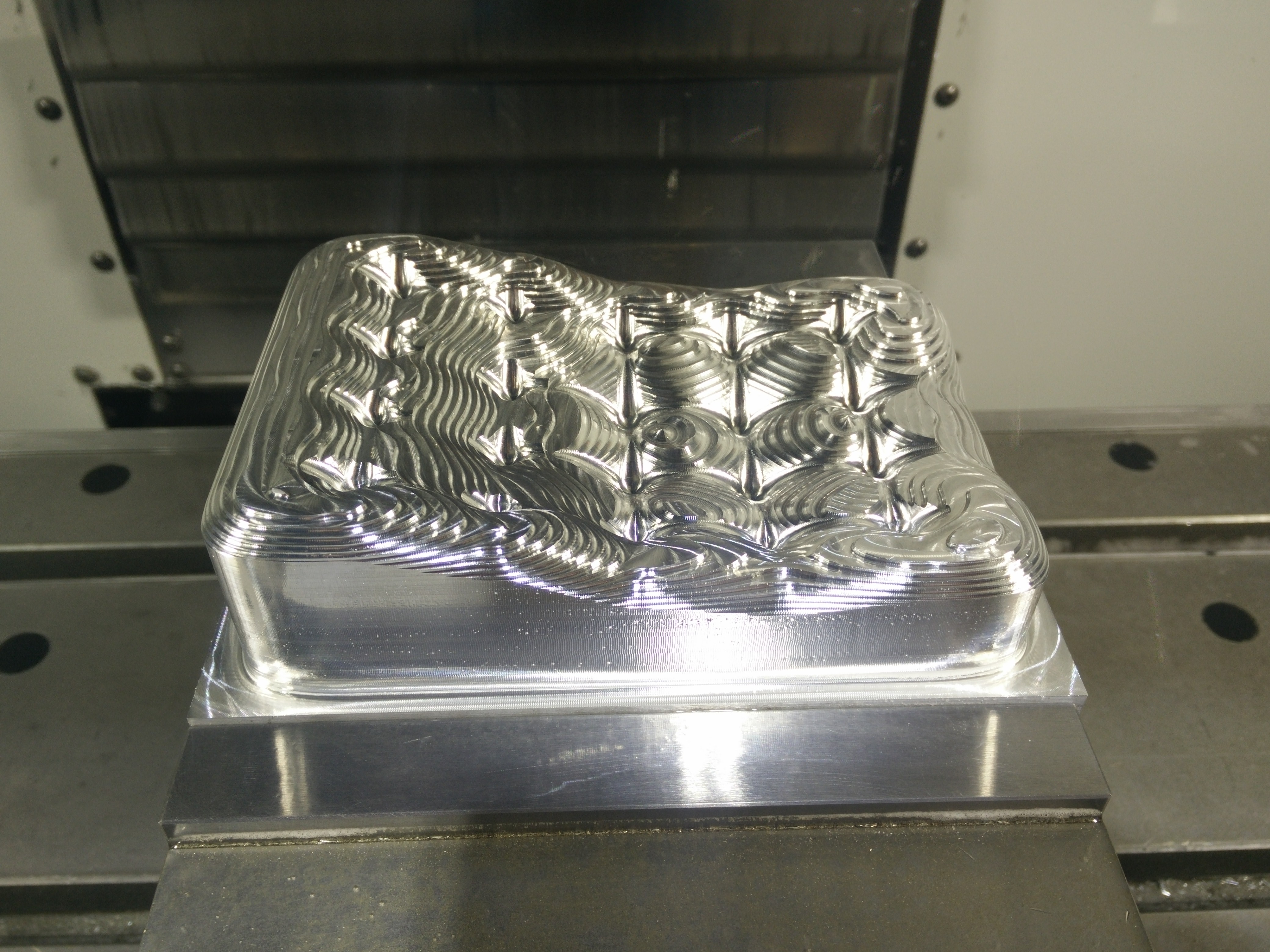
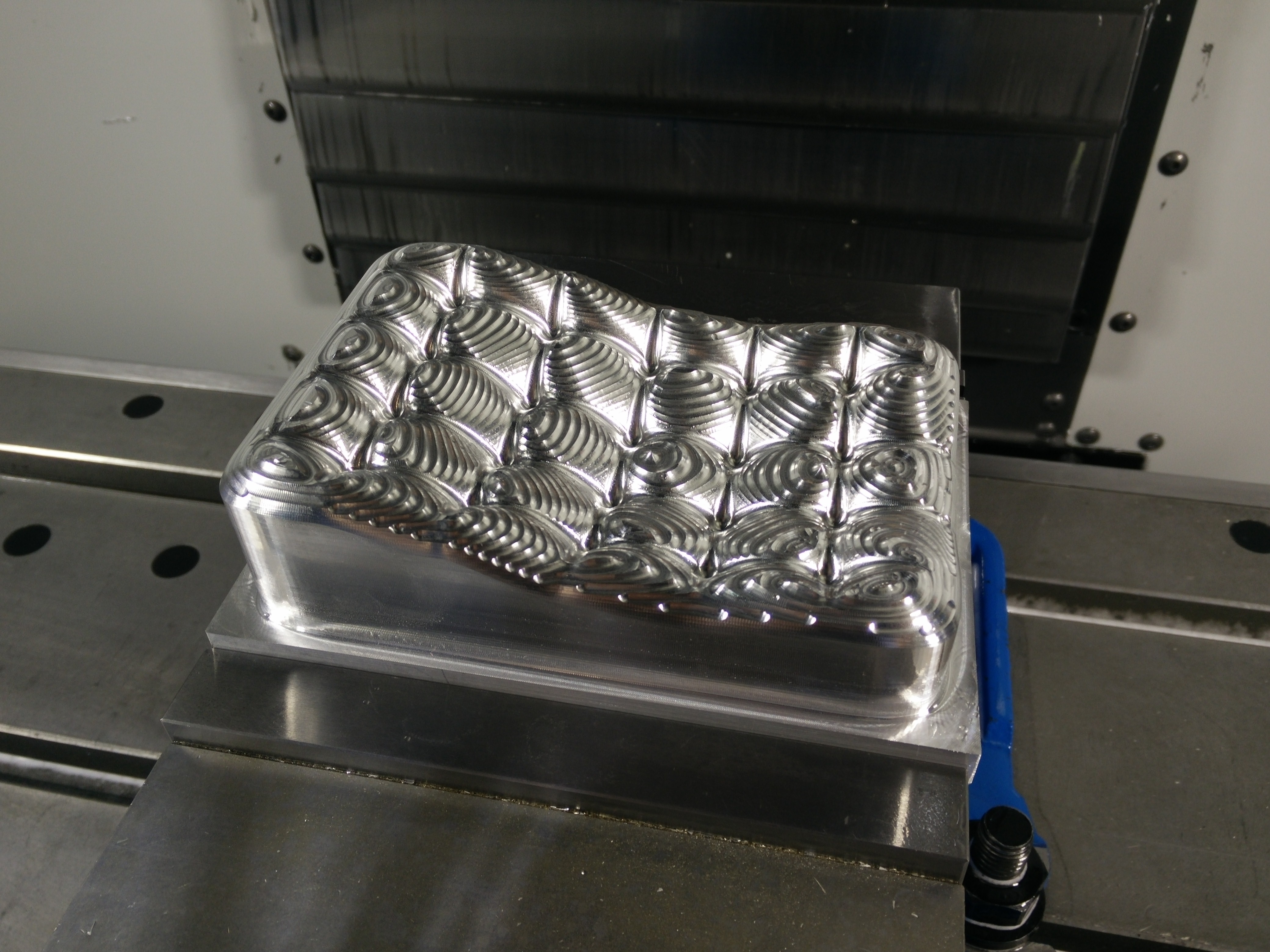
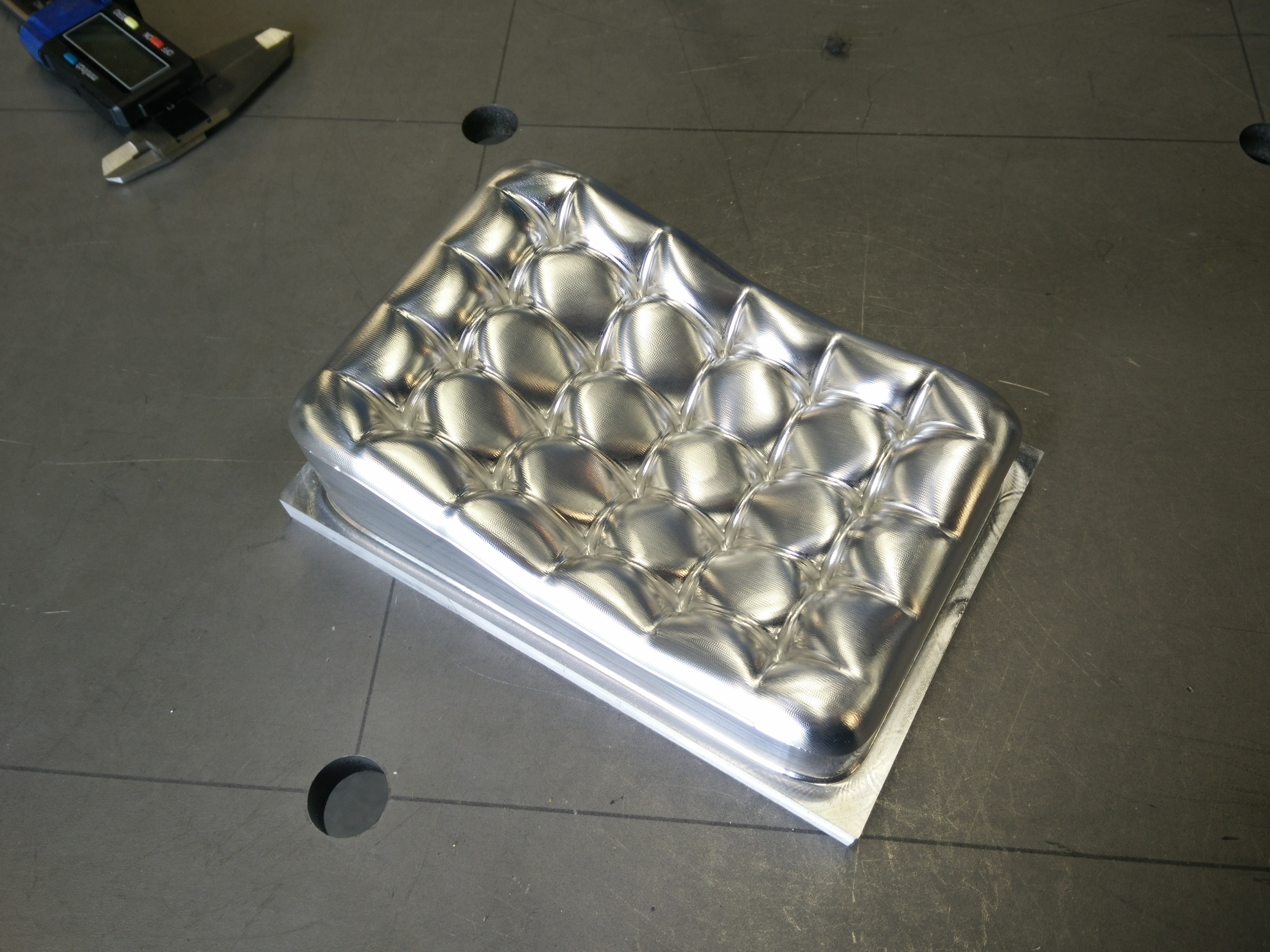
Because of careful planning and a couple important safety steps, milling the Millow on the Haas was a breeze. In order to avoid anything unforseen, I did the following:
- Used Single Block mode at the beginning of each toolpath, so that could verify that the Clearance height of the tool was at a safe height.
- Used the 5% Rapid override so that non-cutting movements would be slow.
- Paused the feed, spindle, and coolant occasionally to allow the doors to be opened and the part examinied (and photographed)
- Put my phone away and stayed focused (except for photo breaks).
In the end, the part came out great. I do wish I had created a 2nd setup to mill away the base after the top was done (as it was I cut it off on a bandsaw, but it took a lot of work). Overall I am very happy and can't wait to make more projects on the Haas!