Mechanical Spider Leg Using a Hydraulic System
by Spidermen in Design > 3D Design
747 Views, 5 Favorites, 0 Comments
Mechanical Spider Leg Using a Hydraulic System
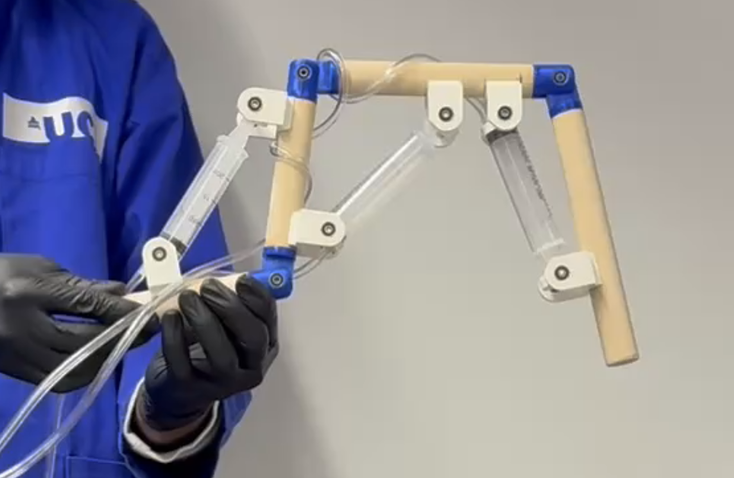
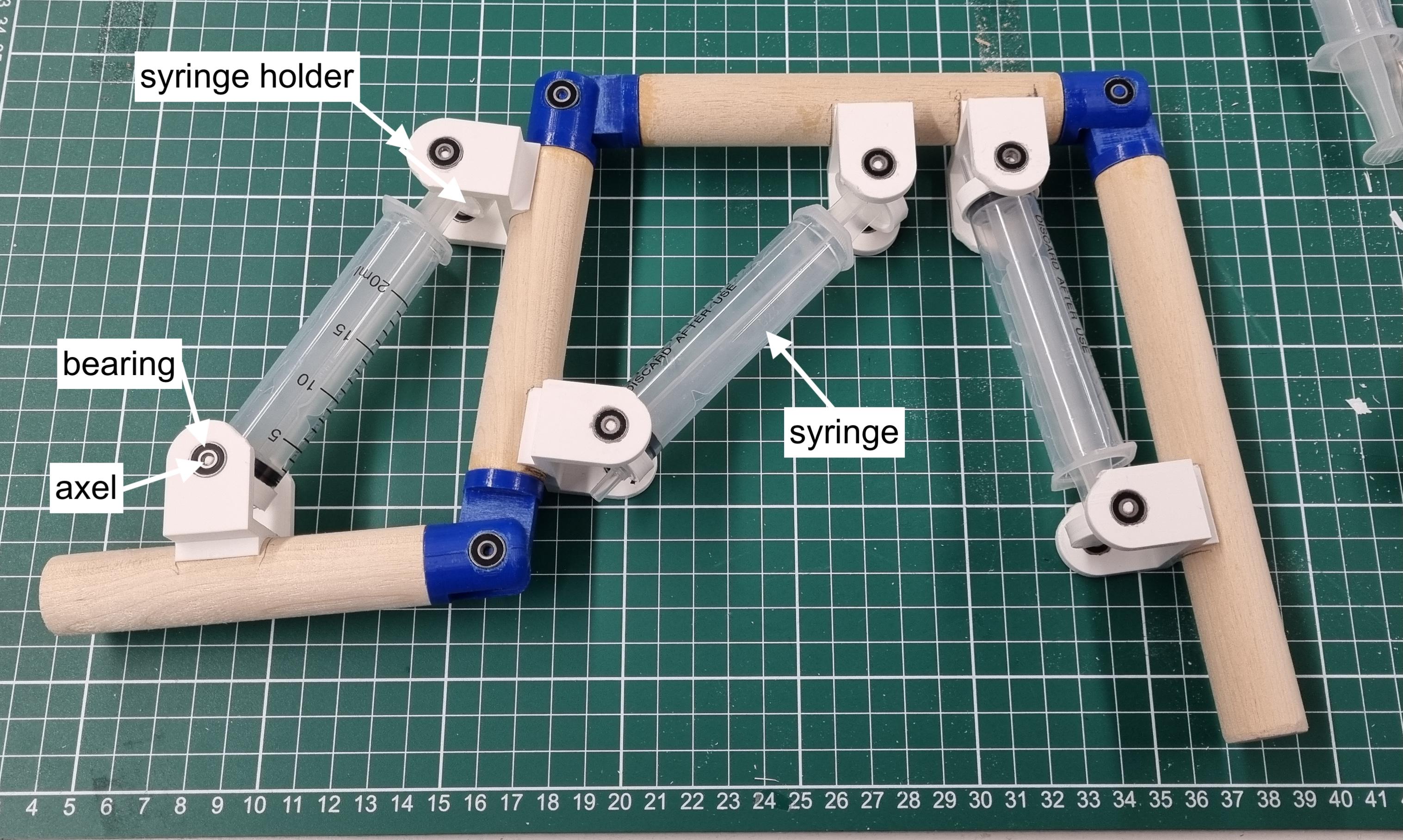

Hey everyone, this is a guide on how to design and manufacture a fully mechanical spider leg. There are no electronics or motors needed, and the whole system is manually operated.
In order to make these spider robots move effectively, we will be analysing the movement of spiders walking and then modelling and manufacturing a design to imitate the spider’s movement mechanically.
For some science: extensor muscles are commonly seen in other animal limbs, while arachnoid legs utilise hydraulic compression or in some specific cases, elastics, in order to rapidly extend their limbs. The abrupt movement paired with the strength from the hydraulics allow them to perform powerful jumps through increasing the haemolymph pressure in their legs.
The anatomy of a spider leg has many components. For this mechanism, the femur, tibia, and metatarsus are implemented only.
Downloads
Supplies
22 mm diameter wooden dowel (1 meter long) - x1
PLA for 3d printing
10 mm outer diameter/3mm inner diameter bearings - x18
Syringes with 20.8 mm diameter - x6
Tubing 1 meter - x3
Super Glue - x1
Saw - x1
File - x1
Sandpaper - x1
Cutting Wooden Dowel
Cut the wooden dowel into three dowels: 140mm (Femur), 170mm (Tibia), and 200 mm (Metatarsus).
Sand the edges smoothly to minimise splinters.
3D Printing the Revolute Joints


Then, we print out the revolute joints (3 of them) which will connect each part of the leg and provide the necessary degree of freedom of movement.
The revolute joints that are created are of two parts: the internal and the external. The measurements of the base of the joints are of the same diameter as the dowels so they can be glued together after.
The axles as well can be printed with the revolute joints.
These revolute joints require support when 3D printed.
Attached the Joints to the Dowels

Once the joints and the axles have been printed, the internal and the external parts of the revolute joint are connected using 2 bearings and an axle.
While the CAD files are designed for bearings of 10mm outer diameter and 3mm inner diameter, if the parts of the joint and axle are not to size, file accordingly.
Then superglue the ends of the joints to the respective ends of the dowels. Make sure that the dowels are connected in ascending magnitudes (140,170,200) and are all connected within the same plane.
3D Printing the Hydraulic System Holder (syringe Holders)

To secure the syringes to the spider leg for hydraulic actuation, we will then create a holder for the syringes such that they can be attached to the wooden dowels. The holders will hold the syringe by having a cap connected to it using bearings and axles. The cap itself will hold the syringe or attach to the syringe.
We can 3D print the holders (make sure to include tree supports when printing).
Then we can connect the caps to the holders using the axles and the bearings provided. File if required.
After that, superglue the holders towards the middle of the dowels such that there is enough space for the syringe to contract and expand fully. Make sure the holders are superglued on the same side of the dowels.
Assembling the Spider Leg
Now, we can plug the syringes to the holders and connect each of the tubing to the end of the syringes. On the other ends of the tubing, connect the other three syringes. You can add water in this step if you want, but just air works too!
Now, you have a working spider leg which can contract and expand for traversal by pushing and pulling the syringes (you may need 2 other friends to hold and use the syringes)!
Conclusion
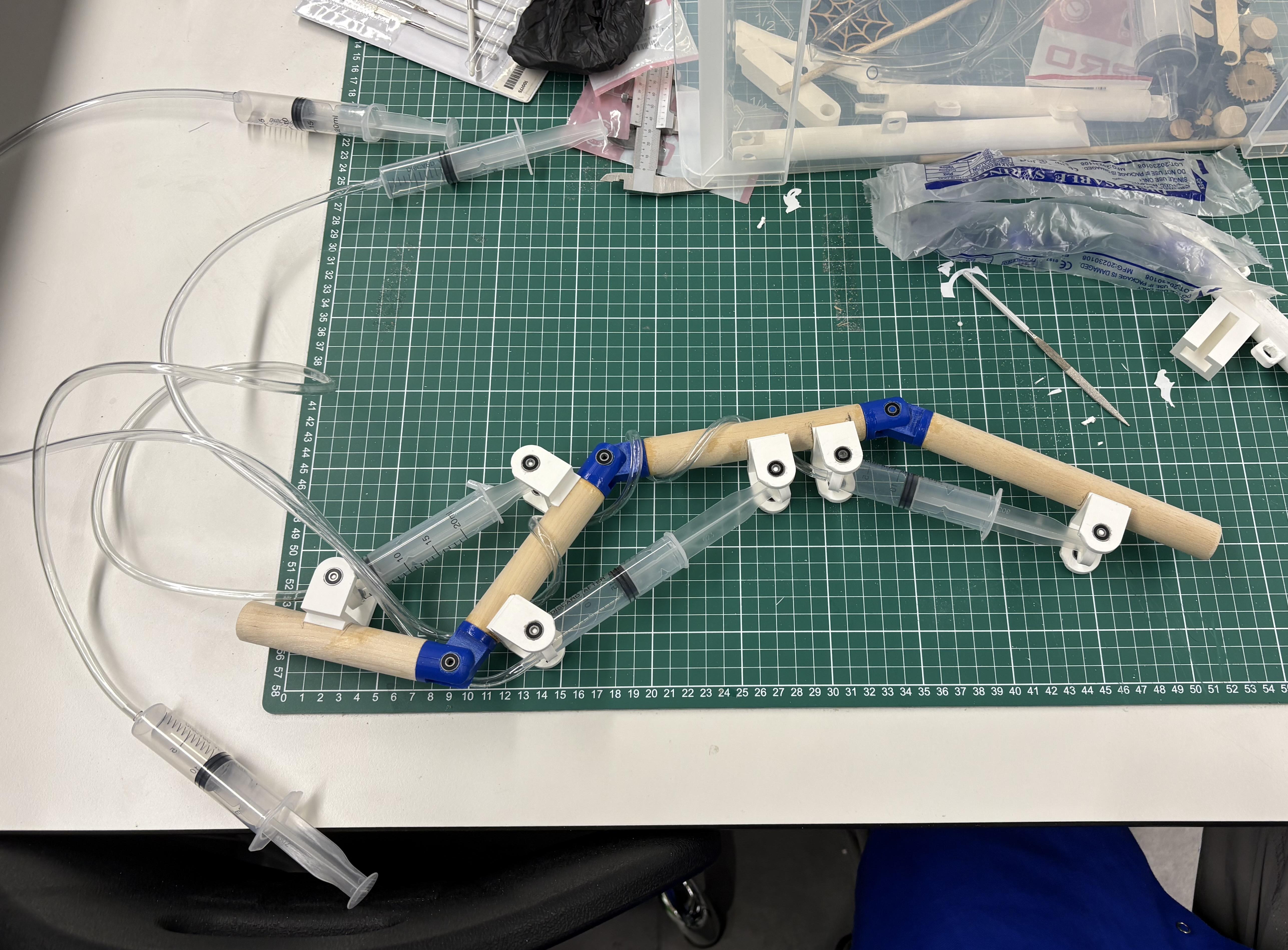
Now, you have a working spider leg! 🕷️
Thank you for reading and I hope you enjoyed this Instructables guide!