How to Make a Sega DreamCast Console Into a Battery Powered Handheld Portable
by MODDEDbyBACTERIA in Circuits > Electronics
54910 Views, 62 Favorites, 0 Comments
How to Make a Sega DreamCast Console Into a Battery Powered Handheld Portable


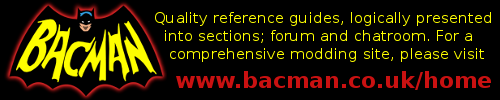
First pic is of the finished item, as per last page of the guide.
INTRODUCTION:
There have only been about a dozen such units made in the past from different modders, one of those was mine a few years ago. I therefore thought it would be nice to make a guide to show others how to make such a unit themselves which is the reason for this tutorial.
I will keep the guide easy to follow and logical.
The guide should be accurate for any reader, apart from the screen used and its wiring; the DreamCast can use VGA, S-video or composite video output so the choice for a screen to use is large; all you need to know is the voltage (and what it needs), and the connections for the video signals - any queries, there are many screens discussed in general on my forum, www.bacman.co.uk/home so if you join up and post your project, I and others will give you assistance in that area too, and you can post your project in progress so when you need advice we can provide it.
The main issue with a DreamCast console unit is because they are a few years old, many consoles don't play many games any more, so you need to test your unmodded console to check it works, plays most games you have and also the controller works too. In my experience about 1/3 of consoles still work fine, others have issues, hence why you need to use a trusted console for a project.
Don't worry, you will not have to do any board cutting or reductions, so the actual build of the system is far easier and less liable to have problems.
The point of course of making a DreamCast into a portable by making a custom case, attaching a screen and controller, and batteries, is to play the system free of cables and not needing to run off the mains for power or use your home television.
One thing though, the DreamCast is a thick unit, there is little you can do about that, and also you need to use the system comfortably - so don't expect to have a slim or small console handheld with a DreamCast - it isn't going to happen. Sure, you can make a system about 3/4 the size of the unit i'm making here however that will need a lot of skill to make well, and defeats the object of a tutorial like this as it would be aimed at an audience that were experienced in modding rather than someone with little experience, which is where this tutorial is aimed at.
In saying that, you will need some knowledge on basic soldering, step-down regulators, voltages and very basic electronics knowledge - again, the reference section on my forum, www.bacman.co.uk/home is there with the guides if you need that knowledge and hand-holding.
INTRODUCTION:
There have only been about a dozen such units made in the past from different modders, one of those was mine a few years ago. I therefore thought it would be nice to make a guide to show others how to make such a unit themselves which is the reason for this tutorial.
I will keep the guide easy to follow and logical.
The guide should be accurate for any reader, apart from the screen used and its wiring; the DreamCast can use VGA, S-video or composite video output so the choice for a screen to use is large; all you need to know is the voltage (and what it needs), and the connections for the video signals - any queries, there are many screens discussed in general on my forum, www.bacman.co.uk/home so if you join up and post your project, I and others will give you assistance in that area too, and you can post your project in progress so when you need advice we can provide it.
The main issue with a DreamCast console unit is because they are a few years old, many consoles don't play many games any more, so you need to test your unmodded console to check it works, plays most games you have and also the controller works too. In my experience about 1/3 of consoles still work fine, others have issues, hence why you need to use a trusted console for a project.
Don't worry, you will not have to do any board cutting or reductions, so the actual build of the system is far easier and less liable to have problems.
The point of course of making a DreamCast into a portable by making a custom case, attaching a screen and controller, and batteries, is to play the system free of cables and not needing to run off the mains for power or use your home television.
One thing though, the DreamCast is a thick unit, there is little you can do about that, and also you need to use the system comfortably - so don't expect to have a slim or small console handheld with a DreamCast - it isn't going to happen. Sure, you can make a system about 3/4 the size of the unit i'm making here however that will need a lot of skill to make well, and defeats the object of a tutorial like this as it would be aimed at an audience that were experienced in modding rather than someone with little experience, which is where this tutorial is aimed at.
In saying that, you will need some knowledge on basic soldering, step-down regulators, voltages and very basic electronics knowledge - again, the reference section on my forum, www.bacman.co.uk/home is there with the guides if you need that knowledge and hand-holding.
Disassemble the Console




Remove the standard screws from the base of the console.
Remove the components, steps as below in the photo.
The transformer takes mains power AC voltage and converts into three DC voltages, 3.3v, 5v and 12v. That is why we can run the console off batteries; the 12v line runs fine using 7.4v Li-ion batteries, and we just use a regulator for the 5v and 3.3v lines. More on that later.
Remove the components, steps as below in the photo.
The transformer takes mains power AC voltage and converts into three DC voltages, 3.3v, 5v and 12v. That is why we can run the console off batteries; the 12v line runs fine using 7.4v Li-ion batteries, and we just use a regulator for the 5v and 3.3v lines. More on that later.
Trim the Metal Drive Support for Better Airflow





Although we are going to use the actual casing from the DreamCast console (so don't throw any of it away), the console gets hot normally, so we need to take steps to keep it cooler for a portable. That means more fans, using heatsinks not metal plates and also increasing airflow.
Use screwdriver to pry off the metal plate that was connected to the chips before, it isn't needed (pic 1).
Be very careful when cutting metal not to get shards of metal in your eyes (wear goggles) and also make sure you are not going to slice off your finger if the cutting tools slip, hold the tools properly, and have fingers out of the way.
Score the metal fairly deeply as per pics below, then bend to snap the metal off. When you cut metal (I used a metal circular cutter on my Dremel), use a sanding drum or similar to remove any metal shards, if you don't and there are little metal shavings, they could cause shorts on your motherboard and kill it, so always take precautions.
The point is to expose the chips on the motherboard to allow space for heatsinks and decent airflow (last pic).
Use screwdriver to pry off the metal plate that was connected to the chips before, it isn't needed (pic 1).
Be very careful when cutting metal not to get shards of metal in your eyes (wear goggles) and also make sure you are not going to slice off your finger if the cutting tools slip, hold the tools properly, and have fingers out of the way.
Score the metal fairly deeply as per pics below, then bend to snap the metal off. When you cut metal (I used a metal circular cutter on my Dremel), use a sanding drum or similar to remove any metal shards, if you don't and there are little metal shavings, they could cause shorts on your motherboard and kill it, so always take precautions.
The point is to expose the chips on the motherboard to allow space for heatsinks and decent airflow (last pic).
Trim the Drive Unit Assembly to Improve Airflow






The disc drive unit needs the side removed that goes over the chips on the motherboard, to allow for more airflow.
Take the drive unit and using a circular cutter on your Dremel (pic 1) cut through the metal side to remove it, taking care. Leave the end supports as per (pic 2).
Take off the metal plate from the underside of the drive unit (pic 2) and (pic 3).
Cut off the metal as per pic - you can use scissors on this if you prefer as the metal is quite thin. Finish off as usual with a sanding drum to remove any metal shards. (pic4, (pic 5).
Result (pic 6).
Take the drive unit and using a circular cutter on your Dremel (pic 1) cut through the metal side to remove it, taking care. Leave the end supports as per (pic 2).
Take off the metal plate from the underside of the drive unit (pic 2) and (pic 3).
Cut off the metal as per pic - you can use scissors on this if you prefer as the metal is quite thin. Finish off as usual with a sanding drum to remove any metal shards. (pic4, (pic 5).
Result (pic 6).
Heatsinks!




The console originally used the metal sheet to cool the chips originally, which is a reason the console gets hot normally, we want to improve the airflow in the system and use heatsinks which are far more efficient. A hot portable console system is inviting problems, we want the system as cool as we reasonably can make it.
So, use some Arctic Silver thermal paste on a cleaned and smooth heatsink, about the amount of a grain of rice (pic 1). Smear the paste with a piece of flat card, so the covering is thin but the paste covers the heatsink backing. Do same for the chips too (pic 2).
Apply a dot of superglue on each corner of the chip so the heatsink will stay on it firmly (pic 3).
Press the heatsink to the chip for a few seconds (press lightly). (pic 4)
Then do same for the other chip (as per pic 4).
So, use some Arctic Silver thermal paste on a cleaned and smooth heatsink, about the amount of a grain of rice (pic 1). Smear the paste with a piece of flat card, so the covering is thin but the paste covers the heatsink backing. Do same for the chips too (pic 2).
Apply a dot of superglue on each corner of the chip so the heatsink will stay on it firmly (pic 3).
Press the heatsink to the chip for a few seconds (press lightly). (pic 4)
Then do same for the other chip (as per pic 4).
Assemble


Put the drive unit in place, you will see there is a nice gap now for the heatsinks to allow good airflow. Use string to secure the metal place to the motherboard in places where the screws used to do it, to keep the units together.
Voltages




As mentioned, the DreamCast needs three voltages. For the 5v line, use a 7805 with a heatsink on the back of it, and for the 3.3v line use a step-down regulator (pic 1) (look in the "batteries and voltages" reference section on my forum for various options here, www.made-by-bacteria.com
That will allow the system to run off the 7.4v battery packs (7.4v can power the 12v DreamCast line so that's covered).
Use snippers to cut off the legs on the post where the voltages go to the board. (pic 2).
Apply a little flux to the pins in (pic 3), then solder, this "tinning" allows for a far stronger solder joint.
Hot glue a spare fan near the heatsinks and wire it to the voltage lines - I used a 5v fan from a dead DreamCast, so connected to the 5v voltage line (and of course ground) (pic 4)
That will allow the system to run off the 7.4v battery packs (7.4v can power the 12v DreamCast line so that's covered).
Use snippers to cut off the legs on the post where the voltages go to the board. (pic 2).
Apply a little flux to the pins in (pic 3), then solder, this "tinning" allows for a far stronger solder joint.
Hot glue a spare fan near the heatsinks and wire it to the voltage lines - I used a 5v fan from a dead DreamCast, so connected to the 5v voltage line (and of course ground) (pic 4)
Optional Step - Relocate the Video and Serial Ports





You don't need to do this process unless you want the option to connect to an external television rather than just the internal one we will use for the portable; if you want this facility then you will want to relocate one or both of these ports (you don't need to relocate the serial connection really, just the video one) so they are able to integrate into your portable's case where you want them located.
First step is just to snip the edge connectors that hold the ports to the motherboard in place, two on each port (pic 1).
Bend off the metal clips and lift the ports up gently (pic 2). Bend them back and forth, gently, until the pins snap off.
Run your soldering iron over the pins, removing the part of the pins still attached, this not only removes those bits of metal debris but also re-solders the joins too, make sure of course you don't "bridge" any connections (ie short across the connections), if you do, run the soldering iron over them to remove the excess solder and therefore the bridge. (pic 3)
Flux and tin the pins (as per step 6), and solder wires to the pin connections (pic 4), then use hot glue to keep them in position, you notice in (pic 5) I have laid the wires flat so it is easy to see what connects to what; hot glue sticks the wires to a piece of paper.
First step is just to snip the edge connectors that hold the ports to the motherboard in place, two on each port (pic 1).
Bend off the metal clips and lift the ports up gently (pic 2). Bend them back and forth, gently, until the pins snap off.
Run your soldering iron over the pins, removing the part of the pins still attached, this not only removes those bits of metal debris but also re-solders the joins too, make sure of course you don't "bridge" any connections (ie short across the connections), if you do, run the soldering iron over them to remove the excess solder and therefore the bridge. (pic 3)
Flux and tin the pins (as per step 6), and solder wires to the pin connections (pic 4), then use hot glue to keep them in position, you notice in (pic 5) I have laid the wires flat so it is easy to see what connects to what; hot glue sticks the wires to a piece of paper.
Video and Audio Connection



The DreamCast can output VGA, S-video and composite, switchable by connecting one/two points to ground, as per the illustration (pic 1).
The example in (pic 2) was for VGA output. Note, it is a good idea to use a 150 ohm resistor on the V-Sync and also H-Sync lines if you are using VGA mode and the image is too bright, and if the image quality isn't totally stable, use a 220uf capacitor on each of the Red, Green and Blue lines (ie RGB).
(pic 3) is a crude diagram but shows the pinout for what the connections are on the back of the board (ie pic 1).
As to the screen, there are many many screens out there, what you want ideally is a 7" or 8" screen, ideally 4:3 format as that's better than widescreen; and ideally runs off 7.4v, that way you don't need to use a step-up regulator to supply the screen with more voltage if it needs it. Many screens that run off 12v run off 7.4v, not all though.
I can't provide a pinout for the screen as each one is different. The reference section on my forum shows many screens, so if in doubt, use one of those, and ask on the forum if you need help (the projects work in progress forum section). Same true for audio - if your screen does not have an audio amp built in, then use a small one (again, in the reference section on my forum www.made-by-bacteria.com )
The example in (pic 2) was for VGA output. Note, it is a good idea to use a 150 ohm resistor on the V-Sync and also H-Sync lines if you are using VGA mode and the image is too bright, and if the image quality isn't totally stable, use a 220uf capacitor on each of the Red, Green and Blue lines (ie RGB).
(pic 3) is a crude diagram but shows the pinout for what the connections are on the back of the board (ie pic 1).
As to the screen, there are many many screens out there, what you want ideally is a 7" or 8" screen, ideally 4:3 format as that's better than widescreen; and ideally runs off 7.4v, that way you don't need to use a step-up regulator to supply the screen with more voltage if it needs it. Many screens that run off 12v run off 7.4v, not all though.
I can't provide a pinout for the screen as each one is different. The reference section on my forum shows many screens, so if in doubt, use one of those, and ask on the forum if you need help (the projects work in progress forum section). Same true for audio - if your screen does not have an audio amp built in, then use a small one (again, in the reference section on my forum www.made-by-bacteria.com )
Test System


ALWAYS test your system as you progress in your project, then it makes it easy to troubleshoot if you get into any problems.
The red connection is the 7.4v line and the black is ground from a power supply.
The red connection is the 7.4v line and the black is ground from a power supply.
The Controller Port




The controller port is thick and needs to be reduced so it fits nicely in the system.
Pry upwards on the ports with a screwdriver (pic 2), and then use pliers to snip off the pin connections. (pic 3)
Cut off the connections to the battery and relocate it with a couple of wires, and hot glue the battery to a piece of card or plastic so there is no chance of a short. (pic 4)
Pry upwards on the ports with a screwdriver (pic 2), and then use pliers to snip off the pin connections. (pic 3)
Cut off the connections to the battery and relocate it with a couple of wires, and hot glue the battery to a piece of card or plastic so there is no chance of a short. (pic 4)
The Controller





The official DreamCast controllers use reed switches to detect how far a joystick is moved or shoulder button; which is little use in a portable as you really need pots not reed switches.
There are some third party DreamCast controllers that use pots - look on the edge and you see the joysticks are connected to pots - ideal. (pic 1)
Open the controller up, you see the back of the board is blank, which is handy. We don't need to trim the controller board down either. (pic 2 and pic 3)
As usual, don't throw any part away as you'll need most of it. Keep all parts in a box for easy location. (pic 5)
Desolder the shoulder triggers and joystick off the board and retain them. (pic 4)
There are some third party DreamCast controllers that use pots - look on the edge and you see the joysticks are connected to pots - ideal. (pic 1)
Open the controller up, you see the back of the board is blank, which is handy. We don't need to trim the controller board down either. (pic 2 and pic 3)
As usual, don't throw any part away as you'll need most of it. Keep all parts in a box for easy location. (pic 5)
Desolder the shoulder triggers and joystick off the board and retain them. (pic 4)
Making the Case - Part 1




The DreamCast is thick so there is no point not using the console's original casing as using a smaller section would need more advanced modding skills.
The case (pic 1, pic 2)
We need to make the sides straight and also square, so use 2mm thick strips of styrene, superglue to the sides. (pic 3, pic 4)
The case (pic 1, pic 2)
We need to make the sides straight and also square, so use 2mm thick strips of styrene, superglue to the sides. (pic 3, pic 4)
Making the Case - Part 2



Now, fill in the gaps, using any type of sandable filler, I use Polyfilla. (pic 1)
Sand it (pic 2, pic 3) to be smooth
Sand it (pic 2, pic 3) to be smooth
Making the Case - Part 3






We want the portable to feel good to hold and stable to hold, right? That means the handholds need to be out about 60mm on each side so when you hold the system your fingers won't get in the way of the middle section of the system (where the console board is).
So, mark out on 2mm thick styrene what your case will end up being in size, taking this into account. (pic 1)
Use an old CD as a template for the rounded corners - reason is we'll use styrene to wrap around the corners (step 18) and any tighter and the styrene will be under too much stress.
Superglue some 6mm thick pine to the inside of the old console case (pic 2) so it can be superglued to the piece in (pic 1), done in (pic 3, pic 4)
Cut out some vent holes from a different case, superglued it in place, filled in the gaps with filler, sanded smooth. (pic 5), filled in the gap the old "on" LED occupied before - I want the LED to show at the front of the system not the back. (pic 6)
So, mark out on 2mm thick styrene what your case will end up being in size, taking this into account. (pic 1)
Use an old CD as a template for the rounded corners - reason is we'll use styrene to wrap around the corners (step 18) and any tighter and the styrene will be under too much stress.
Superglue some 6mm thick pine to the inside of the old console case (pic 2) so it can be superglued to the piece in (pic 1), done in (pic 3, pic 4)
Cut out some vent holes from a different case, superglued it in place, filled in the gaps with filler, sanded smooth. (pic 5), filled in the gap the old "on" LED occupied before - I want the LED to show at the front of the system not the back. (pic 6)
Making the Case - Part 4



Install a grill for the air outlet fan, as per previous step (pic 1, pic 2)
Hot glue it in place (pic 3)
Hot glue it in place (pic 3)
Making the Case - Part 5





Use the case flat piece to mark out the same sized piece of styrene for the front of the case where the screen and controls will be mounted. (pic 1)
Use a sharpie knife to score the window (pic 2), and to make it easy to remove the screen hole, drill out the middle part so you can break off the styrene (pic 2, pic 3)
Use a sanding block to ensure the sides are smooth and straight. (pic 4, pic 5)
Use a sharpie knife to score the window (pic 2), and to make it easy to remove the screen hole, drill out the middle part so you can break off the styrene (pic 2, pic 3)
Use a sanding block to ensure the sides are smooth and straight. (pic 4, pic 5)
Making the Case - Part 6



Good time to check how the system feels like to use - and work out button and joystick positioning.
Two sanding blocks are about the same thickness as we need for the system, for the front that will house the screen and controls, and provide the handholds - 25mm thick is about right.
Two sanding blocks are about the same thickness as we need for the system, for the front that will house the screen and controls, and provide the handholds - 25mm thick is about right.
Making the Case - Part 7




Next job is to make the sides of the case. Superglue some 6mm pine strips to the sides (pic 1), and then superglue 25mm strips of 2mm thick styrene around the sides (pic 2), and then hot glue the edges to add more strength (pic 3).
Superglue 10mm thick pine to the case backing section, so the wood is thick enough to support small screws to hold the sections together later. (pic 4)
Superglue 10mm thick pine to the case backing section, so the wood is thick enough to support small screws to hold the sections together later. (pic 4)
Making the Case - Part 8




The lip of the case where the halves meet isn't tidy (pic 2) so use strips on both sides to cover this up (pic 4). Screw little screws into place so you know where they can go (pic 4).
Installing Joystick and D-pad Holes




You can cut the holes in the case itself, or mount the existing holder for joystick and d-pad from a salvaged controller. In this example, going to use that method.
Using a dead old SNES controller (pic 1), opened it up, cut out the mounting from the d-pad surround and superglued and then hot glued it to the inside of a hole drilled in the case front for it (pic 2). Then, used filler (pic 3), and sanded it smooth (pic 4)
Using a dead old SNES controller (pic 1), opened it up, cut out the mounting from the d-pad surround and superglued and then hot glued it to the inside of a hole drilled in the case front for it (pic 2). Then, used filler (pic 3), and sanded it smooth (pic 4)
Installing Buttons











Buttons have to be in the place your fingers rest when holding a case, same true for the positioning of the joystick and shoulder buttons. If you don't then you'll get your hands cramping.
You will notice the case we use is flat but the case on the controller is sloped (pic 1), what we do is cut out the hole section holders individually (drill around the holders in the controller casing), then use a sanding drum to sand down the holders so the button sticks out enough to use nicely, plus 2mm extra (the thickness of the case front's styrene). (pic 2)
Superglue them onto the case backing. Make sure the buttons are level and straight, use the screen's cut-out window as a reference point. (pic 3)
Use a drill to cut out the holes, but leave about 1mm around the perimeter of the holes, then use a 6mm sanding drum to finish off the circular holes. Check the buttons move freely through the holes (pic 6). Do your cutting from the back of the case not the front to reduce the risk of damaging the case by cutting the holes poorly. (pic 4, pic 5)
You will notice the "start" button is also installed in a similar manner, although for the button, I cut out two pieces of styrene in a triangle shape, and a larger piece for the backing.
To attach rubber tact switches as button presses (they have a nice mushy feel), use some wood posts to secure the tacts in suspension and held securely in place. (pic 7)
Done (pic 8)
When finished, the case front should look like (pic 9) - insides (pic 10) - the white wires are connections to a rumble pack (pic 11), motors are hot glued onto the case (pic 10)
You will notice the case we use is flat but the case on the controller is sloped (pic 1), what we do is cut out the hole section holders individually (drill around the holders in the controller casing), then use a sanding drum to sand down the holders so the button sticks out enough to use nicely, plus 2mm extra (the thickness of the case front's styrene). (pic 2)
Superglue them onto the case backing. Make sure the buttons are level and straight, use the screen's cut-out window as a reference point. (pic 3)
Use a drill to cut out the holes, but leave about 1mm around the perimeter of the holes, then use a 6mm sanding drum to finish off the circular holes. Check the buttons move freely through the holes (pic 6). Do your cutting from the back of the case not the front to reduce the risk of damaging the case by cutting the holes poorly. (pic 4, pic 5)
You will notice the "start" button is also installed in a similar manner, although for the button, I cut out two pieces of styrene in a triangle shape, and a larger piece for the backing.
To attach rubber tact switches as button presses (they have a nice mushy feel), use some wood posts to secure the tacts in suspension and held securely in place. (pic 7)
Done (pic 8)
When finished, the case front should look like (pic 9) - insides (pic 10) - the white wires are connections to a rumble pack (pic 11), motors are hot glued onto the case (pic 10)
Speaker Holes




Mark out the speaker holes and use a template from some old gadget that had speaker holes, as a guide (pic 1)
Use a small drill bit, and let it rest through the holes in the template, and quickly turn the drill on and off, so it cuts through the plastic but not long enough to damage the result (pic 2)
Result (pic 3, pic 4)
Use a small drill bit, and let it rest through the holes in the template, and quickly turn the drill on and off, so it cuts through the plastic but not long enough to damage the result (pic 2)
Result (pic 3, pic 4)
Installing the Memory Card






Use the holder from the old controller case, cut in half (pic 1, pic 2)
Work out the positioning in your case, as per pic, so it doesn't get in the way when the DreamCast's motherboard is in place. Basically, we are using the space the old voltage transformer used, that we aren't using any more. (pic 3, pic 4, pic 5)
Wire up the memory card to the ports from the original controller (pic 6)
Work out the positioning in your case, as per pic, so it doesn't get in the way when the DreamCast's motherboard is in place. Basically, we are using the space the old voltage transformer used, that we aren't using any more. (pic 3, pic 4, pic 5)
Wire up the memory card to the ports from the original controller (pic 6)
Installing the Battery Holders










We want to run the portable off external power (7.4v - 12v input) however we want the system to prominently use batteries.
The DreamCast and screen is a hungry beast to run, it works at 2 amps; so i'm going to use three sets of camcorder batteries, Sony NP-F550 compatible batteries, they are Li-ion cells and have their own protection circuits built in, they are also cheap to get hold of. Three sets of batteries should let the portable run for up to about 2.5 - 3 hours before needing charging.
Now the clever bit - going to have the battery packs removable, so when the voltage is getting low, just change them for a new set and keep playing for longer!
Got some battery charger units for these batteries, very cheap off ebay too, as they are custom made battery holders (pic 1)
Made holes of approximate size for these (which were trimmed about half the thickness) and also for the batteries too in the case (pic 2)
Then, painted the case front and back, and varnished it, and left it for a few days to dry out fully (pic 3)
When the case was dry, then made the holes the right accurate size by using my Dremel and also files. Wanted the holder to fit nicely in place (pic 4)
When in place, hot glued the holder, as i'd drilled out a hole so the hot glue could get inside and hold the holder to the case (pic 5)
As you see, first one done (pic 6), all three done (pic 7)
As you see, the holders are designed to touch the inside of the case against the case front section, so the batteries don't stick out too far, but far enough to remove and insert them (pic 8, pic 9)
The DreamCast logo is stuck back on the case, which was removed before painting.
Painted the inside of the system where the CD rests, to look nice (pic 10)
The DreamCast and screen is a hungry beast to run, it works at 2 amps; so i'm going to use three sets of camcorder batteries, Sony NP-F550 compatible batteries, they are Li-ion cells and have their own protection circuits built in, they are also cheap to get hold of. Three sets of batteries should let the portable run for up to about 2.5 - 3 hours before needing charging.
Now the clever bit - going to have the battery packs removable, so when the voltage is getting low, just change them for a new set and keep playing for longer!
Got some battery charger units for these batteries, very cheap off ebay too, as they are custom made battery holders (pic 1)
Made holes of approximate size for these (which were trimmed about half the thickness) and also for the batteries too in the case (pic 2)
Then, painted the case front and back, and varnished it, and left it for a few days to dry out fully (pic 3)
When the case was dry, then made the holes the right accurate size by using my Dremel and also files. Wanted the holder to fit nicely in place (pic 4)
When in place, hot glued the holder, as i'd drilled out a hole so the hot glue could get inside and hold the holder to the case (pic 5)
As you see, first one done (pic 6), all three done (pic 7)
As you see, the holders are designed to touch the inside of the case against the case front section, so the batteries don't stick out too far, but far enough to remove and insert them (pic 8, pic 9)
The DreamCast logo is stuck back on the case, which was removed before painting.
Painted the inside of the system where the CD rests, to look nice (pic 10)
Assembly of the Case Front Section




Painted the buttons and joystick and then used spray paint sealer (I find the one for metallics best) so the paint doesn't rub off. (pic 1)
Installed the screen and speakers in place (pic 2)
The back of the controller board is flat, (pic 3) which makes it easy to hot glue in pieces of pine in the case so it is out of the way (pic 4)
Installed the screen and speakers in place (pic 2)
The back of the controller board is flat, (pic 3) which makes it easy to hot glue in pieces of pine in the case so it is out of the way (pic 4)
Wire Up the Unit





Use flux and solder to tin the traces on the controller board so you can solder wires to the relocated button places. (pic 1, pic 2)
We also removed the ports off the controller board before (the set of middle pins in pic 2). One row will be connected in our system to the memory card, the other set to a rumble pack.
Using the old SNES controller, I can use the traces board from it, cut down to size, and wire the button contacts to it. This is handy as it means the d-pad will work reliably as it's working the same way as it was originally in the SNES unit. (pic 3, pic 4)
We also removed the ports off the controller board before (the set of middle pins in pic 2). One row will be connected in our system to the memory card, the other set to a rumble pack.
Using the old SNES controller, I can use the traces board from it, cut down to size, and wire the button contacts to it. This is handy as it means the d-pad will work reliably as it's working the same way as it was originally in the SNES unit. (pic 3, pic 4)
On/off Switch and Holding Console in Place



Use screwposts to hold the original on/off switch (taken from the original transformer) in place (pic 1)
Used some pine strips to hold the system in place, and screwed that to the pine strips holding that section to the case front section for support. This is of course when you have inserted the system into the case, and the CD is inserted into position, so a CD disc can spin freely. (pic 2, pic 3)
Wire the batteries in parallel, and the positive voltage line to the switch. The voltage lines that way will operate the console and also to the screen (which takes 7.4v in my case) (pic 3)
Used some pine strips to hold the system in place, and screwed that to the pine strips holding that section to the case front section for support. This is of course when you have inserted the system into the case, and the CD is inserted into position, so a CD disc can spin freely. (pic 2, pic 3)
Wire the batteries in parallel, and the positive voltage line to the switch. The voltage lines that way will operate the console and also to the screen (which takes 7.4v in my case) (pic 3)
Photos Showing System Running Off Batteries



Here are some pics of the system working off batteries; using three sets of Li-ion cells at 7.4v at 2.1 amps per set, yields 6.3 amps at 7.4v, enough to run the system for around 2.5 hours before needing the batteries changed. As covered, when the batteries run low, you can just replace them, while the system is still running, and continue playing. The idea is when the system is "off", and the system is connected to a 12v supply in the port to the batteries, it will charge the batteries in the system. (not in guide but straightforward to do); or use an external battery charger for the battery packs - considering the batteries are stock items and not modified, you can do that easily.
So, pics of the system working, running off batteries:
So, pics of the system working, running off batteries:
Conclusion
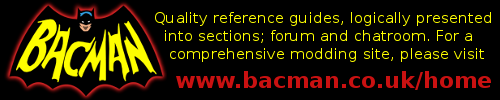
This guide is designed to show how to build your own DreamCast portable handheld console from scratch, in a step-by-step method. There may be some deviations if you build the system differently or use other components of course, however using this guide will allow you to build a system. You can of course add more to the portable system to suit your needs, connecting to external TV, headphone jack, etc - all depends on what you want; this guide however gets you a working system that you can add to if needed.
The DreamCast had quite a few quality games and making such a system into a modern portable gaming system will ensure it is more "relevant" in this modern age and has more gaming life.
If you have any queries or would like to show your project in the making, please join my forum, we are a friendly site and can help you with advice on your build if you need it; also, there is a good reference section to provide skills to do with handheld portable modding, techniques and also more information on the DreamCast too.
www.bacman.co.uk/home
Time to go play on my system now! ...
The DreamCast had quite a few quality games and making such a system into a modern portable gaming system will ensure it is more "relevant" in this modern age and has more gaming life.
If you have any queries or would like to show your project in the making, please join my forum, we are a friendly site and can help you with advice on your build if you need it; also, there is a good reference section to provide skills to do with handheld portable modding, techniques and also more information on the DreamCast too.
www.bacman.co.uk/home
Time to go play on my system now! ...