How to Create a Rotating Cabinet
by capybaralover in Living > Organizing
1068 Views, 12 Favorites, 0 Comments
How to Create a Rotating Cabinet
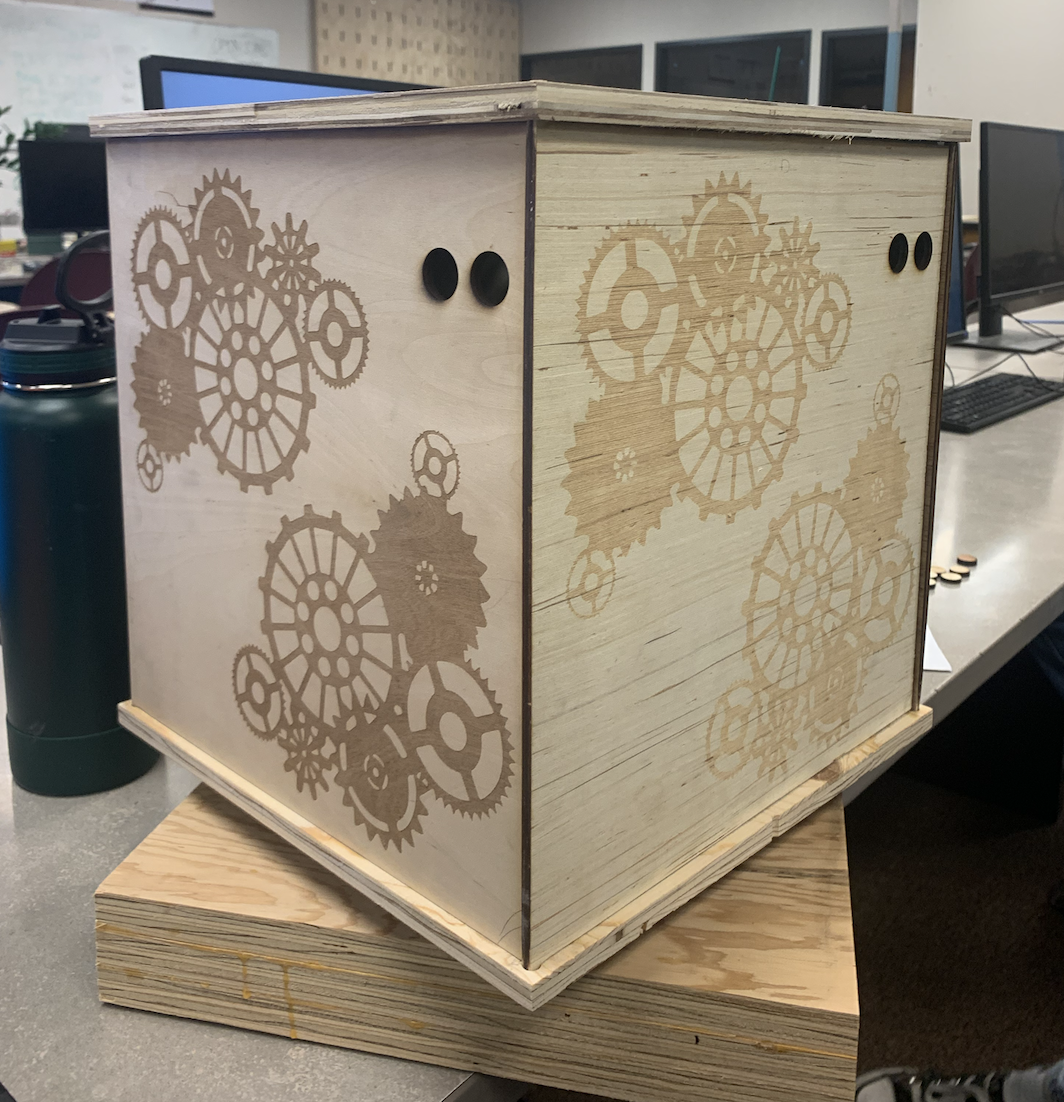
We wanted to create a functional yet aesthetically pleasing product. With custom designs, a rotating bottom, and plenty of storage space, the box will provide a simple yet wonderfully useful item to anyone’s home.
The instructable will be broken down into its three core components: The doors, tapered bearing, and the inner and outer walls. Following the creation of these parts will be the assembly of them.
From three students at Piedmont Hills High School
Supplies
General mixed wood in two different widths
.2 inch
.75 inch
Laser cutter
PLA plastic
CNC machine
Next Wave Automation Shark HD 510
3D printer
Used makerbot Z18 printer, replicator+
Wood Glue
Doors - Create Your Outline
- Start by creating an outline of your door on the Fusion 360 drawing program. Create a 12x12in square.
- To create mock “hinges”, protrude rectangles from the leftmost top and bottom corners with a width of .25in and height of .5in.
- If you want a different sized box, the height of the rectangles should be the width of your thicker wood, and the width should be the same as your door’s thickness.
Doors - Import Outline & Create Design
- Export your files as a png and upload them onto a new adobe illustrator canvas. The lines should be translated into vectors. Change the strokes into .001 thickness and the base red color.
- Pick a design of your choice. This can be taken from this internet or be a design of your own creation. Convert your design into a shape, this can be done by tracing your design with a pen or image tracing it. Set the fill color to gray–this will “shade” in your design with little cuts. The darker the gray, the deeper the cut.
- Depending on where your design is, you’ll want to add two .75in circles as “handles” to your design with .001 stroke width in the base red color.
Door - Laser Cut Design
- Take a thin slab of wood, about ⅓ the size of your thicker wood. This design uses a .25in slab.
- Import the illustrator file to your laser cutting program and cut it. The more intricate your design, the longer it will take to cut.
Door - Adjustments
Using sandpaper, sand down the edges of the “hinges”until they are rounded and can be easily moved in their slots. Slots mentioned in creation of top and bottom pieces. Be careful, the rectangles are delicate and can be easily broken!
Tapered Bearing - Cylinder Ring
- Create a circle 7 inches in diameter around the origin.
- Create a plane along the circle at 0 distance. Make a new sketch on the plane and place a point at the origin (on the path).
- Create an angled plane at -15 degrees to the z-axis. On that plane, make a circle of diameter 0.7 inches coincident to the origin of that sketch. Extrude it both ways. 0.45 inches upwards and 0.5 inches downwards for a total of 0.95 inches.
- Move the cylinder to make the circle’s center point coincident with the point on the 7 inch circle.
- Use the fillet tool to round the edges of the cylinder.
- Create a circular pattern around the z-axis, leaving small gaps between the cylinders.
Tapered Bearing - Top & Bottom Piece
- Hide all the cylinders except the first one.
- Create a new sketch on the xz plane. Project the geometry of the first cylinder.
- Create a collinear line along the outside edge of the cylinder. Make this line pass both ends of the cylinder.
- Create this trapezoidal shape as shown.
6. Create a collinear line on the other edge of the cylinder. Create the following shape.
7. Revolve both sketches around the z-axis.
Tapered Bearing - Print
Print each piece separately, the cylinders can all go together in one print though. I suggest importing one cylinder into a new design, removing the 15 degree angle, and copying/pasting as many cylinders are in the bearing.
Tapered Bearing - Base
- On Autocad, design a 13 by 13 by 2 inch base.
- Create a donut shaped pocket in the center to hold the bearing. Make sure the bearing will peak out of the pocket and has enough room from the inside edge to be able to spin.
Tapered Bearing - Base Cutting
- Save the design and go to the manufacture tab in Fusion 360.
- Generate code for a 2D pocket specific to your machine. If you do not have a saw to cut the 13x13 board from the wood stock (saves time to do manually), include a contour around the edge.
Top & Bottom - Design Sketch
- On Fusion 360, use the sketch feature to make a 13x13-inch square.
- Next, make a 0.75x13-inch rectangle aligned in the middle of the square. Repeat with a 13x0.75 inch square.
- Then, using construction lines, make an 11.875x11.875-inch square centered in the middle of the 13x13 square. Switch back to regular lines and make a 0.27-inch diameter circle centered on each corner of the square.
- Then make another, smaller square also centered in the middle of the 13x13 square. Set the edge of the smaller square to be 0.2 inches to the inside of the 11.875x11.875 square.
Top & Bottom - Extrude
Once the sketch is complete, it should look like four squares arranged in a 2x2 formation. Extrude the four squares to 0.75 inches. Extrude the rest of the sketch except the four circles to 0.5 inches. Do not extrude the four circles.
Top & Bottom - NC Code
- In the manufacturing tab on Fusion 360, create an adaptive clearing operation to machine the parts that are 0.5 inches tall.
- Then, make a bore operation to machine the four holes.
- Finally, make a contour operation to cut the piece from the stock. Make sure to leave tabs so the piece will not be damaged by the bit.
Top & Bottom - CNC & Sanding
- Secure your stock to the spoil board and set your zero either manually or with a touch plate. Do an air cut first to ensure that the GCode does what it is supposed to.
- Then set the zero for the z-axis and run the code. Once the program has finished, remove the stock from the spoil board and pop the piece out of the stock. You may use an oscillating saw to cut the tabs if it is too difficult to pop out by hand.
- Sand any rough edges or remnants of tabs.
Shelf Posts - Grooves GCode
- On Fusion 360, sketch a rectangle with a height of 11.5 inches. The width should be the width of the stock.
- Draw two horizontal lines 0.8 inches apart from each other, touching both vertical edges of the rectangle. Use the rectangular pattern to duplicate the pair of lines 4 times, with 2 inches in between each pair.
- Then, draw a construction line from the bottom edge of the rectangle to the first line above it, and another line from the top edge of the rectangle to the first line below it. Use the equal constraint on both construction lines. The finished sketch should look like a rectangle with four evenly spaced grooves.
- Extrude the grooves to 0.625 inches and the rest of the sketch to 0.75 inches.
- In the manufacturing tab on Fusion 360, create a pocket operation to machine the grooves.
Shelf Posts - Central Post GCode
- In a new design, make a new sketch and draw an 11.5x2.25 rectangle.
- Then, draw a 5.75x0.75 rectangle with the top edge aligned with the top edge of the bigger rectangle.
- Use points and the midpoint constraint to horizontally center the smaller rectangle inside the bigger rectangle. Use the rectangular pattern method from the previous step to make the grooves. The finished sketch should look like a rectangle with two prongs and grooves.
- Extrude the grooves to 0.625 inches and the rest of the pronged rectangle to 0.75 inches.
- In the manufacturing tab on Fusion 360, make a pocket operation for the grooves and a contour operation to cut the piece from the stock. Leave tabs on the contour operation so the piece will not be damaged by the bit.
Shelf Post - Edge Post GCode
- In a new design, sketch an 11.5x1 inch rectangle and use the rectangular pattern method from step 1 to add grooves.
- Extrude the grooves to 0.625 inches and the rest of the piece to 0.75 inches.
- In the manufacturing tab in Fusion 360, create a pocket operation to machine the grooves and a contour operation to cut the piece from the stock. Leave tabs on the contour operation so that the piece will not be damaged by the bit.
Shelf Post - CNC & Sand
- Secure your stock to the spoil board and set the zeros. Be very careful with zeroing, as you will have to flip the stock over and machine the other side as well.
- Run the grooves program from step 1. Once the program has finished, flip the stock over. Adjust the zero so that the programs for the central and edge posts can be run with the grooves on both sides of the stock aligning as closely as possible.
- Cut 2 central posts and 4 edge posts. If needed, use an oscillating saw to cut through the tabs and separate the pieces from the stock. Sand any rough edges or remnants of tabs.
Shelves - Design & GCode
- In Fusion 360, sketch a rectangle with two rectangular notches in the top corners. Set the width of the shape to 5.4875 inches and the height to 5.9875 inches. Make the left notch 1 inch wide and 0.5 inches tall. Make the right notch 0.875 inches wide and 0.5 inches tall.
- Finish the sketch and extrude it to 0.75 inches. In the manufacturing tab, create a contour operation to cut out the shelf. Leave tabs so the piece will not be damaged by the bit.
Shelves - CNC & Sand
- Secure your stock to the spoil board and set the zeros. Run the CNC program from step 1.
- Once it is finished, if necessary, use an oscillating saw to cut through the tabs and separate the pieces from the stock. Sand any rough edges or remnants of tabs.
Shelf Assembly - Connect Central Posts
- Turn one of the central posts upside down and hold them perpendicular to each other.
- Align the slots in the posts and push them into each other until they are flush with each other. You may gently tap the top of the posts with a mallet if they get stuck. When finished, the central post should look like a plus sign from the top view.
Shelf Assembly - Glue Posts to Top & Bottom
- Use wood glue to glue the central post to the middle of the indented + sign on the shelf bottom. Glue the 4 edge posts to the edges of the indented + sign. Make sure the outer ends of the posts are flush with the outer edges of the raised squares on the shelf bottom.
- After the glue dries, apply wood glue to the tops of the posts and place the shelf top on top of the posts, making sure everything aligns the same way it did with the bottom. Wait for the glue to dry before proceeding to the next step.
Shelf Assembly
Slide shelves into the indented grooves, making sure that the larger notch in the shelf is on the corner with the edge post and the smaller notch is on the corner with the central post. Insert as many or as few shelves as you’d like.
Assembly
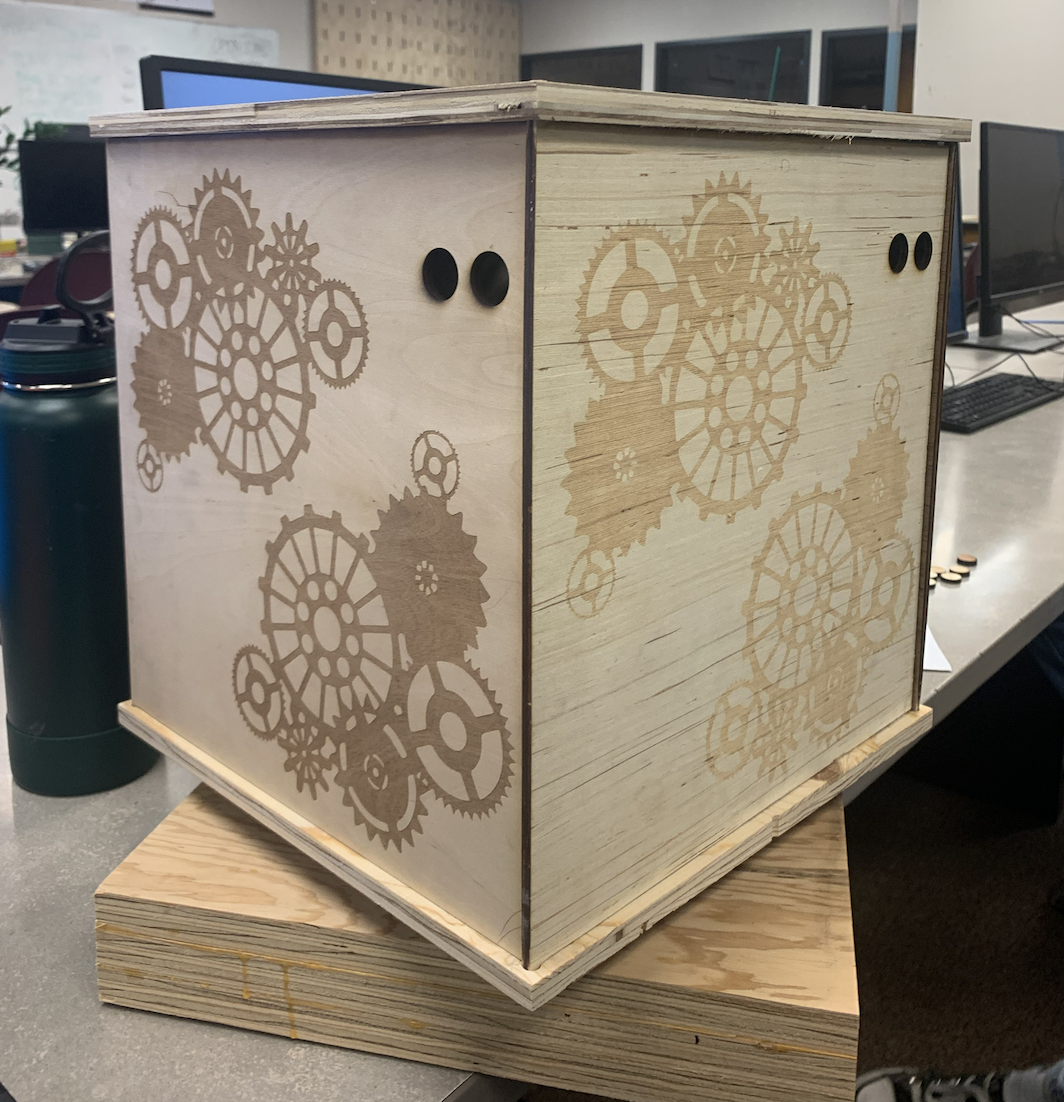
- Place the shelf posts into the bottom piece’s slots. Make sure they fit tightly and do not move. Place the shelves however you like into the slits on the walls.
- Place each door’s “hinge” into a corner hole of the bottom piece in an open position. Place the top piece on the walls while making sure the top hinges of the doors go through as well.
- Place the bearing upside down into the base. It spins better this way under pressure.
- Put glue on the bearing. Place the box on the bearing. Center it well.
Celebrate
Yay! Good job, you've made yourself a rotating cabinet :D