Find the Center of a Circle - DIY LASER Cut Tool
by rdrew5 in Workshop > Laser Cutting
12284 Views, 106 Favorites, 0 Comments
Find the Center of a Circle - DIY LASER Cut Tool
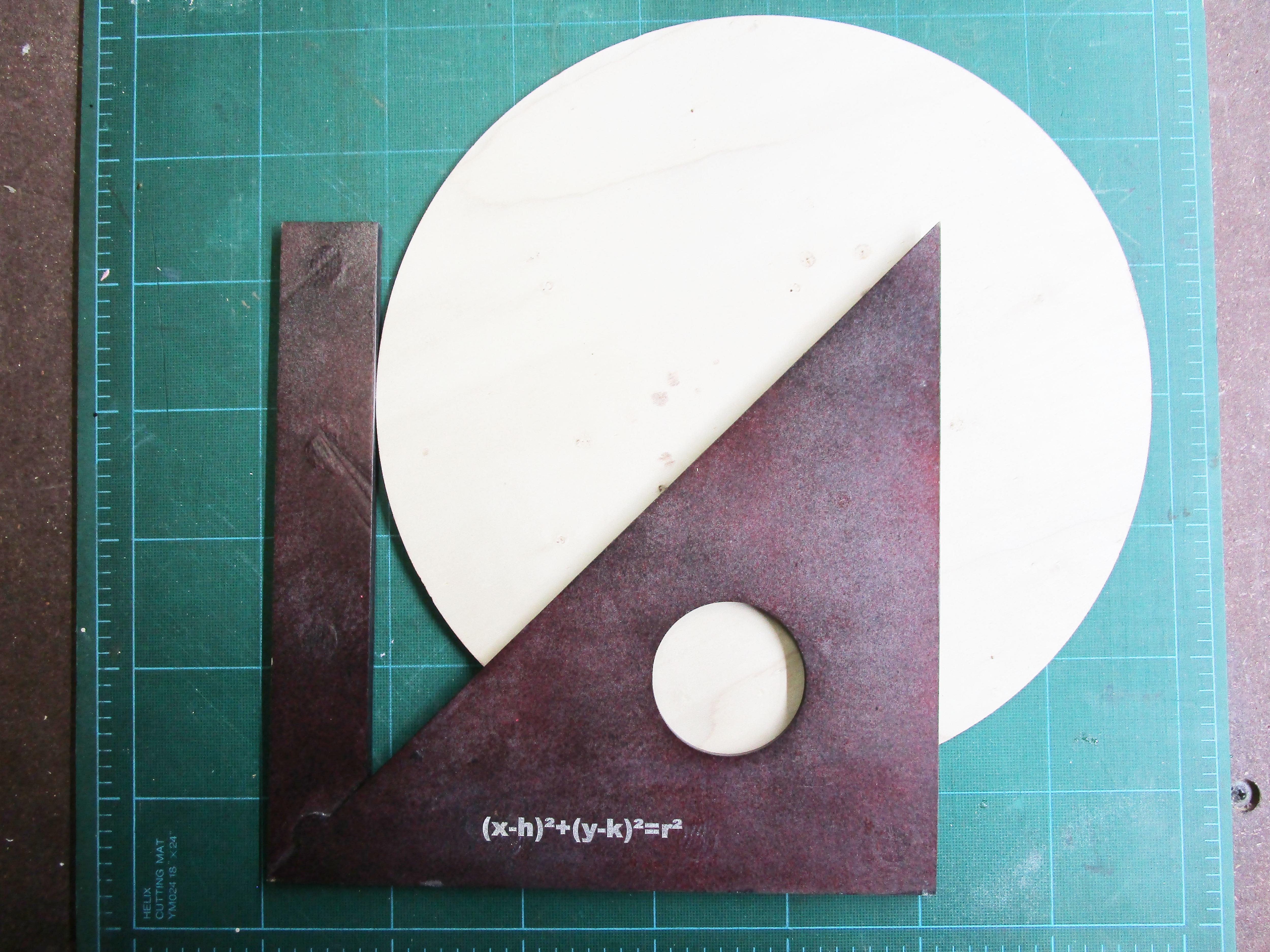
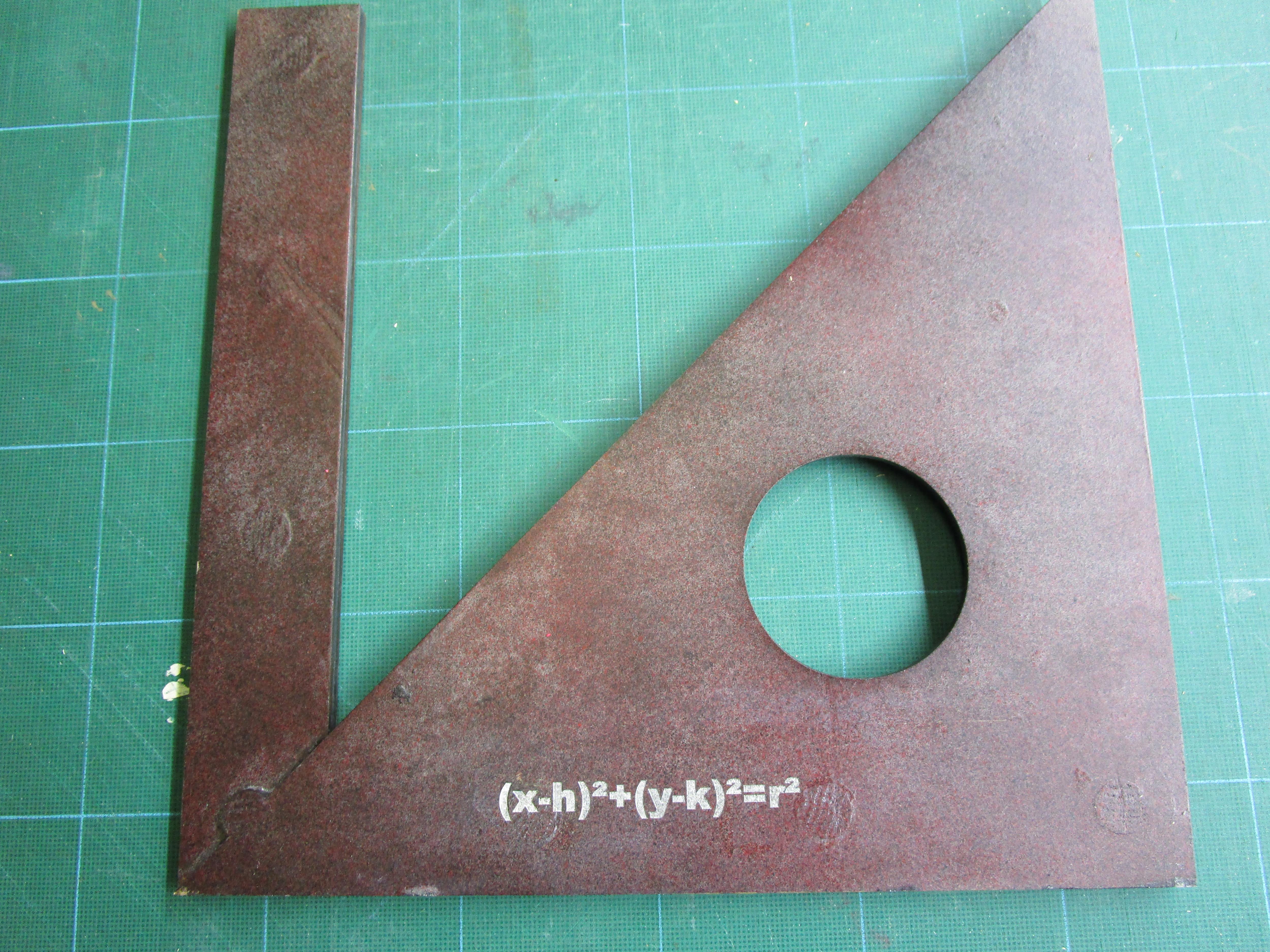
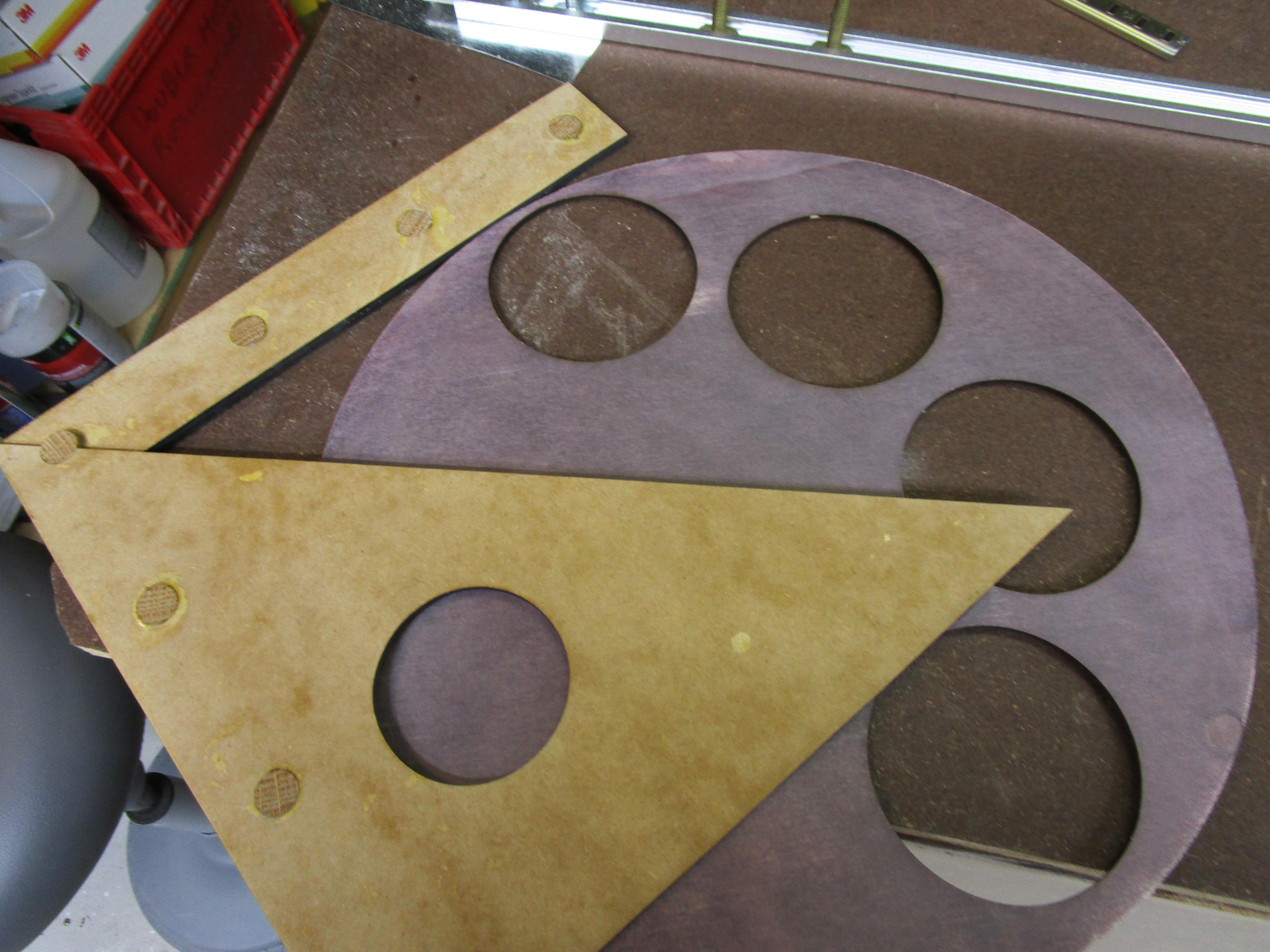
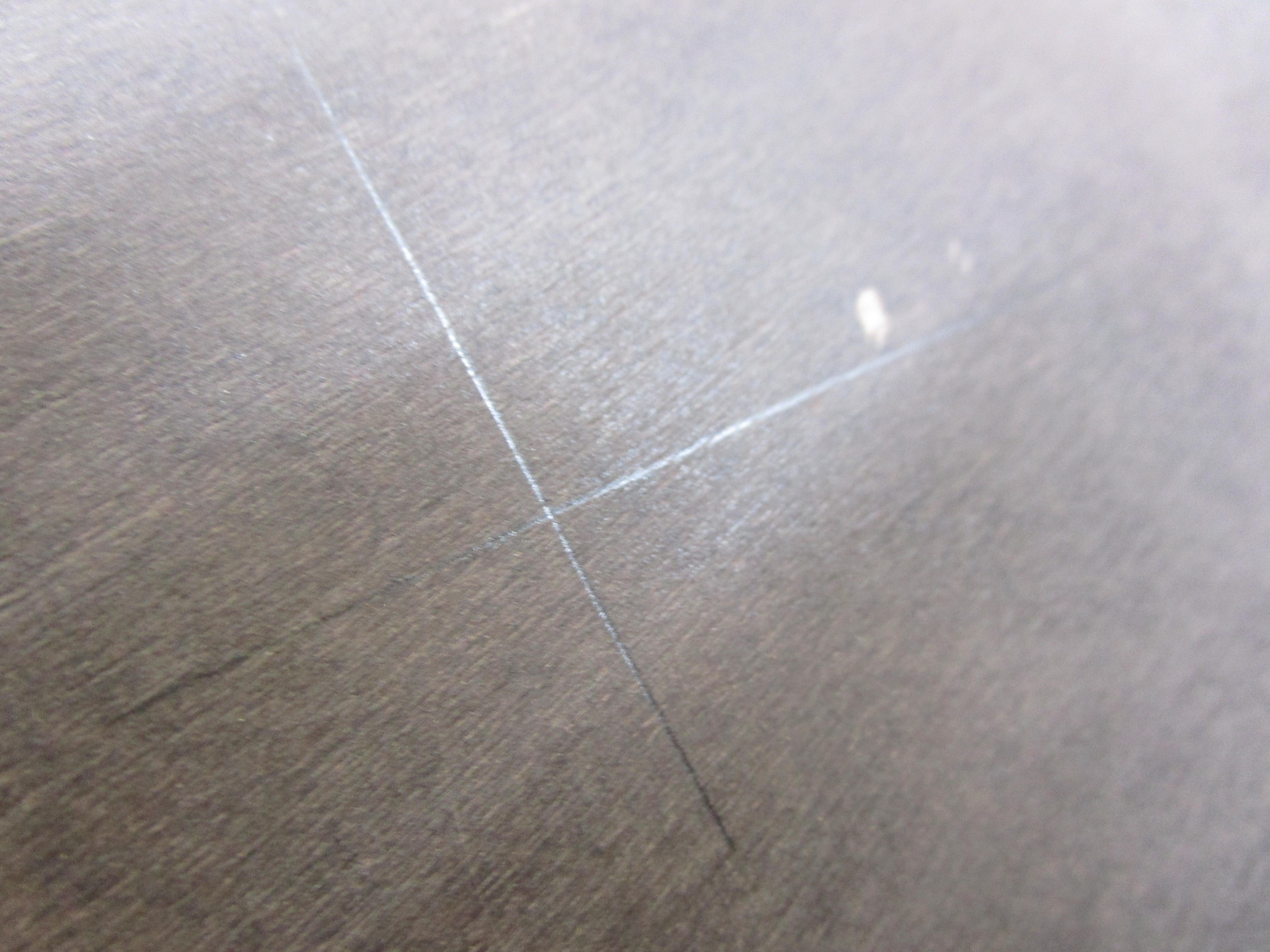
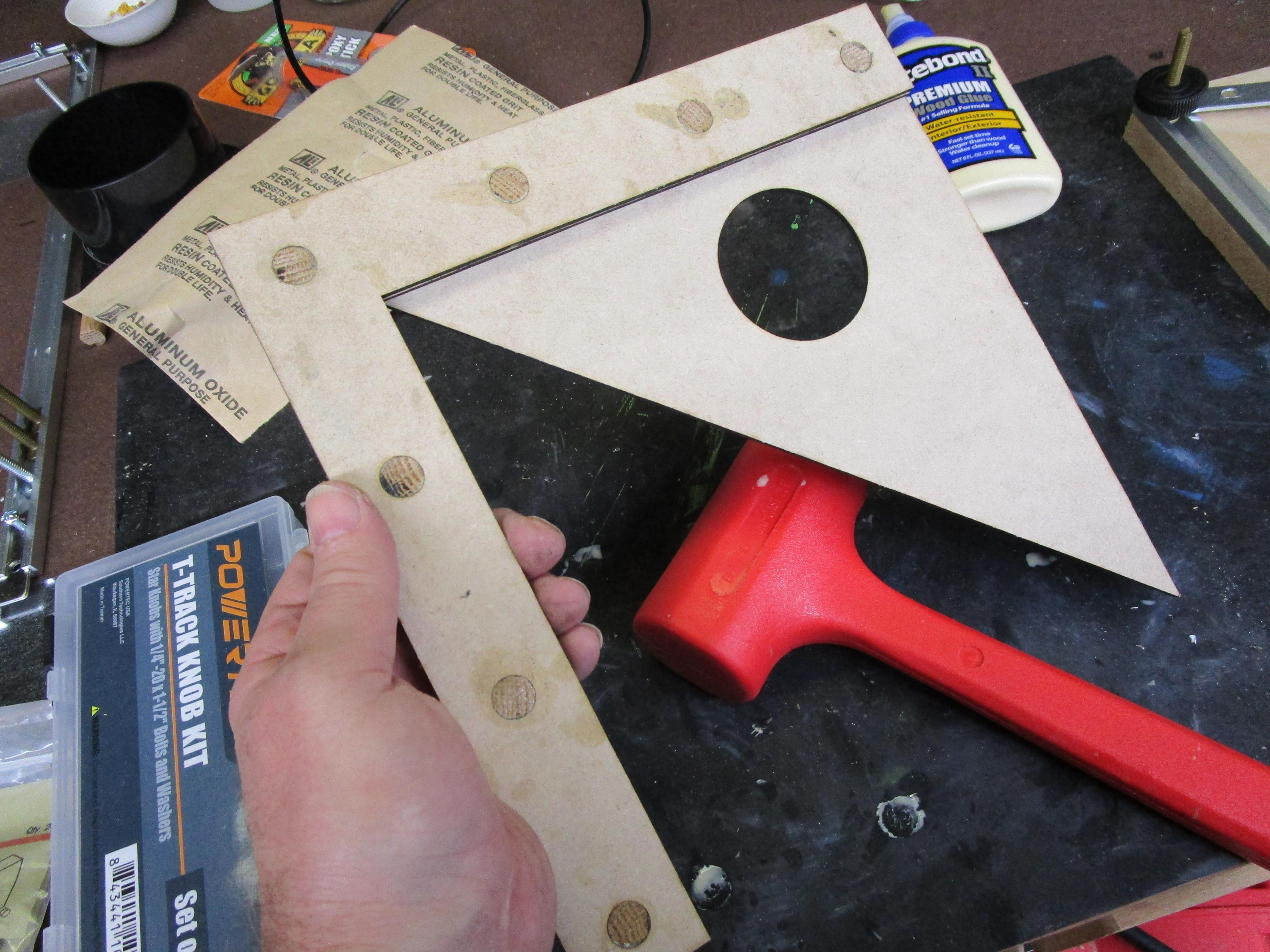
Ever need to work with pre-cut circles? Find the center-point with this quick and easy tool.
Supplies
Materials: 6" of 1/2" wooden dowel and 3mm MDF sheet. Thin plywood works as well. Size depends on size of tool, but 12x12" is fine. Wood glue.
Tools: LASER cutter. Small saw. Sandpaper. Hammer or mallet. Or a 2x4! Clamps.
Intro and Getting Started
I designed this file in LightBurn and to be honest it took me a few tries until I got it just the way I wanted. I was able to fit it on a single sheet of MDF that cost something like $3. I use 1/2" wooden dowels to align everything. If I were to do it again, I'd cut biscuits from the MDF and use the laser to cut slots in the wood - this way the entire thing could be laser cut and would still use one piece of wood. This video takes you through the entire process quickly and may be all you need!
Sure, you can buy a small version of this tool for $15 - but why bother when you can make a huge version yourself? A 10" tool is good for up to almost 20" circles.
This was also one of the first projects I did in LightBurn and it's really simple. I used multiple pieces glued because it is less prone to warping than a single piece, and it's quick to cut.
Creating the File in LightBurn
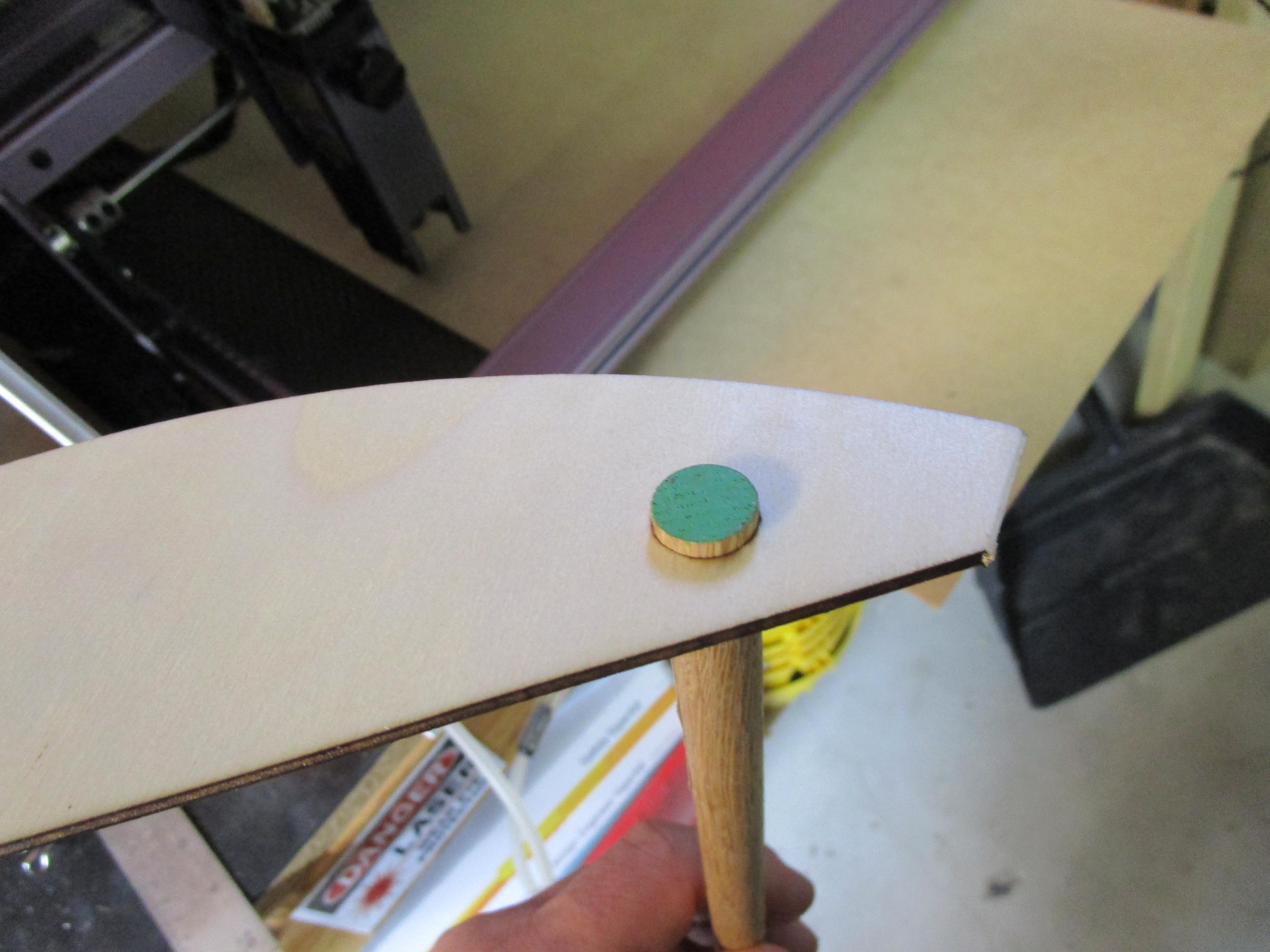
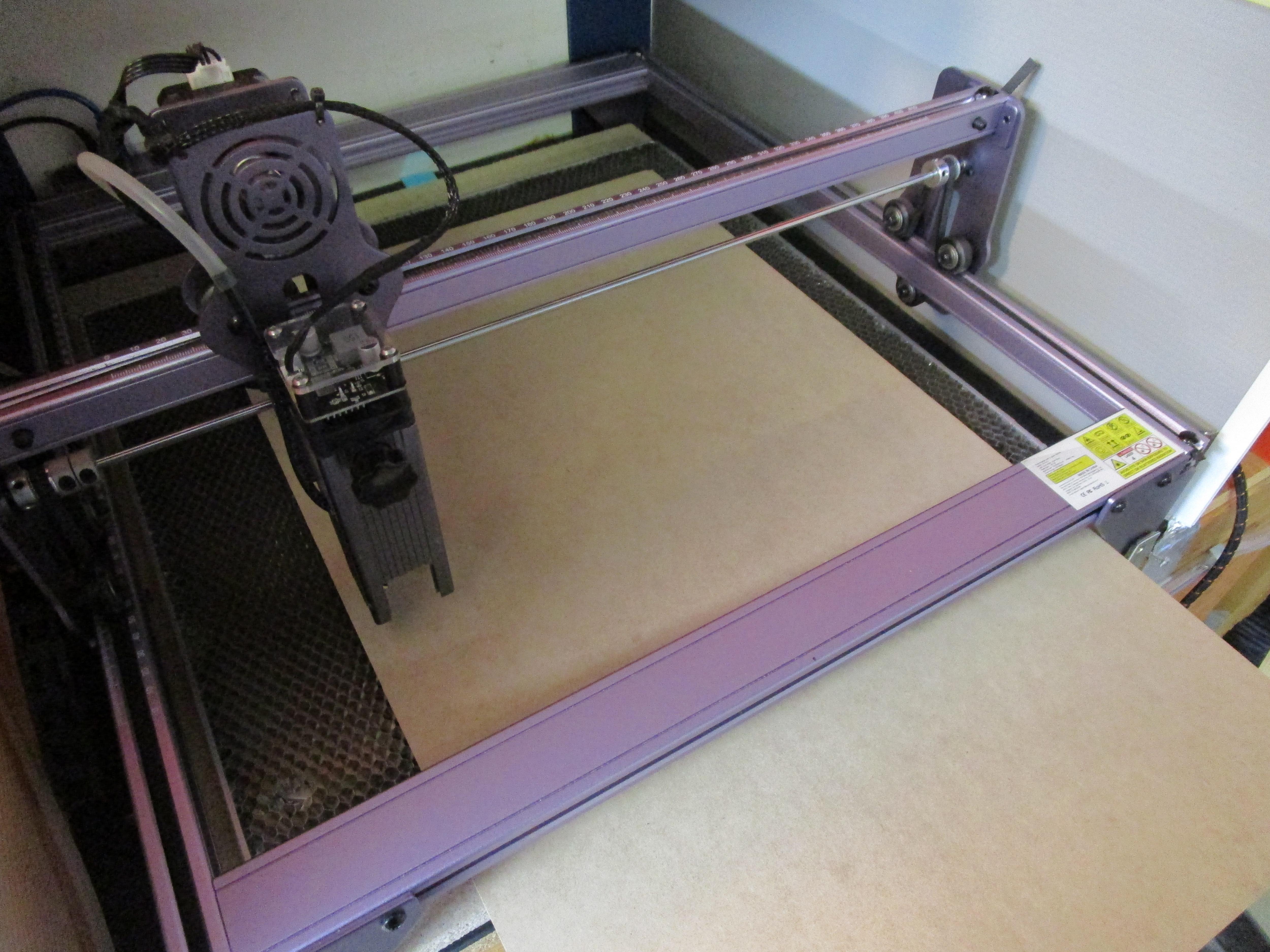
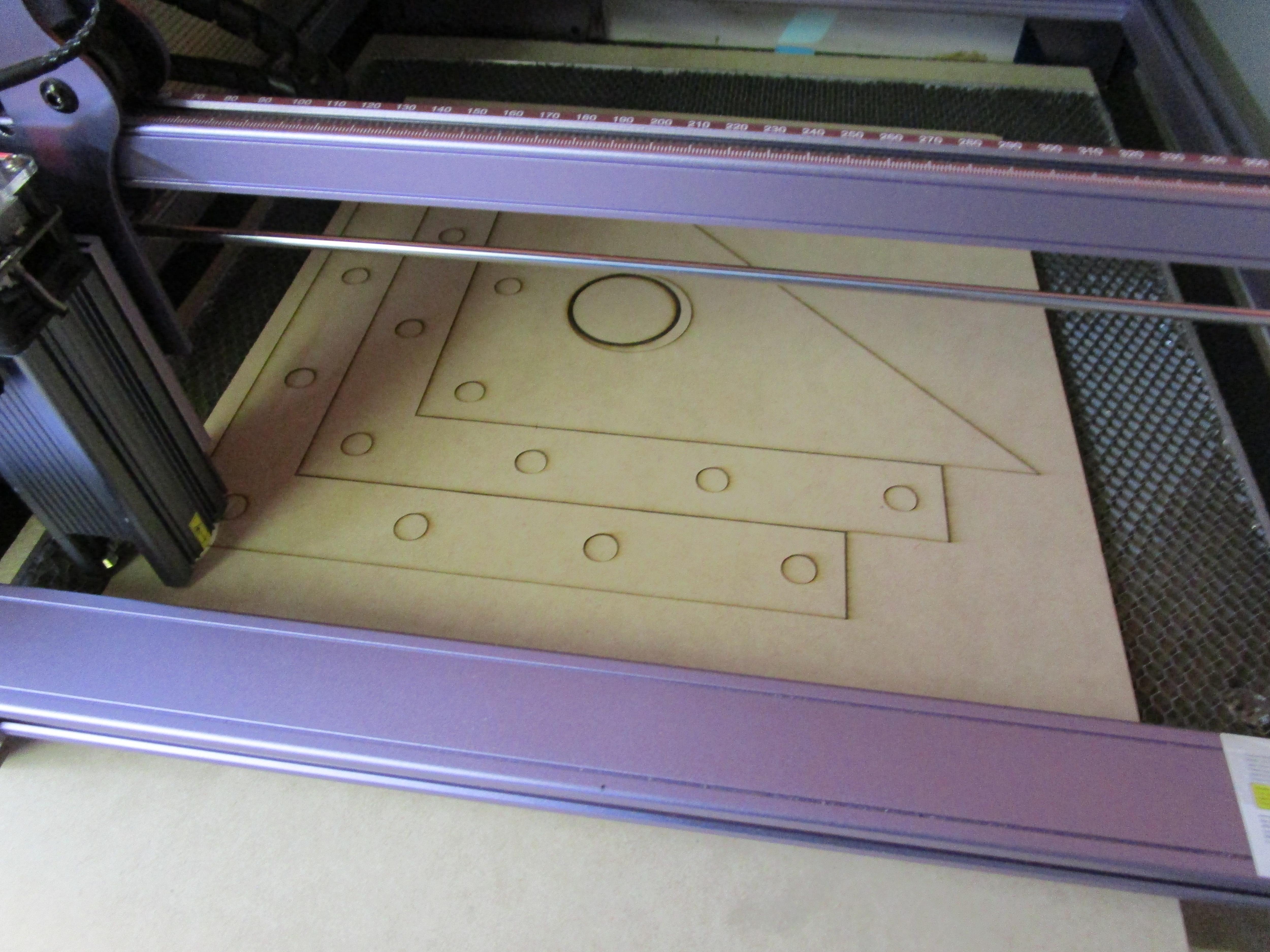
Create and cut the project. If you look at the video I made for this project, the first few minutes are creating the file.
Tip: Before you do this, take a piece of scrap wood and cut a 1/2" circle in it. Make sure the 1/2" wooden dowel is snug. That's the first photo. If it's not, you may have to adjust your LASER's offset or adjust the hole size.
Optimising: In the optimization settings, remove overlapping lines and cut inside shapes first. Delete anything in the priority box.
The design: The tool is two "L" sections and one triangle. The triangle has to rest on top of the stacked "L" sections. All are glued and joined with wooden dowels so alignment is perfect. So in LightBurn you just need to create two "L"'s and a triangle, plus cut several holes at the same position in all three pieces for alignment. It's straightforward.
The "L" shapes are 1.5" wide. I start everything with a 10" square. This way when all three pieces are stacked for optimal cutting, it all fits in the cutter on one sheet. This was my preference - there's many ways you can achieve the same thing. Just remember that anything larger may take two sheets. My laser is 400x410mm, so I designed it to fit that. The reason I butt the edges is to reduce the number of cuts - plus it reduced cutting time by 30%. It's all clear in the video
You'll notice that when I'm cutting the file in the video and in a couple of photos, there's a dark circle already burned. Dummy me - I forgot to lower the LASER when I first started - caught it after the first pass. So I made the circle a little larger and cut again. This way the "oopsie" was in the cut circle. The main reason I have this large circle on the triangle is to determine the number of cuts needed. All wood is different - and can be from day to day (humidity, etc.) So I cut this circle first. For my wood I determined it took 6 passes.
Here's the final layout and test cut. I have the test circle on it's own layer. All the parts for the tool are on a second layer - this second layer is set so it won't output for the circle cut. I use the lower left of the drawing as the starting point. Once you figure out how many passes are needed, then you can turn off the circle layer and turn on the second layer. Total cut time was 48 minutes. I had a speed of 600mm and power of 85%.
Wooden Dowel Segments
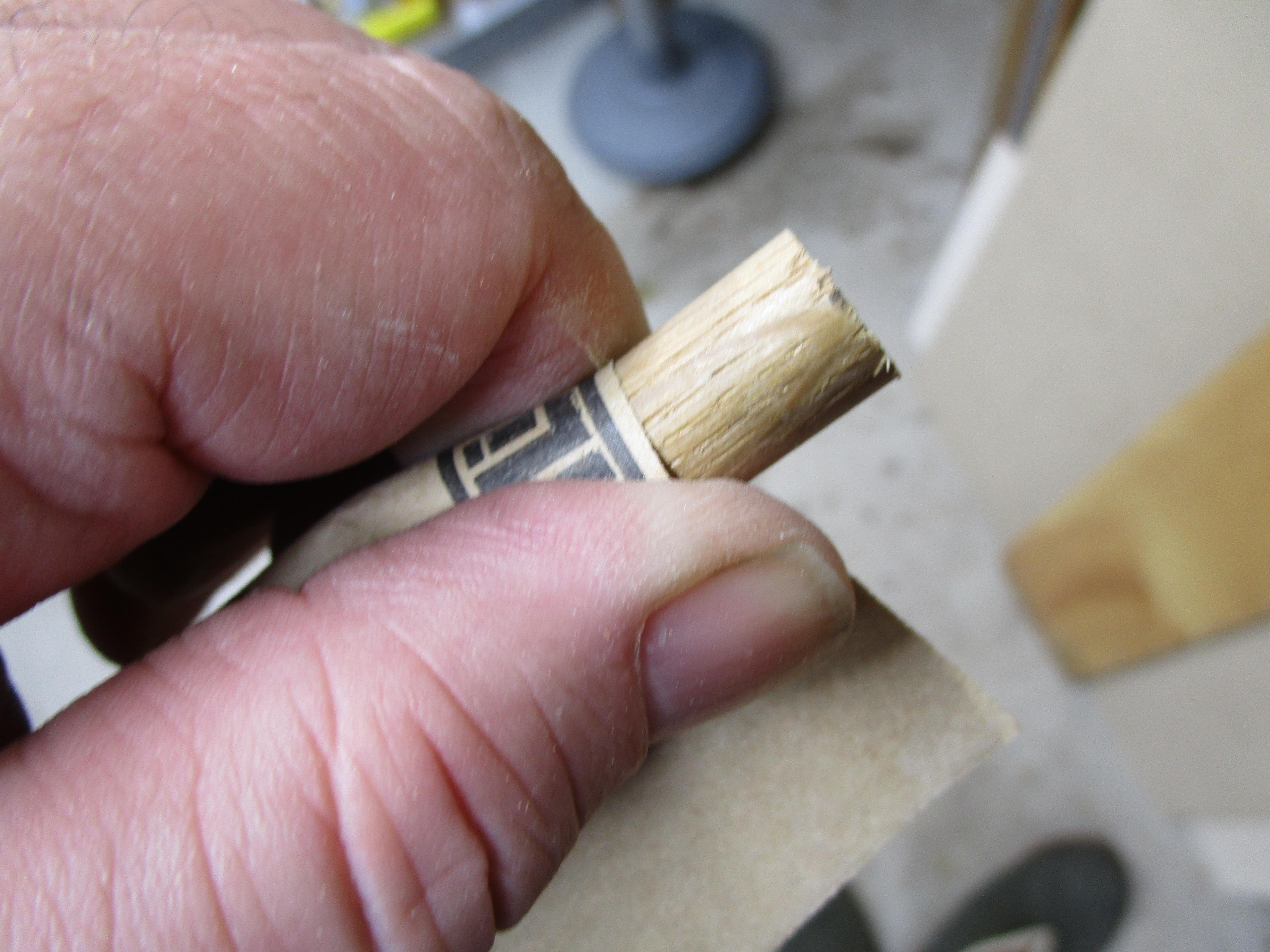
While the LASER is doing it's LASER thing, cut several 3/4" long sections from the wooden dowel. This step was a pain and why next time I'll use LASER cut biscuits. I cut the dowel segments on my chop saw and half flew off somewhere - still looking for a couple. I knew better but was in a hurry. So you may want to use a bandsaw, hand saw, etc. Just make sure one end is flat - that's for the base and will save you extra work later on. You'll also want to sand the bottom 1/4 of the dowel segments so they go in easier.
Assembly
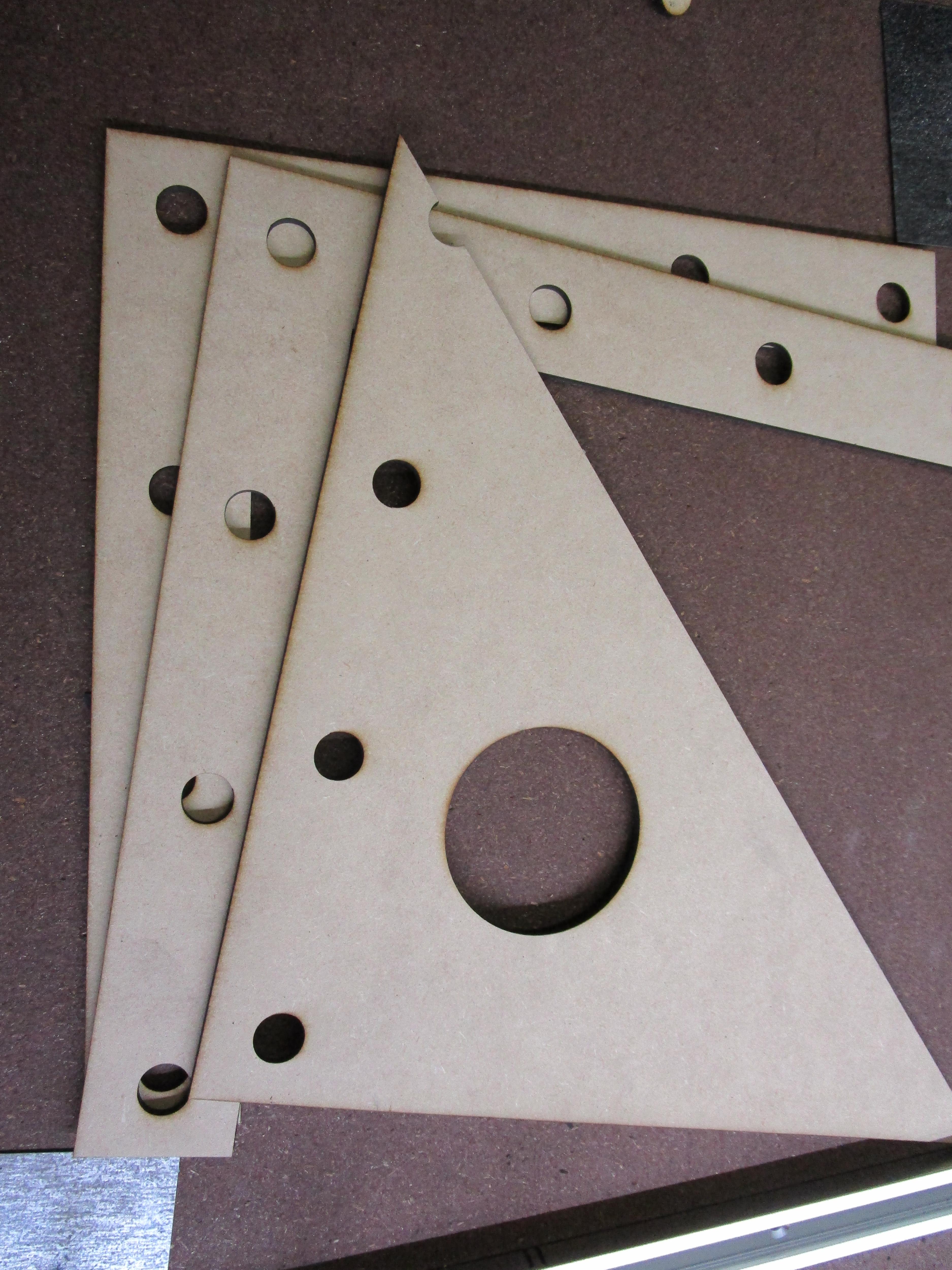
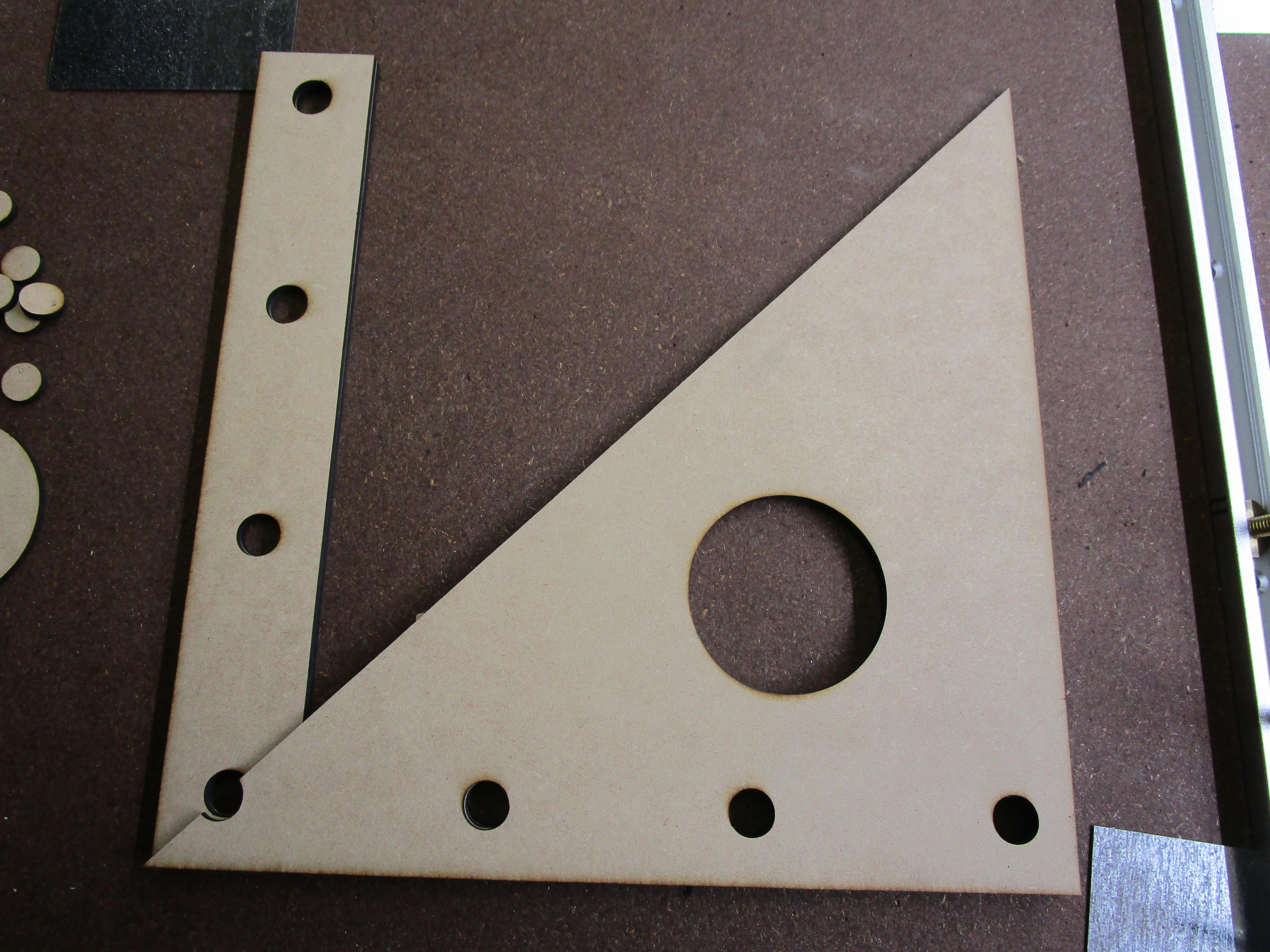
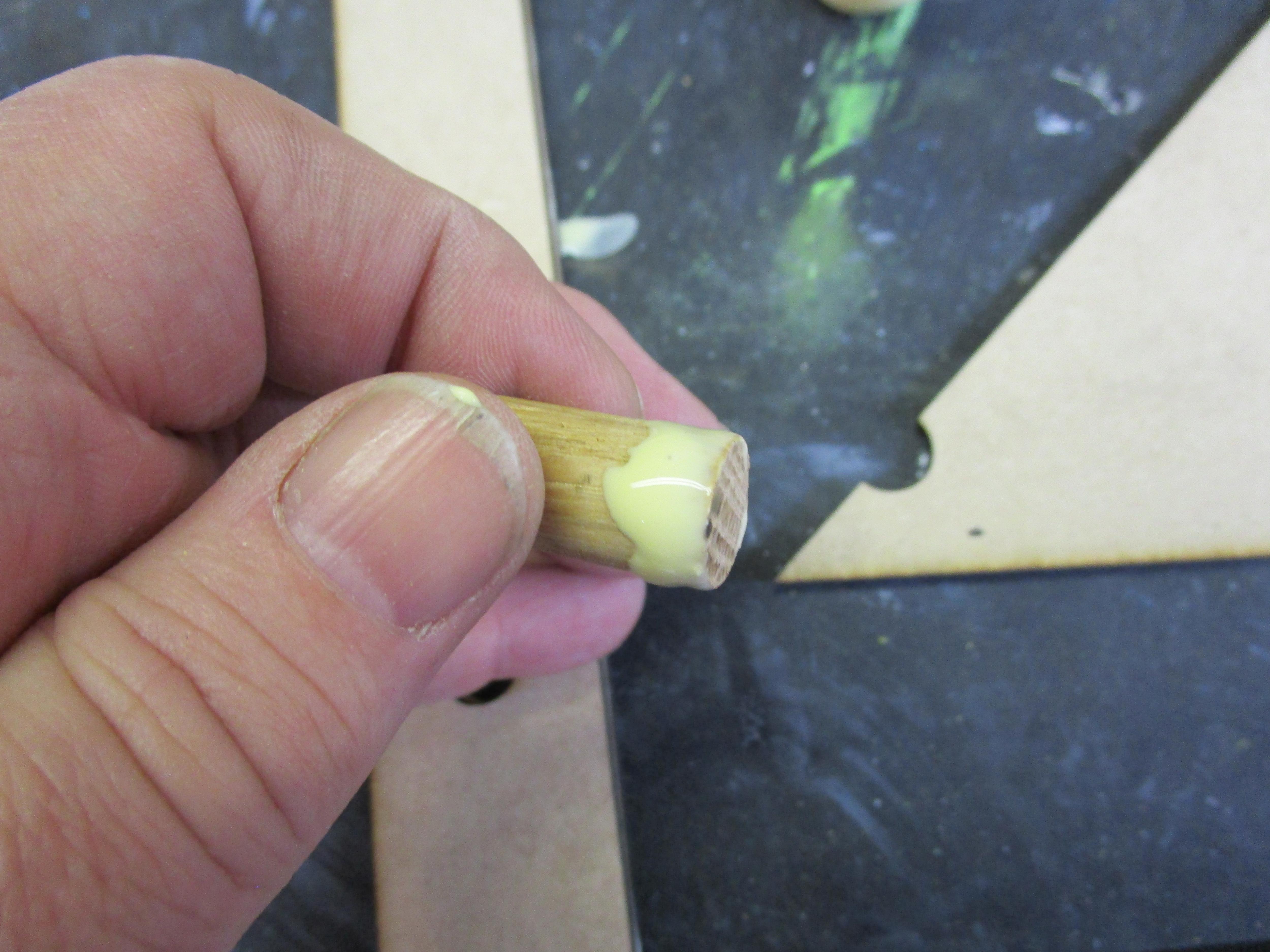
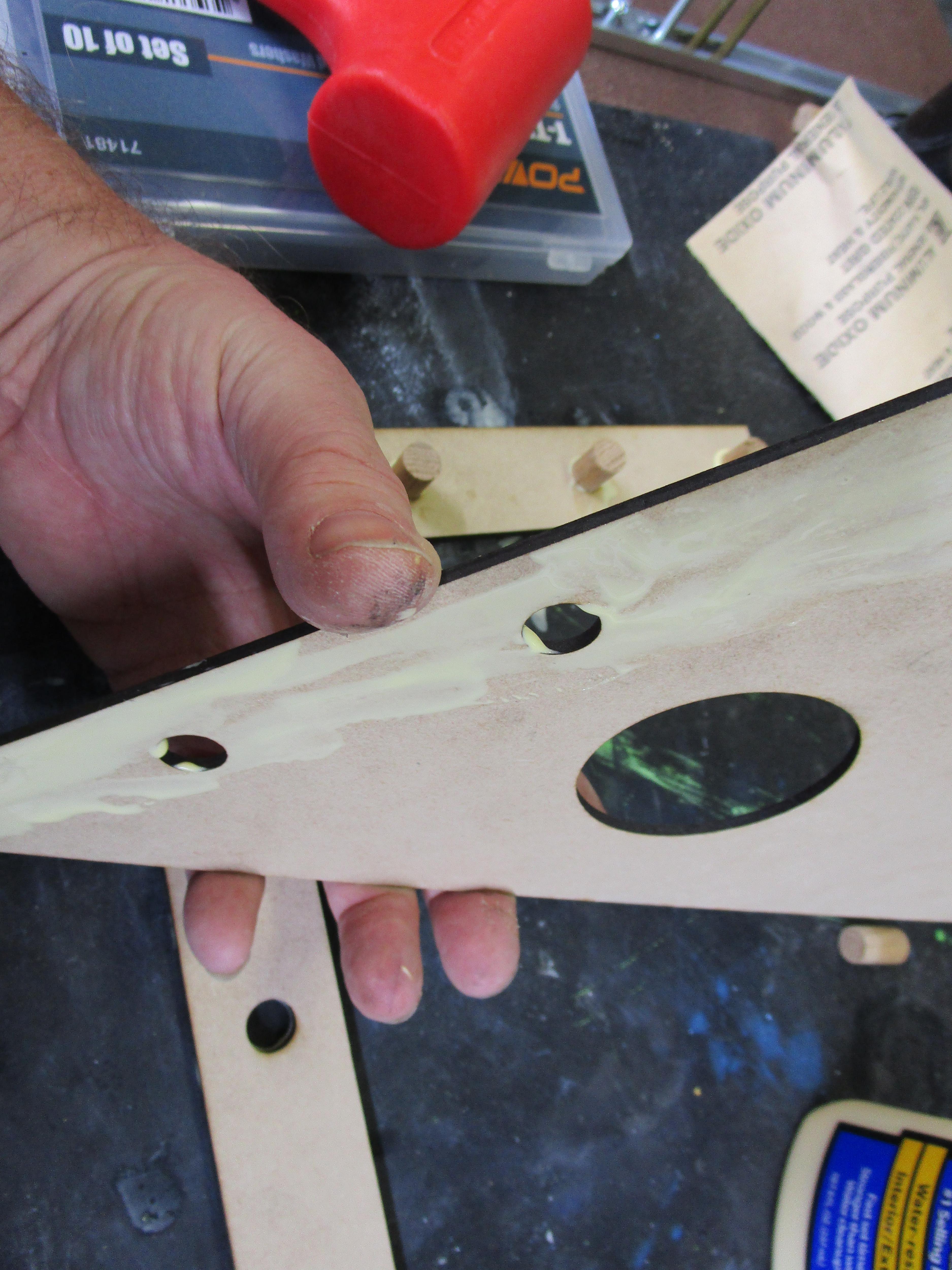
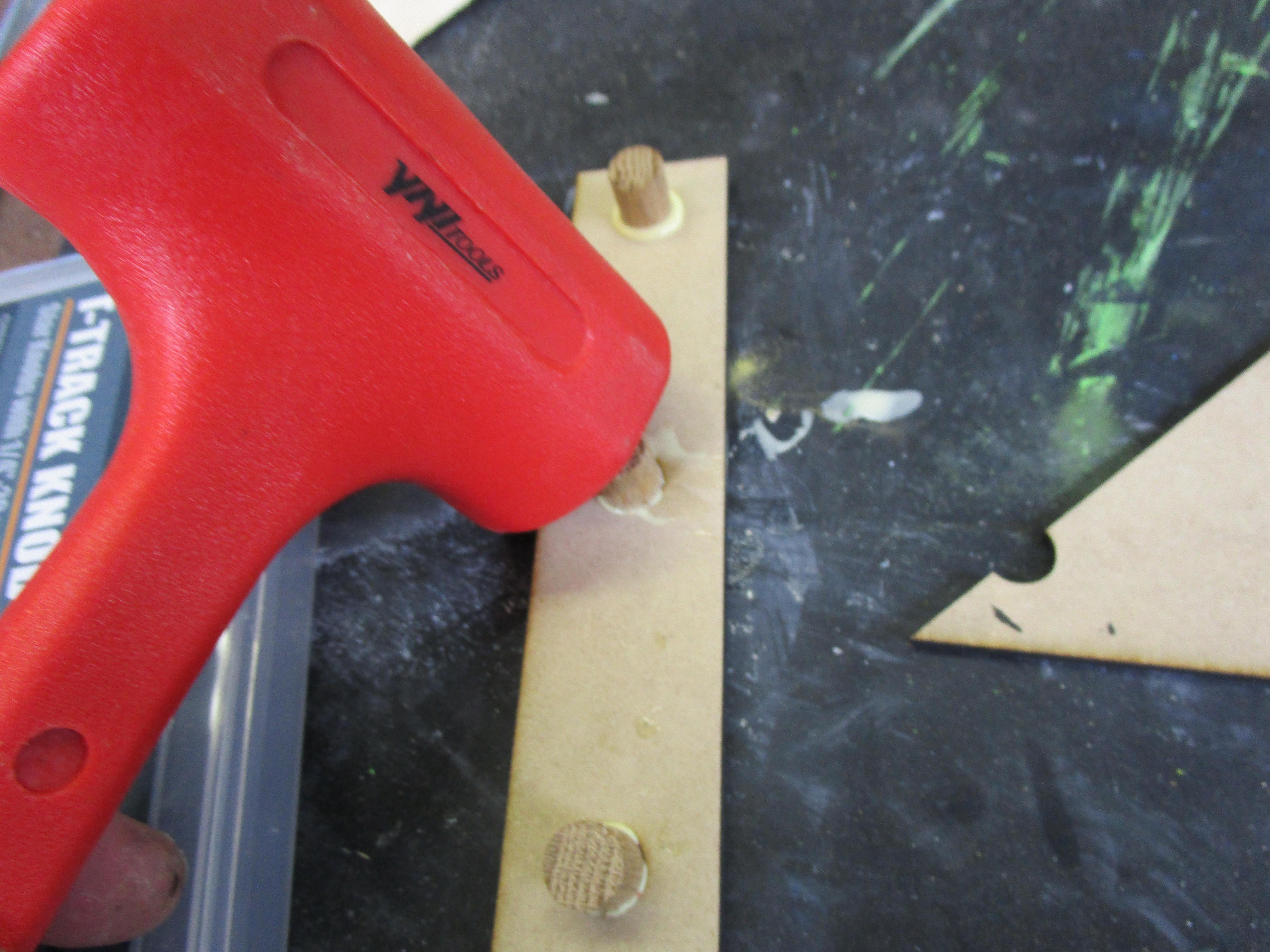
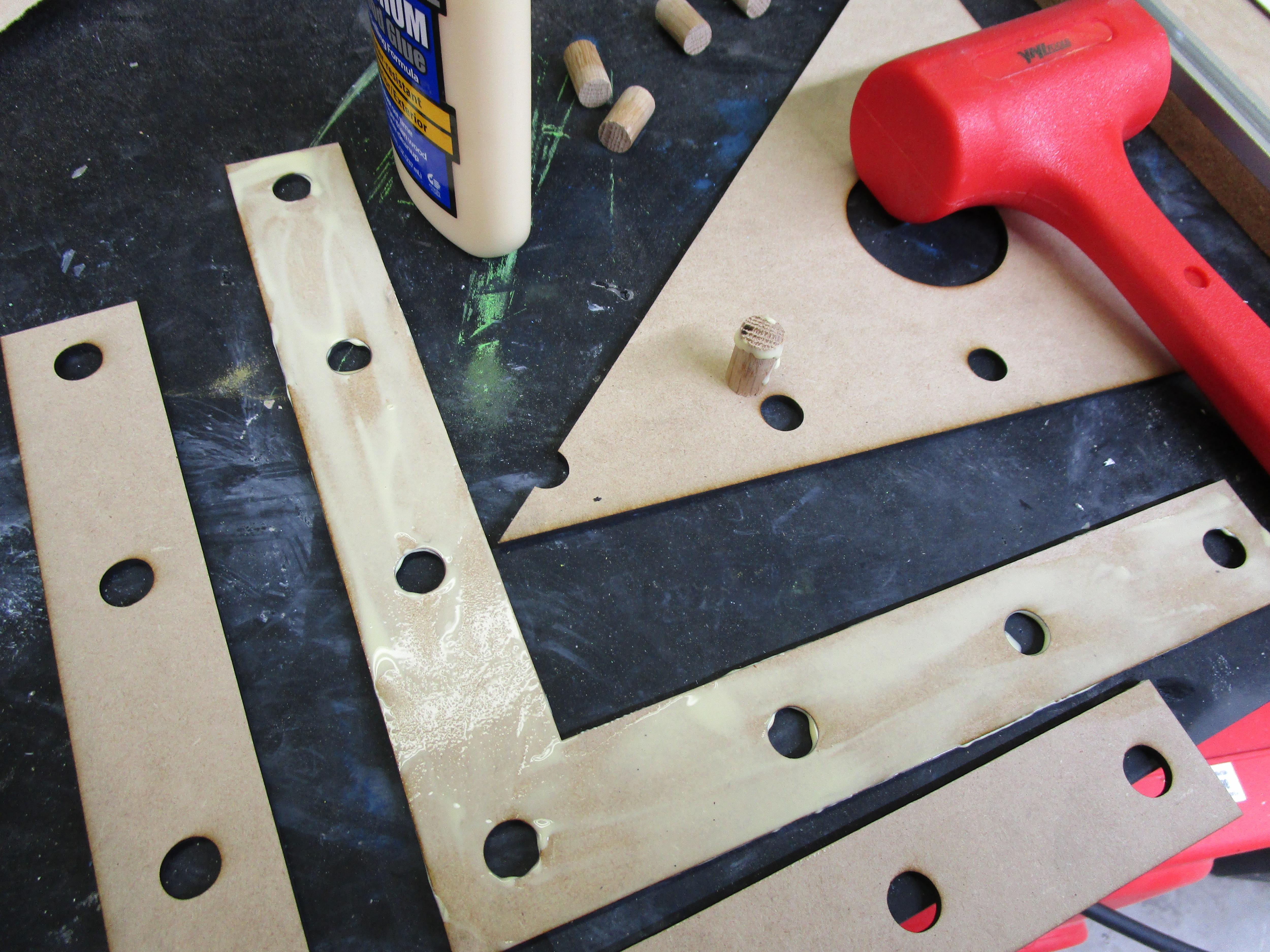

Dry assemble first just to verify there's no errors. Next is glueing the wood and dowels and assembling as shown in the photos. I pounded the dowels in place while the bottom rested on my workbench. This way the dowels did not stick out the bottom and stopped nice and flush. Then I clamped it all together like a wood and glue sandwich - a clamp between each dowel and on the tip of the triangle. Make sure to scrape off ALL excess glue. The inside especially MUST be clean and flat.
Finishing
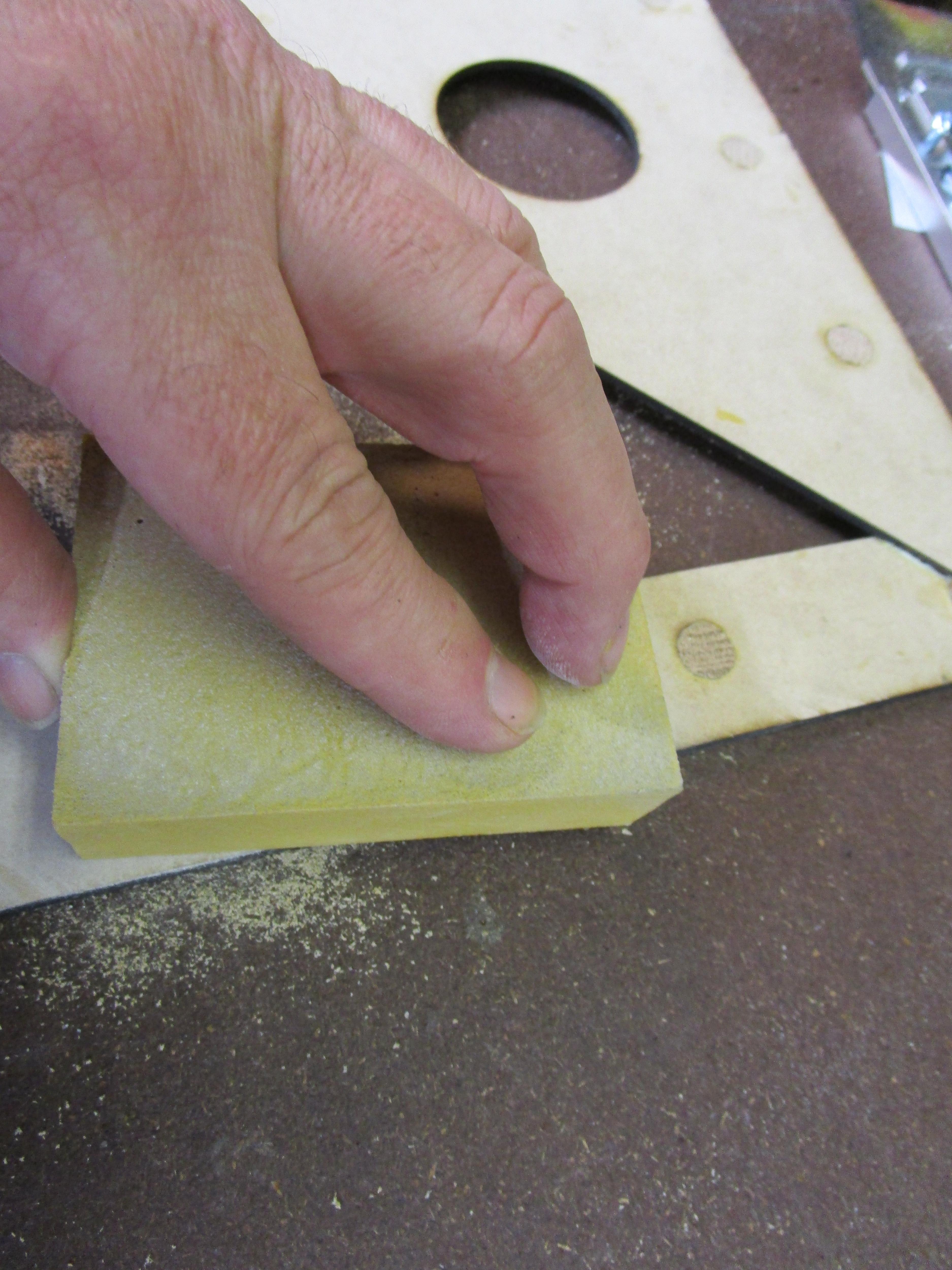
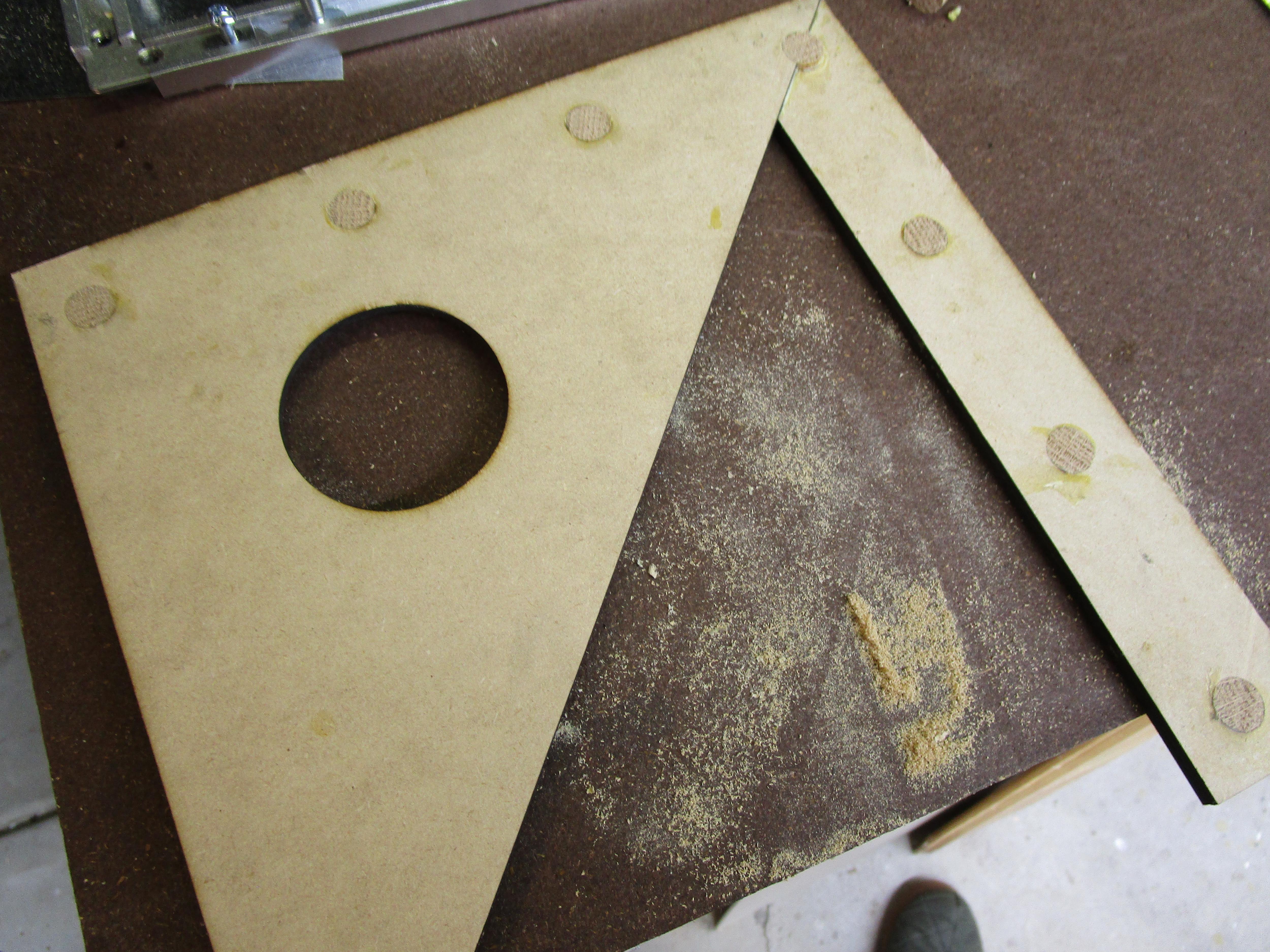
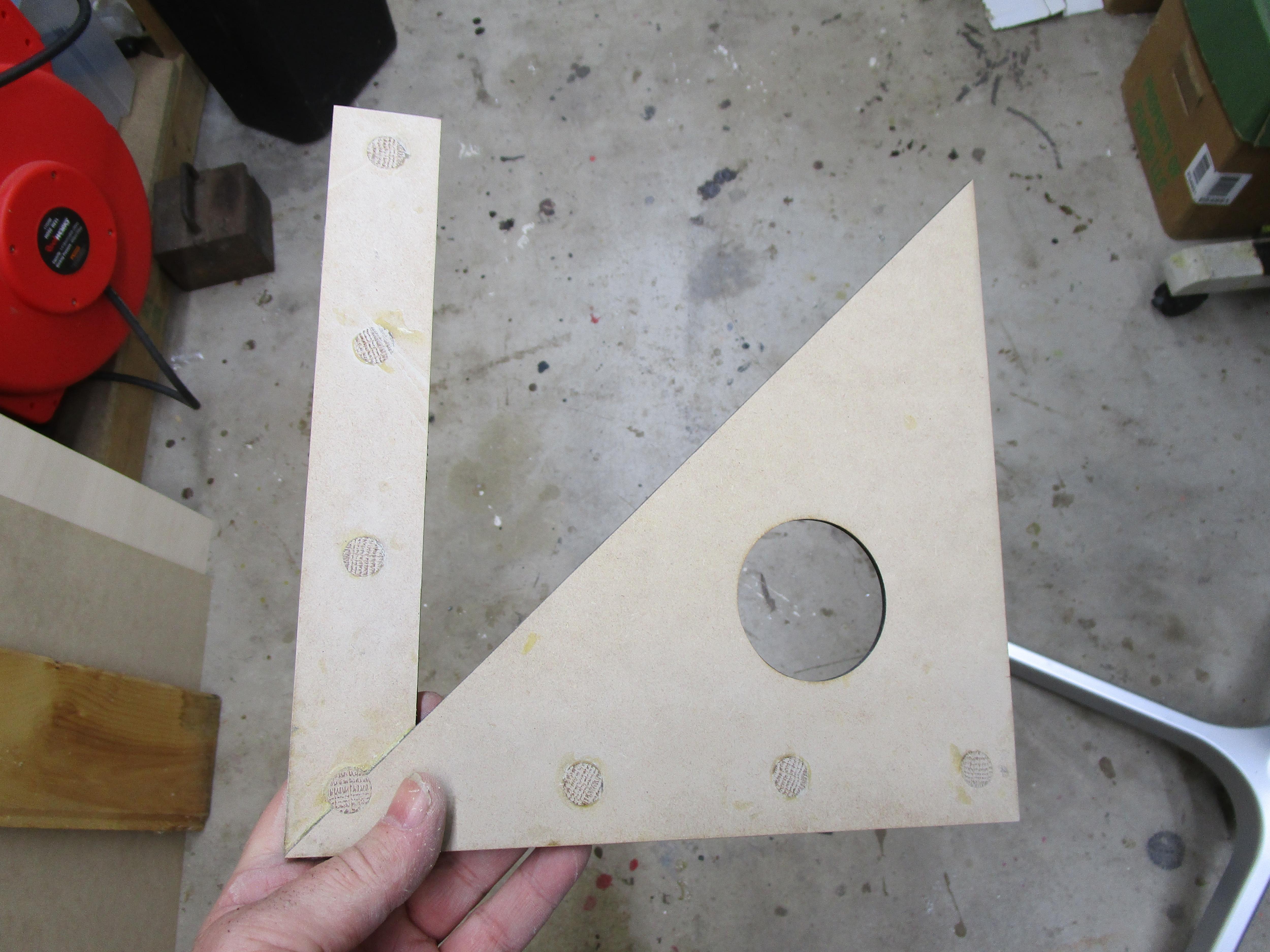
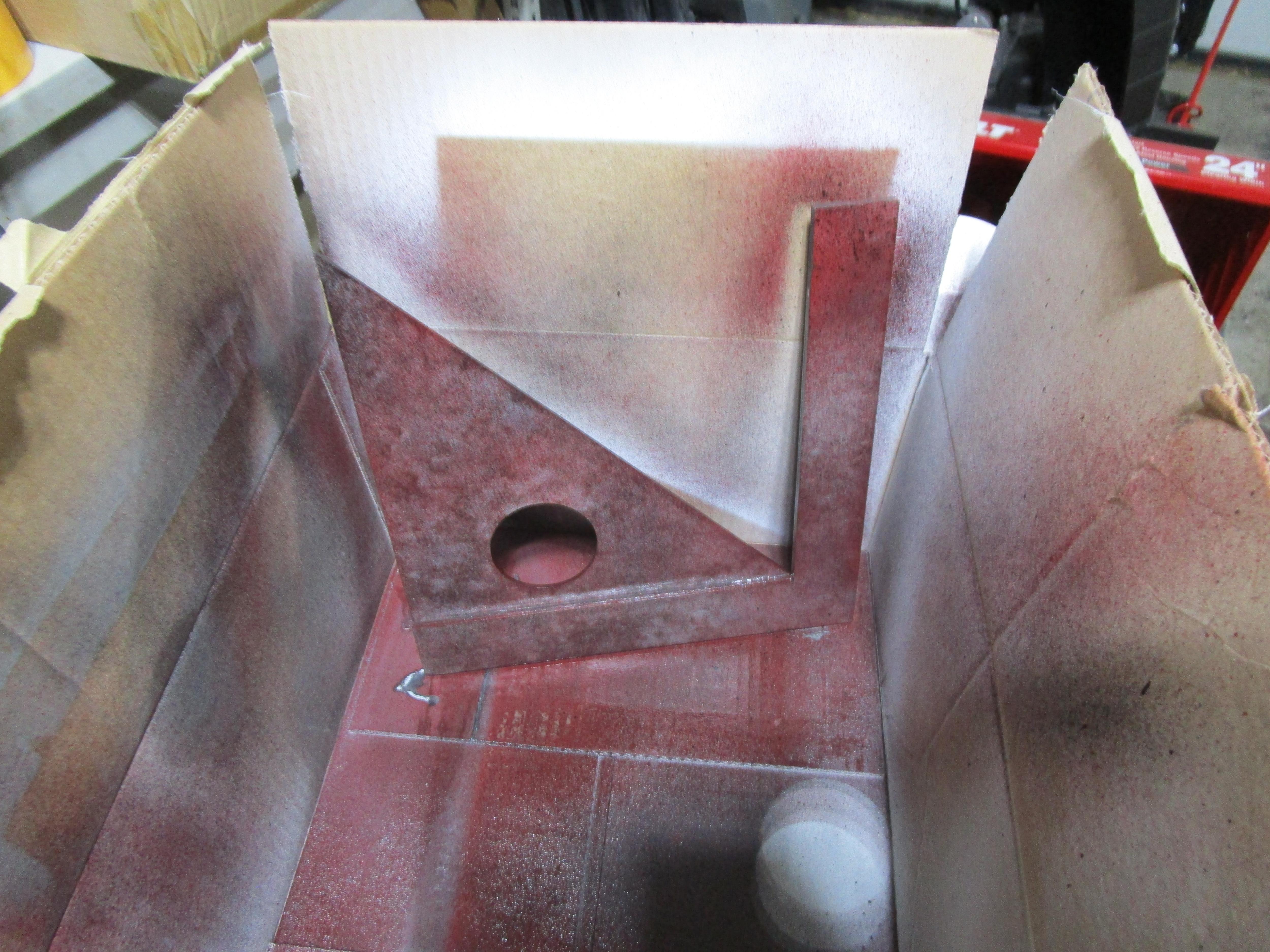
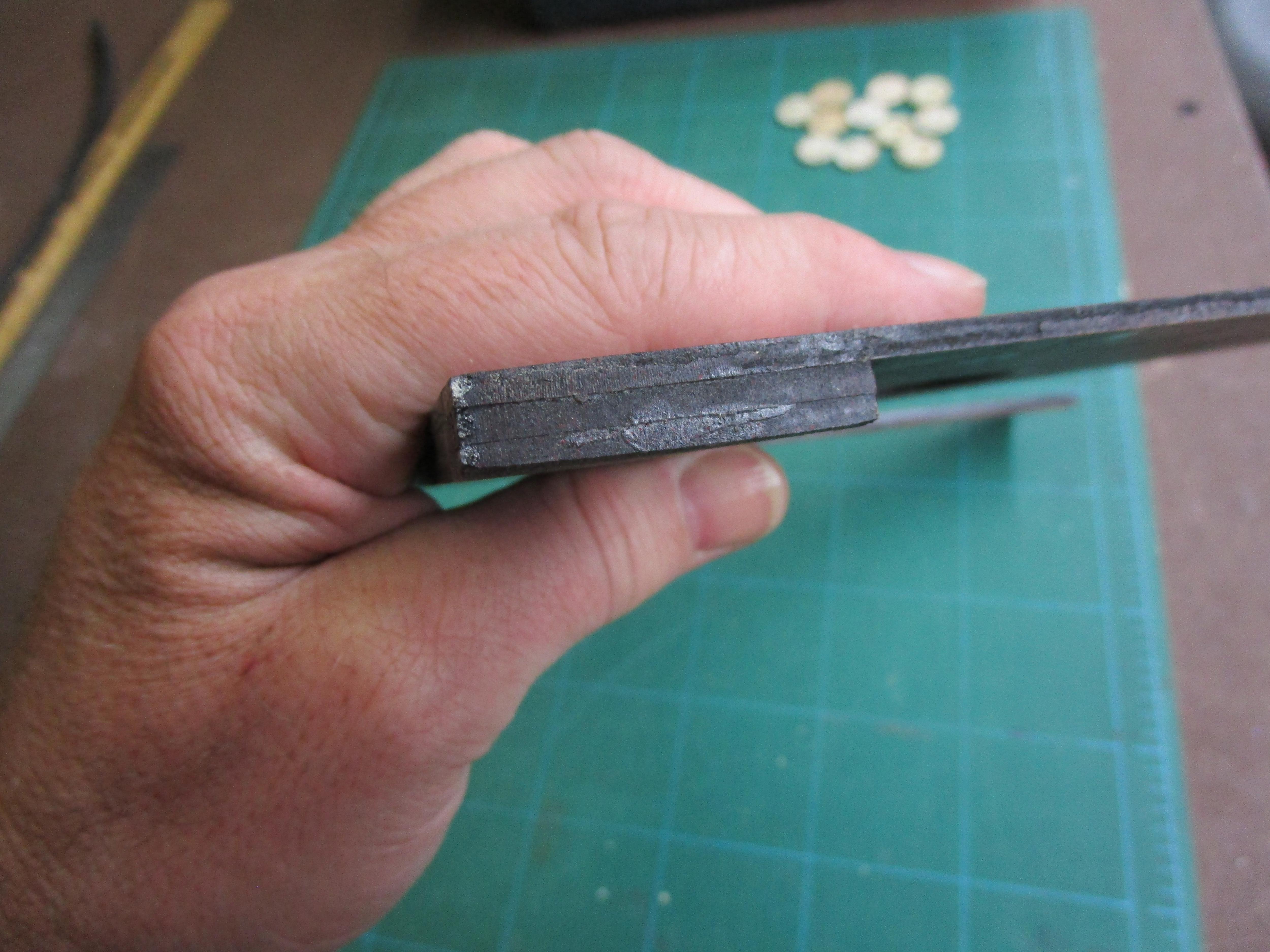
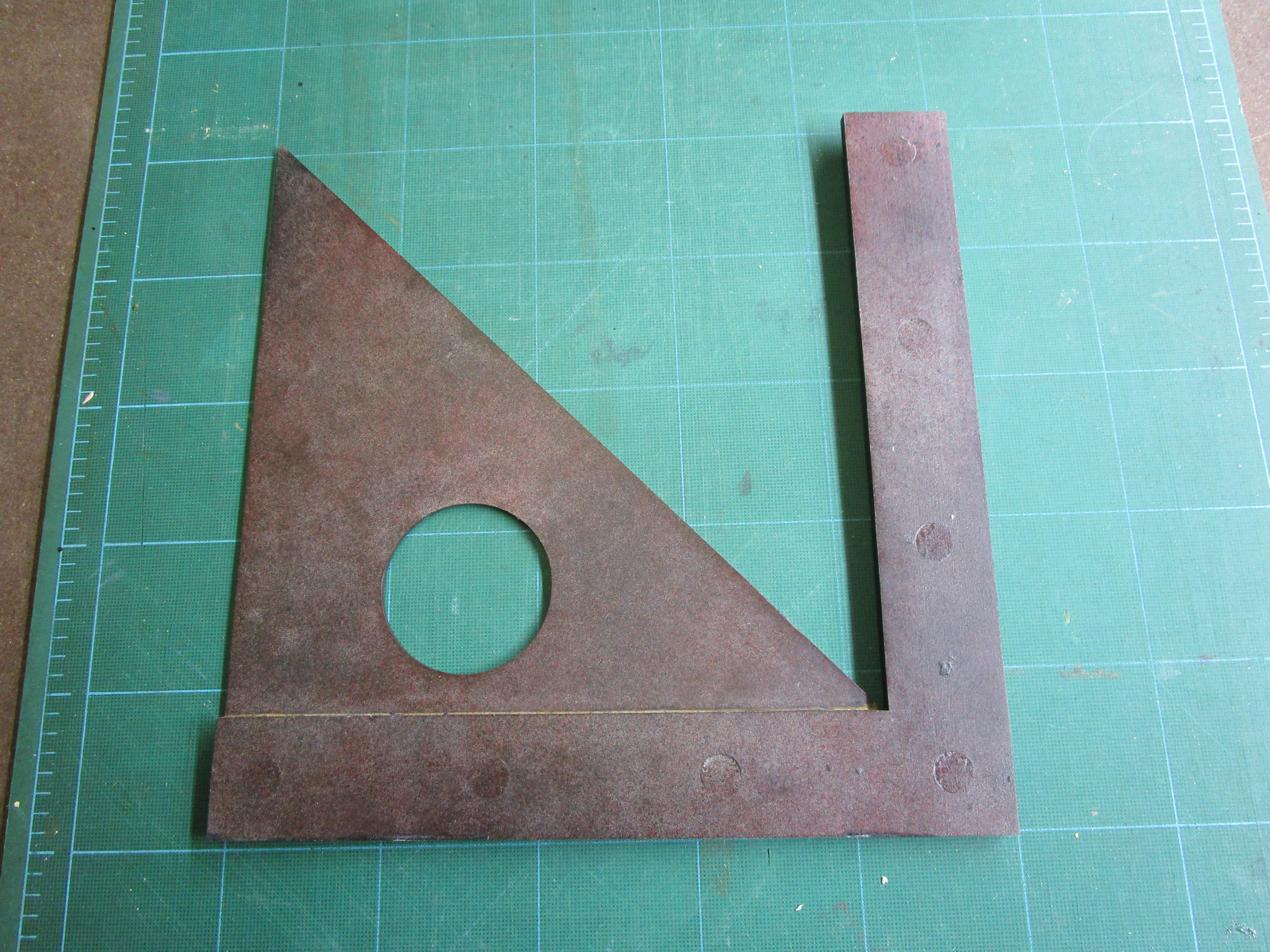
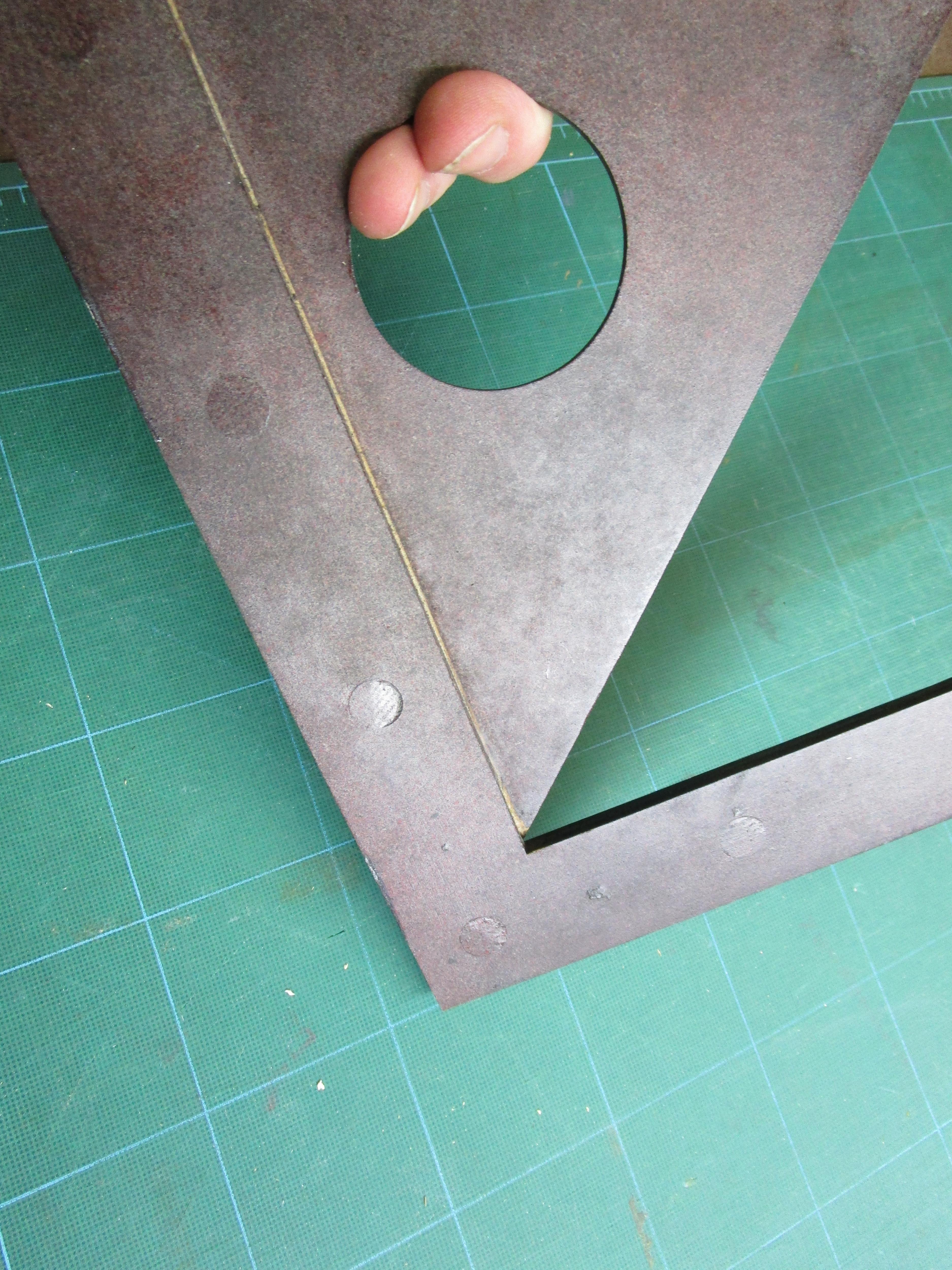
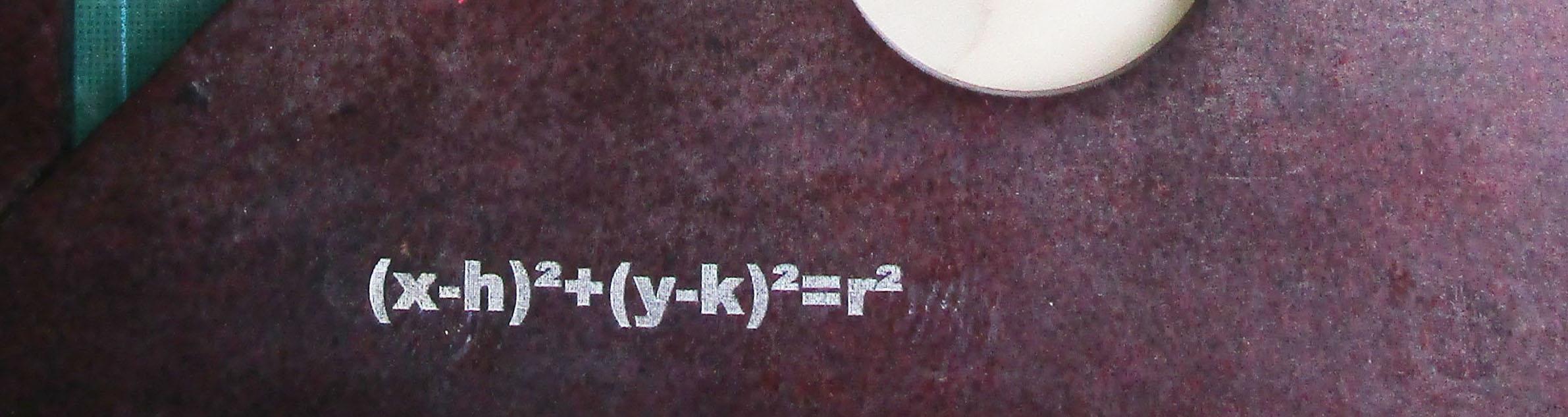
Wait for glue to dry completely then remove clamps. Use a saw to cut off excess dowel, then sand flat. Watch that the saw does not chew into the tool. You want the underside and inside of the "L" to be as smooth as possible. The top is aesthetics. Bottom: Since the dowels should not be protruding and any excess glue should have been removed while it was wet, the underside needs little work.
The "L" needs to be smooth and clean because any defect here can cause an error when measuring with the tool. If there is any glue here, carefully scrape it off.
Paint or leave bare. For grins, I engraved the circle equation in the tool and filled it with silver paint.