Encase Your Friends in Carbonite
by thorssoli in Craft > Costumes & Cosplay
405808 Views, 1802 Favorites, 0 Comments
Encase Your Friends in Carbonite

So I told her.
"Can you really make that?" she asks.
"Sure," says I, "it's actually not such a big deal."
"Does it have to be Han Solo?" says she.
"No," I replied, "it's actually easier if it's someone who can come into the workshop for lifecasting. That'll save me the trouble of finding or sculpting a copy of Harrison Ford's face."
"What if it was me?" says she.
The conversation ended with her gleefully agreeing to come to the workshop and put in all of the labor and pay for all of the materials required to make the project possible. My role was to provide parts and technical advice.
Here's a picture of the finished product. For more information on how it was made, read on...
Lifecasting Hands

The material itself is sold in a powdered form. To use it, you mix it with water and it turns into a gooey mess with about the same viscosity as ketchup. After a few minutes, it hardens into a rubbery solid. It's safe to use in direct skin contact, and you can control how fast it cures by changing the temperature of the water that you mix it with. Warmer = faster.
In order to make a copy of a hand, you mix up a batch of alginate in a bucket big enough to give you at least half an inch of clearance all the way around the appendage in question. Then you stick your hand into the bucket, wiggle it around to work the bubbles away from your skin, assume whatever pose you want the duplicate to have, and wait until the alginate solidifies.
Here's a shot of Jenny showing us what her hand looks like:

After mixing up a batch of alginate, I had her insert said hand. Here she is waiting for set-up time:
Once the alginate has solidified, you need to gently remove the hand by wiggling and twisting and pulling until you break the vacuum and you can slide out.
Here's Jenny wiggling (always a fun thing to watch):
Once she'd slid her hand out, this was the hole that was left behind:
The little bumps you see on the left side of the hole are the pores in her skin. The alginate picks up every fine detail. So much so, that the resultant castings will actually have fingerprints that are identical to hers.
The one drawback to alginate is that, once it cures, it will shrink as the moisture dries out of it. So it's important to pour the casting as soon as possible. In this case I used black casting resin:
During the pour, you have to tip the mold down toward the fingertip side in order to let any trapped bubbles out:
Once the resin sets up, it's a simple matter of breaking apart the alginate and getting the cast resin piece out:
The result: a plastic hand identical to the original:
If you're making this same project at home, you need to repeat these steps as necessary for the number of hands your model has.
Lifecasting the Face

Here's the materials:
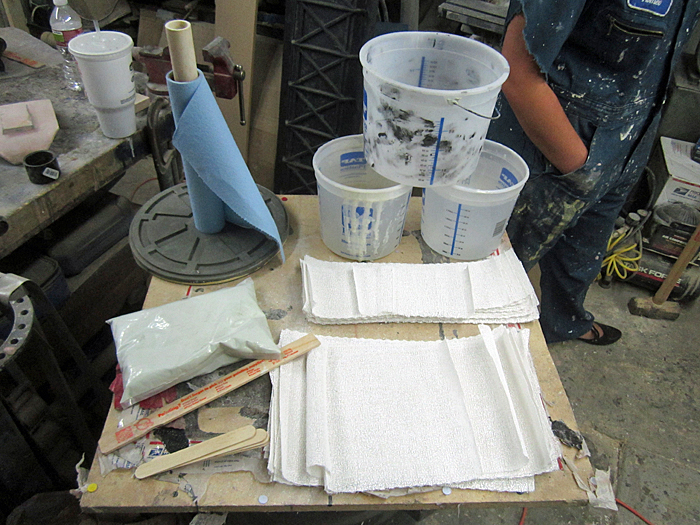
You'll also need a pair of straws for your victim model to breathe through:

It's also a good idea to have your model wear a bald cap and coat their eyebrows and any facial hair with a healthy portion of moisturizing skin cream to keep the alginate from tugging at their hair. Finally, you should place them in a comfortably reclined chair.
Since this project was done on the cheap and I'm an inconsiderate jerk, we taped a plastic bag over her hair and had her sit on a bucket with her head leaned back on a nearby folding table. Good enough.
With all of that set up, it's time for the gloop:

In this case, since the desired duplicate will end up having a healthy dose of exposed cleavage, I also had to layer the alginate over a significant portion of her chest. These are the sacrifices we make.
In order to speed up the process, you should mix the alginate with water that is at least lukewarm. The warmer you make it, the faster the alginate will set up. The trade-off is that you still need to give yourself enough time to get the whole job done before the alginate solidifies, so you don't want it to be too warm.
Once the alginate has set up, you need to build a layer of plaster bandages over it in order to support everything and maintain its shape once the person is removed from the inside.
Again, warmer water will help speed up the process. Here's the beginning of the plaster bandage layer being laid up:
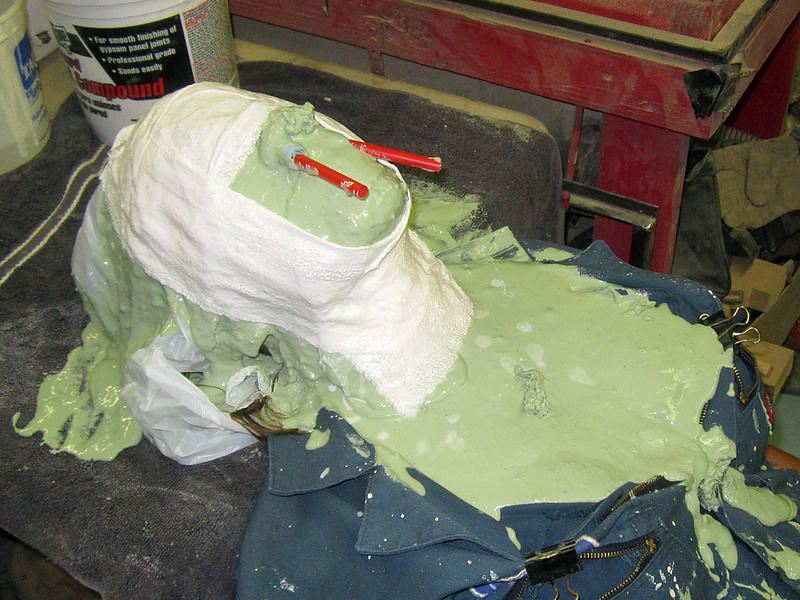
Work as quickly as possible to minimize the time your model will spend cocooned inside:
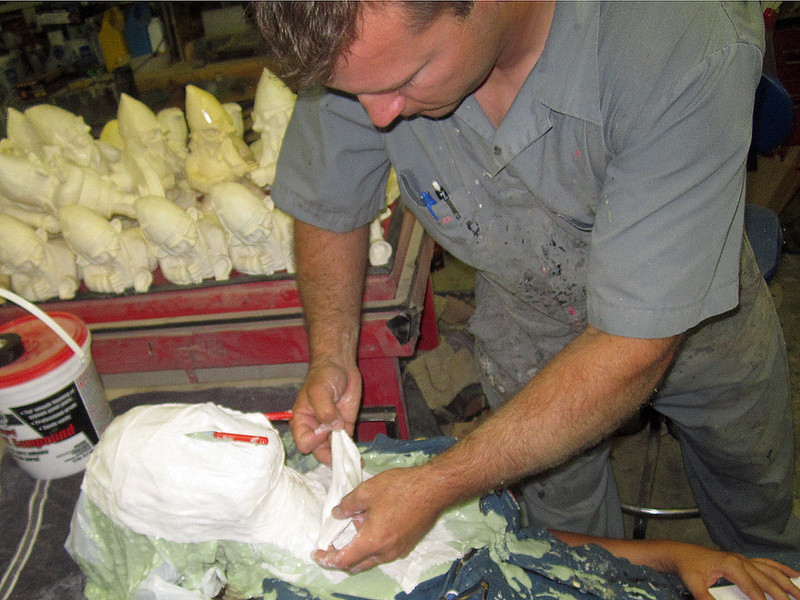
It's probably a good idea to ask long before you get to this point whether or not your model is claustrophobic.
Just saying.
Using warmer water will help the plaster bandages cure faster. You know the whole thing is solid enough to remove it from the model's face when it has cured to the point where you can write embarrassing things on it:

With the plaster bandages hardened, have the model lean forward. Once again, they'll have to wiggle and squirm until the alginate gives up its grip on the skin. In this case, I told her to smile her way out of it:
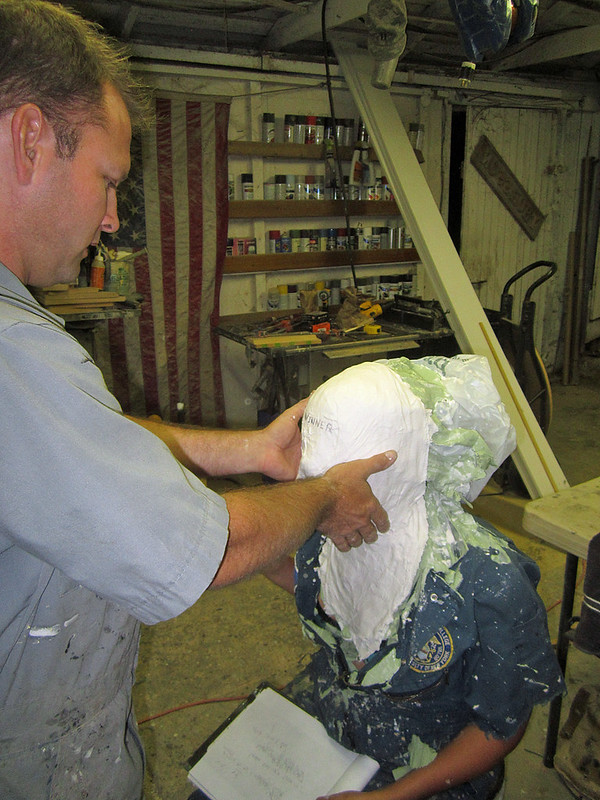
While the model goes off to pick the alginate out of her hair and teeth, I coated the inside of the mold with resin:

Then a bit more resin:

When the resin was built up thick enough to support itself, it was time to remove the plaster shell:
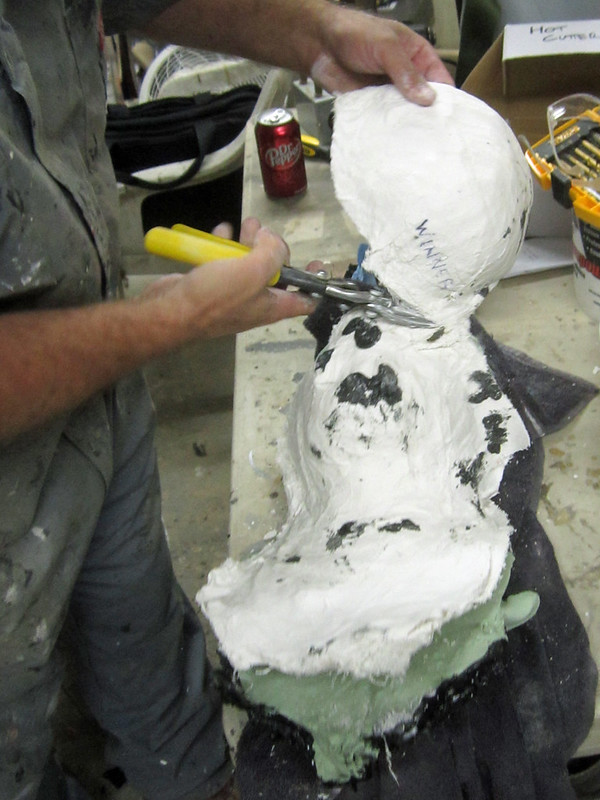
With the plaster shell torn away, it was time to clear away the layer of alginate:
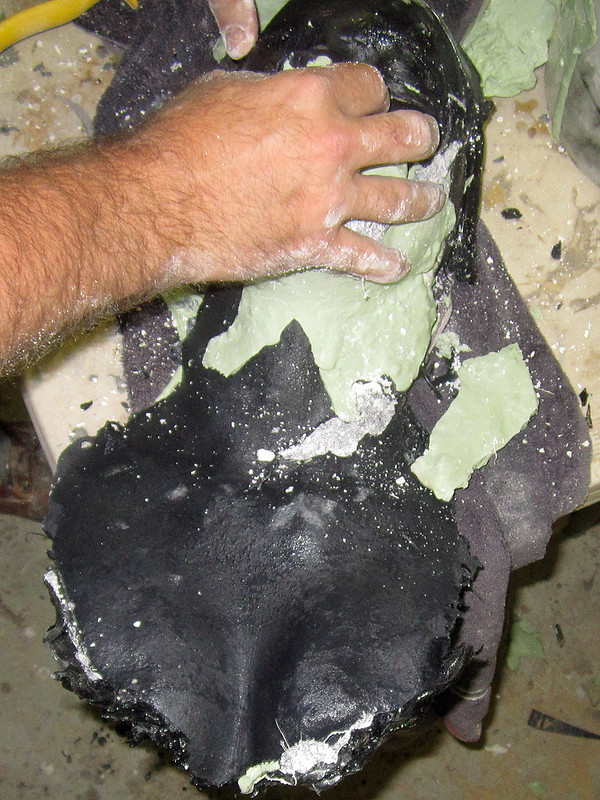
How did it come out? Let's check:

I see significant flaws. The alginate had separated from the plaster shell around the nose and I didn't notice in order to push it back into proper alignment. The result was a somewhat pug-nosed casting with the nose and upper lip pushed in. There was also a split in the mold along the left cheek that resulted in a somewhat excessive ridge on that side.
We can fix it.
Clean Up the Castings

First step: cleaning out the nostril plugs. If you've ever wanted to take a power drill to someone's face, now's your chance:

Next step: adding a bit of Bondo auto body filler to straighten out the squished nose:

It's a good idea to keep the original close at hand so you can make regular comparisons:
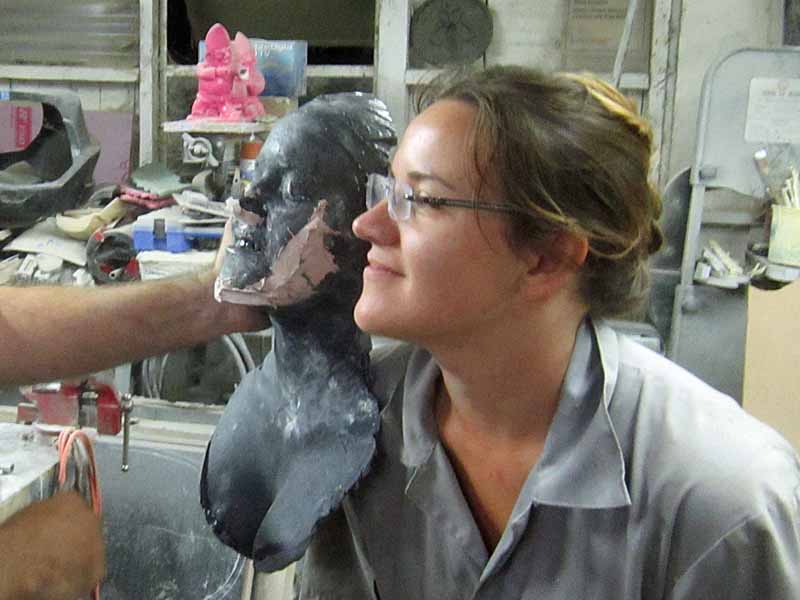
While the Bondo is still soft, you can get away with doing fine-tuning with a knife. Do not attempt this on the original:

Once the Bondo has hardened further, you can do more fine-tuning with coarse sandpaper (also not a good idea to try this on the original):
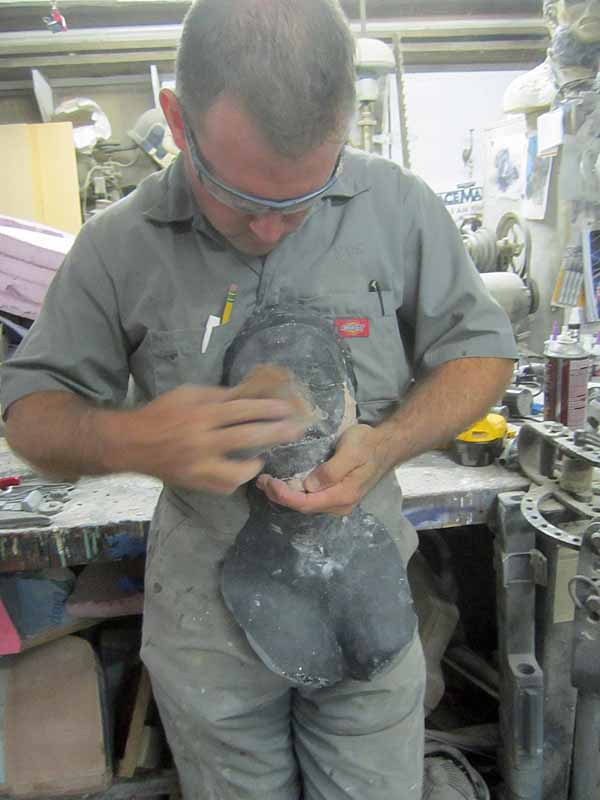
When it seems like you're done, you can spray on a quick coat of primer to check the shape:
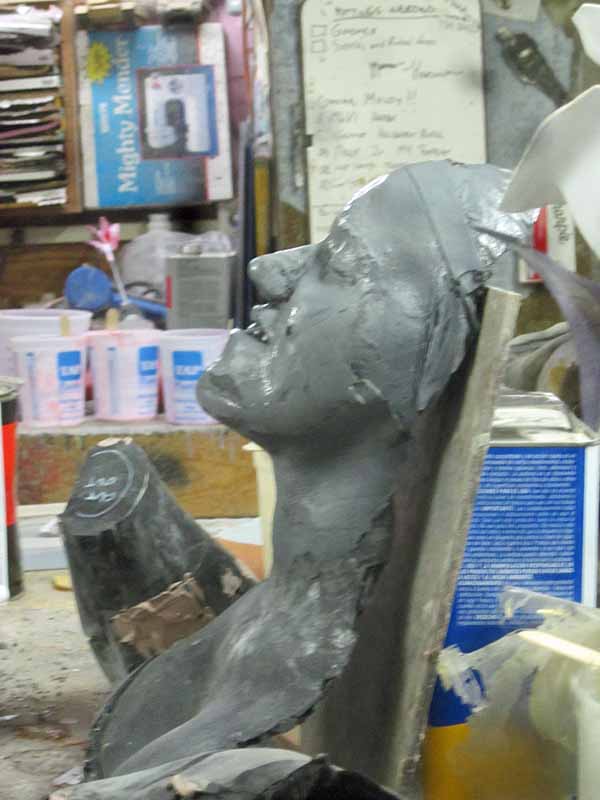
Good enough.
Build the Box

The original piece was tapered slightly from bottom to top. It was also slightly tapered from back to front. Since this was a rush project and there was no reason to go completely insane matching all of the angles, I decided against making screen-accurate tapered sides. I also re-sized the whole piece because Jenny is quite a bit shorter than Harrison Ford was when they built the original.
So I drew up a simplified template to match the look of the original while eliminating some of the less important details. Here she is laying out the cutouts that will go on the sides of the box:

Because she was providing all of the labor, she was supposed to do all of the cutting and drilling. Unfortunately, at this point she had almost no power tool experience, so she needed to be watched in order to prevent her from drilling holes into her hands or, worse, something expensive.
Here she is drilling starter holes:
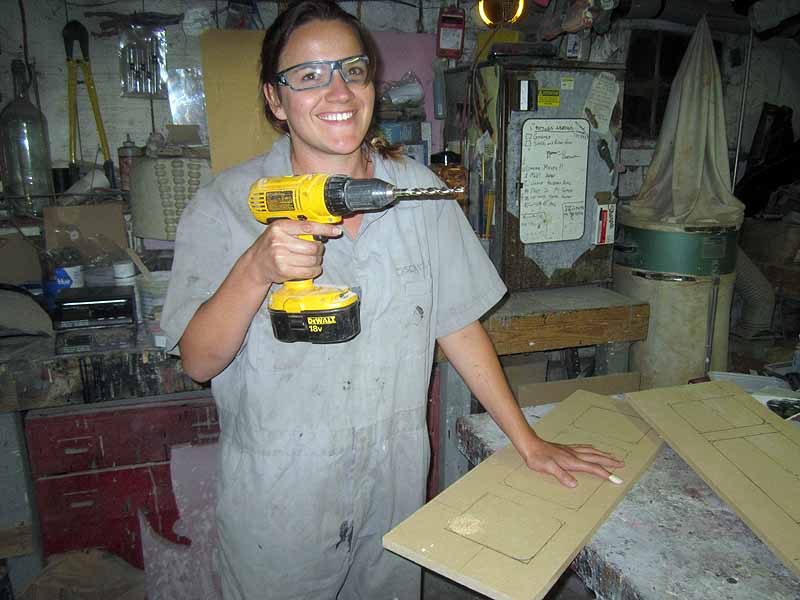
With the starter holes drilled, it was time for her to learn to use the jigsaw:

Here's a side piece all cut out:
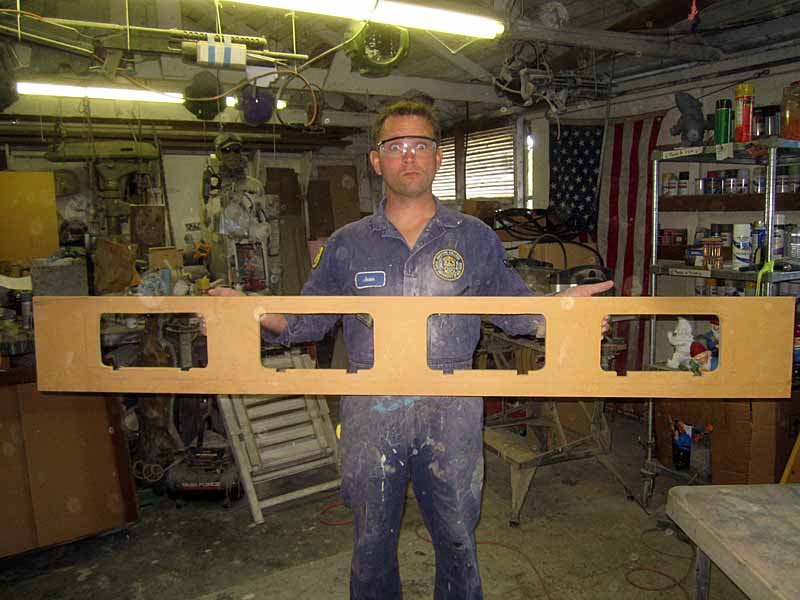
Once the parts were all cut out, all of the seams were glued together with Gorilla Glue:

NOTE: Gorilla Glue will stick to your hands and make a tacky mess that will turn black with dirt and not wash off until you've scrubbed off the skin that it's attached to. Usually it'll take a week or two to get it all off. If you're not ready for that level of commitment in an adhesive/skin relationship, wear gloves.
In addition to the glue, they were screwed together too:

Here's the first three sides of the box coming together:

There was a fourth side too, but I neglected to take a picture when it was attached.
Attach the Body Parts


After adjusting her position to match the pose from the original, I traced the outline of her body on the front panel:

Standing the whole thing upright, I glue the lifecast parts onto the surface, then screwed them on from behind:


This is about the time that this thing became large enough to be a nuisance filling up space in the workshop, so it was time to speed up the rest of the build.
Part 4: the Body
The next step was building up the parts of the body that would be covered in clothing. Since they would be covered, there was no need to go through the lifecasting process. Instead, I sculpted these parts from scratch. I started by mixing a batch of expanding foam:
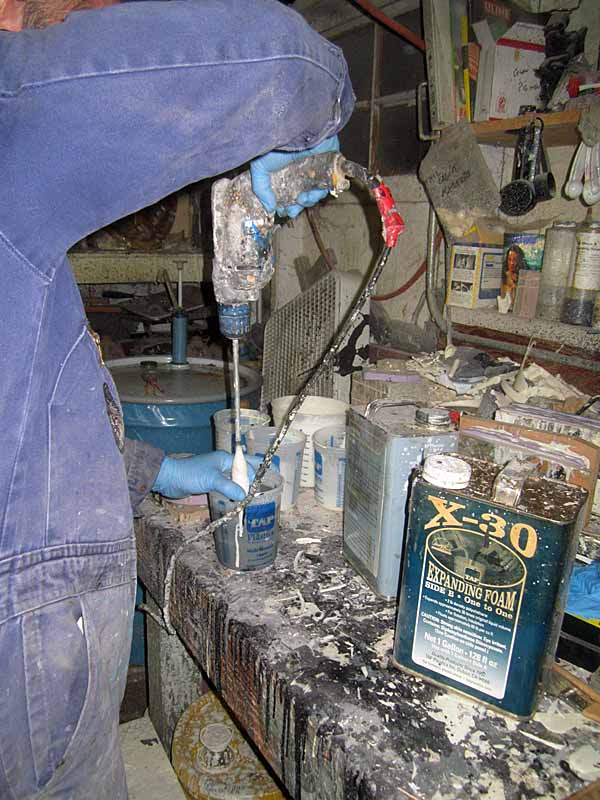
Then poured it into the outlined area:

Since the first batch was too small, I went ahead and poured another batch on top of it:
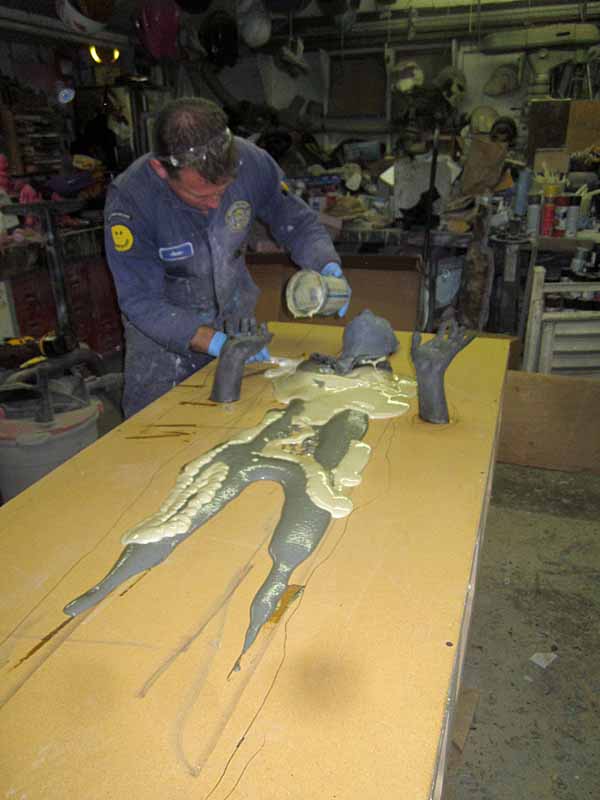
After about an hour it had expanded to full size and hardened enough to start shaping:

Rough shaping was achieved with a kitchen knife:

Smoothing and finer shaping was done with a body rasp:

After a few minutes of work, I had a reasonable facsimile:

To trim the outline of the front panel, I cut strips of 1/2" MDF sheet:
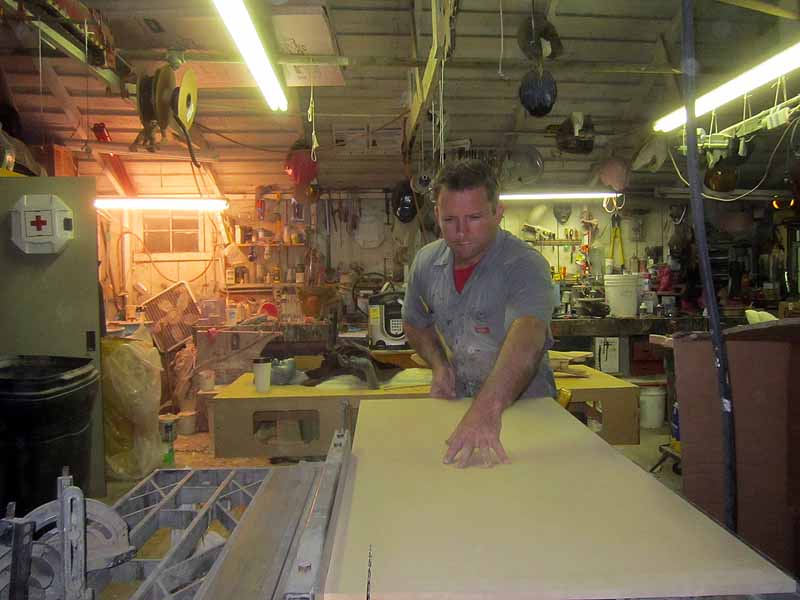
These strips were then glued and screwed onto the surface:

With that, the bodybuilding was done. It's considered poor form to encase someone in carbonite when they're nude, so the next step was dressing up the body.
Dress the Body and Make It Solid


With the unnecessary parts of the dress removed, the next step was to drape the remainder over the body and decide how the fabric will fall:
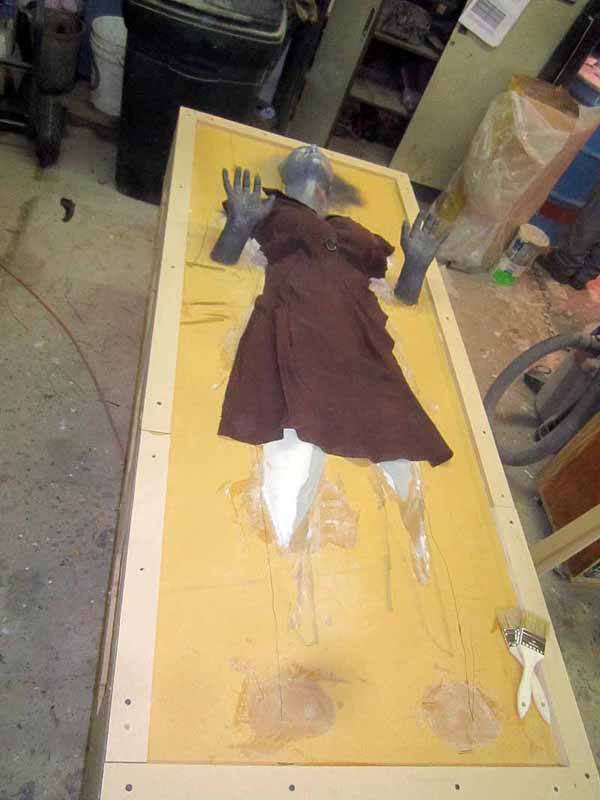
Once I was satisfied with the look of the dress, the next step was to coat the foam body form with a batch of urethane casting resin:

Working as quickly as I could, I re-draped the dress and soaked the fabric with more resin:
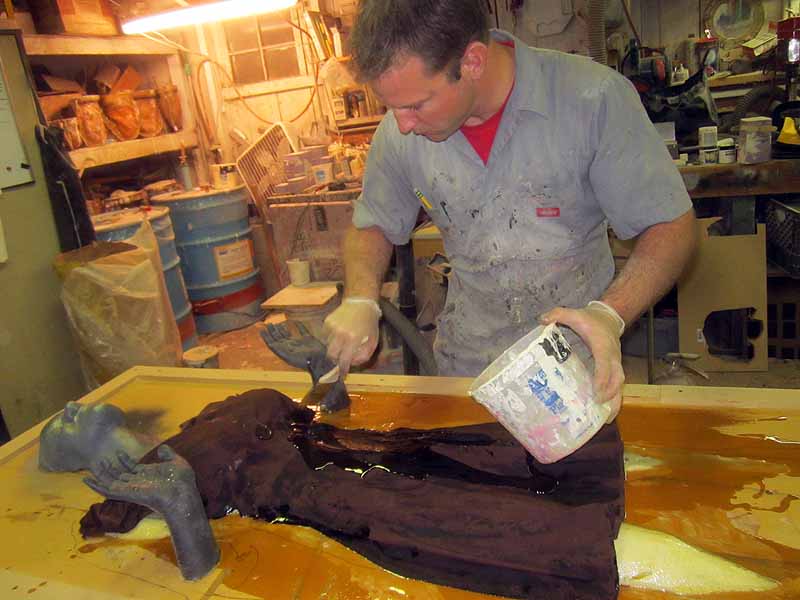
Here you can see the resin turning off-white as it starts to cure:

I mixed a couple of smaller batches of resin and used them to add texture to the flat open areas on the front of the piece. The goal was to stir up and stipple and puddle the resin so that there were no smooth areas left on the front panel.
With that done, all that remained was to mix a couple of batches of Bondo and fake a quick and simple hairdo:

Then it all got a good coat of black primer:
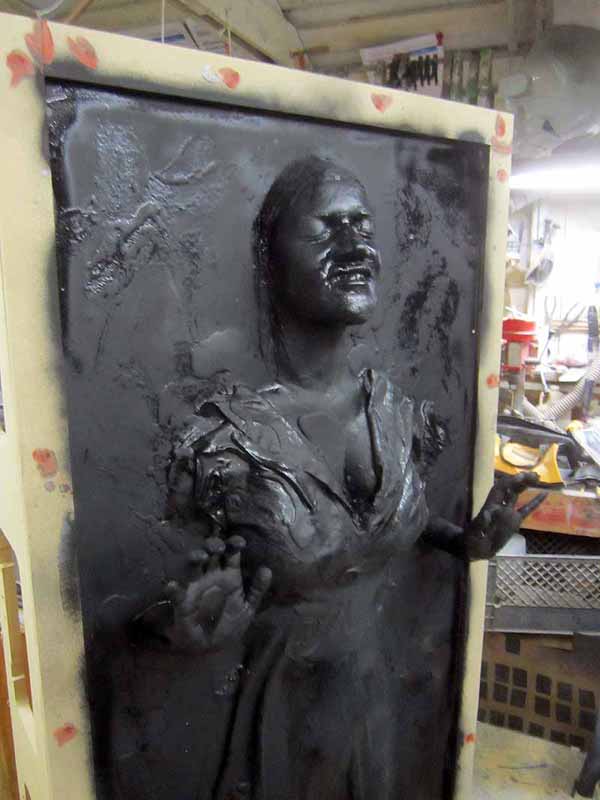
Here's a full-length shot:

With the big parts done, now it's time to focus on the small parts.
Add the Little Details

I tasked Jenny with finding a photo of one of the original panels. Then I handed her a block of MDF and told her to add sheet plastic to it and cut in windows so it would look as close as possible to the original. Here she is in the middle of that process:
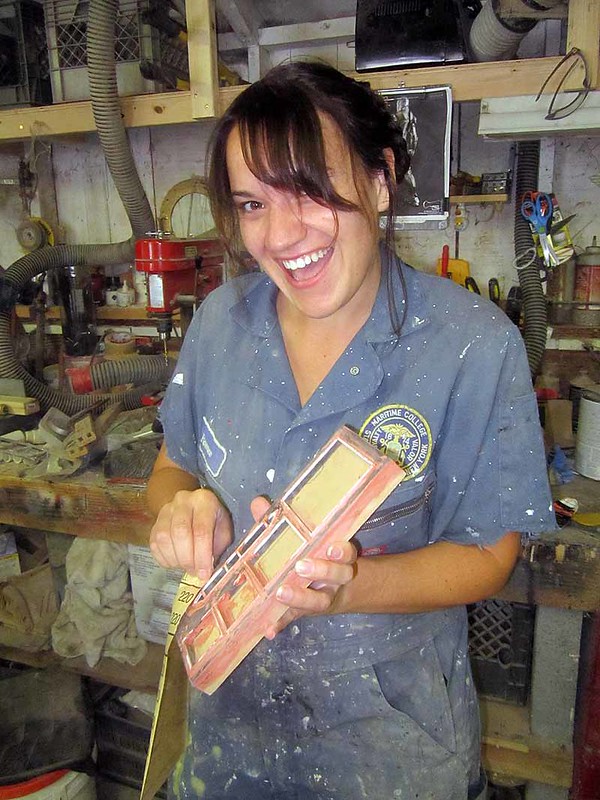
I also had her cut panels out of 1/2" MDF to match the holes in the side panels:

Here's one of them fitted in place before being pushed in for an adequate recess:

The original display panel Jenny made was molded and eight copies were cast in urethane resin.

Holes were drilled randomly in the display panels and we wired them up with LEDs:

Lots of LEDs:
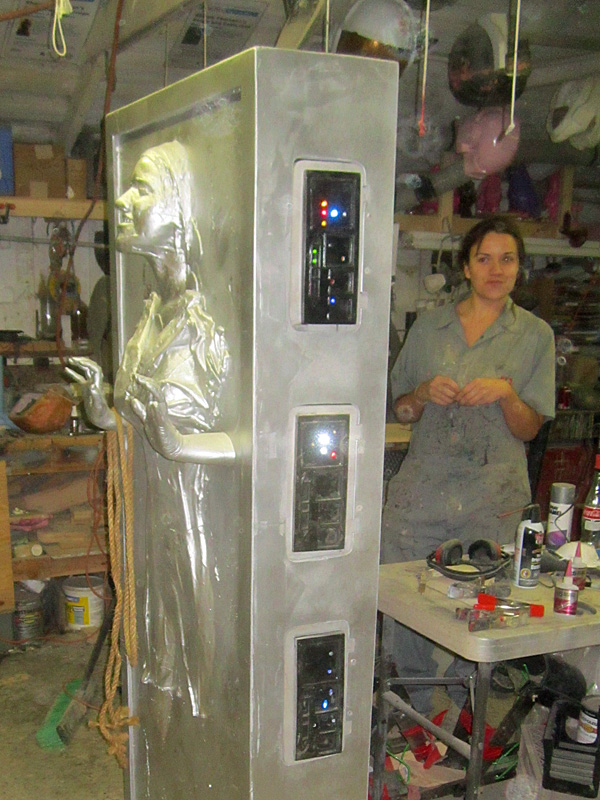
Seriously. Lots:
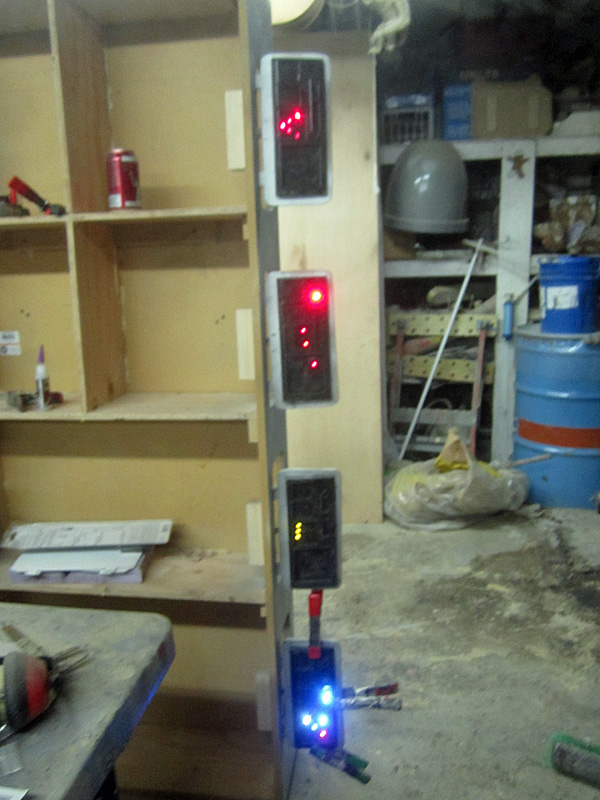
Some of them were blinking LEDs, some of them were high-intensity, all of them were completely added at random. Once the wiring was done, scraps of tinted acrylic were cut out to fit into the display windows and make them look a little less cheesy. Then we took some random small parts left over from the Ghostbusters project and glued them on to make the panels a tiny bit more interesting.
Here's what it looked like after it was painted:


Here's some closeup shots of the panels:


Oh, right. I haven't described the painting process...
Paint

The whole process began with a few coats of silver spraypaint:

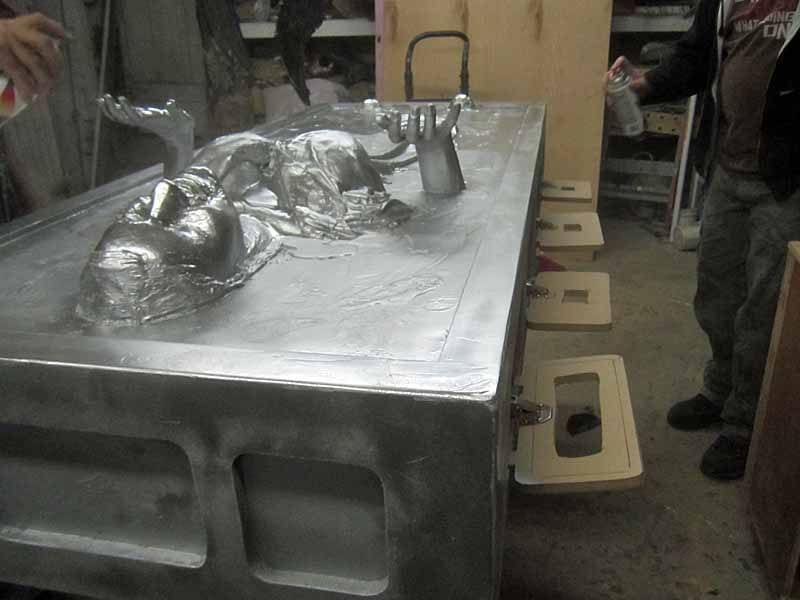
In between coats, Jenny put another layer of filler on the visible screw holes:
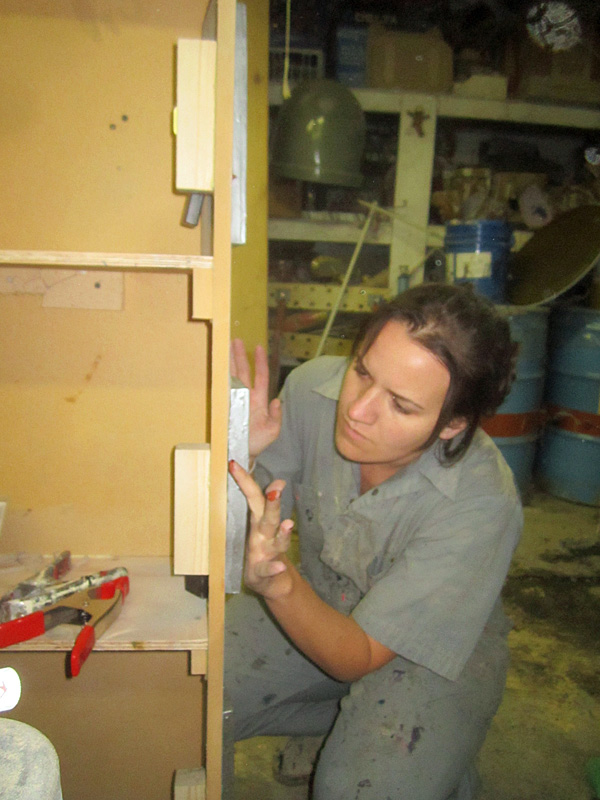
When the base color was completely done, it looked like so:

Once the silver had had plenty of time to dry, it was time for a blackwash. This would darken the color and bring out all of the various details and textures. In this case, I began by slathering it with black acrylic paint:
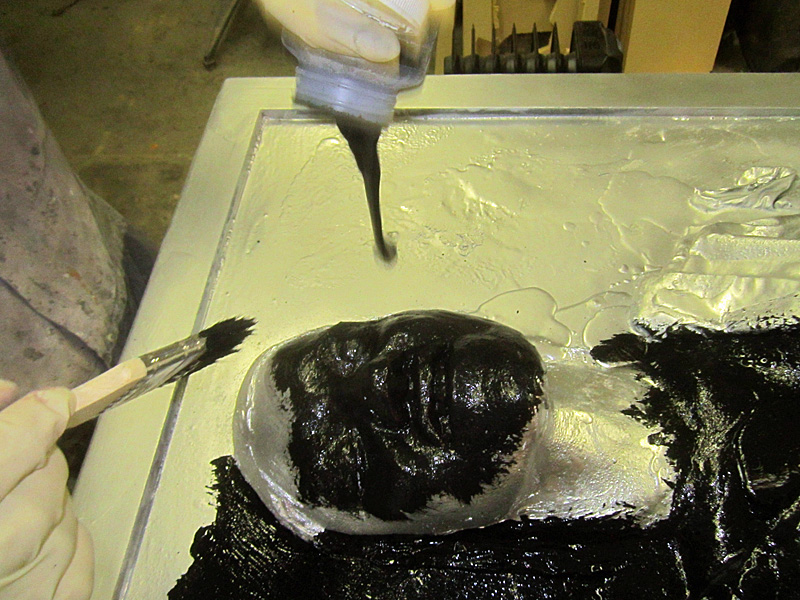
Jenny spread the acrylic paint over the whole thing:

Before the paint had any time to dry, the next step was to water it down and then wipe, dab, spread, and smear it all over with very damp rags:

As the paint started to dry, we gradually switched to dryer and dryer rags until we were buffing nearly dry paint off of the highest surfaces and most prominent details. The resulting finish looked like so:
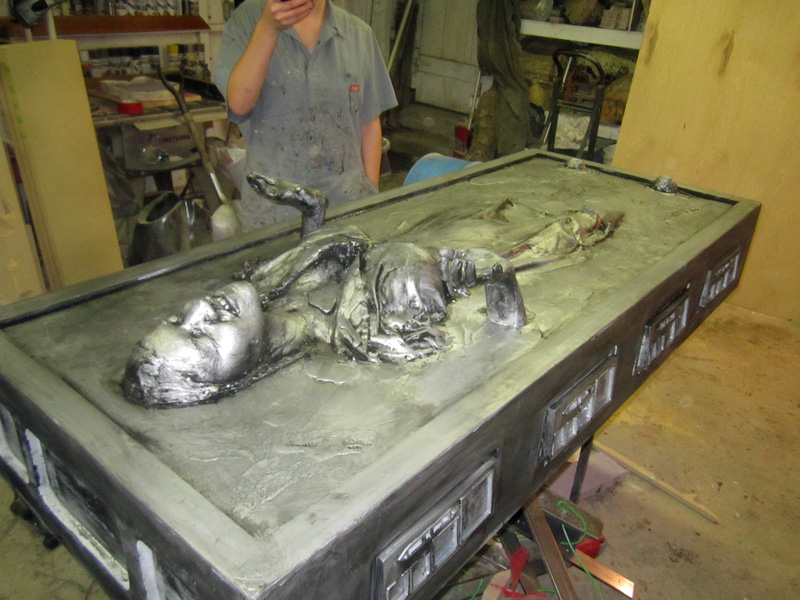
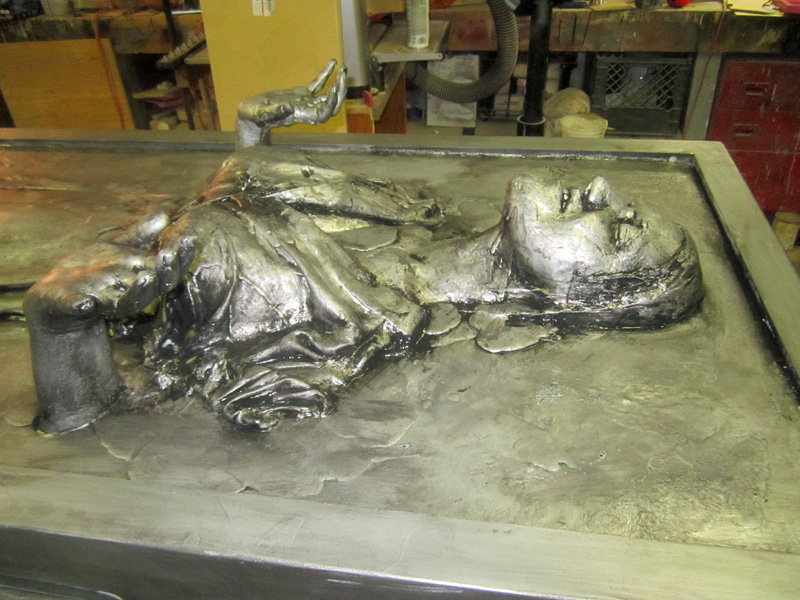
I think we managed a fairly decent approximation of the look of the original:

With the look of the outside all taken care of, it's time to figure out how the whole thing will work.
Make It Functional

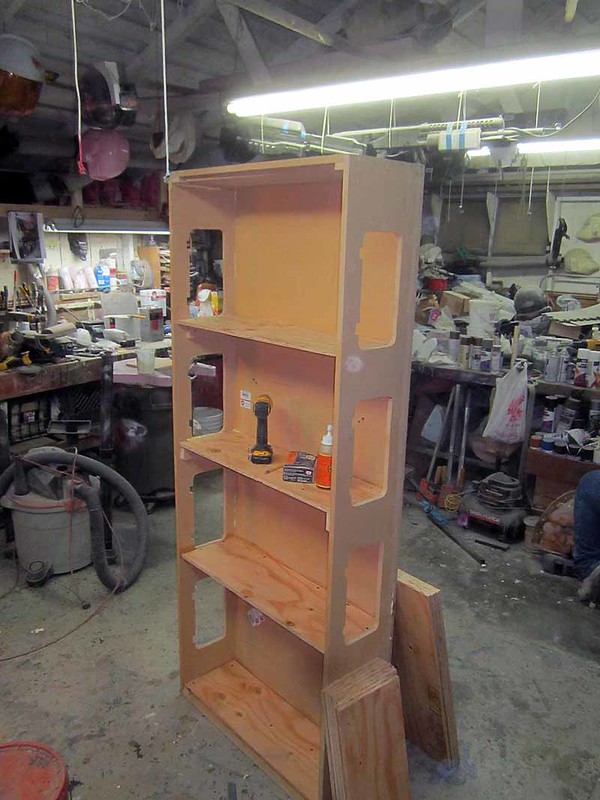
The recessed panels that the display panels are attached to are actually hinged:

Hinge installation gave Jenny another excuse to use power tools and frighten everyone within arm's reach:

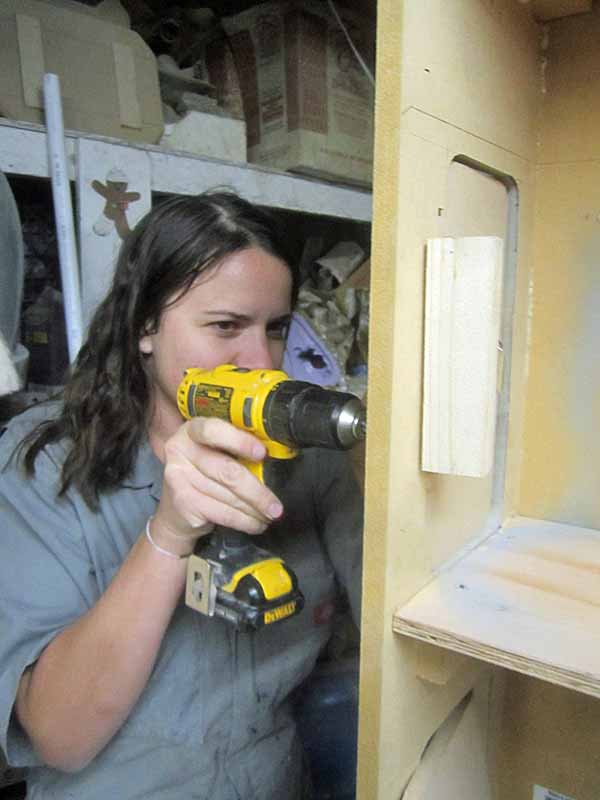
With all of the shelves installed and the hinges mounted, it was time to close up the back and fit it with cleats for hanging it on the wall:
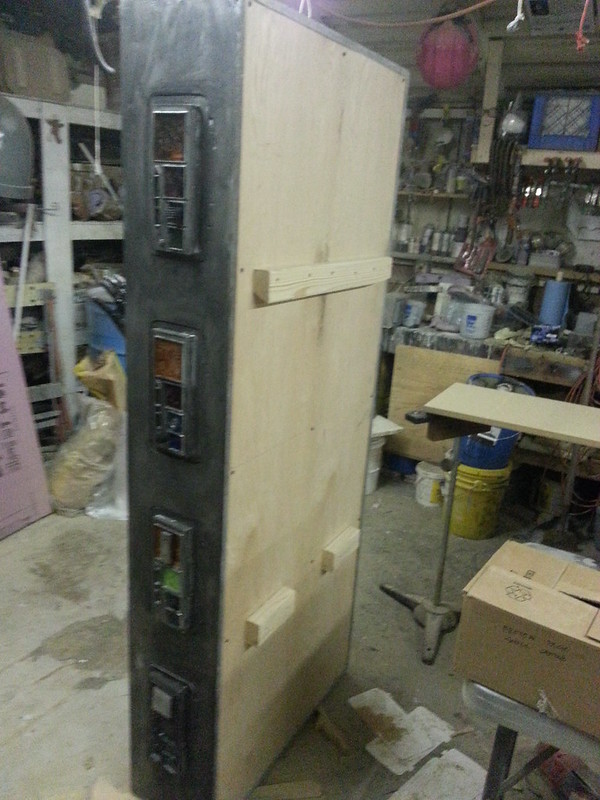
Finally complete, all that was left was to load up "Jenny in the block" for delivery:
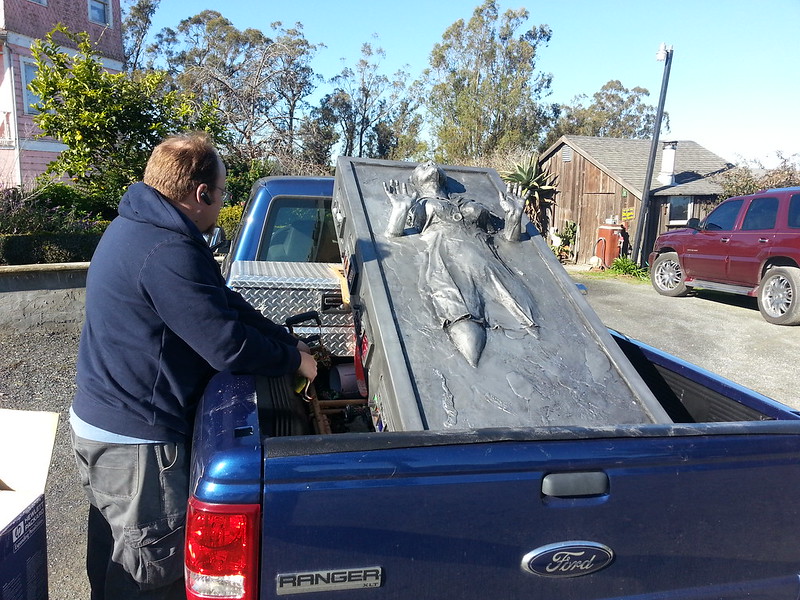
Once we had it in the back of the truck, I donned my Boba Fett helmet and we paraded it all the way through town before heading over to her house and surprising her with the finished piece (by leaving it there when she wasn't home).
Mission accomplished.