DIY Stylish Wooden Keepsake, Jewelry and Gift Box!!
by tin-foil-hat in Workshop > Woodworking
4559 Views, 44 Favorites, 0 Comments
DIY Stylish Wooden Keepsake, Jewelry and Gift Box!!




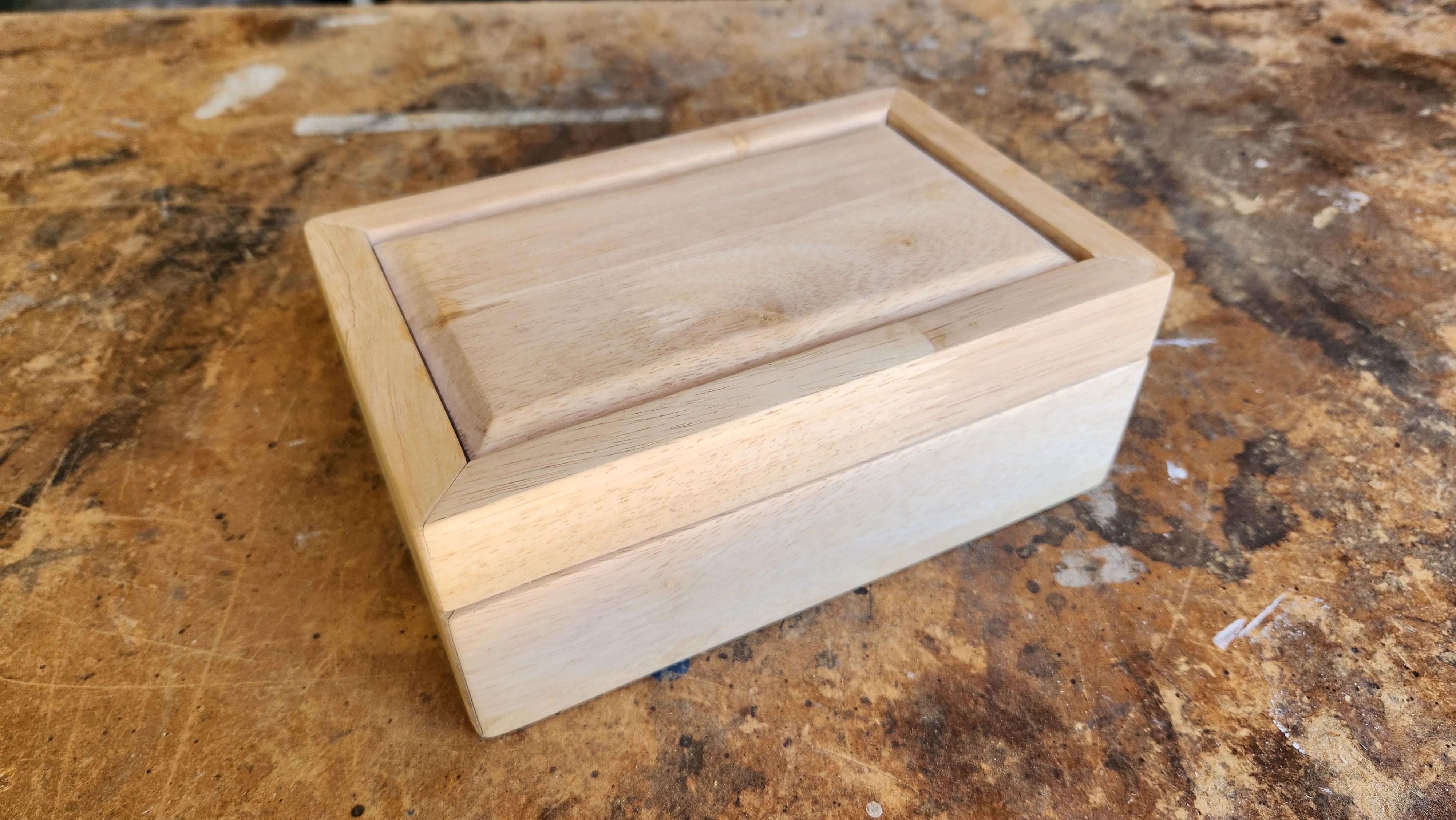







Do you love woodwork but are looking to level up your projects? Well then this instructable is for you! This stylish keepsake box has a wide range of intermediate woodworking skills such as rabbets, grooves, mitres and routing to help you take your next woodworking step as a beginner. With Christmas (just passing) and valentines day around the corner, this could be a perfect opportunity to give someone a baked gift in more than just a plastic tub. In my case, I wanted to gift someone my home-baked gingerbread and needed a small box to do so. Additionally, you could scale this box up/down to be used as a storage chest or small jewellery holder (although I think the current size is a sweet spot between practicality and storage capacity). It is a perfect weekend project you could do to get outside or spend time with your parents/kids.
Supplies



For this project you will need the following materials:
- Wood (the dimensions are part of the next step)
- 2x hinges (for my size box I bought the cheapest hinges I could find, which were 50 x 40 x 1.2 fixed pin butt hinges)
- 8x screws to suit the hinges (they almost always come with the hinges themselves)
- Wood glue (I used PVA)
- Masking tape (Used for the glue-up)
You will also need some basic tools:
- Circular saw (or table saw)
- Sandpaper & Vibratory/Orbital sander (or a lot of determination to do it by hand)
- Hand saw (or table saw)
- Drop saw (or a saw capable of 45deg mitre cuts)
- Plunge router & straight cut bits (I used 8mm & 12mm) & a large chamfer bit
- Hand planer (or thicknesser - or buy wood the correct thickness ~15mm)
- Drill & drill bits to suit screws
- Ruler & pencil (or similar for marking lines)
Optionally:
- Ribbon (for wrapping it as a gift)
- Scissors/Knife to cut the ribbon
- Fork (to tie bow)
- Lighter (to seal the end of the cut ribbon)
- standard fencing wire (to make a branding iron)
- wire cutters & long nose pliers
- blowtorch (or gas stove)
Dimensions
I chose to make a 200 x 130 x 80mm box out of a 15mm thick panel of wood (that I salvaged from an old tabletop). For this, you need the following pieces of wood:
- Two 130x80mm side panels (with 45deg mitres on the short edges)
- Two 200x80mm front and back panels (with 45deg mitres on the short edges)
- Two 180x110mm top and bottom panels
When you choose the orientation and layout of your pieces, remember the direction of the grain. You want the grain to run lengthwise along all panels (this isn't strictly necessary but will make the finished product look nicer). I will talk more about layout in step 3.
You can choose any size for your box, but (assuming you use 15mm thick wood) subtract 20mm from the width and depth of your desired box to get the measurements for the top and bottom. Generally, for a nice-looking box, you can divide the length of the box by the golden ratio (~1.6) and then round up or down to get the depth, and similarly, you can divide the depth by the golden ratio to get the height. This isn't a rule, but can help you if you are new to woodworking!
e.g. 200/1.6 = 125 (rounded to 130) > 125/1.6 = 81.25 (rounded to 80) > thus 200mm wide x 130mm deep x 80mm high
Thickness




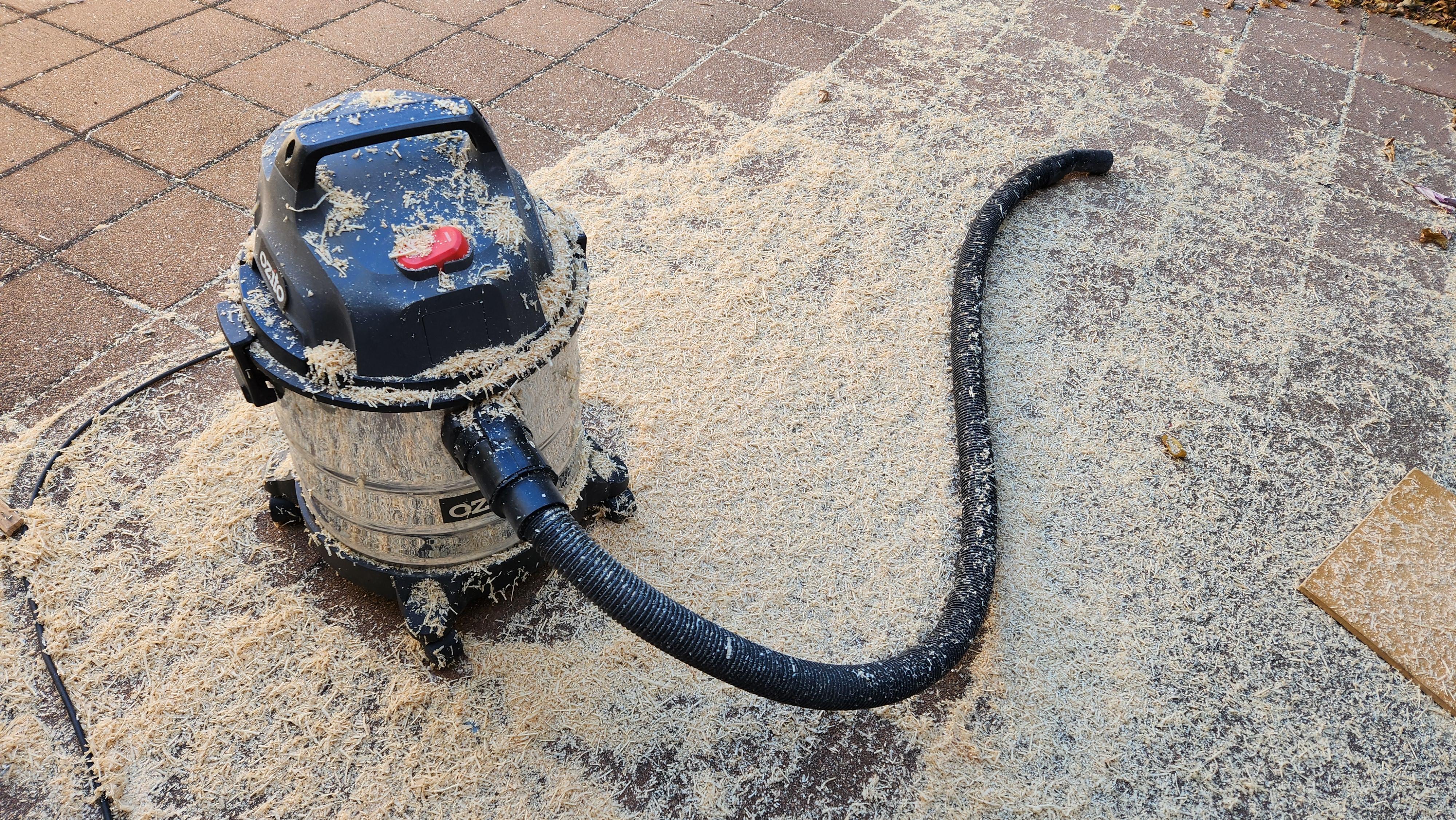
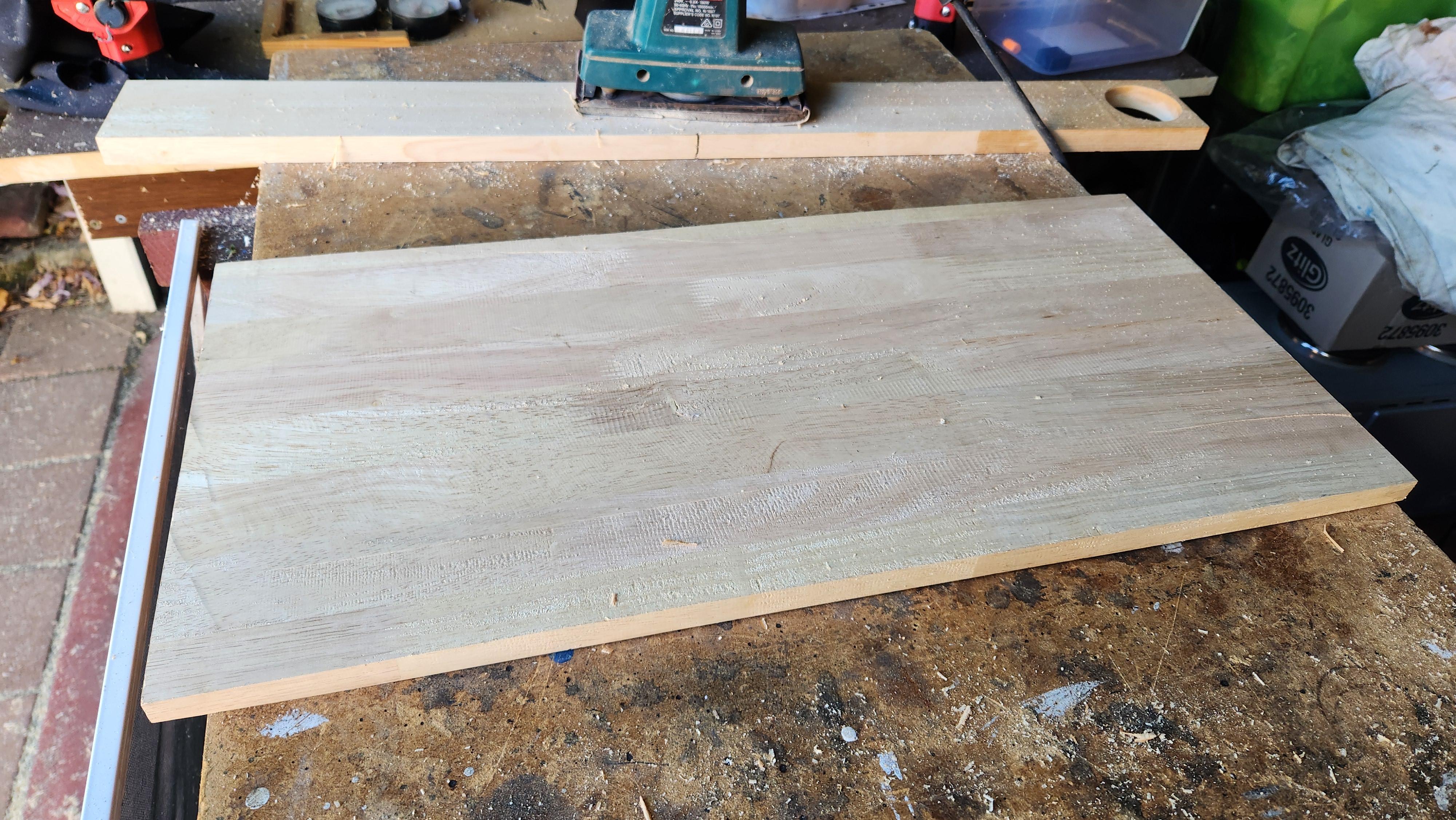




The first step is to take your material to thickness. You don't want it to be too thick as then your box will weigh a ton, but similarly, you don't want it too thin that it'll break if you look at it too hard. I opted for 15mm thick. If you have a drum sander or thicknesser this step will be super easy for you. Otherwise, grab yourself a power planer and get to work! I recommend taking around a 0.5 - 1mm pass (depending on if you are using hardwood or not) and moving left to right such that your adjacent pass doesn't take any more material off the first pass. I also recommend scribbling a squiggly line with a pencil over your entire work face between passes so that you can see where you have already planed. In the end, you might be left with little score marks, but you can sand those out with an orbital/vibratory sander. If you are planing by hand, you should sand your surface so that it is relatively flat, and so that it is uniform in thickness (more or less) over the entire board. The more time you take to get your stock material correct, the more likely everything will fit later on.
Mark Up Cuts

This step is only needed if you don't have a tablesaw, or if you want a visual representation of the layout we are going to cut. Regardless, you should use the pictures above as a guide to help you figure out how to lay out your material layout. If you are using a completely different-sized material (for example a plank rather than a board) you should use a cut list optimiser (I use https://www.cutlistoptimizer.com/) to figure out how to minimise waste. If you are marking up the boards, remember to account for curf (aka the material lost to the width of the saw blade), most commonly the curf is 3mm.
Rip Cuts



If you are using a panel/board like me, you need to rip it down into plank-like strips. If you have a table saw, you can just set the fence width and run the board through. If you are using a circular saw like me, you will need to clamp down the material, set up a fence using a scrap piece of wood, and then move the fence far enough away from the cut such that the circular saw will cut in the desired location. Your circular saw may have a small line to indicate where it will cut, but make sure you do a test cut first, as I found mine was wildly inaccurate. A good trick my Dad once showed me was to cut into a scrap board (see the darker brown board in the images above) about halfway, such that you can use it as a reference when lining up the "fence" (see the lighter yellow piece of wood in the images above).
Routing Grooves





After we have cut out our strips/planks, we want to route some slots in the two thinner boards (which will make up the 4 sides). To do this, take a plunge router and screw in a straight cut bit that is thinner than the board thickness, but not much thinner than 5mm (mine was 8mm wide). Then plunge around half the depth of your board (for me, this was 6mm). If you have laid out your pieces the same way that I have, then you should have some excess on either end which means you don't need to go right to the edge. Remember that these side panels will be cut at 45deg mitres which means that the side you route, will become the inside face of the edge. You want to set the width such that the top & bottom will sit flush with the rest of the box. For this, take the width of your board (15mm) and then subtract the width of the router bit (8mm), this leaves 7mm (in my case). Set your plunge router fence such that it results in a 7mm gap between the edge of the board and the start of the slot's edge. To check your fence is set correctly, you should first test this in a scrap piece. The distance between the furthest side of the groove to the edge of the piece of wood should be equal to the thickness of your material.
Cutting the Top and Bottom to Size


To cut the top and bottom to size, simply use a drop/circular/table saw and dock them to length. This should be a straight 90deg cut.
Cuting Mitres





Next, we want to cut all the edges to size. These need to be cut at a 45deg mitre. For this, I used a drop saw but you could use any saw capable of a 45deg cut. You need to ensure that the shorter side has the slot, and make sure that each edge of the side has opposite 45deg angles such that you can assemble it into a box. If you are unsure of what I mean, refer to the second image above.
Routing the Top & Bottom








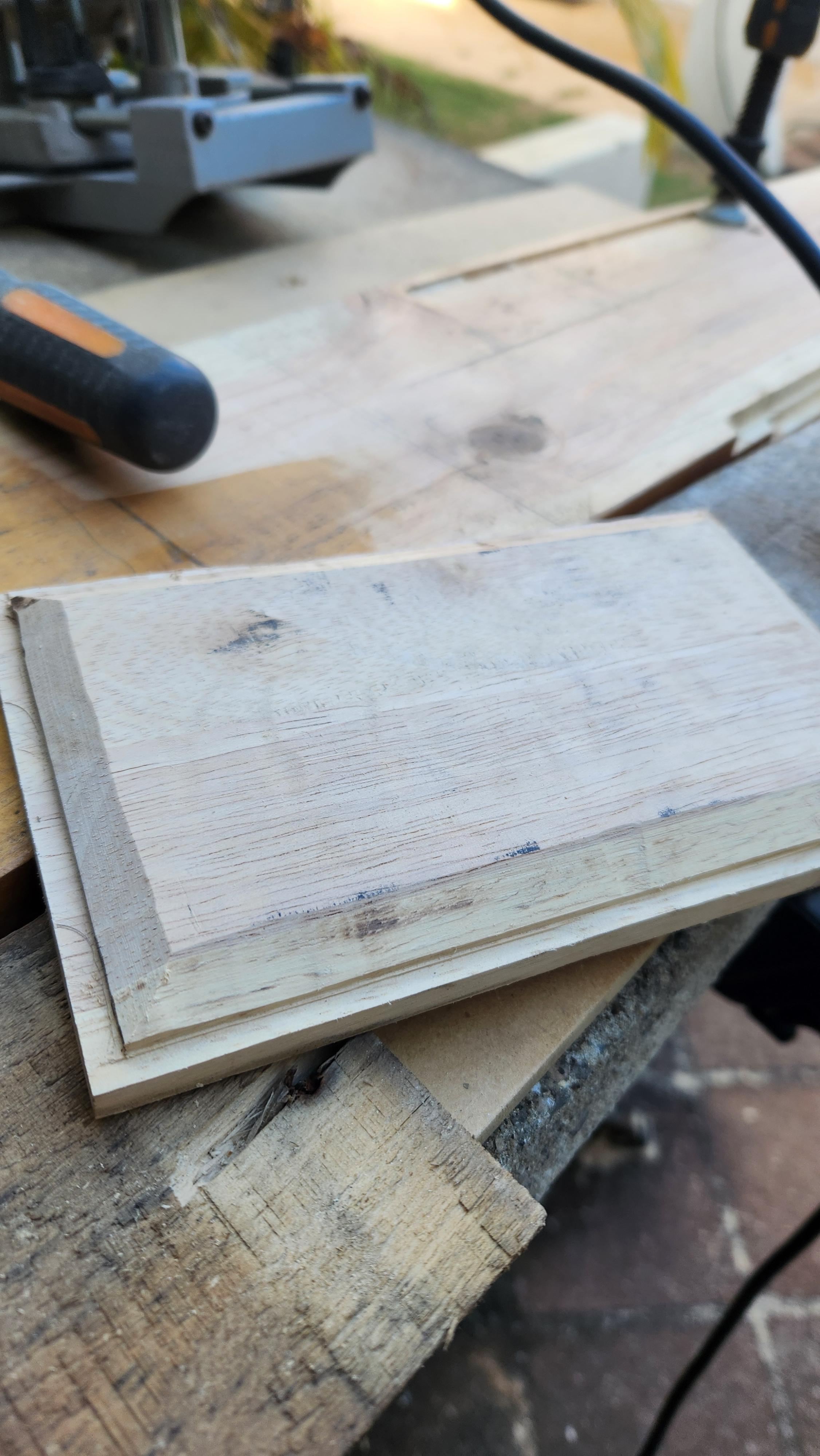


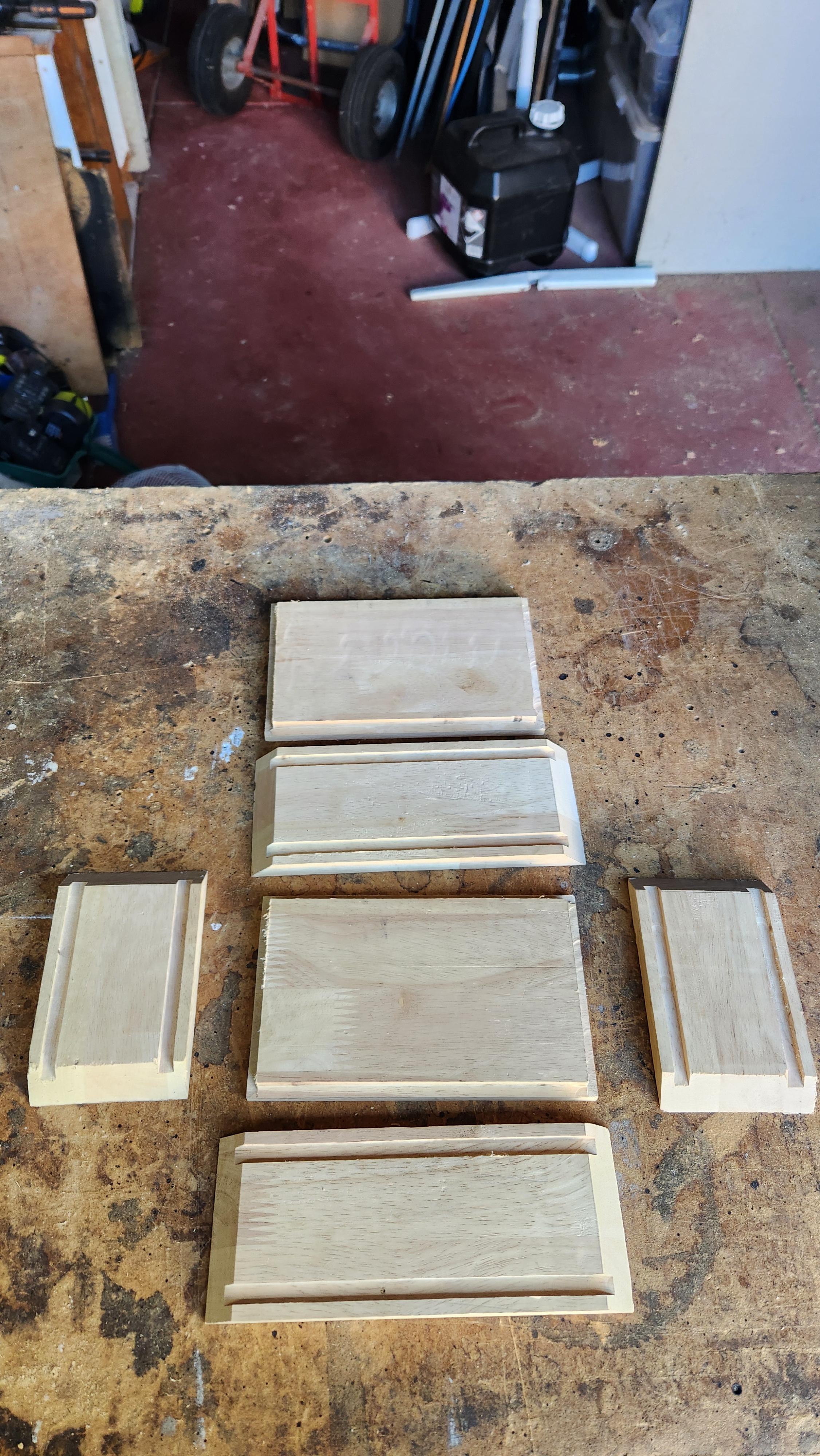


Originally my plan was to have a flat bottom such that everything would sit flush. However, I then later decided I'd rather have a small recess on the bottom (just because I think it looks good). This means that I ended up flipping my base over to leave a deliberate recess in the bottom. If you also want this style, I would recommend planing (or finding a different piece of wood) that is the thickness of your bottom groove so that it doesn't use up extra space within the box. Otherwise, if you want a flush bottom, you can take your original thickness board and route an edge on it as described later in this step.
(See the two base examples. Left: Flush base, Right: Recessed base)
If you are making a flush base you will need to take a straight-cut router bit and route away a rabbet such that the depth of the cheek (not the rabbet as shown in the image below) is just smaller than the width of the groove (around 7.8mm in my case as my groove was 8mm) and with a width just shy of the depth of the groove (so 5.8mm in my case as the depth of my groove was 6mm). By having the width of the rabbet slightly shy of the depth of the groove, it means that if the wood expands with changes in seasons and humidity, it should help prevent any cracking. Make this same rabbet on all 4 edges of both the top and bottom.
Do also note, that you can still use the same base for both flush and recessed (as that is exactly what I did), but you will lose a small amount of space inside if you use the flush base upside down (to make it recessed).
Then on the top only, use a chamfer bit in the router to chamfer all 4 edges as seen in the photos above. This doesn't need to be any exact measurement as it is purely for aesthetics.
(Credit to rockler for the image above)
Sanding




Before you assemble and glue up this box, you need to sand all the faces to their final grit (this is because after the glue up you won't be able to easily access a lot of these faces). For this, I used a combination of a vibratory hand sander and hand sanding with sandpaper stapled to a block of wood. If you are new to woodwork, you should start with the lower grits and work your way up. You can start at around 80-180 and work up until you are happy with the smoothness of the box. I prefer a slightly more "textured" feel so I only went to 240 grit.
Glue Up


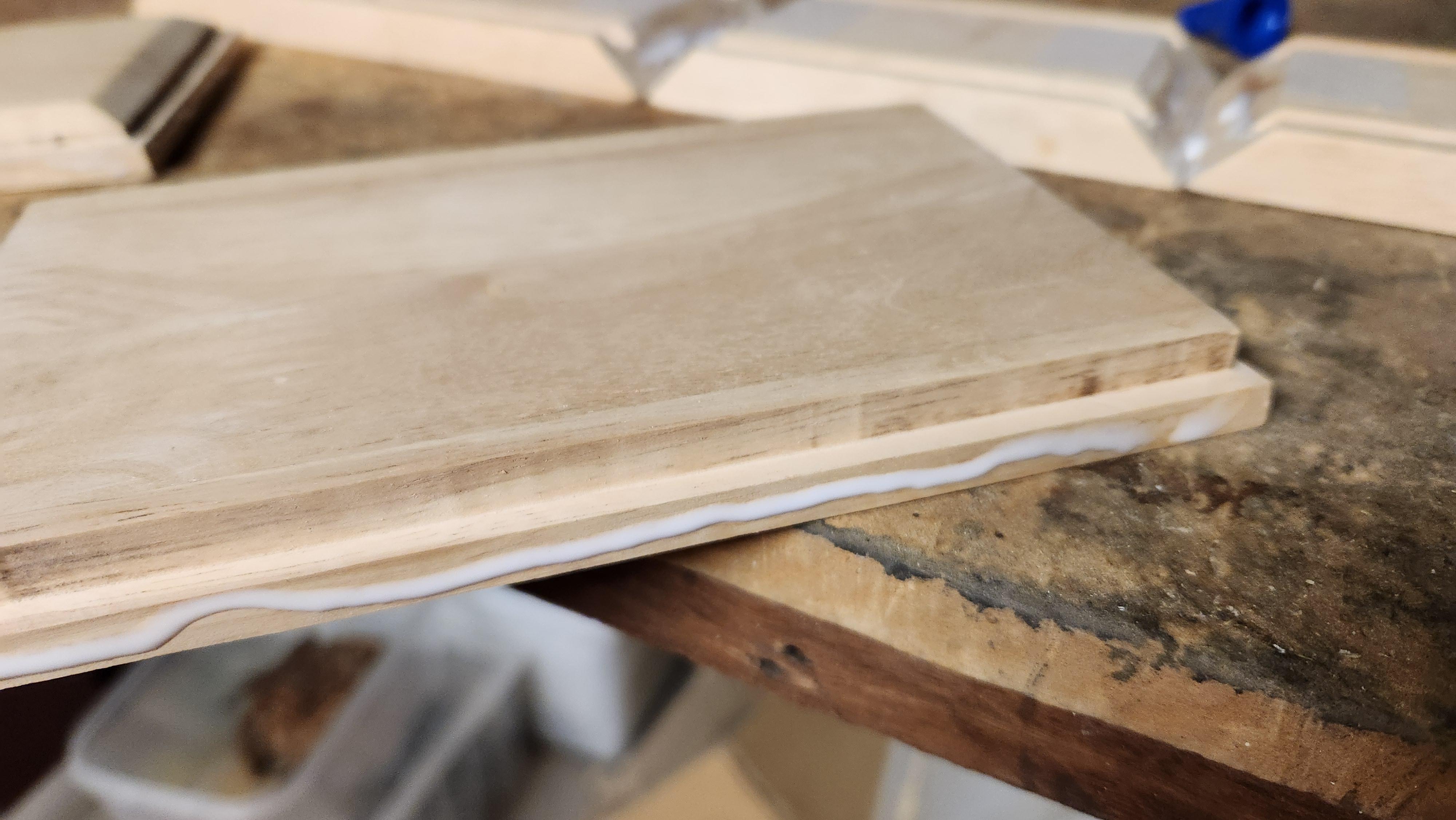




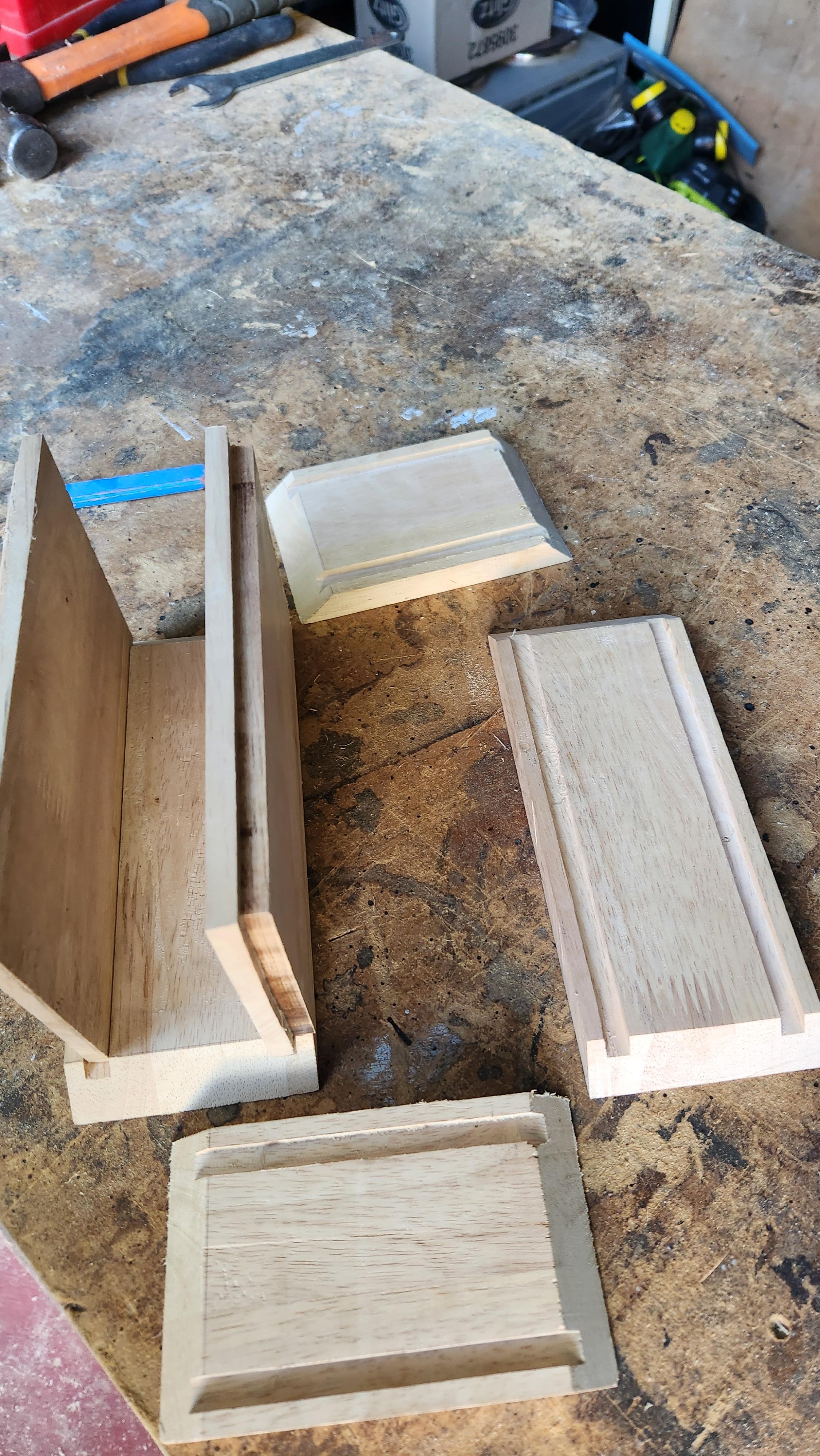





An easy trick to gluing up mitre boxes is to tape all the sides of the edges together in a long chain. Then simply add the glue between the edges and in the grooves before inserting the top and bottom (make sure they are orientated in the correct direction) and folding the edges around. Make sure you do a dry fit first without glue. After gluing up the box, apply clamps to every edge to help bring it all together. Leave it to dry for at least 24 hours (or as long as the glue you are using instructs). I just used a basic wood PVA glue. Try not to add excessive glue to any join as any squeeze-out will be difficult to sand out later.
Cutting Off the Top








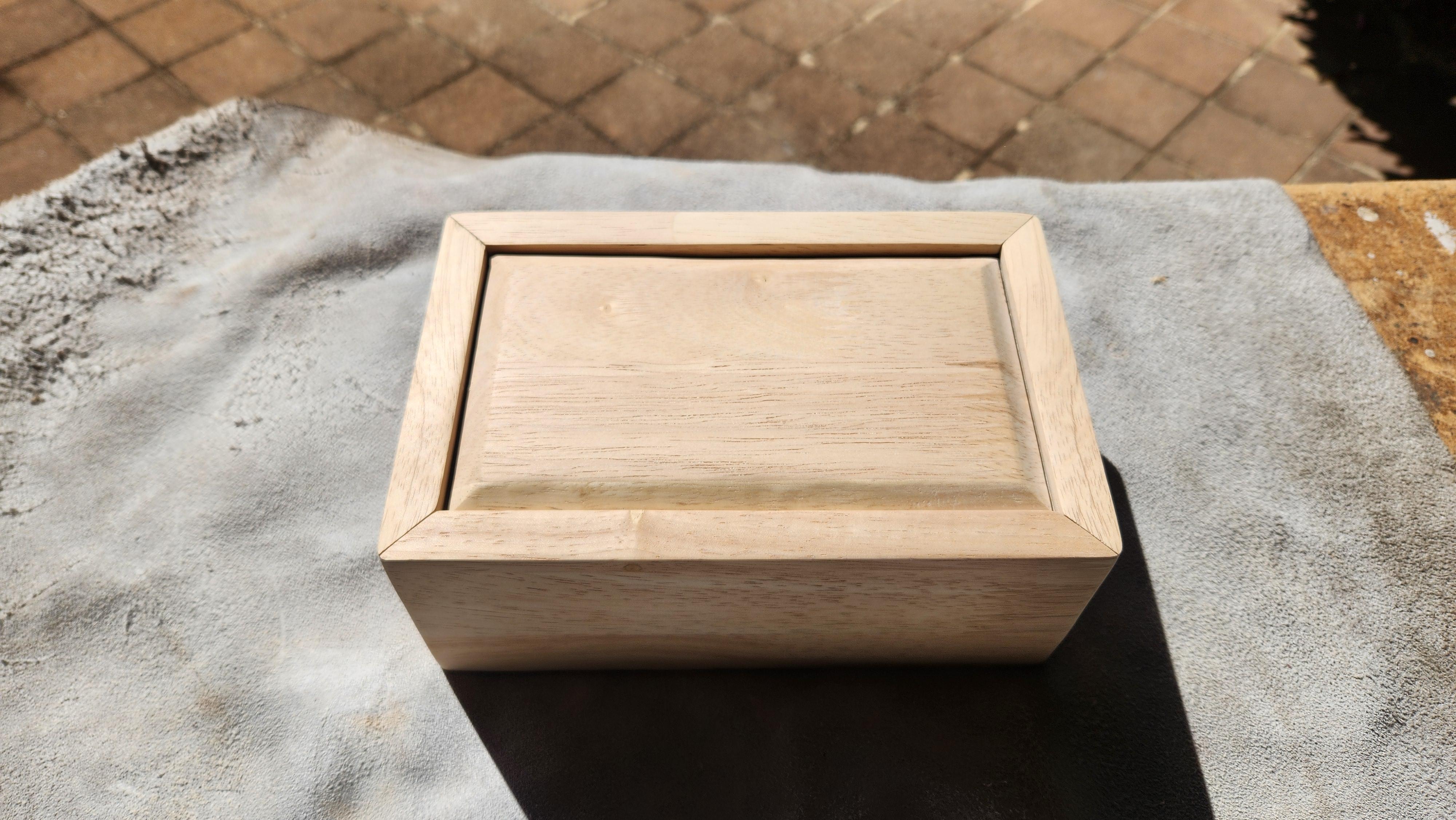










After the glue is dried, we need to cut off the top so that we can actually use the box. You can choose how large you want the lid but I chose 28mm from the top. I have seen people use a table saw to do this, and in my opinion that would yield the best result as all cuts would be straight and of equal width, but if you haven't figured it out by now, I don't have a table saw. So for this, I opted to use a hand saw. If you also choose to cut this by hand, take your time and make very light gentle cuts to prevent chipout. You should use callipers or a scrap block to mark a line around the entire lid such that there is one continuous line around the entire box. Then gently cut, constantly checking your bade is inline and square to the cut. Luckily if you have any slight deviations, it won't matter as the deviation will be the same on the lid and the base, so they will still line up.
Sanding (again)






Now that the lid has been cut off, we want to do the final sand. Make sure to sand out any blade marks on the lid and base's mating face, but if you cut the lid off by hand, do not sand these faces too much as you want them to line up flush (as your cut is likely not perfectly straight). On the contrary, if you have a large belt sander, you could deliberately sand away 1-2mm on both the lid and the base to account for any mistakes when cutting by hand. I also decided to slightly round over each corner as I didn't want a sharp edge. I also rounded over the top and base edges so that the top feels smooth and the base leaves a small shadow line when resting on a flat surface. Similarly, I very very slightly rounded the edges of the lid and base mating face so that they cast a small shadow line on each other.
If you used a nice piece of wood (such as jarrah, oak, walnut etc), I would recommend applying a quick oil finish to help bring out the colours. I made this out of an old tabletop scrap I had lying around, which meant I was using some weird laminate board and when I did a test, I didn't like the oil finish so opted to leave it as is. If you plan to finish your box, you should do it now (unless you plan to brand your box, in which case, complete step 14 first, and then return to this step).
Adding Hinges
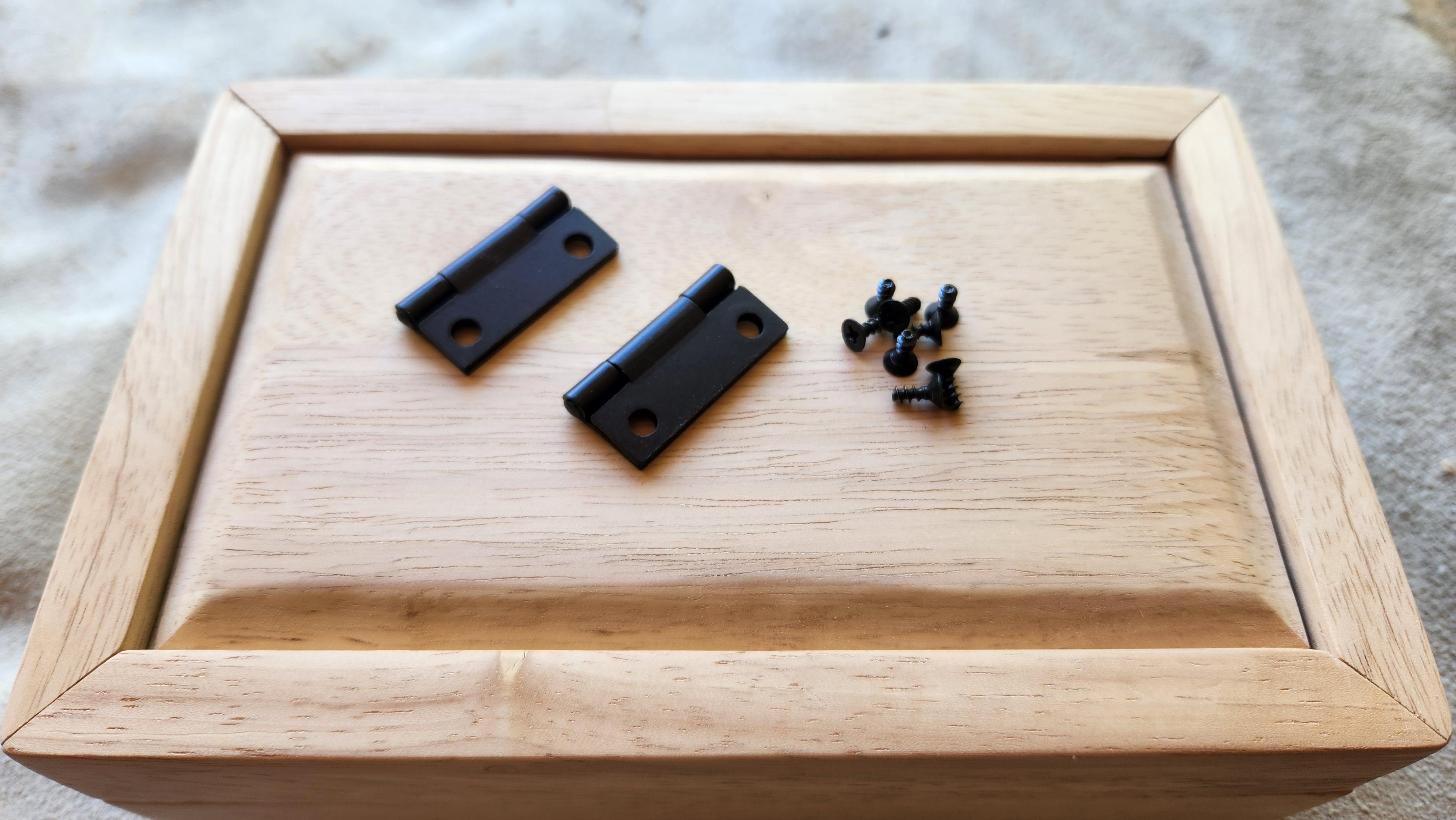






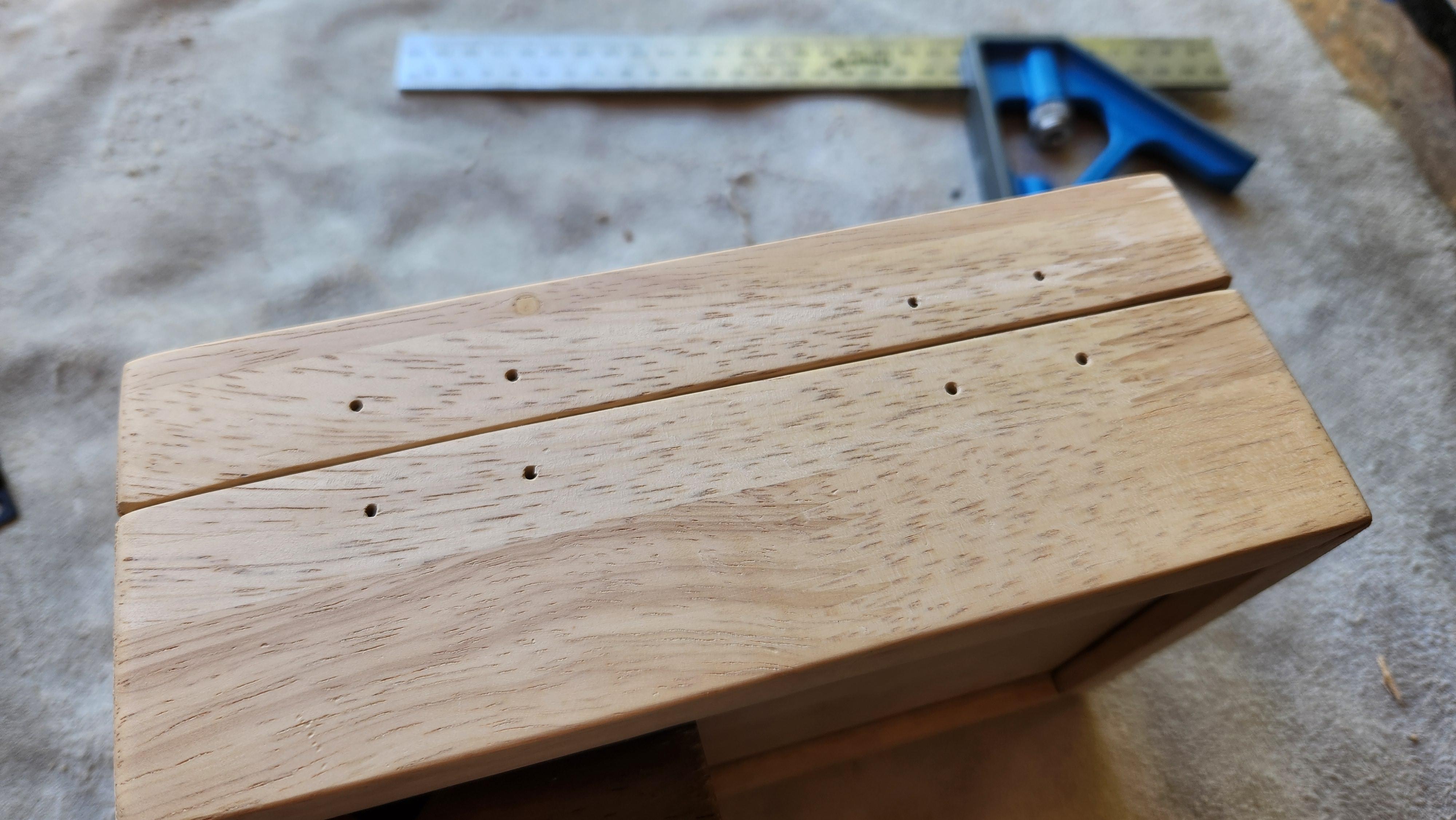





I had bought prime-coat hinges so painted them (and the screws) matt black. After the paint had dried, I lined them up where I wanted them to be on the back of the box. Make sure your hinges are the same distance from their respective outer edge, and that they are lined up with the "seam" between the lid and the base of the box, this will ensure that they will allow the lid to easily open and close. My hinges were brand new, but if you have squeaky hinges, you can add a small amount of oil before adding them to your box. Then drill the piolet holes and screw the hinges in.
And with any luck, you've just made a beautiful wooden box!!
Branding (optional)















Since I was giving this box away as a gift, I wanted to brand it so that it would be more of a personal item. This is an optional touch that you can skip.
Making a branding iron
There is no need to buy some expensive branding iron (unless you want to). For this project, I just took standard fencing wire I had lying around and bent it into a heart shape. You can make any shape you want but try to avoid any with sharp corners. I found it was easier to bend two half-hearts and weld them together as that way I could ensure they were symmetrical. Once you have bent your shape, try to flatten it out as much as possible. Then weld on (or bend) a loop/handle for you to hold the branding iron with.
Branding the box
To brand the box, first mark out (lightly) with a pencil the outline of where you want the box to be branded (which should obviously match the shape of your branding iron). Then holding it with pliers and/or welding gloves, heat it up with a blowtorch or over a gas stove and after around 10-20 seconds, press it firmly into the piece of wood and wobble it slightly so that all sides get pressed in equally. I would recommend practising a few times on a scrap piece of wood. If you find that it wasn't hot enough, or that you missed a section, simply re-heat the iron and press again in that specific location. You do not need to push down hard. Once you have branded it, sand it back slightly to remove any excess charring.
Adding a Hasp and Staple (optional)

Optionally, you could also add a decorative hasp and staple by screwing/nailing one onto the front of your box. I chose not to do this as I liked it without. I stuck one on with sticky tape as shown in the image above just to get a feel as to what it might look like. You could also add any number of other types of clasps and locks.
Wrapping With Ribbon (Optional)


If you are giving this as a gift, you won't want the lid flapping about, so what better to do than wrap a ribbon around it! I didn't have a long enough ribbon to both wrap it and tie a traditional bow, so I tied a fork bow (which I learned here) and used a small drop of super glue to glue it onto the ribbon which I then tied around the box with a tightening knot on the underside (which I learned here). The advantage of this is that you can pull the ribbon tighter (or loosen it if you need to take it off) even once it is tied, helping to make it look that extra bit professional!
Final Comments


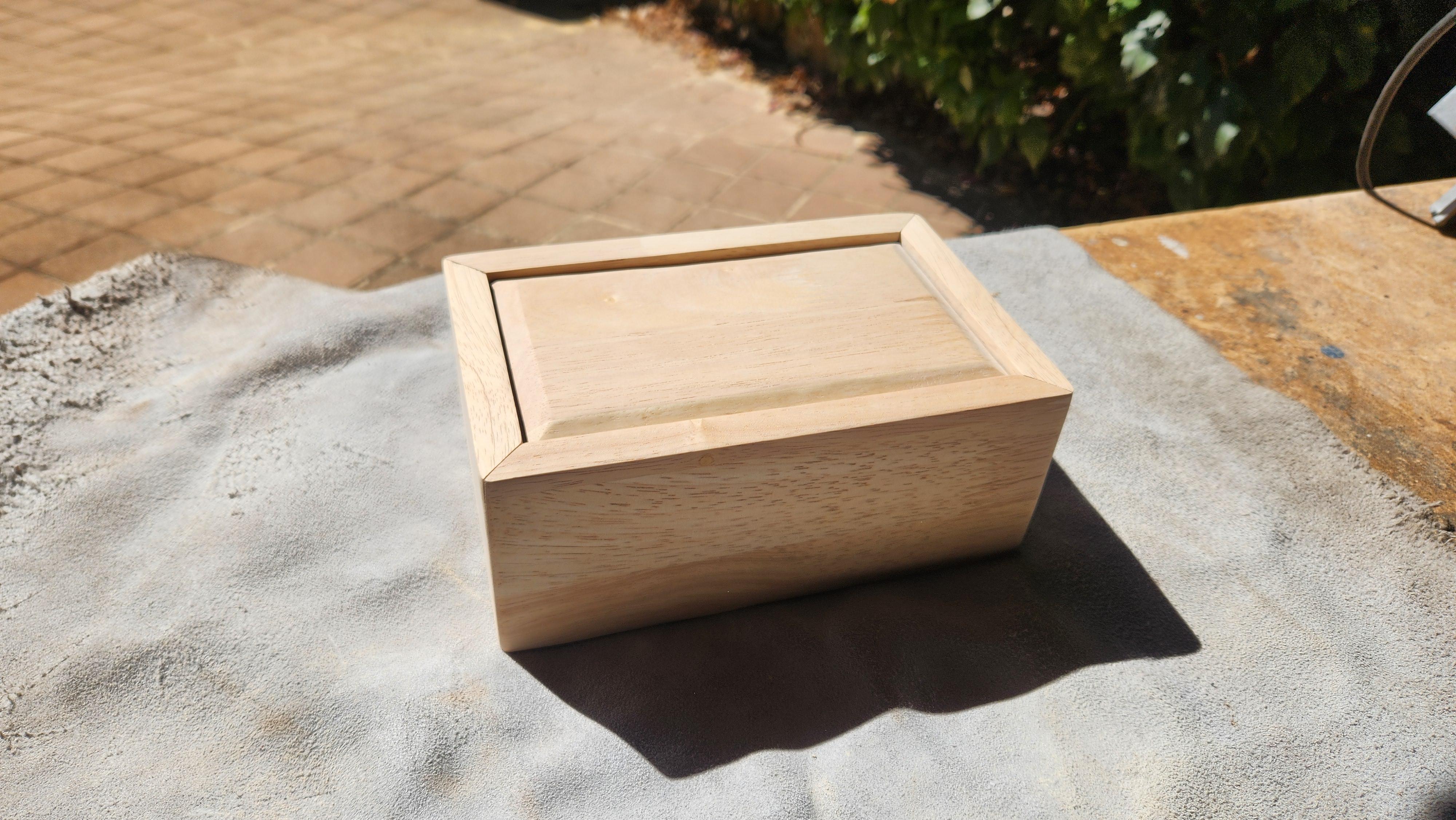



I love how this project turned out, and remember any imperfections are just features :)
If you made it this far, it is a sign that it is time for you to tackle a woodworking side quest this weekend! All the best and I hope this tutorial was helpful.
Thank you to Range Wookworking for inspiring this project of mine, I just made a slightly less perfect version with much cheaper tools and a bit of my creative touch :)