DIY Hose/Tubing(and Wire) Slicer/Splitter
by redragoon in Workshop > Tools
6141 Views, 8 Favorites, 0 Comments
DIY Hose/Tubing(and Wire) Slicer/Splitter
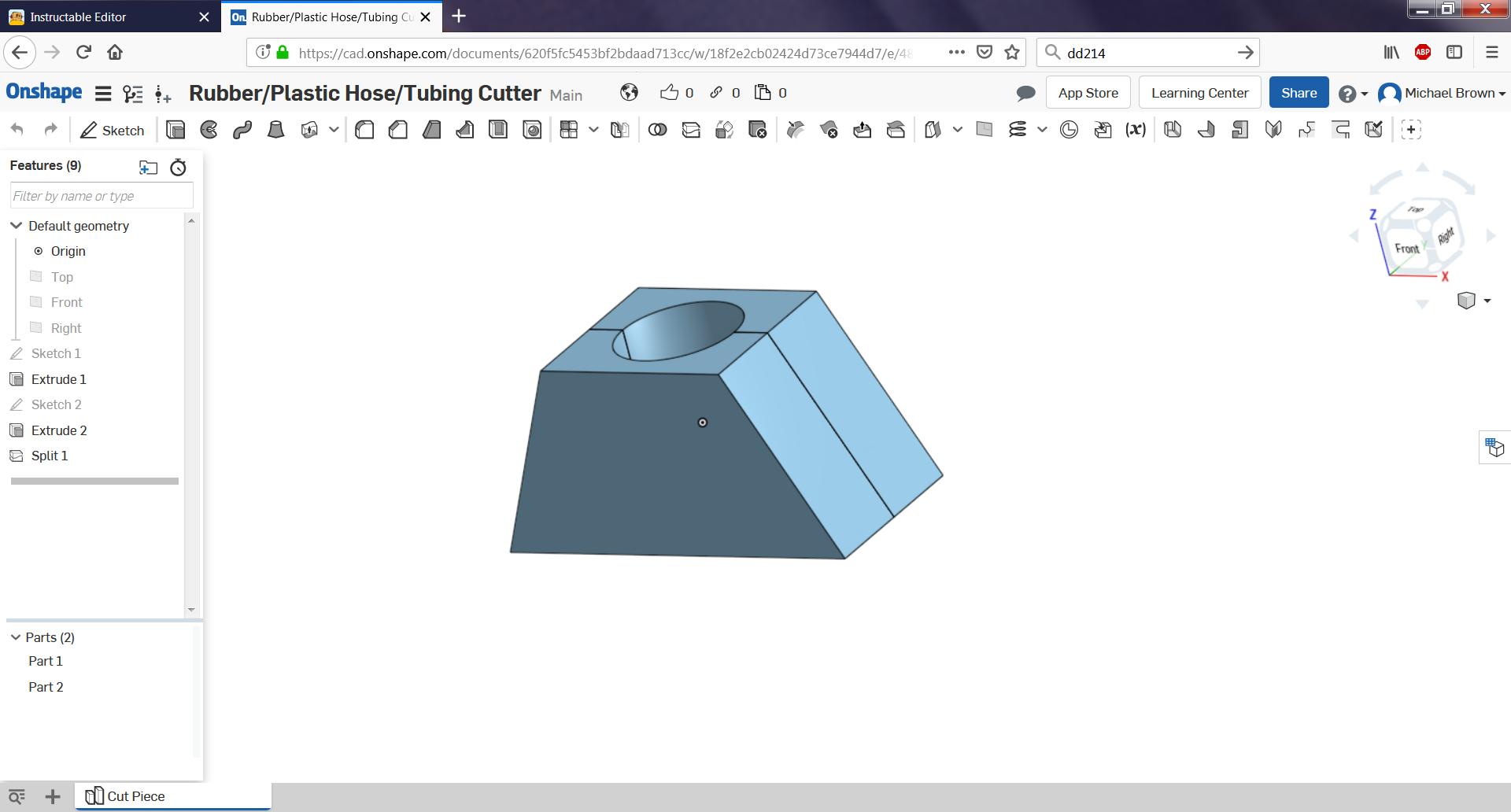

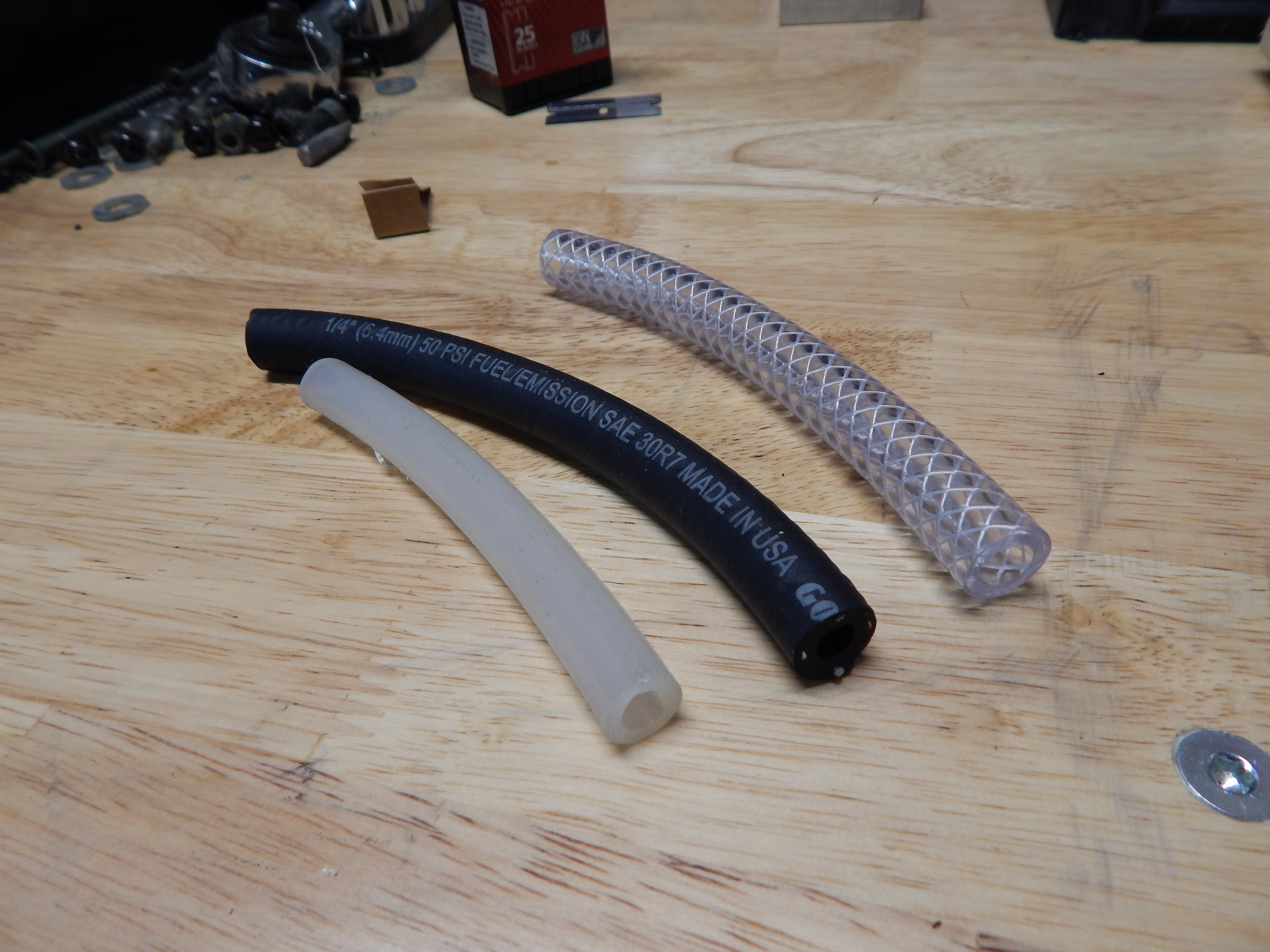
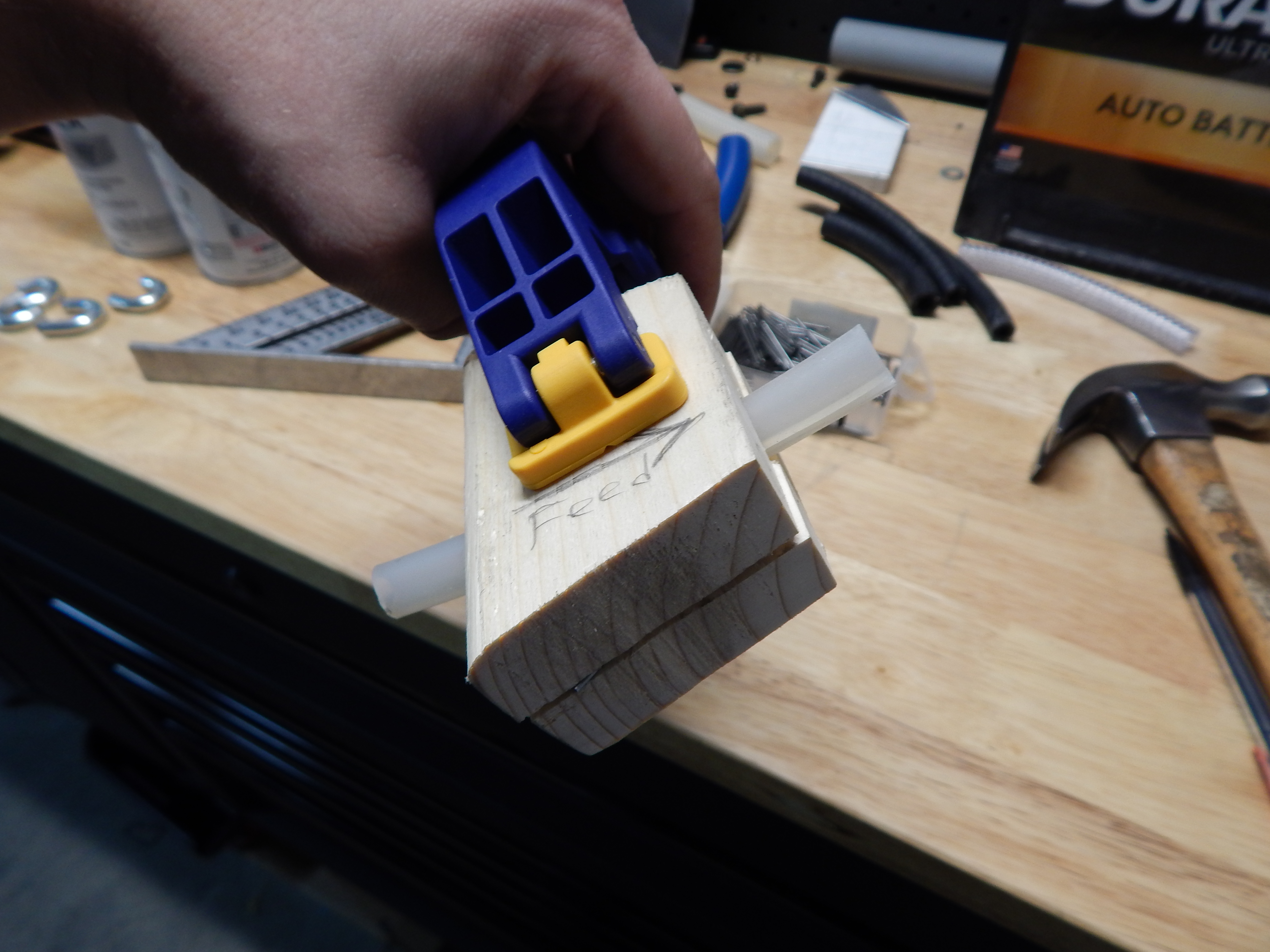
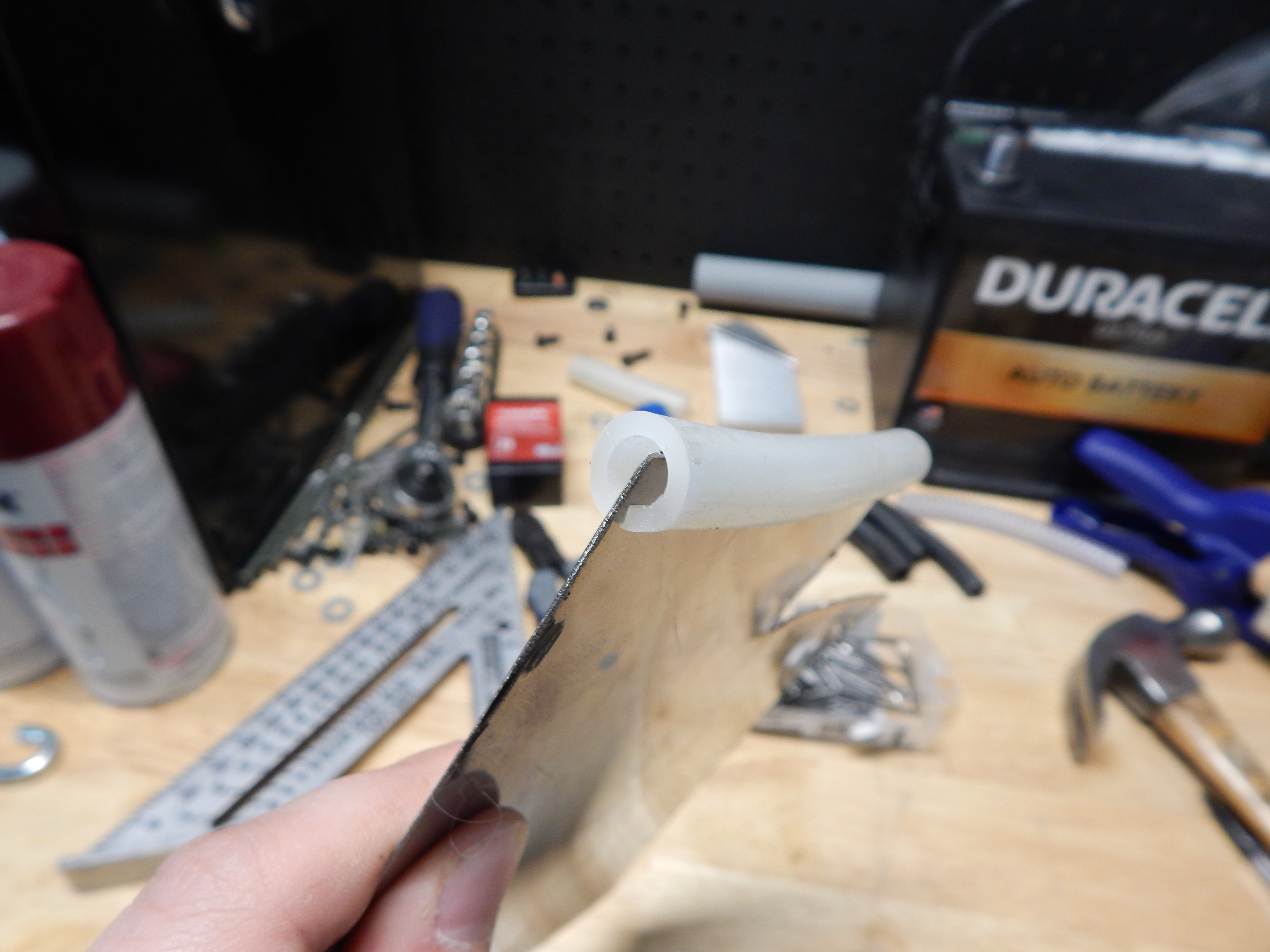
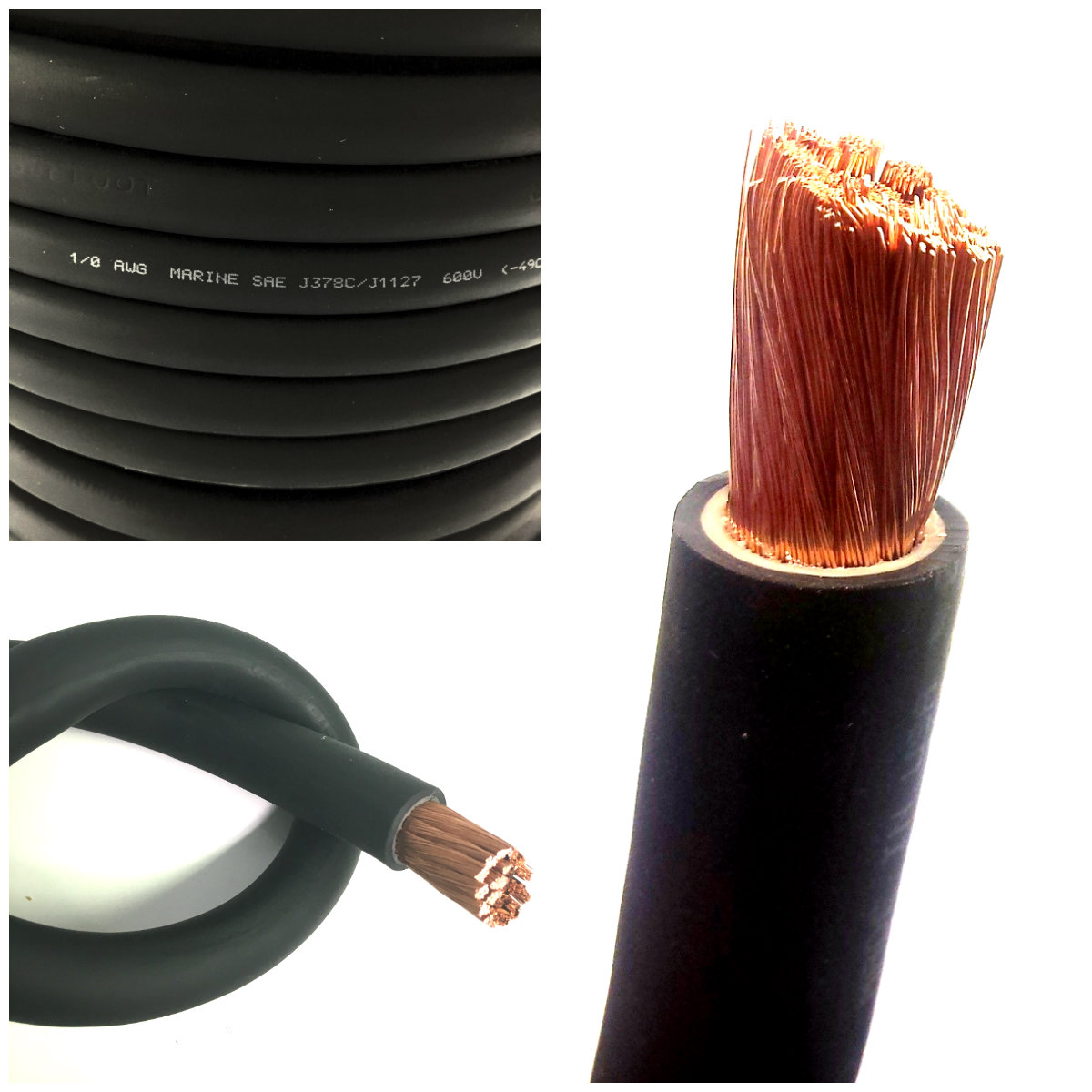
Trying to slice the side of a hose/tube/wire with a razor can be difficult, but this quick DIY tool makes it extremely easy.
I saw a version of this tool on Stacy David's show, Gearz. It was a good idea, but there were no detailed instructions to make it. I made a few changes and listed out the steps needed.
This tool can be used to split tubing/rubber hose to make edge guards or for other needs. It can also slice the tubing/hose into halves to make rubber edging as a bumper or soft stop.
It can also help slice insulation off of wiring/cables which are too big to fit in my wire stripper.
Note: I used SAE measurements since that was convenient. All of this can be converted to the closest metric sizes.
Step 1: Materials and Tools
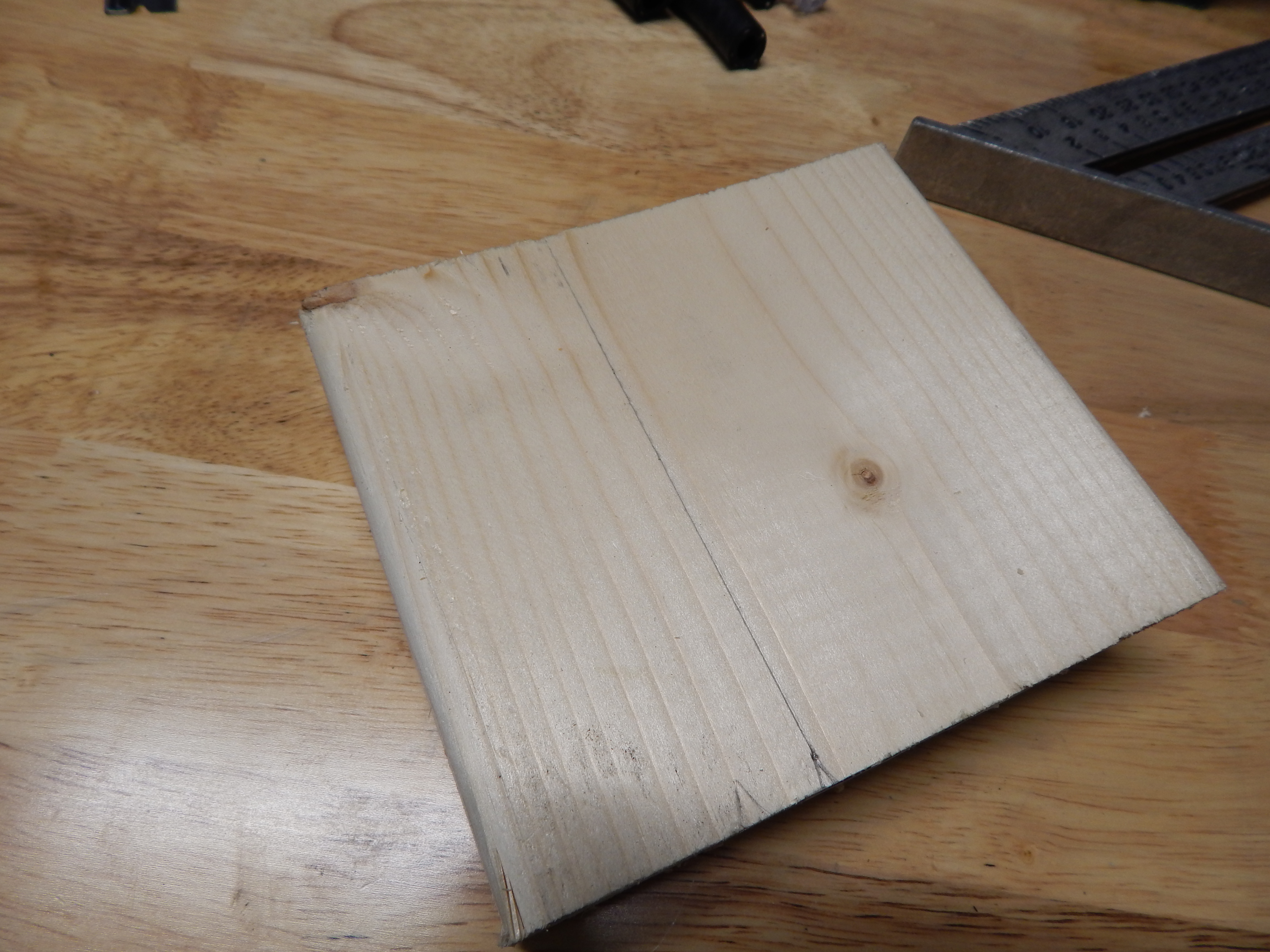
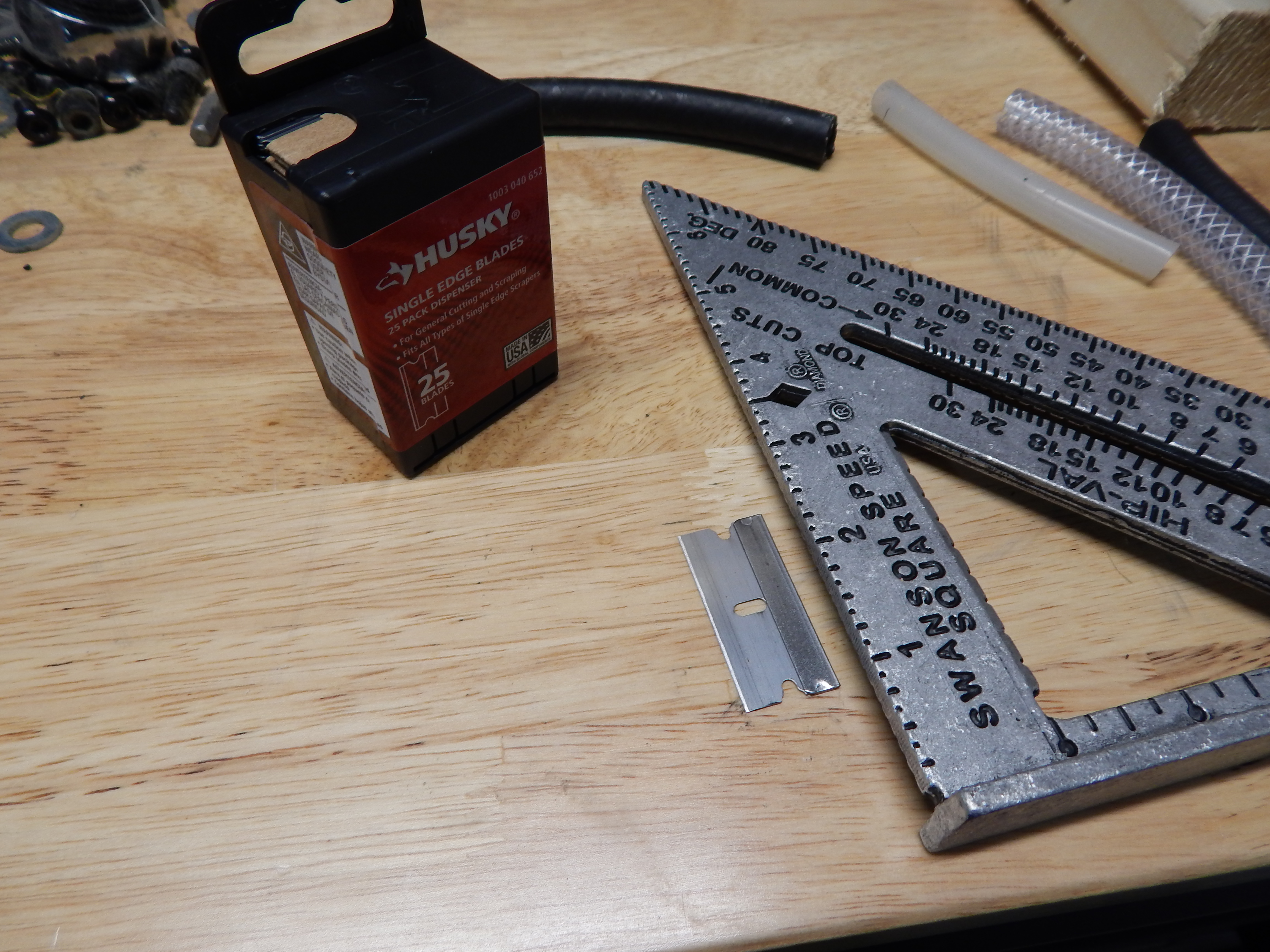
Materials
Block of material - This tool can be wood (I used a scrap cut of 2x6 lumber), metal, plastic, or 3D printed. Total size is approximately 3.0" x 2.0" x 2.0" when finished. This makes it just large enough to cover all of the cutting blade.
Razor Blade - I prefer to use the straight blades for this tool as they are cheaper and smaller. Larger angled ones can be used, but their cutting edge will stick out of a block this size.
Alignment Pins - Not required, but these make it easy to assemble and hold the cutting blade so it doesn't fall to the floor. I used some 1.5" finish nails that I cut in half.
Spring Clamp - I used a spring clamp to hold the pieces together and sandwich the cutting blade. You could also use any other clamp, vise, or other holding device (looking at my piles of zip ties). Just make sure it has enough pressure to keep the pieces together without sliding while cutting. The alignment pins remove the sliding issue entirely, though.
Tools
Layout tools - I used a square and pencil. You could also use a ruler and pen, knife and eyeball measurements. Just whatever you want to make sure the cuts and hole are in the general spot you need.
Saw - This is to cut whatever material you decide to use. Nothing needs to be an accurate cut for this to work so hand tools or power tools will work.
Drill - The hole only needs to be along the center split. Straightness and accuracy beyond that is not needed. I used a drill press to make it easier to increase the hole size until I had the final dimensions, but a hand drill works just as well if you know the final size already.
Drill Bits - Any drill bit, forstner bit, or auger will work for this. You should use a smaller bit to make the starter hole if the final size will be larger than a 1/2" diameter. This wood block can manage up to 1.0" holes until it will probably need a larger base block for anything greater than that. I needed a 5/8 in. hole to fit all of the tubing/hose pieces that I had (1/4" to 5/16" ID sizes).
Hammer - This is to drive the alignment pins into the block. If you don't use them, you don't need a hammer.
Clamps - The clamps listed here is to hold the block to the workbench while cutting and drilling.
Step 2: Basic Design
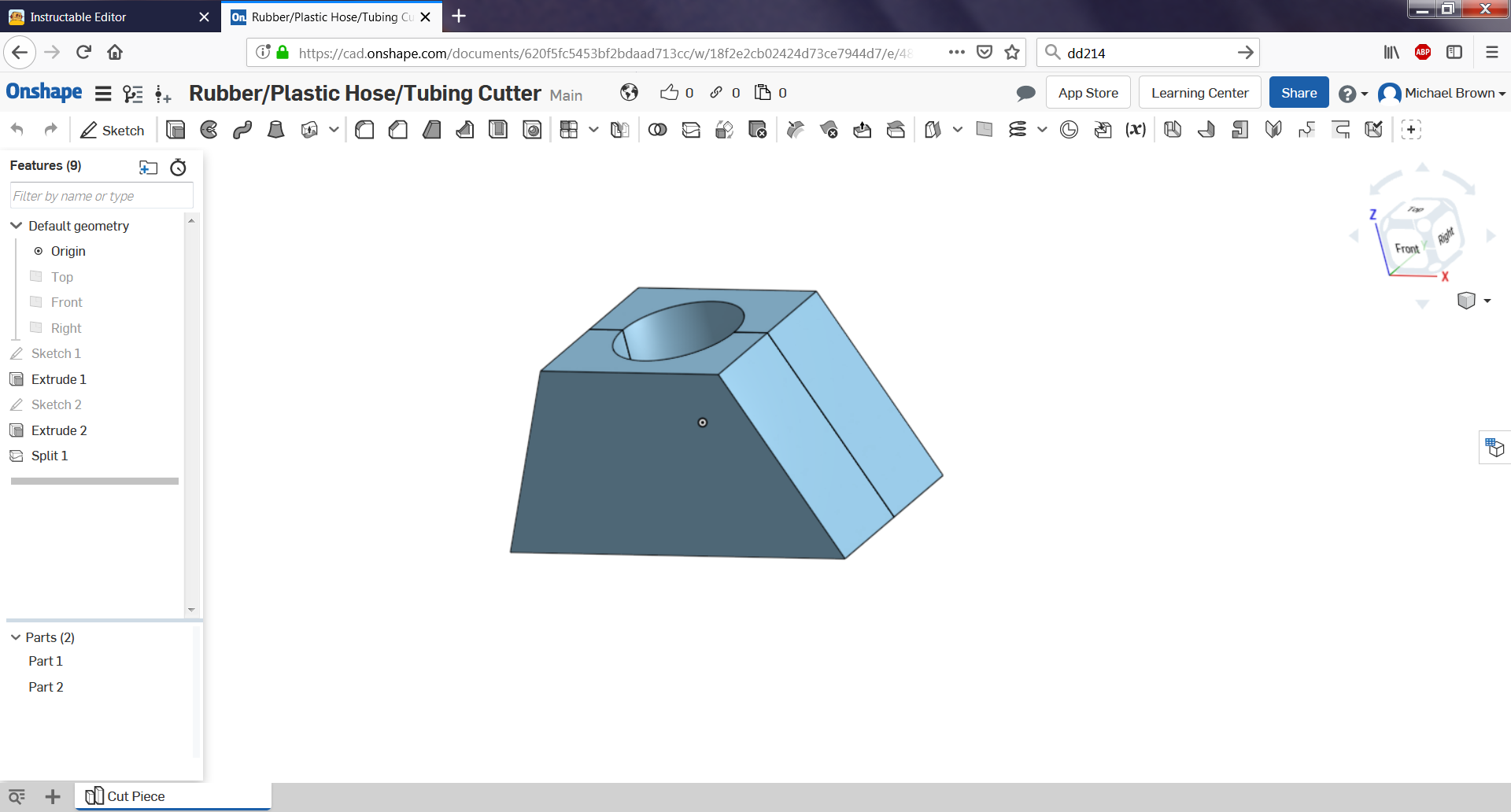
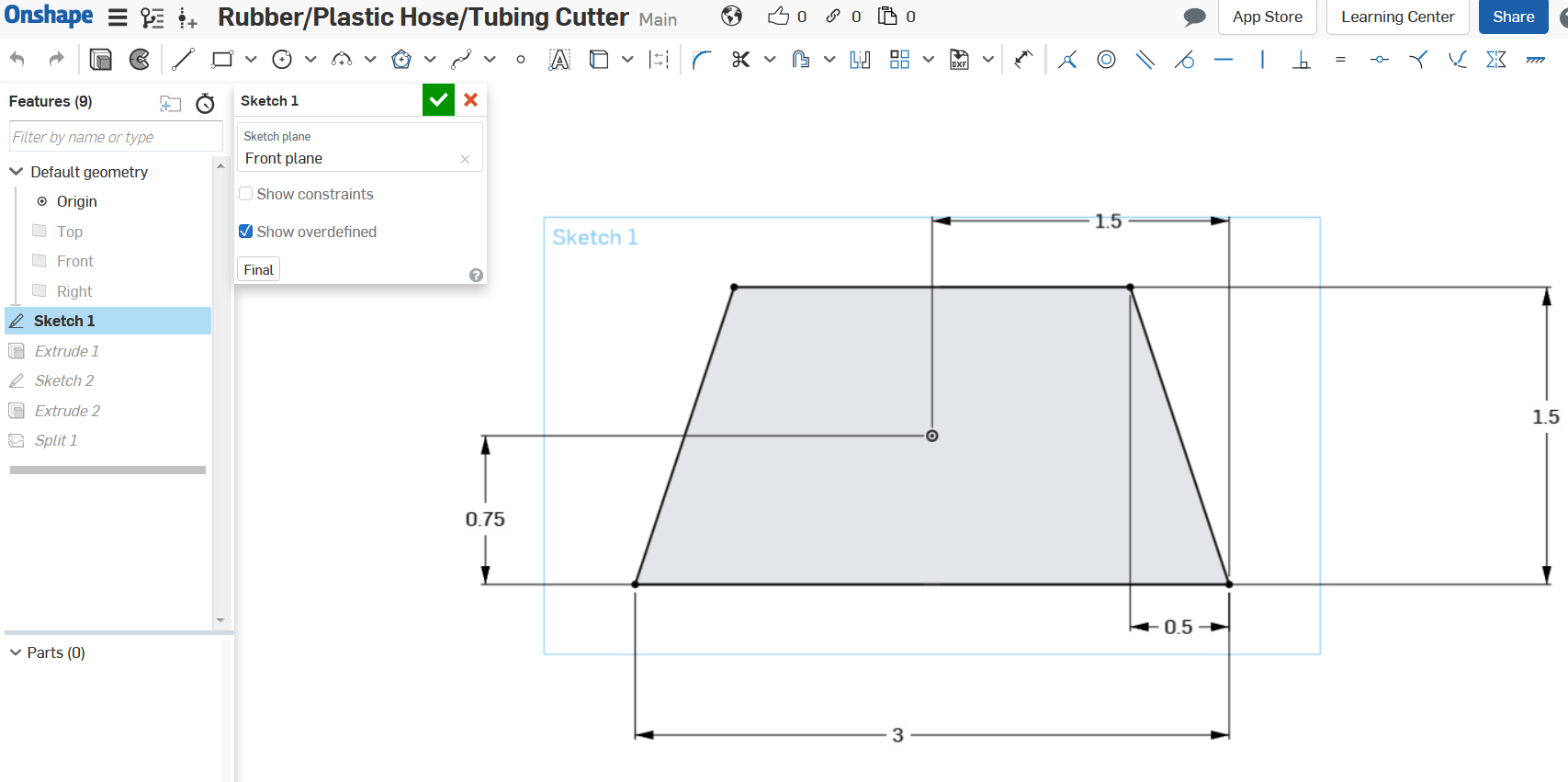
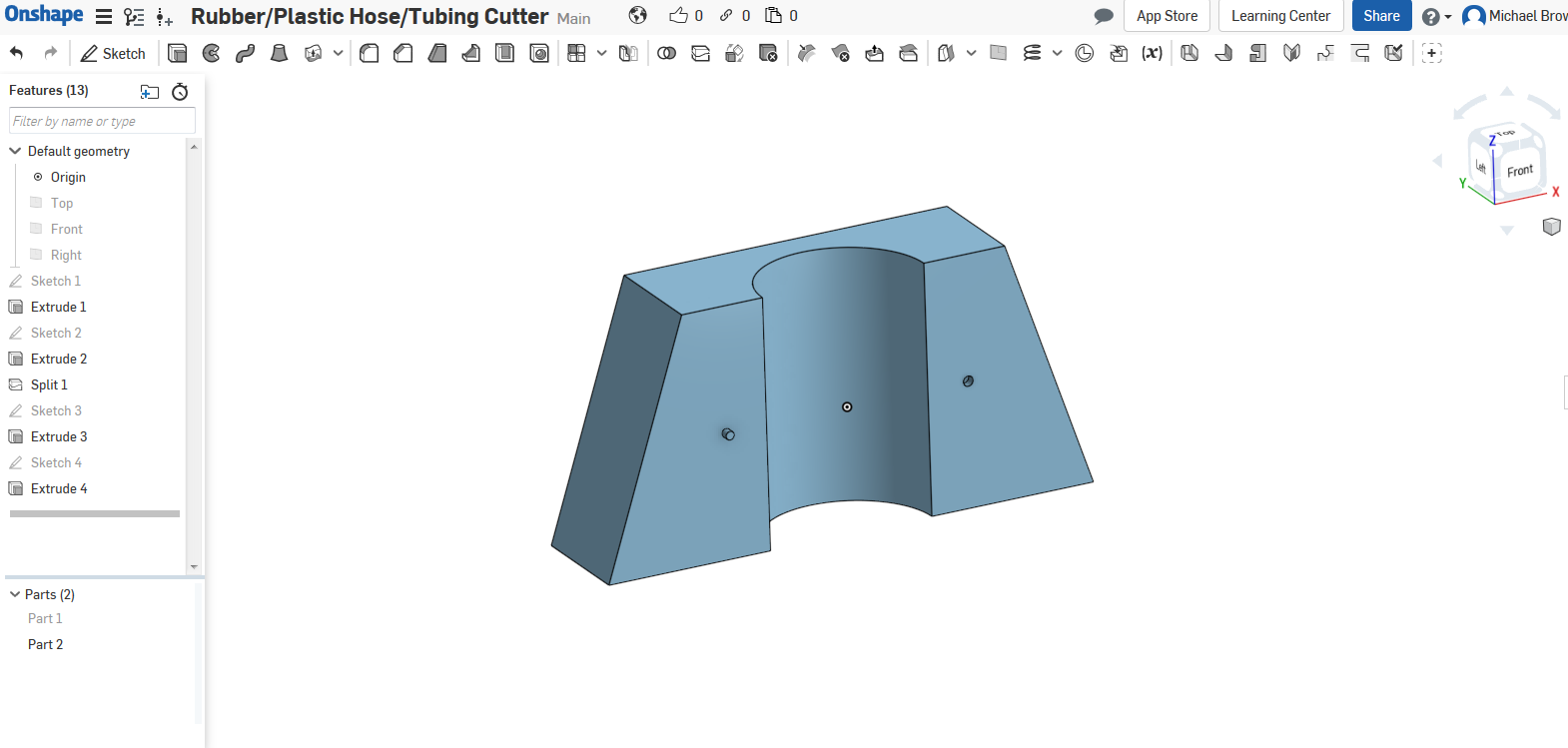
I made the basic shape in a CAD tool called Onshape. This helped me get an idea of how large of a hole I could fit in the material.
If you are going to 3D print this tool, you can remake this design in your preferred software. Make the hole appropriately sized for your tubing/hose and know that the rubber will stick or drag along the sides if it is too tight. The last image shows some built in alignment pins to be printed with the part.
Once you are happy with the design, you just wait for the finished print and skip to step 7.
I don't have a 3D printer, so I had to move on to the old fashioned way.
Step 3: Cutting Block to Size
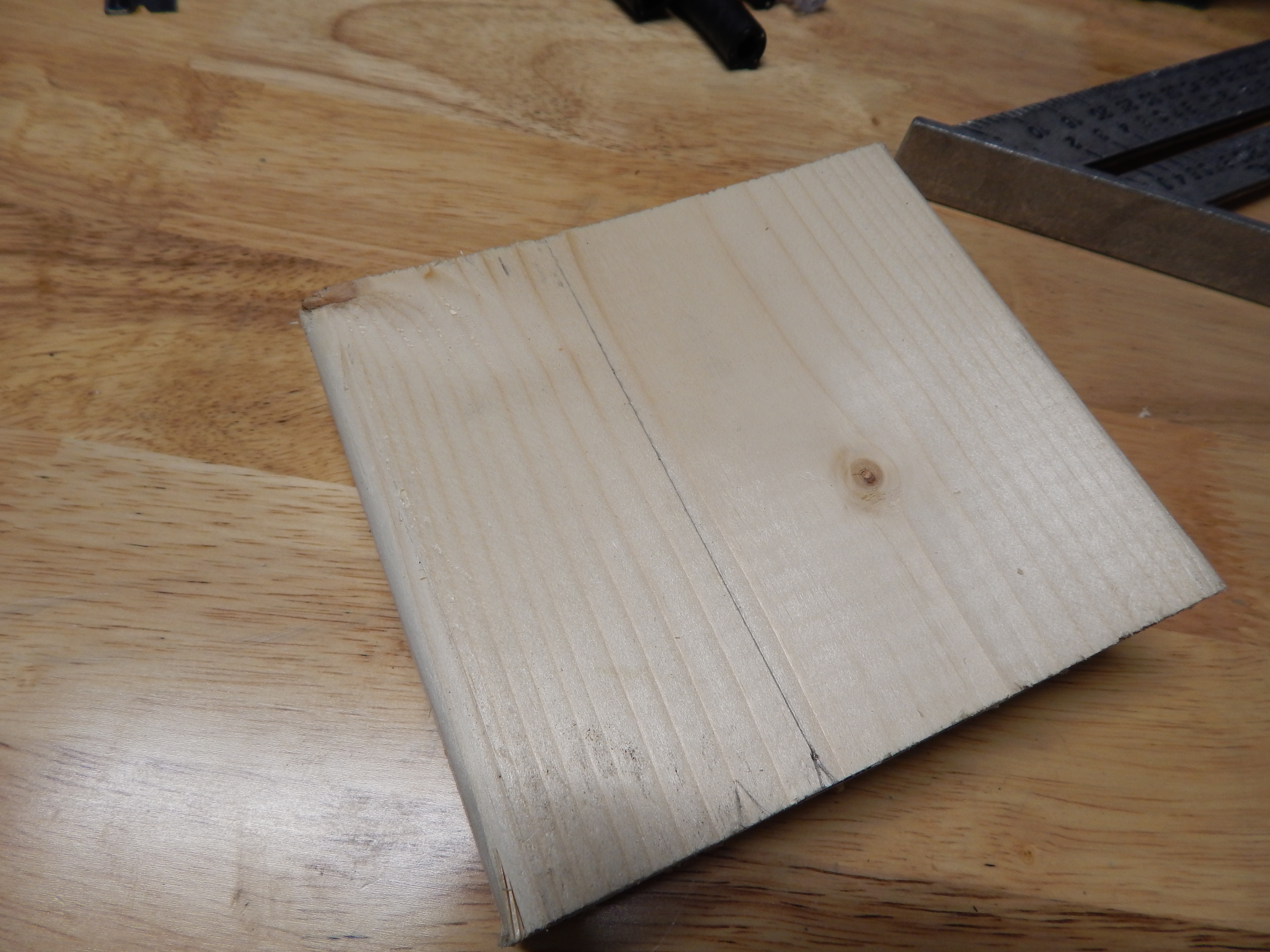
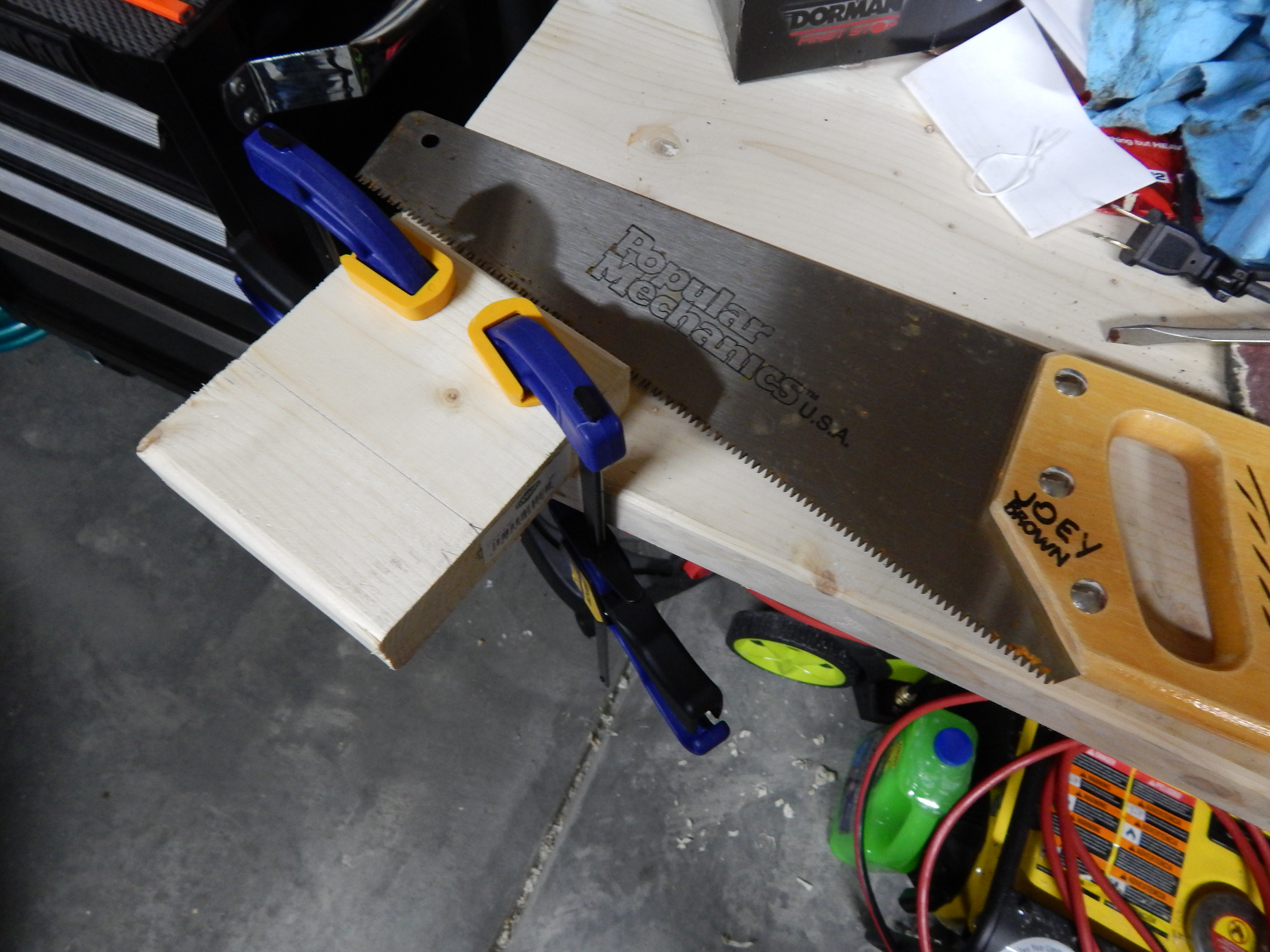
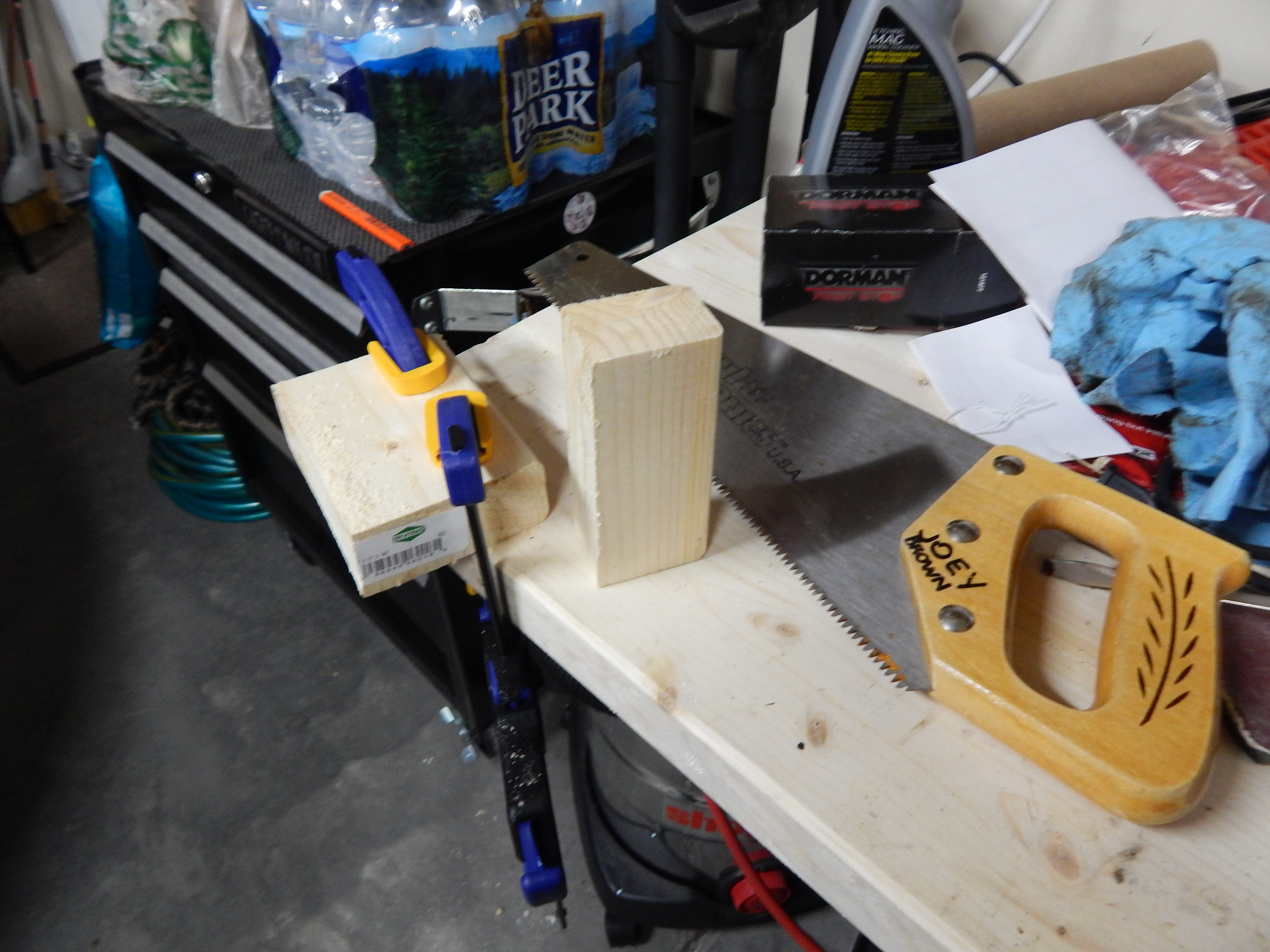
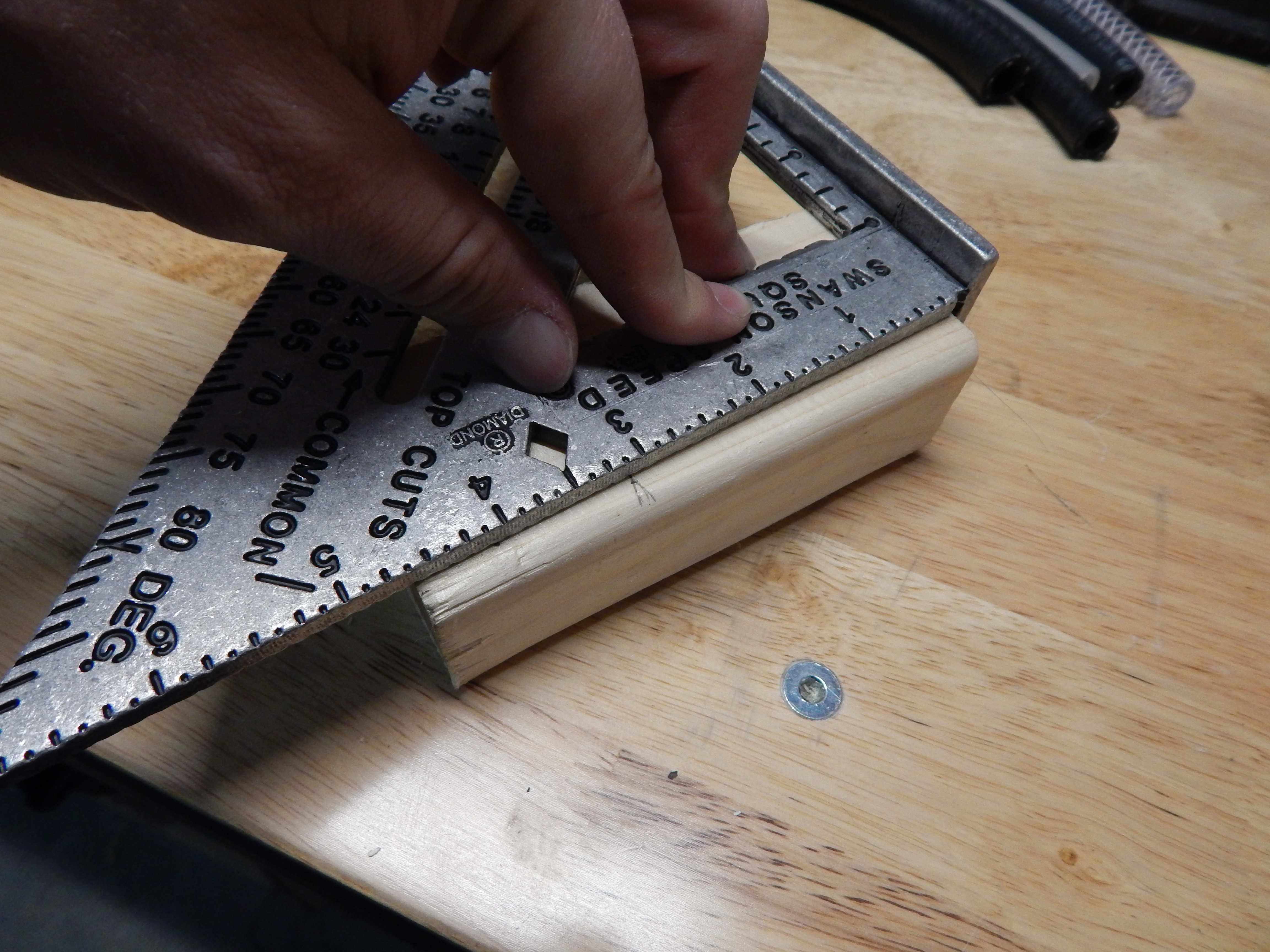
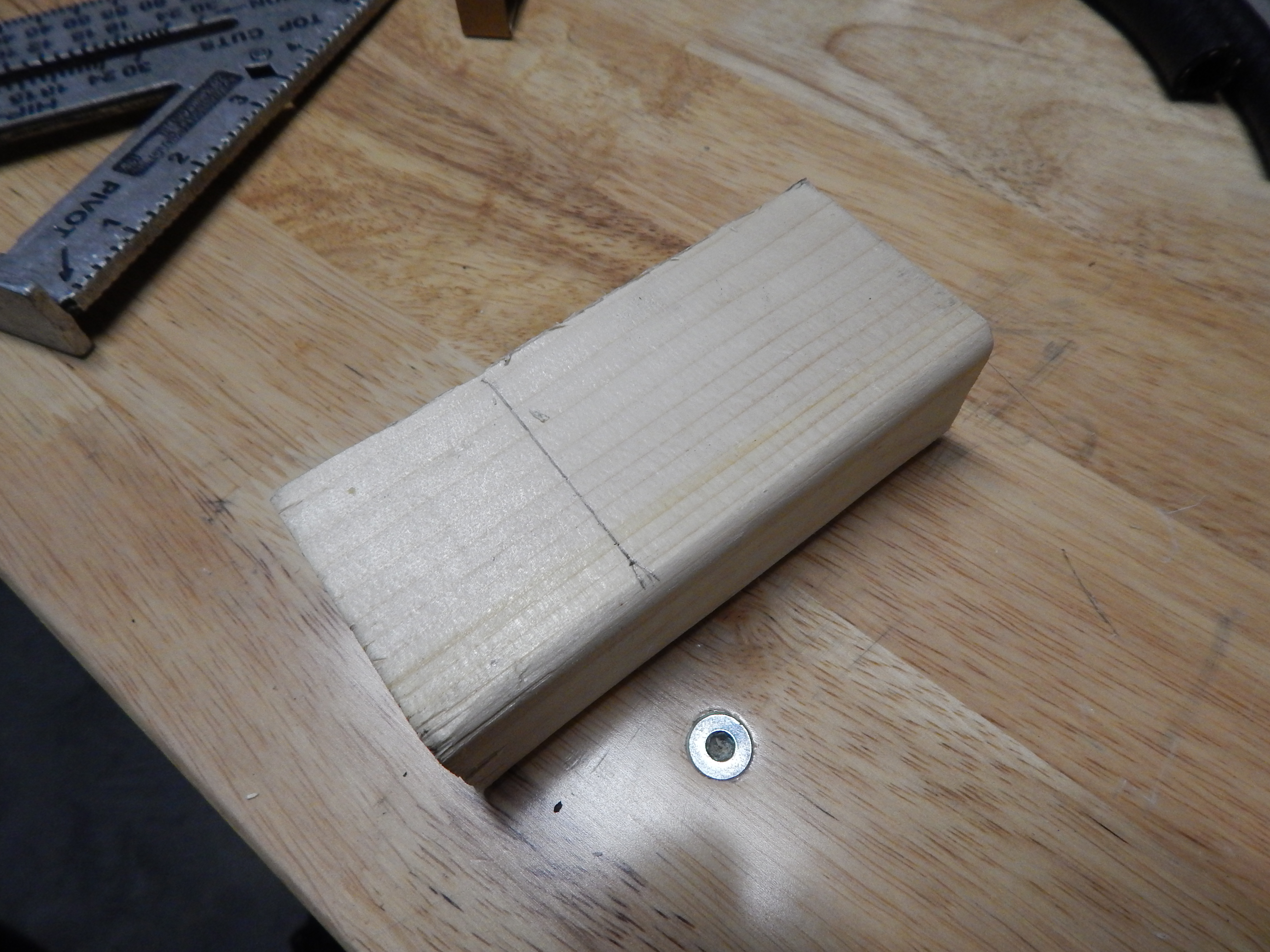
- Make a mark 2.0" from one side. Draw a line using a square to mark the first cut
- Cut it using whatever method you prefer. I clamped it to my workbench and used an old hand saw, because I didn't feel like plugging in a saw.
- Next make a mark at 3.0" from the edge.
Step 4: Angled Cuts
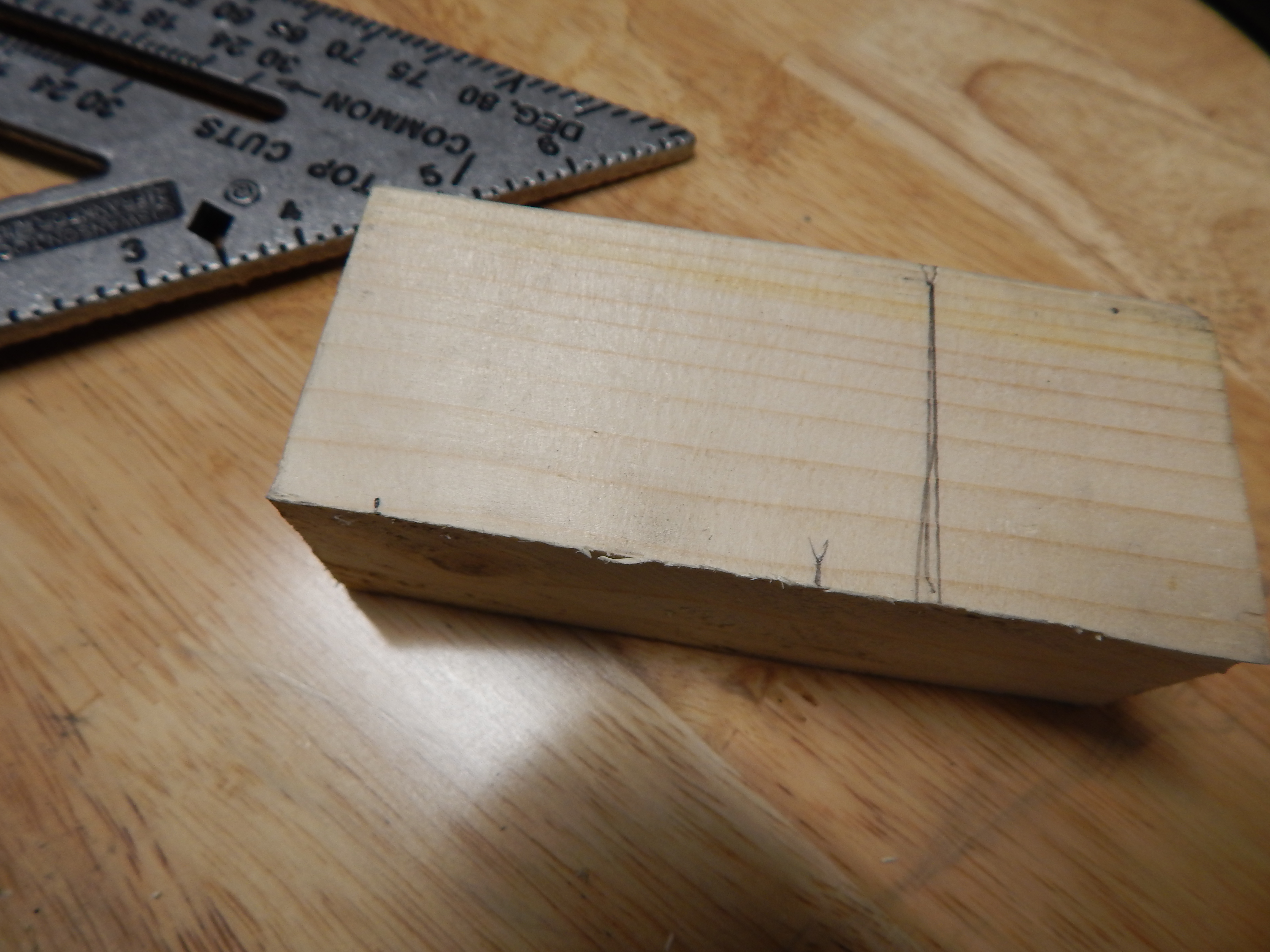
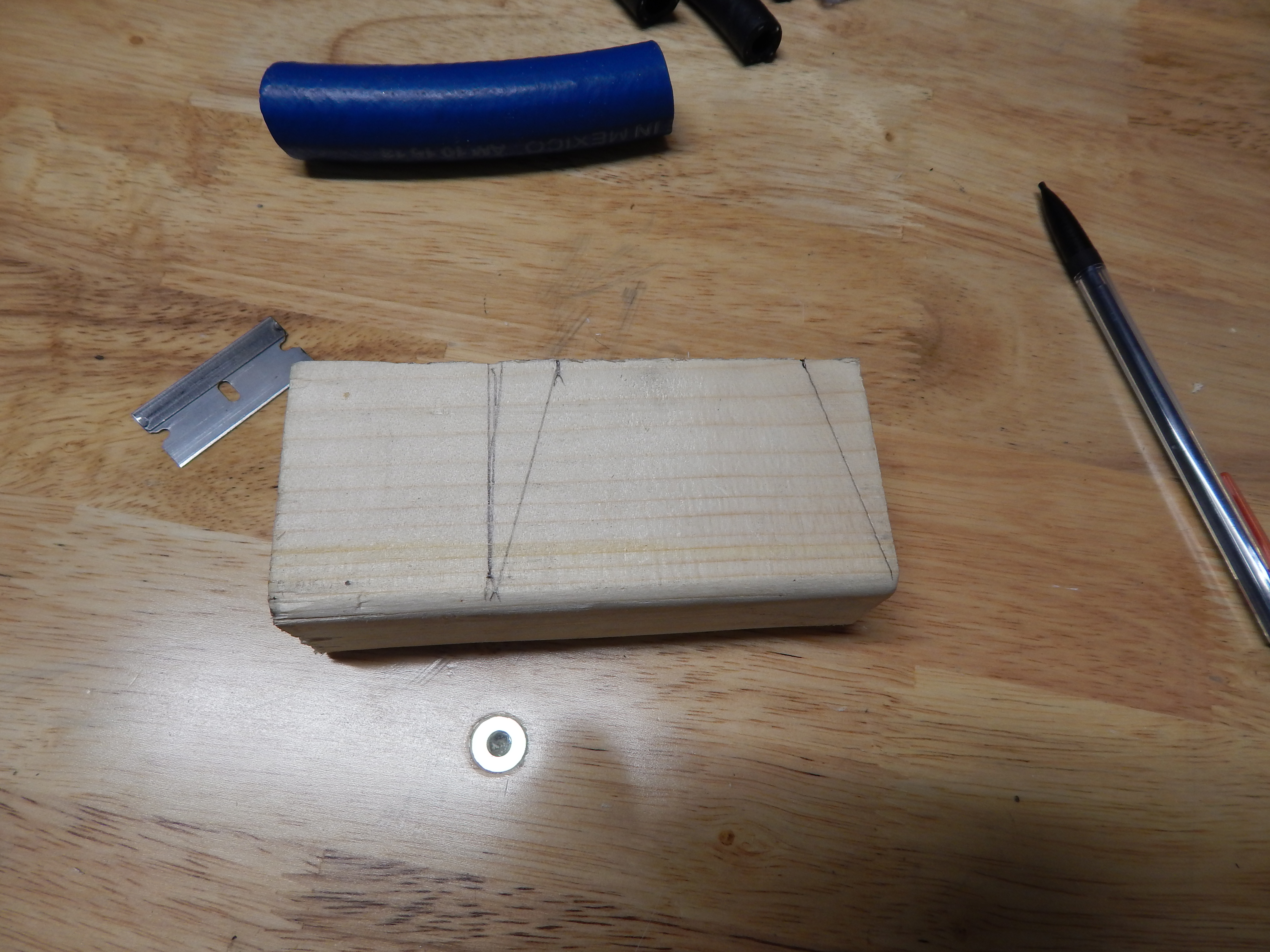
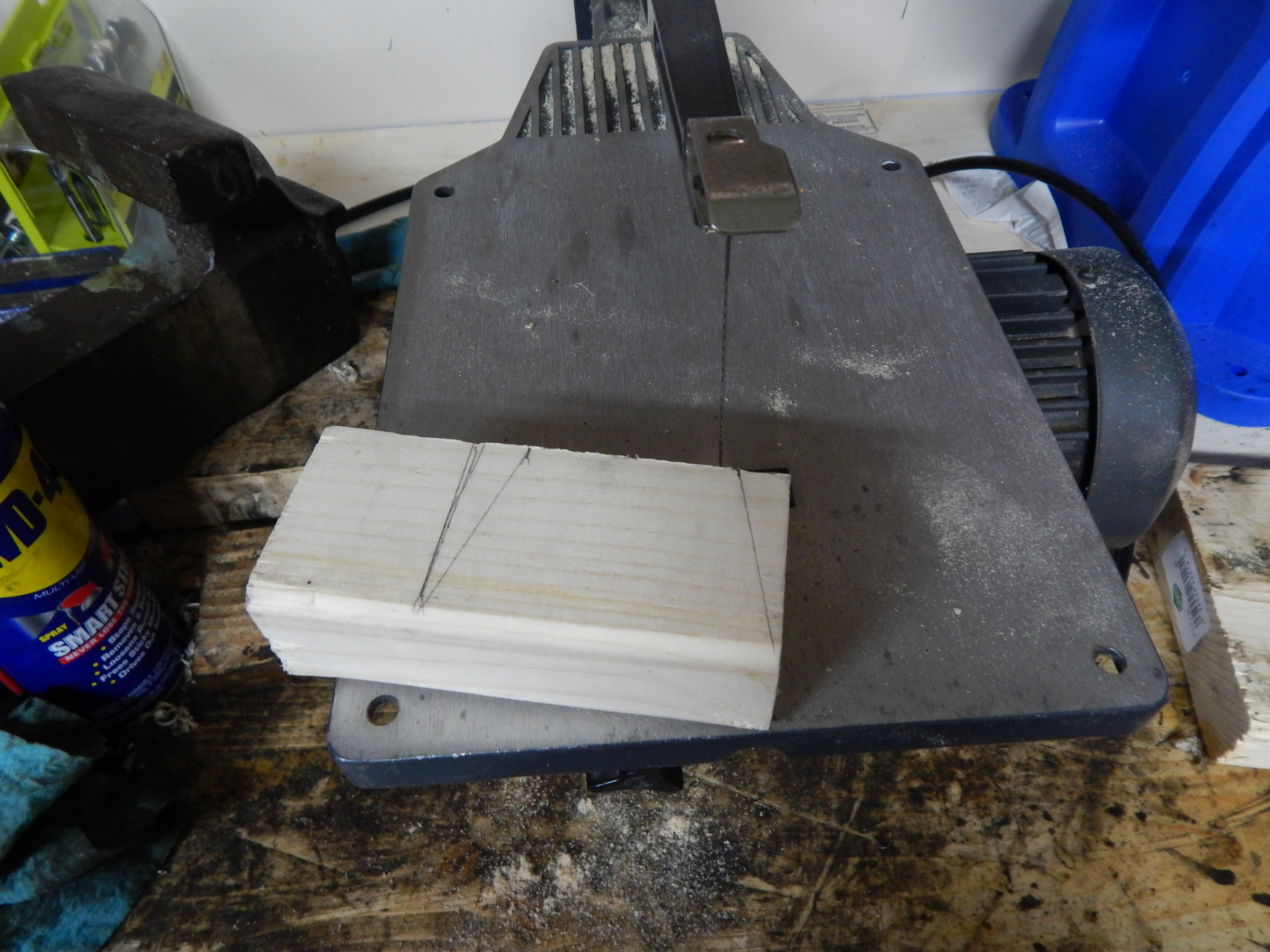
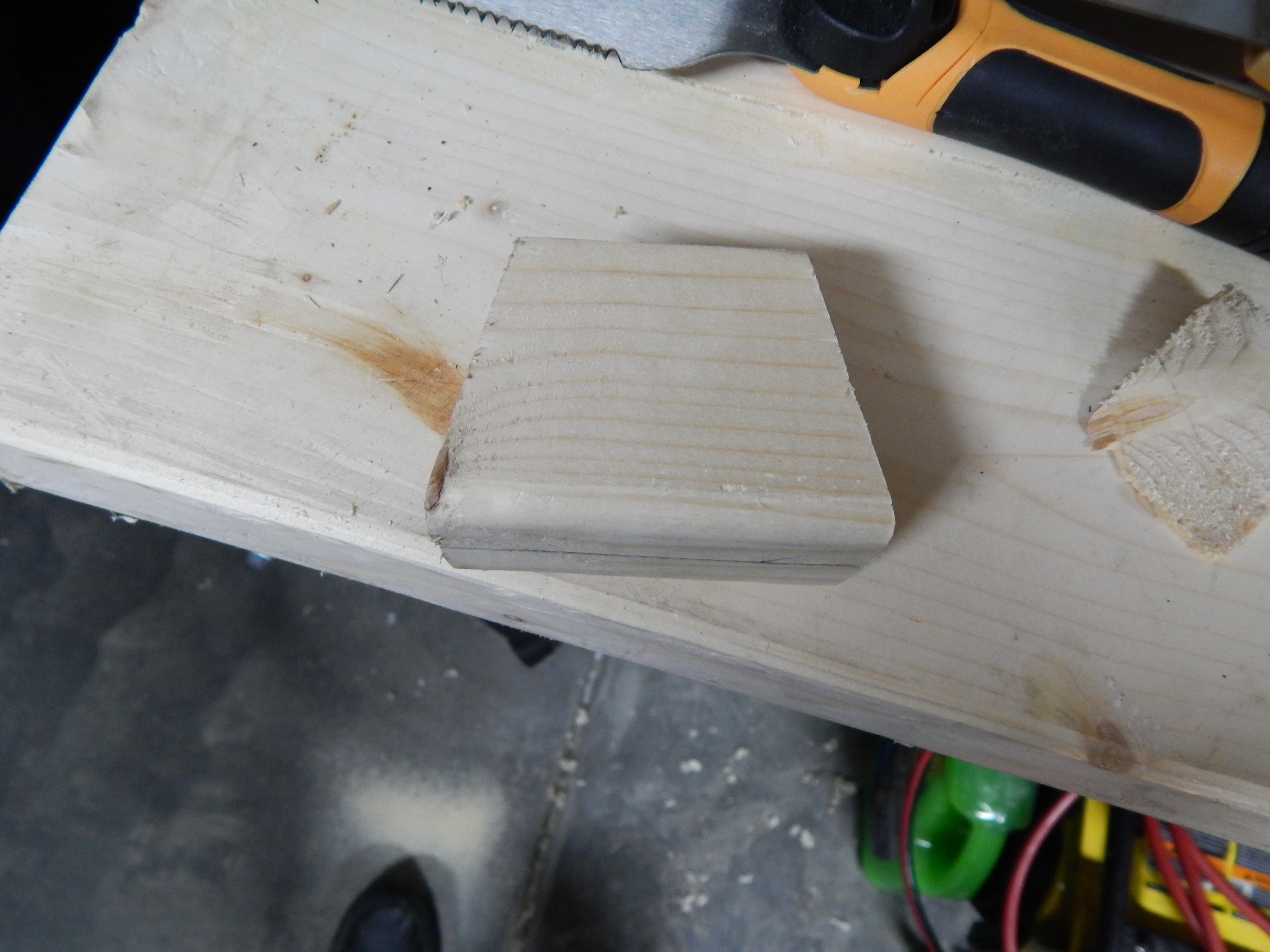
- Make marks 1/2" from the edge and the line you just drew at 3.0"
- Use those marks to make angled lines.
- Cut along those angles using your preferred method. I started with a scroll saw (the only powered saw not in storage) before returning to a hand saw.
- You should now have the shape in the final picture
Step 5: Making the Halves
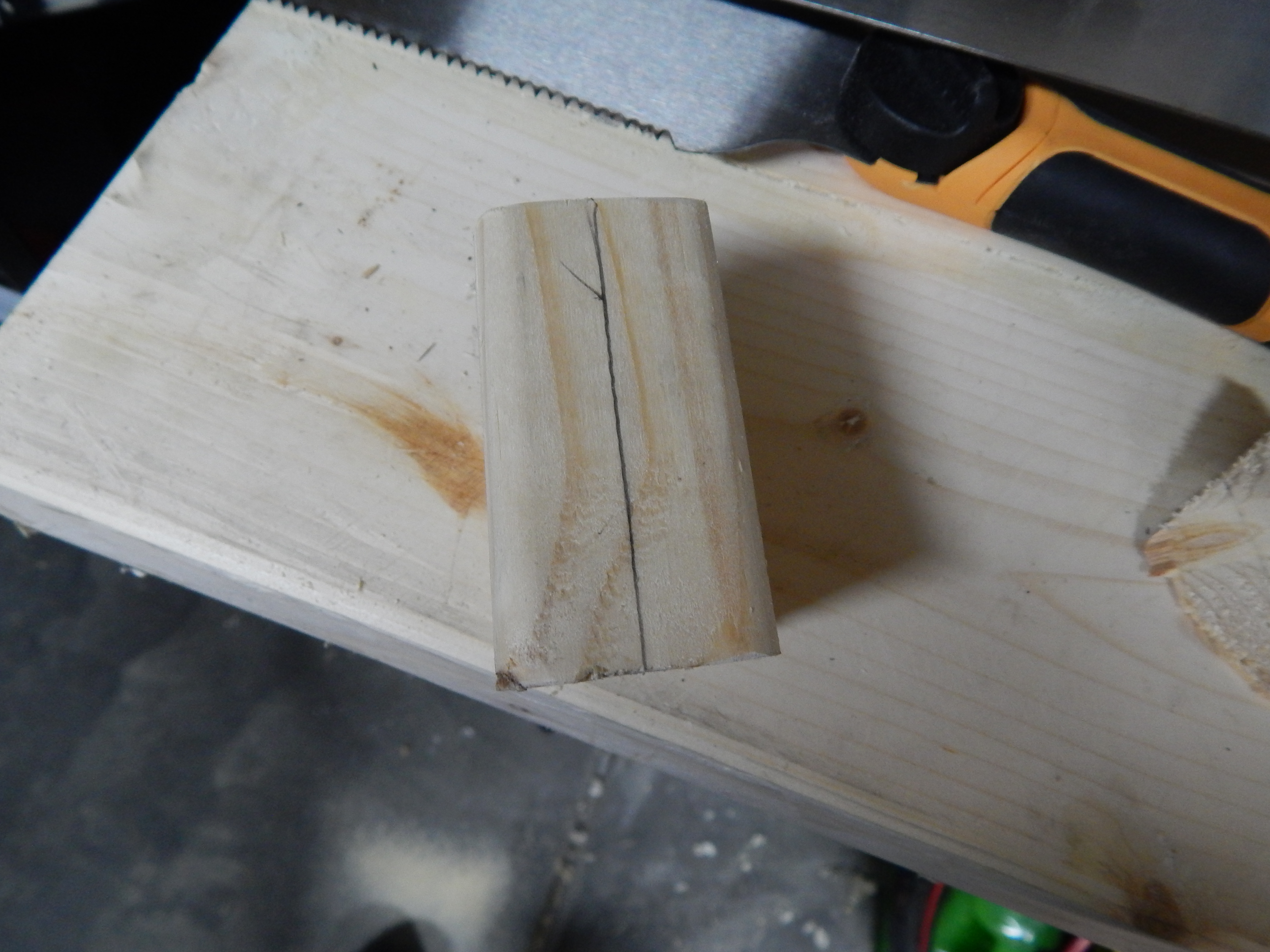
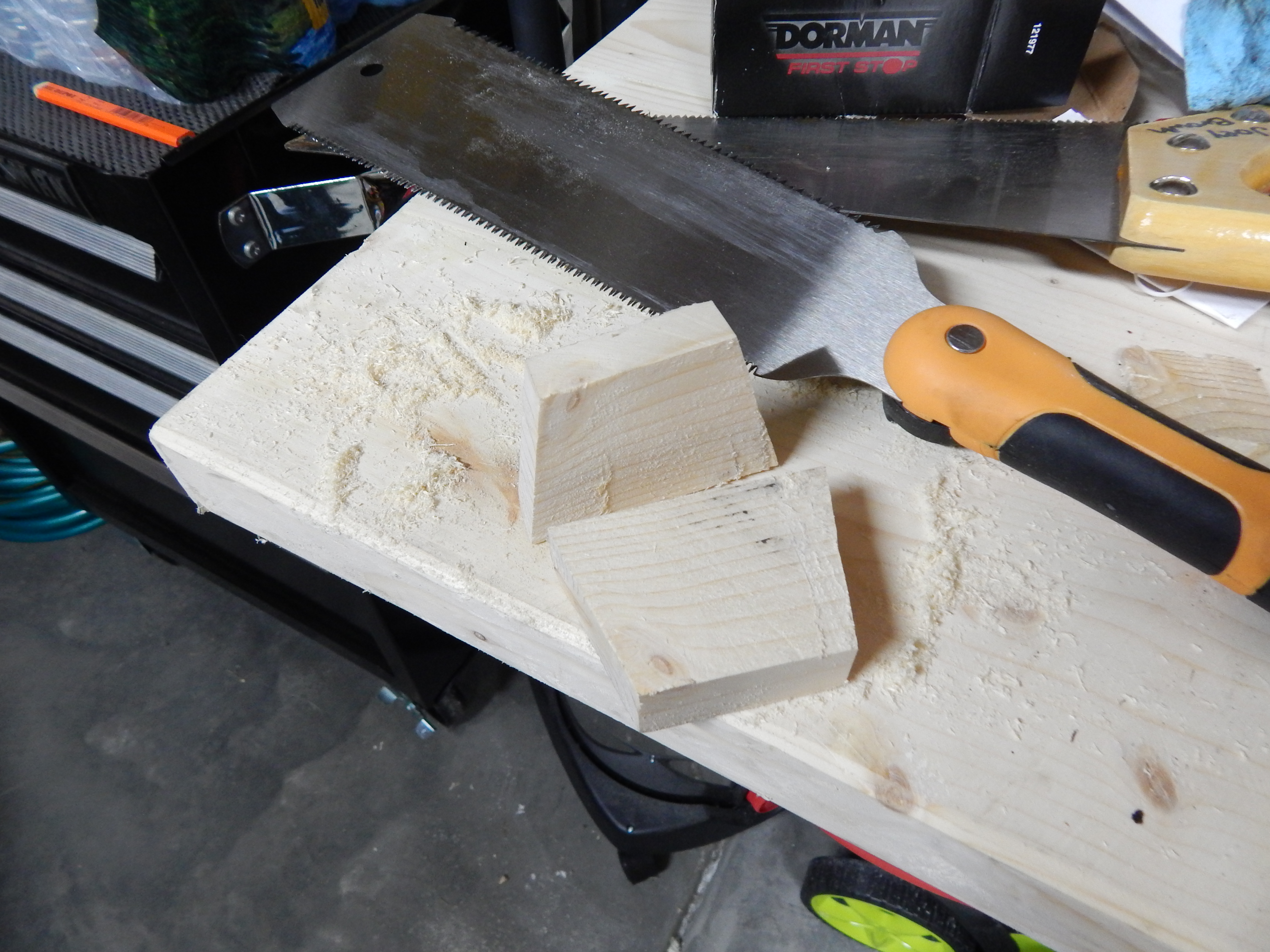
- Make a mark down the middle of the block along the bottom edge. Since 2x6 material is really 1.5" x 3.5", the center is 3/4" for this block.
- Cut the block into 2 halves along this line. If it is not very precise, don't worry. You just need 2 halves to split apart.
- You can sand these pieces to help them fit better when assembled.
Step 6: Hole Drilling
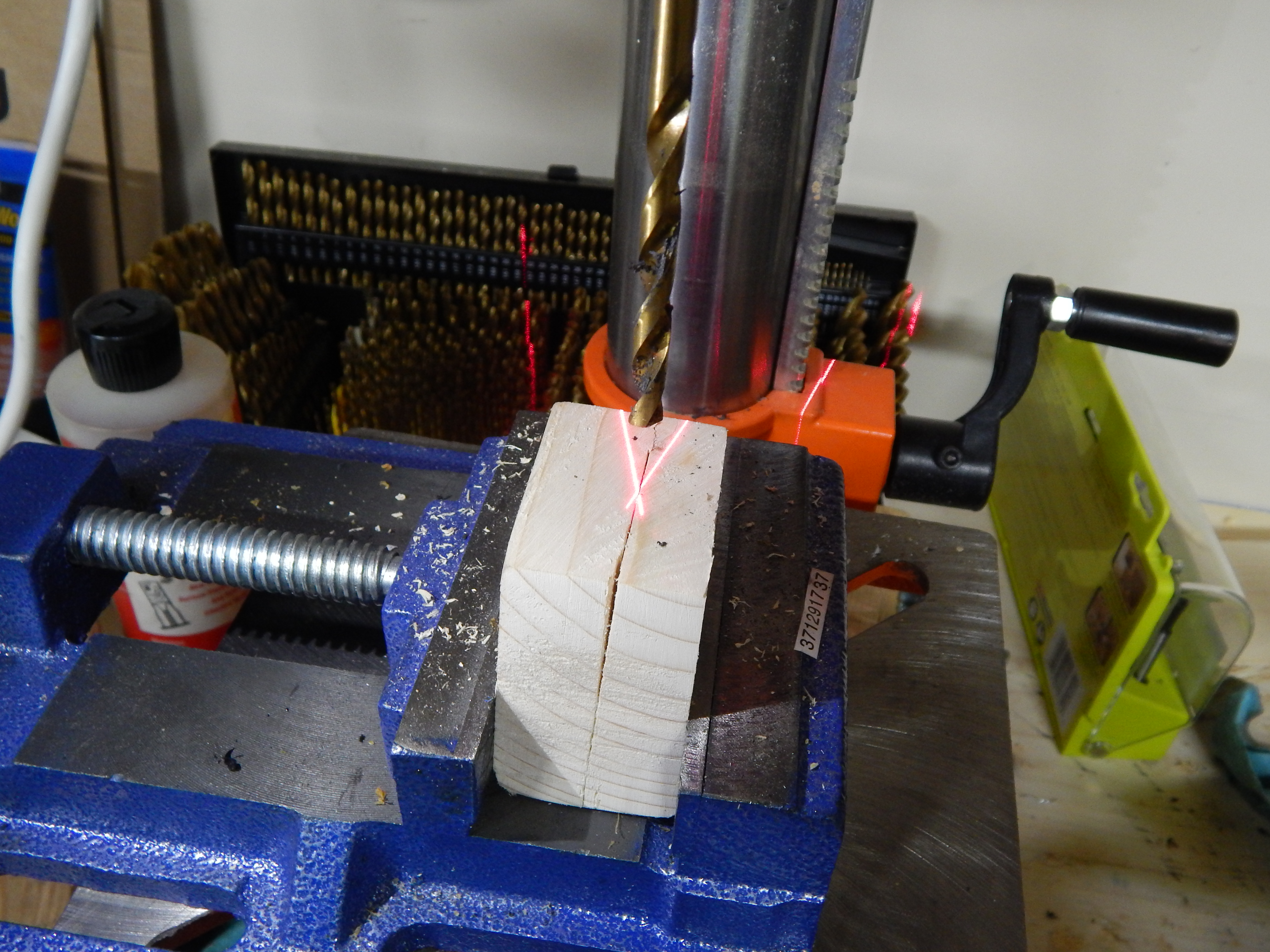
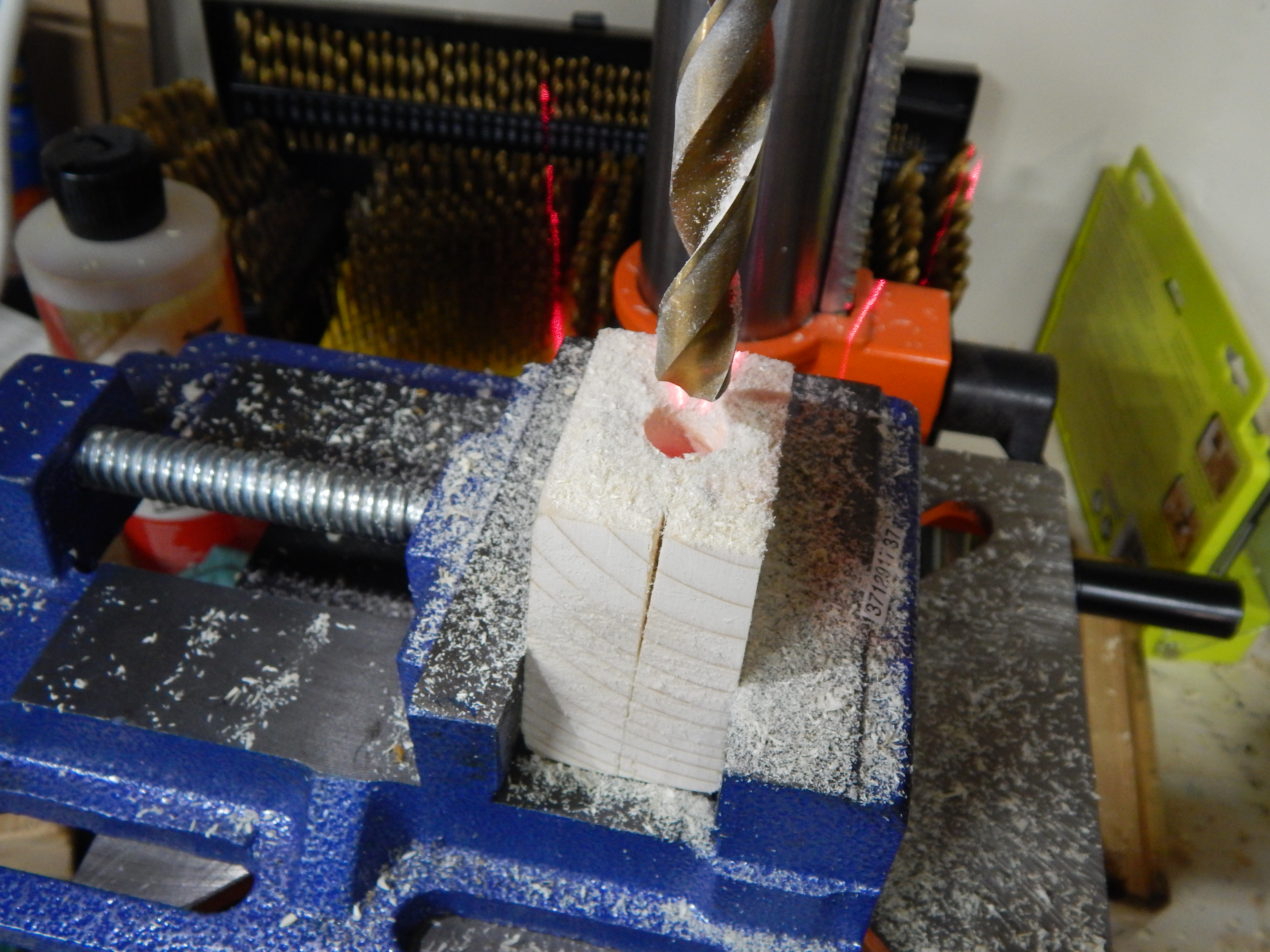
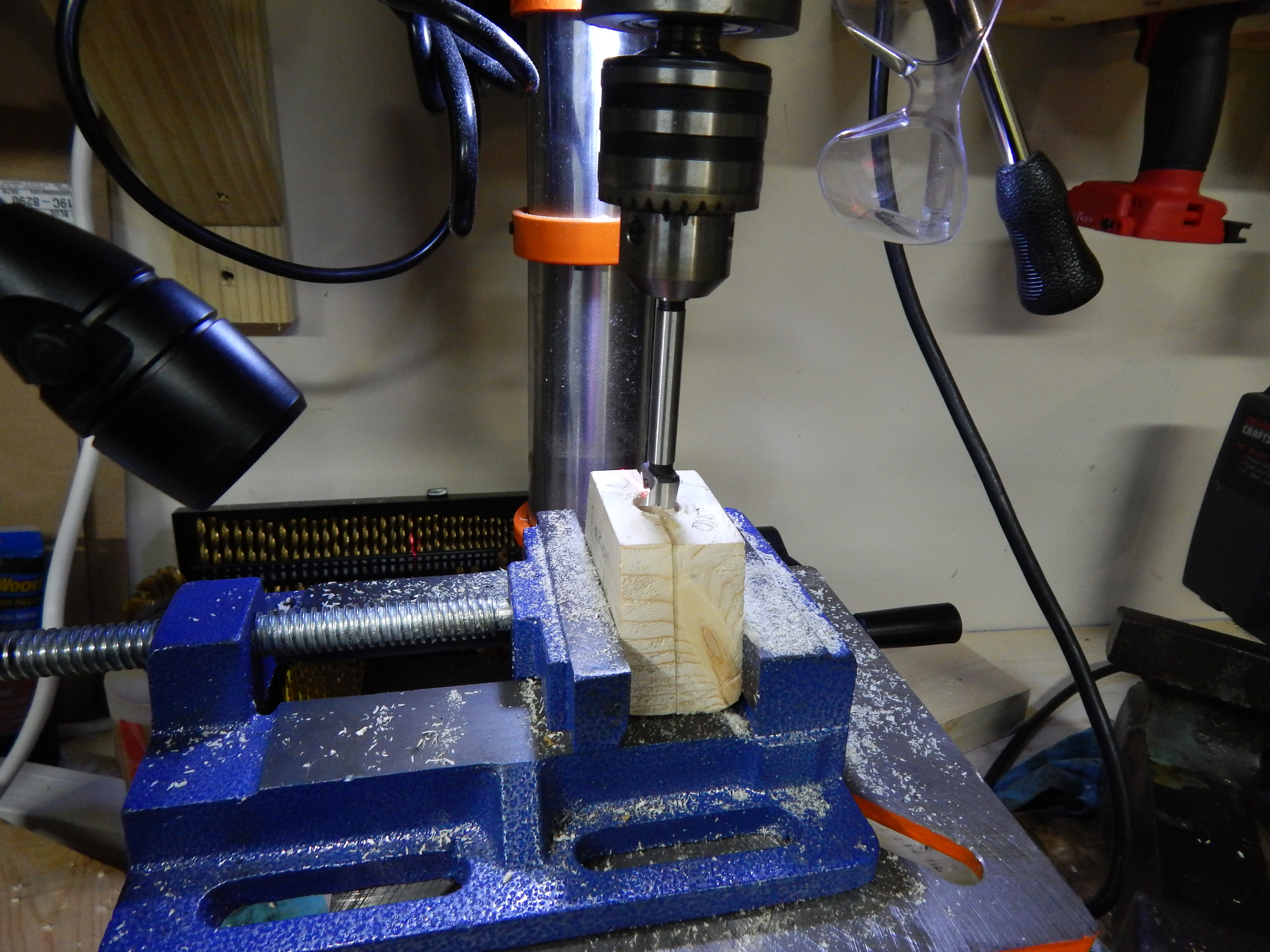
This is the only part that requires any sort of accuracy. You also want to cut the block before drilling the hole to ensure that the blade will be centered for making the cuts.
- Begin drilling the hole in the center of the cut in the block, not the center of the block. I started with a 1/4" drill bit to make the first hole.
- I then used my 1/2" bit to enlarge the hole.
- 1/2" was too small for the tubing to go through without binding so I re-drilled with a 5/8" forstner bit.
Step 7: Add Cutting Blade and Clamp
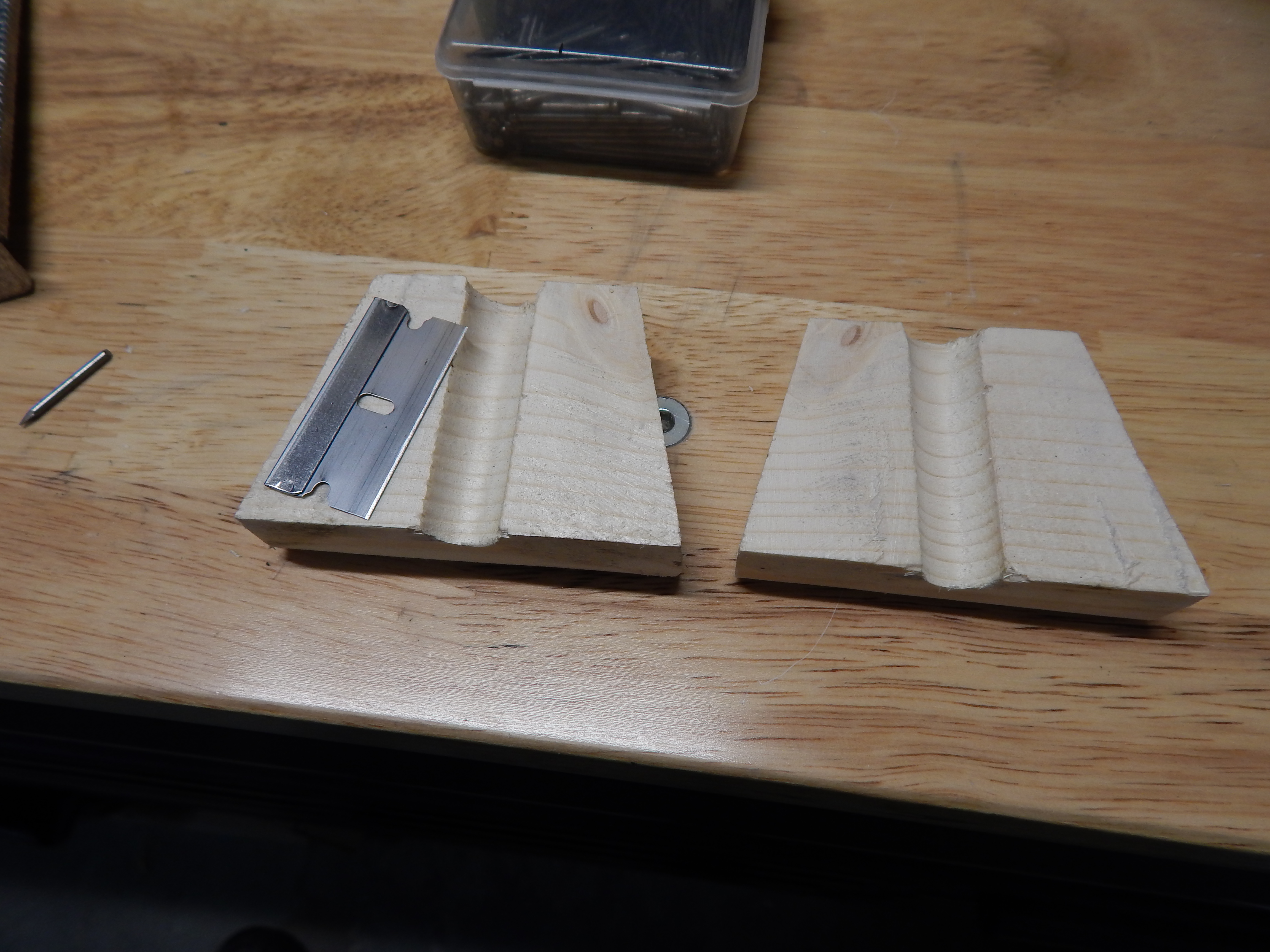
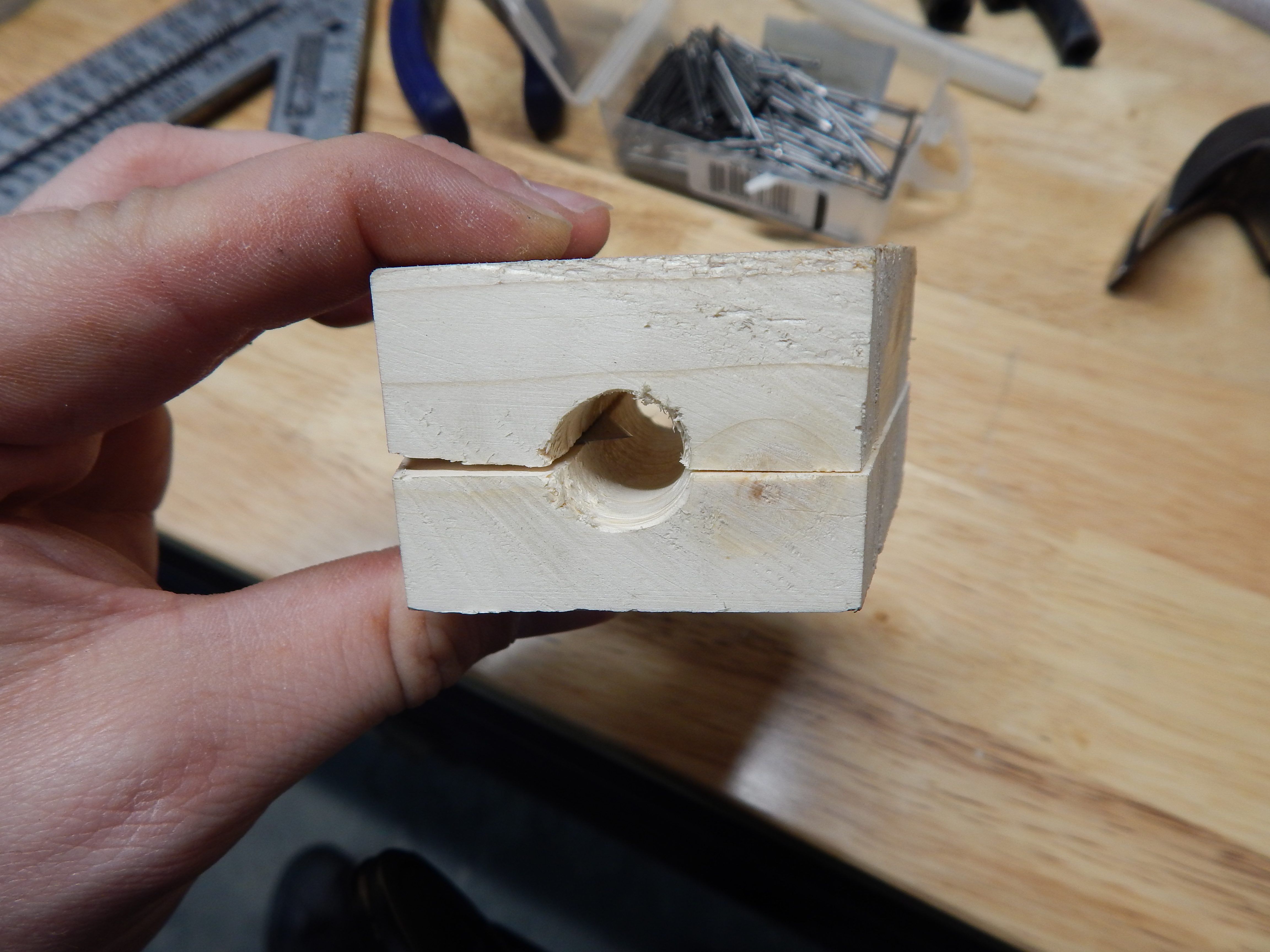
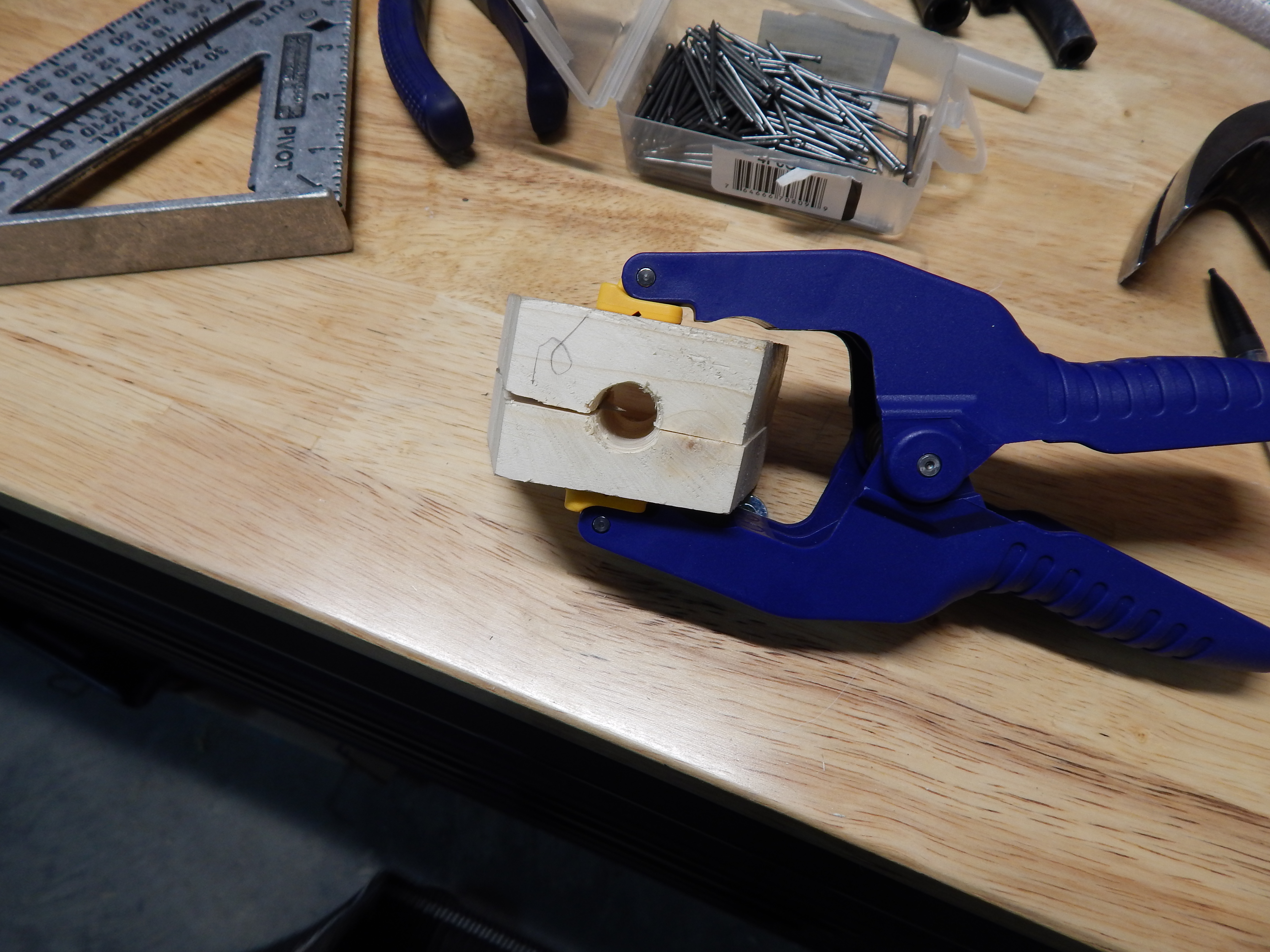
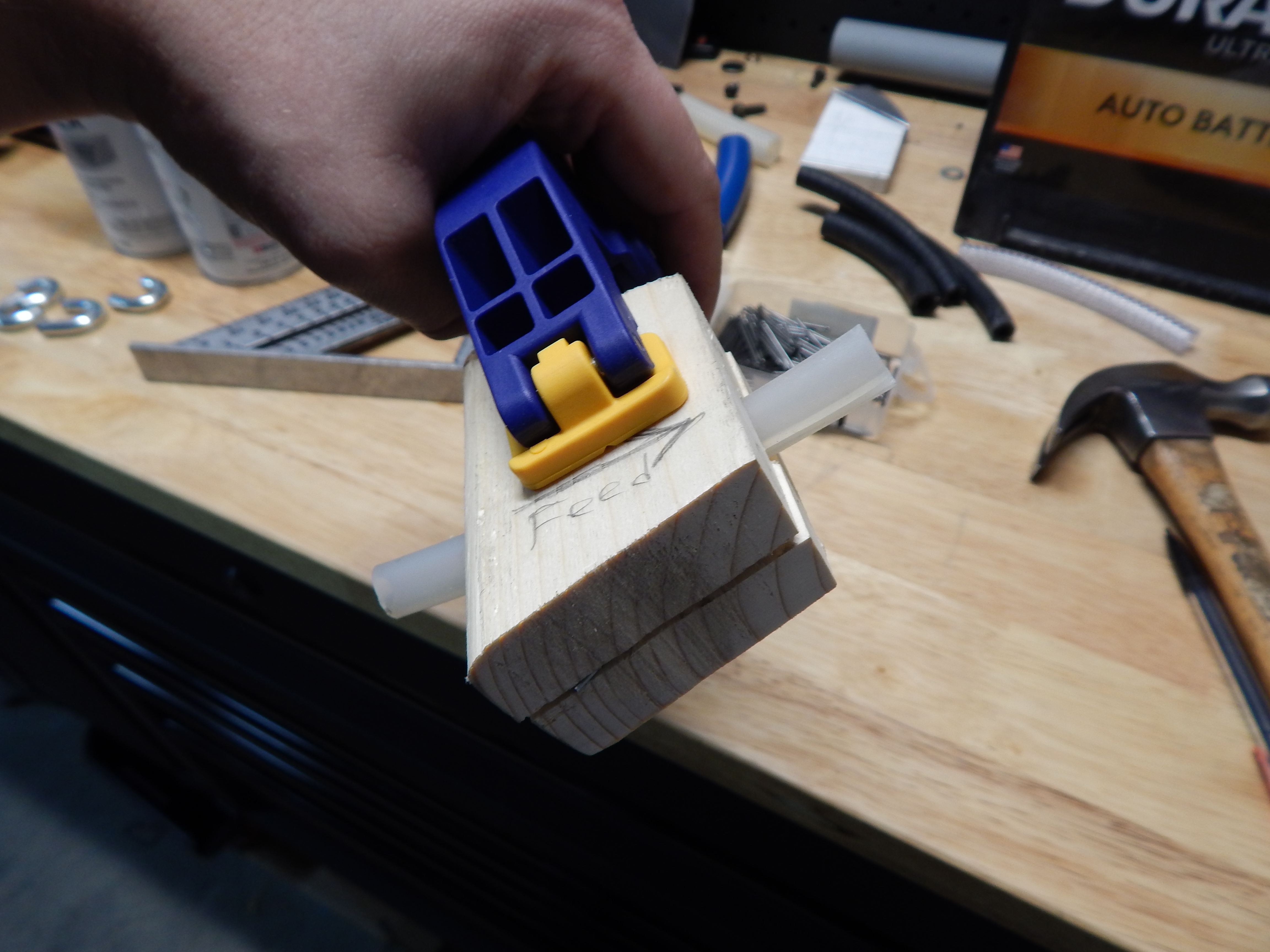
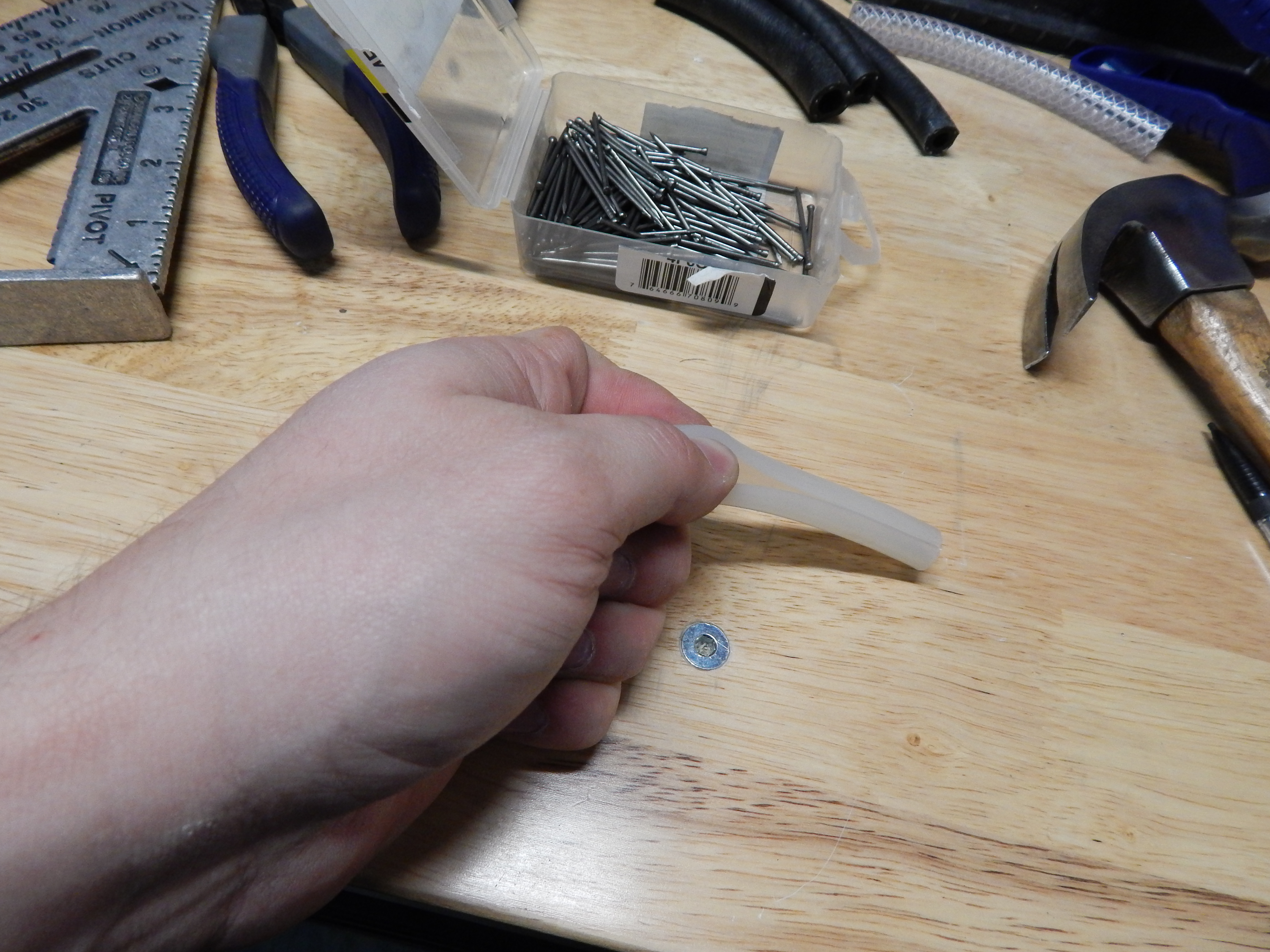
- Place the cutting blade onto one half so that the tip of the blade enters the hole at an angle
- It should protrude no more than halfway for most uses. When stripping large wire insulation, reduce the amount of cutting edge inside the hole.
- Clamp the 2 halves together with a strong clamping force.
- Insert the tubing into the bottom and pull when it extends through the tool.
- You will now have a smooth cut all along the edge. I know it is hard to see on this white tubing.
If you are in a hurry to get this tool usable, you can stop here.
I added a few features in the next steps and show the general usage.
Step 8: Alignment Pins
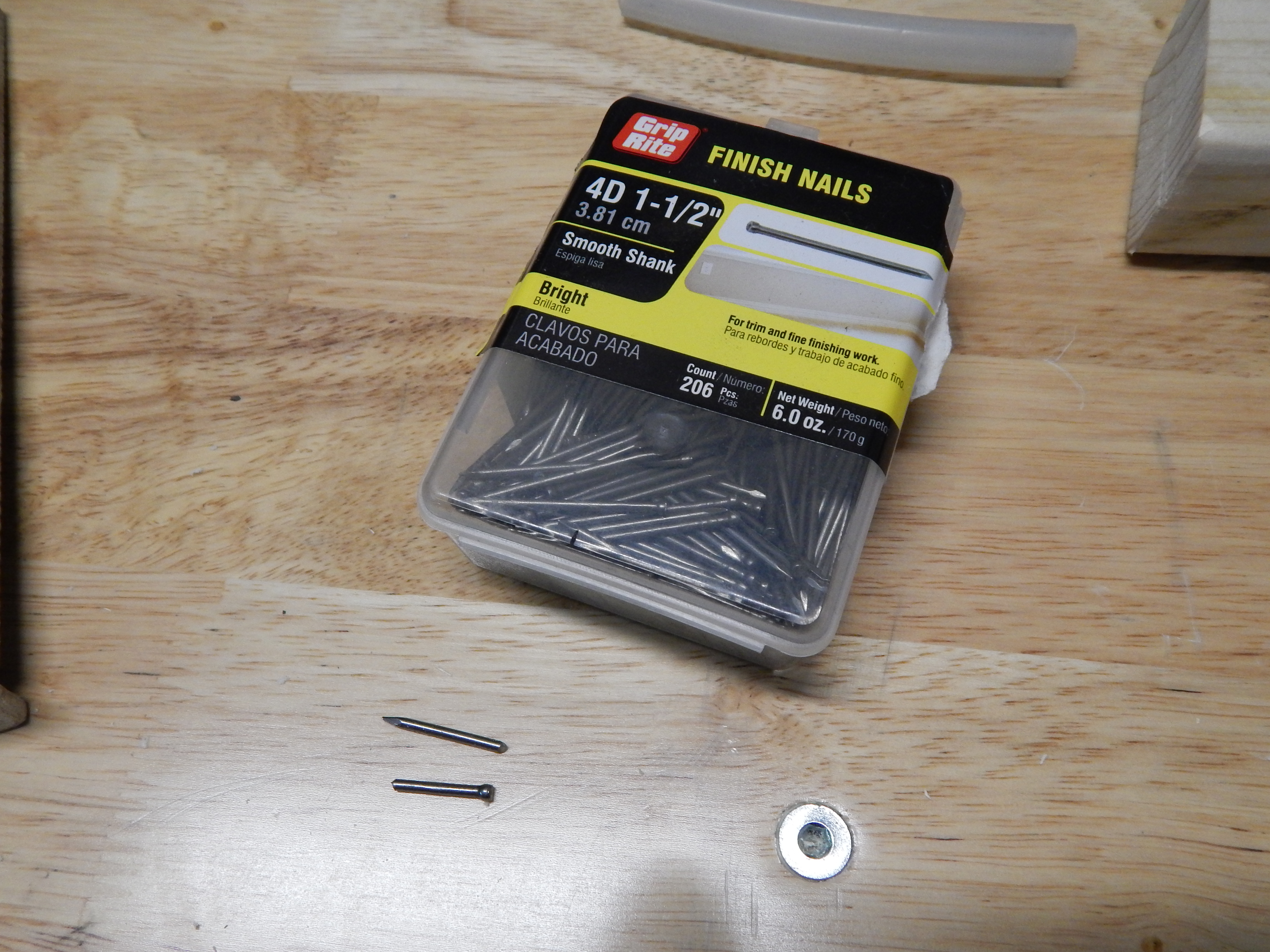
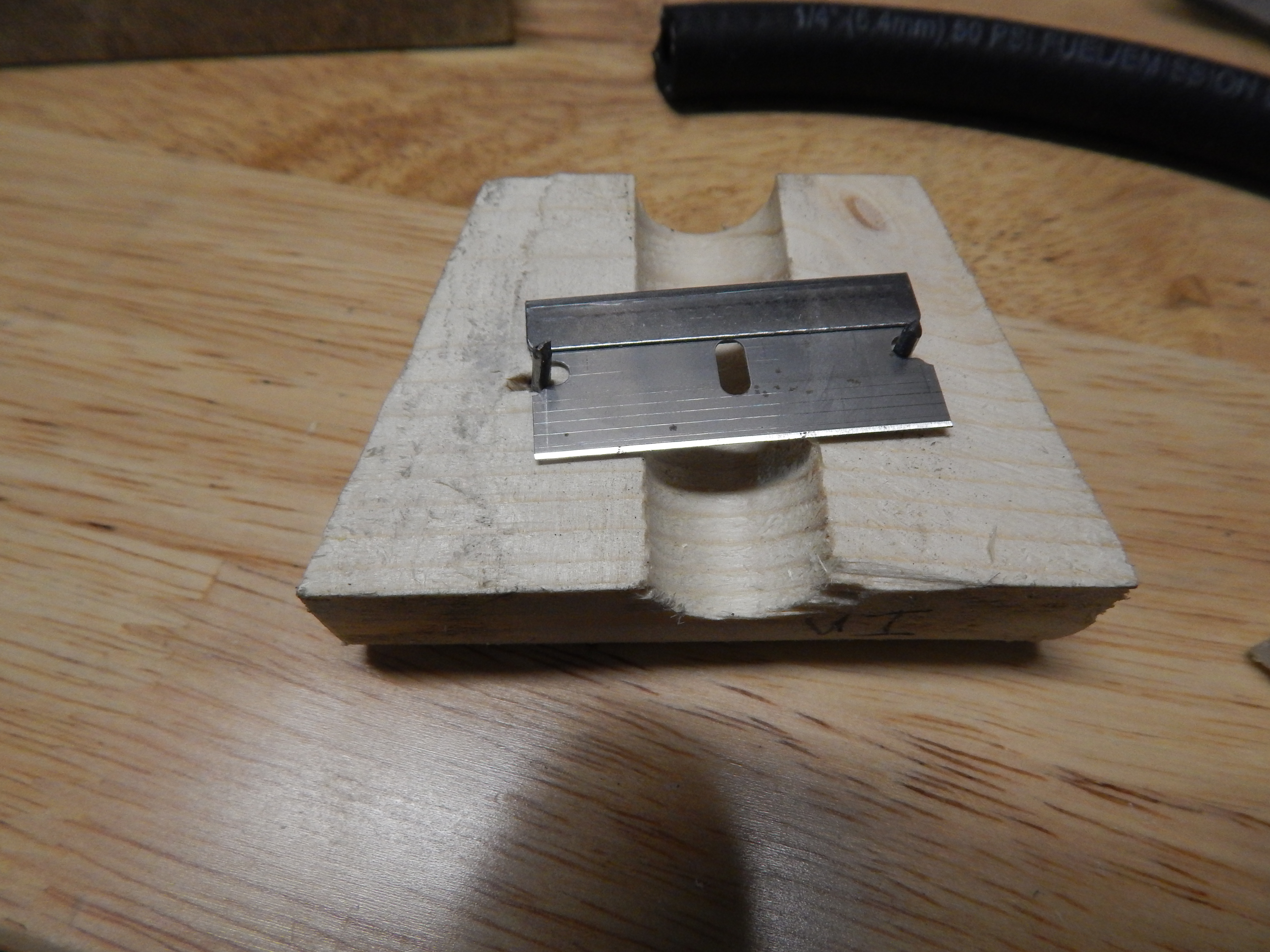
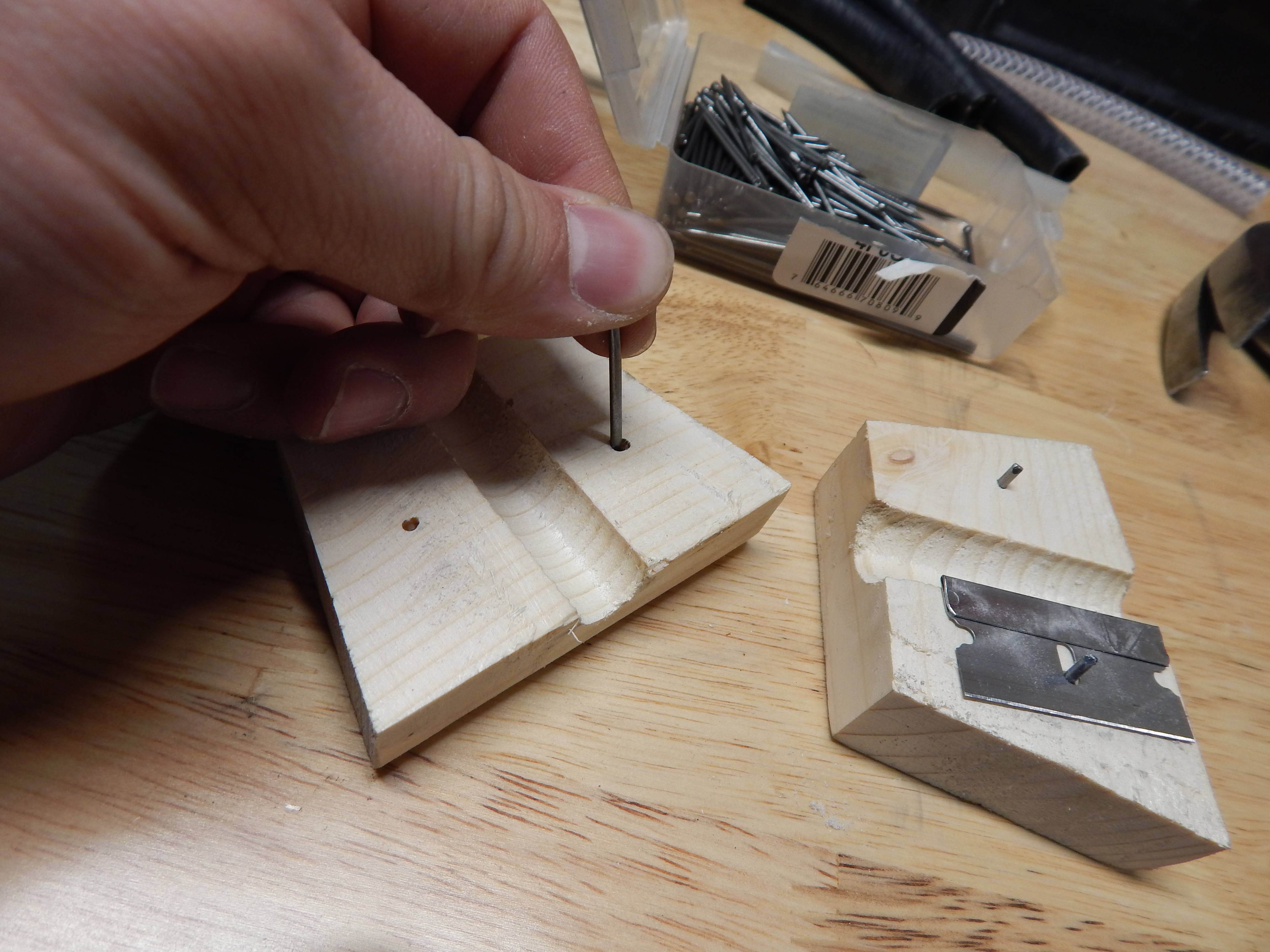
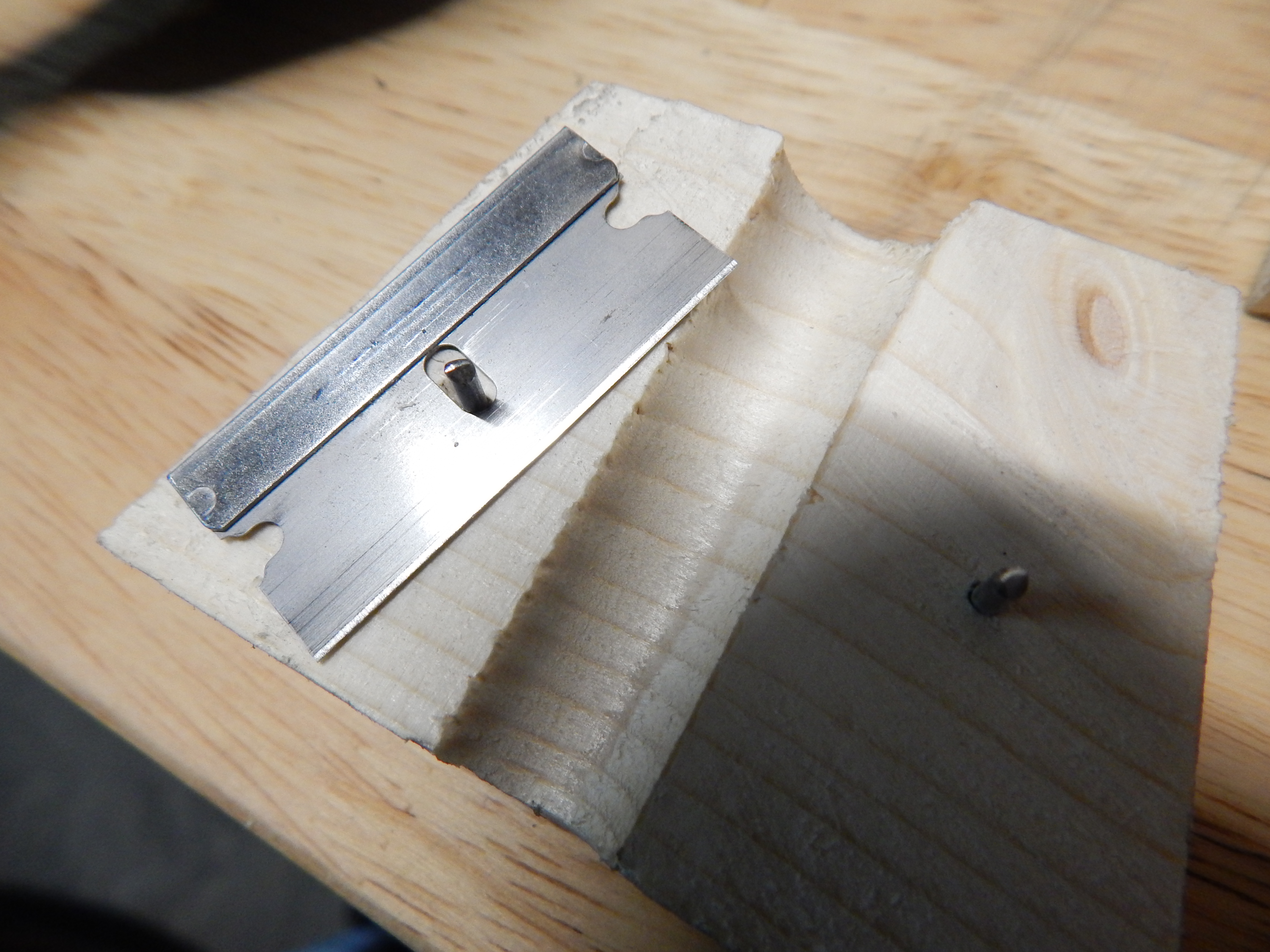
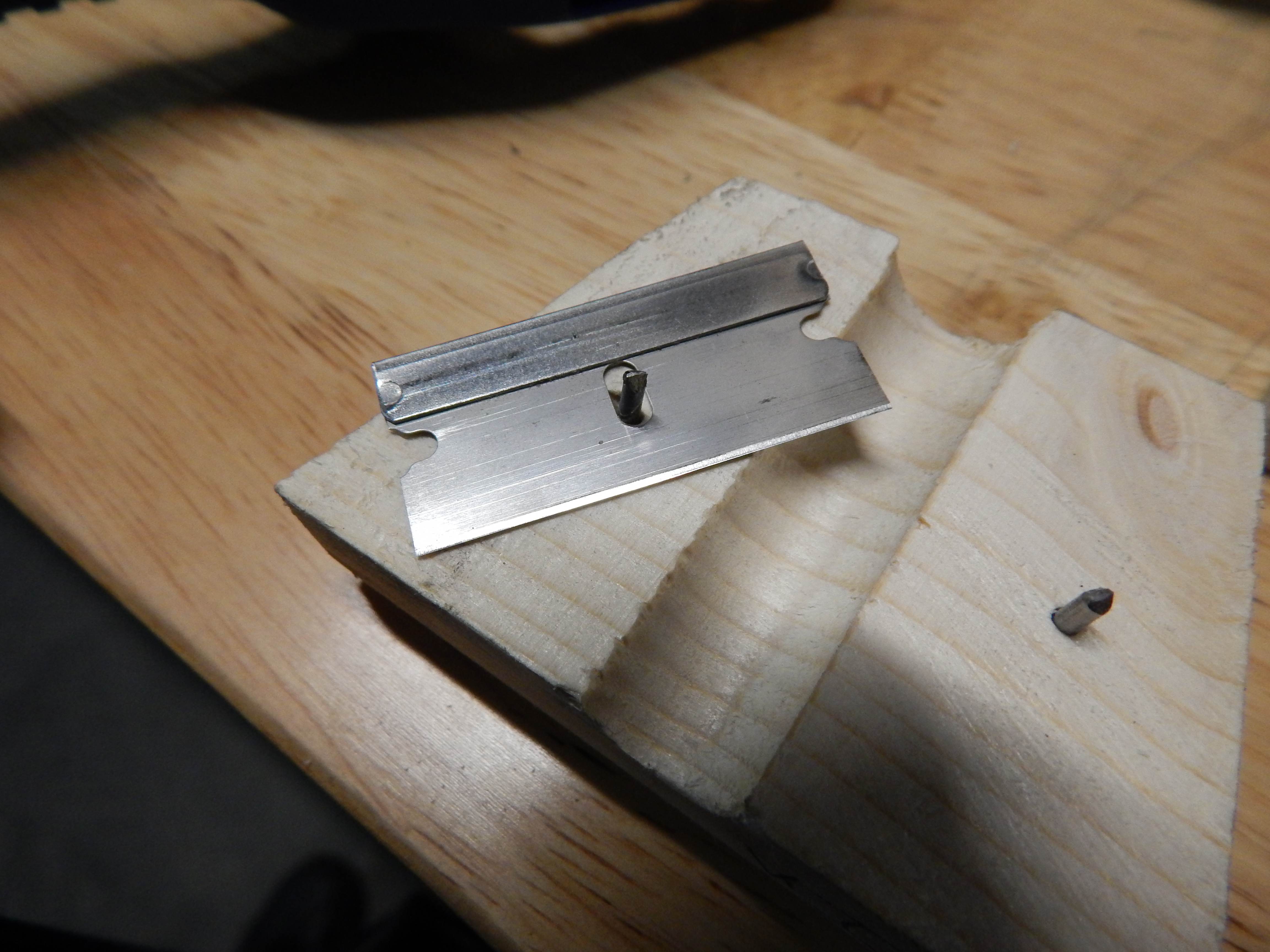
These help align the pieces before clamping and hold the cutting blade from falling when the clamp is removed. They are not required for the tool to work.
- I used 1.5" finish nails and cut them in half to be 3/4". A smarter person would just use smaller nails.
- My blades had 2 notches on the side. I used these to space the pins and hammer them into one side.
- Place the other half over the first piece and tap it with a hammer to make some marks where the pins fit.
- Hammer another nail into these holes about halfway through the block. Wiggle the nail when removing to enlarge the holes. This is so the pieces separate easily instead of always being nailed together.
- The blade had a hole so it could be placed over the pin without interfering with the cutting depth adjustments.
Step 9: Markings
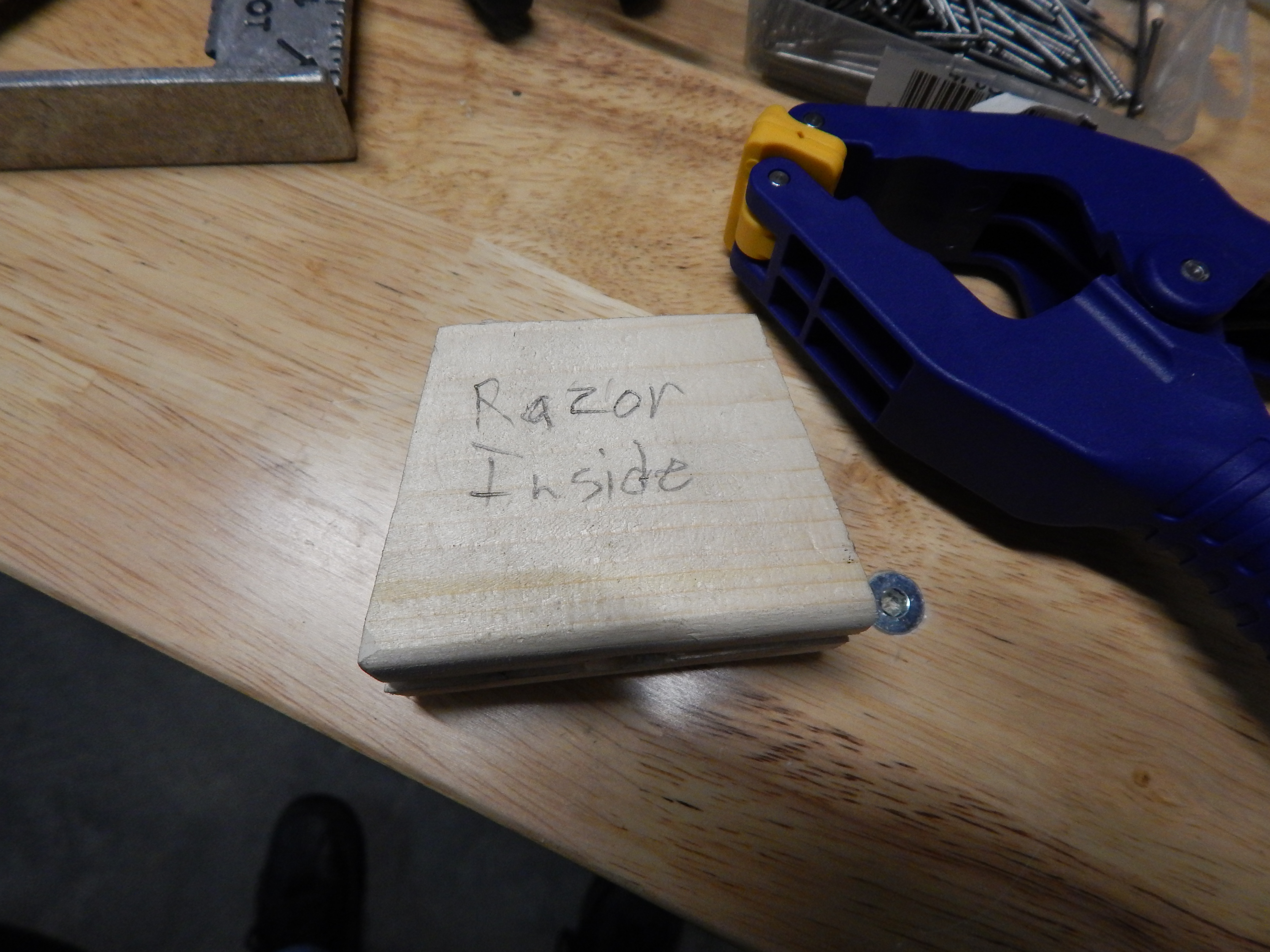
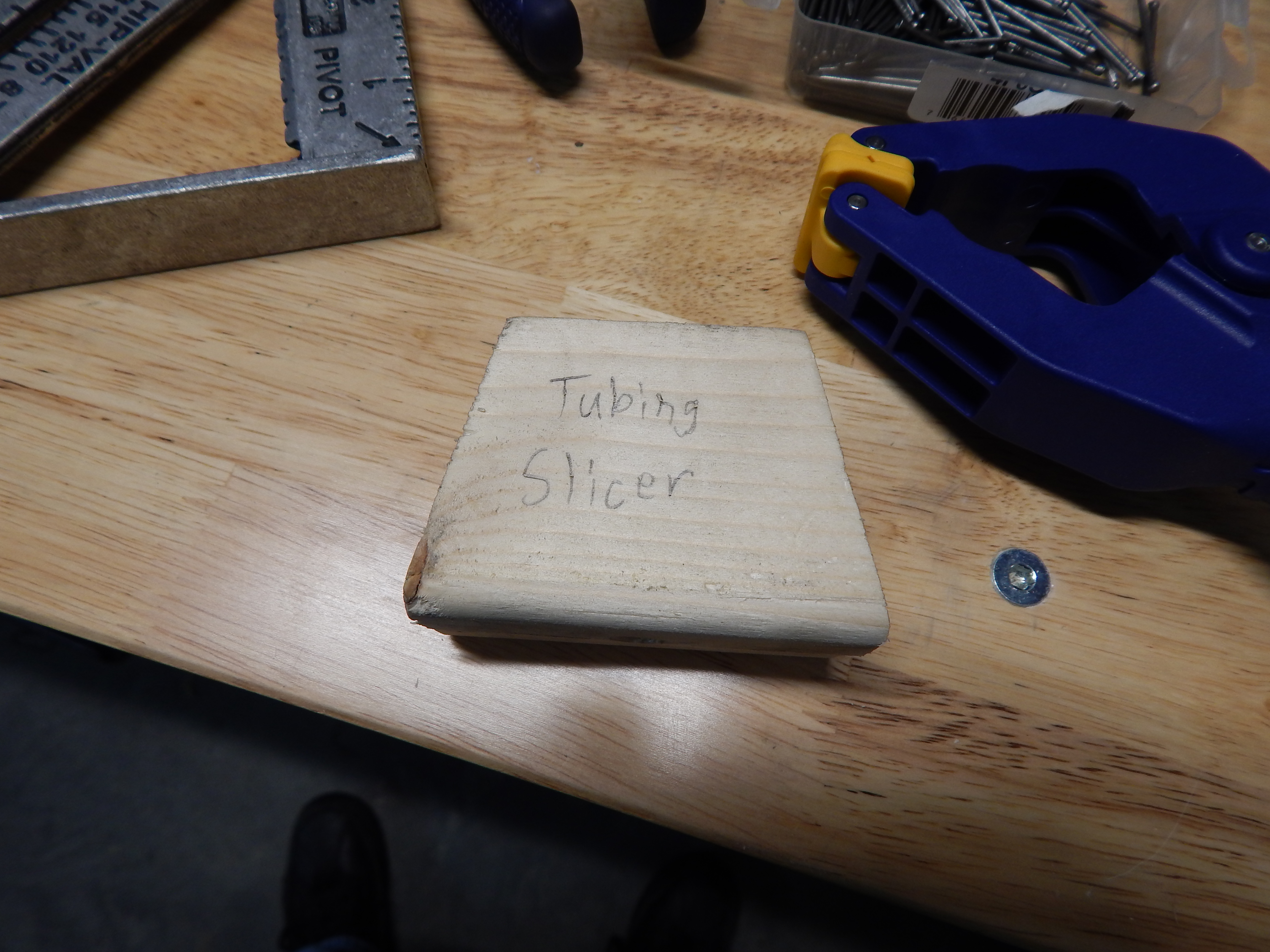

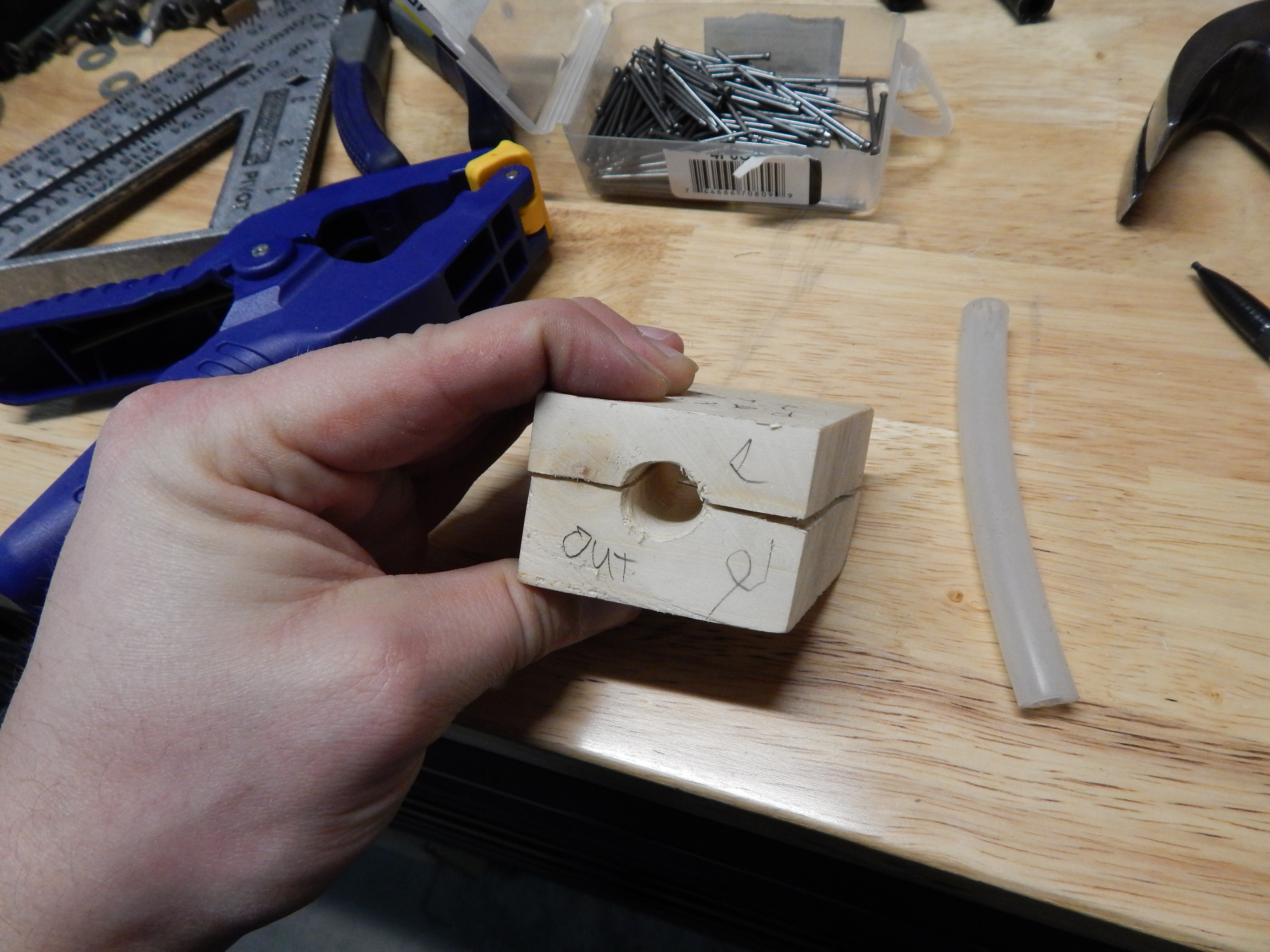
I made some basic markings so in the distant future, I still know what this is and how to use it. Also to make users aware that there is a hidden razor blade.
- Razor inside - there is a sharp hidden object
- Name
- Inlet hole
- Output hole
- I also added a feed direction arrow on one side
Step 10: Using the Tool for Side Cuts
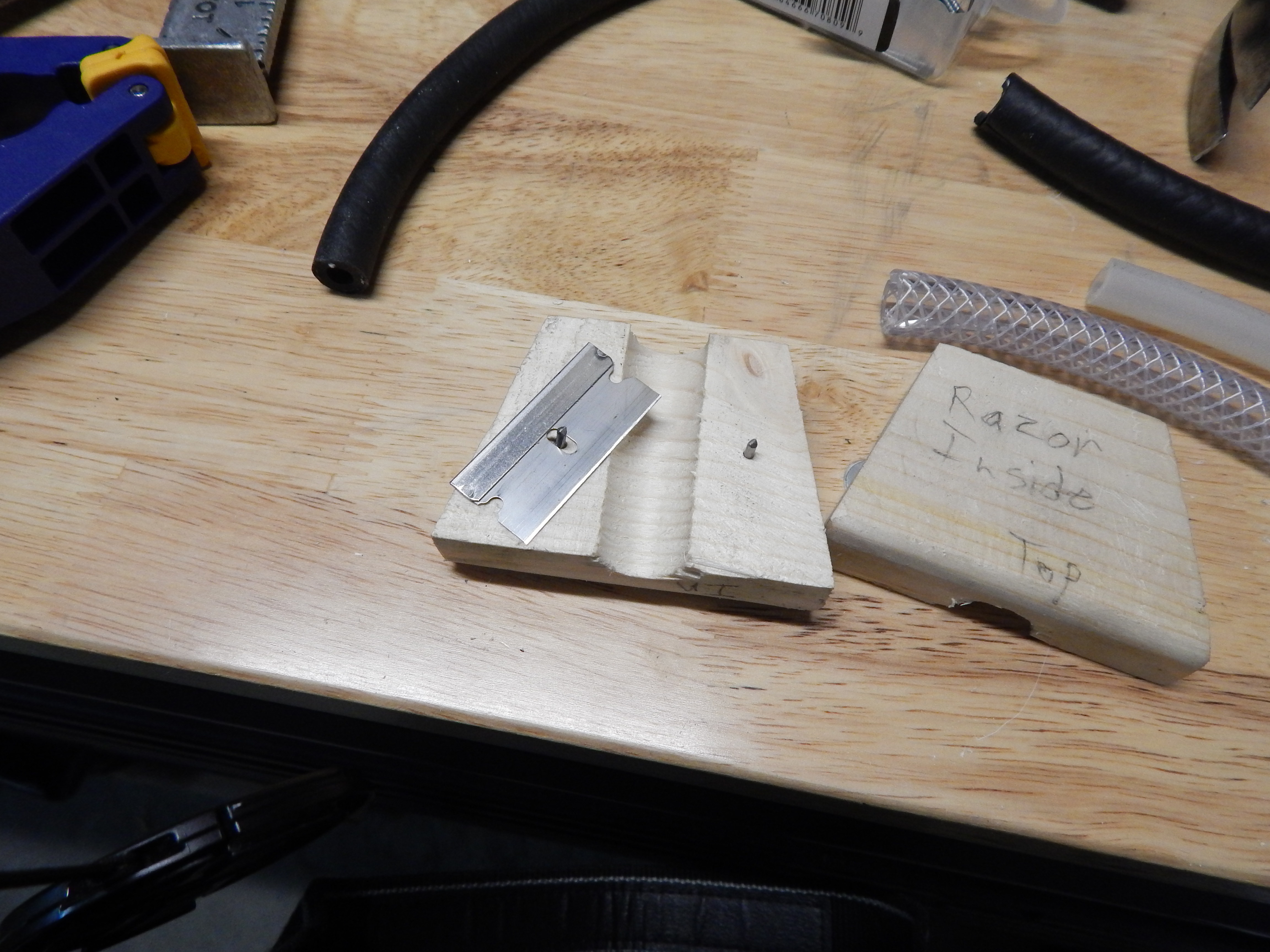
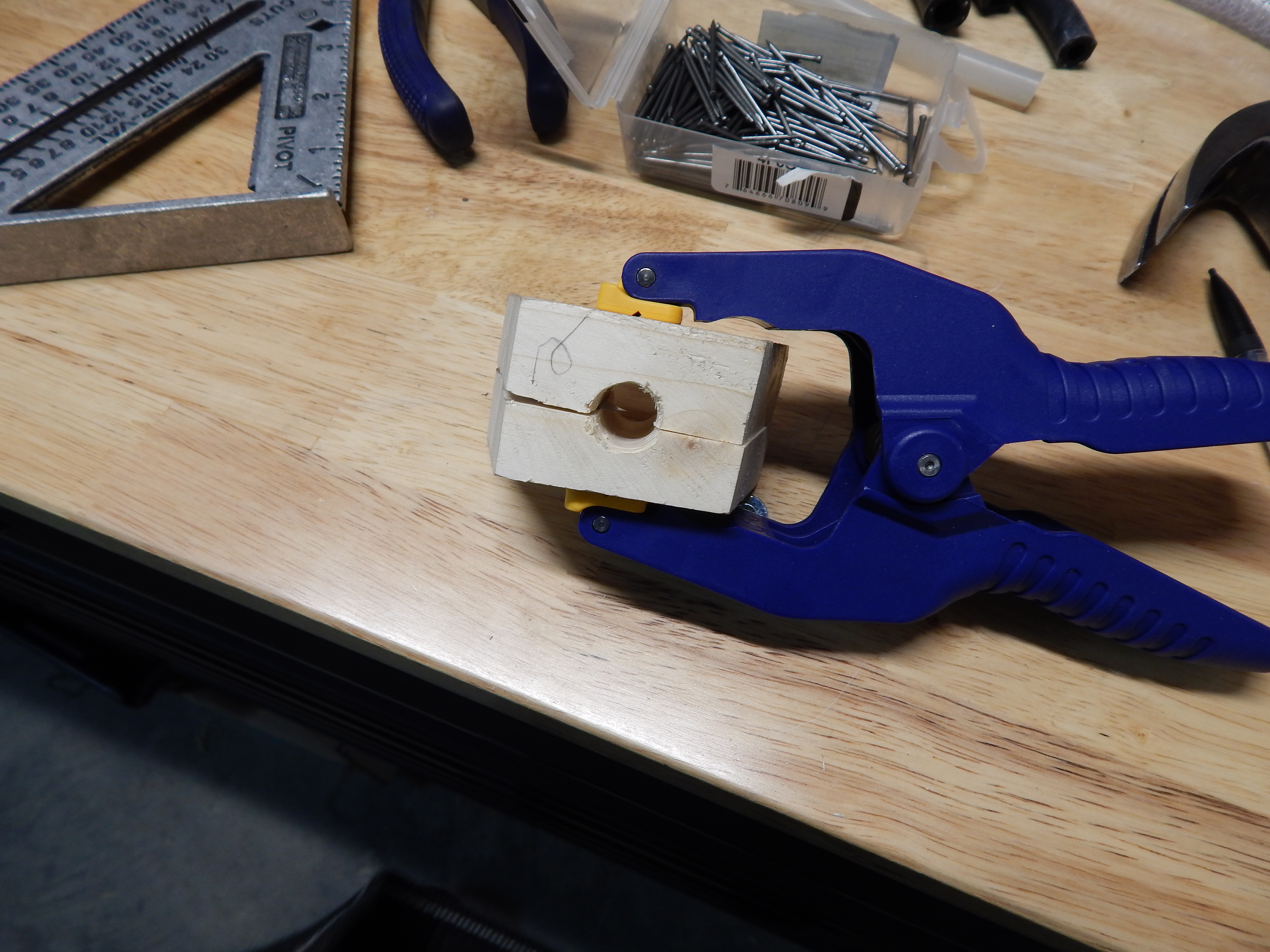
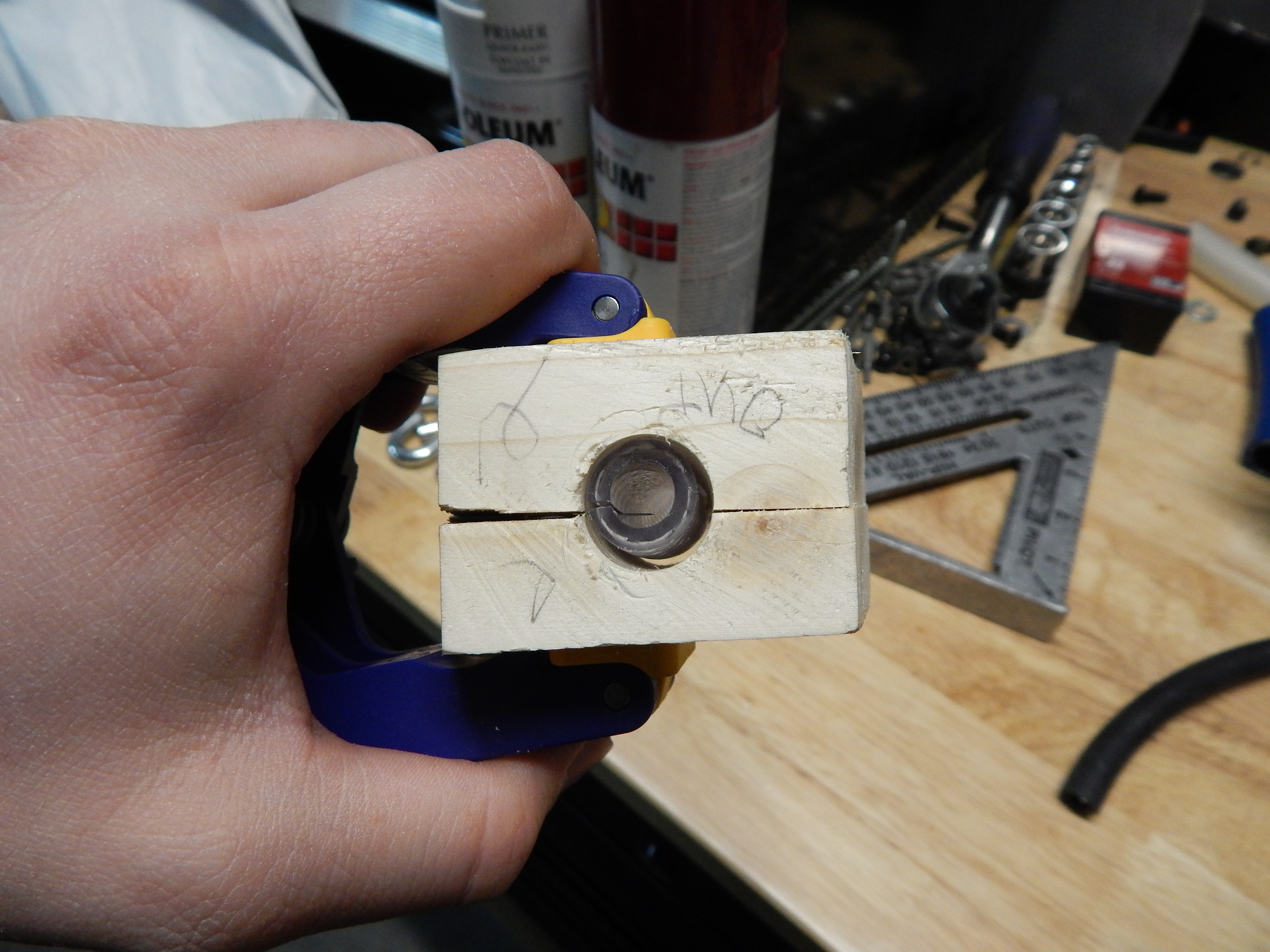
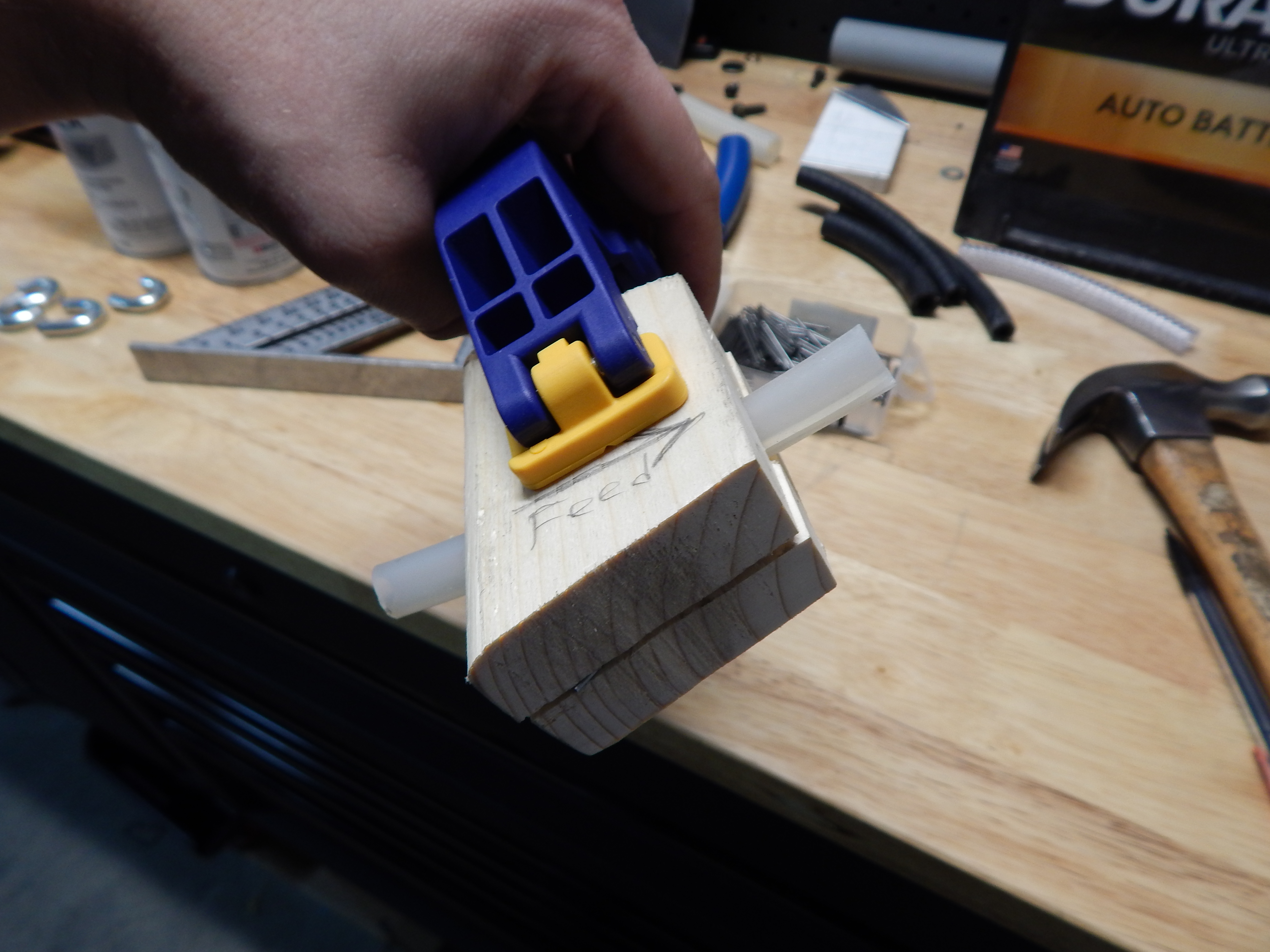
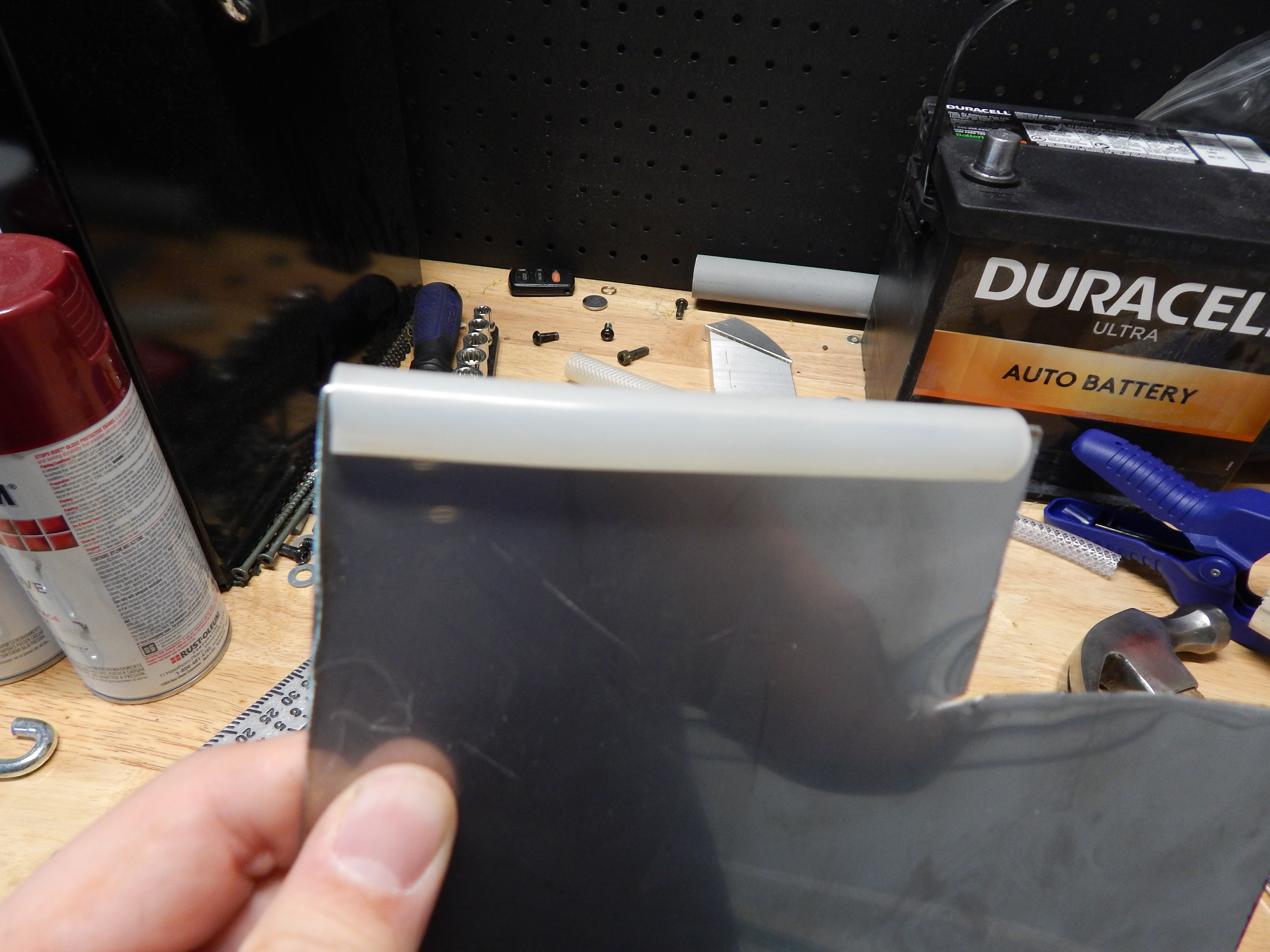
- Set the blade on the pin and to the desired cutting depth for your task. Usually halfway into the opening works well.
- Clamp the assembly together. Check that the blade is still in the correct position.
- Push the tubing through the cutter. Pull it the rest of the way. Thicker/stiffer rubber or reinforced types will take more effort. Change to a new blade if this becomes too difficult. The blade can also be rotated to use the other half of its cutting edge.
- Place the rubber along an edge or wherever it is needed. This can be used to make rubber edge guards or custom grommets around a hole held in place with zip ties or adhesive. This is especially useful if the hole for the grommet is not circular.
Step 11: Other Uses
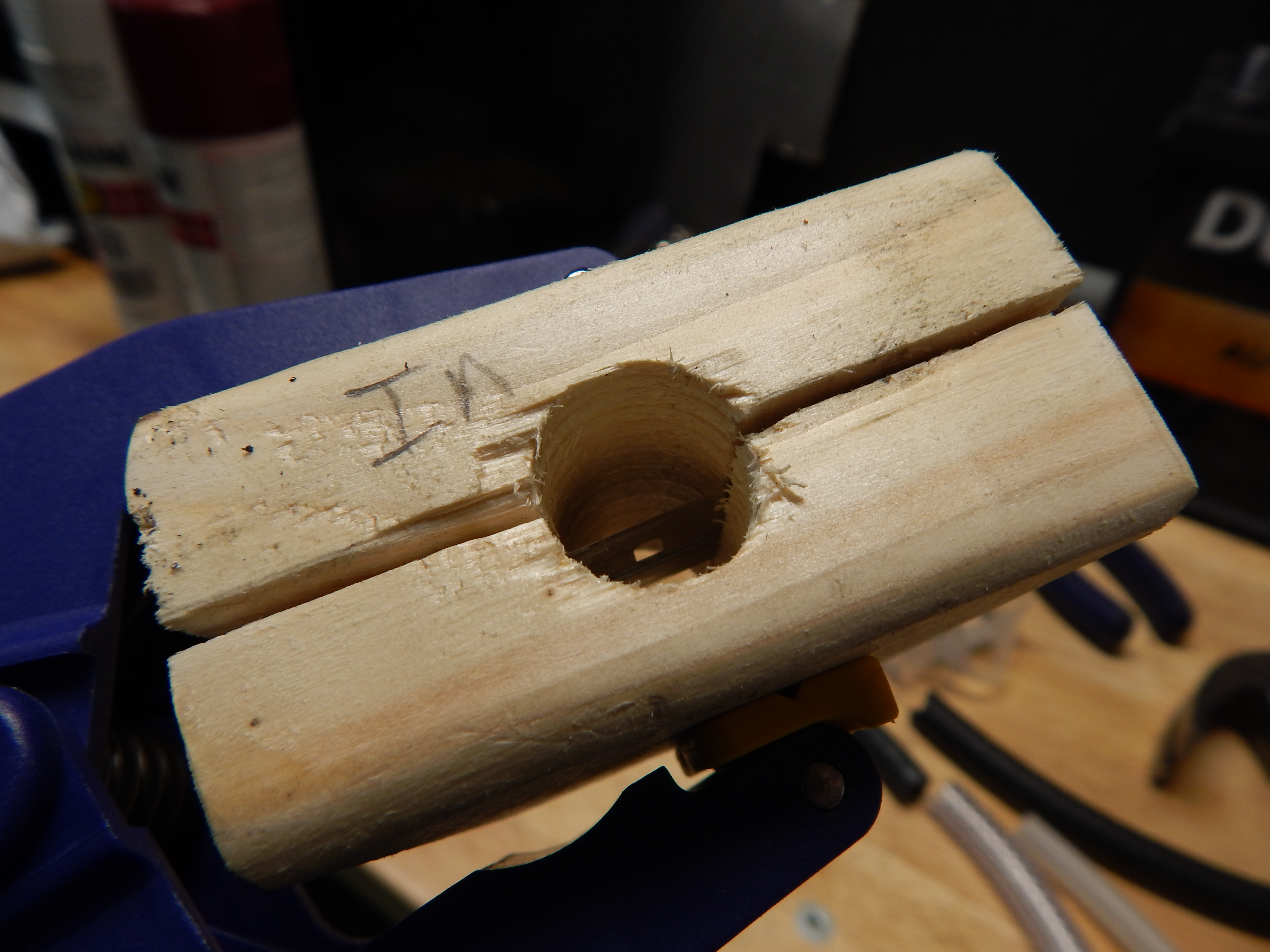
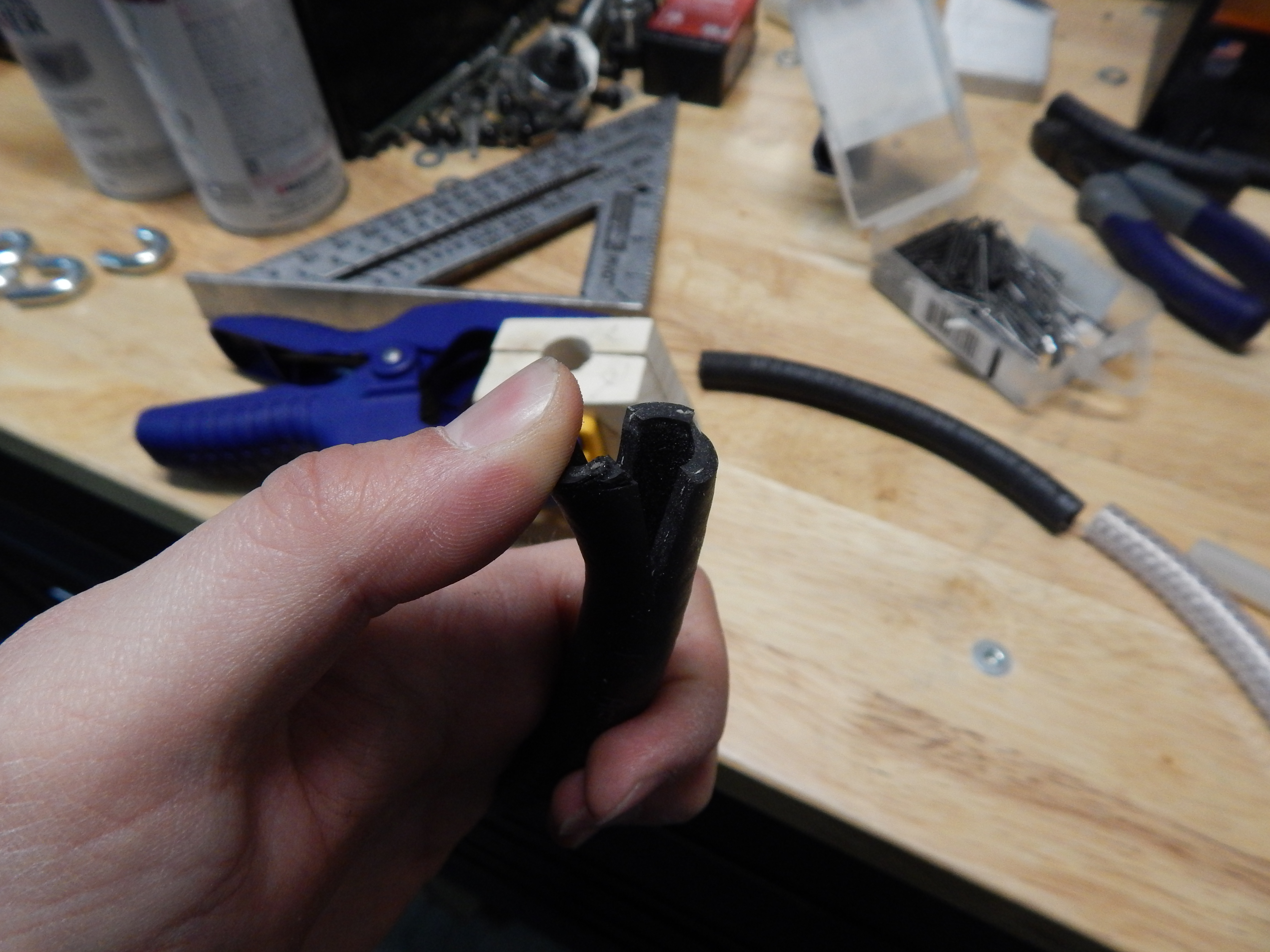
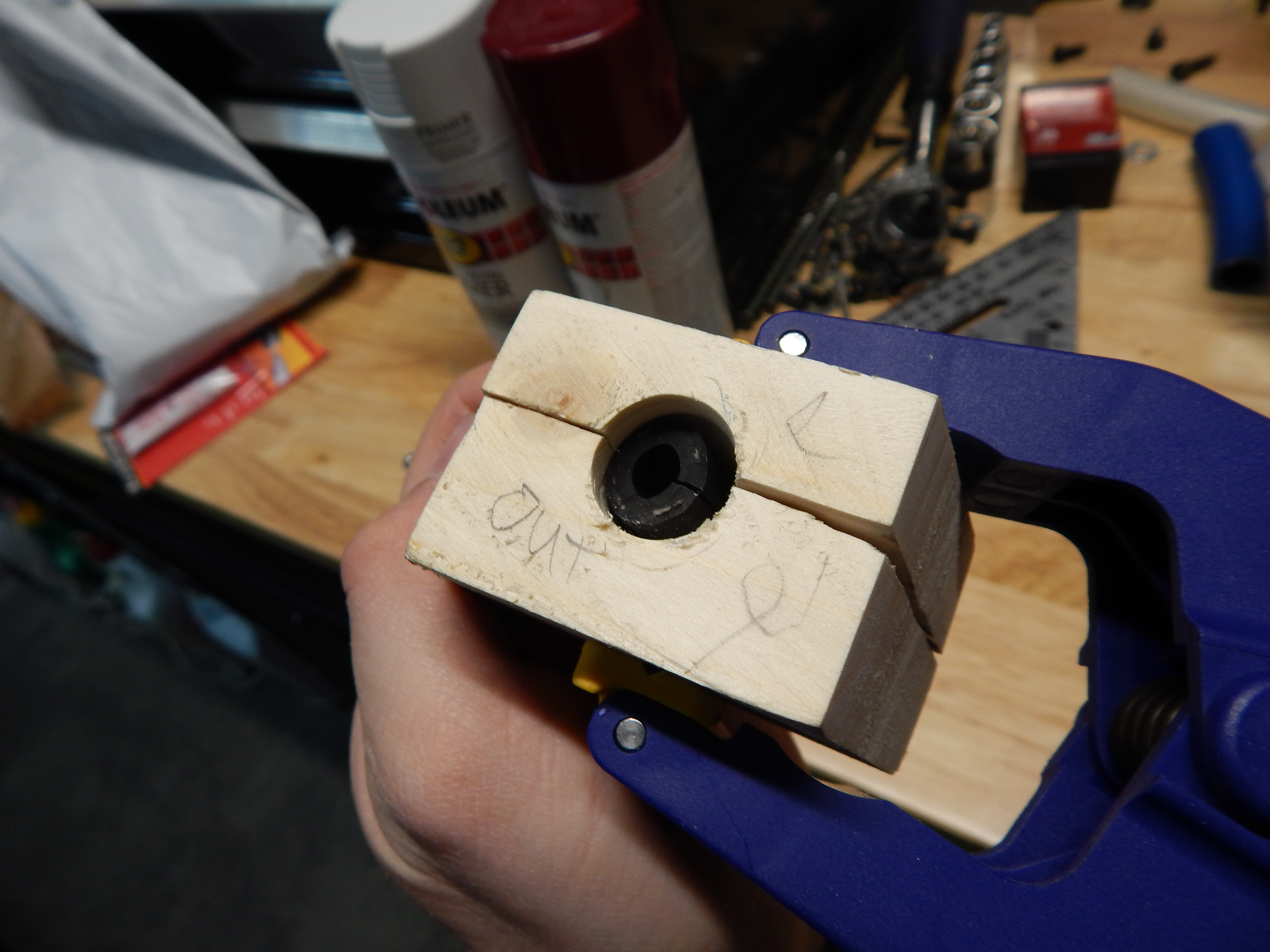
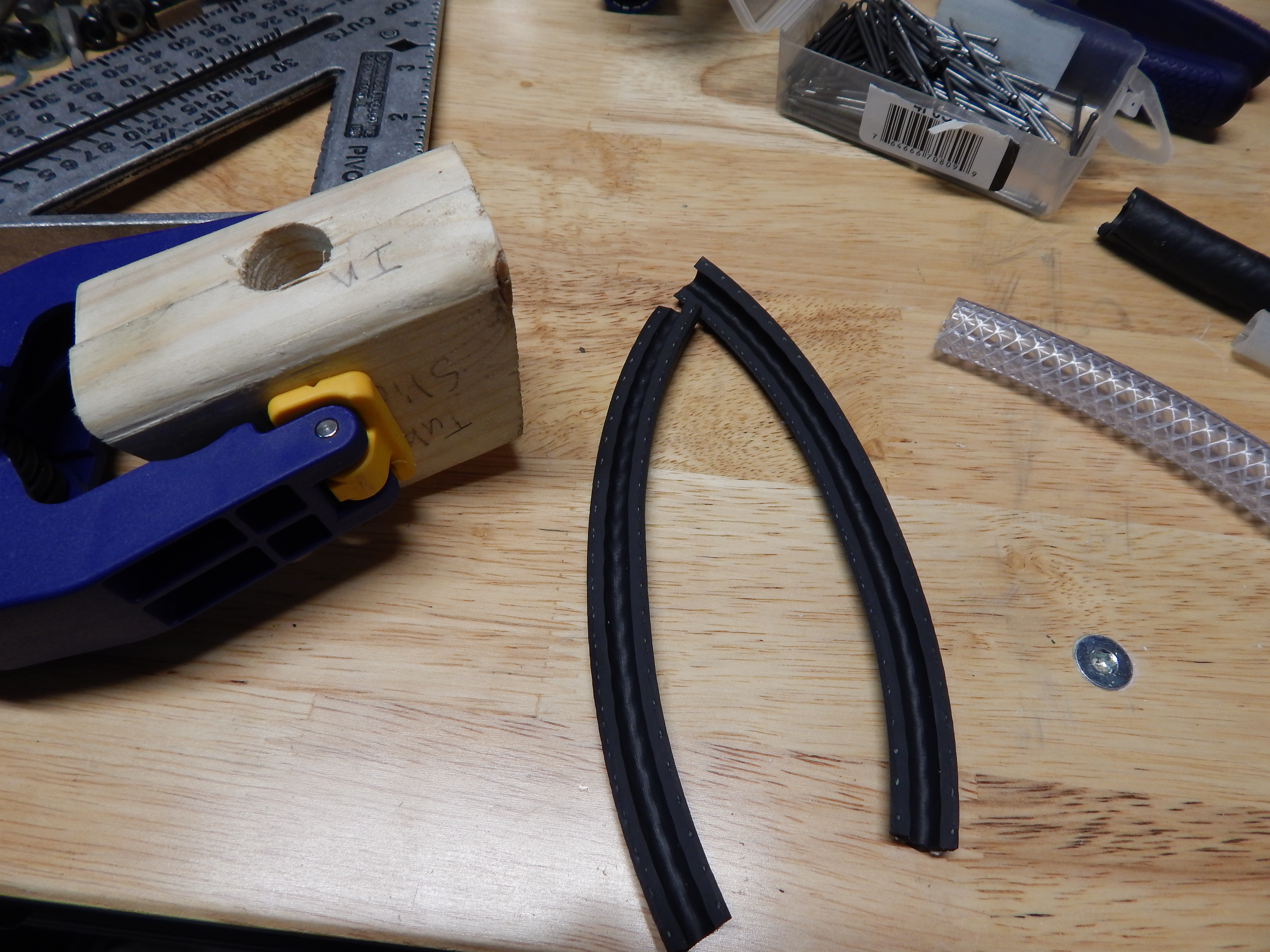
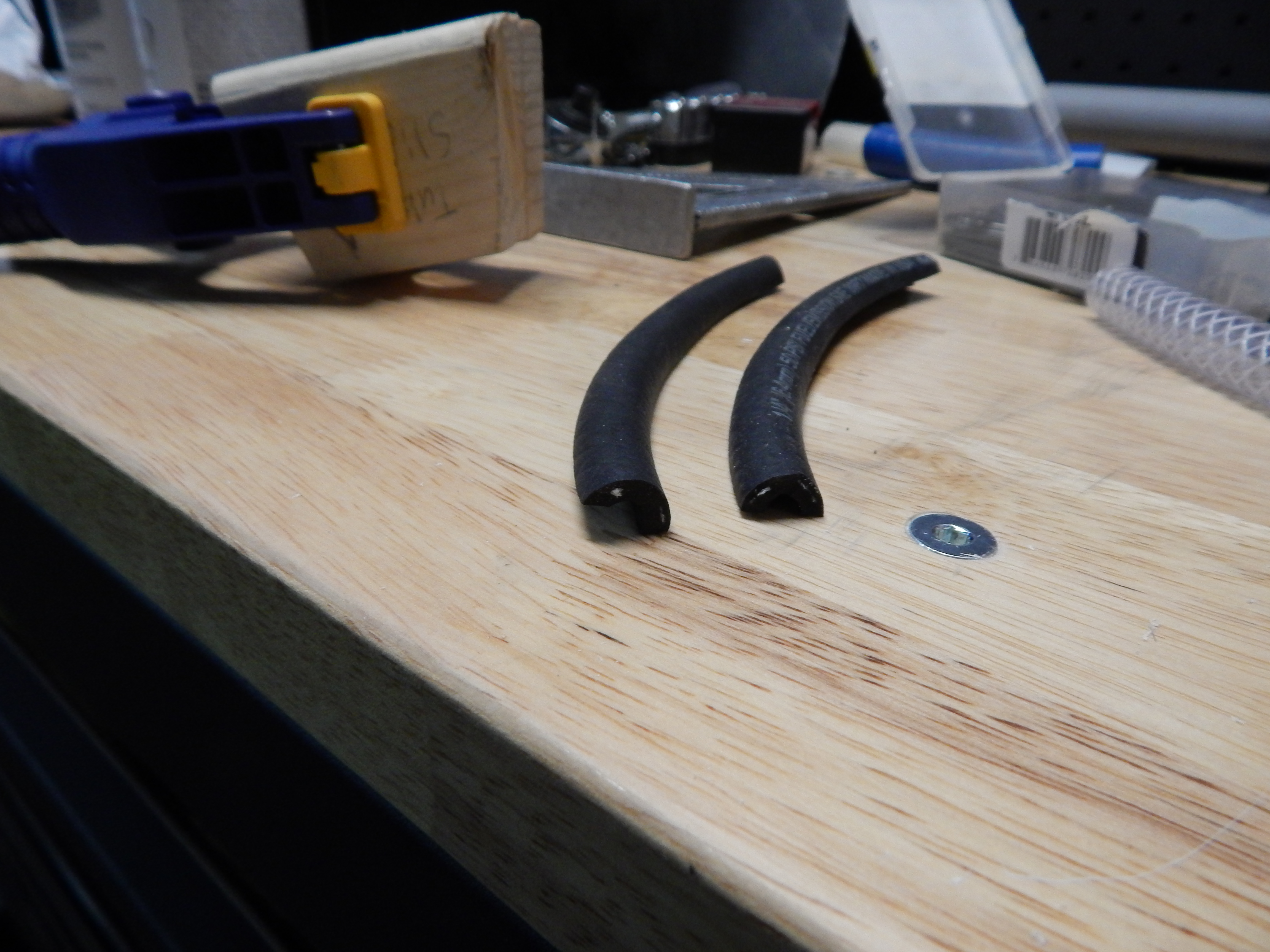
- Placing the blade so that it completely spans the hole will make a short double slice into the end of the hose/tubing.
- The hose will spread after cutting, preventing it from exiting the tool. This can still be useful to get the hose over a large barb fitting or other object.
- Rotating the hose 180 degrees and making a second cut will create 2 half round lengths
Final Thoughts
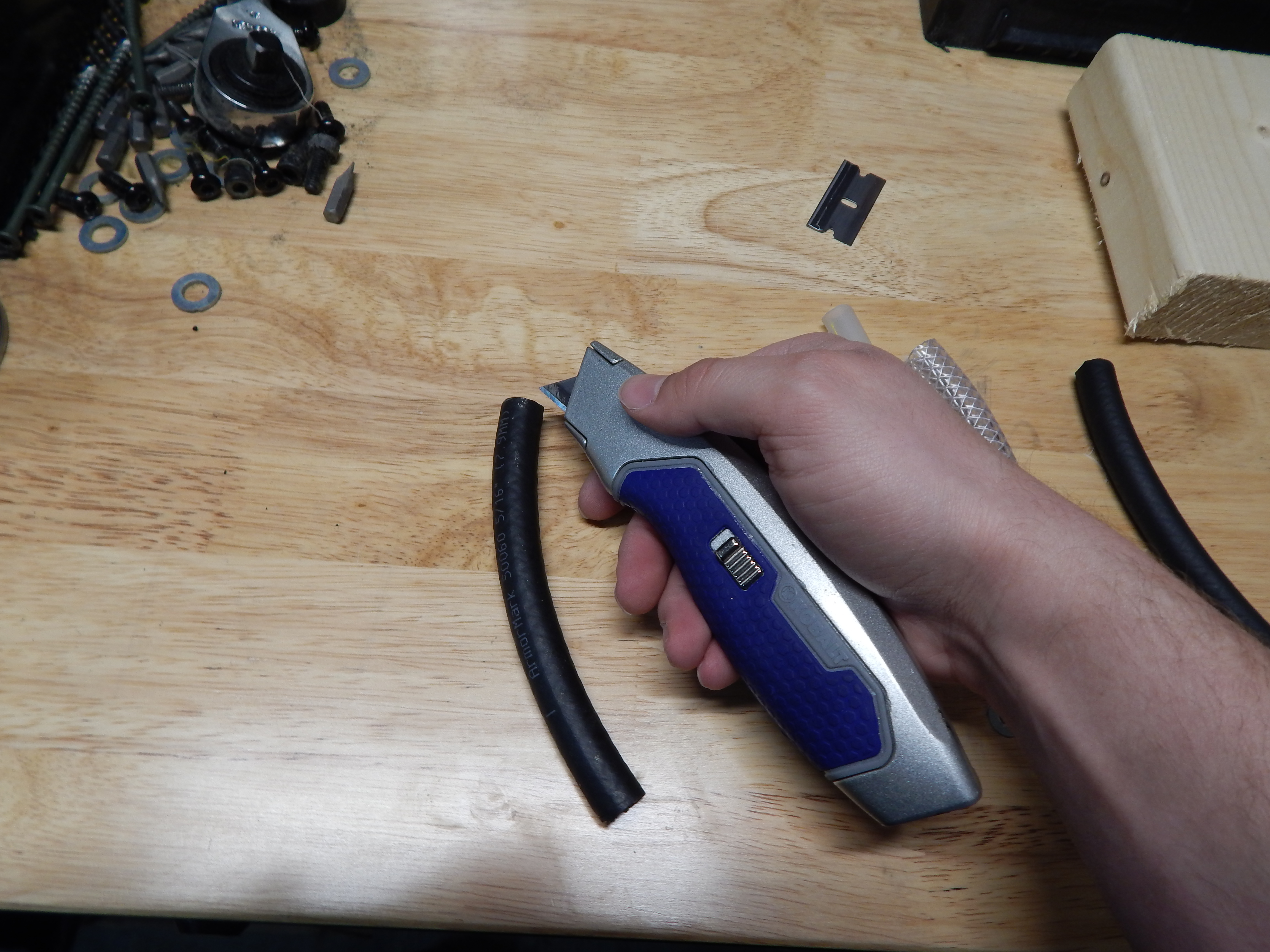
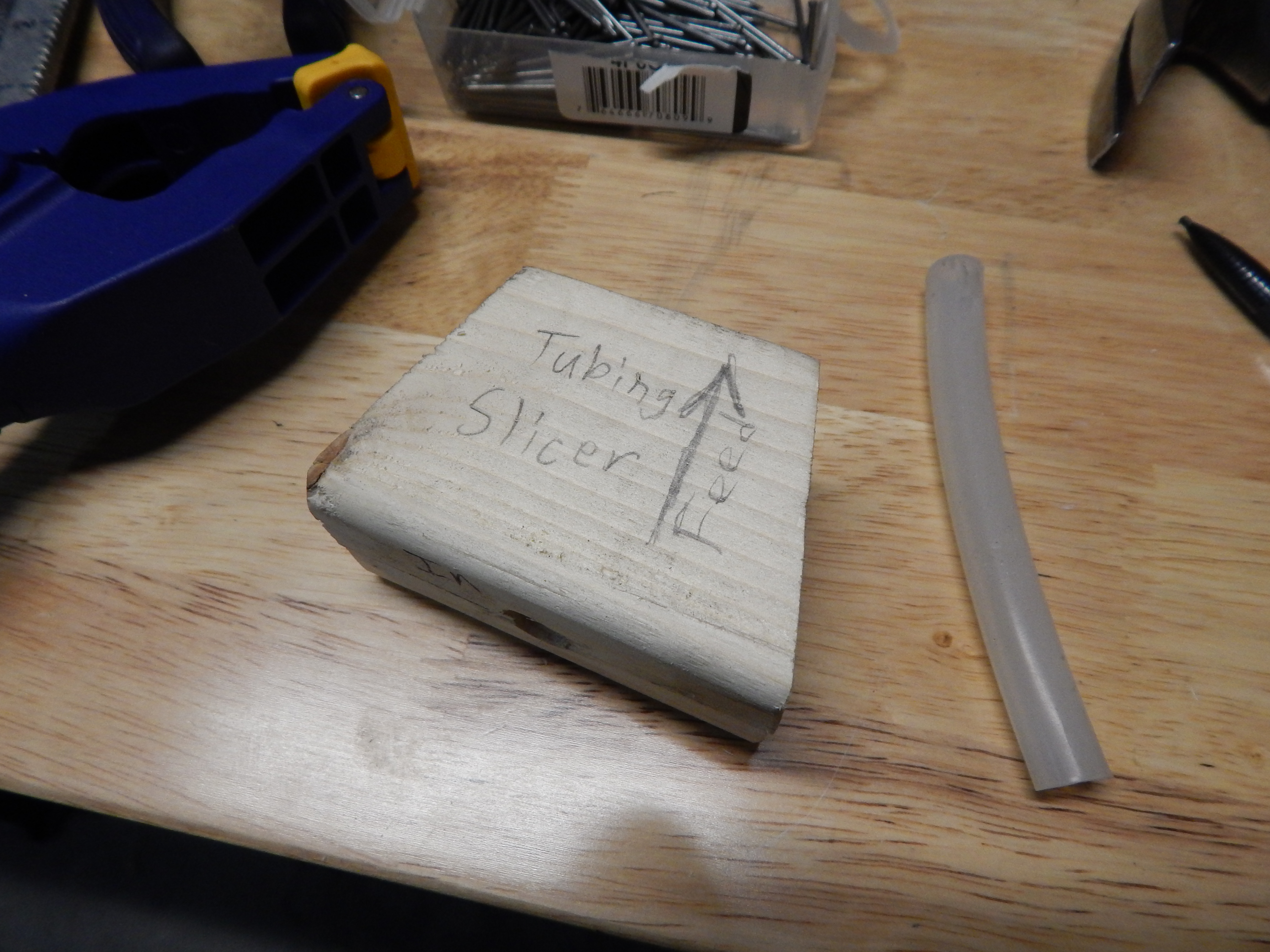
This tool is simple, easily made with scrap pieces, and has even more uses than I can currently devise. In any case, it is far safer and easier than trying to hold a narrow, round shape while cutting with a razor.
Comment with any other versions of this that are made.