Creating an HDPE Forming Stake
by flame_mistress in Circuits > Tools
5198 Views, 7 Favorites, 0 Comments
Creating an HDPE Forming Stake
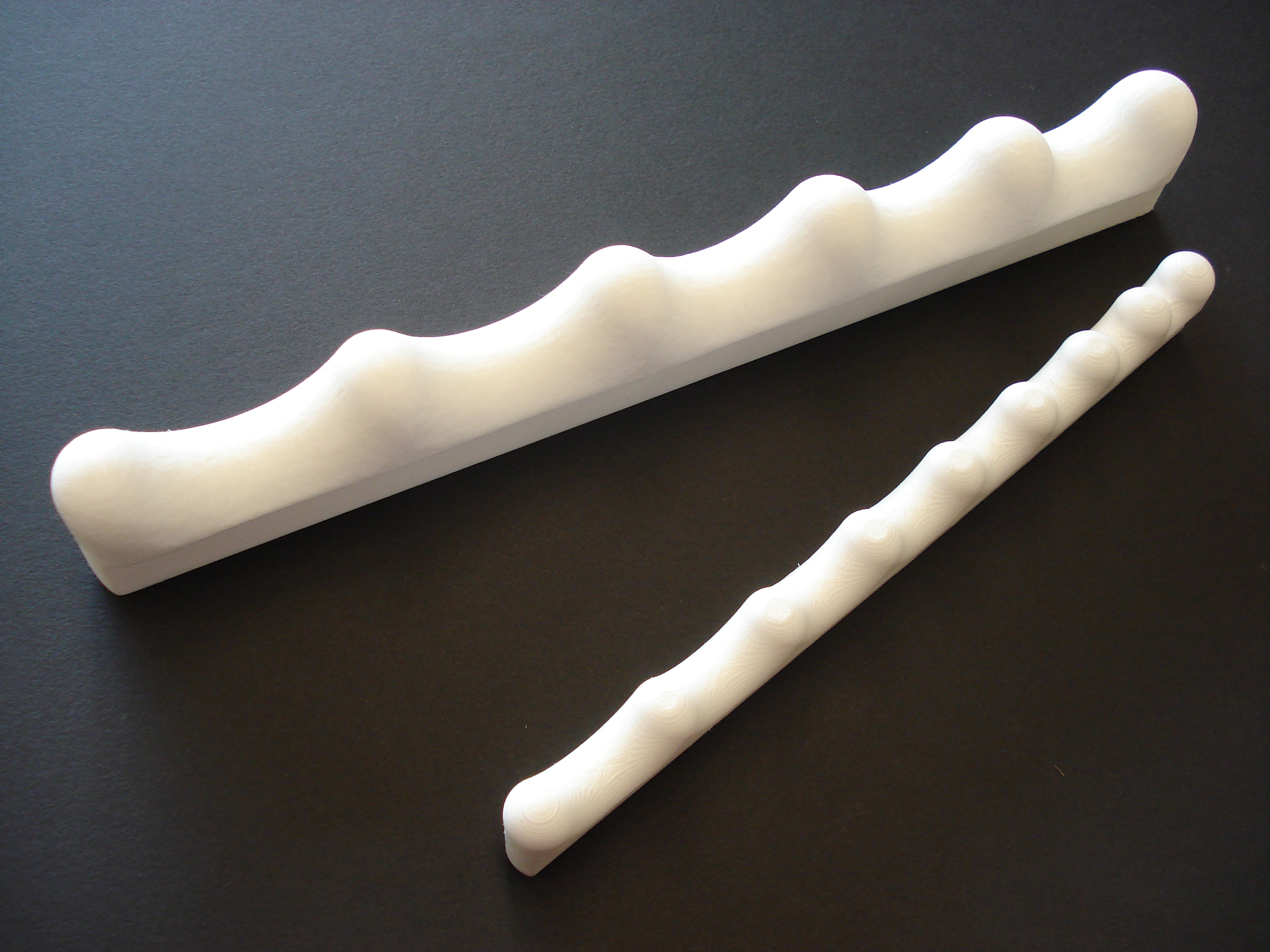
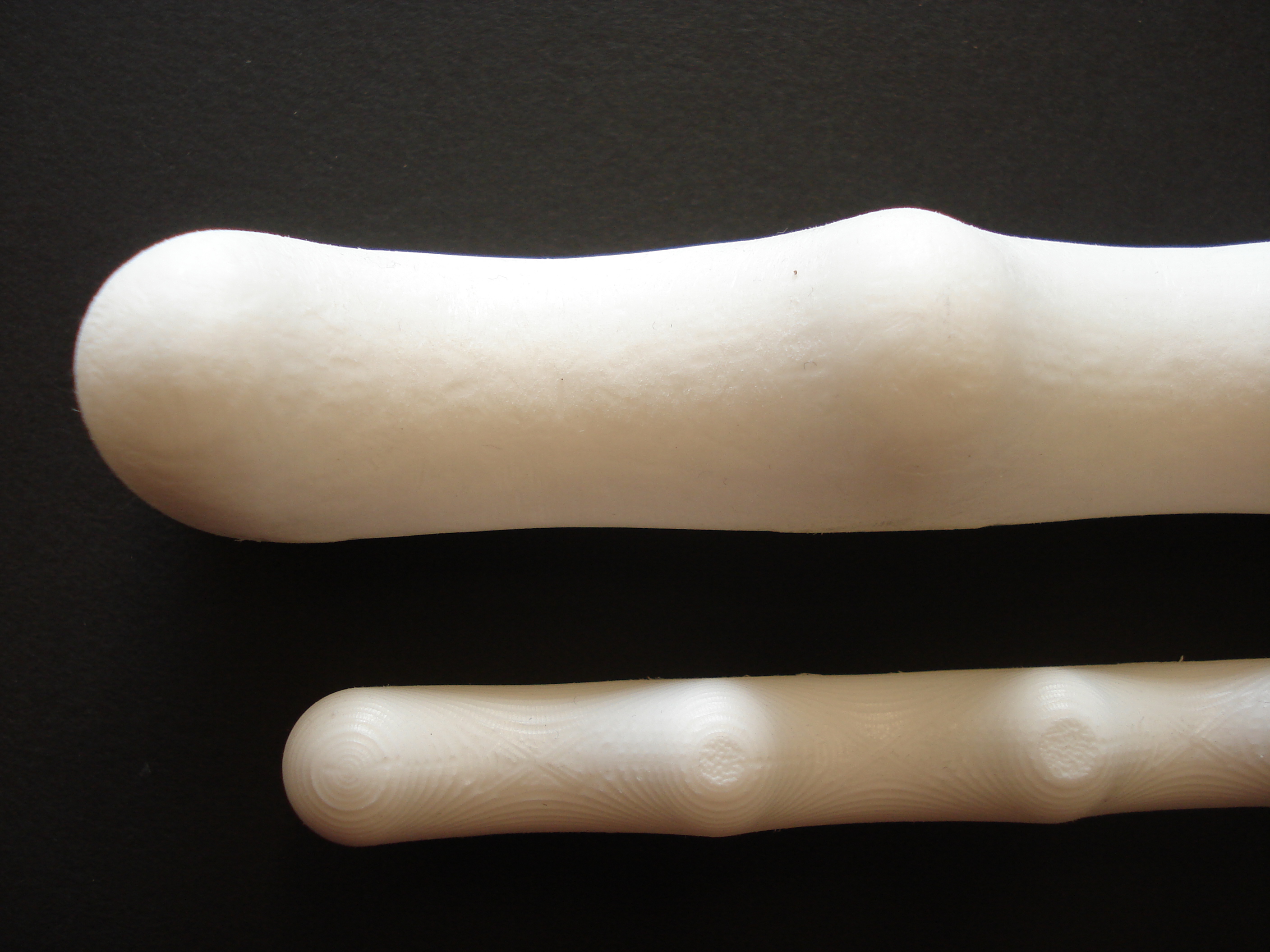
Materials:
- HDPE (10.055” x 1.5” x 0.983” minimum for larger stake; 7.59” x 1” x 0.5” minimum for smaller stake)
- 3D design software (I used AutoDesk Inventor)
- toolpath software (I used SprutCAM)
- USB stick
- appropriate bits for the CNC milling machine
- CNC milling machine (I used a Tormach)
- files and sandpaper for finishing
This forming stake is similar to one used in the jewelry industry for doing “anticlastic raising” (for more information on this topic, check this out, and go from there). I picked up a piece of scrap HDPE at Tap Plastics (Delrin would be best, but this was cheap), and decided I would try making my own. I made this project at the TechShop (www.techshop.ws) using their extensive software suite and the Tormach CNC milling machine.
1. Start by modeling the stake in your 3D design software. You can see the sketches that I started with in AutoDesk Inventor. I made two stakes, one that started with a 0.125” diameter “divot” and ended with a 1” diameter “divot”, for smaller projects, and one that started with a 1” diameter “divot” and ended with a 2” diameter “divot”, for larger projects.
2. Open the file with your toolpathing software and lay out the cuts. Keep in mind that you will need some reference point for each cut when you make the actual piece. To make sure you have this, start with the bottom cut, and cut to a depth just over ½ of the stake; this will form the side that will ultimately be held in your bench vise while you do your anticlastic raising. Flip the work piece over (bottom to top, but NOT left to right), load the bottom in the vise on the mill, and cut the lumpy top side (again, to a depth just over ½ of the stake).
For the larger stake I used the following cuts and tools:
Bottom side:
Roughing waterline with a 0.5” end mill.
Finishing waterline with a 0.5” conical mill with a 90 degree included angle.
Top side:
Roughing waterline with a 0.5” end mill.
Finishing drive with a 0.5” ball mill.
Finishing combine with a 0.5” ball mill.
For the smaller stake I used the following cuts and tools:
Bottom side:
Roughing waterline with a 0.5” end mill.
Finishing waterline with a 0.1975” conical mill with a 60 degree included angle.
Top side:
Roughing waterline with a 0.5” end mill.
Finishing drive along curve with a 0.25” ball mill.
Finishing combine with a 0.125” ball mill.
How much finishing work you want to do by hand will determine how small a mill you use on the final pass. In the photos, the larger stake has been finished with a file and sanded. The smaller stake has not been worked beyond the milling step.
3. Export the toolpaths through the postprocessor to get your G-code files.
4. Save them on your USB and transfer them to the CNC milling machine’s computer.
5. Following the procedures you learned in your Tormach SBU at the TechShop, cut your stakes....
Grab your hammers, and start making those spiculums and anticlastic forms that you’ve always wanted to make!
- HDPE (10.055” x 1.5” x 0.983” minimum for larger stake; 7.59” x 1” x 0.5” minimum for smaller stake)
- 3D design software (I used AutoDesk Inventor)
- toolpath software (I used SprutCAM)
- USB stick
- appropriate bits for the CNC milling machine
- CNC milling machine (I used a Tormach)
- files and sandpaper for finishing
This forming stake is similar to one used in the jewelry industry for doing “anticlastic raising” (for more information on this topic, check this out, and go from there). I picked up a piece of scrap HDPE at Tap Plastics (Delrin would be best, but this was cheap), and decided I would try making my own. I made this project at the TechShop (www.techshop.ws) using their extensive software suite and the Tormach CNC milling machine.
1. Start by modeling the stake in your 3D design software. You can see the sketches that I started with in AutoDesk Inventor. I made two stakes, one that started with a 0.125” diameter “divot” and ended with a 1” diameter “divot”, for smaller projects, and one that started with a 1” diameter “divot” and ended with a 2” diameter “divot”, for larger projects.
2. Open the file with your toolpathing software and lay out the cuts. Keep in mind that you will need some reference point for each cut when you make the actual piece. To make sure you have this, start with the bottom cut, and cut to a depth just over ½ of the stake; this will form the side that will ultimately be held in your bench vise while you do your anticlastic raising. Flip the work piece over (bottom to top, but NOT left to right), load the bottom in the vise on the mill, and cut the lumpy top side (again, to a depth just over ½ of the stake).
For the larger stake I used the following cuts and tools:
Bottom side:
Roughing waterline with a 0.5” end mill.
Finishing waterline with a 0.5” conical mill with a 90 degree included angle.
Top side:
Roughing waterline with a 0.5” end mill.
Finishing drive with a 0.5” ball mill.
Finishing combine with a 0.5” ball mill.
For the smaller stake I used the following cuts and tools:
Bottom side:
Roughing waterline with a 0.5” end mill.
Finishing waterline with a 0.1975” conical mill with a 60 degree included angle.
Top side:
Roughing waterline with a 0.5” end mill.
Finishing drive along curve with a 0.25” ball mill.
Finishing combine with a 0.125” ball mill.
How much finishing work you want to do by hand will determine how small a mill you use on the final pass. In the photos, the larger stake has been finished with a file and sanded. The smaller stake has not been worked beyond the milling step.
3. Export the toolpaths through the postprocessor to get your G-code files.
4. Save them on your USB and transfer them to the CNC milling machine’s computer.
5. Following the procedures you learned in your Tormach SBU at the TechShop, cut your stakes....
Grab your hammers, and start making those spiculums and anticlastic forms that you’ve always wanted to make!