Creating Custom Side Panels for a Youth Robotics Team
by joebob007 in Workshop > CNC
1053 Views, 3 Favorites, 0 Comments
Creating Custom Side Panels for a Youth Robotics Team
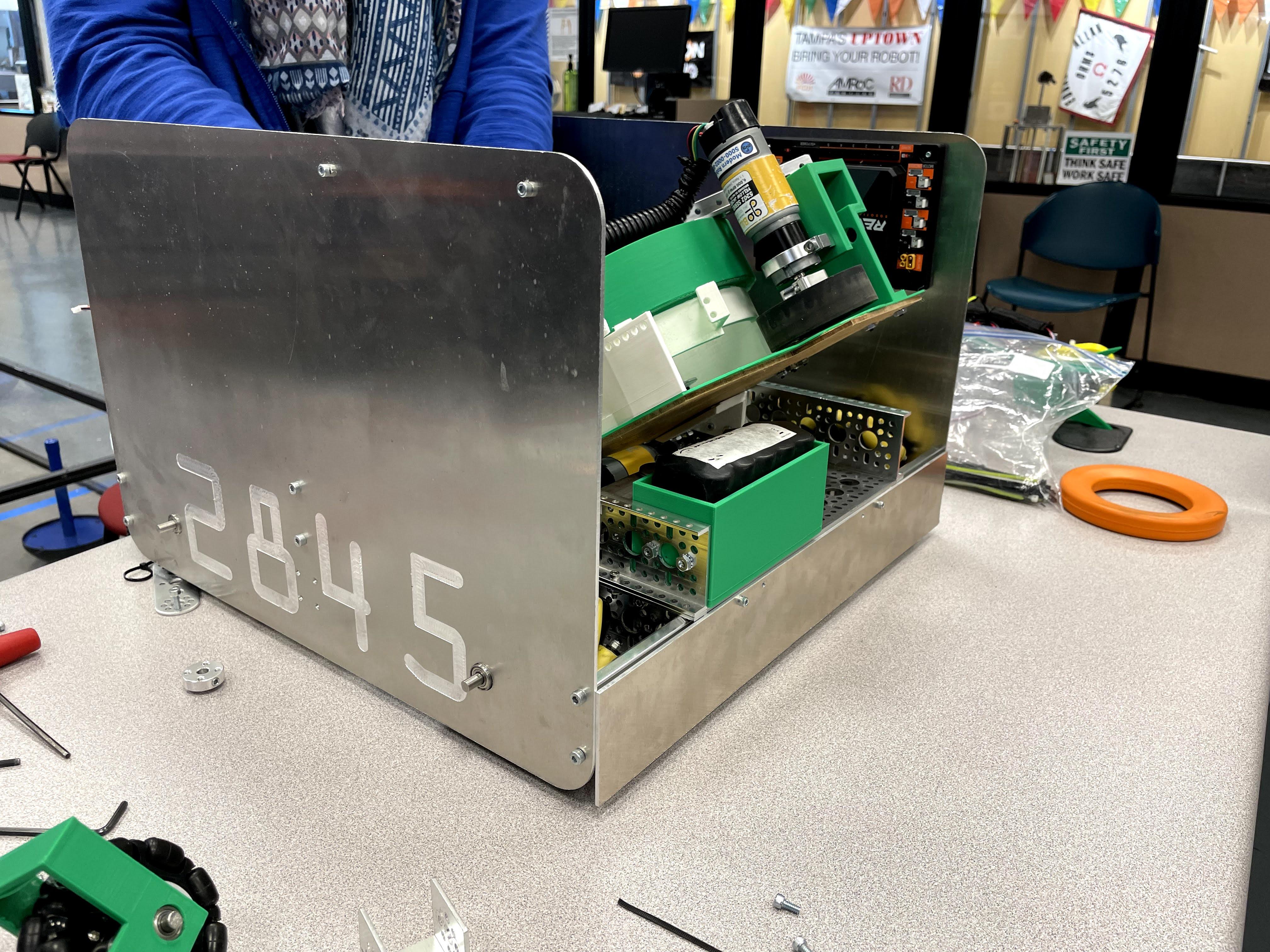
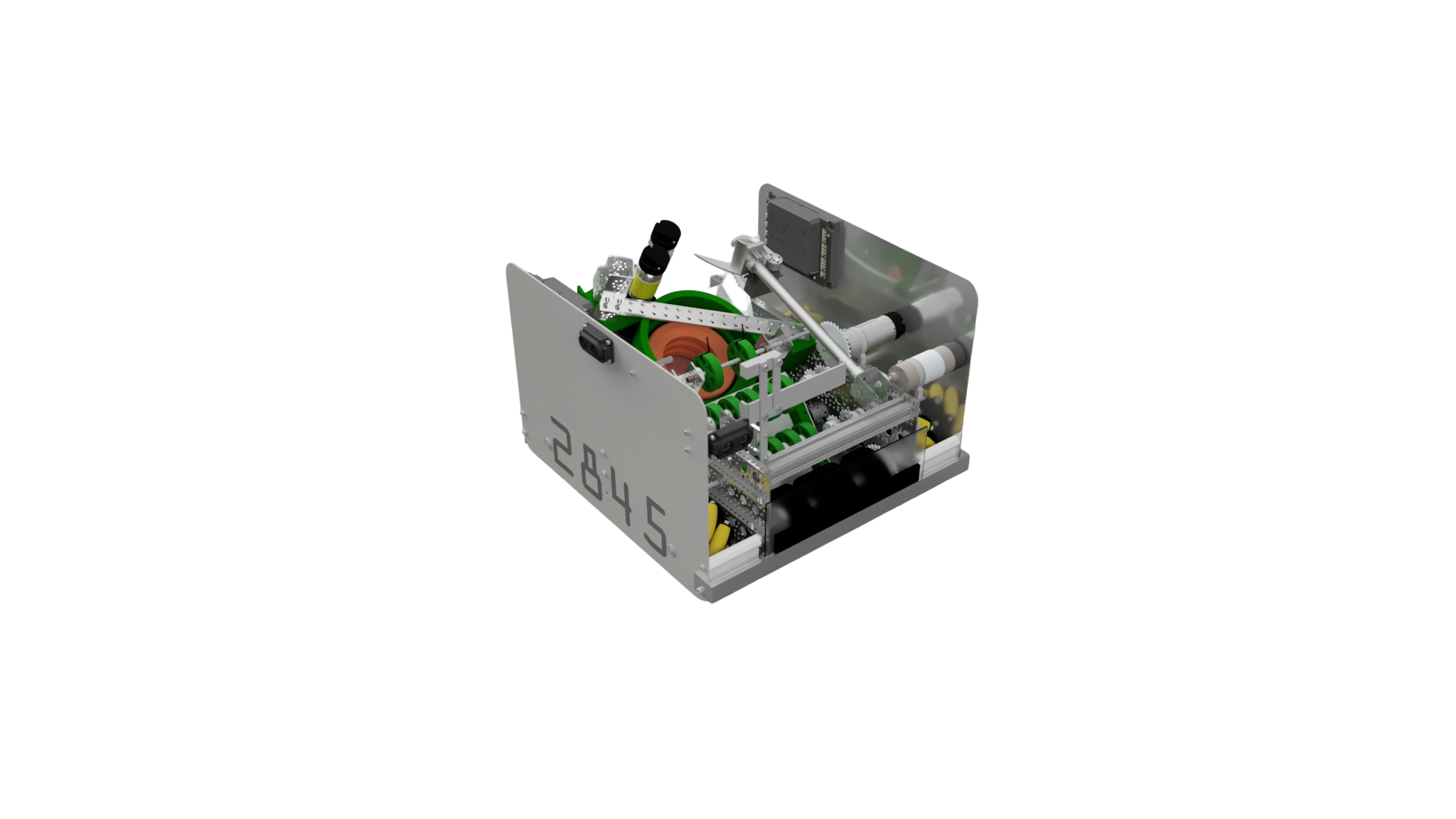
This Instructable will document the journey of Robotics Team, 2845 Team Duct Tape, designing and making custom side panels for their robot. There will be tips and tricks for others learning how to use a CNC machine.
What is a CNC machine?
A CNC machine, or Computer Numerically Controlled Machine is one that helps assist the user in producing custom parts. In a nutshell, a CNC machine is the opposite of a 3d printer. 3D printers are an example of additive manufacturing, rather CNC machines are an example of subtractive manufacturing. Think of a CNC machine as a machine that has a drill that can move in both the x and y axis, but also the z axis.
What is required to create a part in a CNC machine?
To create a part in a CNC machine, you must first have an idea of what you want to create. For example lets use what this robotics team wanted to do. They wanted to create a flat panel with their custom dimensions and had their team numbers edged in. So the first step is to pick a CAD (Computer Aided Design), of the part you want to create. There are many softwares out there, for example there is Autodesk Inventor, Fusion360, solid works, and many more. After designing the part you will want to open the part in the CAM portion of the software.
What are my credentials to teach you how to use a CNC machine?
I am certified in Autodesk inventor, Fusion 360, and have hundreds of hours of training using these softwares. About two years ago I started learning about CAM. So I am not really a expert on using CNC machines but feel that my advice will help other users of this awesome type of manufacturing. If you need the help of a professional, I would recommend visiting local maker-spaces, or machine shops where there may be experts to help you.
Supplies
To create items using a CNC machine, you will need the following items:
- Your choice of material for the final product
- Spindle, size based on criteria from your part
- Screws, to temporarily mount your material to the bed of the machine
- Vacuum, to clean up all the mess
- Laptop/Desktop to design and export your design to g-code
Designing Your Part in CAD
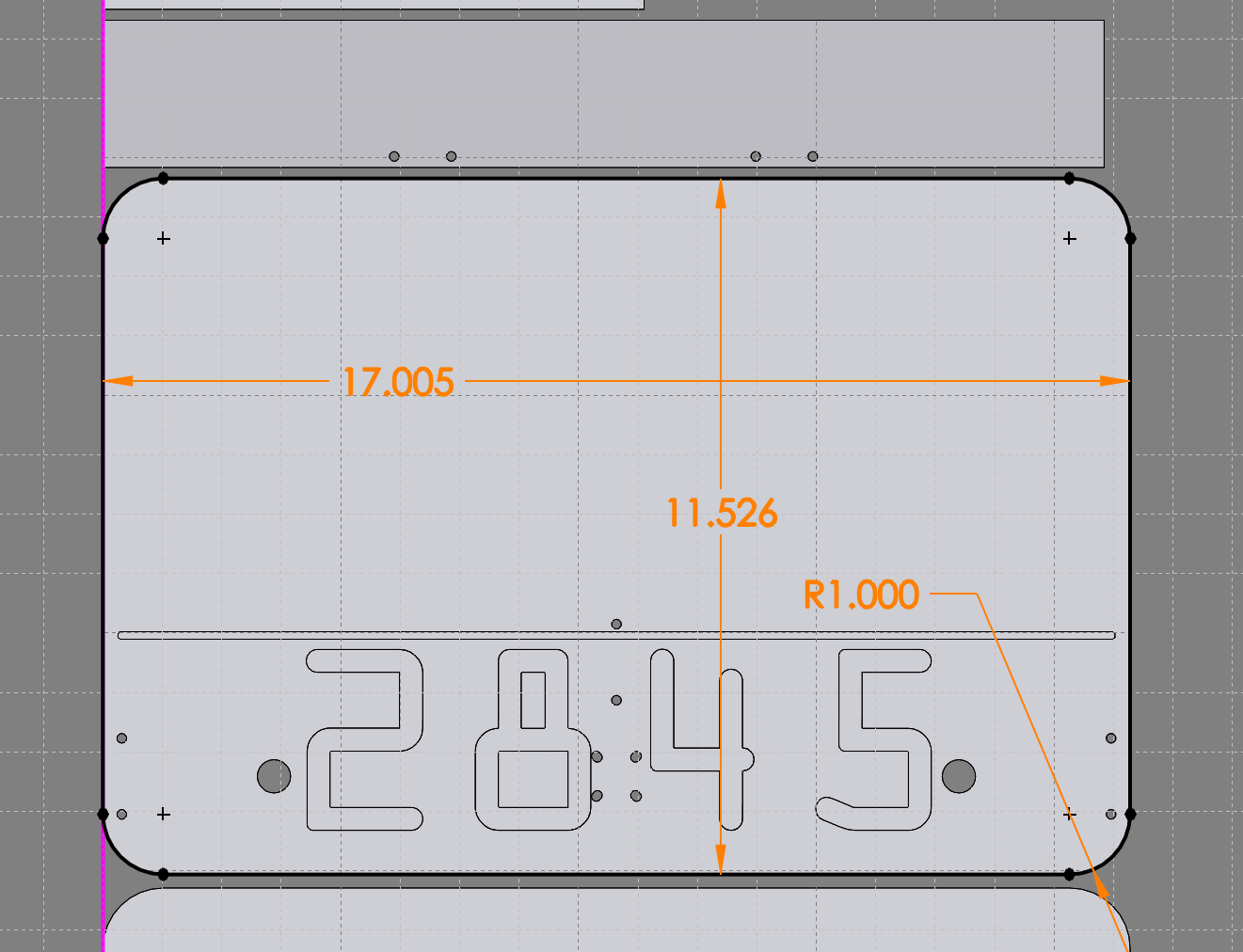
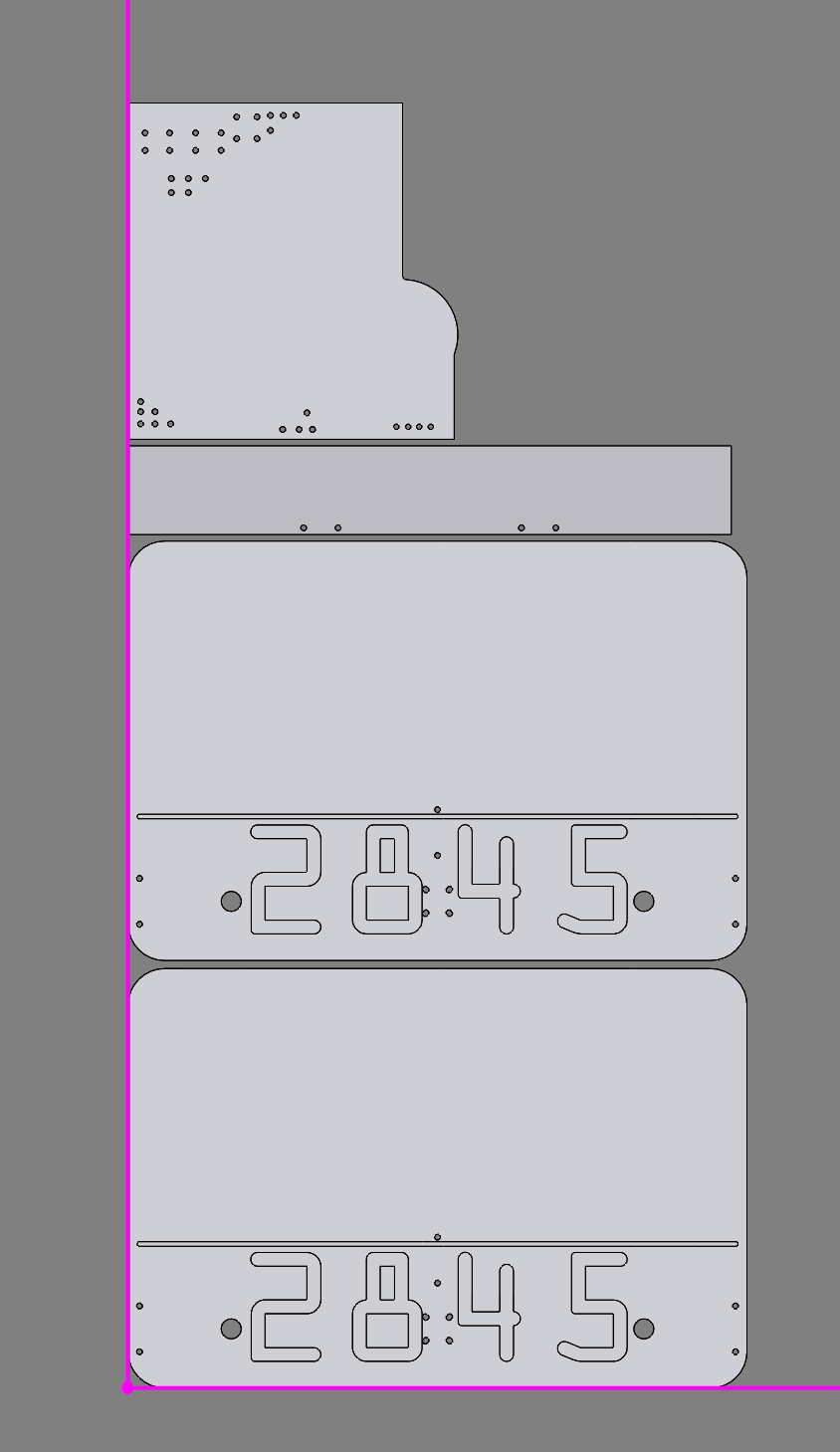
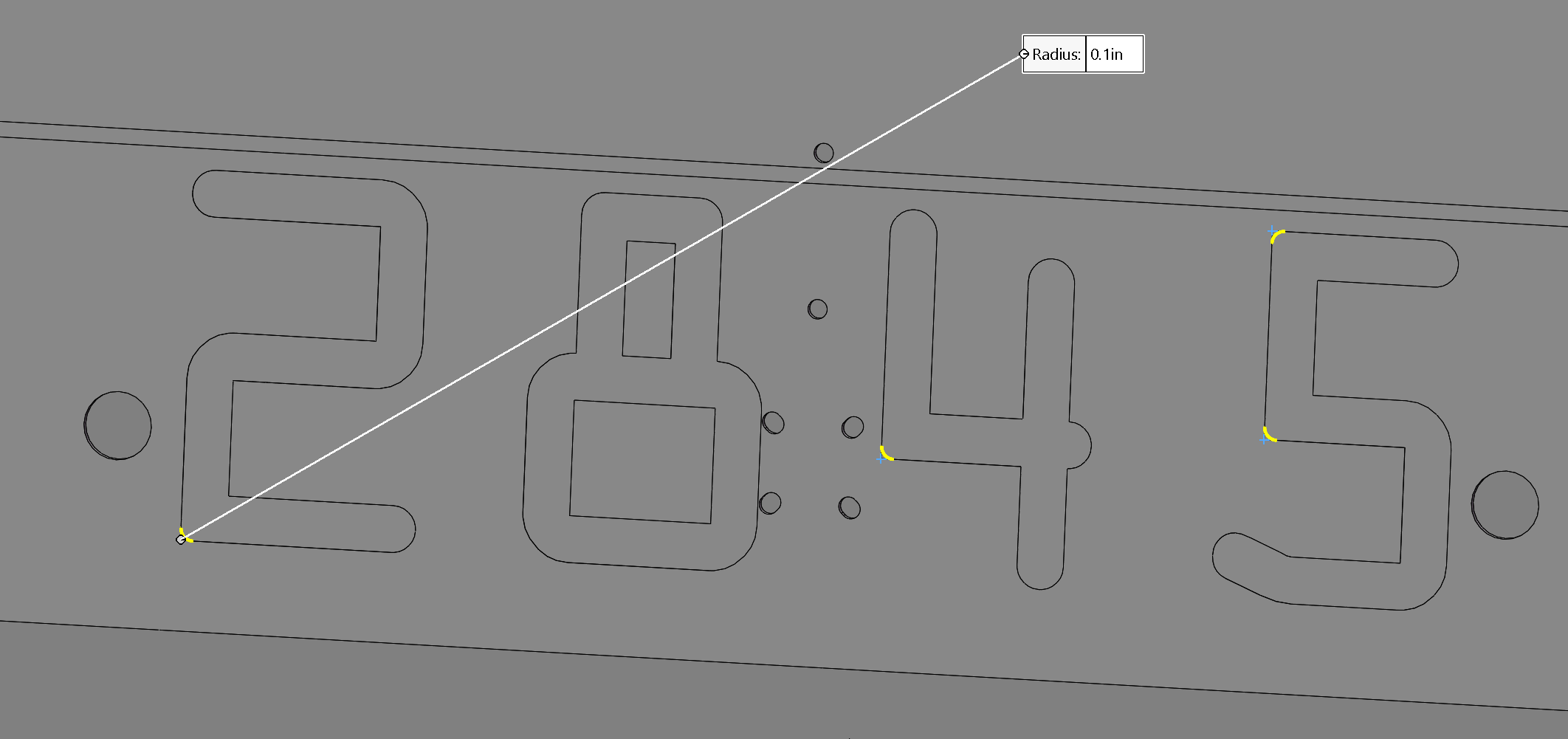
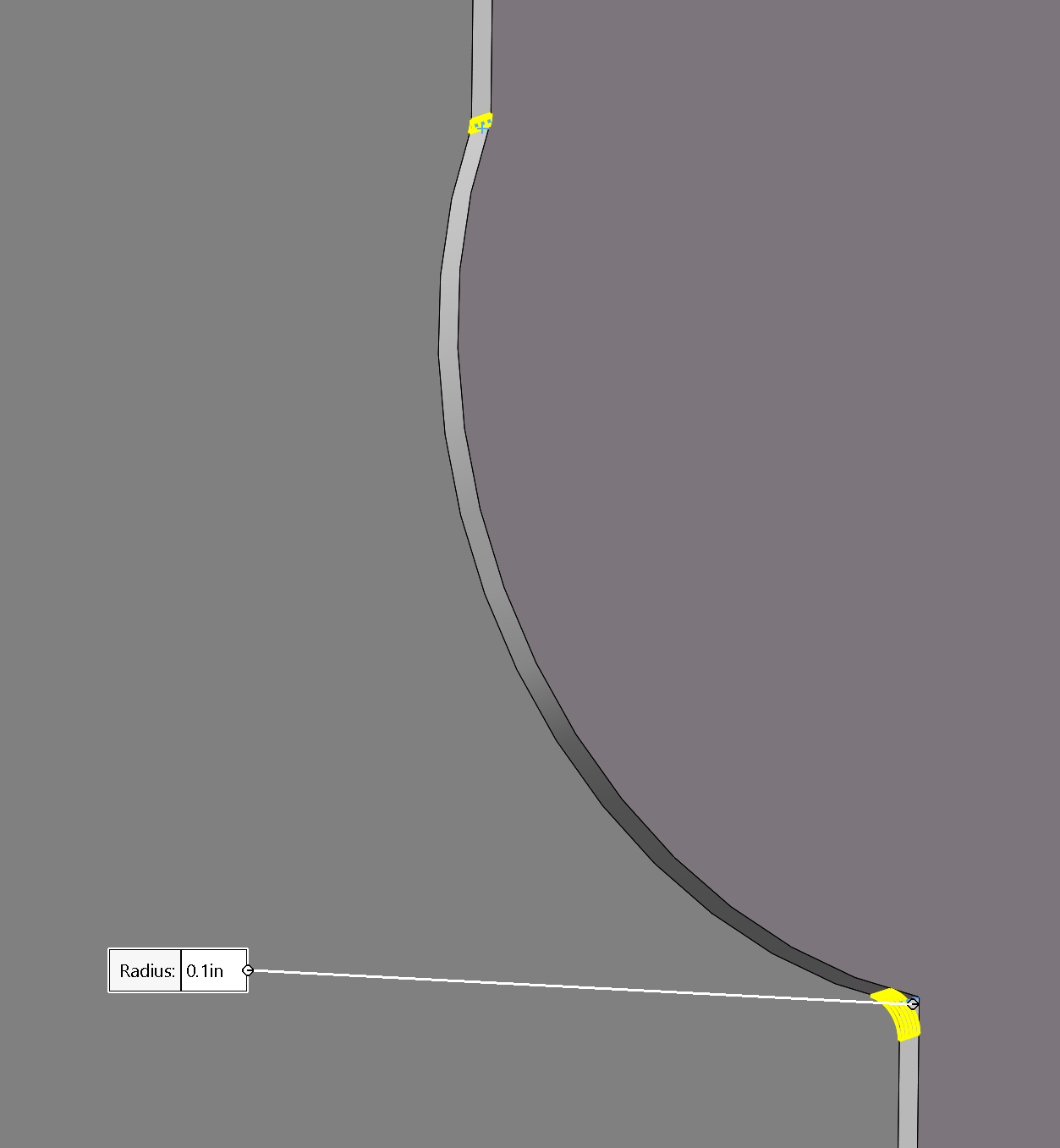
When designing your part in CAD, please make sure that you keep your part as simplistic as possible. This will lead to a machined part with the possibility of less flaws. Another thing to consider when designing your part is that if you have a combination of large and small items that you are removing from the part, then you will need to use a smaller spindle or you will have to run it again with the larger spindle but it will have to use a different program. Other than that you can be as creative as you want. in the pictures above this team started off designing their part in fusion 360, they found out that for their spindle size, the radius of each corner would have to be 1 inch. They also had their team numbers edged in since they went with a .08 in sheet of aluminum. So running your part in a simulated environment to see how the machine will cut the part is very helpful. it allows for you to see areas in your design that will have to be modified in order to fabricate your part. Then you will export the code to your CNC machine.
Setting Up the Machine
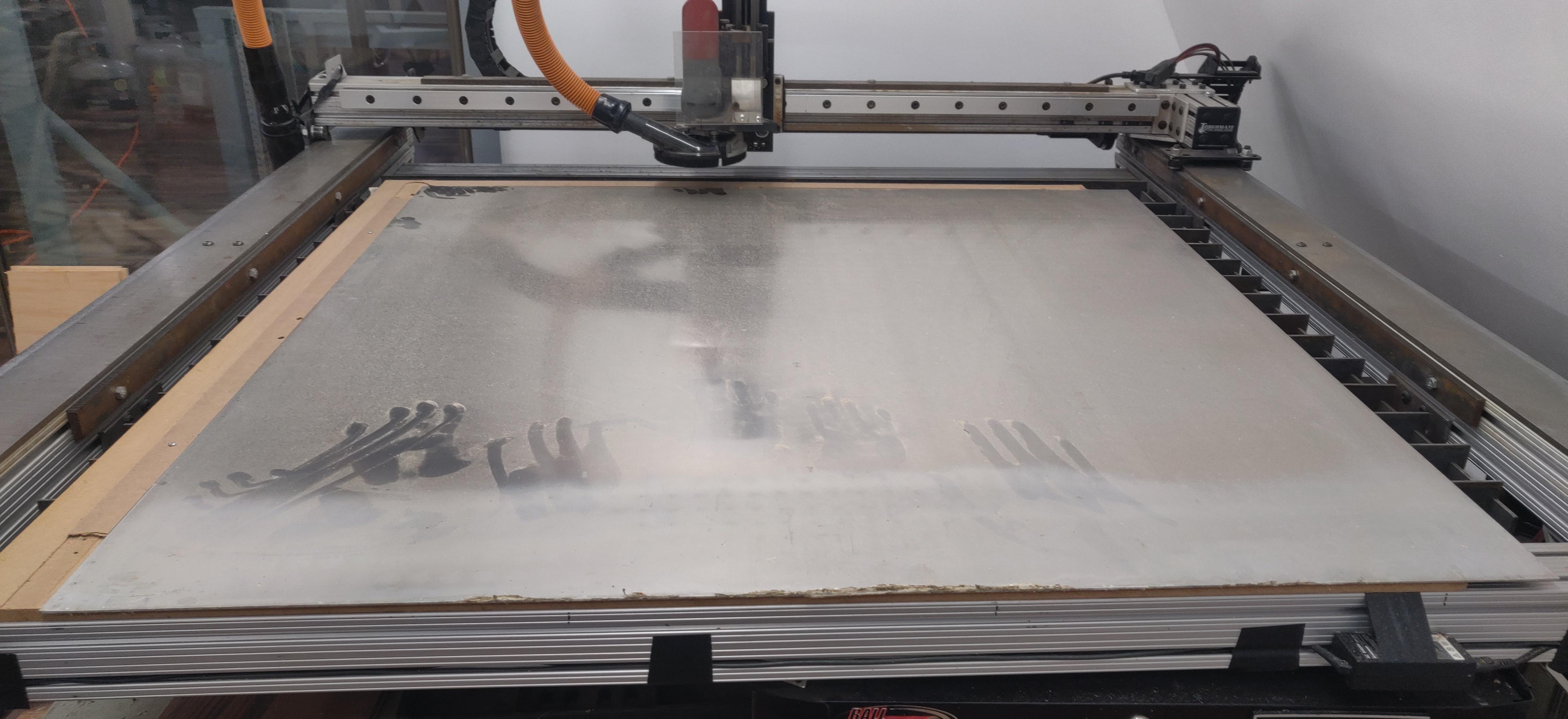

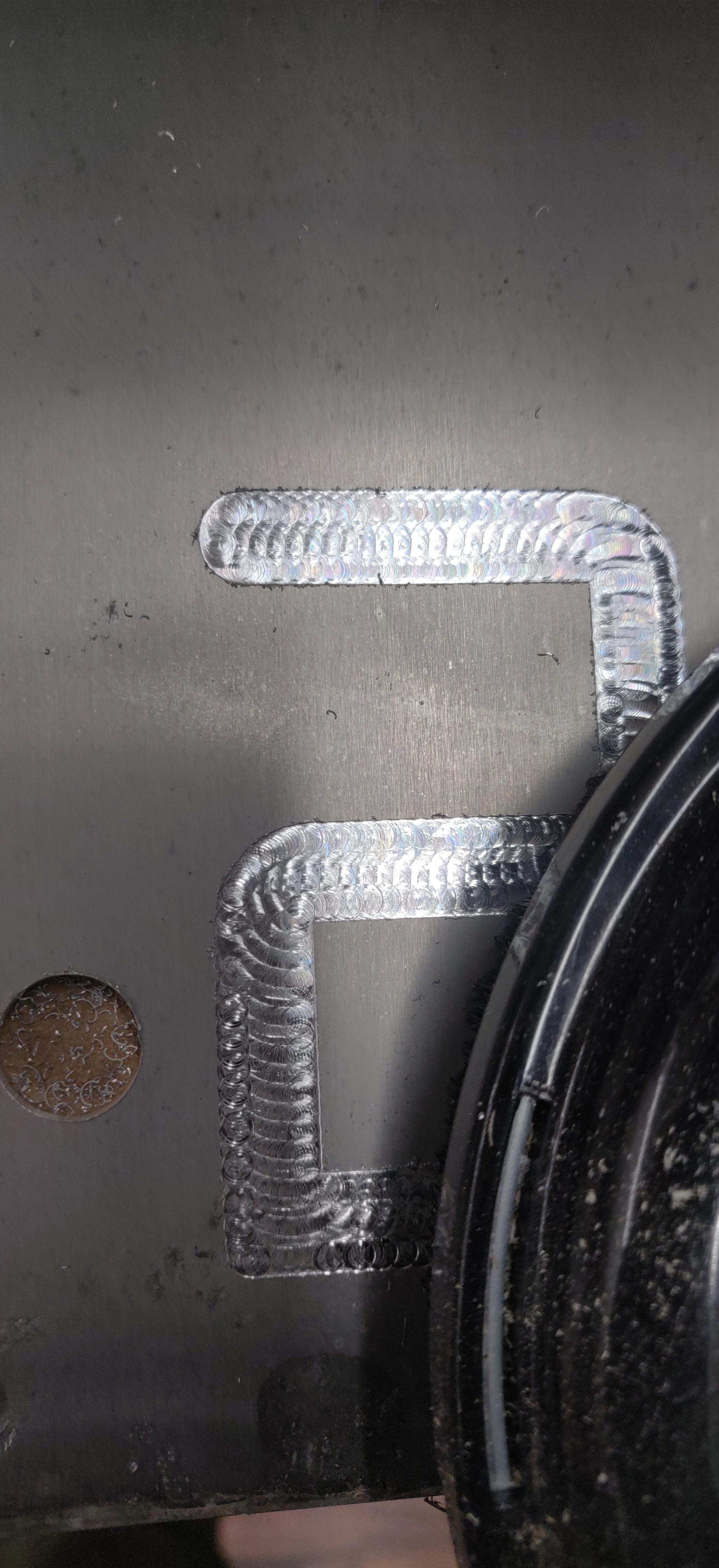
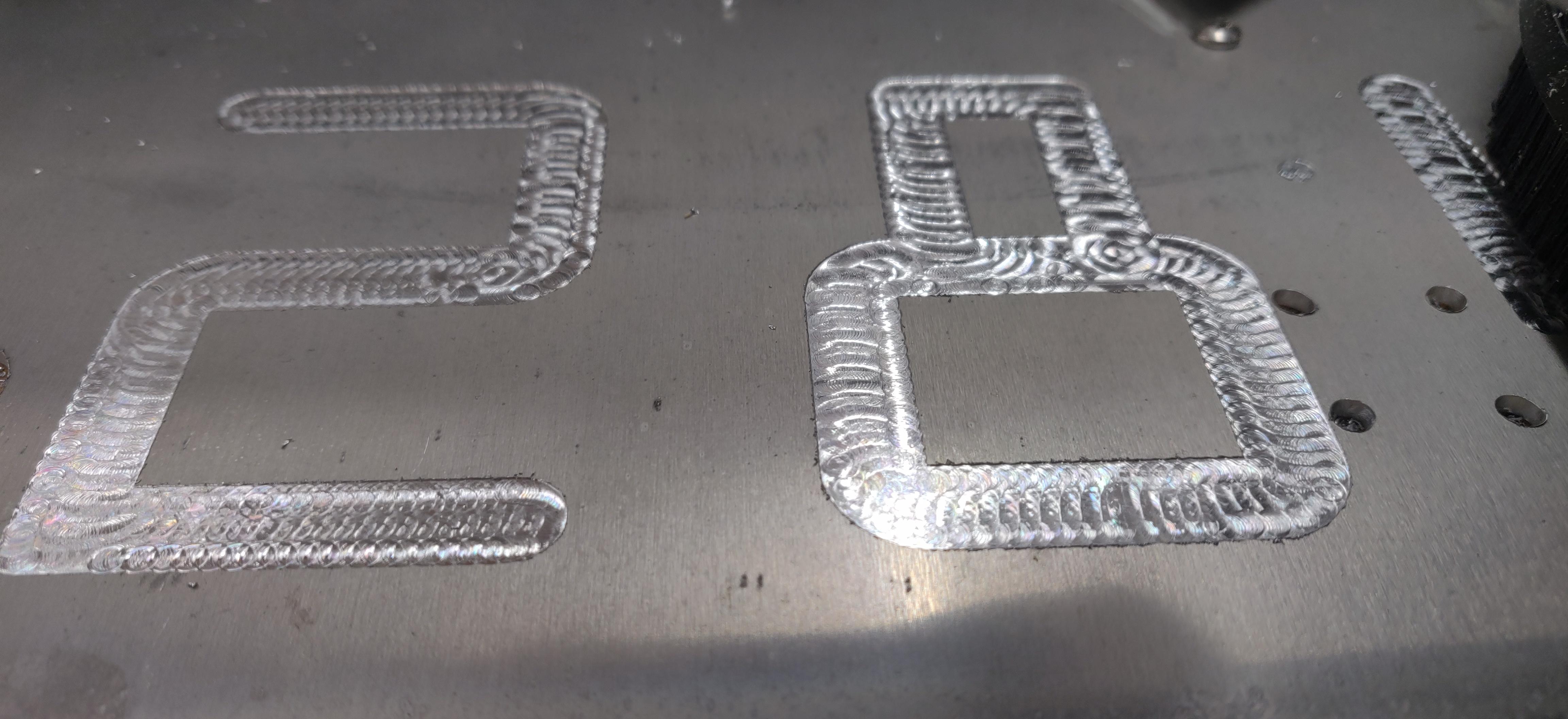
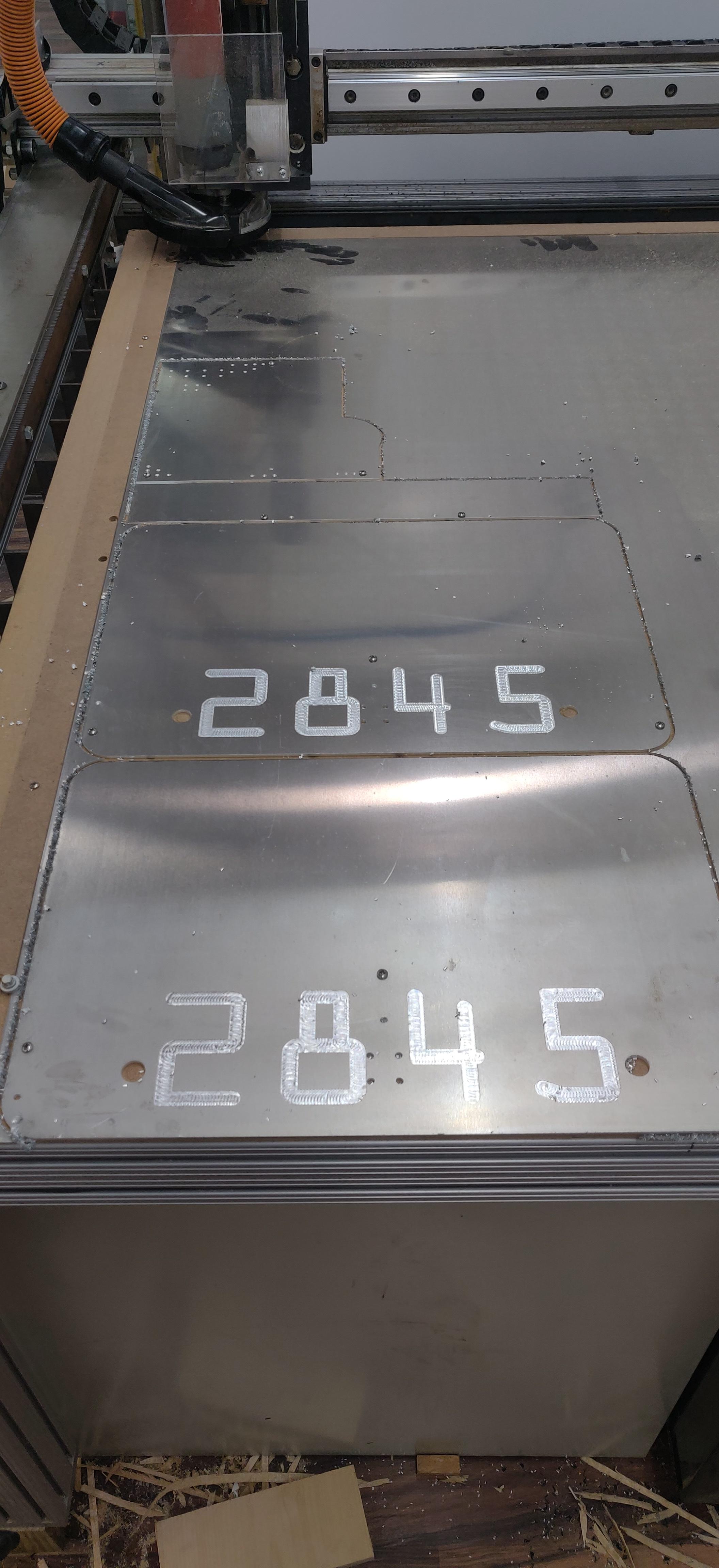
So something to be aware of before you begin is that these machines can either work relative or absolute on the work bed. So it is important to make sure that you have your sheet of material and have it start in the corner that you had your design start in. Another thing that you should do is either create a frame around sheet of material or drill into each of the four corners so the sheet can't move. Make sure that whichever way you choose to secure the sheet down doesn't interfere with the CNC machine while it is moving. So once these steps are done, insert your spindle to the machine and begin the machining process. In the teams example, they secured their sheet of aluminum by drilling 1 screw into each corner in a way that wouldn't interfere with the machine's movements. Their parts came out amazing. The only issue they had with their parts was that the ball-bearing holes were a bit too small, which could be a result of the cad being slightly off or the tolerance wasn't large enough when machining it. So they had drill out the holes bigger, other than that they had no issues. For the teams first time using this type of manufacturing, it was very impressive. They have said that they want to transition some of their 3d printed parts to aluminum parts using a CNC router.