CNC Machined Guitar Bridge - Made at Techshop
by workislove in Workshop > CNC
14508 Views, 67 Favorites, 0 Comments
CNC Machined Guitar Bridge - Made at Techshop
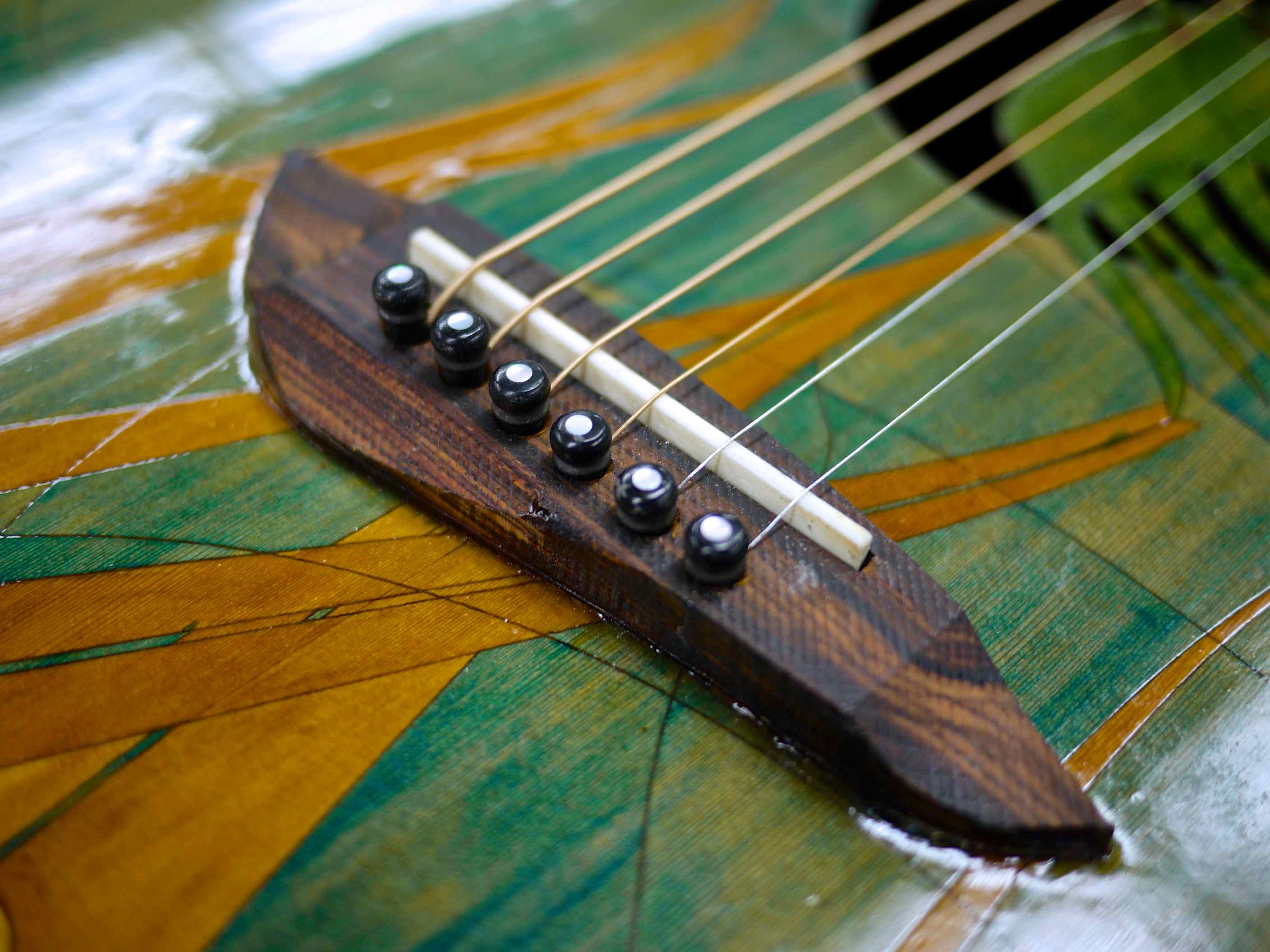
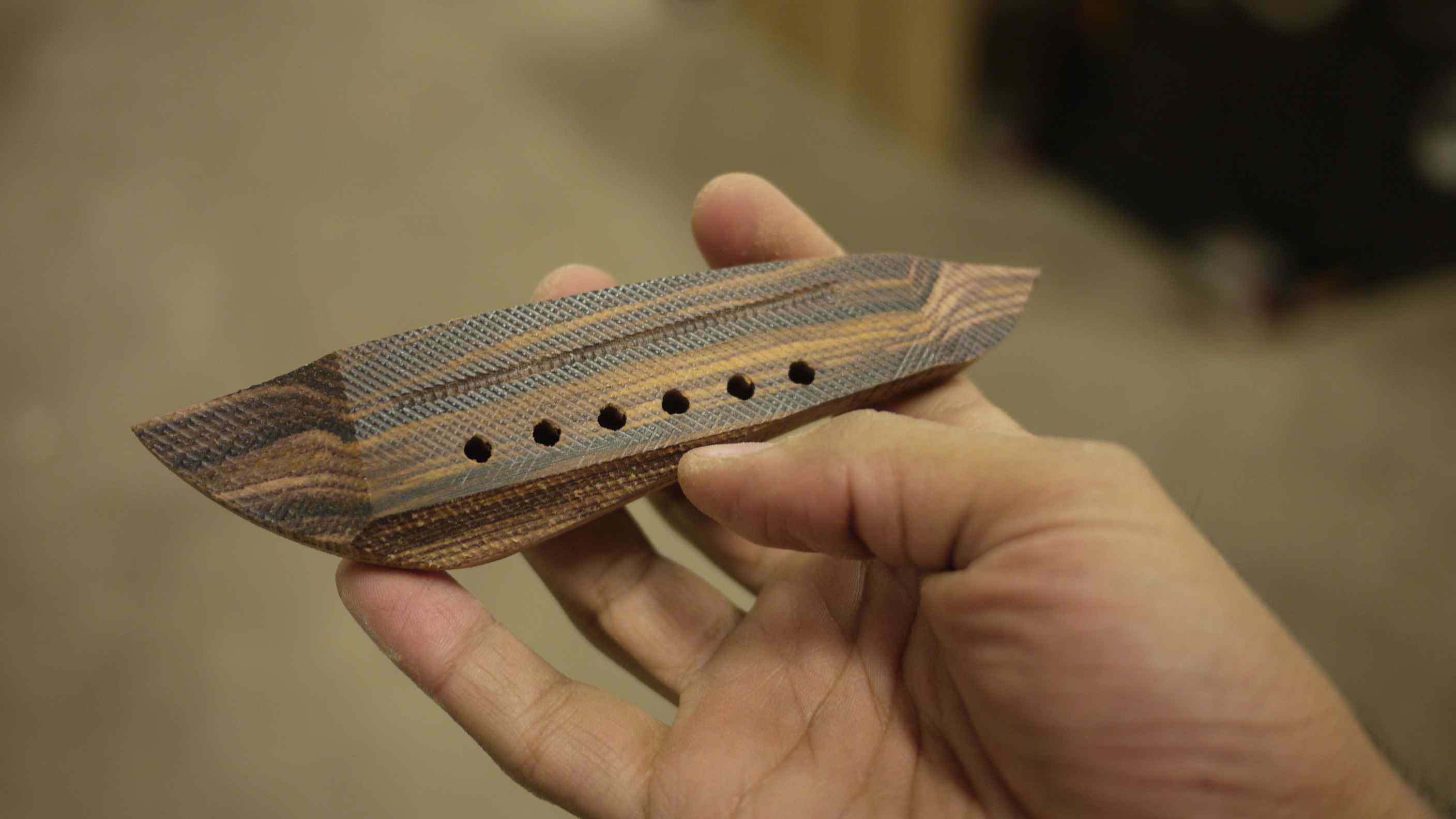
In this instructable I will show you how I made the bridge base for my carbon fiber acoustic guitar using the ShopBot CNC machine and software available at Techshop.
I designed the bridge based on the signature bridge of Bashkin Guitars, with some small modifications. I copied the bridge slot and pinhole layout from another student in my workshop. I've included the .STL 3D model of my bridge, as well as a 2D tracing of the shape in the photos.
You definitely don't need access to a CNC machine to make a nice bridge. I've found many discussions online about how to make bridges with hand tools and traditional routers. There are also many good books detailing the traditional process of building a guitar, including bridge construction. One book I found at my local library that helped me understand and install the bridge was Build Your Own Acoustic Guitar - by Jonathan Kinkead.
I designed the bridge based on the signature bridge of Bashkin Guitars, with some small modifications. I copied the bridge slot and pinhole layout from another student in my workshop. I've included the .STL 3D model of my bridge, as well as a 2D tracing of the shape in the photos.
You definitely don't need access to a CNC machine to make a nice bridge. I've found many discussions online about how to make bridges with hand tools and traditional routers. There are also many good books detailing the traditional process of building a guitar, including bridge construction. One book I found at my local library that helped me understand and install the bridge was Build Your Own Acoustic Guitar - by Jonathan Kinkead.
Disclaimer:
Before I get started, I want to say that I am NOT an expert luthier (stringed instrument maker). I tried my best to do my own research, but only time will tell if I was successful. If you choose to make your own guitar, please do your own research using professional guides. There are amateur luthier communities online, as well as good books, such as the one I mentioned above.Downloads
Tools and Materials
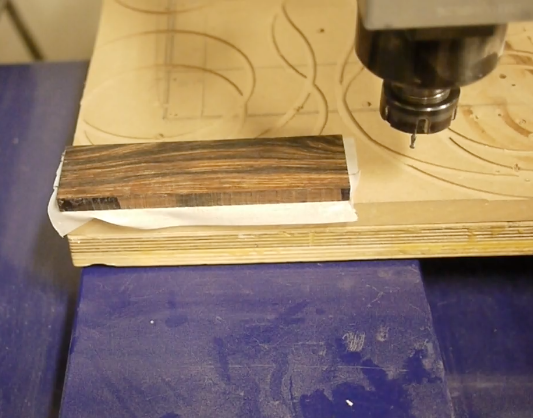
Tools & Software used
- Shopbot Buddy with 1/8" ball endmill
- Autodesk Inventor
- Vectric Cut 3D
Materials used
- Cocobolo bridge blank. Can be any piece of hardwood, mine measures 16.5 cm X 3.8 cm X 11.1 cm.
- Bone saddle
-
Ebony pins
- Blank, pin and saddle bought from Luthiers Mercantile International
- Double sided carpet tape
Design the Bridge - Drawing / Tracing
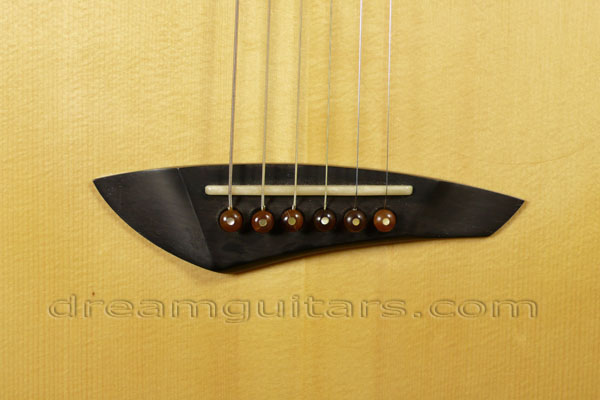
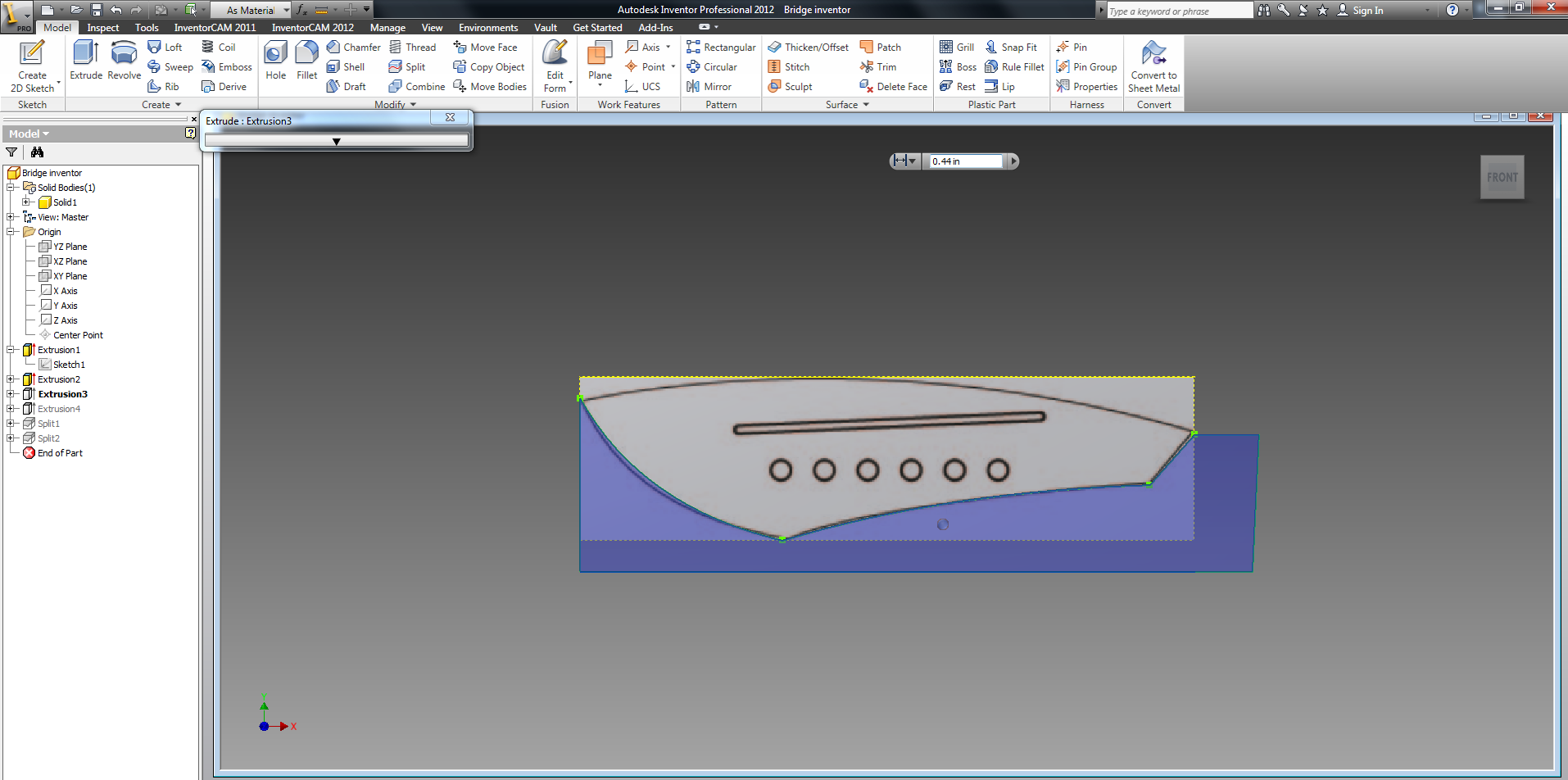
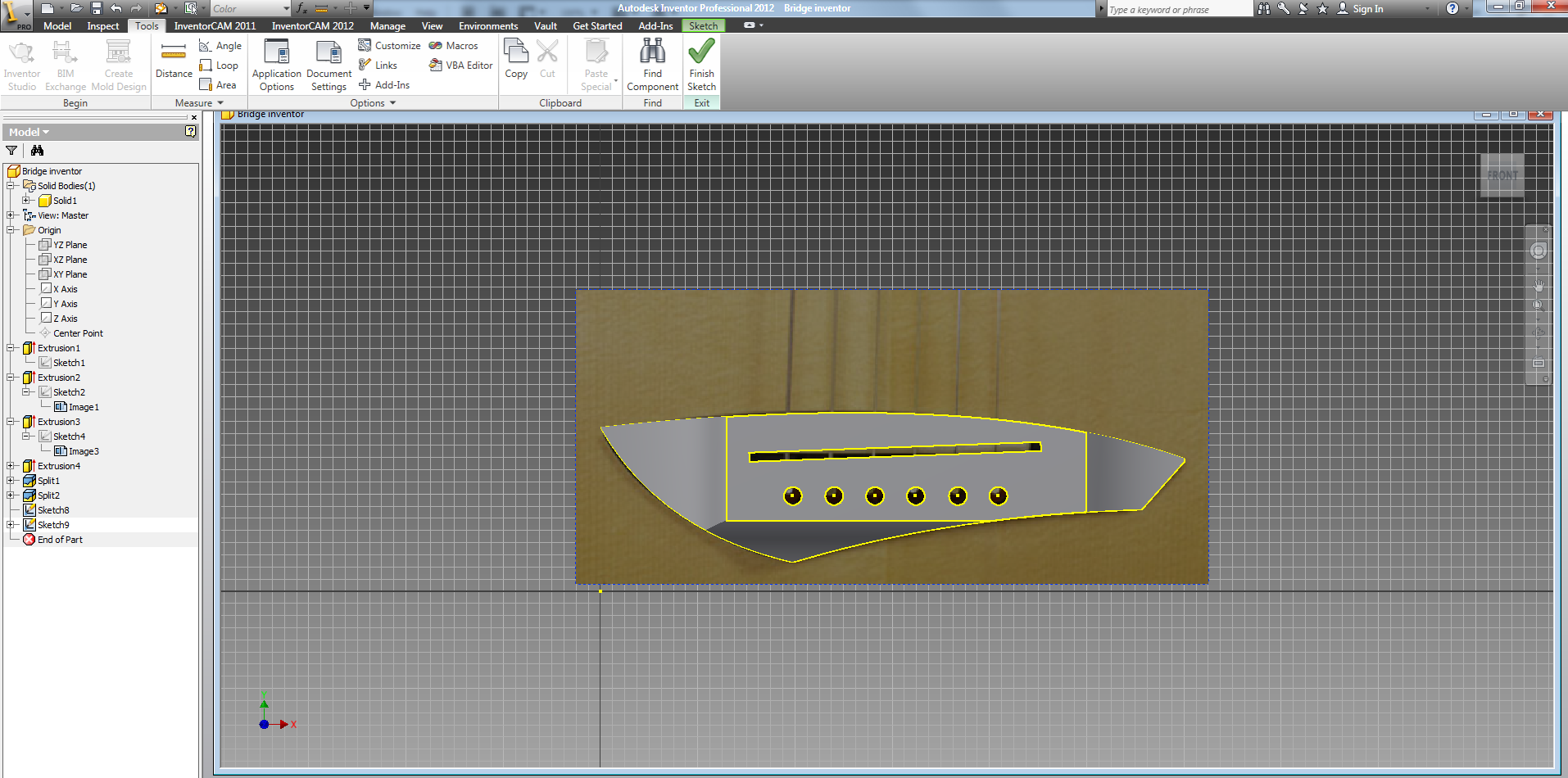
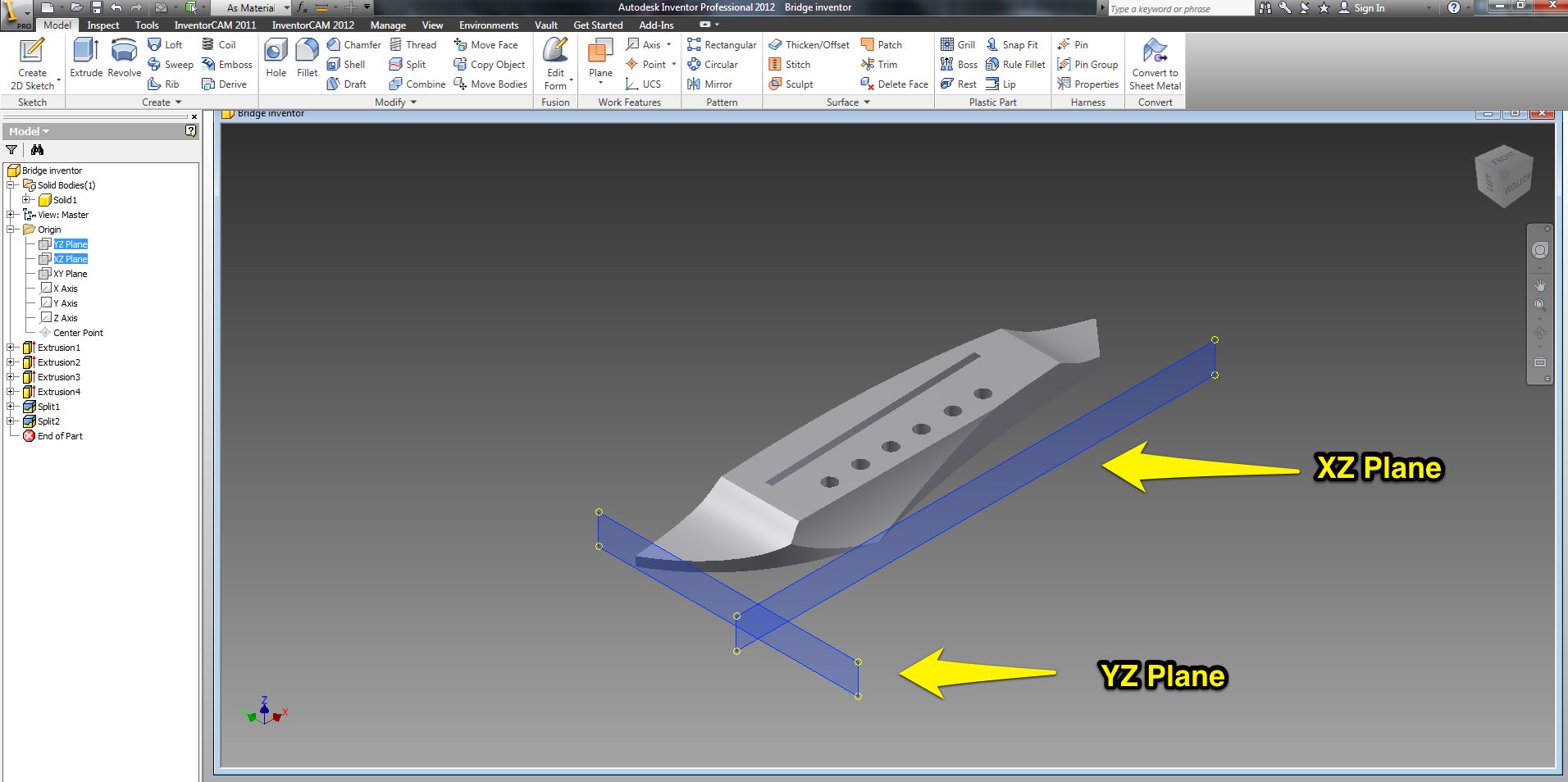
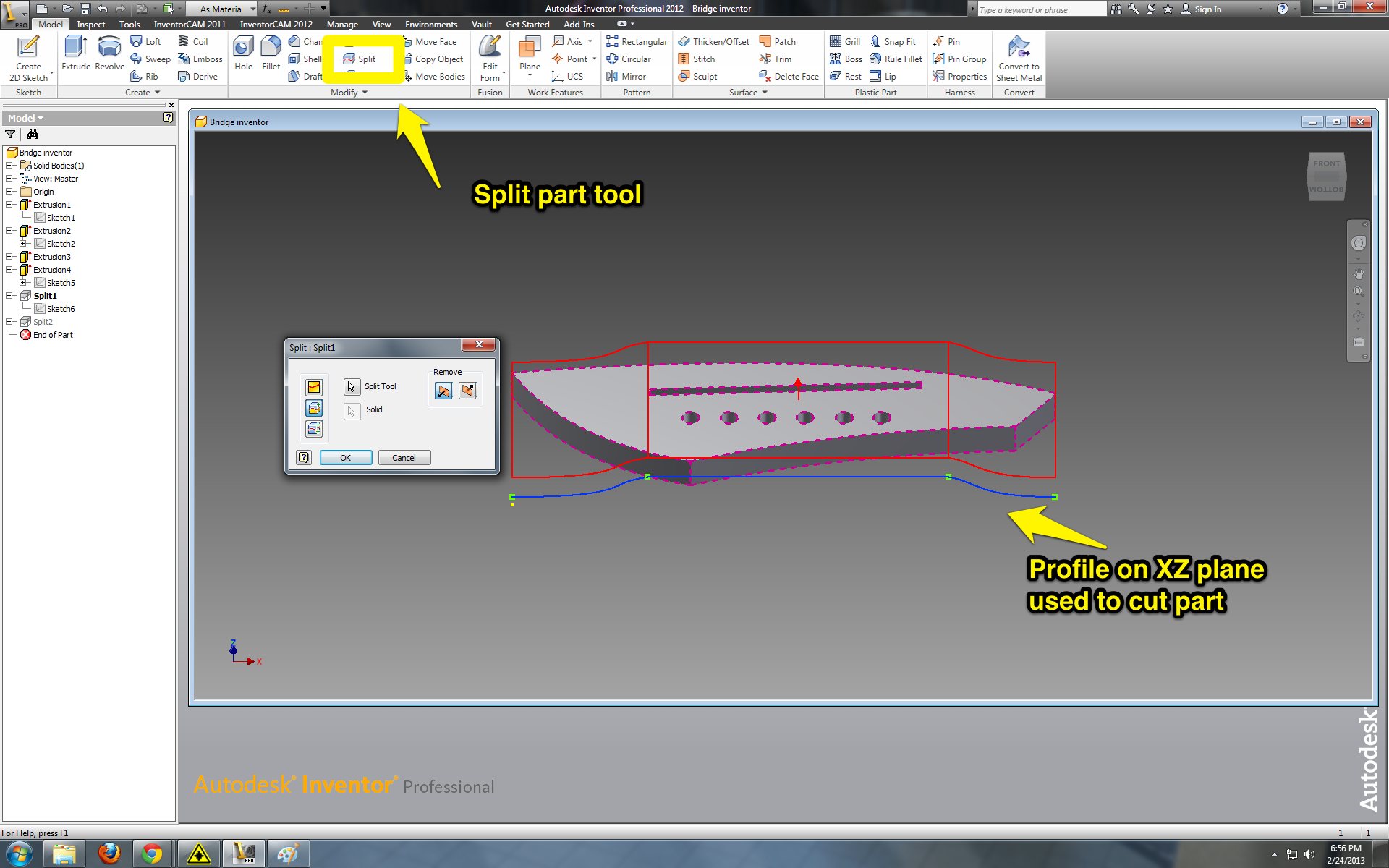
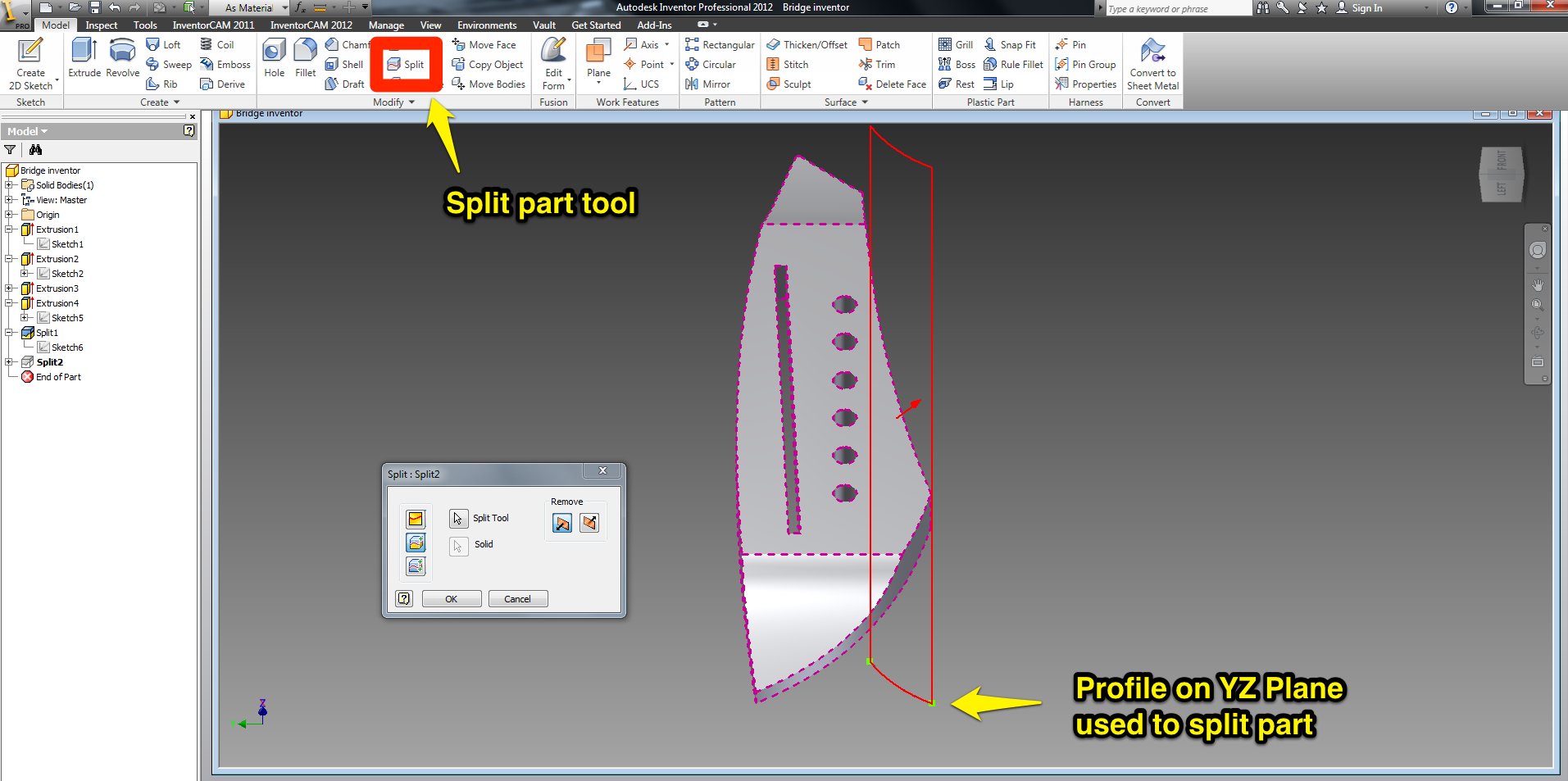
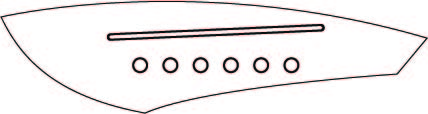
I thought about designing my own bridge from scratch, to go with the custom look of the rest of the guitar. But I wasn't sure how that might affect the final sound of the guitar, so I decided to go with a tested design from an existing builder.
I wanted something a bit different from the standard designs, and after looking around online I really liked the look of asymmetrical bridge bases. Also, given the free-flowing image on my soundboard, I wanted a design with complex organic curves instead of a flat base. I used google images to search for bridge designs, and the one that jumped out at me was that of Bashkin Guitars. I liked the flowing edges and asymmetrical design.
I couldn't find any existing 3D models of them, so I traced a photo and tried my best to form my own 3D version. I've included a .STL model of my bridge, as well as an outline of my bridge shape with slot and pin holes.
I wanted something a bit different from the standard designs, and after looking around online I really liked the look of asymmetrical bridge bases. Also, given the free-flowing image on my soundboard, I wanted a design with complex organic curves instead of a flat base. I used google images to search for bridge designs, and the one that jumped out at me was that of Bashkin Guitars. I liked the flowing edges and asymmetrical design.
I couldn't find any existing 3D models of them, so I traced a photo and tried my best to form my own 3D version. I've included a .STL model of my bridge, as well as an outline of my bridge shape with slot and pin holes.
Tracing the shape
- First, I made a new file and created a block the size of my bridge blank.
- Next, I started a new sketch on the top face of the block I just made. I found a good top-down photo of the Bashkin bridge on this site and imported the photo into my sketch.
- I used the spline tool to trace the edges of the bridge. I finished the sketch once I was happy with the 2D shape.
- I used the extrude tool to pull away all the material outside of my tracing, leaving only the bridge shape.
- I then made another sketch on the top of the new part to improve the slot and pin hole placement, based on an illustrator file one of the instructors had used on their guitar.
- I tried to import the Illustrator vector lines directly, but only some of the shapes worked, and the results were very buggy, I'm still not yet sure why. So instead of using the vectors, I just traced this image as well, using the circle tool for the pin holes, and the line and arc tools to trace the slot.
- After tracing the holes I used the extrude tool to cut the shapes out of the bridge
Shaping the sides
- In the left menu, I selected the XZ plane to make a new sketch
- Looking at the bridge from the front, I used the spline tool to make the profile I wanted. I had to make sure the contours of my profile didn't cut into the slot and pin holes.
- Once I was happy with the profile, I finished the sketch and used the split form tool to cut out the profile from the part.
- To cut out the section at the bottom, I did a similar operation on the YZ plane. I sketched a curve just to the side of the bridge, then used the split part tool to cut away the bottom of the bridge.
Design notes
- I purposefully did not cut out the pin-holes to their full size. Guitar pins are usually tapered, so that they wedge into the hole and hold the strings in place. I wasn't confident in my ability to accurately model this taper, so I cut the holes to the smallest size of the tapered pins, then drilled them to full size by hand.
- The same things goes for the saddle slot - it's just a hair smaller than my saddle bone blank. I later used a file to cut away the slot until the bone JUST fit inside.
- The saddle slot is supposed to be slanted. From what I understand the bass strings bend differently than the treble strings when playing, thus the slant helps them keep the same effective distance from the saddle.
- So far my bridge seems fine, but the person who gave me the slot and pinhole layout said they were not happy with the setback of the bridge pins - they wish they had put them further back. They are worried there is too much pressure on the saddle bone from the strings being installed at a steep angle. Consider this in your own design.
Import Into Cut 3D
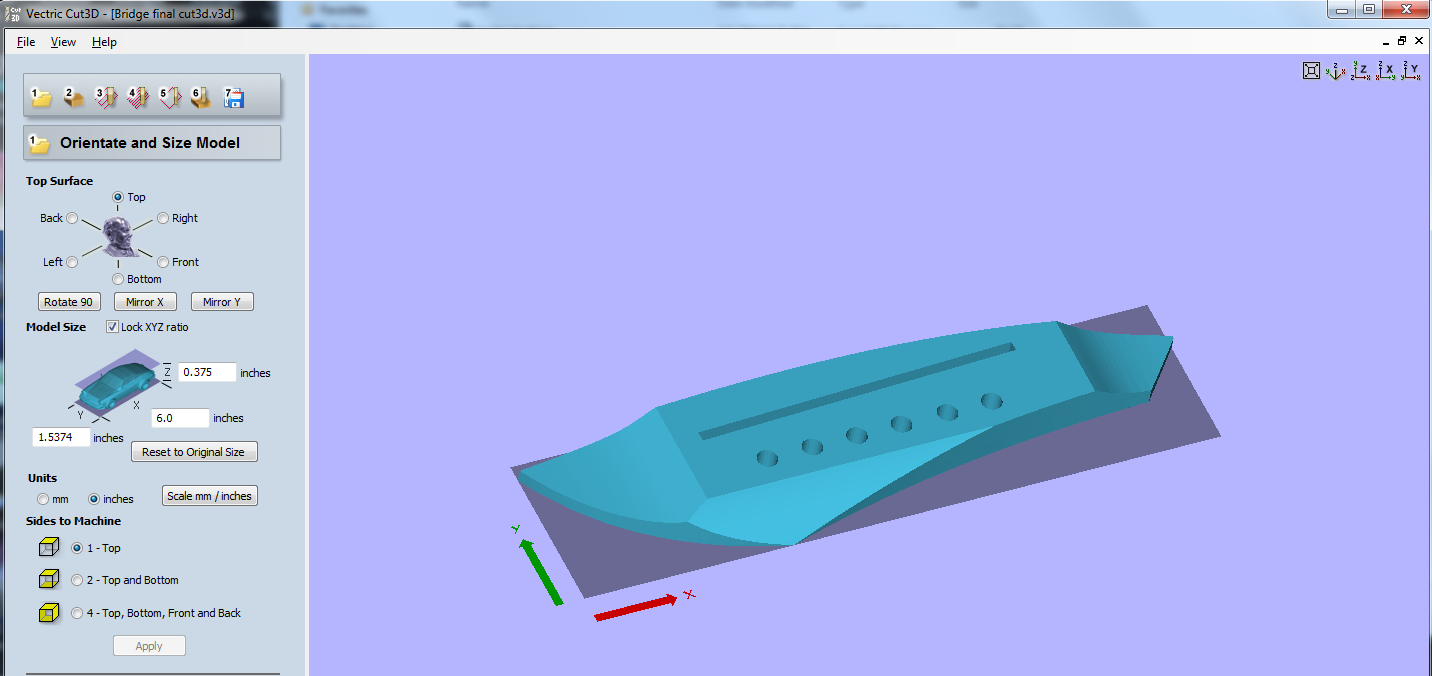
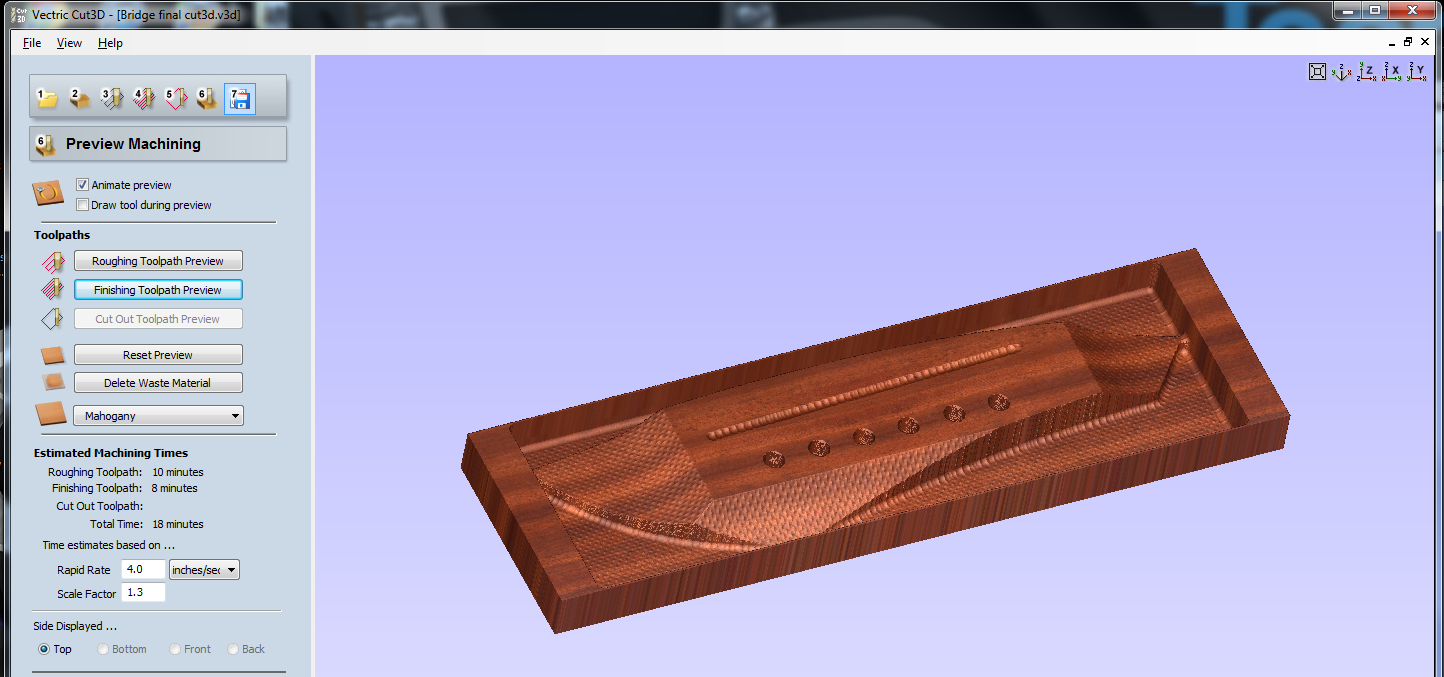
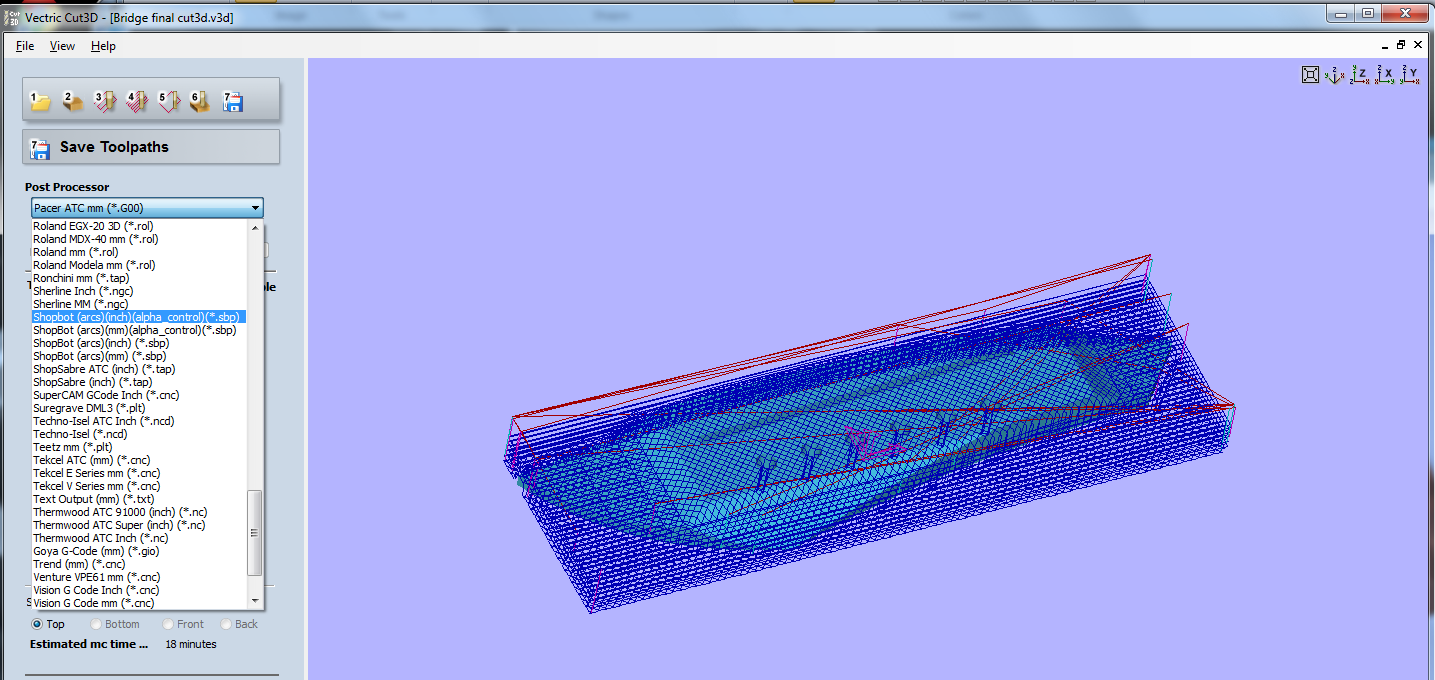
To make machine code for my part, I used Vectric Cut 3D. This is a good, intuitive CAM program for generating machine code from models. Apparently Inventor now also have its own CAM program, Inventor CAM, allowing one to make machine code directly within the model itself. But I haven't learned how to use this yet, so I stuck with Cut 3D
Making the CAM file
- Export the part from inventor as a .STL file
- Import the .STL into Cut 3D
- Set the dimensions of the bridge itself. Check the size - Cut 3D should be able to see the size from the file being imported, but often it will resize it slightly.
- Set the dimensions of the material and the Z-zero position. I usually set Z-zero on the bottom, not the top, especially when cutting completely through a part. Whatever your choice, make sure you remember it and set the machine correctly when it's time to cut.
-
Steps 3-4 in Cut 3D are the roughing and finishing tool-path. Since this part is very small, and I wanted to avoid any potential errors from tool changes, I used the same size bit - 1/8" ball nose end mill - for both passes. I was worried that using a larger size bit might be too intense for the double stick tape used to hold my work. My settings are as follows
- Tool size: 1/8" ball nose end mill (roughing and finishing)
- Spindle speed; 12000 RPM
- Feed speed: 1.5 inches / second
- Plunge rate: 0.5 inches / second
- Pass depth: 0.625 (5/8") inches
- Stepover: 40%
- Finish pass: raster 45* + extra pass at 90* to first
- I did not use a cutout tool path - I just left the extra material on the edge of the part and cut it out later using a bandsaw and sander.
- Preview the cut within the program, make sure everything seems right
- Export the file to your CNC machine of choice - in my case the Shopbot
Cut on the ShopBot
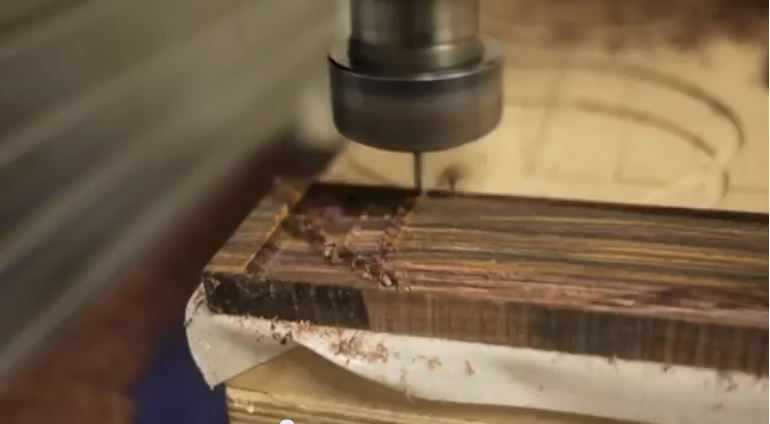
Once the part is designed, and the G-code generated, I moved over to the ShopBot. I strongly recommend at least doing an air-pass over the material to make sure the cutter is tracking properly. Even better, I recommend making a practice part out of scrap wood, especially if your bridge blank comes from a specially chosen piece of wood.
This worked well, but two times the tape nearly came unstuck - I saw the wood starting to vibrate, paused the machine and pressed it down again. I think this was because some small wood shavings and dust were trapped under the tape, and the machine bed had been cut deep by the last user - so the tape didn't have full contact. I guess I'll be more careful when putting tape down next time.
Total cut time was ~17 minutes
Work-holding
There are different ways to hold the work. If the blank material is much larger than the bridge itself, go ahead and screw the material to the machine base, or a sacrificial base. In my case, my bridge blank didn't have enough room to screw down the material, so I used double stick tape.This worked well, but two times the tape nearly came unstuck - I saw the wood starting to vibrate, paused the machine and pressed it down again. I think this was because some small wood shavings and dust were trapped under the tape, and the machine bed had been cut deep by the last user - so the tape didn't have full contact. I guess I'll be more careful when putting tape down next time.
Total cut time was ~17 minutes
Finishing & Mounting the Bridge
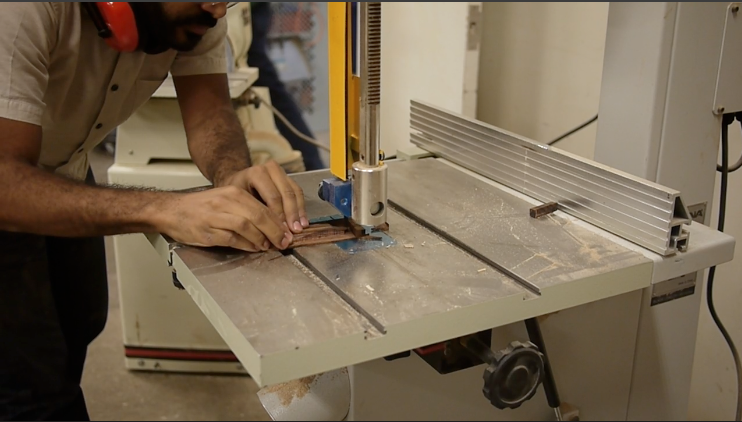
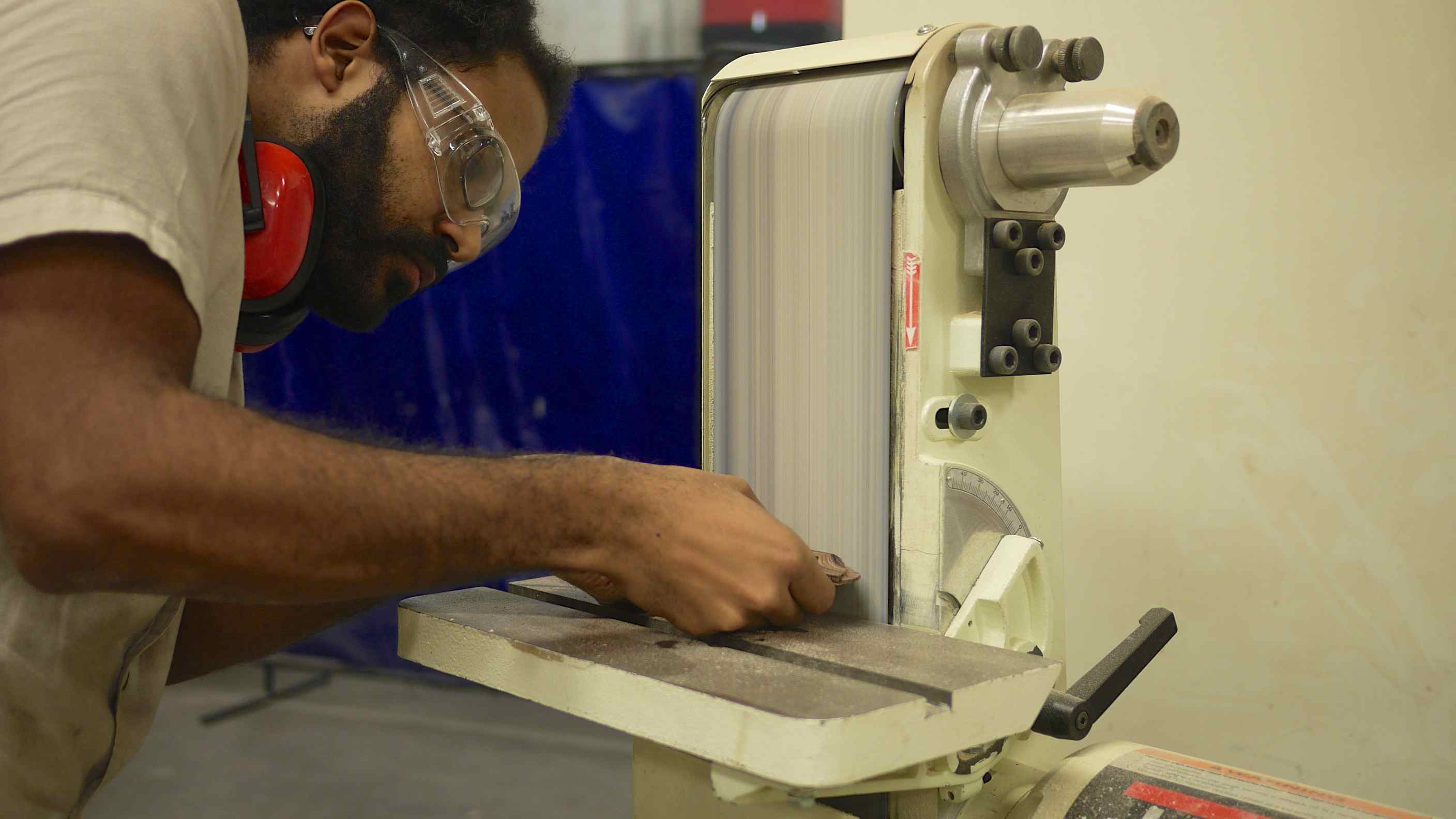
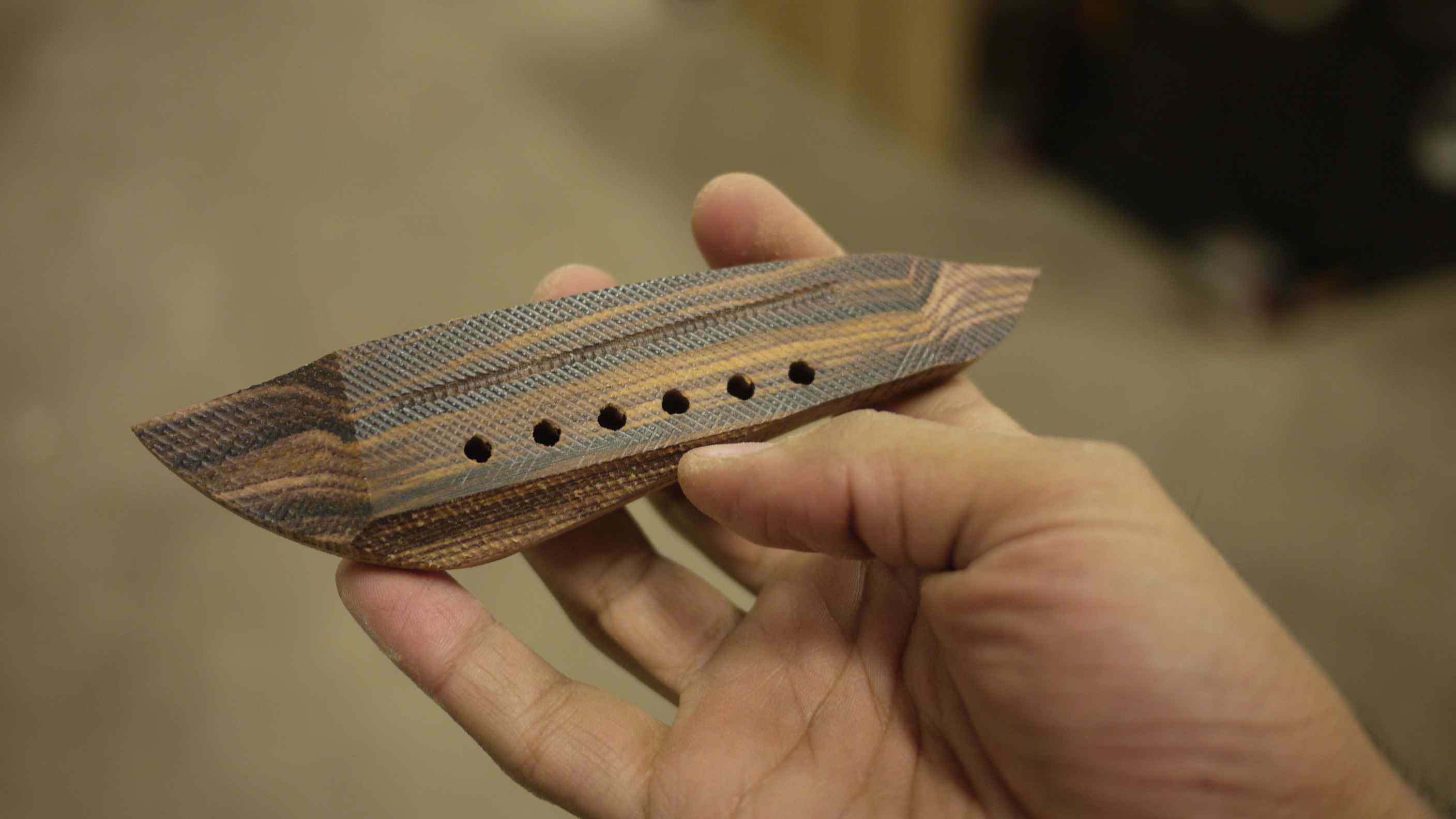
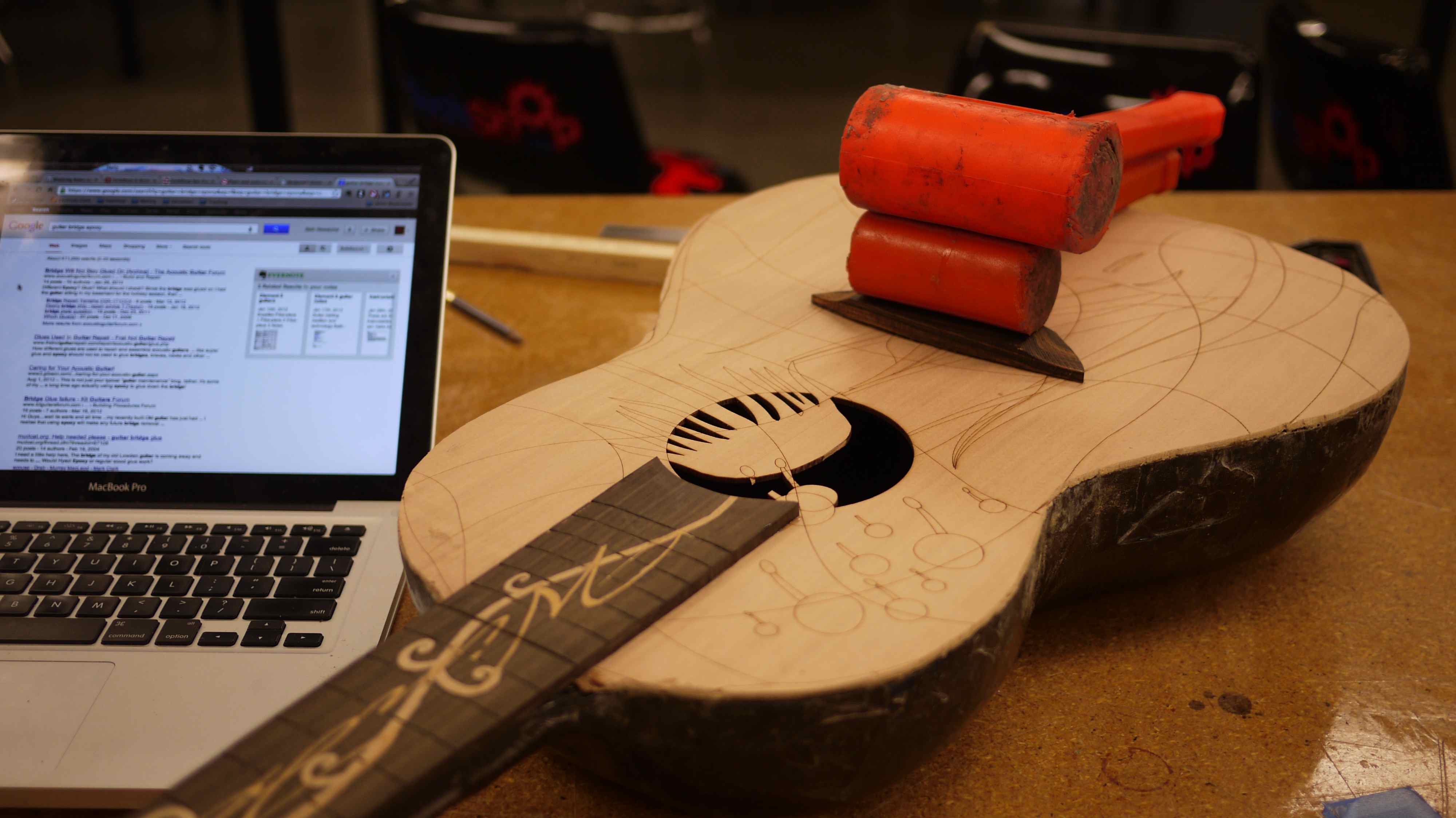
Finish the bridge
I left the tabs on my bridge, to make sure it had as much support from the double stick tape as possible. So after the ShopBot finished cutting, I went to the bandsaw to cut away the extra material, then lightly sanded the edges.My choice of a 2-step finishing pass left a neat cross-hatched texture on the bridge itself. I was planning to sand this away to make a smooth finish, but the more I handled the bridge, the more I liked the texture - so I decided to keep it. You may also notice that the slot isn't properly cut - this is due to a mistake in my original file, and I had to go back and finish it later. This can be fixed by checking the file and altering the extrusion.
Mounting the bridge
In the end, one basically glues the bridge to the soundboard and hopes for the best. But there are some very important considerations to make when mounting. Is the soundboard flat, slightly concave, or slightly convex? Is the bridge centered along both axis of the guitar? What is the distance to the nut?All of these considerations have a big effect on the rest of the guitar. If you are a fellow first time building, I strongly recommend finding some professional advice for assembling the guitar. Look for luthier websites, or look for books on guitar building - there are many good books out there. I found a whole section on the topic at my local library, and ended up using Build Your Own Acoustic Guitar by Jonathan Kinkead as my go-to reference book.
With that said, here are some important things to consider
Properly seating on the soundboard
Often times after being glued and installed, the guitar soundboard can be slightly curved in the middle, either dipping down in the center, or having a slight peak in the center. I was lucky and my soundboard was almost dead flat. But if your soundboard is curved, do not try to force a flat bridge onto it - over time the tension of the strings may eventually damage the soundboard, breaking it near the bridge. Instead, try to gently shape / sand the bottom of the bridge until it sits flat on the soundboard
Properly centering the bridge
If the bridge is mounted off-center, or mounted at an angle, the alignment of the strings may be off, causing them to hit each-other, chatter on the fretboard, or be difficult to play. Measure carefully from both sides, and if your bridge is asymmetrical, be extra careful.
The distance from the nut to the bridge
In the plans for the guitar mine is based on, it specifies that the bridge should be 163 cm from the nut. This distance is important, because it is the basis for the harmonics of the instrument. This basically means that the placement and size of the frets on your fretboard will change depending on this distance.
- If you place the bridge too far up or too far down on the soundboard, then the scale on the guitar will change location and won't be where you expect them to be
- If you are designing your own guitar completely from scratch, then you can put the bridge anywhere you want, even in unconventional positions - just remember that you will have to adjust your fretboard and playing style to compensate. There is a mathematical formula to determine the new scale position, but I don't feel confident describing it since I didn't actually apply it. Any professional guide or book on guitar building should include it.
- If you are being particular, there are a few additional measurements to take that can even account for the effect of the strings bending while you play
Final touches
- After mounting the bridge, I used a handheld drill and reamer to widen the holes to their final size and drill through the soundboard. Unfortunately I don't have pictures of this step.
- I also used a small file to gently widen the saddle slot until the saddle bone fit snugly inside
That's it, I hope this helps someone or gives people ideas.