Bantmobile 1957 Corvette

Among the first set of Corvettes that Chevrolet produced, the 1957 model is a bonafide classic! Designer Ben Light put a modern CNC twist on this stunner by showing you how to build a wood and acrylic toy version using the versatile Bantam Tools Desktop PCB Milling Machine. This intermediate-level project assumes you have some experience with the Bantam Tools Desktop PCB Milling Machine, Bantam Tools Desktop Milling Machine Software, and are comfortable using hand tools. If you're just getting started, be sure to check out our series of introductory guides.
Gather Your Tools and Materials
TOOLS
Bantam Tools Desktop PCB Milling Machine
Computer with Bantam Tools Desktop Milling Machine Software installed
Flat end mill, 1/8"
Hammer
Clamps
Flathead screwdriver
Drill and ¼" drill bit
MATERIALS
Plywood, 5" x 4.5" x 0.475" (2)
Acrylic, red, 5" x 4.5" x 0.25" (2)
Dowel pins, ¼" diameter 1" long (3)
Wood glue
Adhesive spray
Sandpaper, 220 and 400 grit
Paper towels
MATERIALS FOR WHEELS AND AXLES
Nylon door roller, 1½" (4)
Nylon spacers (4)
Binding barrels and screws (2)
O-rings (4)
SVG FILES
vette_wood_outside.svg
vette_wood_inside.svg
vette_wood_engrave.svg
vette_plastic_outside.svg
vette_plastic_engrave.svg
vette_plastic_holes.svg
vette_plastic_flip_outside.svg
vette_plastic_flip_engrave.svg
vette_plastic_flip_holes.svg
CUSTOM TOOL LIBRARIES
Custom tool library for milling wood
Custom tool library for milling acrylic
Note: We suggest buying more material than you think you need. A good rule of thumb is to take the amount you think you need and times it by pi.
Safety first: Before you get started, take the time to learn the proper procedures for your mill, your bits, and your materials. Always use a clean mill. Take care to properly mount the material to the bed. And never leave a running mill unattended.
Create the Design
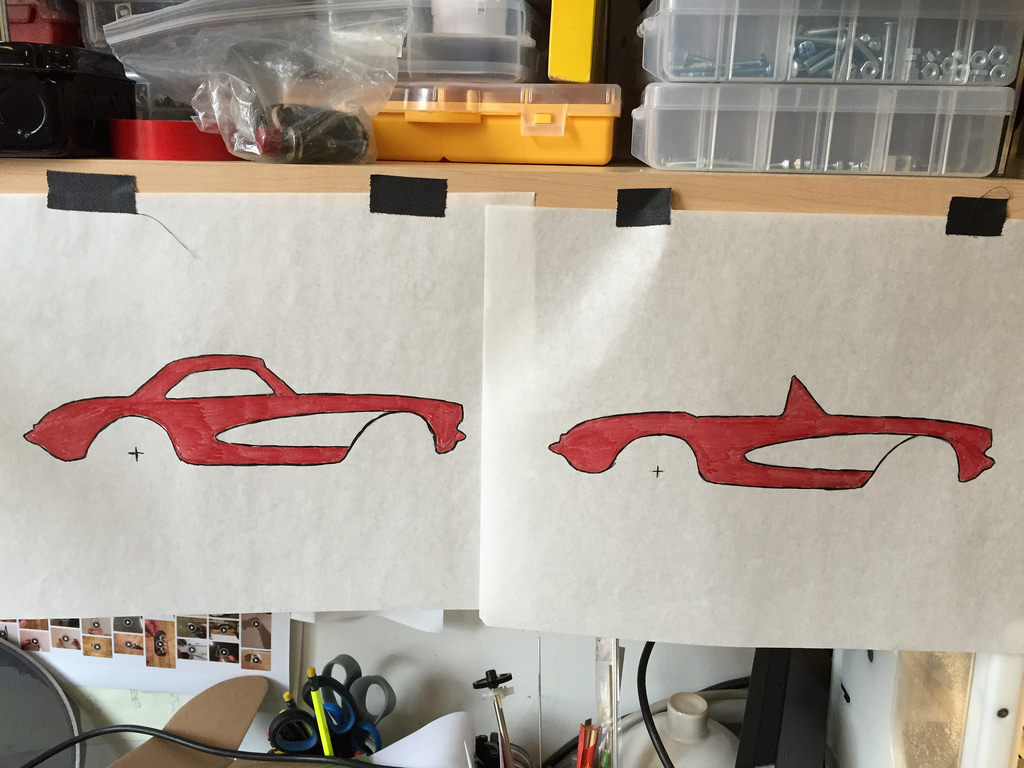
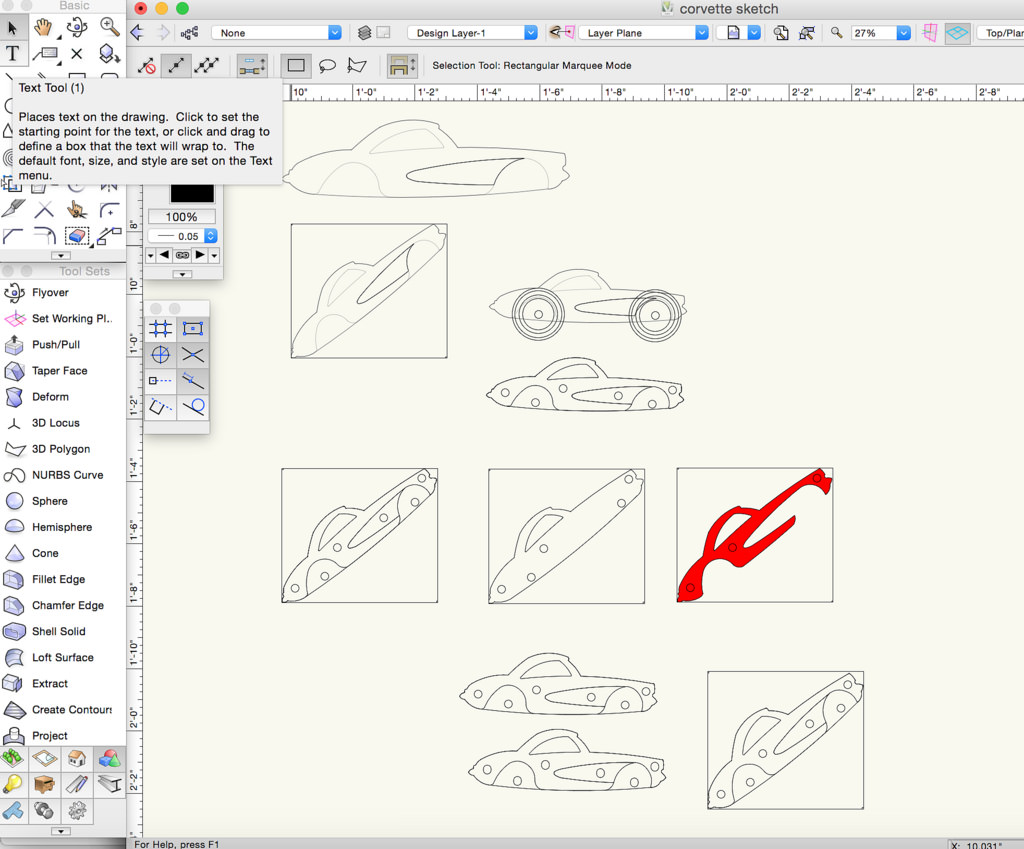
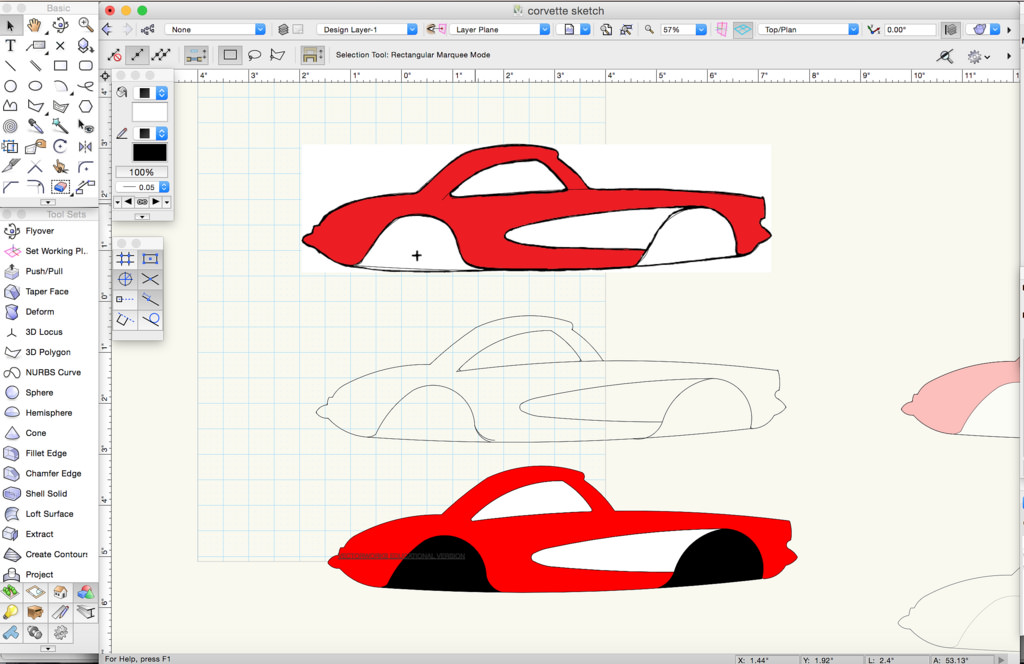
The SVG design files you need are all provided in this tutorial. Download them all from the Tools and Materials list.
To create them, Ben first drew a simplified version of a ‘57 Corvette and scanned it. He then opened the scan in Vectorworks (which is free for students) and traced on top of the image, mostly using the Arc tool. The file was manipulated until it fit along the diagonal of a 5" x 4.5" rectangle. Finally, that file was opened in Adobe Illustrator, where the SVG files were created.
Download and Import the Tool Libraries
Before you mill, download the Bantam Tools custom tool libraries for wood and acrylic.
For wood, download this file, which contains all the recommended feeds and speeds. Then open the Bantam Tools software, click File > Tool Library, click the “Import” button, and select this file.
For acrylic, download this file, which contains all the recommended feeds and speeds. Then open the Bantam Tools software, click File > Tool Library, click the “Import” button, and select this file.
Before using these settings, it’s a good idea to read through the Bantam Tools Speeds and Feeds Guide.
Mill the Plywood Parts
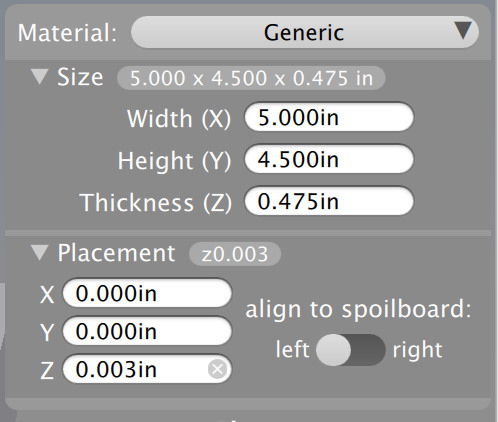
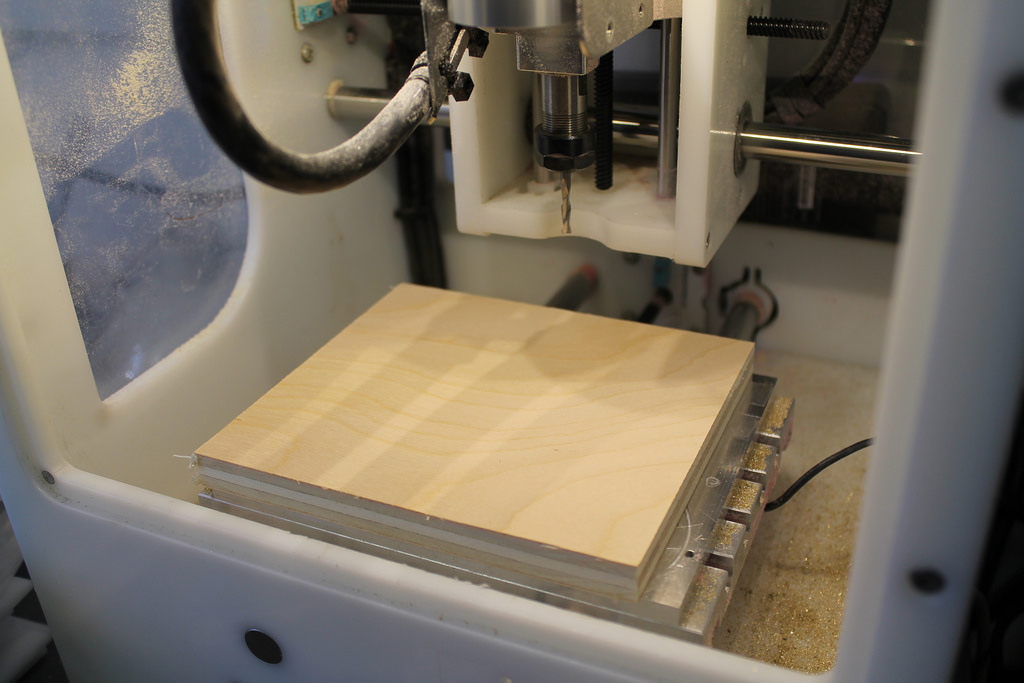
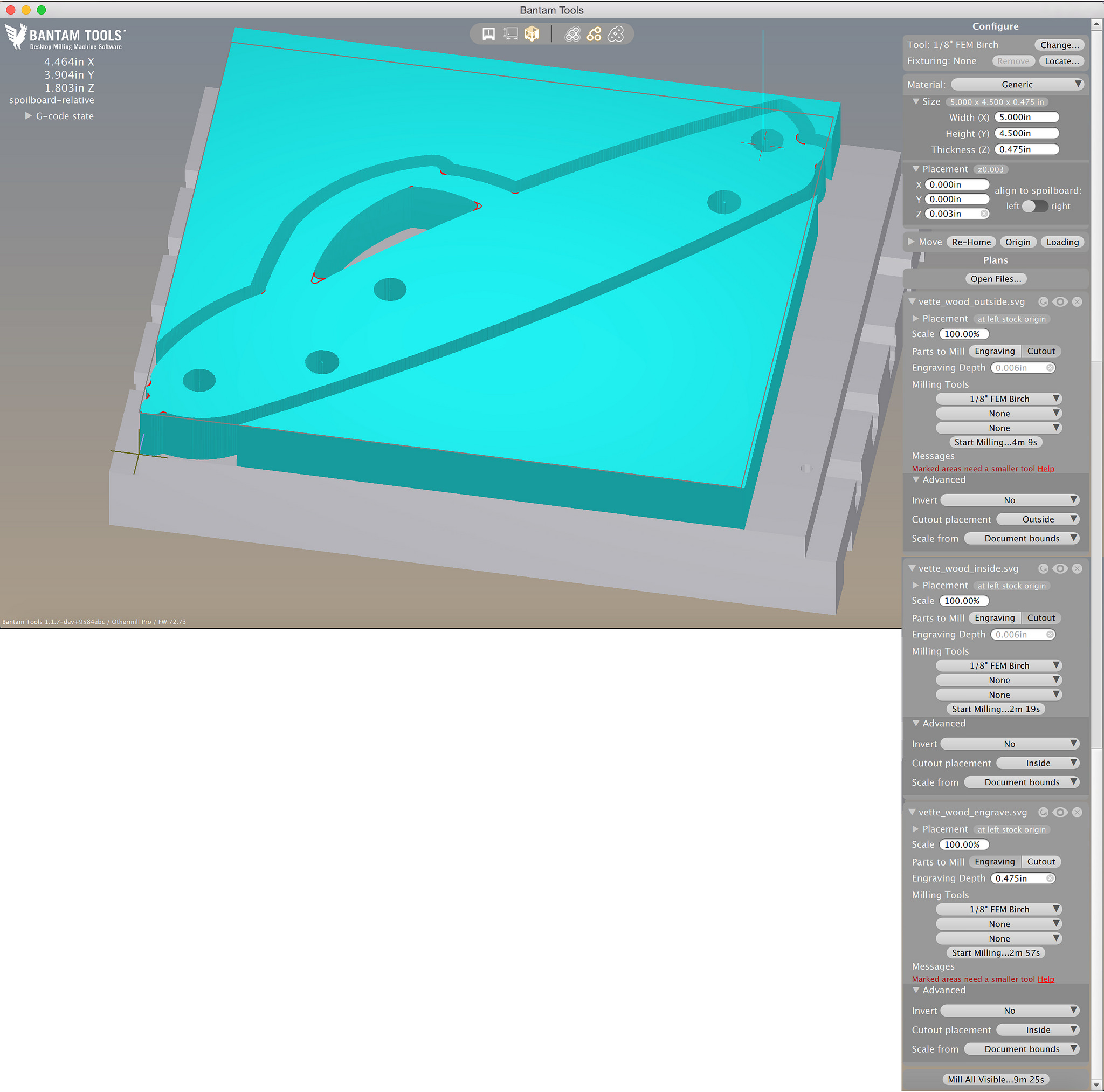
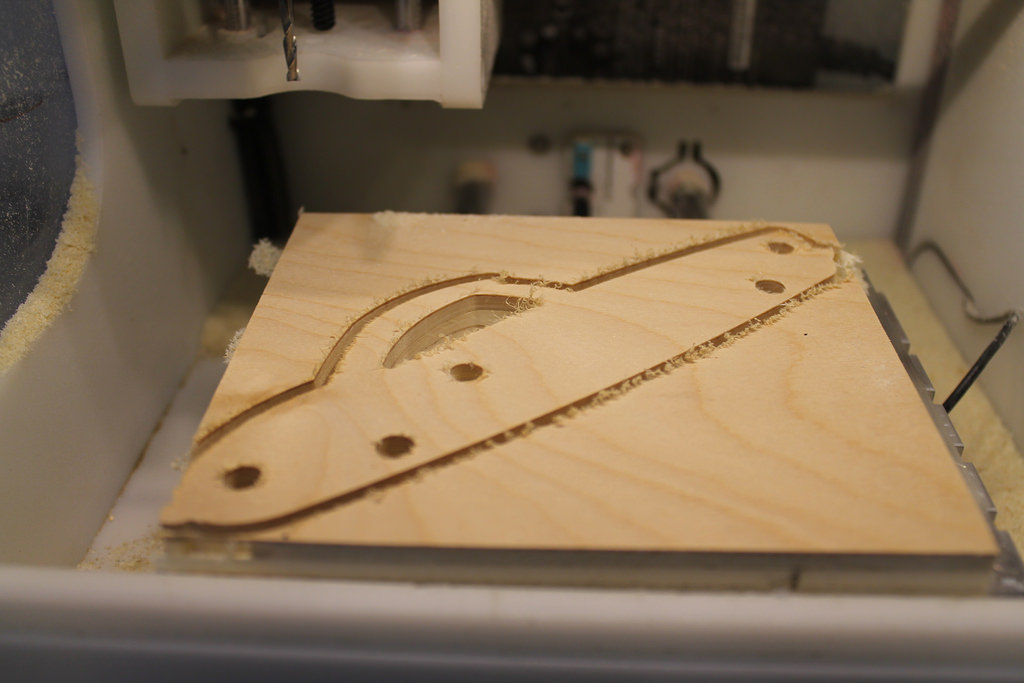
Measure the thickness of the plywood with digital calipers (½" plywood is not always exactly ½" thick). Our plywood measured in at 0.475" thick.
In the software, set Material to “Generic” and Size to your specific measurements (ours was 5" x 4.5" x 0.475").
The double-sided tape we're using to mount the plywood to the spoilboard is 0.003" thick. In the software, set Placement to 0.003" for the z-axis. Mount the plywood to the mill bed with the double-sided tape.
To mill the wooden parts, use these files:
- vette_wood_outside.svg
- vette_wood_inside.svg
- vette_wood_engrave.svg
And follow these instructions:
- Choose the bit ⅛” FEM Birch for all files.
- For all files, under “Advanced”, set "Scale from" to “Document bounds”.
- For vette_wood_outside.svg, unclick the “Engraving” option.
- For vette_wood_inside.svg, unclick the “Engraving” option.
- For vette_wood_inside.svg under “Advanced”, set Cutout placement to “Inside”.
- For vette_wood_engrave.svg, unclick the “Cutout” option.
- For vette_wood_engrave.svg, set Engraving Depth to 0.475”.
Mill each part. Then remove the plywood, clean the machine, and attach another piece of plywood to the mill bed with double-sided tape. Repeat until you've milled all three parts.
Mill the Acrylic Parts
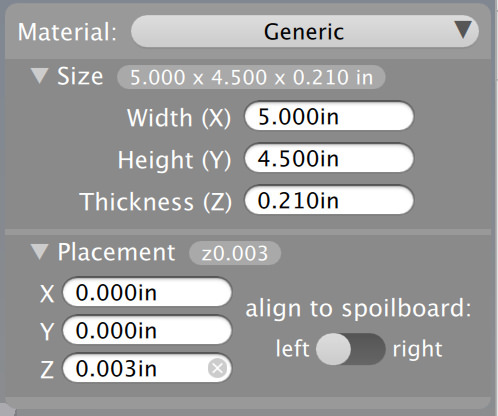
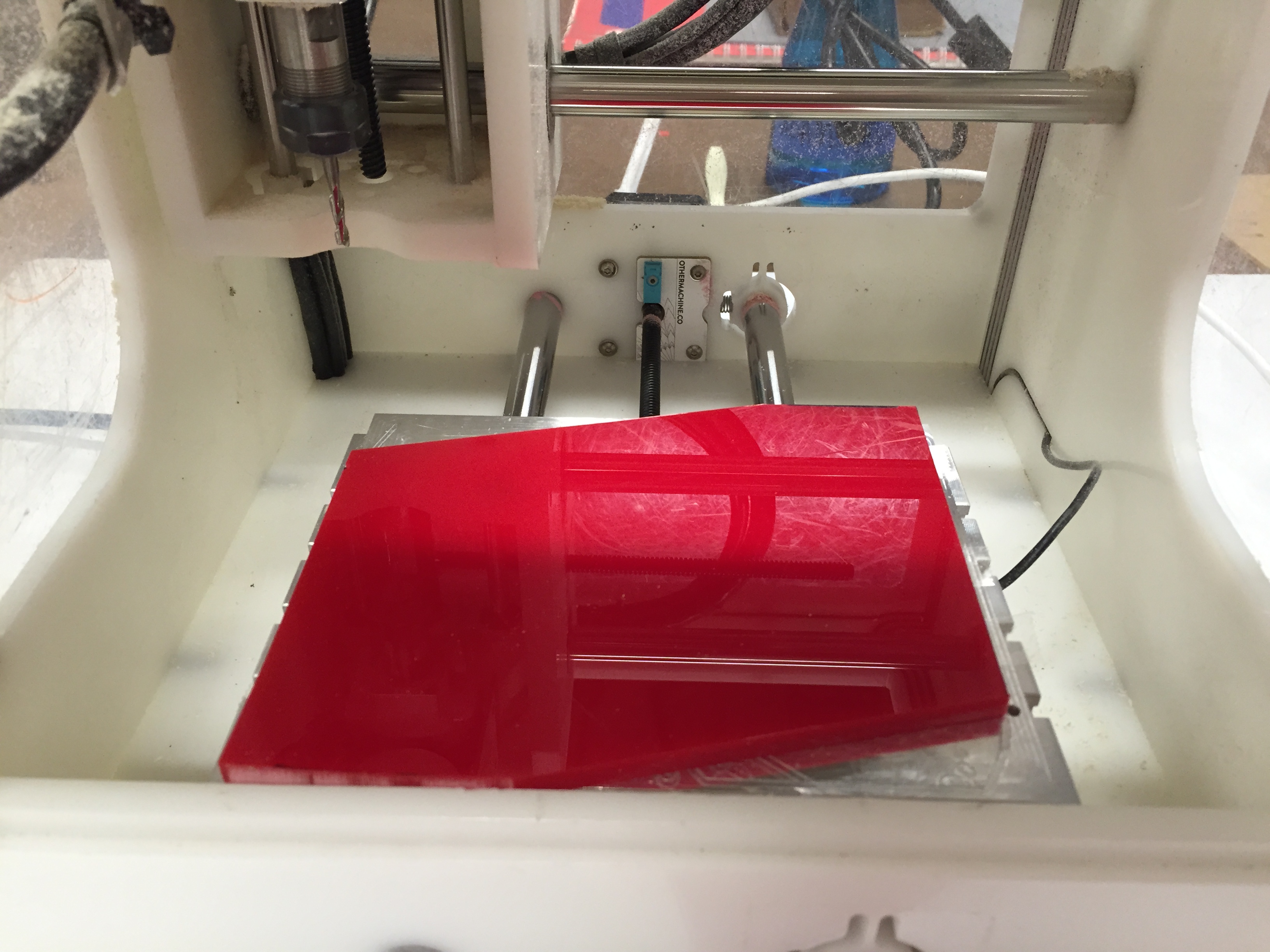
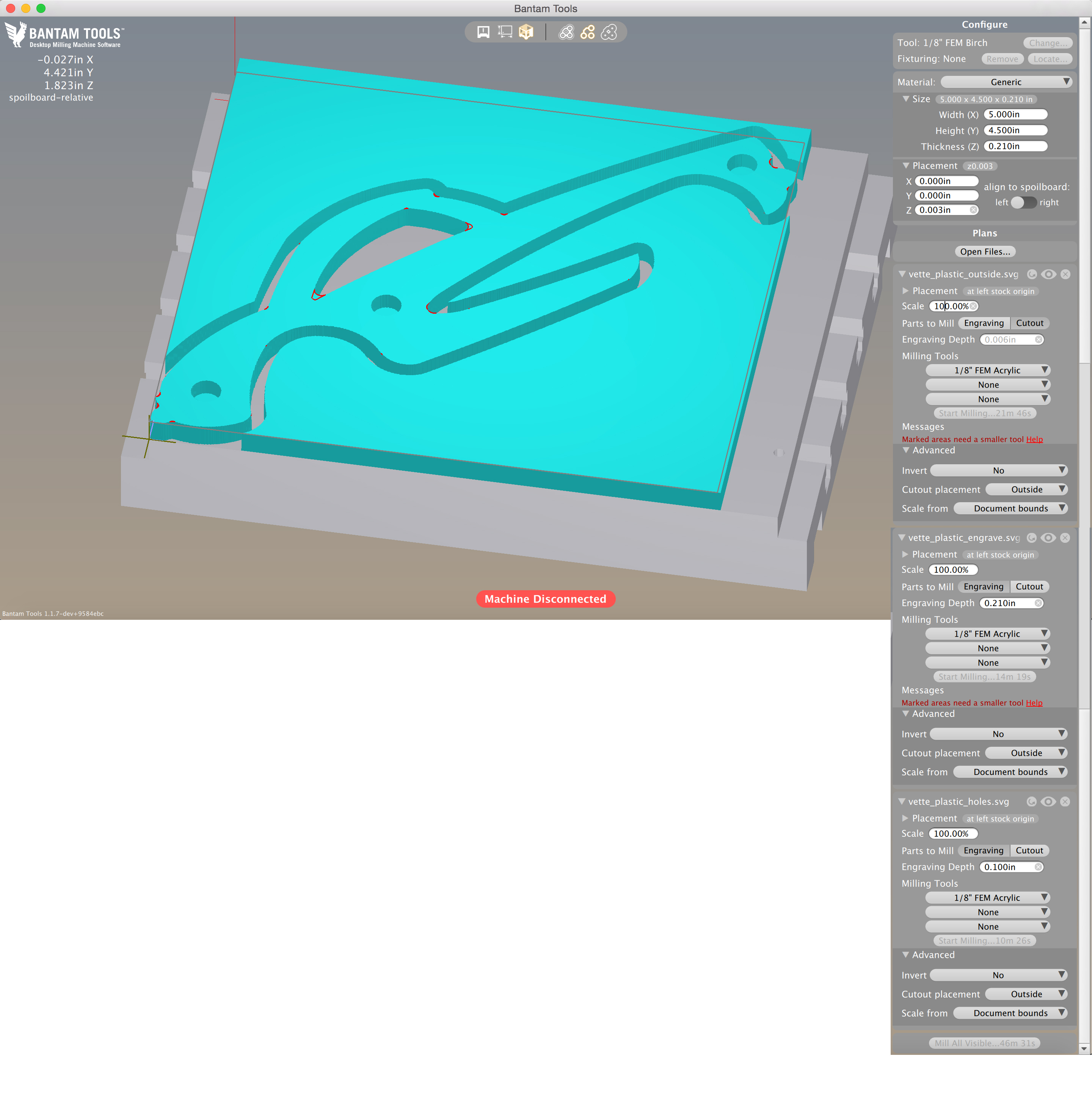
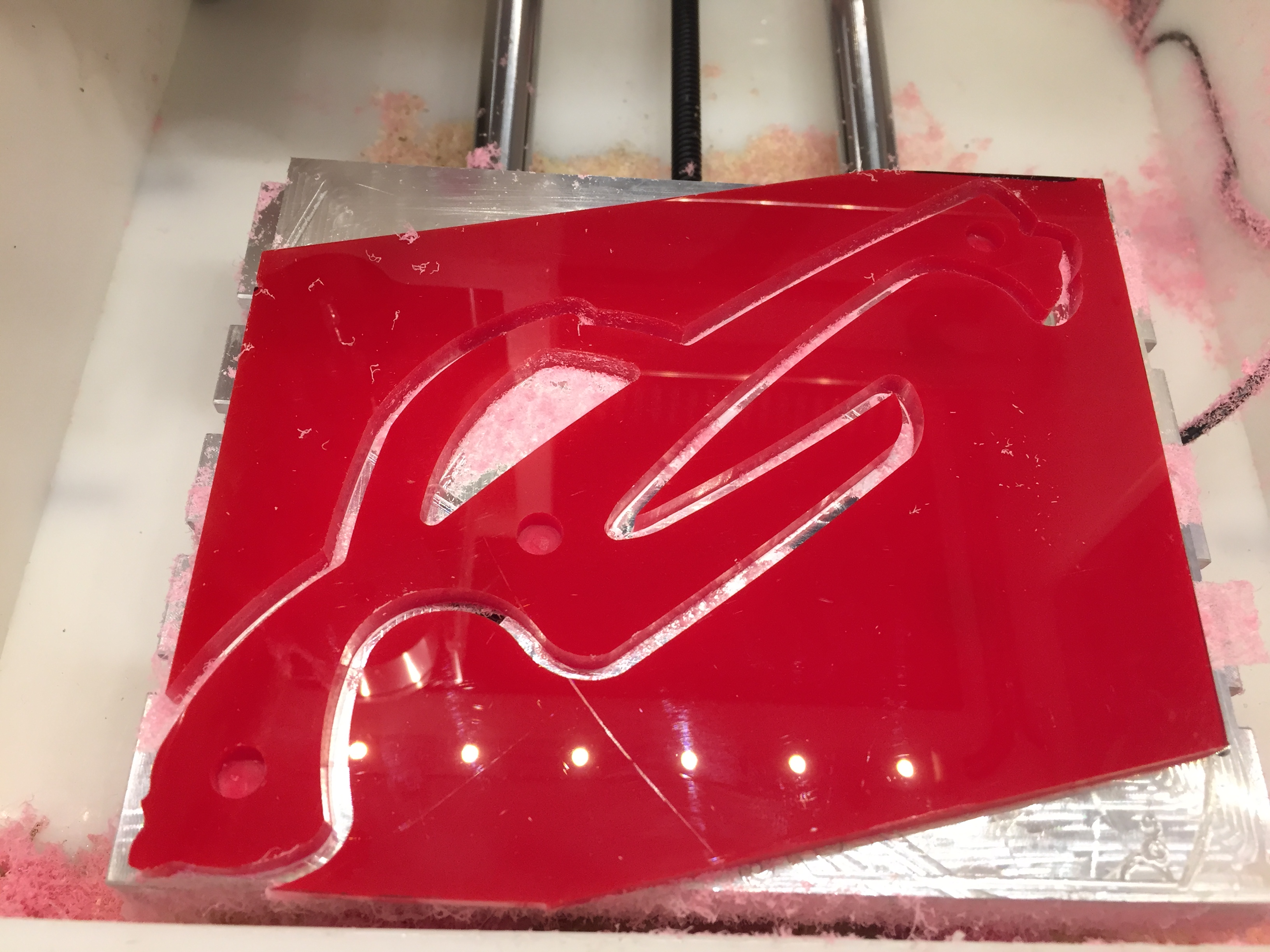
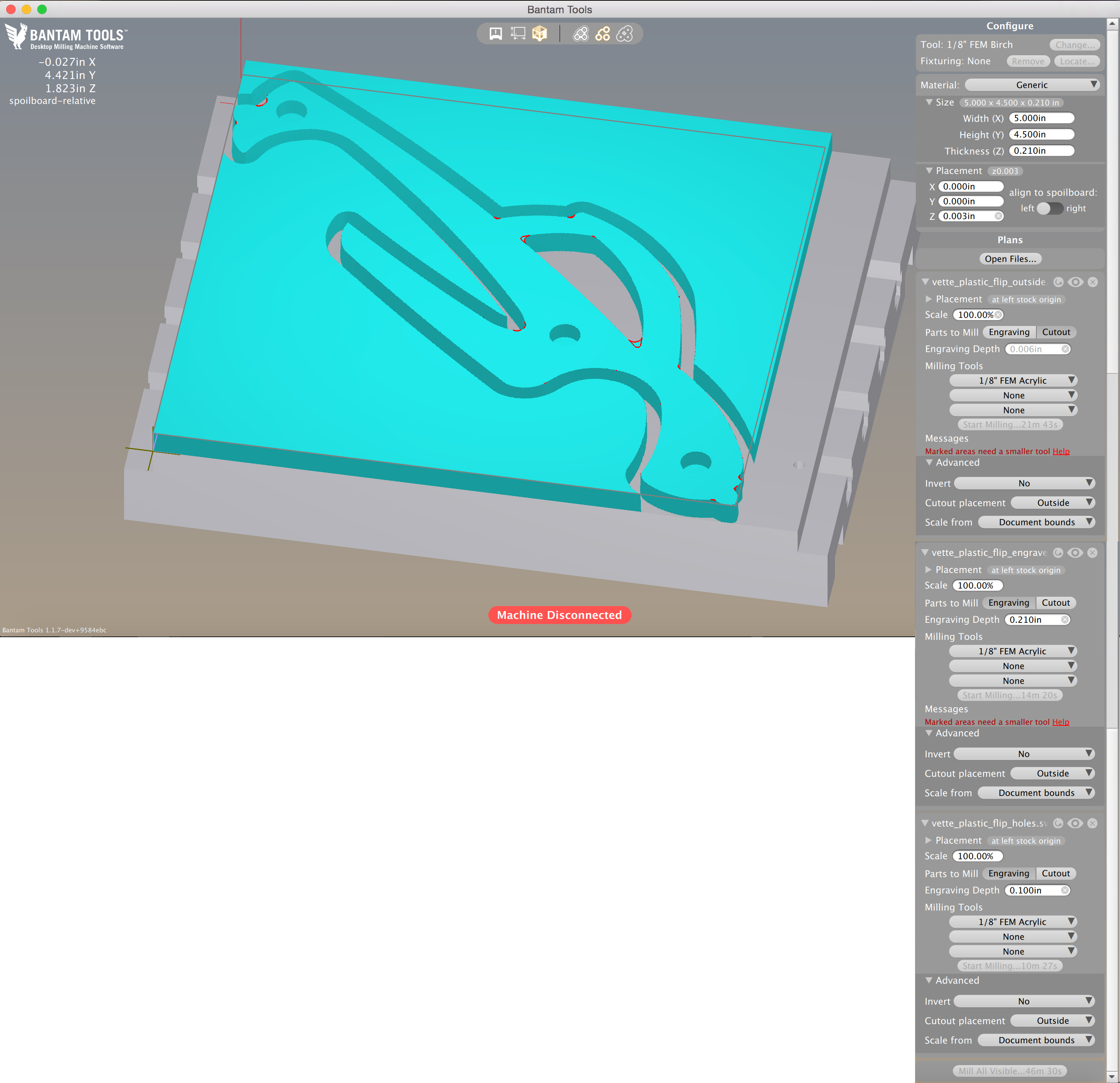
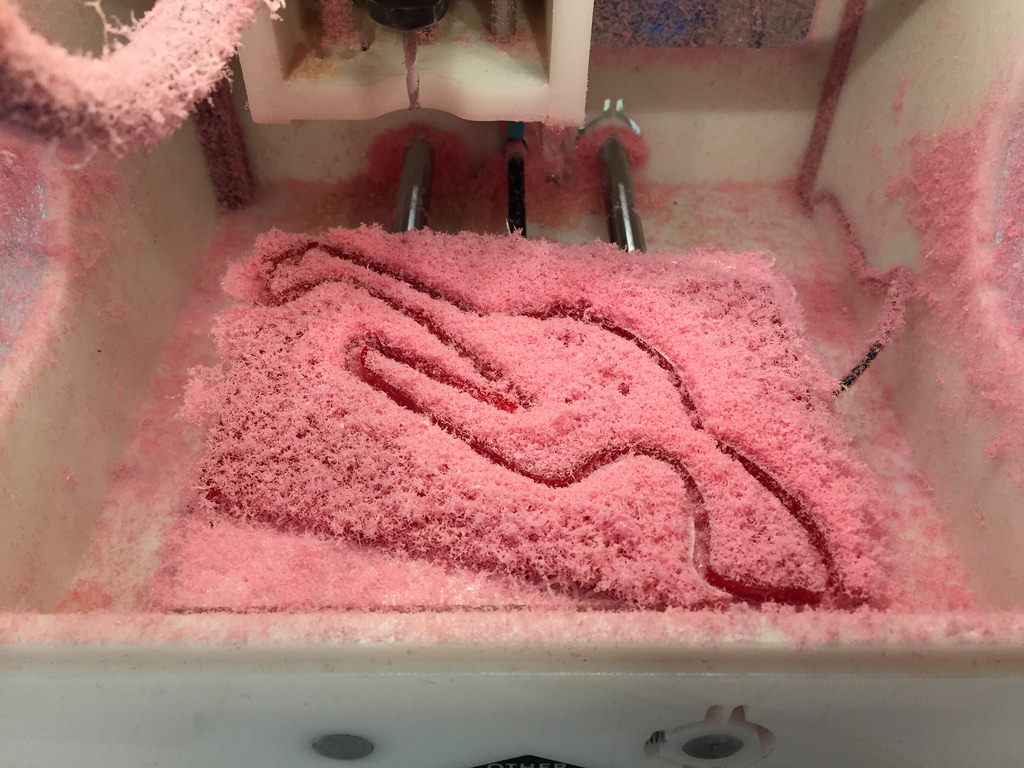
Make sure you measure your material thickness with digital calipers (¼"-thick acrylic is not always ¼" thick). Our acrylic thickness measured in at 0.21".
In the software, we set Material to “Generic” and Size to 5" x 4.5" x 0.210".
The double-sided tape we're using to mount the acrylic is 0.003" thick. In the software, set Placement to 0.003" for the z-axis. Mount the acrylic to the mill bed with double-sided tape.
To mill the first acrylic part, use these files:
- vette_plastic_outside.svg
- vette_plastic_engrave.svg
- vette_plastic_holes.svg
And follow these instructions:
- Choose the bit 1/8" FEM Acrylic for all files.
- For all files under “Advanced”, set "Scale from" to “Document bounds”.
- For vette_plastic_outside.svg, unclick the “Engraving” option.
- For vette_plastic_engrave.svg, unclick the “Cutout” option.
- For vette_plastic_engrave.svg, set Engraving Depth to 0.21".
- For vette_plastic_holes.svg, unclick the “Cutout” option.
- For vette_plastic_holes.svg, set Engraving Depth to 0.1".
- Mill the part.
To mill the next acrylic part, use the same placement and material size as the last operation, but use these files:
- vette_plastic_flip_outside.svg
- vette_plastic_flip_engrave.svg
- vette_plastic_flip_holes.svg
And follow these instructions:
- Choose the bit 1/8" FEM Acrylic for all files.
- For all files under “Advanced”, set "Scale from" to “Document bounds”.
- For vette_plastic_flip_outside.svg, unclick the “Engraving” option.
- For vette_plastic_flip_engrave.svg, unclick the “Cutout” option.
- For vette_plastic_flip_engrave.svg, set Engraving Depth to 0.21”.
- For vette_plastic_flip_holes.svg, unclick the “Cutout” option.
- For vette_plastic_flip_holes.svg, set Engraving Depth to 0.1”.
- Mill the part.
Assemble and Sand the Car
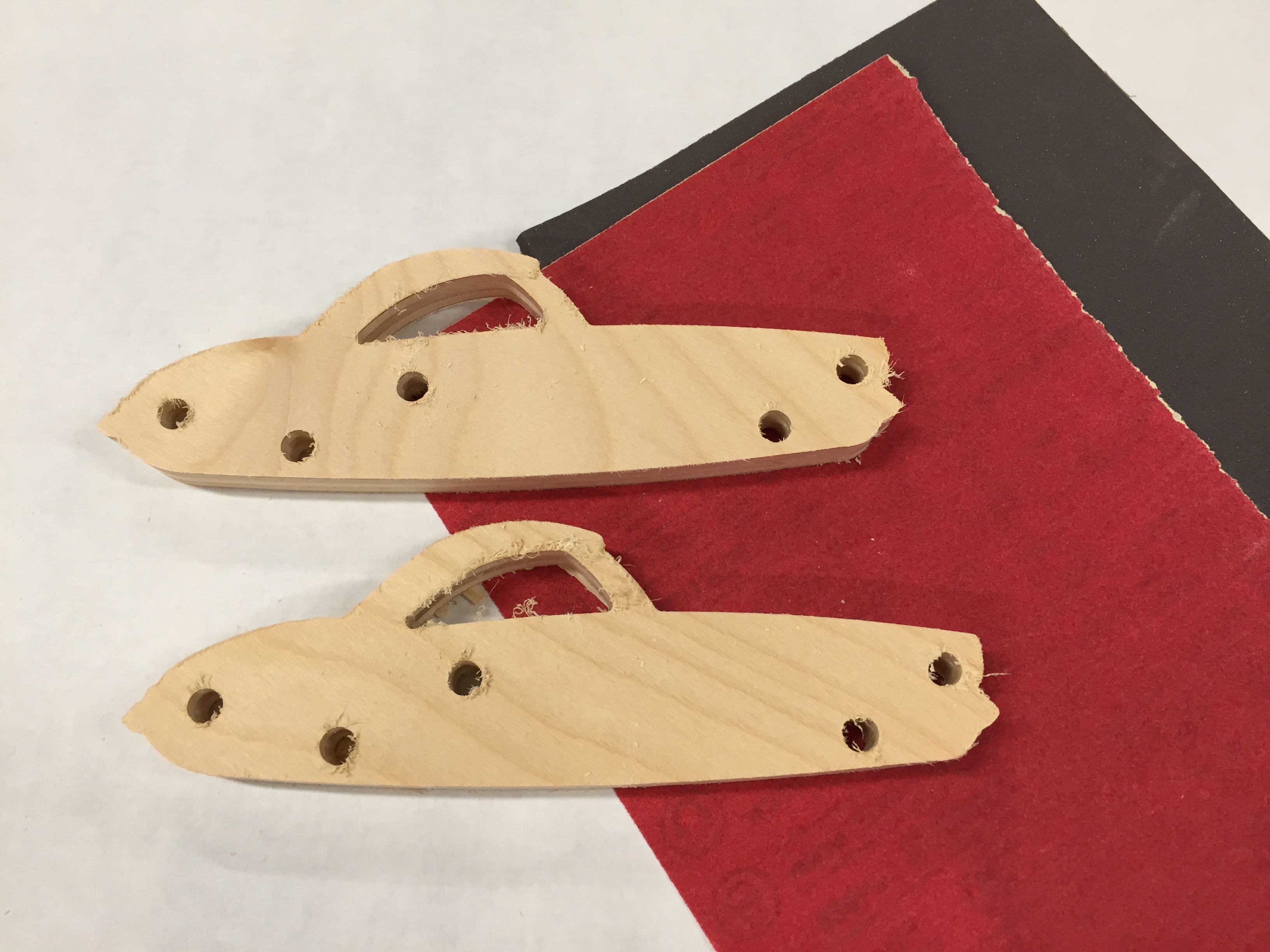
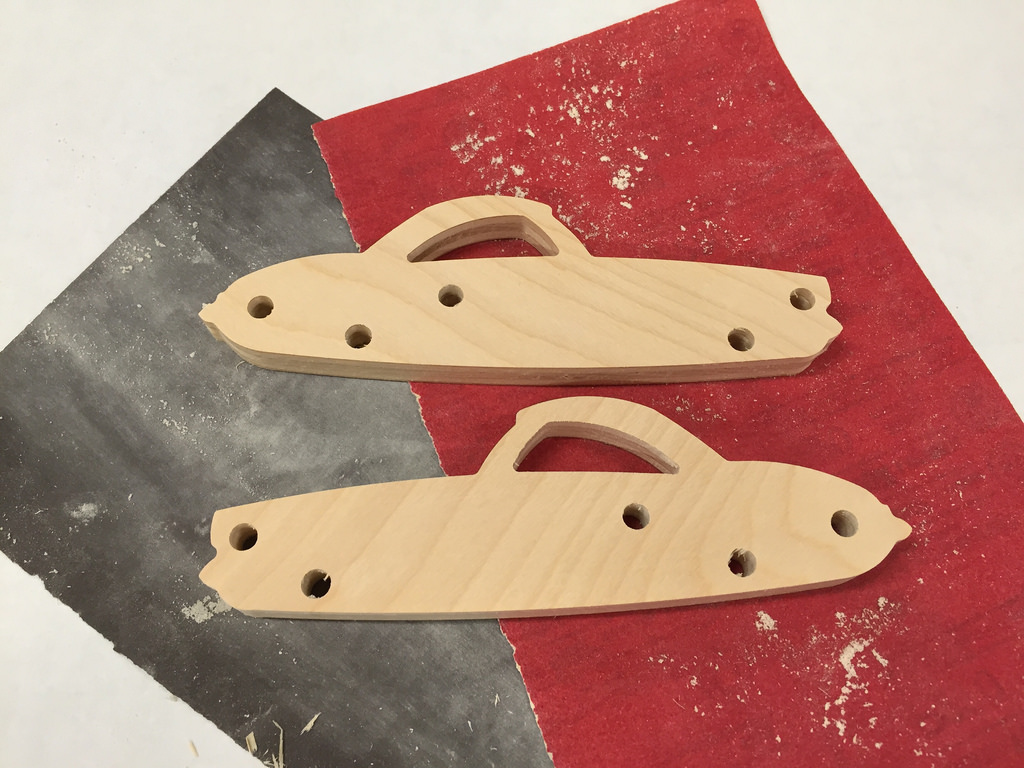
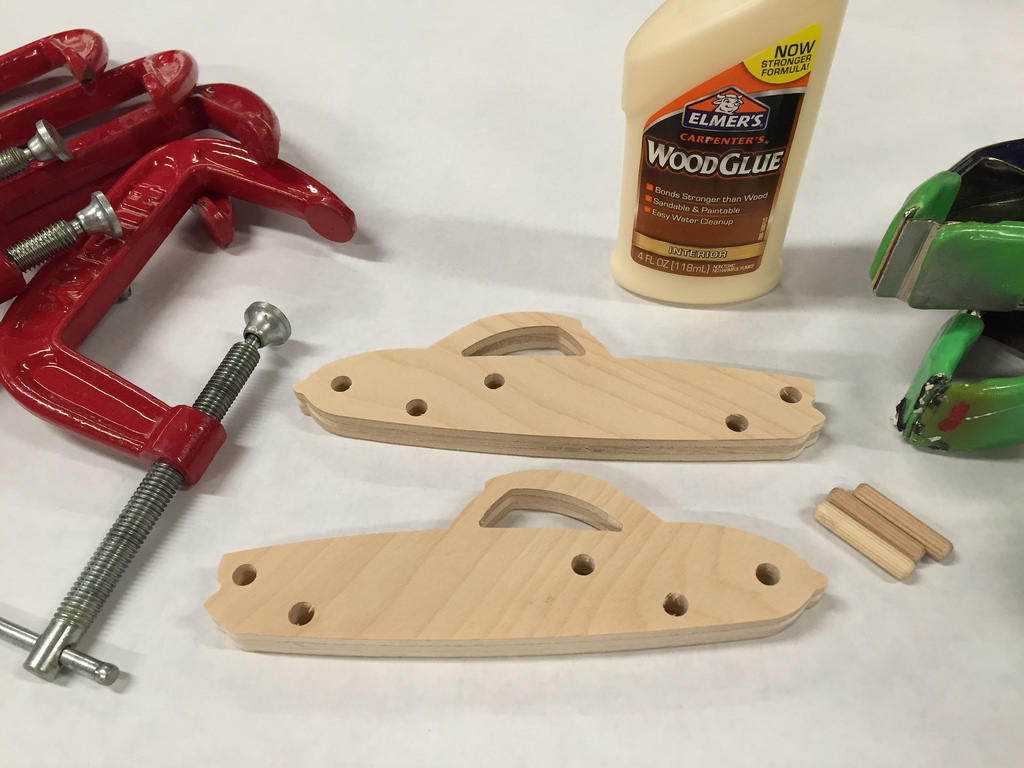
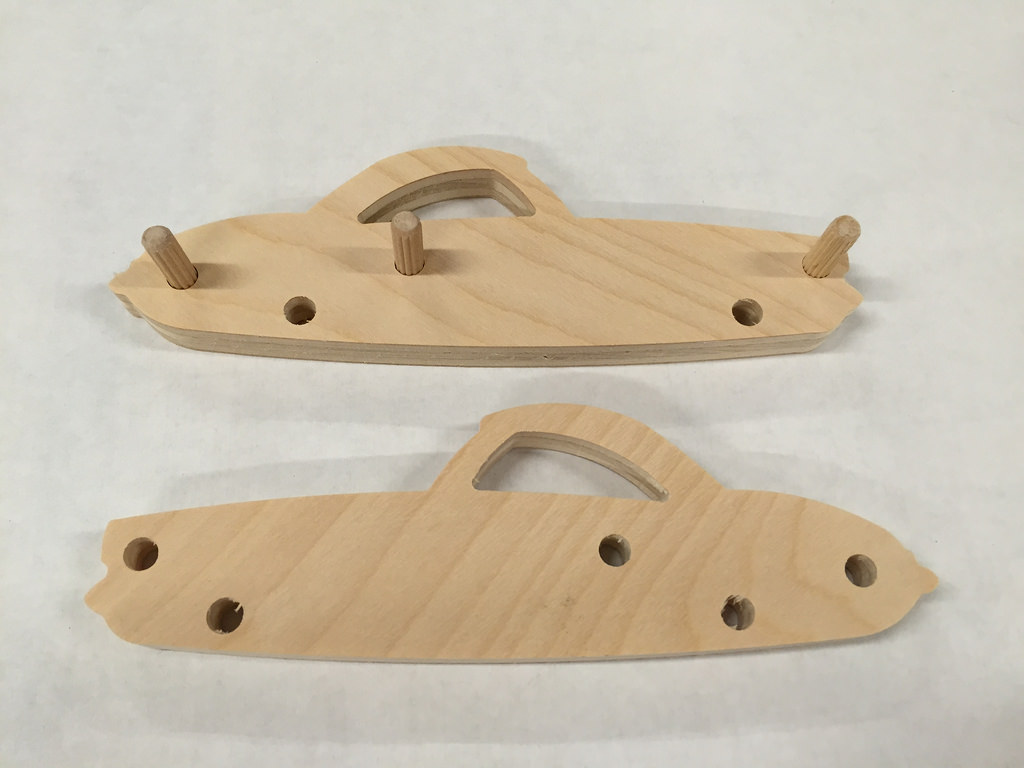
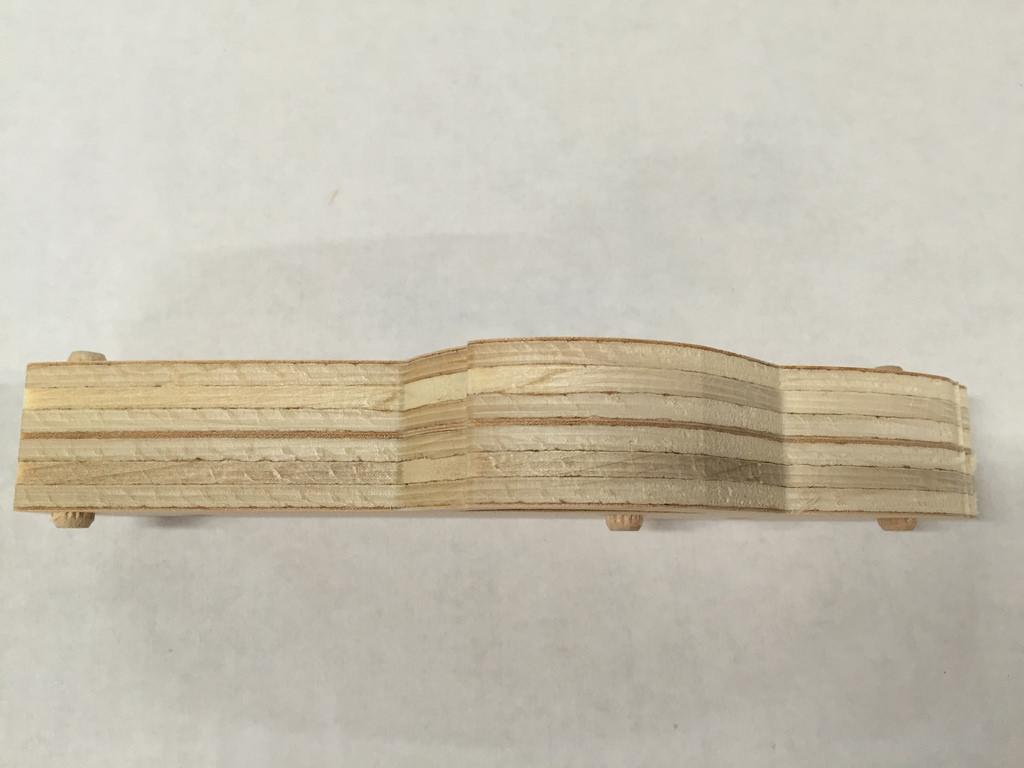
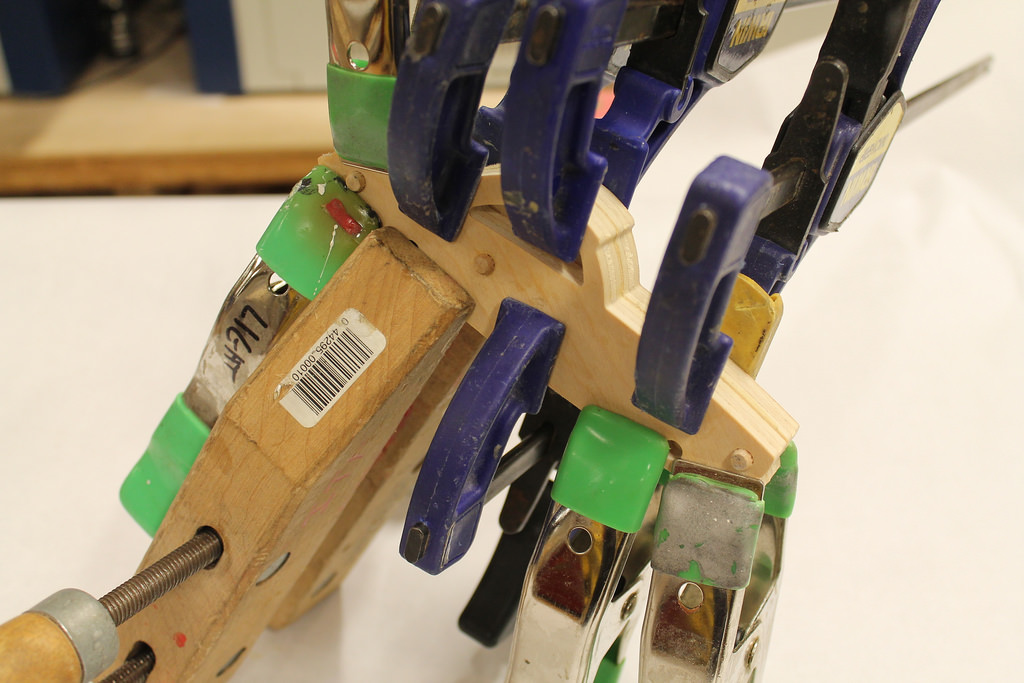
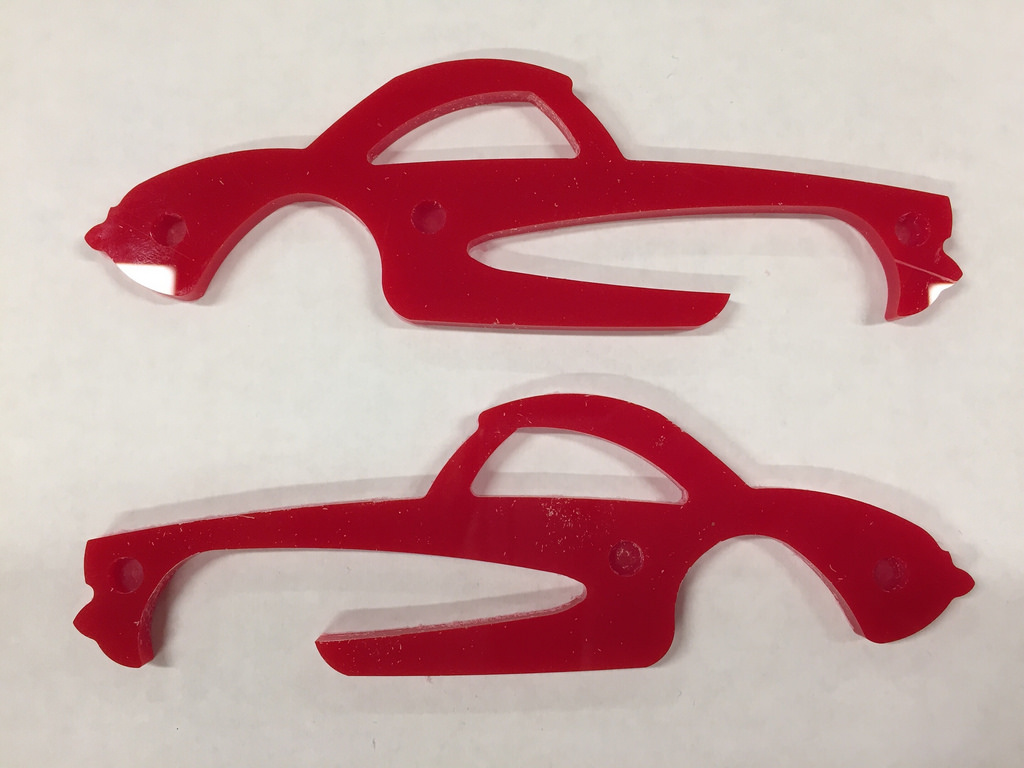
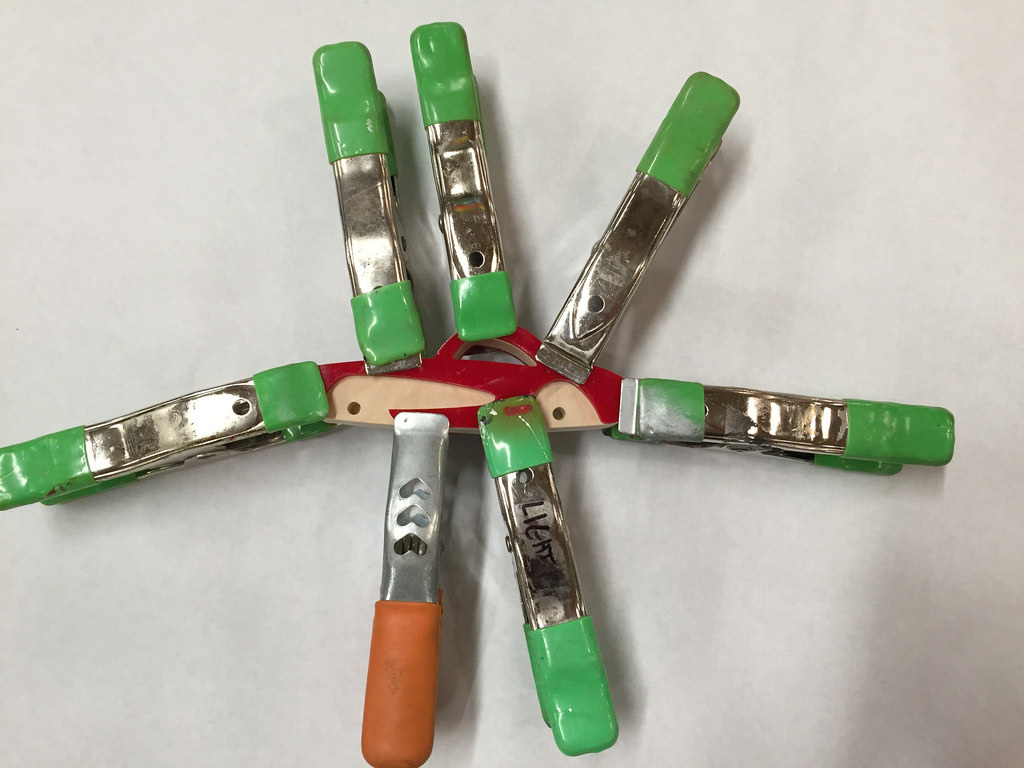
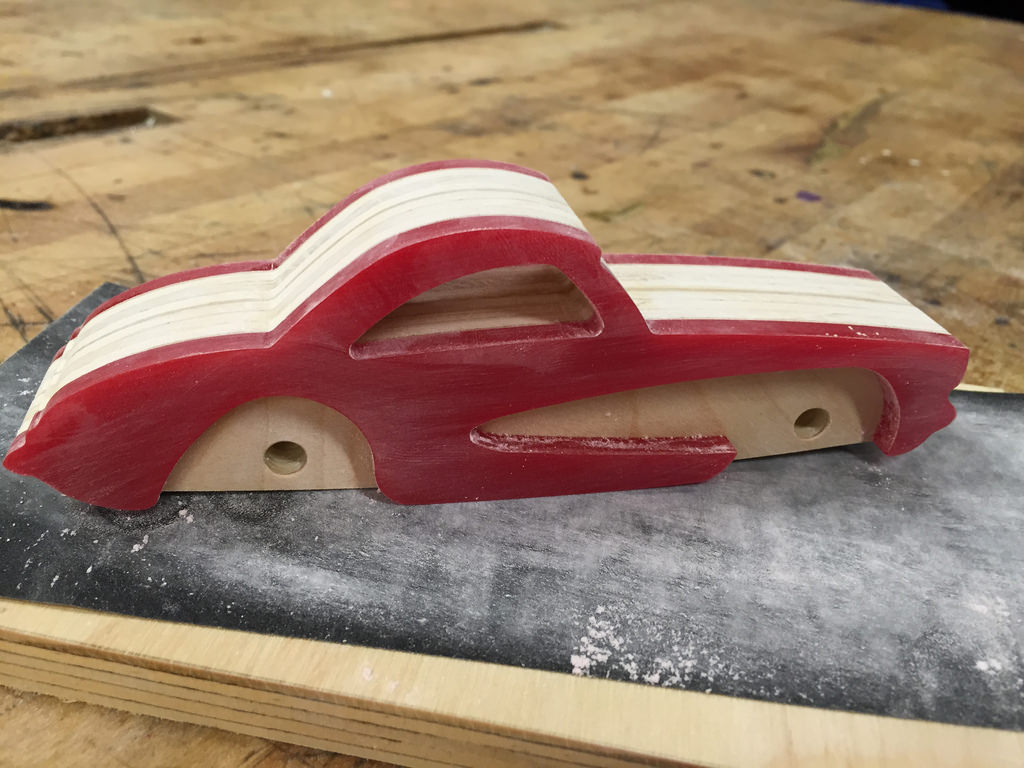
The plywood can be a little fuzzy after milling. Give the plywood pieces a quick sanding with the 220 and 400 sandpaper before glue-up.
Place a dowel pin in each of the three holes indicated in one of the images shown here.
Spread a little bit of wood glue on the other piece of plywood (a little goes a long way). Squeeze the two pieces of plywood together, using the dowel pins to align the two halves. The dowel pins should stick out a little on both ends.
Clamp the two pieces together. Clean any glue that squeezes out with a wet paper towel. Allow to dry overnight.
Place the red pieces of milled acrylic on a flat surface, holes side up. Spray the adhesive on the acrylic surfaces.
Fasten a piece of acrylic on both sides of the plywood car. The acrylic should line up with the dowel pins that are sticking out. Clamp the assembly with spring clamps. Allow to dry overnight.
When everything is dry, sand all the outer edges and inside the window with 220 sandpaper. Then sand everywhere with 400 sandpaper, including the acrylic surfaces. You can continue to sand with higher and higher grits to get a smoother finish.
Wax the Acrylic (Optional)
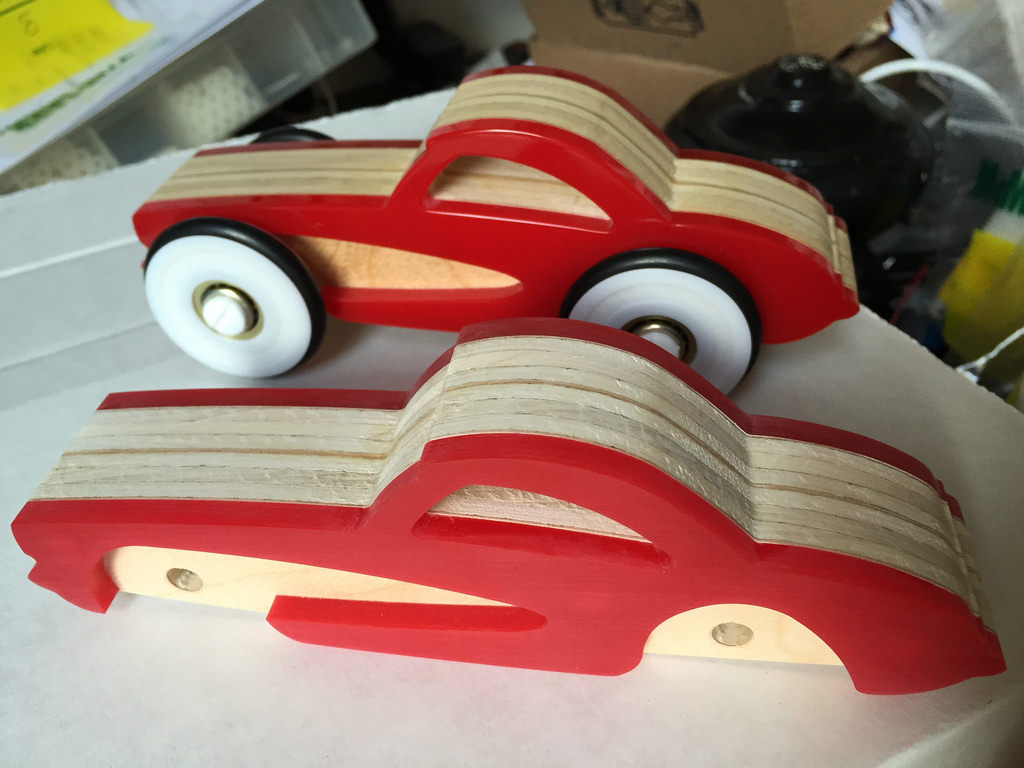
Obviously not everyone has access to a wood lathe with a wax-polishing wheel attachment, but if you do, this is the recommended way to finish your Bantmobile. Just a few minutes on each side using only the Tripoli Polishing Buffing Compound leaves an amazing glass-like finish. It also has the added benefit of softening all of the sharp edges of the acrylic. In the image here, the car in the back is sanded and waxed but the one in the front is just sanded. Big difference!
Assemble the Wheels and Roll
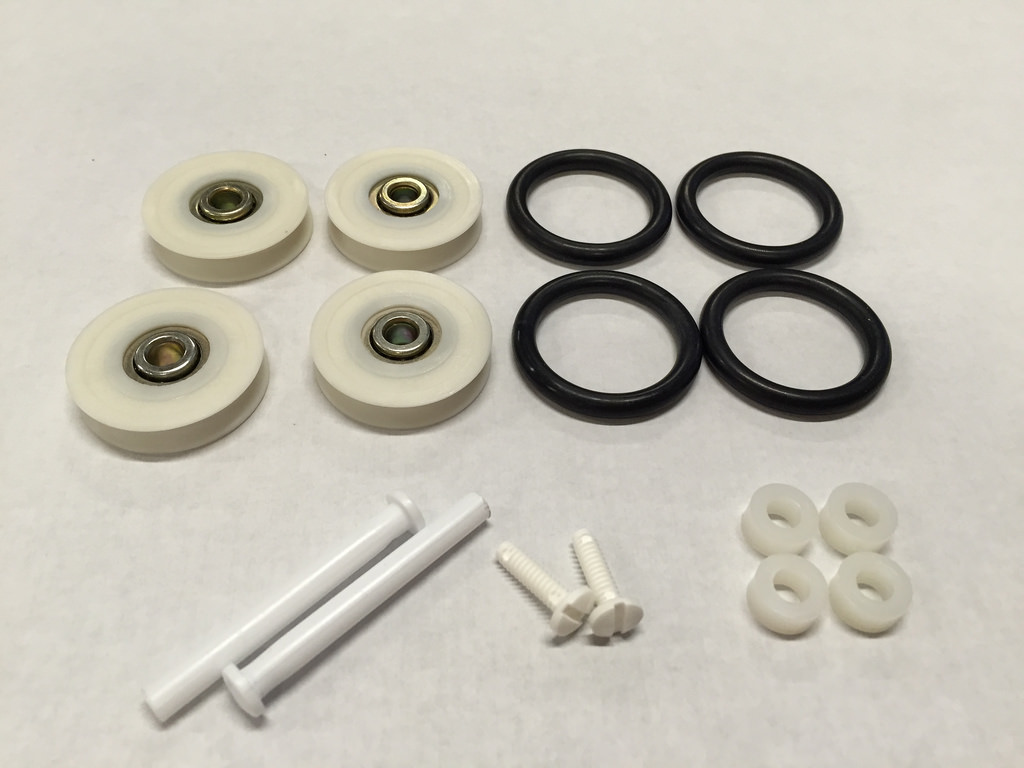
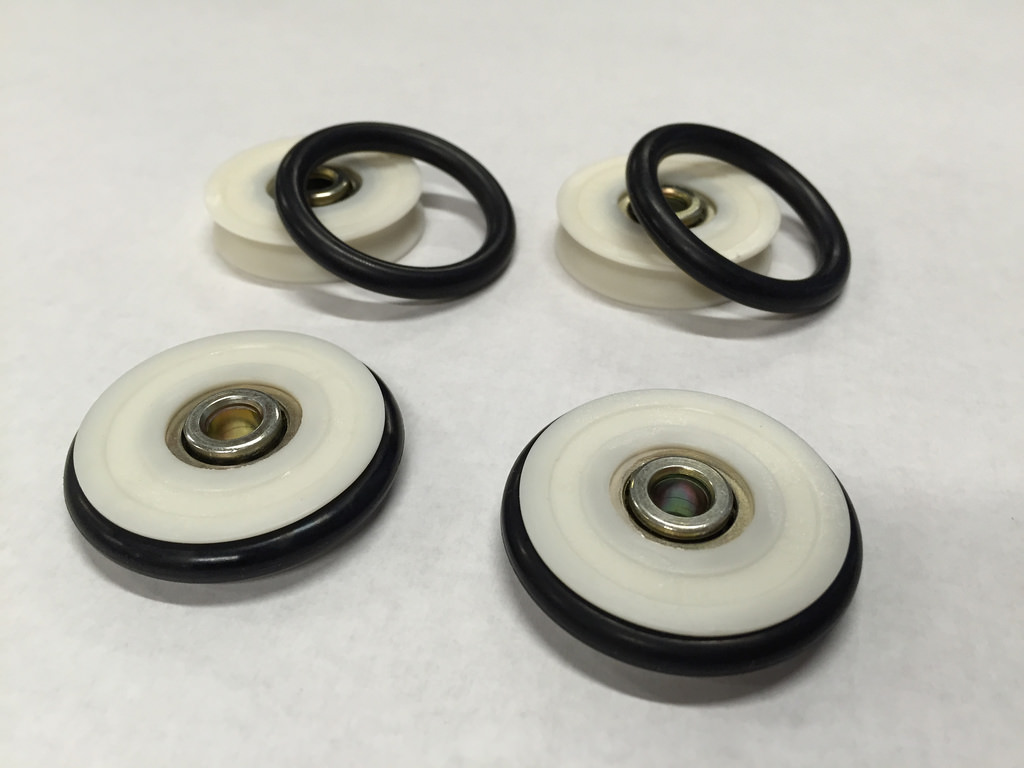
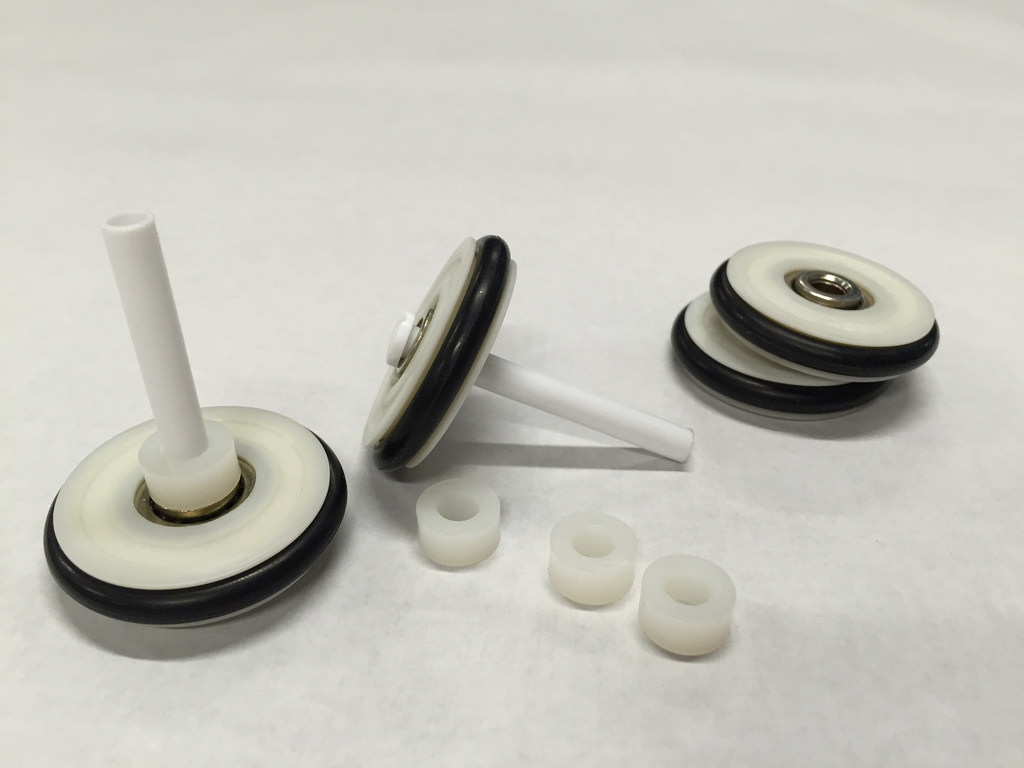
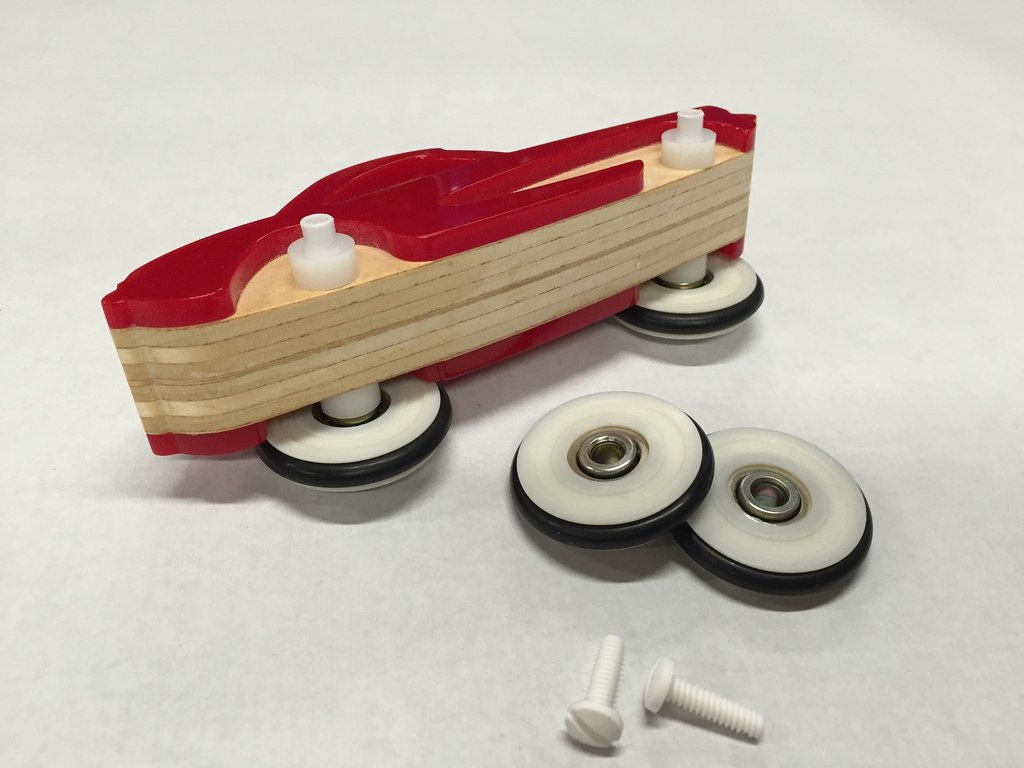
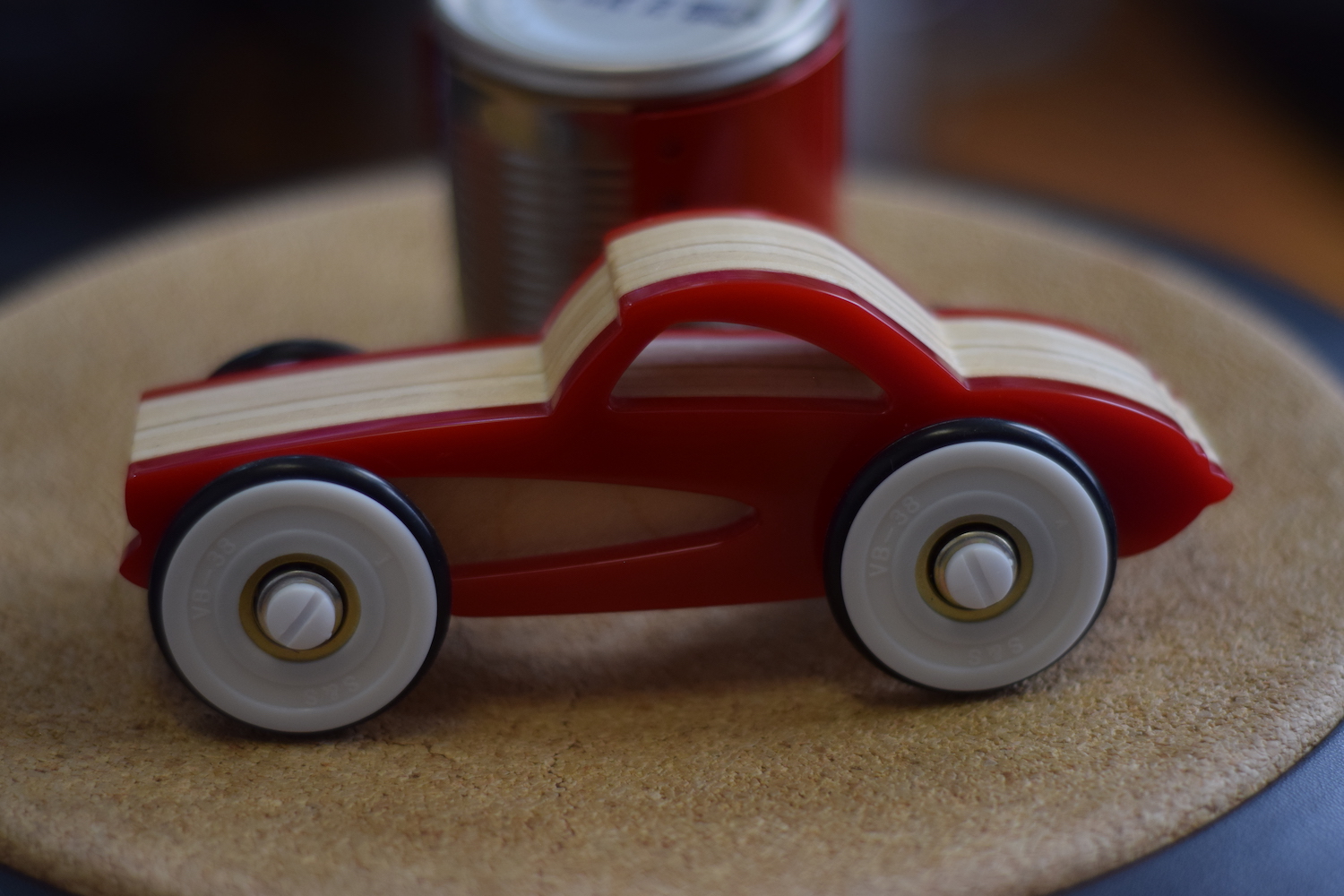
Put a rubber O-ring around the outer edge of each of the white door rollers.
Put one roller onto each binding barrel, then put one nylon spacer on each binding barrel.
Slide each binding barrel into the holes in the wooden car body. Then place a nylon spacer onto each binding barrel.
If the holes are clogged with dried wood glue, clear them out with a drill and ¼" drill bit.
Place a roller onto each binding barrel and screw in the binding barrel screws with a flathead screwdriver. Do not over-tighten — make sure the wheels spin freely.
That’s it, you’re ready to roll!