Baileigh Combination Shear Brake Roll: a Quick Start Guide for Pier 9
by tinkertinker in Workshop > Tools
8324 Views, 54 Favorites, 0 Comments
Baileigh Combination Shear Brake Roll: a Quick Start Guide for Pier 9
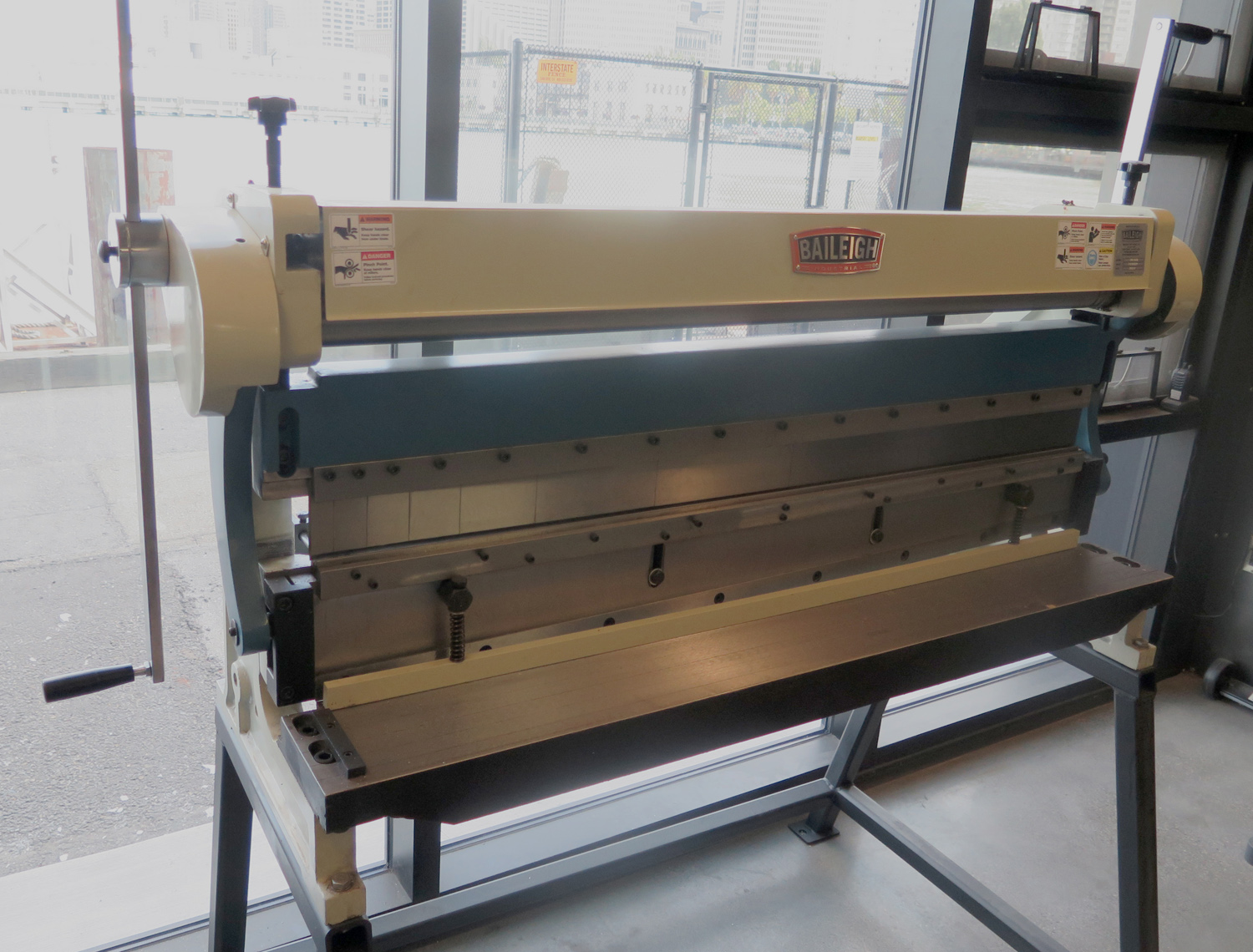
The Baileigh Combination Shear/Brake/Roll is located at the Autodesk Pier 9 Workshop in the Metal Studio. If you want to work with sheet metal at Pier 9, this tool is for you.
The Baileigh Combination tool can shear mild steel sheet up to 16ga. and up to 52" wide.
It can make 90 degree or greater bends in 16ga. mild steel sheet. By removing some "fingers" of the brake, you can make adjacent bends, such as a 5-sided box.
It can roll the same material into curves or cylinders as small as ~3" radius. The roller dies on the Baileigh machine also have grooves for rolling round rods. They are sized for 1/4", 5/16", and 3/8" diameter mild steel rods.
Requirements for using this machine at Pier 9:
- Take General Workshop Safety Class
- Read through this Instructable
- Do your first operation with Shop Staff
Safety First
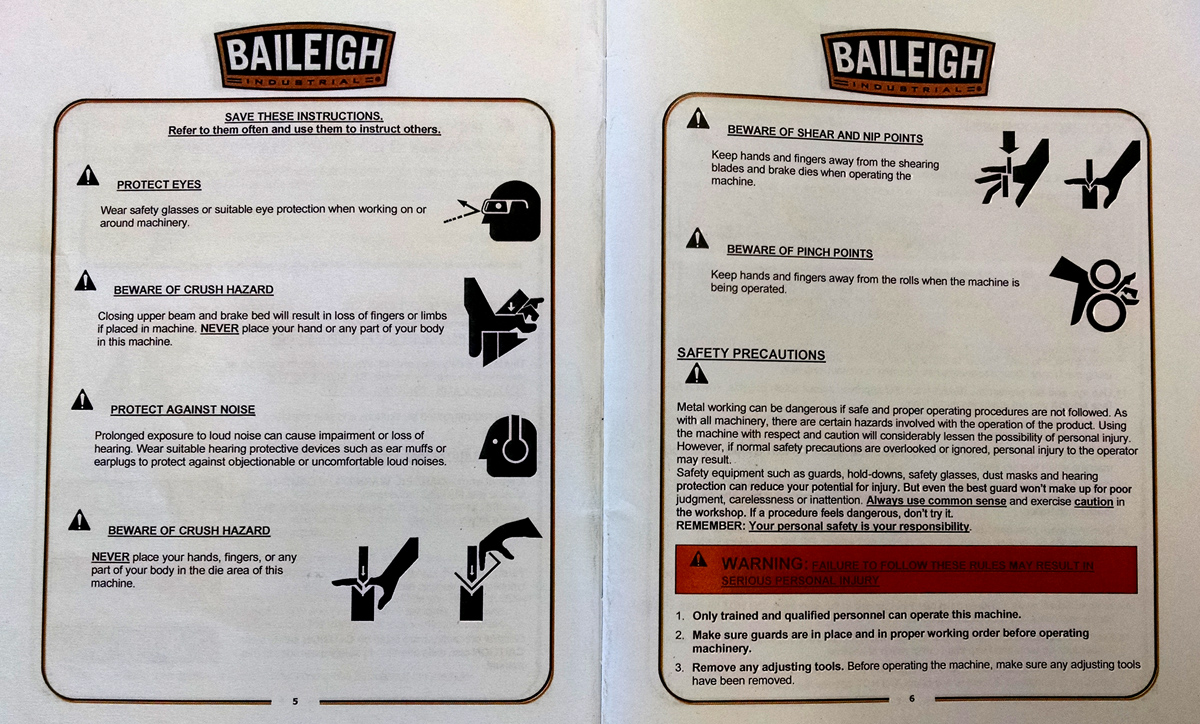
Protect yourself and the tool:
- Wear Safety glasses when using this tool
- Sheet metal edges, especially sheared edges, can be extremely sharp. Gloves may save your hands from nasty cuts.
- Anything harder than mild steel (for example: stainless steel, titanium) OR thicker than 16ga. (0.0598") can damage the tool. Check with Pier 9 shop staff if you are working with a hard material or a material of unknown hardness.
- This tool has many Crush, Shear, Nip, and Pinch Points. Always be aware of where your hands are when operating this tool. Avoid distractions such as conversations and using your phone when operating this tool.
The Baileigh Combination Shear/Brake/Roll uses a single crank to operate all three functions. The cranks at either side of the machine roll the rollers while simultaneously driving a block that contains the shear blade and the brake die up and down. It is important to be aware that when you are using one function of the machine, the other two are also moving, and can be dangerous to you and others.
Get Answers:
- Have a general question about the Baileigh Combination Tool? The tool manual is located in the binder marked "Metal Shop Manuals; Large Standing Tools" on the hardware wall.
- Need more information? Always ask Shop Staff before experimenting with the machine.
Shearing
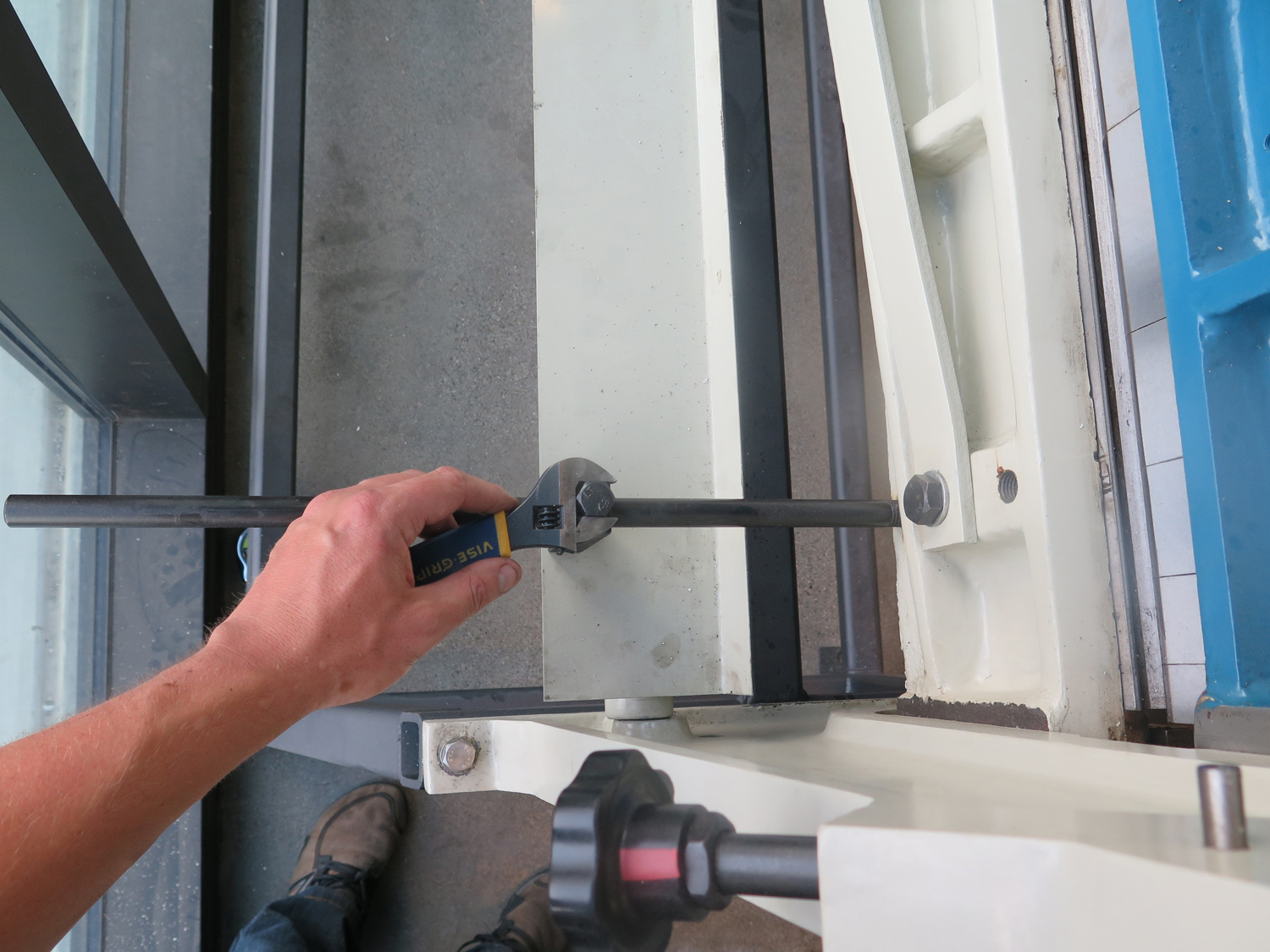
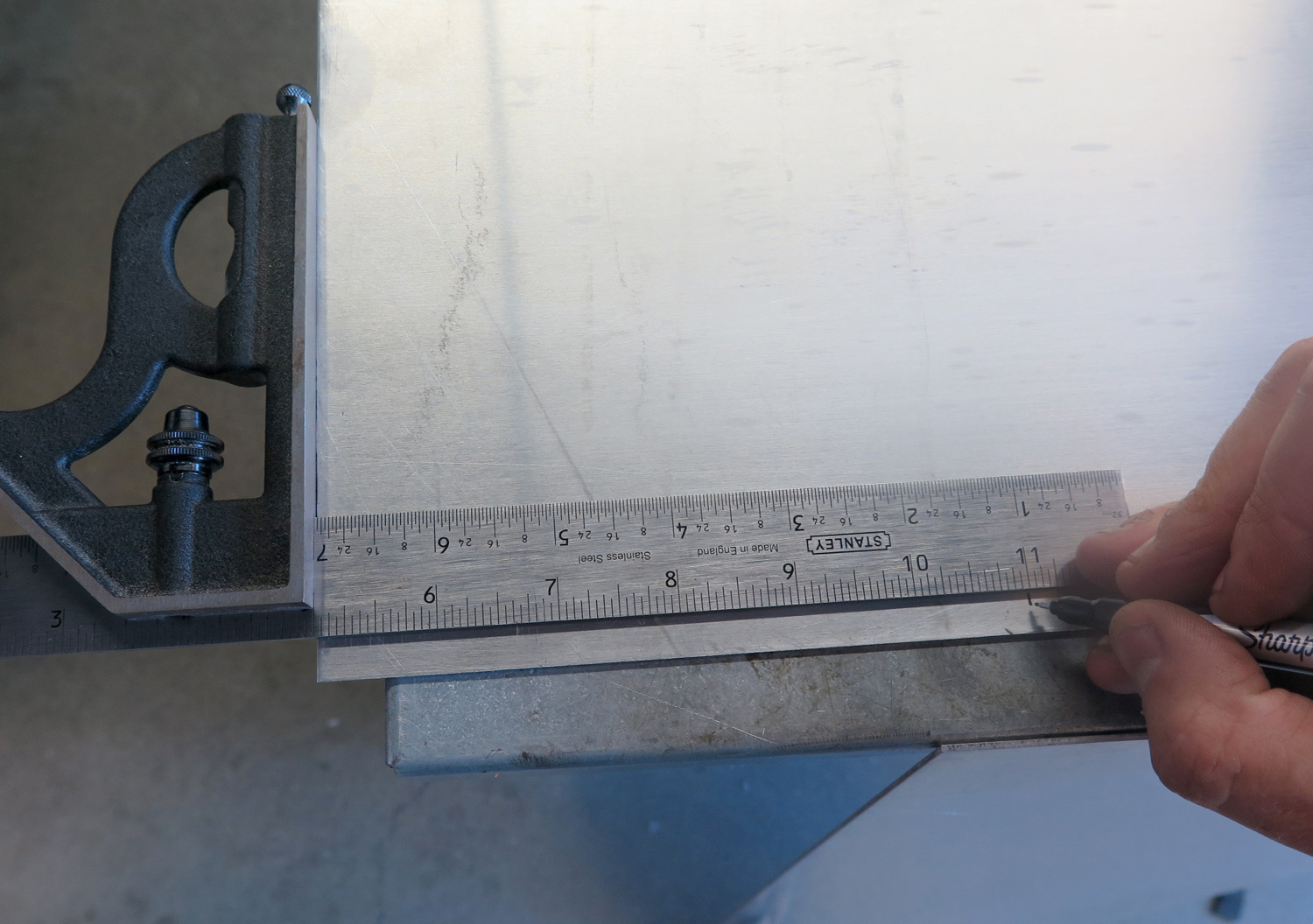
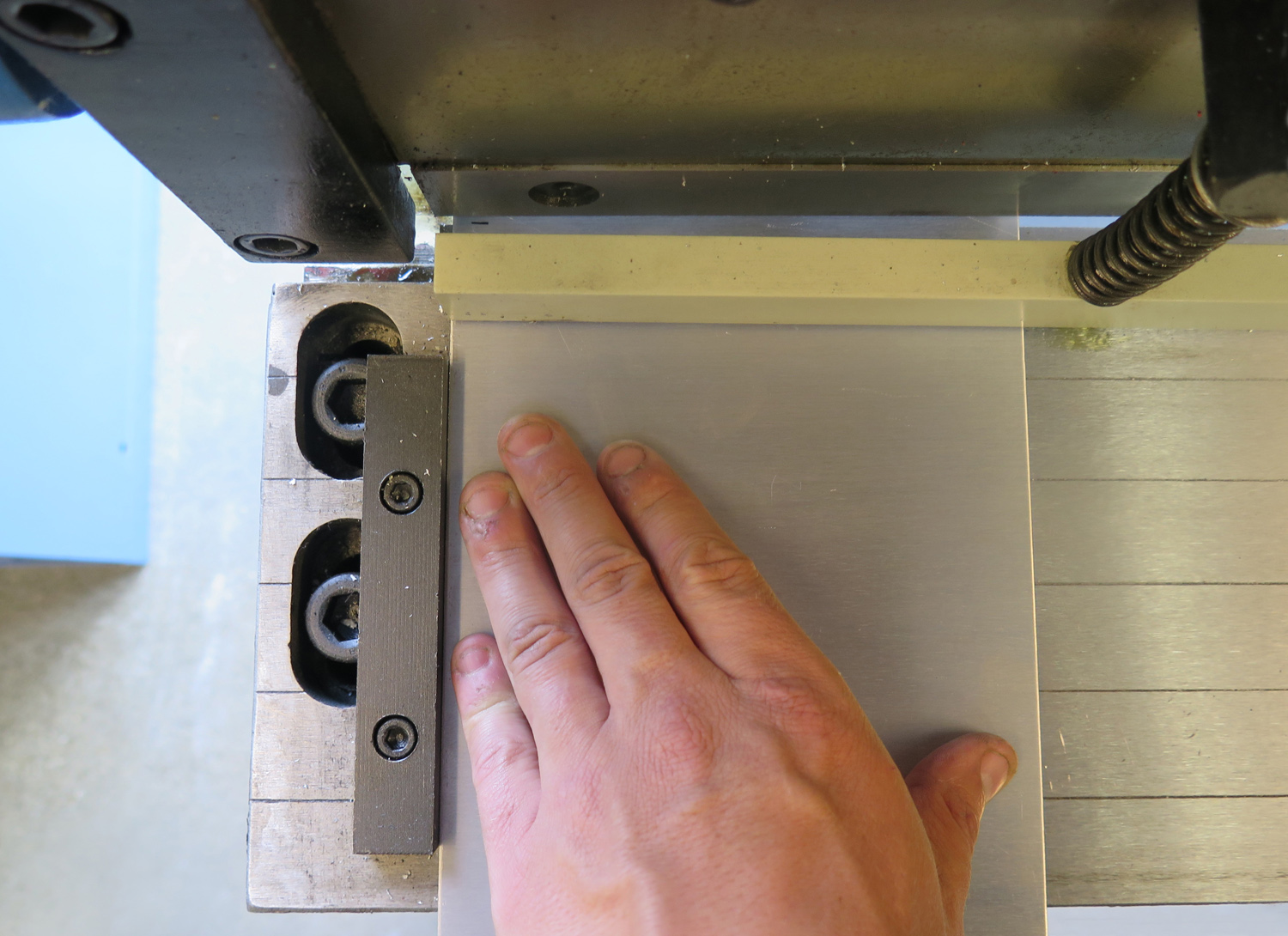
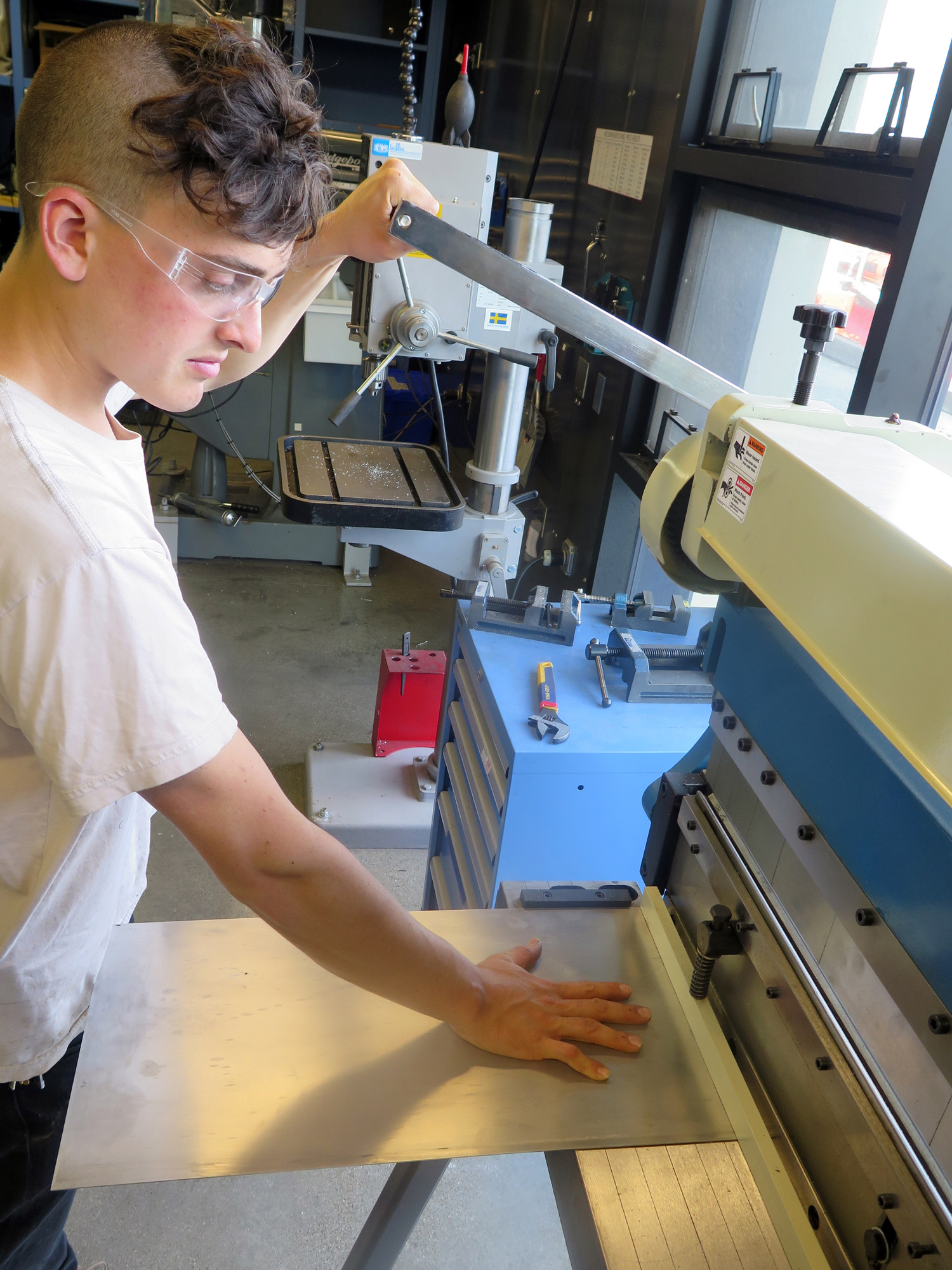
The shear is located at the base of the machine. There is a pressure plate in front of the blade that holds your material down on the table (as well as keeping your fingers out). There is a 90 degree fence on the left hand side of the table for making square cuts. There is also an adjustable guide behind the machine that can be set for multiple uniform cuts.
- Mark you metal where you want to cut it. If you are going to use the fence at the left side of the table, one mark at the left end of the cut is fine.
- Rotate the handle at either end of the machine until the shear blade is at its highest point.
- Place your material in between the table and the pressure plate, and line your mark up by eye with the edge of the blade.
- Keep your left hand on the material and use your right hand to lower the shear blade down until it bites into your metal. Use steady pressure to complete your cut.
- Never cut a strip thinner than 8 times the thickness of your material (0.48" for 16ga. mild steel). Thin strips can bend instead of shear, and become stuck in between the blade and table of the shear.
Braking
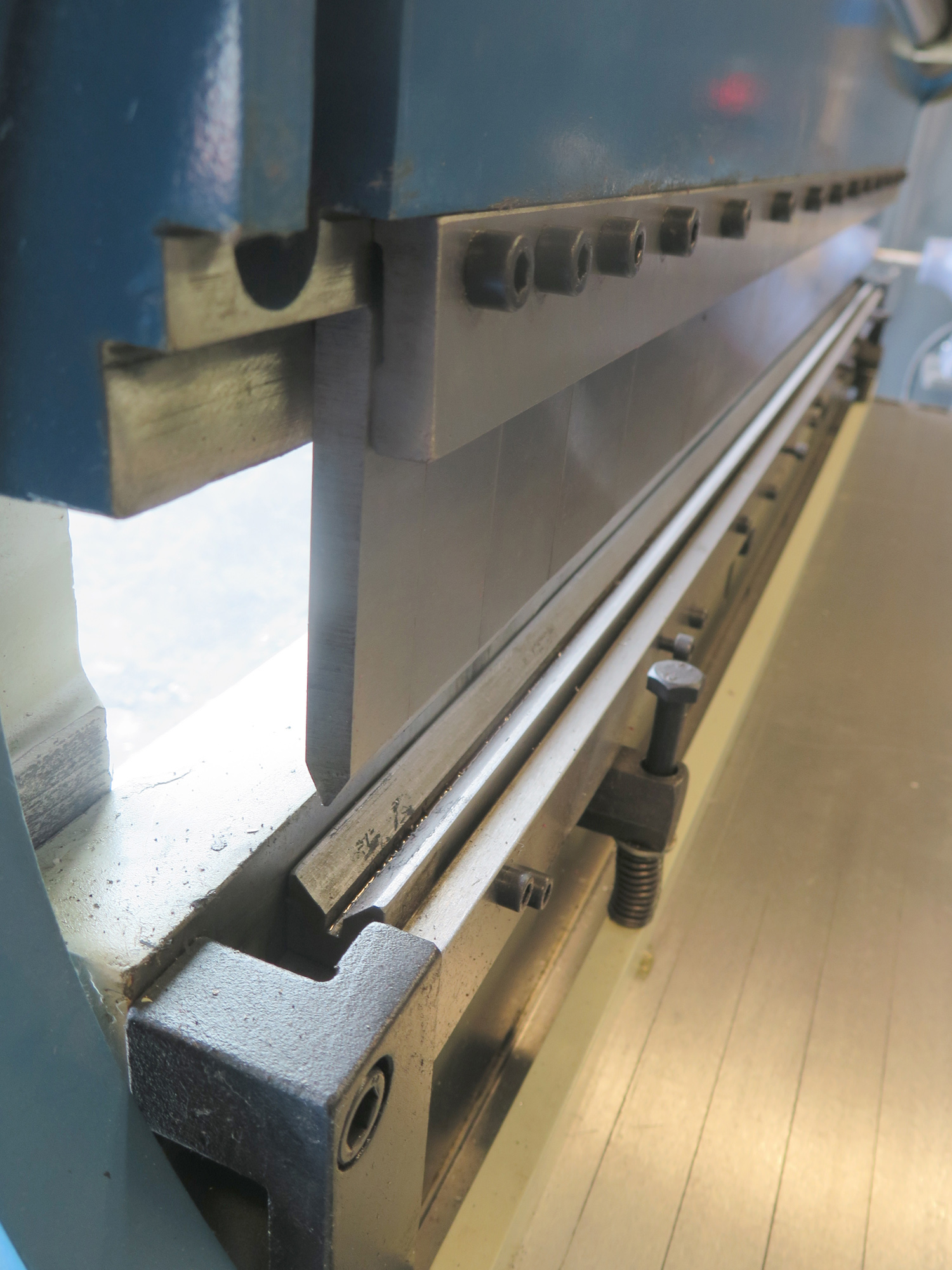
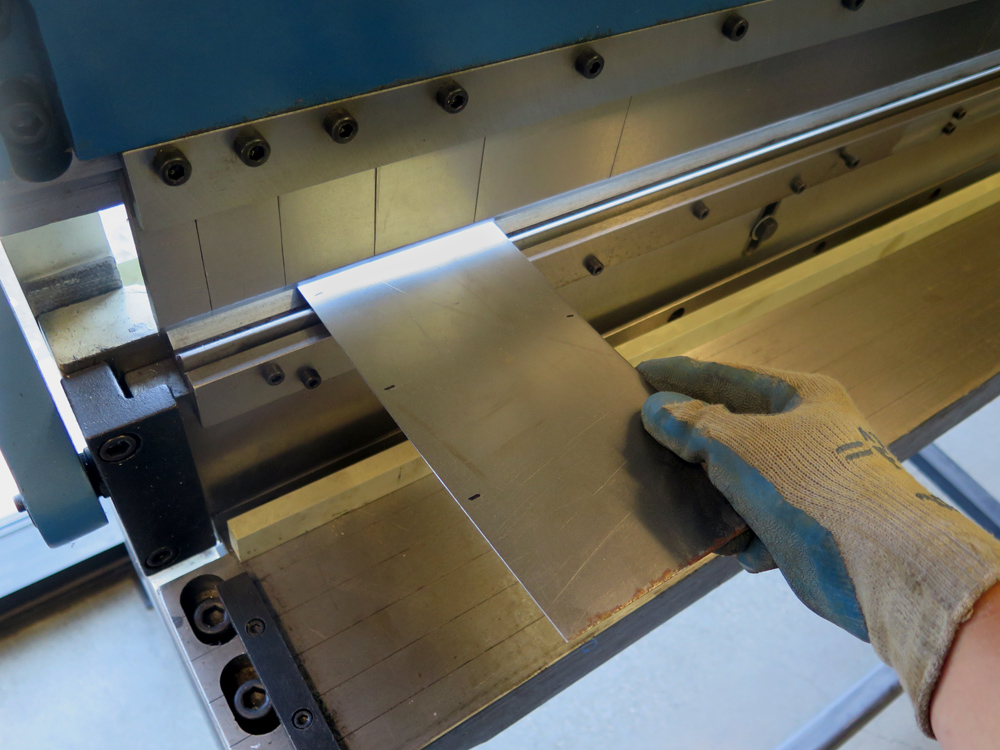
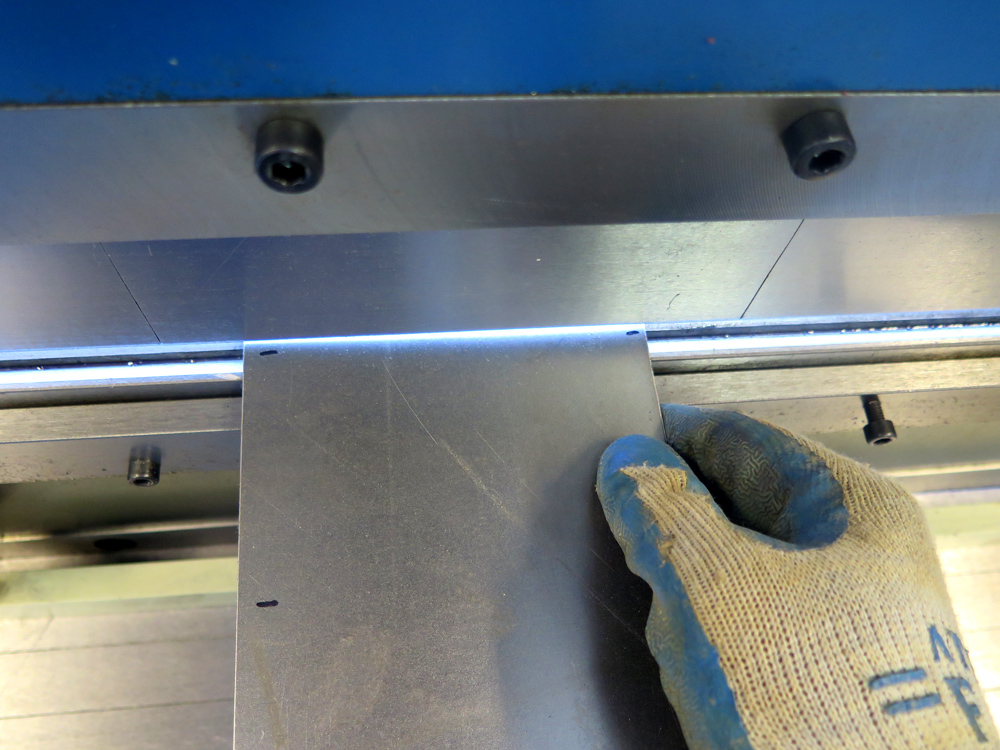
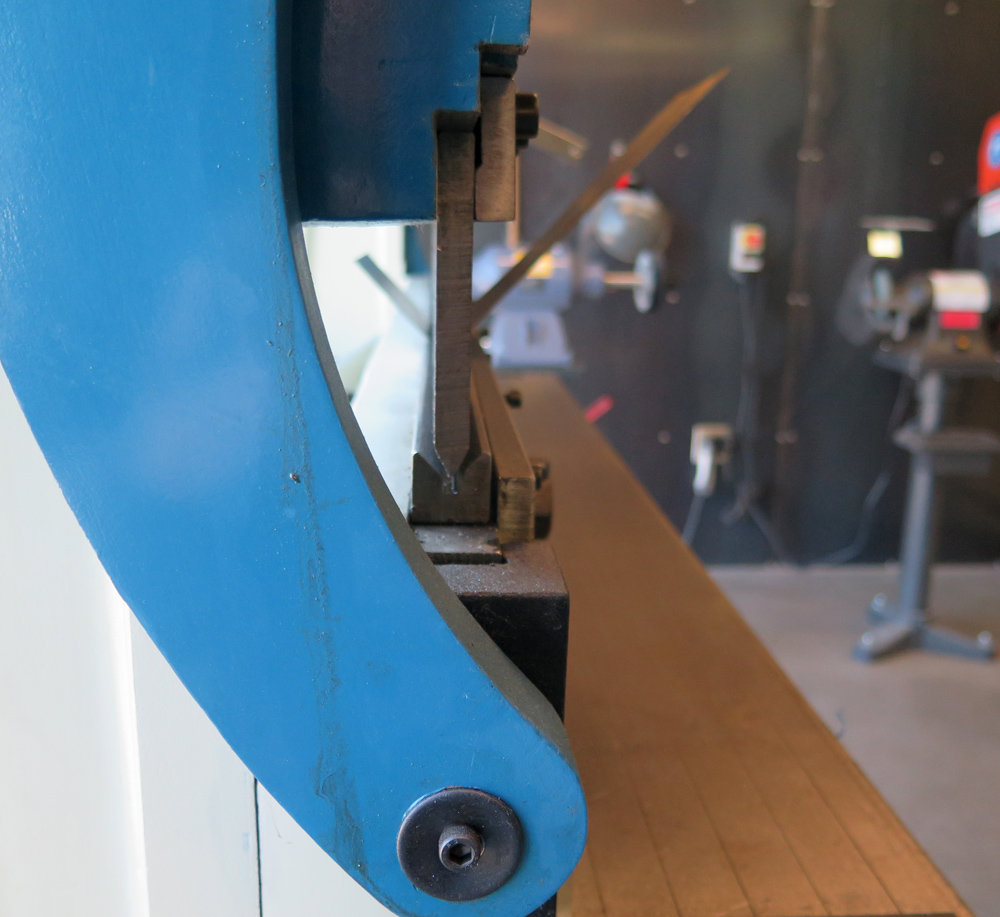
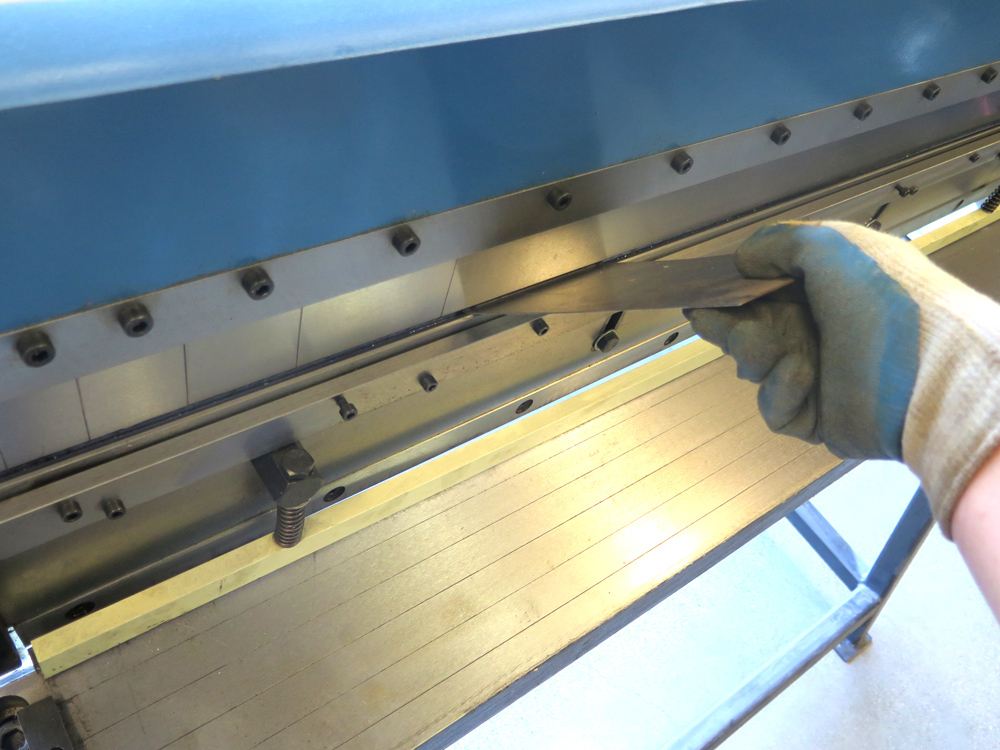
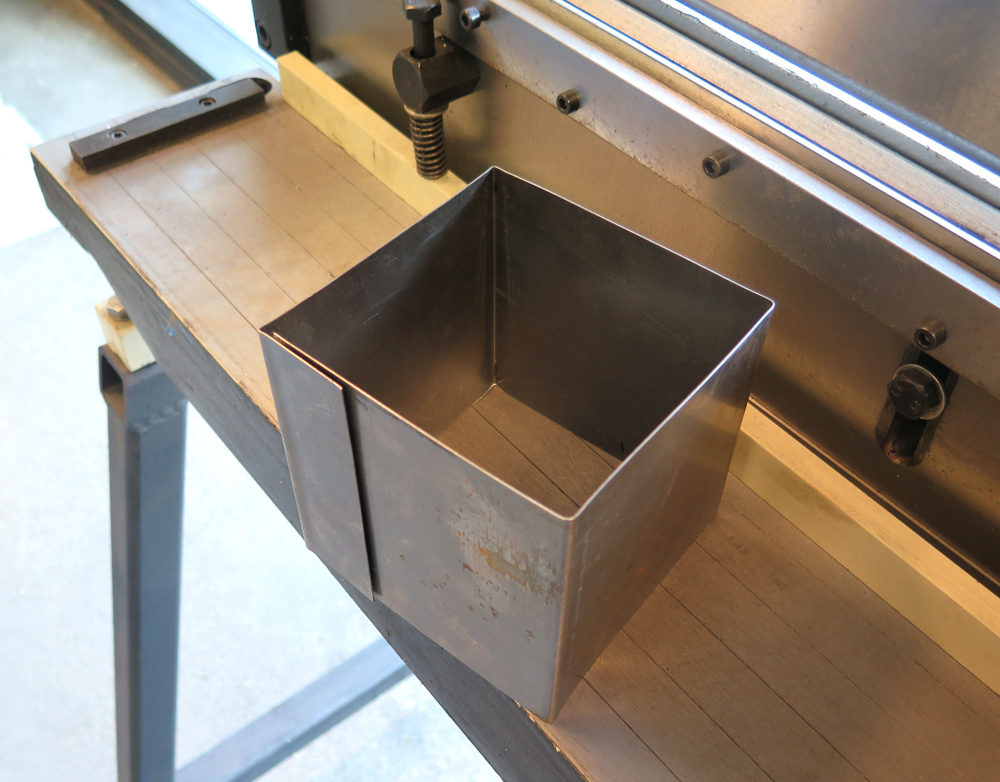
Braking (not breaking) means bending sheet metal along an edge. This method can be used to create hollow volumes, form joinery, prevent thin parts from warping, etc.
The brake on the Baileigh has two parts: a bottom V-groove die that moves up and down with the shear, and a rack of fingers that push the sheet into the die. The fingers are removable to make room for adjacent bent edges. This is great for making boxes, but be careful to test your design to make sure it will fit into and be removable from the machine.
You can use the adjustable fence behind the machine to set a stop, but it is easier and more reliable to mark your material and hold it under the brake fingers at the marks. NB: there is no 90 degree fence to make sure your bends are perpendicular to an edge; you have to use your marks or scribe a line.
- Mark your metal where you want to bend it, either at both edges or all the way across
- Raise the brake fingers using the handle at either side of the machine, and insert your material.
- Bring the fingers down onto your workpiece slowly, and watch it carefully. You will need to bend it slightly past 90 degrees to get a 90 degree bend because of spring-back, but don't just turn the crank all the way, or you'll end up with a very tight bend.
- Back up the brake and remove your material.
If you are doing several bends, or working with a large piece of material, keep in mind it can be difficult and sometimes impossible to remove your work from the machine after the bending. Try removing some of the fingers if you have trouble.
Rolling
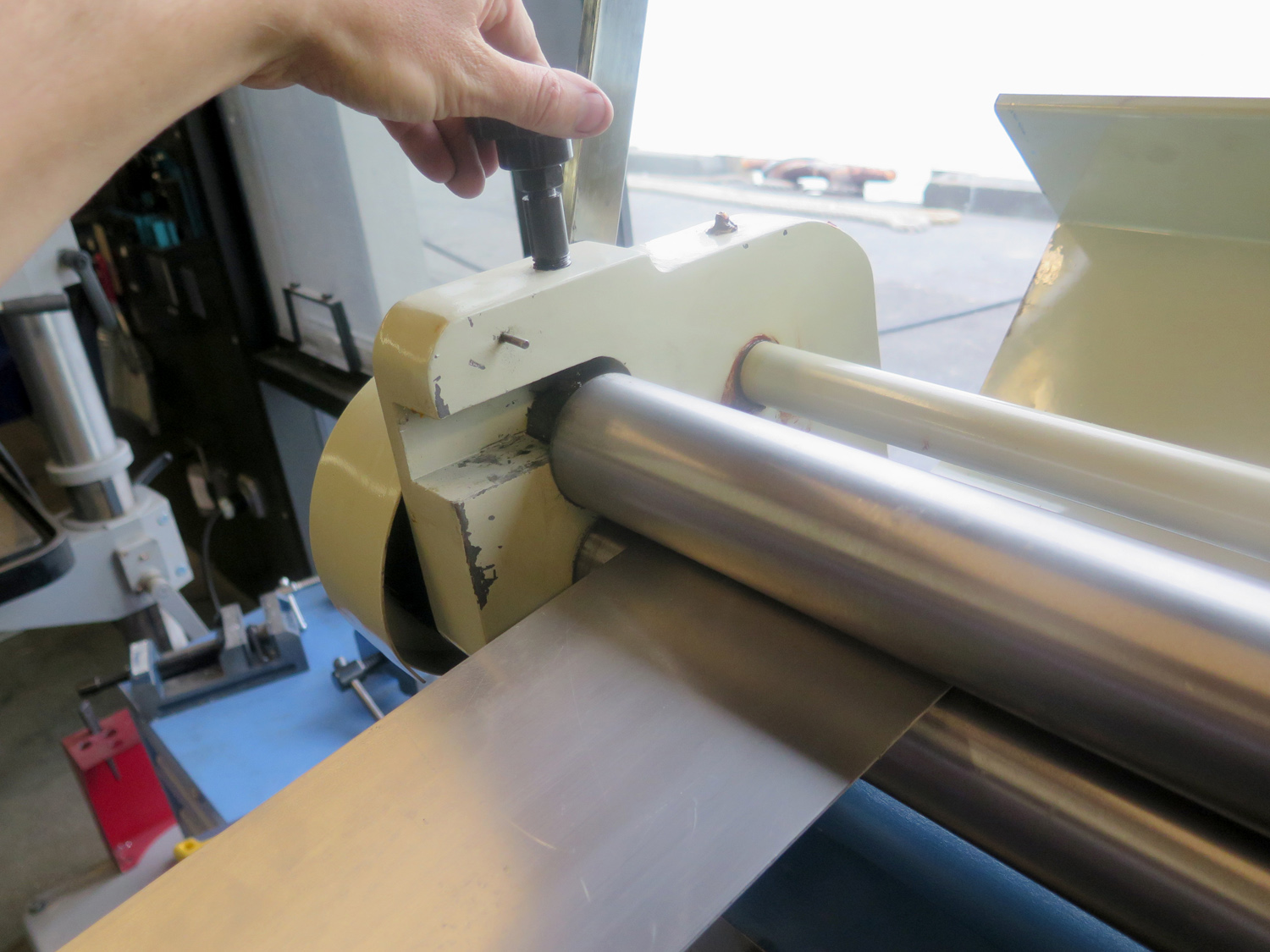
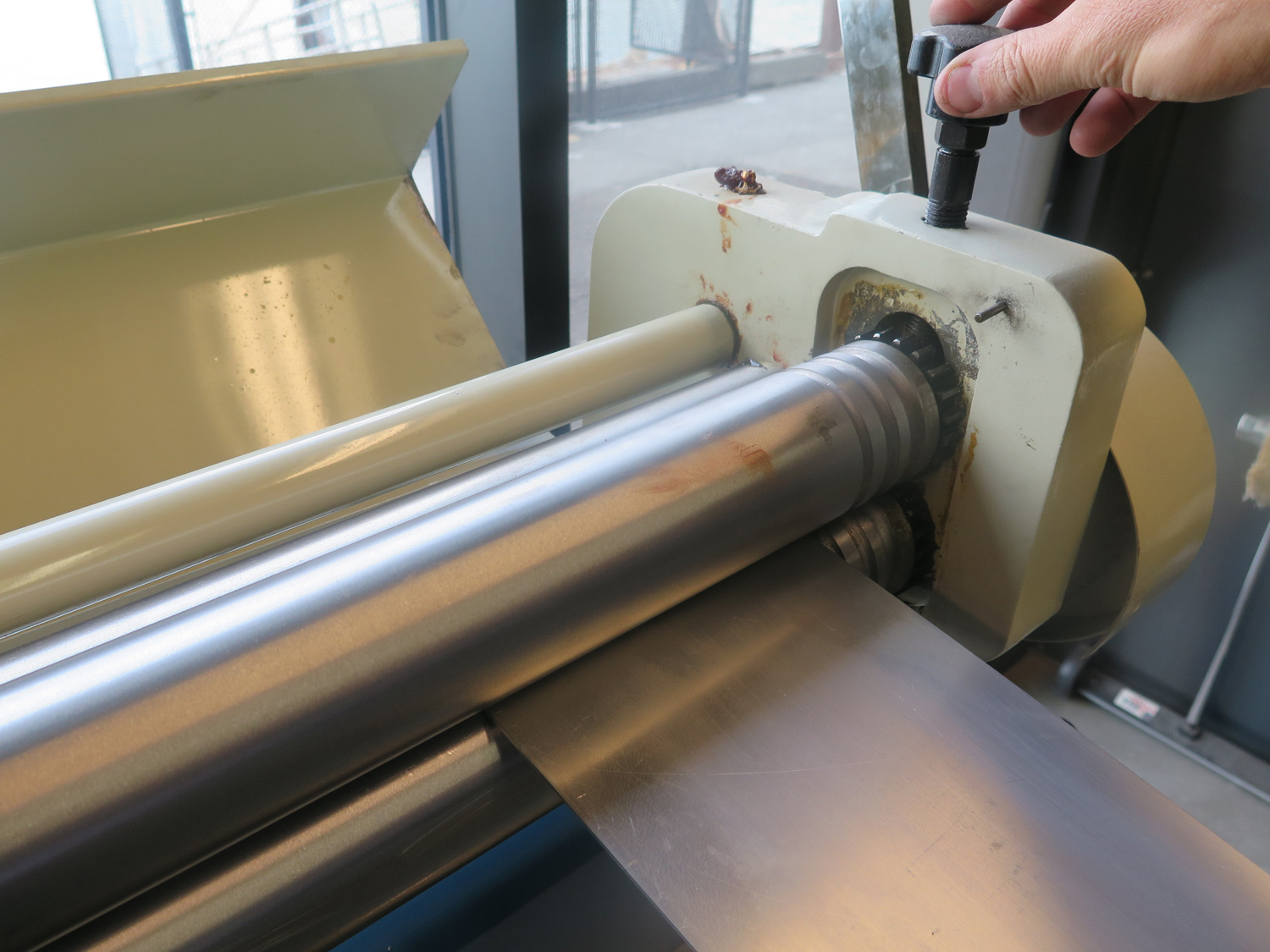
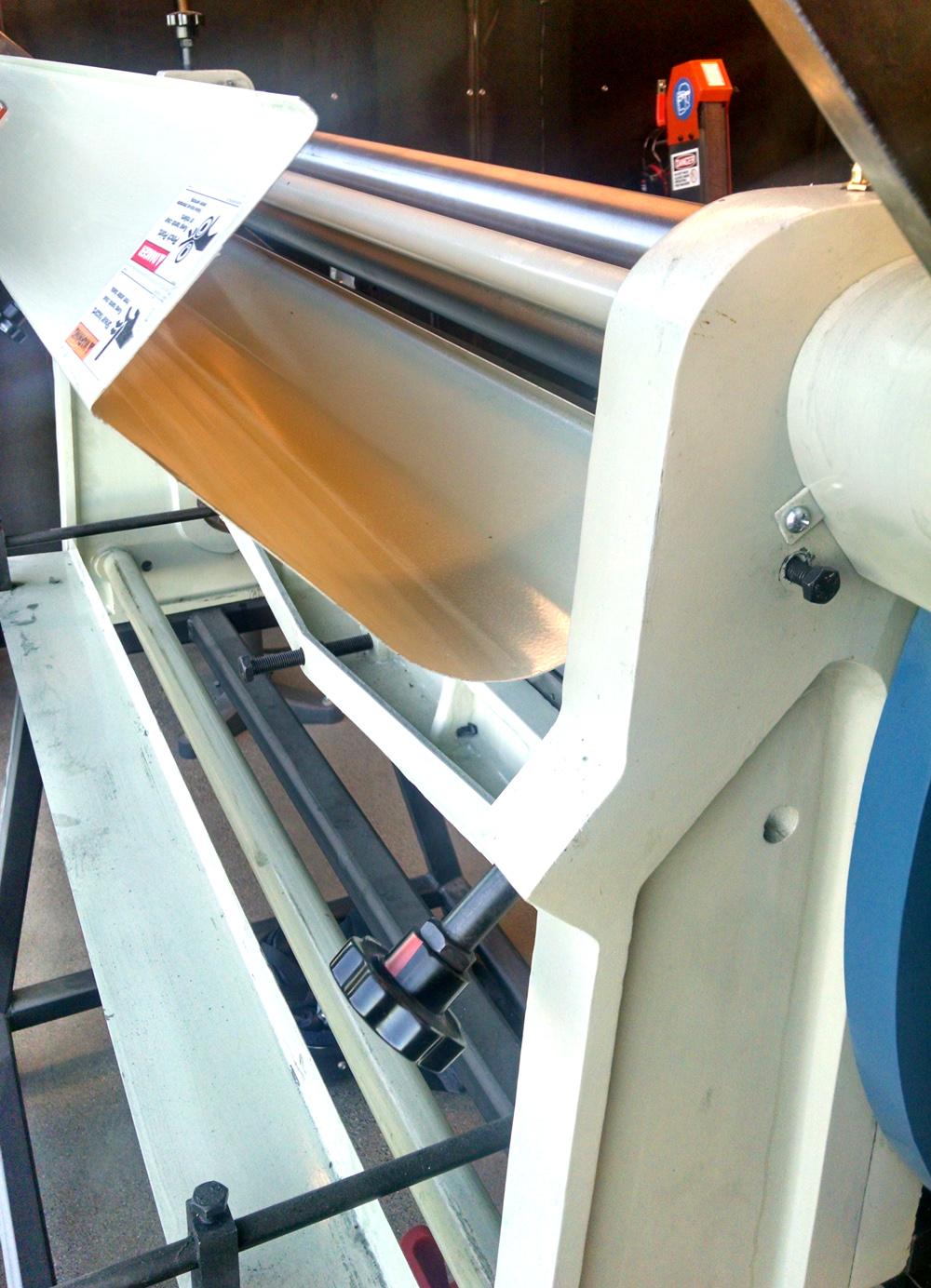
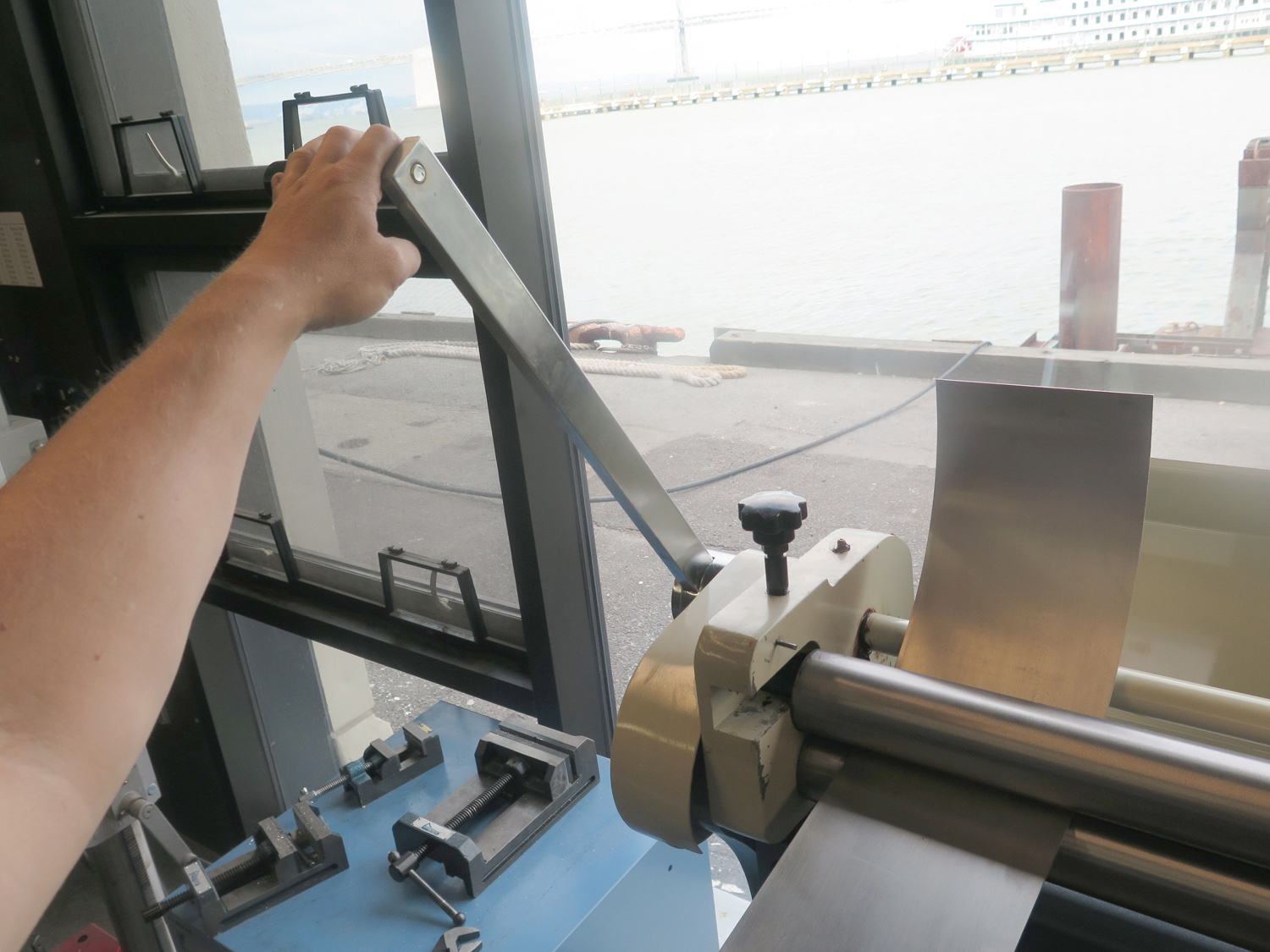
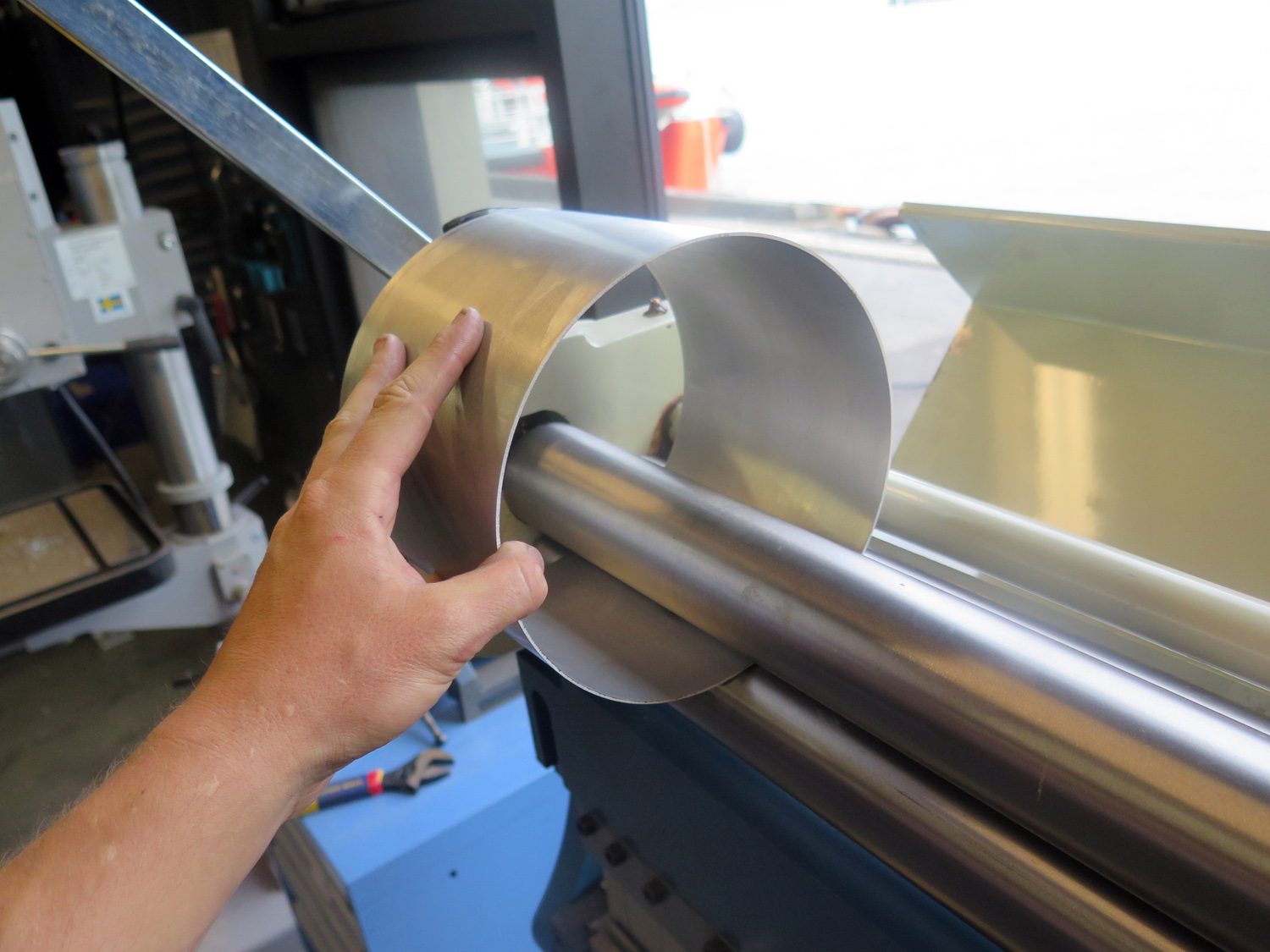
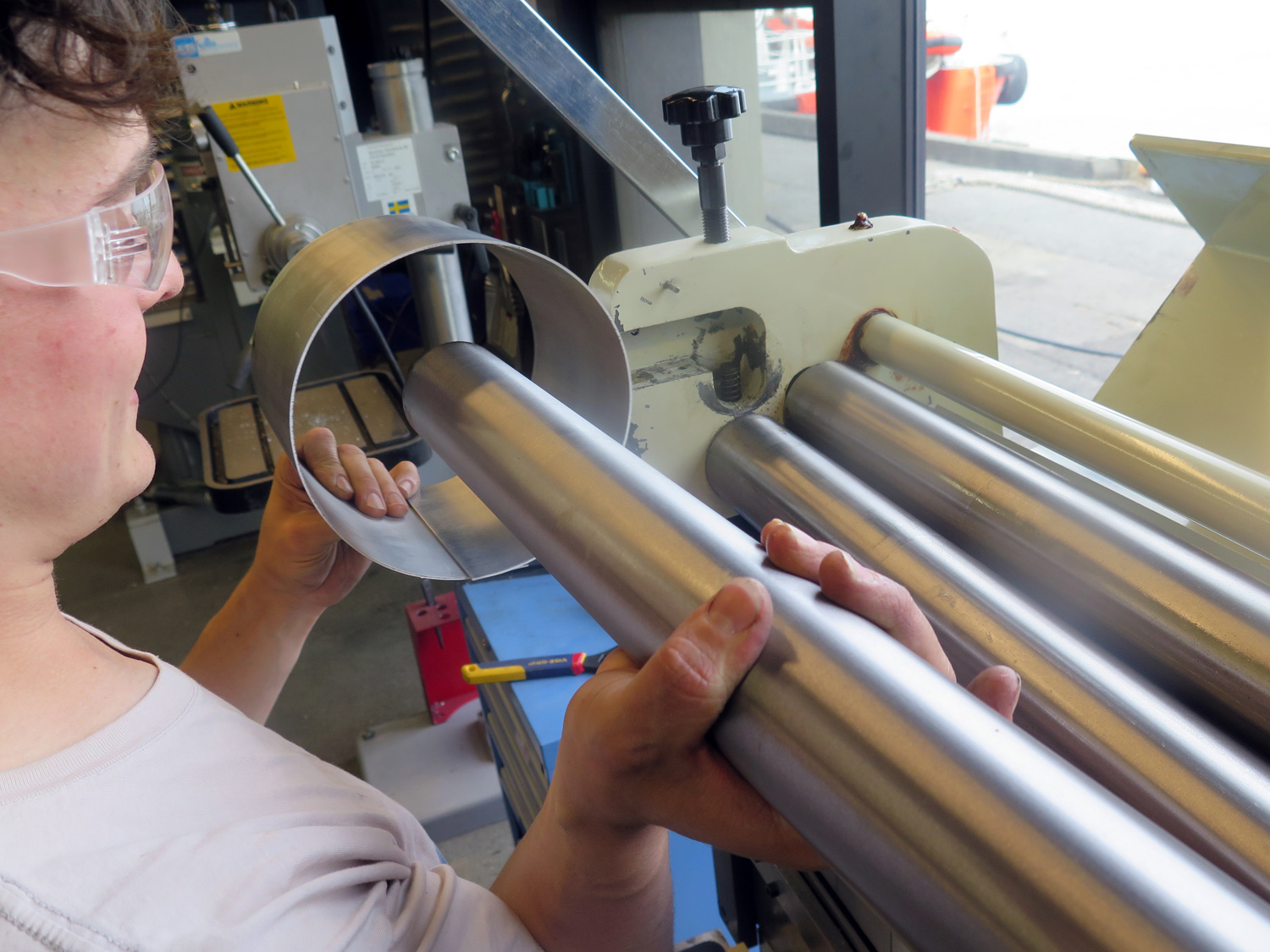
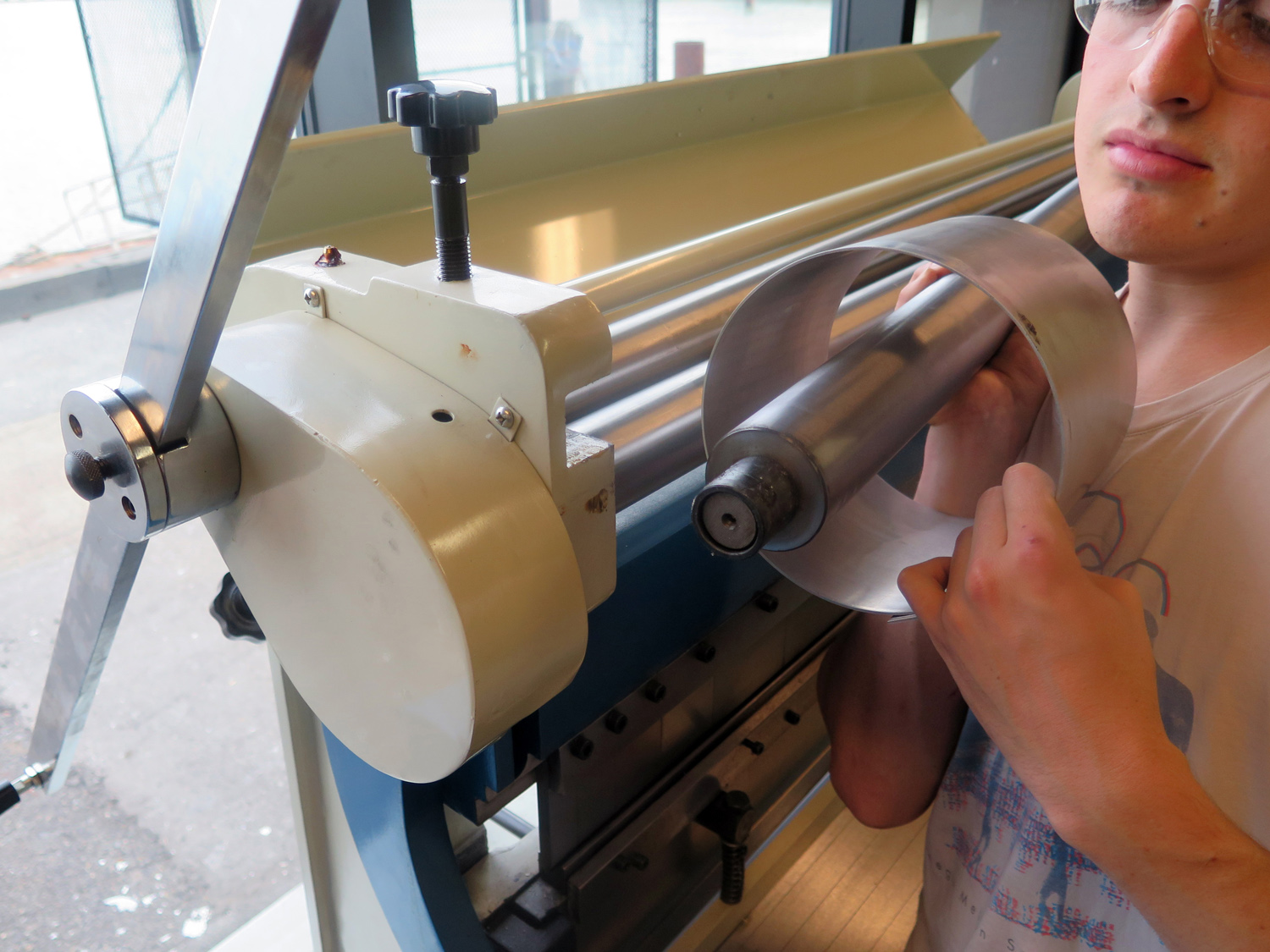
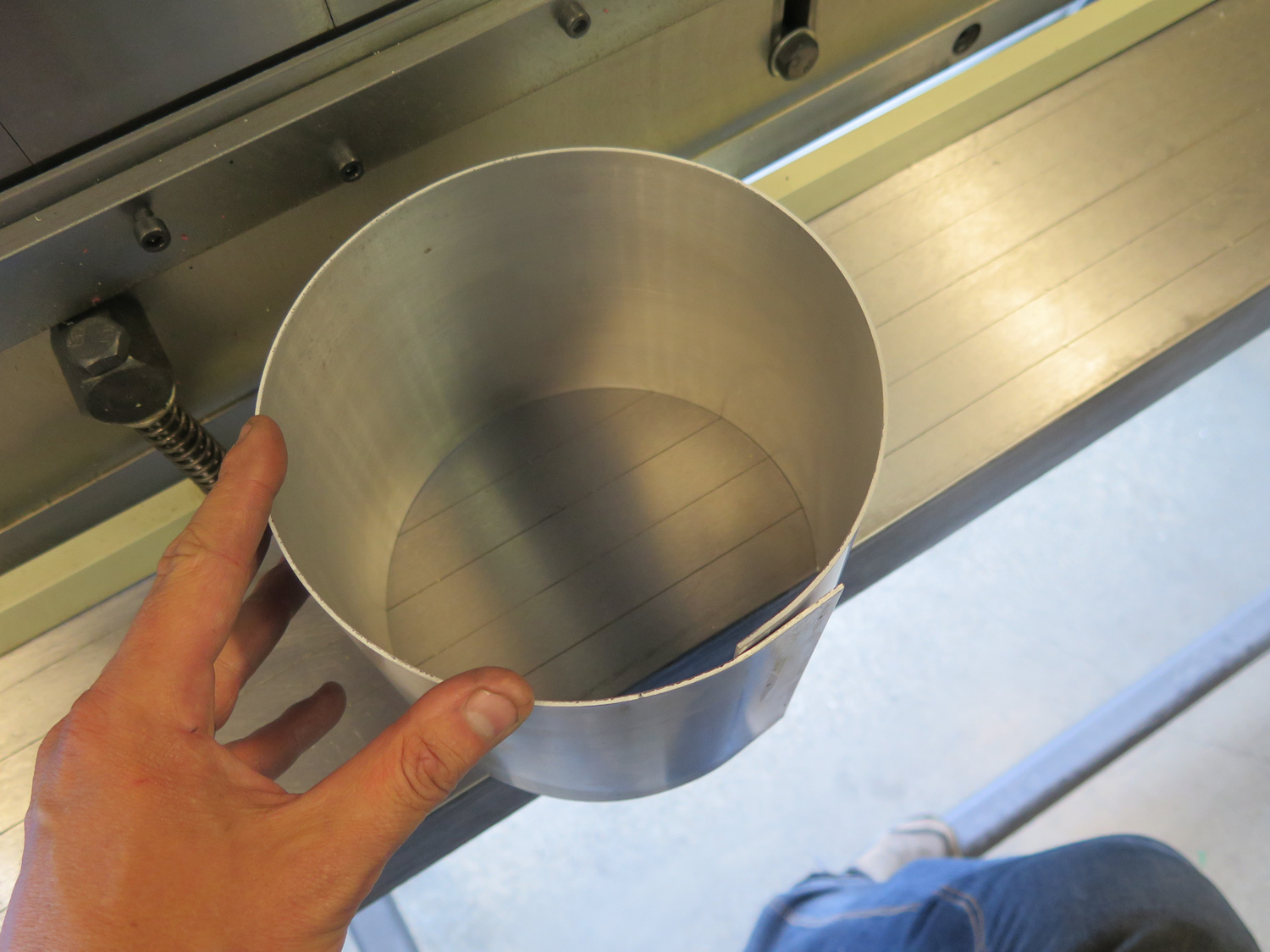
The roller dies are located at the top of the machine and are usually covered by a protective lid. Please re-cover the rolls with the lid when you are done using the machine to avoid damage to them.
There are three rolls: two at the front of the machine which are geared together to draw material through, and a third roll behind which is adjustable to control the radius of the rolled material.
There are two adjustments for you to make before you roll your material:
1. Use the knobs on top of the machine at both sides to adjust the front rollers so that your material just fits through them. Test your material, or a sample piece, at both ends of the rollers to ensure they are parallel.
2. Use the knobs behind the machine, pointing up toward the rear roller, to adjust how tight your roll will be. If the roller is not parallel, your piece will roll into a cone-shape, so if you want a cylinder, make sure the roller is parallel to the others. You can use your fingers or a piece of round bar to feel along the gap between the rollers, and use the red marks on the knobs to ensure both get turned the same amount when adjusting.
Now you are ready to roll! If you can, roll a test piece first to get a feel for how the rear roller adjustment will effect the material. You may need to pre-bend the leading edge of your material by hand to get it started. Once you start, you can roll the material back and forth while adjusting the rear roller to tighten the diameter until it is satisfactory.