Automatic Communion Wine Filler Dispenser
by BuddyBoy42 in Living > Life Hacks
743 Views, 4 Favorites, 0 Comments
Automatic Communion Wine Filler Dispenser
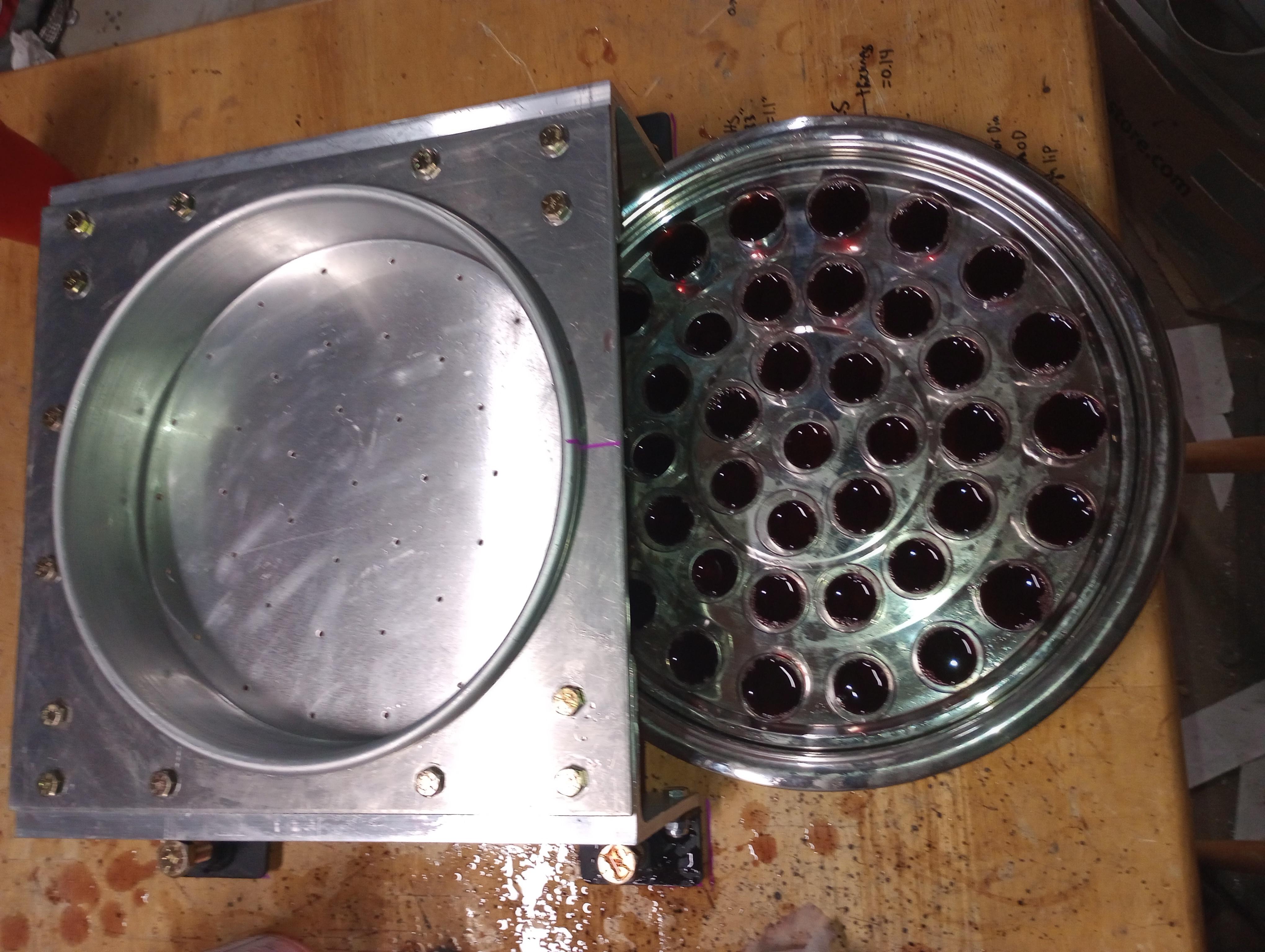





This is a device that automatically fills an entire tray of communion cups at the same time.
This will save a lot of time for churches that have a lot of members or do communion every week.
My friend came to me with a need, his church has a prep guy for their communion that wishes it didn't take so much time to fill all the cups, because although he enjoys prepping for The Lord's Supper, he wishes he could get it done faster to serve the church in other ways as well. This device was designed to fill that need.
There are other communion tray fillers that do a better job than this one. The main drawback to this filler design is that not every cup is filled perfectly evenly, so there is an additional step at the end that involves using a syringe to even out the level of grape juice in each cup. But I will say that only a few cups need this; and even with that extra step, this will save a lot of time and frustration!
The other designs that I mentioned, which work a bit better are ones like this one and this one and this one. Although the work a bit better at filling the cups more evenly, there are reasons why churches don't use them today and they are not quite as practical to use as my design:
- It is not possible to buy them. Years ago, industrious individuals had companies that built them and sold them to churches, and the companies are no longer in business. So the churches that didn't buy these products during the short window of time that they were available are out of luck.
- The time to clean these fillers out when done using it appears to be high and may negate the time savings used to fill the cups, unless many trays were filled.
- The designs are generally too complicated for a church to build their own without spending a lot of money getting it machined. Furthermore, there are no designs available -- i.e.; individual churches would have to get their own designed and built.
I created this design to fill a void that is in place currently:
- My design is easy for any church to build with simple hand tools and some time.
- The clean-up time for my design is quick.
- The design is available here for any church to use and doesn't require outsourcing to a machine shop.
It is my hope that churches everywhere can benefit from the time-savings that my design offers!
Supplies
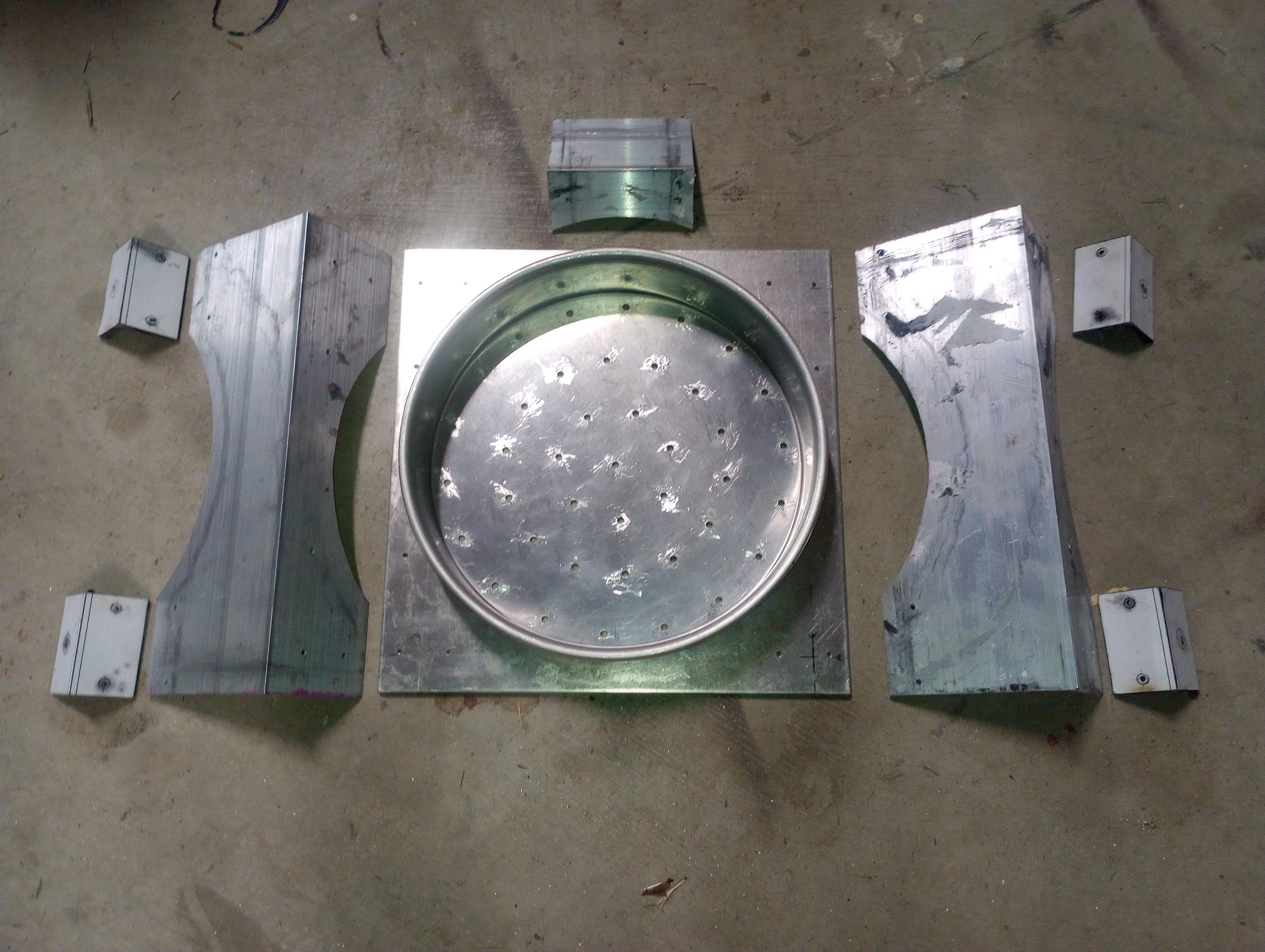
Here are the tools that I used:
- Jigsaw, to cut out the aluminum
- Jigsaw blade, I used these
- Angle grinder with cutoff wheel (to cut through 1-1/2" angle iron)
- Deburring tools
- Bench grinder. One end of my bench grinder has a grinding wheel, the other has a wire wheel
- Deburring tool such as this
- Mini Triangular scraper. The hole sizes in the cup filler are too small for a standard deburring tool to work, so you need something like this. There are bigger scraper sizes, but I prefer the mini one because I think the larger ones make it too easy to mess up the shape of the hole, affecting your fill consistency
- Half-round file
- Clamps or a Vise
- Drill and drill bits. Below are the sizes I used:
- 1" Hole Saw, used in step 2. You can probably get away with something else, you just need a drill bit size large enough for your jigsaw blade to go through the hole.
- #50 (0.07") drill bit -- this is the smallest size that fits in the chuck of my hand drill. Your results may vary.
- #46 (0.081") drill bit
- #44 (0.086") drill bit
- #42 (0.093") drill bit
- #38 (0.101") drill bit
- 17/64 drill bit -- for every hole which gets 1/4-20 bolts
- 9/16 drill bit (If your drill chuck size is 1/2", you need a special drill bit with a reduced shank size so that it will fit in your drill)
- Because you're not supposed to go straight to a 9/16 drill size, you will need various (common) drill bit sizes to step up to your final 9/16 size
- it's also good to have some smaller sizes of drill bits for your pilot holes into your templates
- Cutting fluid. Some types can stain aluminum, so I got one for aluminum.
- Center punch, for starting holes. There are the type that require you to use a hammer, and there are also the spring-loaded auto punches. For your bolt holes, you can use an auto-punch. For the holes in the cup filler, I think the auto punch uses a bit too much force, and I was worried about denting the Pizza Pan used to make it. So for that reason, I went with the type of punch that requires a hammer.
- A welder. I used a flux core, I'm sure TIG or MIG would work and probably stick. If you don't have any way to weld steel for this project, you could use a tap instead.
- A marker. You can use a permanent marker, but I found that the cutting fluid washes the marker away. Instead, you could use paint marker such as this one that stays better.
- Digital or Dial Calipers
Here are the materials that I used:
- 10" Heavy Gauge Aluminum Deep Dish Pizza Pan with straight sides. I used an American Metalcraft HA80102, obtained from here.
- 5" x 3" Aluminum Angle, 1/4" thick. I bought 3 feet of 6061AL from MetalsDepot.com, Stock # A35314. They only sell lengths in even feet (2, 4, 6, etc) so you can check out with a custom length of 3 feet and save some money.
- 12" x 12-1/4" x 3/16" 5052-H32 Aluminum Plate. Purchased from MetalsDepot.com, Stock # P3316-5052. Check out with a custom cut of the size you need, then you won't need to cut it yourself :)
- About a foot of 1-1/2 x 1-1/2 steel angle iron, 1/8" thick. If you decide to forego the welder and tap holes instead, you definitely need something thicker.
- 1/2" bolts, 1-1/2" long QTY 5.
- 1/2" nuts, QTY 6
- 1/4"-20 bolts, 1" long. QTY 14
- 1/4"-20 bolts, 3/4" long. QTY 8 -- If you forego the welder and tap holes instead, you will need something longer
- 1/4-20 lock nuts, QTY 22
- About 4 feet of 2x6 wood
- QTY 12 deck screws, 2 to 2-1//2" long
- Glue stick and tape, to attach paper templates to your materials
Here is what I used for when going to use it:
- Food-Safe measuring container, for measuring out how much to pour into the filler. I used this one
- Food-Safe syringe, for evening out the fill amount after it's poured. I used these
This design works with a specific communion tray. I can't guarantee that this design will work with every tray because the dimensions may be different, or the hole pattern for the cups may be different. So this is the communion tray that this was designed for:
It has an ISBN number on the back, 978-080548555-4
Build the Filler





The filler is a pizza pan with forty 0.101" holes drilled in it. The hole size was determined after much trial and error.
I've attached a paper template for you to use. You simply glue or tape it on the back of the pizza pan.
- Because the Pizza Pan is 10" in diameter, your standard 8.5 x 11" sheet of paper is too small to fit the whole template on. The easiest way is to print a template on an 11x17 sheet of paper, but I know that not everybody has access to that. So I've included two types of templates. One is for 11x17 paper, and the other templates are for 8.5x11. If you use the 8.5x11, you will need to cut the template from two pieces, then tape it together.
- When you print the template, make sure your print settings are correct. Most printers default to "Fit to page size" You need to set it so that your Print Scale is either turned off or the Scaling is 100%.
When you've cut the template out and attached it to your pizza pan, use the center punch on the center of each hole to guide your drill bit when you drill the hole. I was afraid of denting the pan, so I cut with a jigsaw a circular piece of wood for the pizza pan to go over, and screwed it together with deck screws. Make sure that the side with the screw head is facing down so that your drill bit doesn't hit the screws in the wood.
Once your holes are punched, drill them out. I found that you need to start small and work your way up. If you immediately drill to the final hole size, they won't be perfectly round and you will end up with cups that are overflowing, while other cups don't fill at all.
- As you're drilling, try to drill as straight as possible. Try to mind your hole depth as you're drilling. Once you're through, don't go any deeper. We want each hole to be as nice and uniform as possible.
- As you're drilling, you may find that the pan wants to run up the drill bit. You should avoid this if possible. Either hold it down or find a way to keep it held down.
I started with a 0.07" drill bit, because it was the smallest size that would fit in my drill chuck. Once the 0.07" size is drilled, I don't use the wood piece underneath the pan anymore, trying not to push too hard on it as I'm drilling.
- After this I deburred it with the mini triangular scraper. A note about deburring, try to be gentle so you don't mess with your hole shape. I like to run the scraper around the edge of the hole at an angle (gently cutting the burr), then trying to knock it loose holding the scraper straight up in the hole while spinning it in my fingers. I've attached pictures so you can see what I'm talking about. Sometimes I used my fingernails to help knock a burr off. I have pretty thick fingernails though, not sure if that would work with everybody.
- The good news about stepping up the drill bit size like this is that after you deburr the first time, the holes don't seem to get burrs as bad as that first time. So deburring will be easier in the future.
Then I drilled to 0.081".
Then I drilled to 0.086"
- I deburred it again here
Then I drilled to 0.093"
Then I drilled to 0.101"
- Deburr a final time.
The reasoning for deburring so often while drilling is that I wanted to keep the burr sizes small and manageable so that I could be less intrusive when doing the final deburr, so as to not affect the hole shape. It's possible that you can skip some of this deburring (since it is a 30min-1hour ordeal each time). But I wanted to give you instructions that I was sure would work, and I feel confident in these instructions.
Cut Out the Top Plate
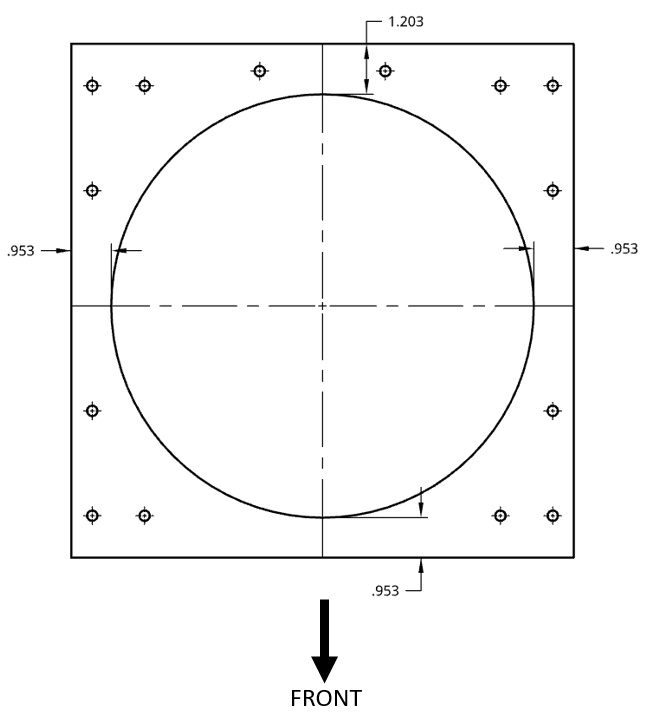
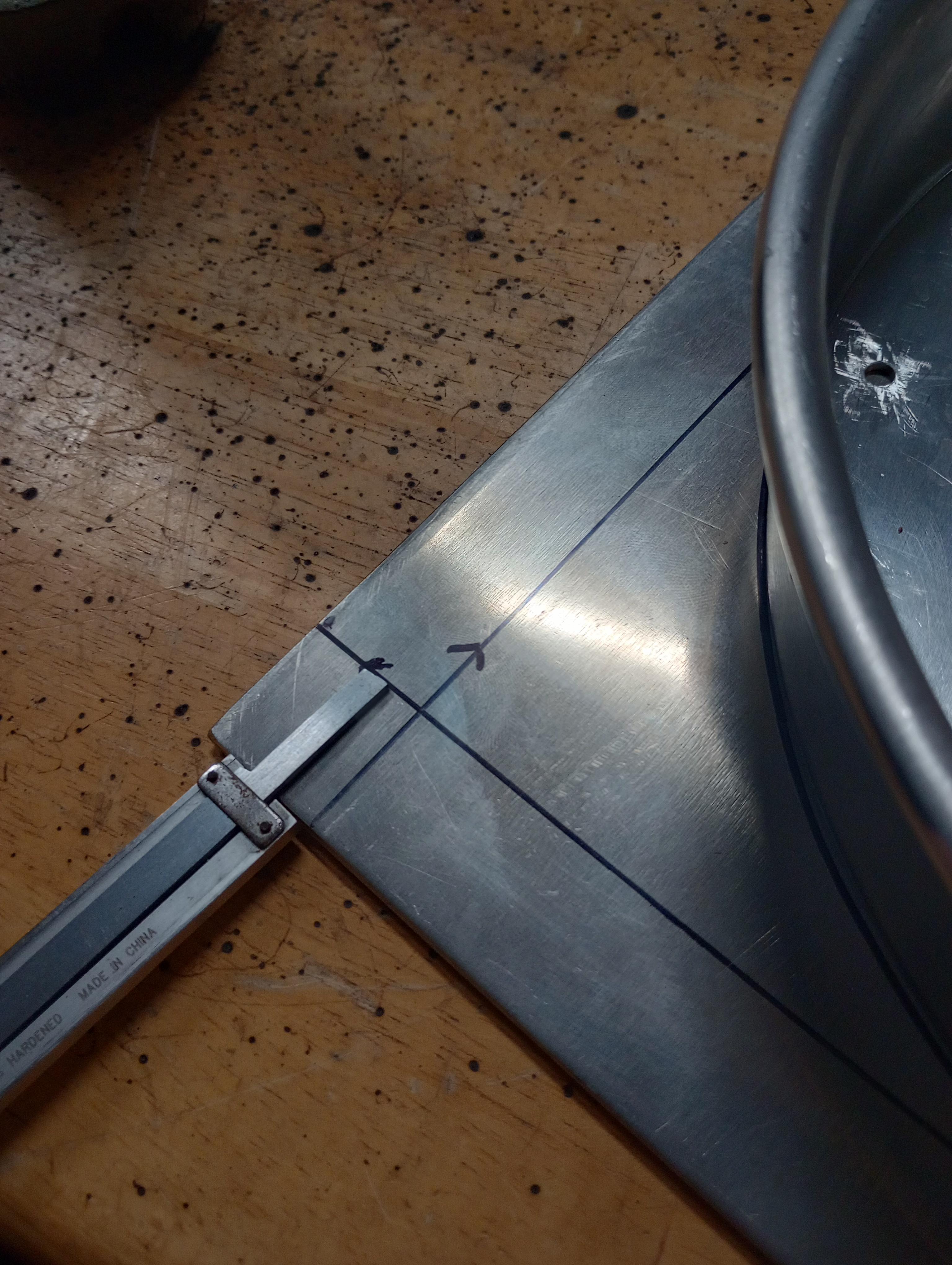

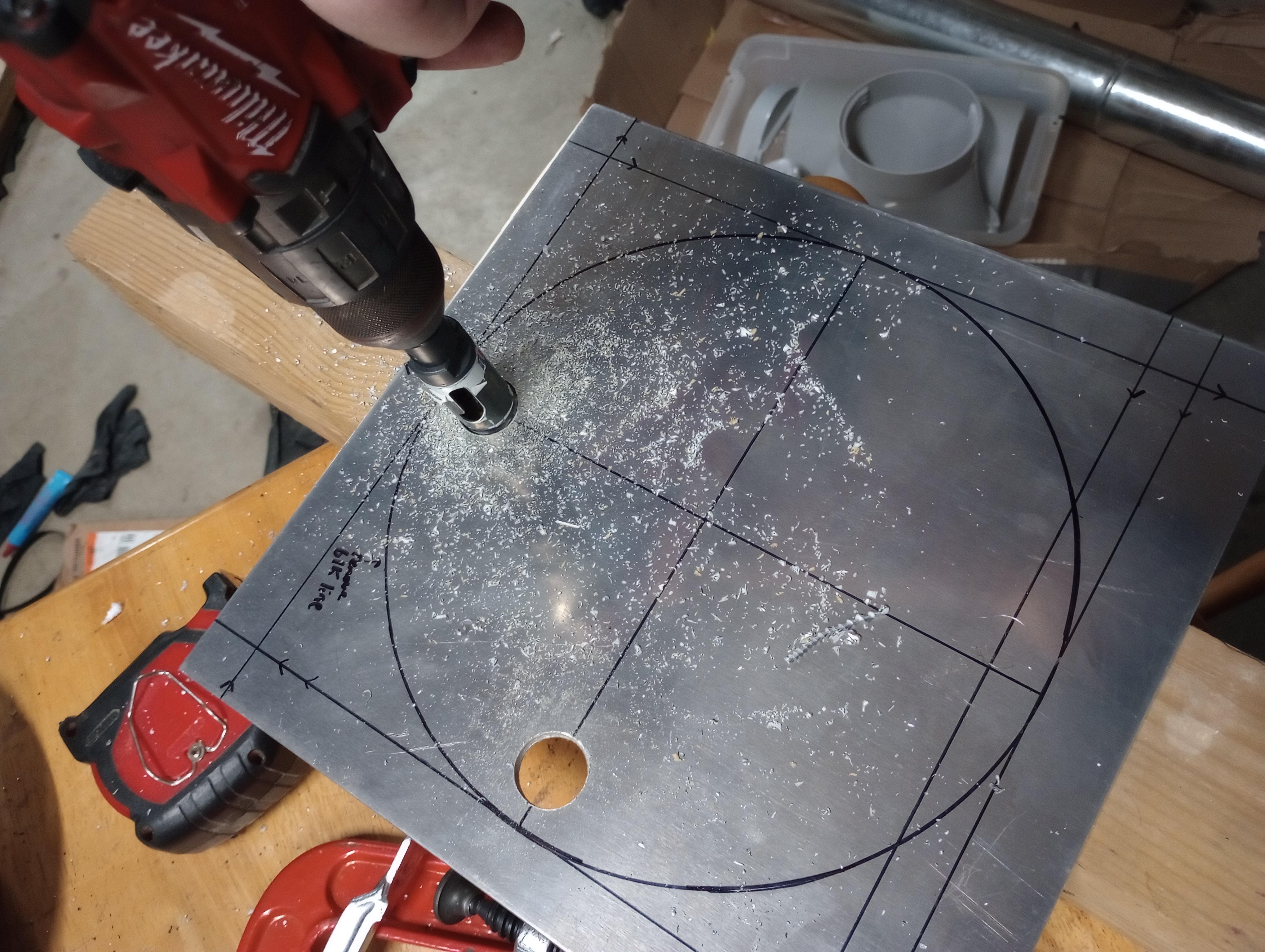

You need to cut a hole in the center of your plate for the Pizza pan to go into.
Note that the pan doesn't actually go in the dead center of the plate with this design, the hole location is a bit closer to the front of the plate because I wanted the end user to have a bit of clearance so that they could see the edge of the tray underneath the filler and line the cups up correctly.
So you have to measure out the distance from the edge of the plate to the point where the edge of the pan will be. Mark it with a marker. Do this for all 4 edges. Then you can line up the edge of the pan with the marks you made on the plate. Look at the images to get a better idea of what I'm talking about and for the dimensions you need. I used calipers (see image) to measure it, because the dimensions are atypical.
Once you've got the pan lined up with your marks, get your marker and draw around the pan to mark out the hole you need to cut in the plate.
- Try to be mindful about how you have the marker angled when you are drawing the mark. You don't want your hole size to be too small (the pan won't go in) or too big (the pan moves around too much in the hole). You may want to put something heavy on the pizza pan so that it doesn't move around while you're marking it.
- Be mindful about where on the line you want the jigsaw blade to cut. The outer portion? The inner portion? You want to guarantee the pizza pan will fit without having too much end play when you're done. (Although a little is OK)
Now you're ready to cut out with a jigsaw. Be mindful when you're cutting so that you don't bend the plate. If the plate gets permanently bent, the tray filler will never work right because it has to be level to work. I cut out four "pizza slices" (see image) because I thought it might help prevent bending of the plate, but after I cut it, I didn't think that was necessary. I drilled a hole with a hole saw near the edge and then used that hole to start my cut.
Also, remember that cutting fluid will wash away permanent marker. It's possible to cut without cutting fluid, but you may go through jigsaw blades more quickly.
When you're done, deburr it so that nobody cuts themselves.
Drill Holes in the Top Plate
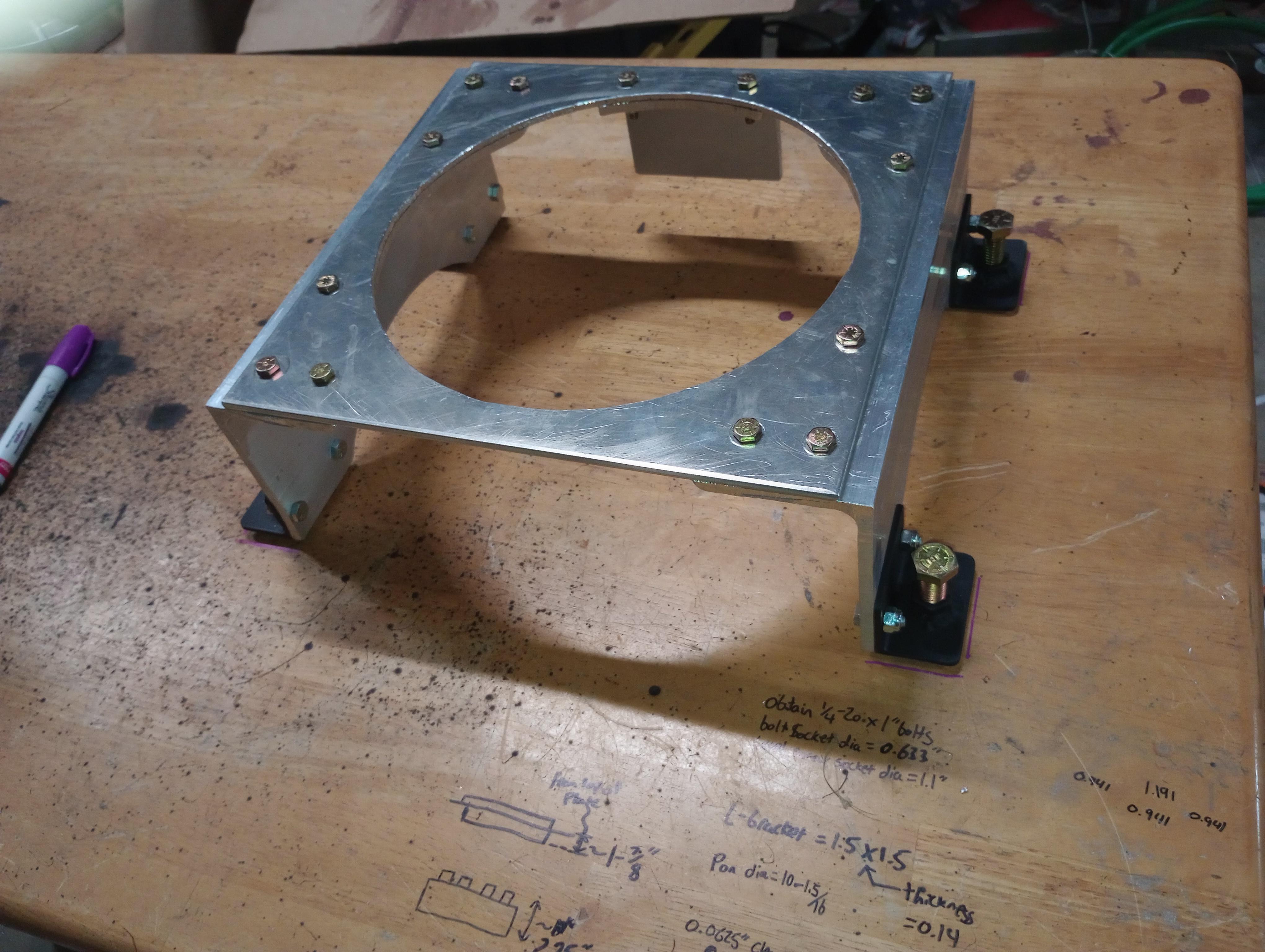

There are 14 holes that need to go in the top plate. Because it's so big, there are two templates. One for the left side and one for the right side. I've included templates for those who only can print with 8.5x11 paper, you will have to tape your template together.
It's also possible that you can do this step before Step 2.
Print your templates out; cut and glue or tape to your plate. Punch your holes and drill them out. It's best to start with a smaller-sized drill bit and then drill the hole size you actually want. Otherwise, your hole may end up moving a bit as you are drilling and not line up later.
The final hole size I used here was 17/64", so a 1/4" bolt would go through.
Don't lose sight of which direction the plate goes. Put a mark on it if you need to. The holes go along the 12.25" length of the plate, and the large hole for the Pizza Pan in the plate is closer to the front than the rear. Refer to the attached image for help.
Build the Left and Right Angle Pieces
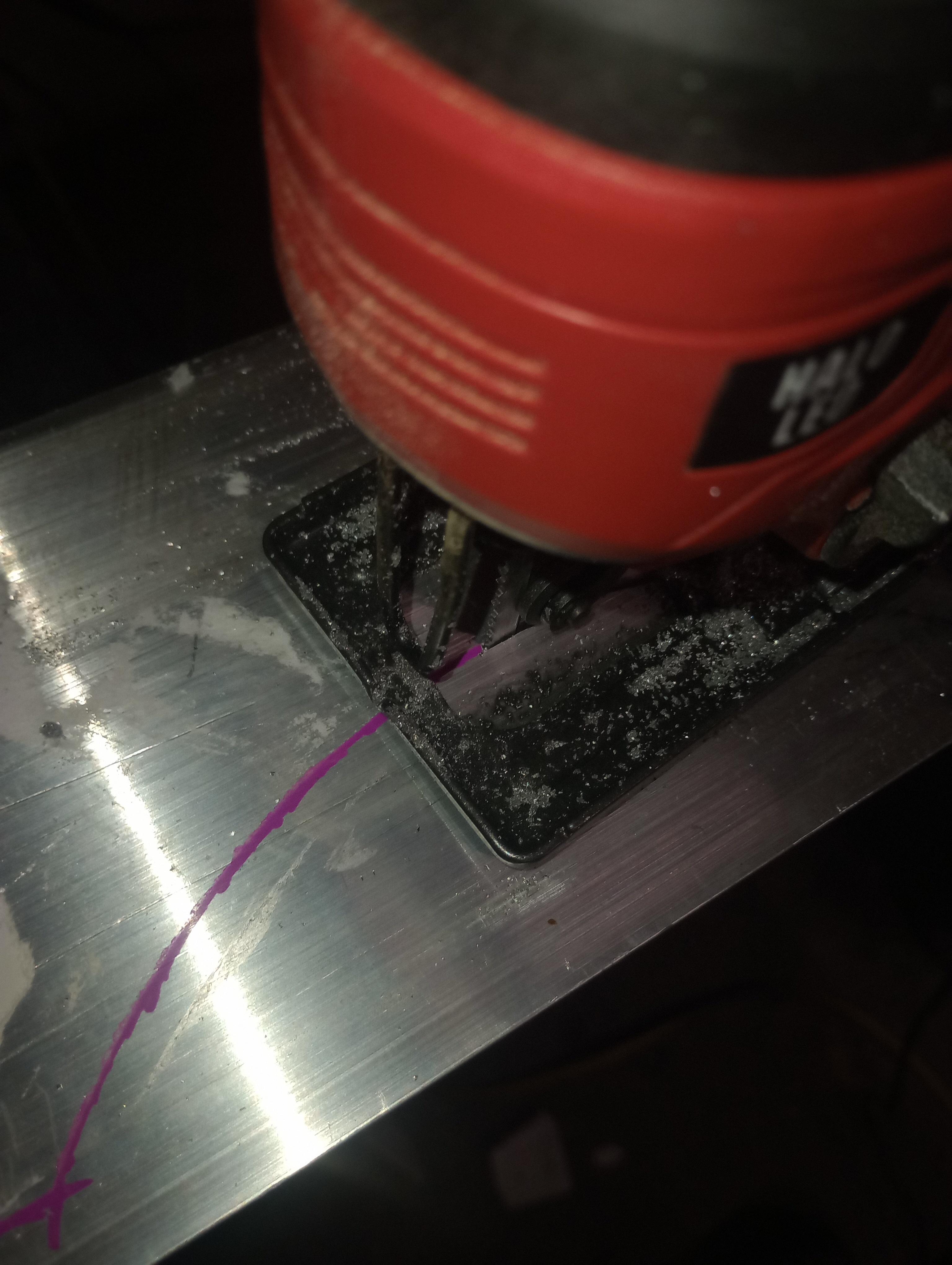
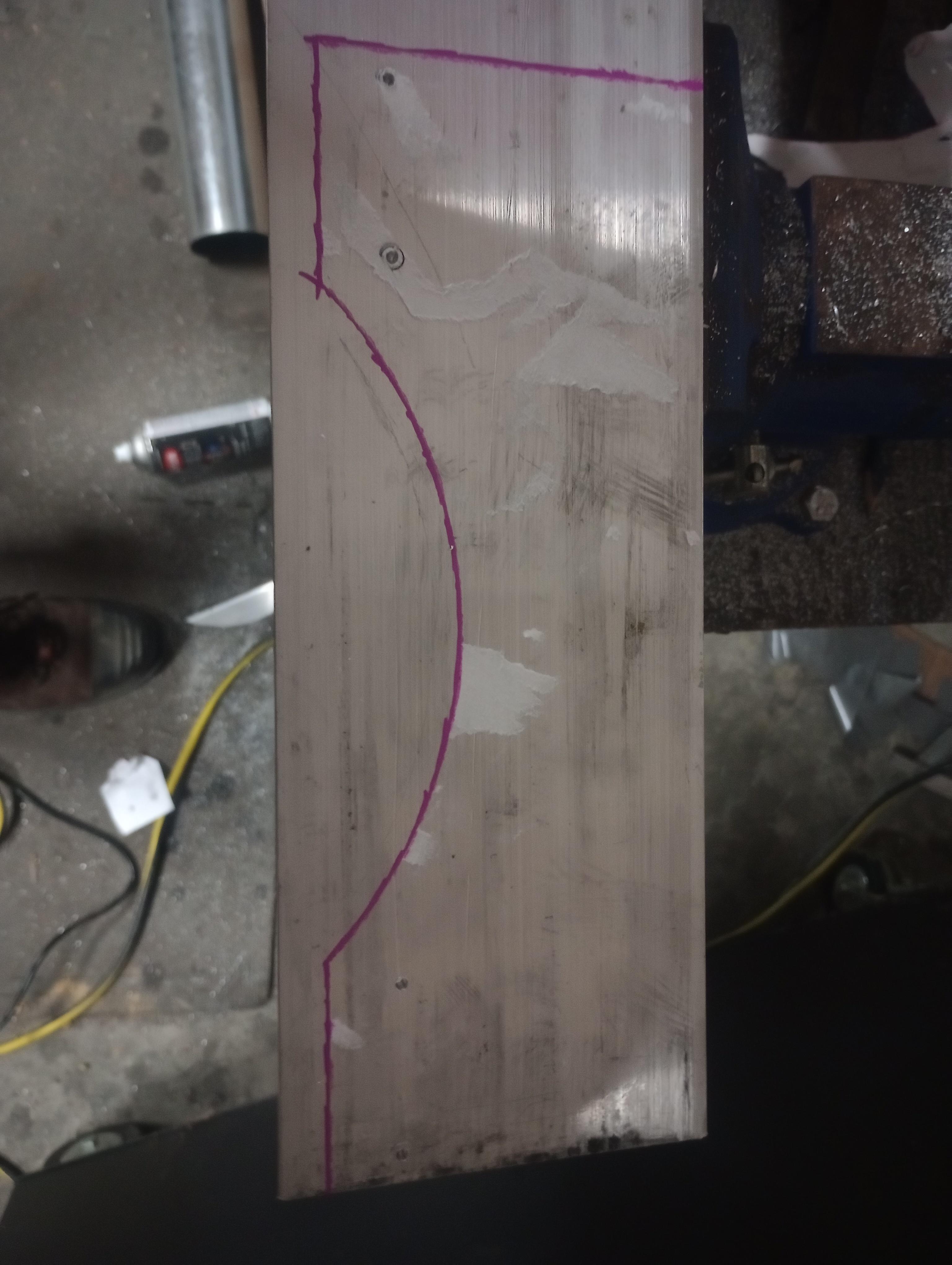



Print out the paper templates and glue them to your 3" x 5" Aluminum angle. Obviously, the wider template goes on the wider leg of the angle.
Punch the center of the hole. Draw the outline with your marker. If you're using a permanent marker, don't use cutting fluid. You will go through blades more quickly, but it's better than losing your line.
I like to drill the holes, then cut it out. Start with a smaller "pilot" drill bit so your hole location doesn't wander.
- All holes on the Left and Right Side Pieces are 17/64", so a 1/4" bolt can go through.
Deburr it so that nobody cuts themselves.
PRO TIP: The left and right pieces are NOT interchangeable. Be sure to keep track of them or else it won't all line up. That's why I like to cut out the pieces one at a time.
Build the Back Angle Piece

Print out the template and glue to your 3x5" angle.
The longer end goes on the 5" leg.
Punch out the holes, draw the outline with your marker. Drill the holes and cut it out.
- Start with a smaller "pilot" drill bit so your hole location doesn't wander.
- The holes are 17/64", for a 1/4" bolt.
Deburr it so that nobody cuts themselves.
Downloads
Build the Four Leveling Feet
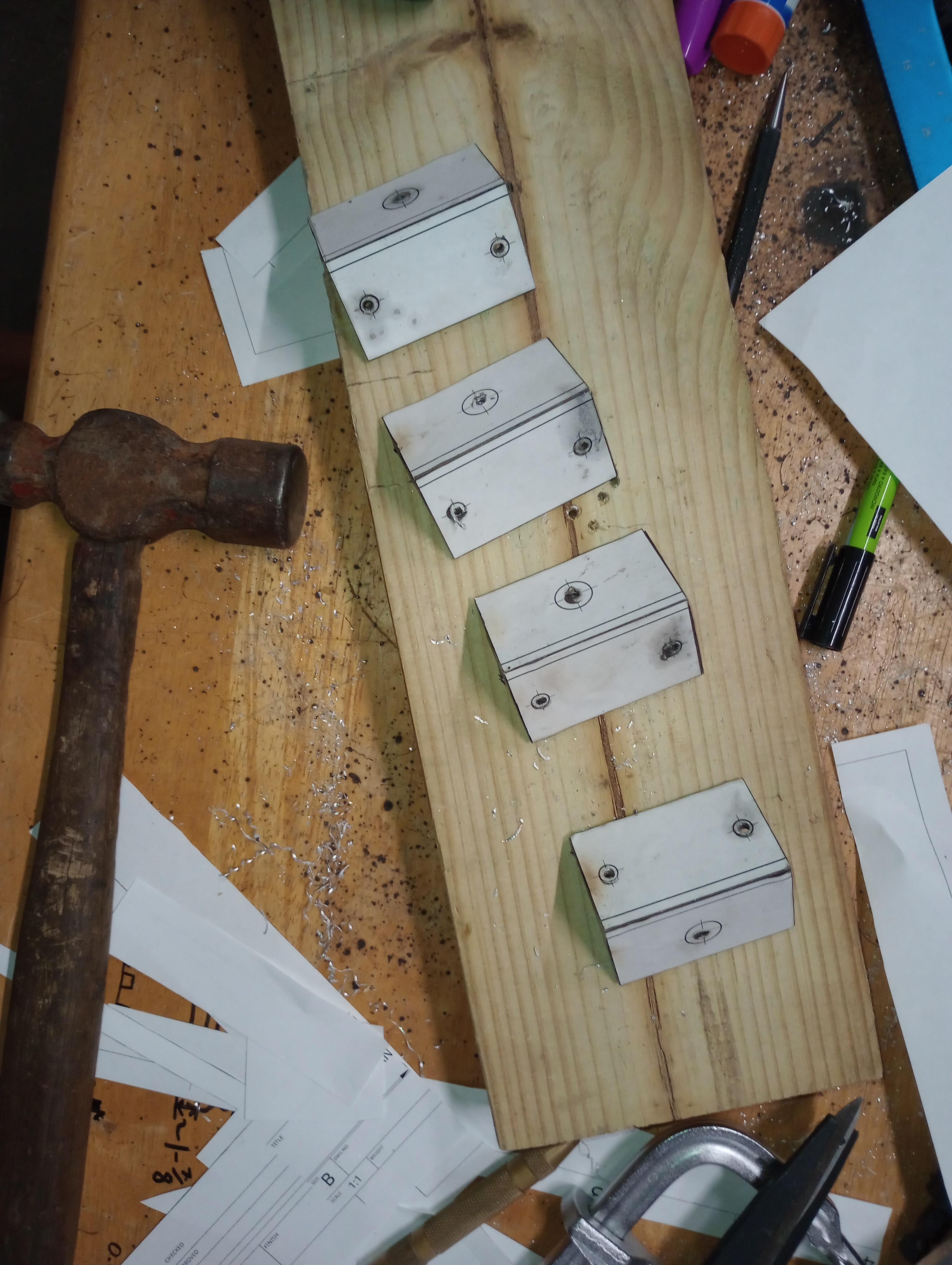


This dispenser doesn't work unless it is completely level. For that reason, there are leveling feet in all four corners so that the end user can level the device.
- This is accomplished by welding 1/2" nuts to a piece of angle iron, while a bolt goes through the angle iron and the nut and adjusts the level.
Print out the templates and attach them to your angle iron with a glue stick or tape.
- Note that the orientation of your template is important. Don't get it 180 degrees out of rotation. See the image I've included to see what I'm talking about.
Draw your lines, punch your holes and drill them out. Cut it out with your tool of choice. I used an angle grinder with a cutoff wheel.
- For the two smaller holes, that a 1/4" bolt will go through, my final hole size was 9/32. This is because I painted the brackets before trying to assemble everything, and I wanted to be sure I wouldn't have any issues with the holes lining up. As always, start with a smaller pilot drill bit so that your hole location doesn't wander.
- When you're drilling your large hole that the 1/2" bolt goes through, your final hole size will be 9/16". You're not supposed to go straight to that size. You're supposed to start with smaller drill bits and then work your way up to the final hole diameter.
Deburr the parts so that nobody cuts themselves.
Downloads
Weld the Nut to the Leveling Feet
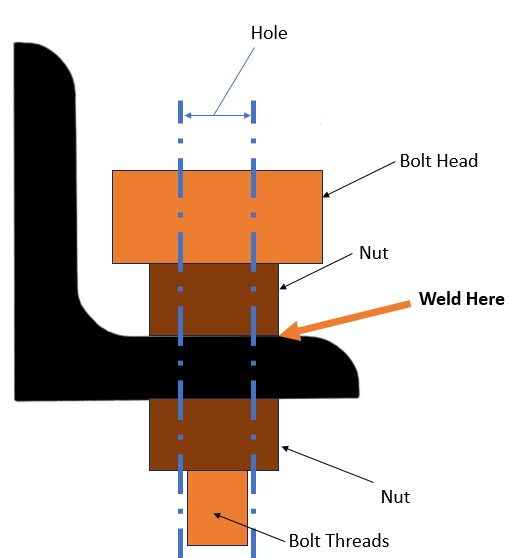

Now you have to weld the 1/2" nuts to the angle iron.
- As mentioned earlier, if welding is out of the question, you can probably tap a hole instead, but you should use thicker angle iron (and therefore longer bolts to attach the angle iron to everything).
Now, if you've never welded a nut over a through hole like this, here is some advice:
1) You need to remove the coating from the nut. I like to run all the nuts up over a bolt (see image) and wear it off with a wire wheel. Do this at your own risk :) Try to orient the rotation of the wire wheel in relation to everything so that it runs the nuts further onto the bolt rather than off of the bolt.
2) If you don't know how to hold the nut over the hole, I like to use a bolt, the nut to be welded, and an additional nut to hold everything in place. (see image) This way you can guarantee that the bolt will line up with the hole and keeps the nut from moving when you're welding.
- That's why I added a 5th 1/2" nut and bolt to the list of materials, because you need an additional nut to do this. The extra bolt is because the heat from welding will burn away the coating on the bolt. So I like to use the same bolt for every hole I weld, then toss it for fresh bolts once everything is welded.
Then weld it up!
I spray painted after this step. Try to find some way to keep paint from going into the nuts, otherwise it will be more difficult to turn the bolts when you're done.
- I like to run some old bolts up through the nuts to protect their threads, then paint them.
- I like to use different bolts than the ones that will be on the final product, so that I don't get paint on them.
Assemble

At this point, you're just bolting everything together.
- The shorter bolts (1/4-20 x 3/4") go through the side holes
- The longer bolts (1/4-20 x 1") go through the top holes (unless you went with thicker angle iron and tapped holes rather than welding a nut in place)
As you're tightening the bolts, try to alternate which side of the plate that you're tightening the bolts on. (Similar to how you would tighten the lug nuts on a car in a star pattern). This is to reduce the risk of deforming the Top Plate when you're tightening everything.
How to Use


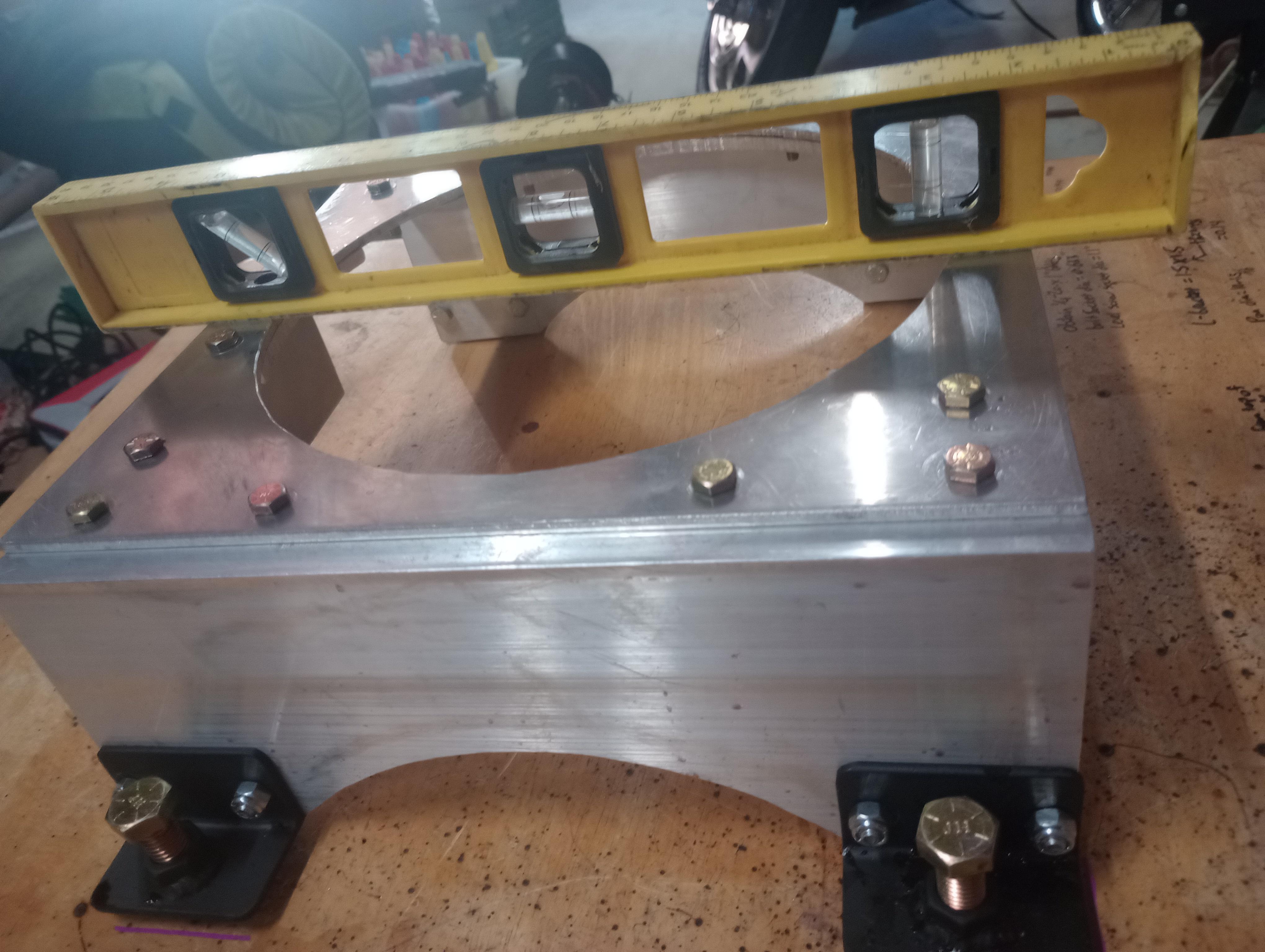




I've included a video that says how to use it.
Link also here: Automatic Communion Wine Filler Dispenser
On the tray, there is a row of cups that is perfectly straight. The cup on the end of that row is called the "master cup". That is how you line everything up. Draw a line that's in-line with your "master cup" on your pizza pan, and draw a line in the dead center of your top plate (see image).
Set the dispenser on a table where you intend to use it. Use a level and the leveling screws you built to make sure everything is level.
Put your communion tray underneath the dispenser. The side and back pieces will ensure that everything is lined up. Make sure that the "master cup" lines up with the lines you drew on the top piece and the Pizza Pan filler.
Pour your communion wine into a measuring pitcher. I have found that 12 ounces works perfect for me.
I've found that your pouring method into the dispenser matters. So take the 12 ounces that you've poured into the measuring pitcher, and put it into two separate cups, 6 ounces in each.
Pour the communion wine from the two cups into opposite ends at the same time. See image. Do it as fast as you can without splashing communion wine out of the filler.
Once all the cups fill up, you will notice that communion wine is no longer pouring in, but is slowly dripping in. At this point, you could take the tray out; however, it is likely that some will drip onto your tray and make a mess. To prevent this, take a towel and wipe the remaining communion wine out of your pizza pan filler.
Now you can pull the tray out.
The book of Proverbs says, "we may roll the dice, but the LORD determines how they fall." I say, 'we may pour the communion wine, but the LORD determines how it falls". You may need to make adjustments to ensure it is all level. So take your food-grade syringe, and suck some out of the cups that have too much and put them in the cups that don't have enough. Get everything even. If you're worried about some dripping out of the syringe while you're transferring the liquid, you can slowly pull up on the plunger as you're transferring it. That way, none drips out.
That's it... you're done!!!