An Engineer's Guide to Making a Theatrical Prop
by RocketEngineers in Craft > Costumes & Cosplay
3951 Views, 21 Favorites, 0 Comments
An Engineer's Guide to Making a Theatrical Prop
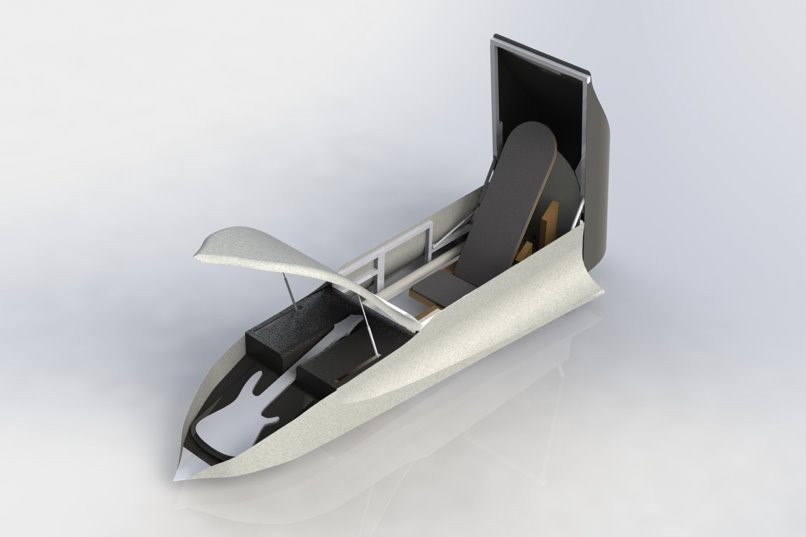
Building the perfect prop is no small feat, as our team of Mechanical Engineers from Cal Poly has learned through our Senior Project. Such a feat not only requires creativity and imagination, but also time, planning, and lots of hard work. Our team worked towards designing, building, and testing a spaceship prop for the RSVP XXV: Call and Response performance put on by the Sound Design program here at Cal Poly. Sadly, we did not get to see our spaceship come to fruition due to the COVID-19 pandemic. Although we did not get to complete our project, our team is proud of all we have learned through this process and is incredibly grateful for our ability to continue our education remotely during this troubling time. As such, we have decided to ‘finish’ our project by providing you with some insight as to what we have learned through this process that can hopefully be applied to any prop! This Instructables, thus, serves as a guide for building any theatrical prop, but is geared towards props that move—and, more specifically, can transport a person! Although examples from our project will be provided, we sought to keep this step by step guide general enough that anyone can find it useful.
Make a Schedule
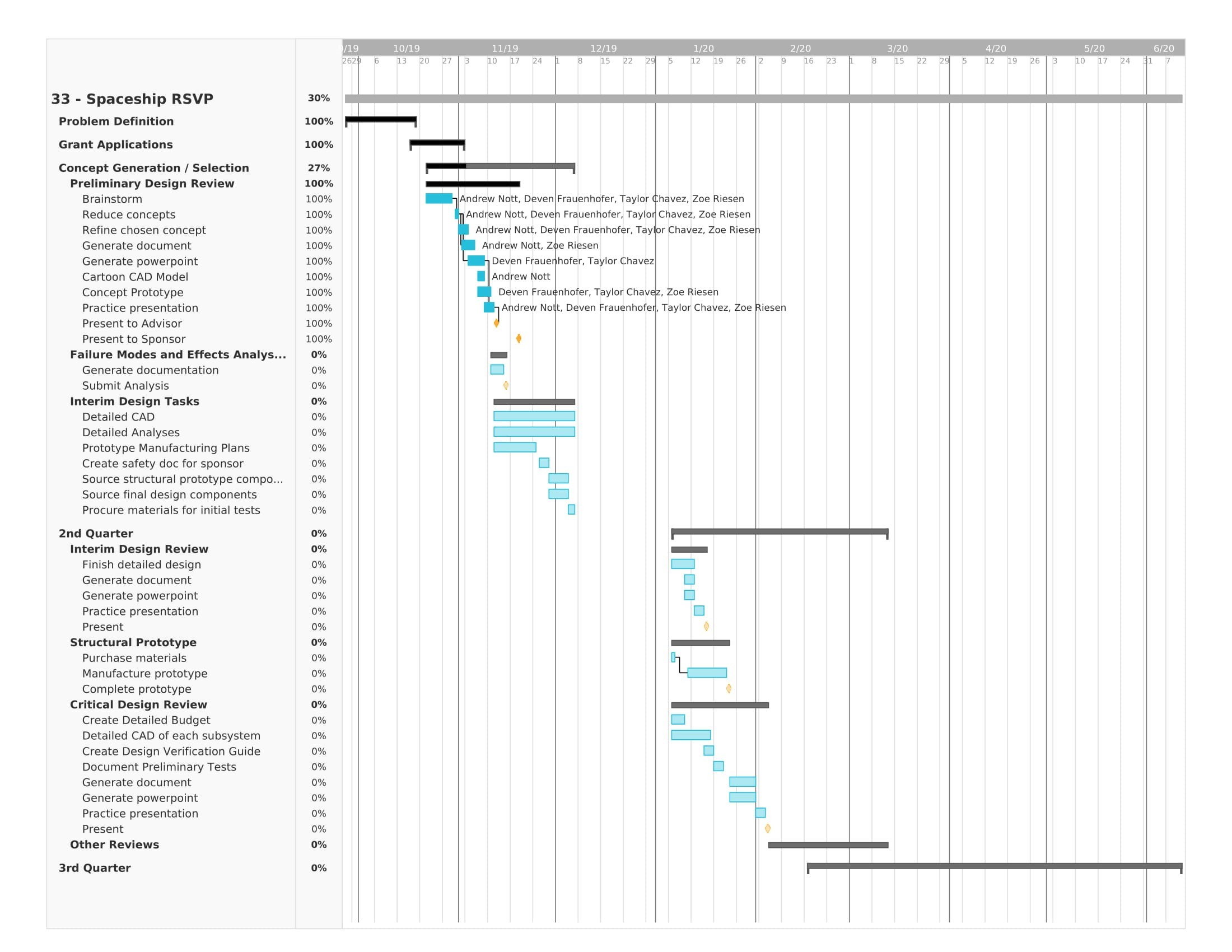
You want to start planning major deadlines in your project out early. One major deadline is the date your production starts! That being said, you will want to plan to have your prop finished and ready for the production earlier than when your actual production begins—you will likely want to use it during dress rehearsals (and it’s always wise to give yourself more time than you think you need). Once you’ve determined the date when your project needs to be completed, you can work backwards from there to set other major deadlines and milestones. Although you don’t need to complete a perfectly detailed schedule right off the bat, it’s a good idea to think about the big picture early. It may be a good idea to schedule Periodic Design Reviews with your Creative Director to ensure that you both are on the same page. Some time frames you may want to include in your schedule are:
- Defining your project
- Research and ideation
- Concept prototypes
- Modeling your design (CAD)
- Develop a Manufacturing Plan
- Develop a Testing Plan
- Structural Prototype
- Manufacturing and Assembly
- Testing
- Develop an Operator’s Manual
A great resource to help you keep all of scheduling in order is a Gantt Chart. Here, you can include the task to complete and the anticipated timing thereof, as well as assign team members responsible for completing the task. It also allows you to include dependencies: for example, if you don’t finish your research and ideation on time, then building your concept prototype would also be delayed. We included a picture of our Gantt Chart to give you an idea of how your scheduling might be organized. For our project, we had several Periodic Design Review: the Preliminary Design Review, the Interim Design Review, the Critical Design Review, and the Final Design Review. Additionally, we delivered a “Scope of Work” to our Creative Director at the beginning of the project and had communications with him on a bi-weekly basis.
Define the Problem
Before you tackle this project, it is essential to know the specifics of the problem at hand. Missing details or having the wrong idea of what the problem is will waste countless hours. This is the earliest stage of the project, so it’s the best time to prevent future mistakes, and the easiest time to make changes. You won’t have to redesign or rebuild yet, just re-conceptualize.
This stage consists of several steps: creating a problem statement, setting the boundaries of your project, defining what your director wants, and how to turn those wants into technical specifications for your prop. These specifications will drive your design.
Create a Problem Statement
You want to make a “problem statement,” a written paragraph of what you think your director wants out of this prop. What does it need to do? Where does it need to come from? What needs to be in it? What scene(s) will it be in? How often does it need to move? Does it need to move in front of the audience or between scenes? Think of as many questions as possible and try to answer all of them concisely in your problem statement.
For the prop we created, we summarized the problem like this:
“Our director, from the Sound Design Program in the Music Department, coordinates the production of an annual multi-media concert, RSVP. For this year’s production, a rockstar shredder will make his grand return in a sportscar-turned-spaceship. This prop must emerge from a tight space under the stage in a sleek and silent manner to maximize the surprise and awe from the audience. Special effects will reinforce this awe factor. The key is reliability: if this prop snags or fails during one of the five performances, the climax will be ruined. Structurally, the prop must be able to hold an adult male. He must be able to get in while the prop is under the stage, exit in the case of an emergency, and exit the prop elegantly once it has emerged.”
Draw a Boundary Diagram
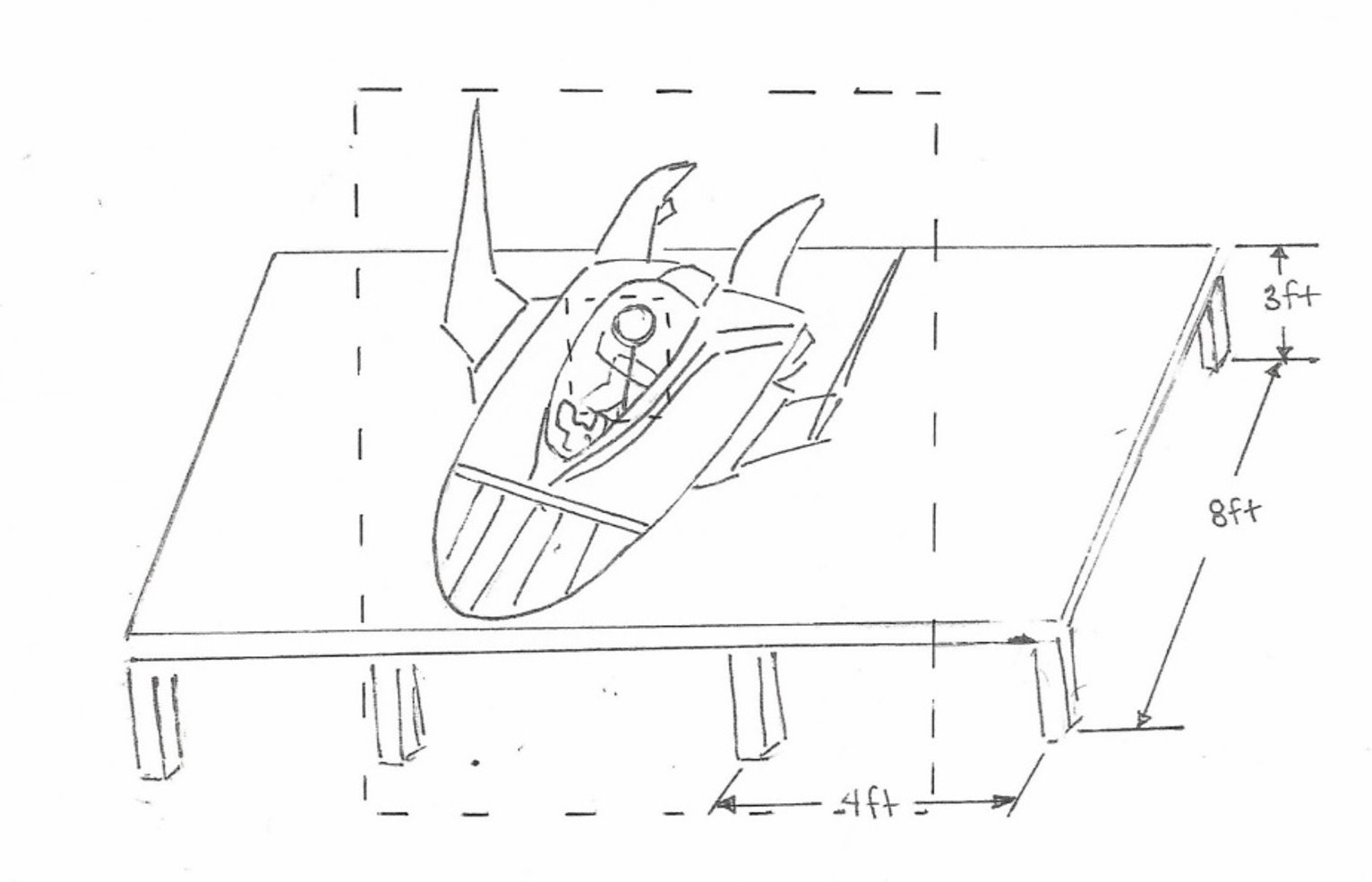
A boundary diagram is a visual tool that shows the boundaries of your prop and what external surroundings will influence the design. Things under your control should be fully in the box, while things your prop is interacting with should cross the boundary as something external to consider while designing.
For our design, the dimensions of the stage as well as the passenger of the spaceship were fixed — both these constraints influenced the design. Although it was not imperative that the spaceship was deployed onto the stage, it needed to fit under the stage, and thus, the design could not exceed a maximum height of 30 inches. It should be noted that while standard panels for our stage assembly were eight feet by four feet, we had a chance to design custom panels. This would have allowed for a wider range in dimensions for our spaceship — and why the boundary in our diagram encompasses part of the stage.
Develop a Wants/Needs Summary
Now that you have a problem statement and an idea what boundaries your project has, it’s time to categorize your constraints. Some things are required, like being able to fit your prop under the stage. Other things are not essential; they’re nice to have, but the prop will still work without them. This could be a paint job, an extra mechanism, lights, sounds, etc. It really depends on your prop, your performance, and your director.
Defining all the needs here will let you see all the constraints you have to meet. If it seems like too many, it might be worth asking your director if any needs can be relaxed, or if there are any creative ways you can remove needs. For instance, maybe the prop can be hidden behind the curtain instead of under the stage.
You have to consider everyone’s needs and wants. Your director is one customer, but you also have to consider the audience, the stagehands who will be moving it, the actor using it, and yourself for building it. You need to be able to build it, and you want to be able to build it easily. The actor needs to fit in it, and they want to be comfortable in it. These are all things to weigh in your design.
Our prop had a wide range of needs and wants. Here’s what we came up with:
First and foremost, the final product must be reliable. It needs to deploy fully and must maintain its reliability for a total of five deployments (two to three performances and during rehearsals). It must deploy silently—and in a timely manner—from a hidden location in order to maximize the surprise and awe from the audience. The spaceship must be hidden throughout the majority of the performance, which requires it to fit comfortably under the stage (3.5 feet by 8 feet by 30 inches). The spaceship must accommodate an adult pilot with an approximate height of 5’ 10” and approximate weight of 150 lbs. The pilot must be able to enter and exit the spaceship with ease in order to maximize the quietness and speed of deployment, as well as allowing for a quick exit in the case of an emergency.
The aesthetics of the final product are very important. It should look like a sleek spaceship from an old sci-fi movie with design elements from sports cars. It should also include some special effects to increase the “Wow!” factor such as smoke and lights. Ultimately, it must meet any safety requirements for use in the production. And lastly, it must be manufacturable so that it can be built within the timeframe and budget available.
Research
After defining your problem statement, you are almost on your way to brainstorming and coming up with your concept. Your first step beforehand should be as much background research as you can. The better your research, the more ideas you will be able to come up with during brainstorming!
To help you with your research, we have broken down the process into three categories:
- Customer Research
- Product Research
- Technical Research
For customer research, see if you can interview your sponsor or department lead. More often than not they will have a wealth of information and considerations regarding prop specifications, function, and logistics. Some early questions to ask include where your prop will be stored during the play, how it will emerge to the audience, and how it will exit the stage. If someone will be riding the prop: what is their weight and height, how many riders will there be, and will they have to enter or exit the prop. Your sponsor may also have access to, or at least point you in the right direction to, any codes and standards that you might have to design around. Questions like these will help drive your ideation and avoid unnecessary conflicts later down the design process.
It may be worth your while to do research on the type of prop itself. Though not always, there may have been someone who has constructed a similar prop in the past. Taking inspiration from their techniques and processes can help shape your design path to avoid ideas that have failed and consider ones that have succeeded. Here's a great resource for tips and trick within prop design: Hart, Eric. The Prop Effects Guidebook: Lights, Motion, Sound, and Magic. Focal Press, 2018.
Finally, do some research on the technical side of the prop. If you are designing the shell to prop, what materials might you be using? If there will be special effects, be sure to do some research to understand the feasibility of incorporating it into your prop. We recommend spending a lot of time researching as many technical aspects of the prop as you can. Understanding your different alternatives will be invaluable when you eventually compare them against each other.
Create a 'House of Quality'
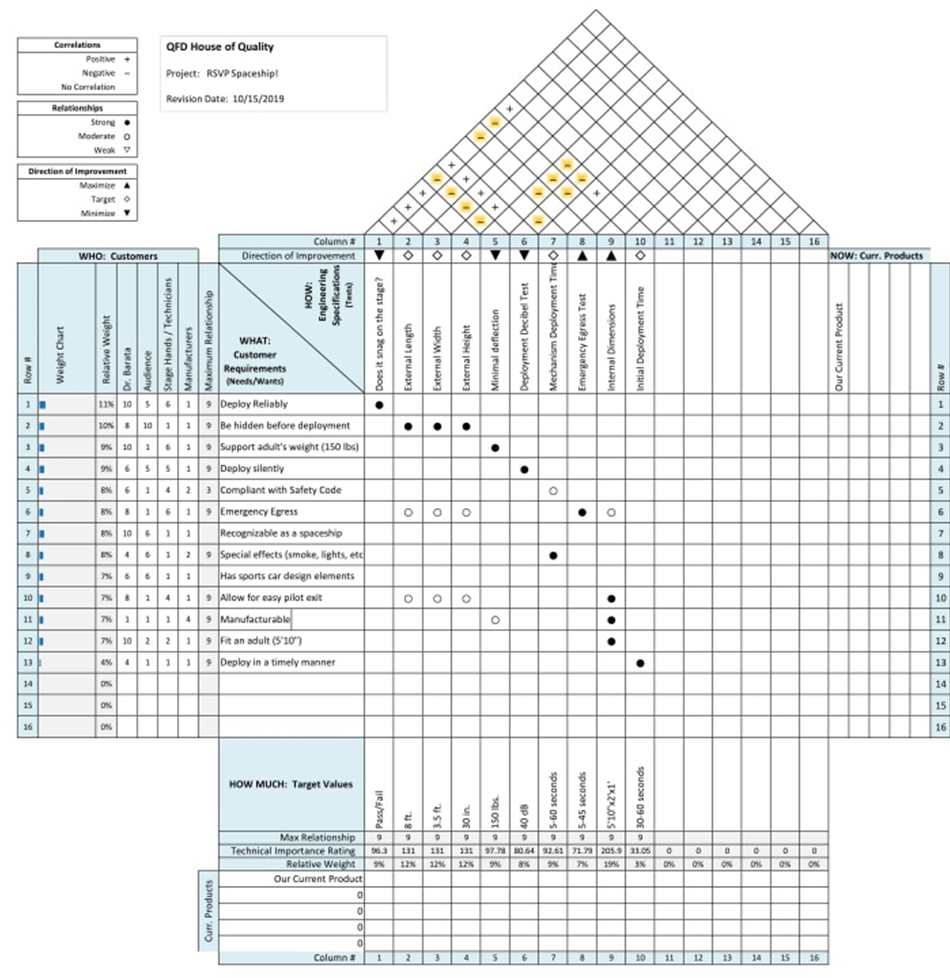
There is a type of chart called a House of Quality. It is designed to turn customer wants and needs into measurable specifications for your prop design. You can access a blank chart here. Start by listing every customer along with all the needs. Each need needs to be weighed for each customer under consideration. For you, the director or audience might carry the most weight. After weighing these needs for each user, design measurable specifications for testing each need on the final product. If a need is not quantifiable or testable, call it a design constraint. It’s still something you need to do, but it’s more qualitative, like whether this prop looks sci-fi.
Brainstorm
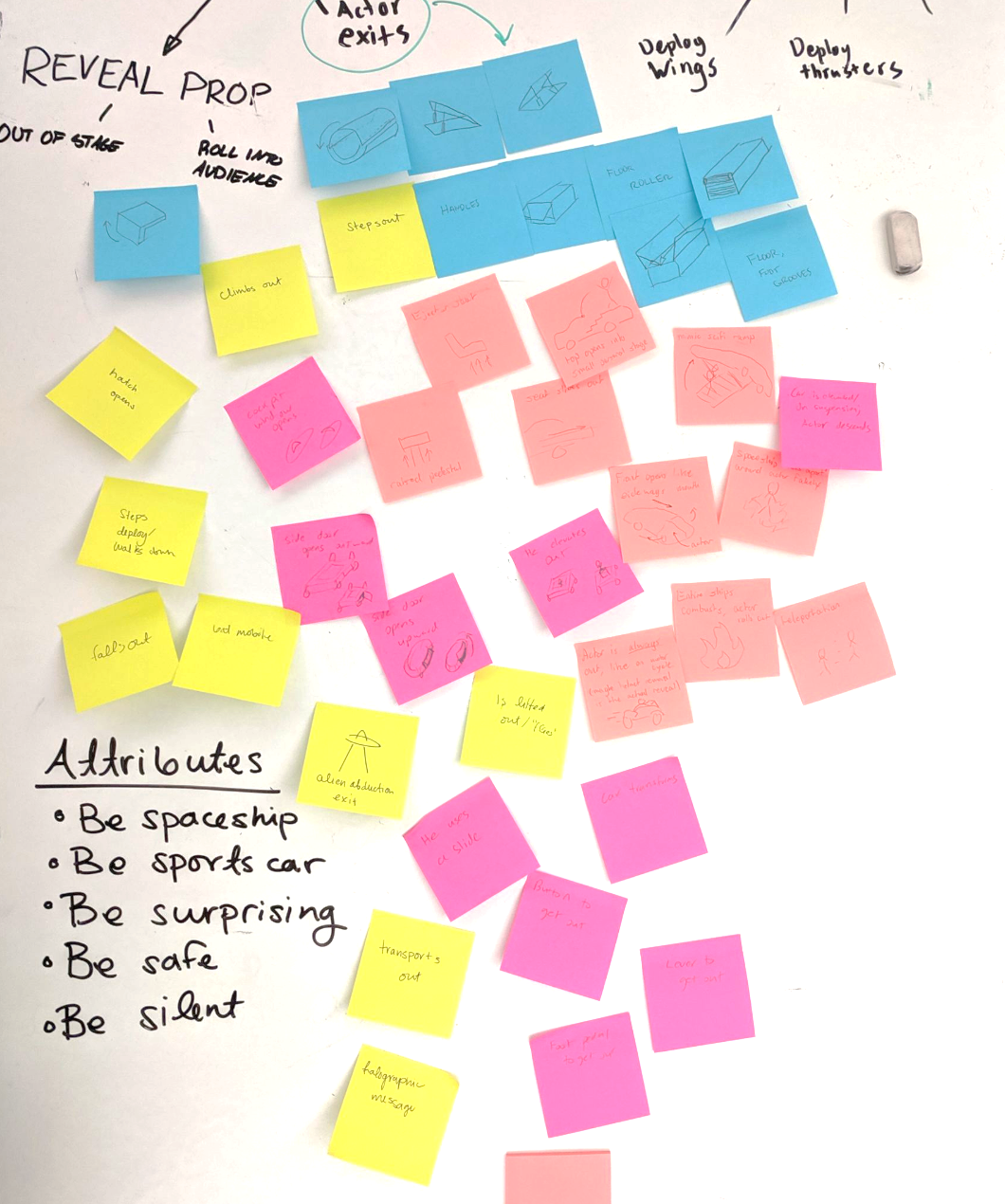
After breaking down each function, you should begin brainstorming how the prop will carry out its functions. We recommend trying many different methods of brainstorming. Some work better for certain teams, and some work better for certain individuals. A brainstorming session where everyone shouts out their ideas may not let the introverts in the room communicate their ideas, while writing or sketching on sticky notes might have a better shot. On one occasion we wrote every function on a whiteboard and would attach dozens of sticky note “solutions” to each function. Another time we invited people passing by to give comments and ideas.
Later in the brainstorming, see if you can make small concept models out of Play-Doh, Legos, or other quick and easy materials. Get creative with your brainstorming and try what works for you and your team! Remember, there are no bad ideas at this point; even a seemingly random idea can lead to further inspiration!
Idea Selection
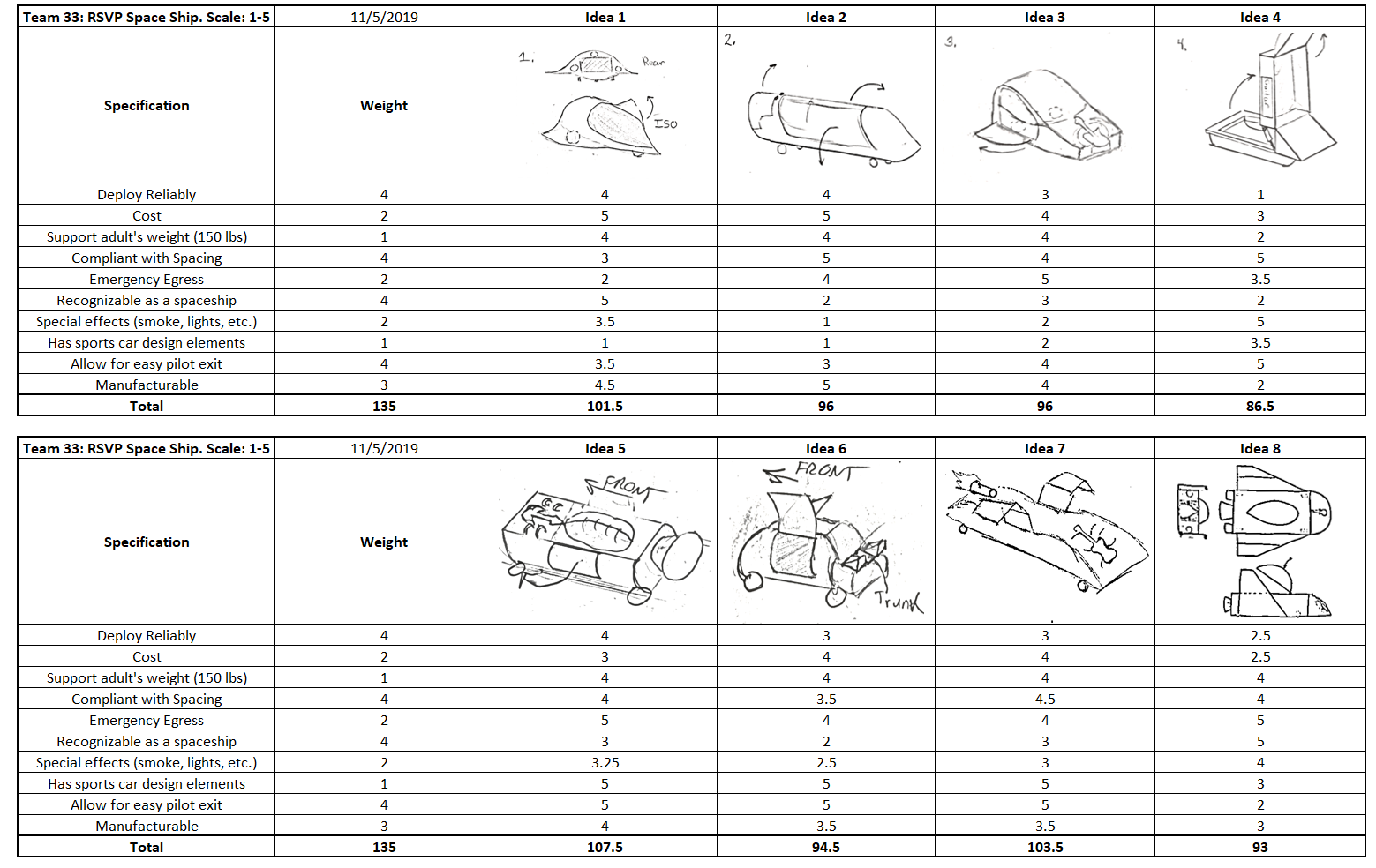
Now that you have all your ideas formed from your brainstorming, it’s time to put them together into separate design ideas. All your functions should add up to one prop, so a set of solutions to these functions should do the same. You should create a means to organize these functions and ideas. Our team used a morphological matrix, which was invaluable when deciding our final concept. Use the matrix, or an equivalent, to come up with different design concepts. From there, weigh each idea against each other. Develop criteria such as cost, manufacturability, and ease of deployment.
Here is our weighted decision matrix. As you can see, the alternatives vary wildly. Some are very similar, others are completely different. We considered all of our specifications, or requirements, and weighted the design based on a point system from one to five. Even if only one idea gets the most points, it’s still okay to take positive aspects from other concepts. For instance, during our process, idea 5 had the most points, but we loved the body design of idea 1 so much that we incorporated it into our final design. Take all of this into consideration when choosing ideas.
Determine Your Design Specifications
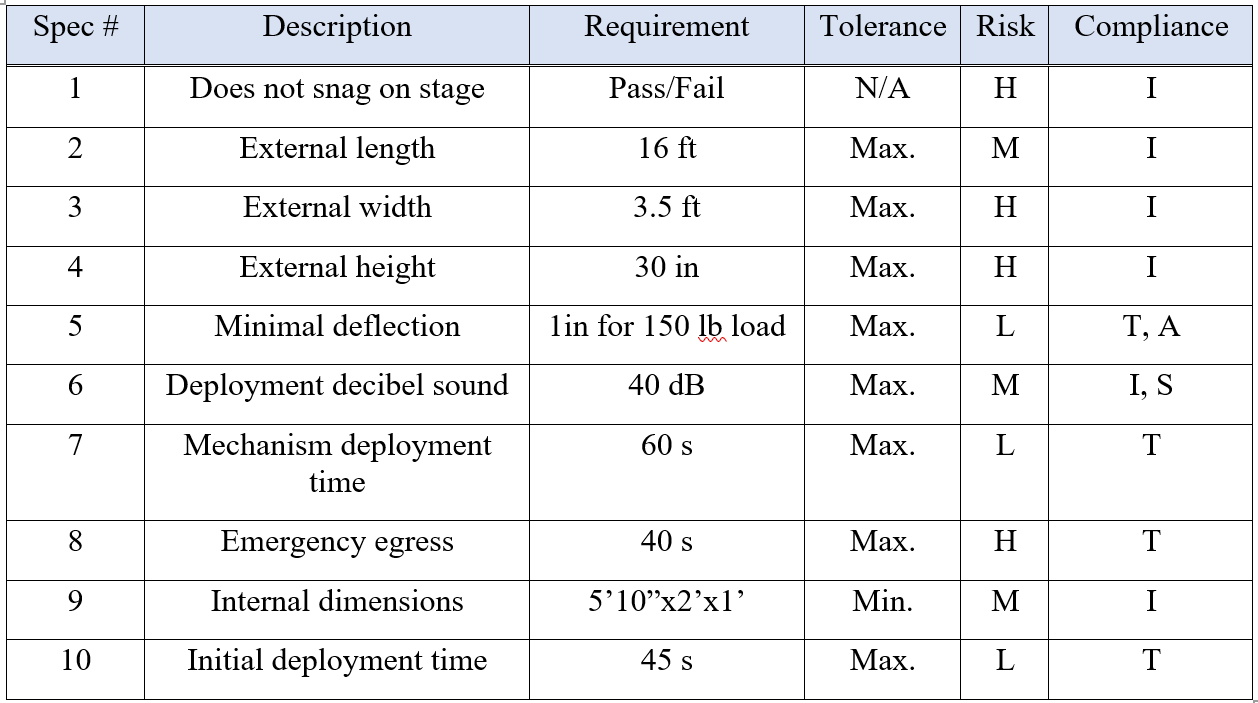
Create a new table. In it, place each specification from your House of Quality chart, the tolerance on it, the level of risk (how likely a failure would be to degrade the performance), and what type of test is needed to see if the specification has been met.
We boiled the customers’ desires down to 13 needs, two of which—looking like a spaceship, and looking like a sports car – we decided to keep as design constraints instead of full specifications. Each specification was designed to ensure a need will be met. These are included in the Specifications Table. We have divided compliance into four categories: test, analysis, and inspection. For specifications requiring inspection, the project will be compliant if, by observation, it falls within the required tolerance. For specifications requiring testing, a test plan will be written for data collection, in order to compare it to our required tolerance. After compiling this table, you can move into design with full knowledge of the constraints you have.
Make Sure You (and Your Actors) Don't Break a Leg
As with any design, it is critical to explore potential risks, so as to avoid them as you continue through the design process. Any risks you come across, consider a means to mitigate them. Some things to consider are the safety and well-being of your actors. Will your actors be sitting in a position of a long period of time? Ensure that they can be in as a comfortable position as possible. Maybe the actor has to exert some effort to stand or get out of the prop. Make sure you develop the right mechanisms to let them do so with ease.
Because our prop was to be used only for a few performances, maintenance was not a major concern for our team. However, when you are designing your prop, it will be important to consider the life you want it to have. Should you want to use your prop for years to come, you may want to consider developing a maintenance plan. Aside from the longevity of the prop, you should also consider immediate dangers that could arise during rehearsals or performance. You’ll want to make sure that you are using nonflammable materials and that if any electrical power is required for your prop, it is approved beforehand. For our team, the main of concern were the thermoplastic shell, as it could be damaged if someone fell and put their all of their body weight onto it. However, for us, it was worth the risk because thermoplastic is a forgiving material; if it becomes dented, we can remove it, place it on a mold, heat it up, and the dent will be gone.
Additionally, we considered the safety of the actor that would actually be inside of our prop. If you chose to have someone inside of your prop, it is of paramount importance that you consider how they will exit under strenuous circumstances. For our team, that meant adding a quick release gate latch to ensure that our actor could easily exit at any time. With whatever materials and design you chose, it is important that you develop tests to verify your specifications and you develop a safety plan in the event something goes wrong.
Stick to Your Budget
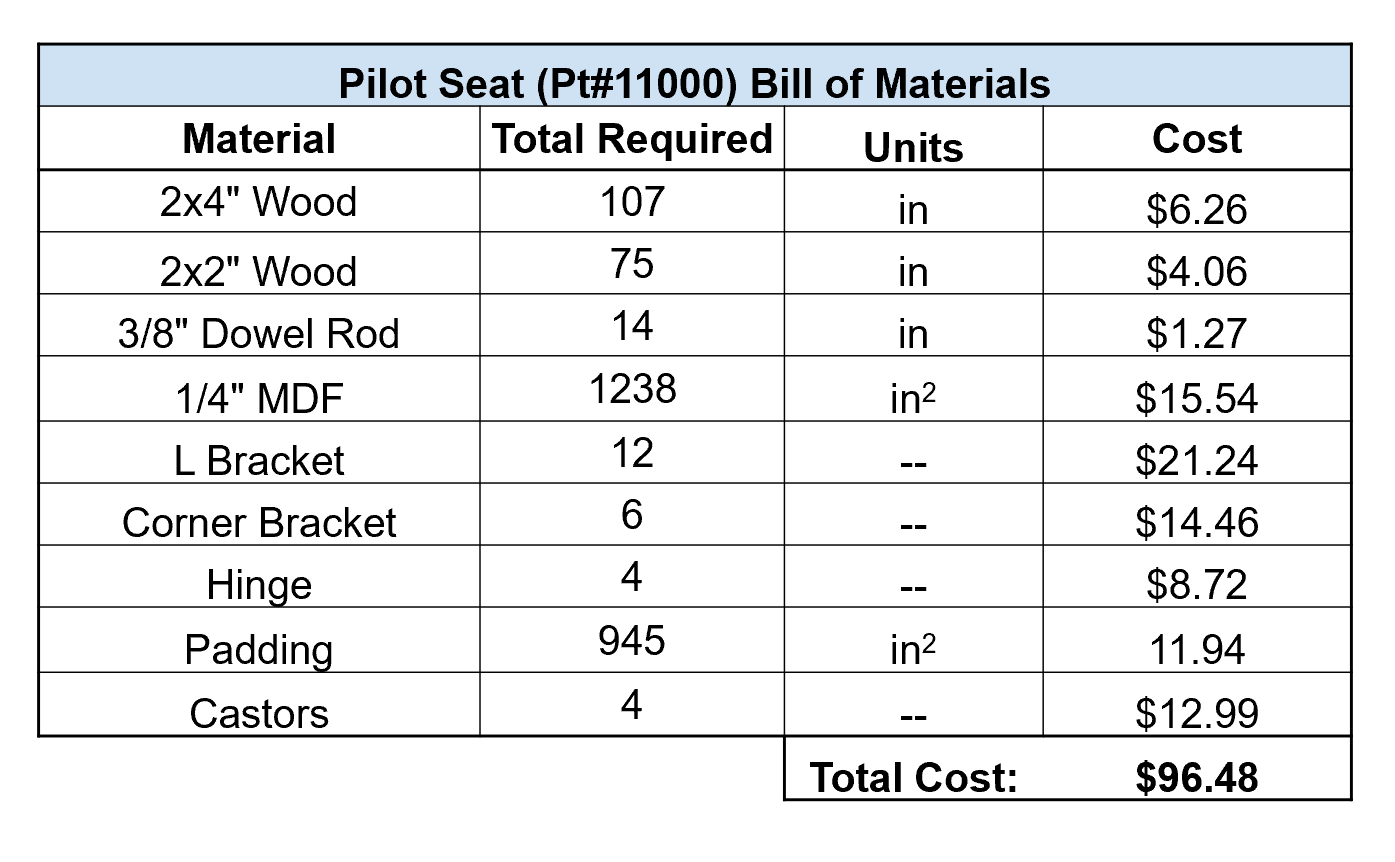
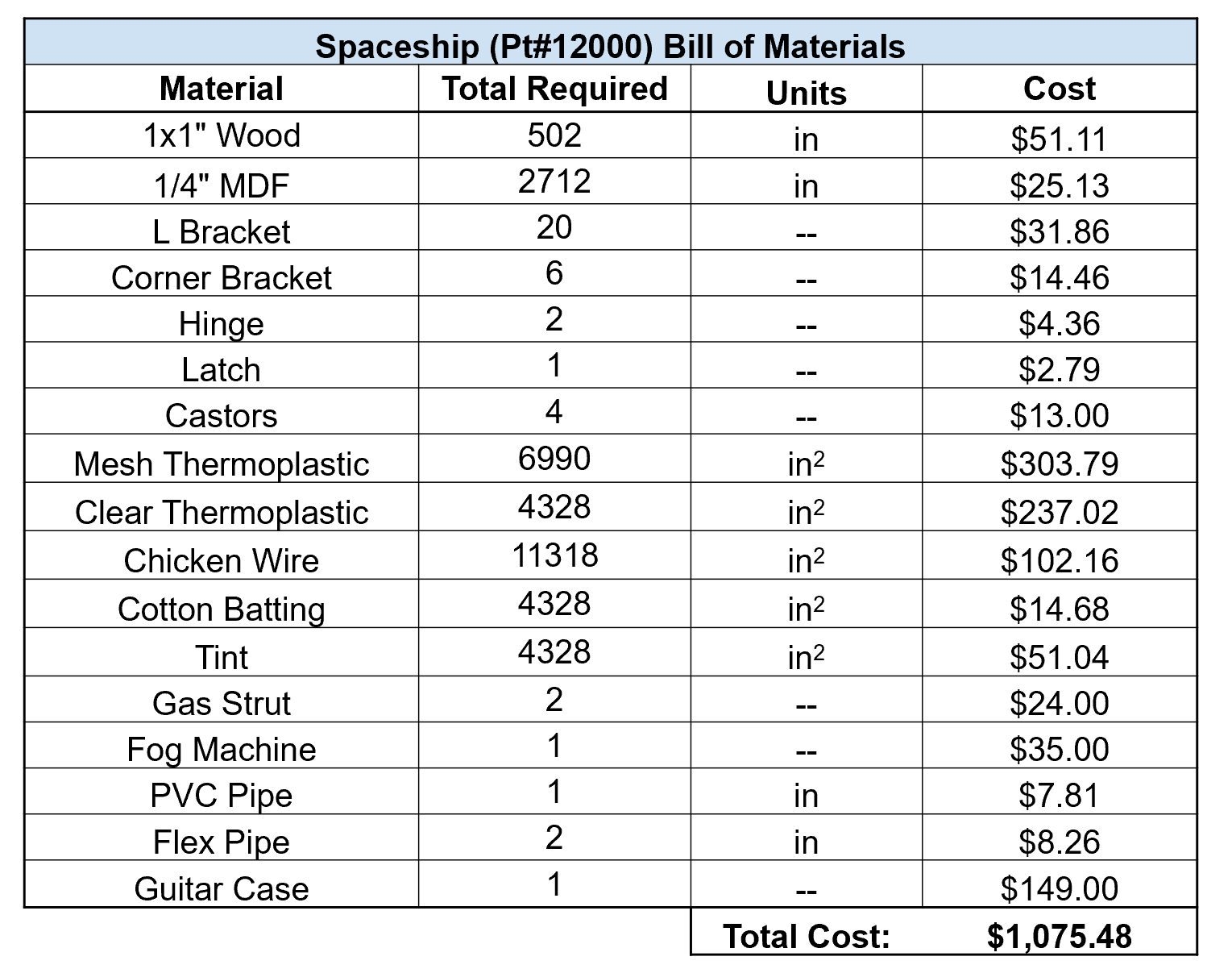
Knowing your budget early on will help simplify the entirety of the design process. Although you don’t want to put any constraints on your creativity during the ideation phase, having a budget will help you to narrow down some of your ideas as to what is most feasible for your production. Once you have broken down your design to the nuts and bolts level (this is the Modeling your design phase as mentioned in the scheduling section), you can create a detailed Bill of Materials. Here, you will want to include every part you will need for your project (ideally broken down into prop subsystems), a vendor that sells the part you need, and an anticipated price of your part (don’t forget shipping costs if you are ordering online). You’ll also want to consider how your will be manufacturing your prop:
- Are there any specific tools that you need that you don’t have access to, and will you need to buy or rent that equipment?
- Are there any parts that you will have to outsource manufacturing, and what is the associated cost of that?
- Is there any sample materials required for testing, and how much will that cost?
- Is the time you spend building the prop coming out of the budget, and how much do you anticipate that being?
Once you have completely fleshed this out, you should have a fairly good sense of the cost of your project. Now, you’ll need to compare the anticipated cost to your budget. If your anticipated cost is equal to or below your budget, you can begin to procure necessary materials, but if you are over budget, you may need to reconsider your design or budget—and this may set you back in terms of scheduling.
Buying/ordering materials early on can help you stay on track with your schedule. Remember, if you order parts online, there is likely at least a week of lead time before your part arrives. Make sure to keep track of what you’ve bought in your Bill of Materials and update the actual cost of them (you can even compare your anticipated cost to your actual cost of materials). Additionally, keep track of what has arrived, and try to keep all your parts as organized as possible. If you’re building a sizable prop, you’ll need to find a large workspace to store all of your materials.
Concept Prototype
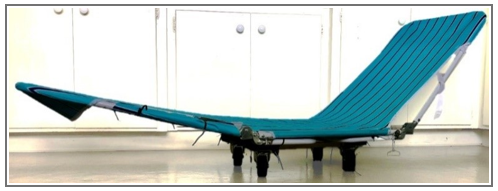
If you feel confident with an idea for your prop, consider making a concept prototype. This prototype does not have to be perfect; it only to give an idea of how well your concept can perform. It also does not have to be a prototype of your whole prop, it can be one function.
Our team wanted to develop a rolling mechanism separate from the outer spaceship shell itself. For our concept prototype, we strapped a beach chair to a dolly to simulate how we can roll our pilot into the ship from underneath the stage. We found the idea to be so successful that the concept was used in our final design.
Structural Prototype
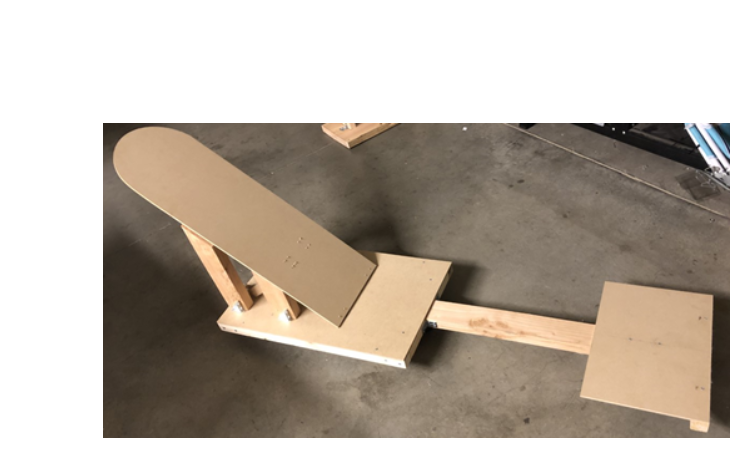
Similar to the Concept Prototype, the Structural Prototype is an early prototype of your design. At this point you should have your project more fleshed out and can now make a prototype that better reflects your final design. You have a couple options with how to pursue your structural prototype. You can create a rough version of your overall prop. This will allow you to see if everything fits together and will function as intended. Otherwise, you can create a final version of one of your key components. This will allow for early testing to ensure your component will function properly. If you are short on time, we recommend the latter option.
Our Structural Prototype was an extension of our Concept Prototype. We really wanted to focus on how easy it was for our pilot to be able to get into and out of our prop. Thus, our Structural Prototype allowed for critical testing earlier on.
Designing Your Chosen Concept
Now that you’ve chosen the best overall concept, it’s time to dive into the details. This stage of the process is about figuring out how everything fits together BEFORE you start building. We’ll go over how to break the overall design into manageable chunks, the best tools for rapid designing, the best times to run it by your director, and what to include in the final design. Keep in mind at all points that you will be building this, so you want to design it to be as easy to manufacture and assemble as possible given the tools and expertise you have.
Subsystems
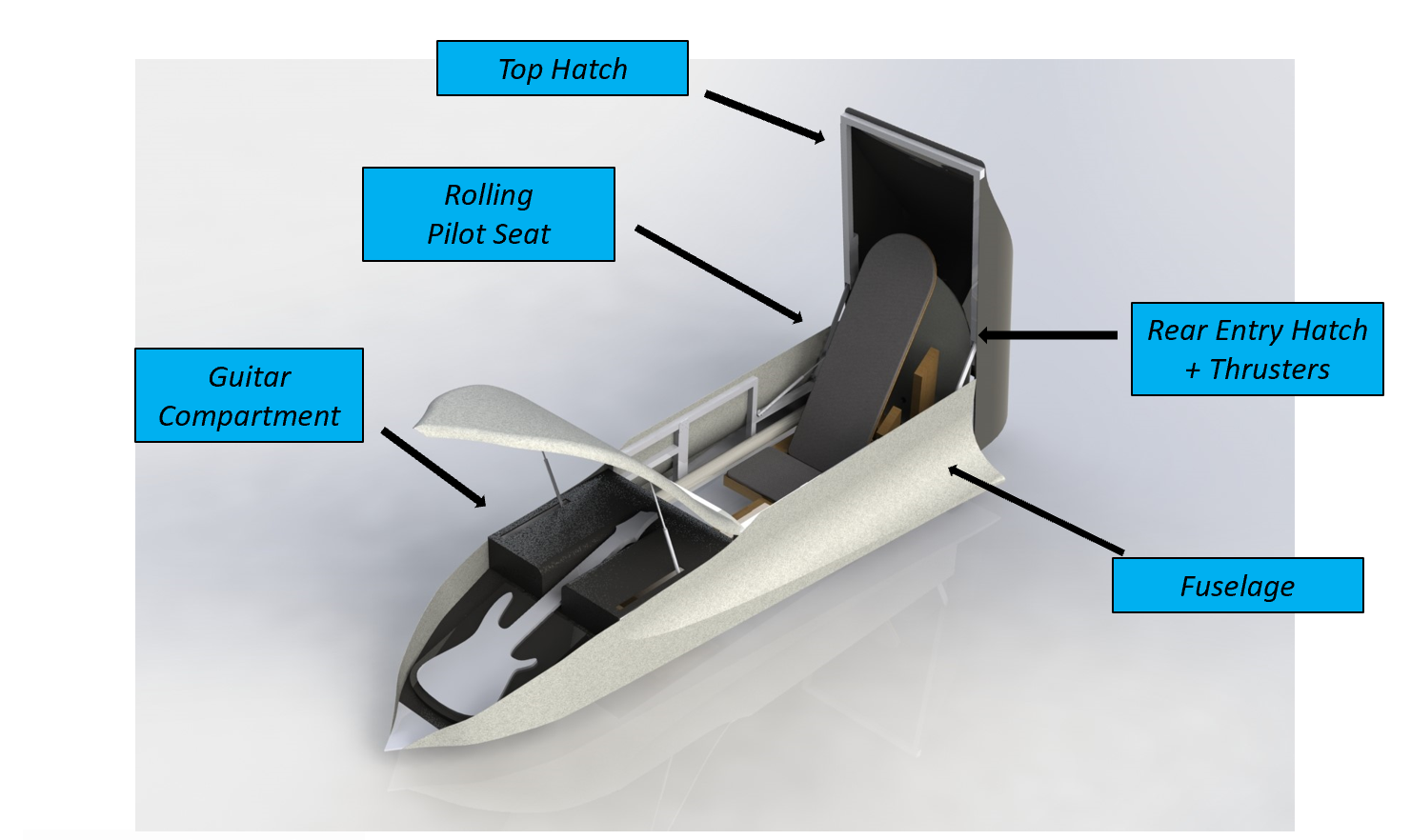
During your brainstorm, you broke each concept down into a set of functions. A subsystem is a part of your concept that accomplishes a function. Most designs have between three and six subsystems. It doesn’t have to move: a rigid frame has the function of support.
Once you have several subsystems, determine rank them by which is the most important to get right. You want to develop these first because they have the most potential to go wrong, and the worst impact on the performance if they do go wrong. You’ll catch more bugs in the design, and it will be done first, allowing you to prototype it earlier. This prototype will catch more bugs. Since it was done early, you’ll have enough time to fix everything before the show.
Having multiple subsystems makes it easy to divide and conquer. If you have a team working on this prop, one person can take each system, as long as you’re all communicating constantly about how the systems fit together and what space they need to take up. Alternatively, one person can design while the other take on the other tasks outlined in this Instructable.
Computer-Aided Design (CAD)
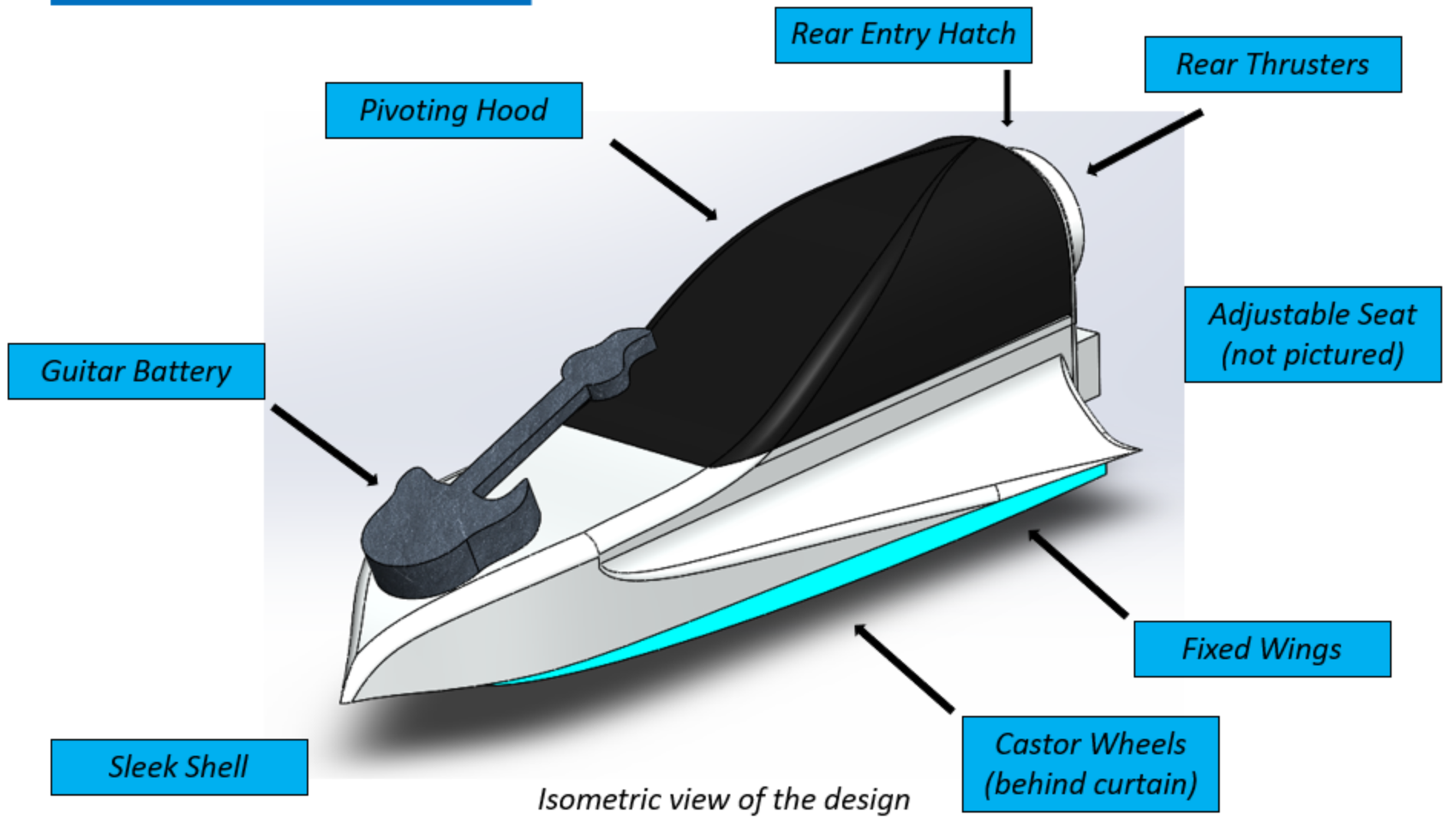
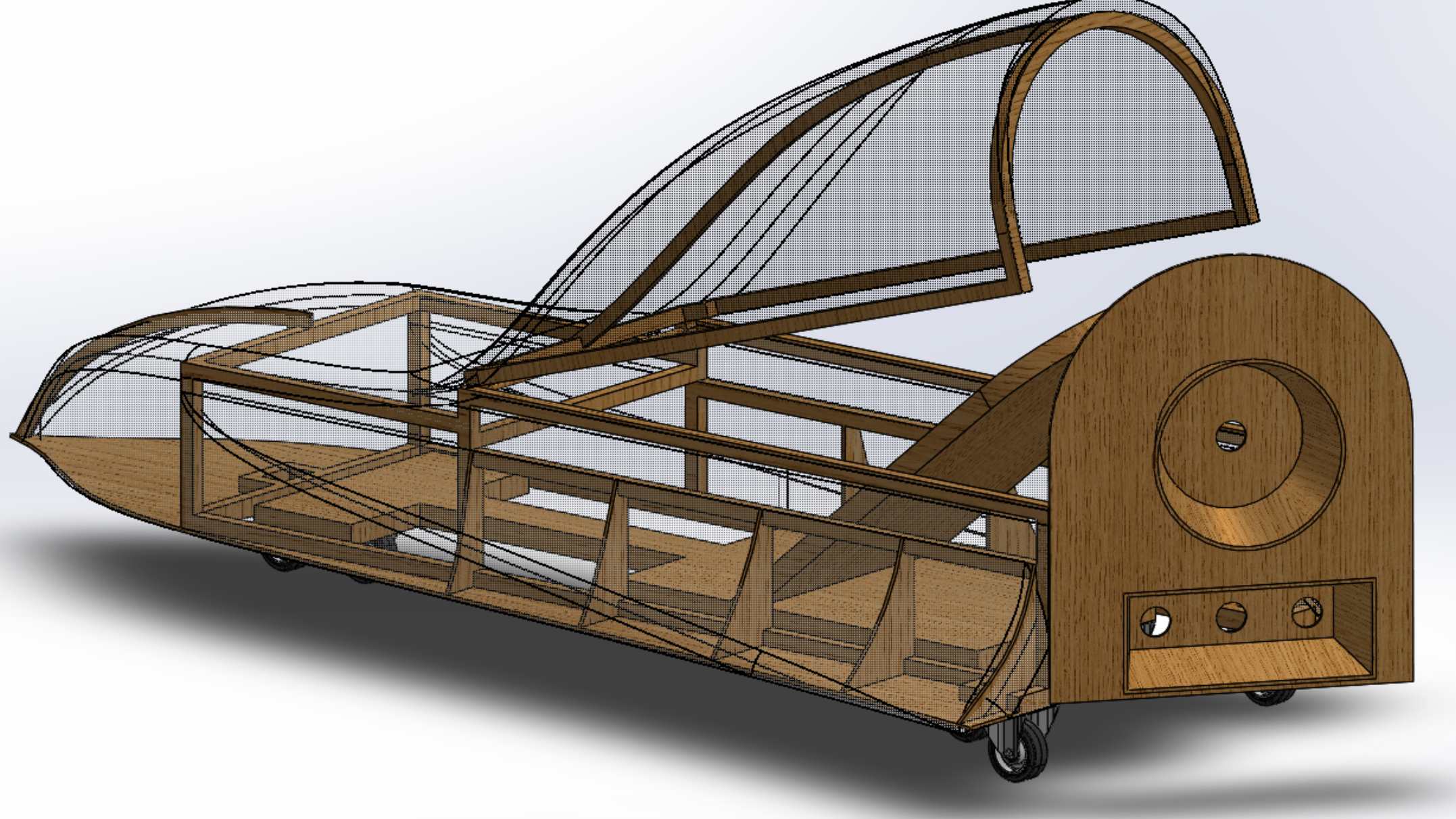
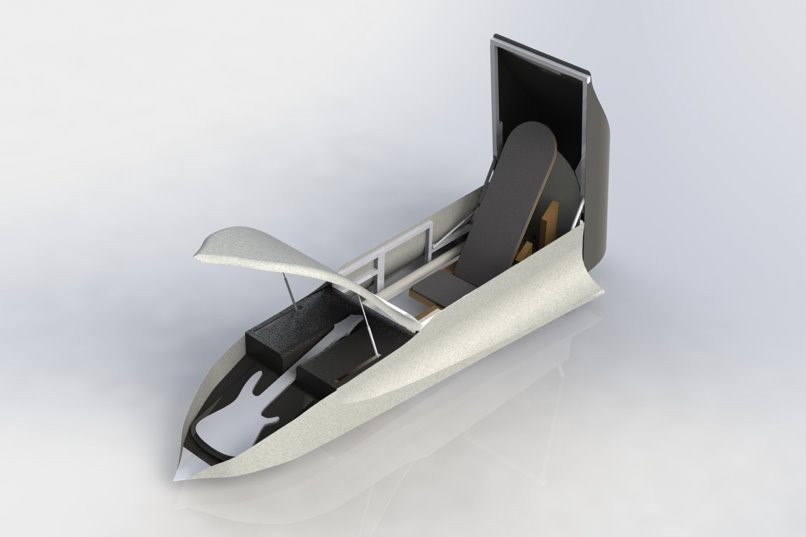
Hand sketching worked well for communicating rough overall concepts during the brainstorm, but it won’t work well for detailed design. Every piece needs to be the right scale, checked from different perspectives, moved, resized, deleted, altered, or replaced countless times as new problems crop up. This is where digital programs, CAD, are a huge help.
Most of these programs are expensive, but if you’re a student, you can access some professional software for free. Even if you’re not a student, you have options. For students, I would recommend Solidworks or Autodesk Inventor. For non-students, try out Fusion 360 or FreeCAD.
Once you have the software, it’s best to progress in three stages for complex props:
1. Overall design with key dimensions. In this stage, model each subsystem as just a few large parts. You want to make sure key dimensions work spatially. Does the prop fit where it needs to be stored? If you’re holding a human, is there enough room for them? Can all the subsystems fit together without clashing? Does every moving subsystem have the space to move without running into anything else?
2. Detailed design with realistic pieces. With rough dimensions set, subsystems can now be modelled realistically. Think about how the prop might be built while creating each part. If you’re making a door, what material will it be? What thicknesses does this material come in? How will this door attach to the frame, hinges? How will it be manufactured, tablesaw? What constraints do these tools put on the shapes you can create?
3. Nuts-and-bolts level. Once all the pieces of all the subsystems are complete, you can start modelling how everything comes together. Which parts will be glued, which need screws, which need hinges or pistons or curtain rods or staples. Think about how components within the subsystems will go together. Think about how the subsystems themselves will come together. Once you have a good idea, you can move on from modelling with CAD.
Design Checkpoints
It’s easy to get lost in the details and miss things when designing. Bring in another pair of eyes whenever possible, asking them to double check and tell you if anything doesn’t make sense. There are a few key moments in design to get your director’s feedback.
After selecting your concept. Show your director the rough sketch and explain the subsystems and functionality of the prop. Ask if they approve of it, and whether they have any changes to it if so.
After the 1st step in CAD, when overall dimensions are checked. Show the model to your director, how it fits when stored, how it looks on the stage, and describe the aesthetics. This scale 3D model will give a better idea of exactly how the prop is going to look.
After the 2nd step in CAD, when you know the pieces and processes you’ll use to make them. Running the design by your director now will give them a good idea of what it will cost, the materials, and the true complexity.
After the 3rd step in CAD, when the design is finalized. The director shouldn’t have much feedback at this stage, but getting final approval is important to ensuring everyone is on the same page before the most time-intensive part – the building – begins.
If you check in at least during these key times, you’ll ensure you don’t waste time designing in the wrong direction and having to start from scratch. Once parts of your design are finalized, you can start prototyping them, even while working on other parts of the design. If everything is done and approved by your director, you should start building the final prop!
Procure Materials
We found it easiest and most economical to procure as many manufacturing materials as possible from the same vendor. We found that Home Depot was a good source for fasteners, wood, wood glue, and PVC pipe. You may need to find other special materials elsewhere.
Manufacture Parts of the Frame
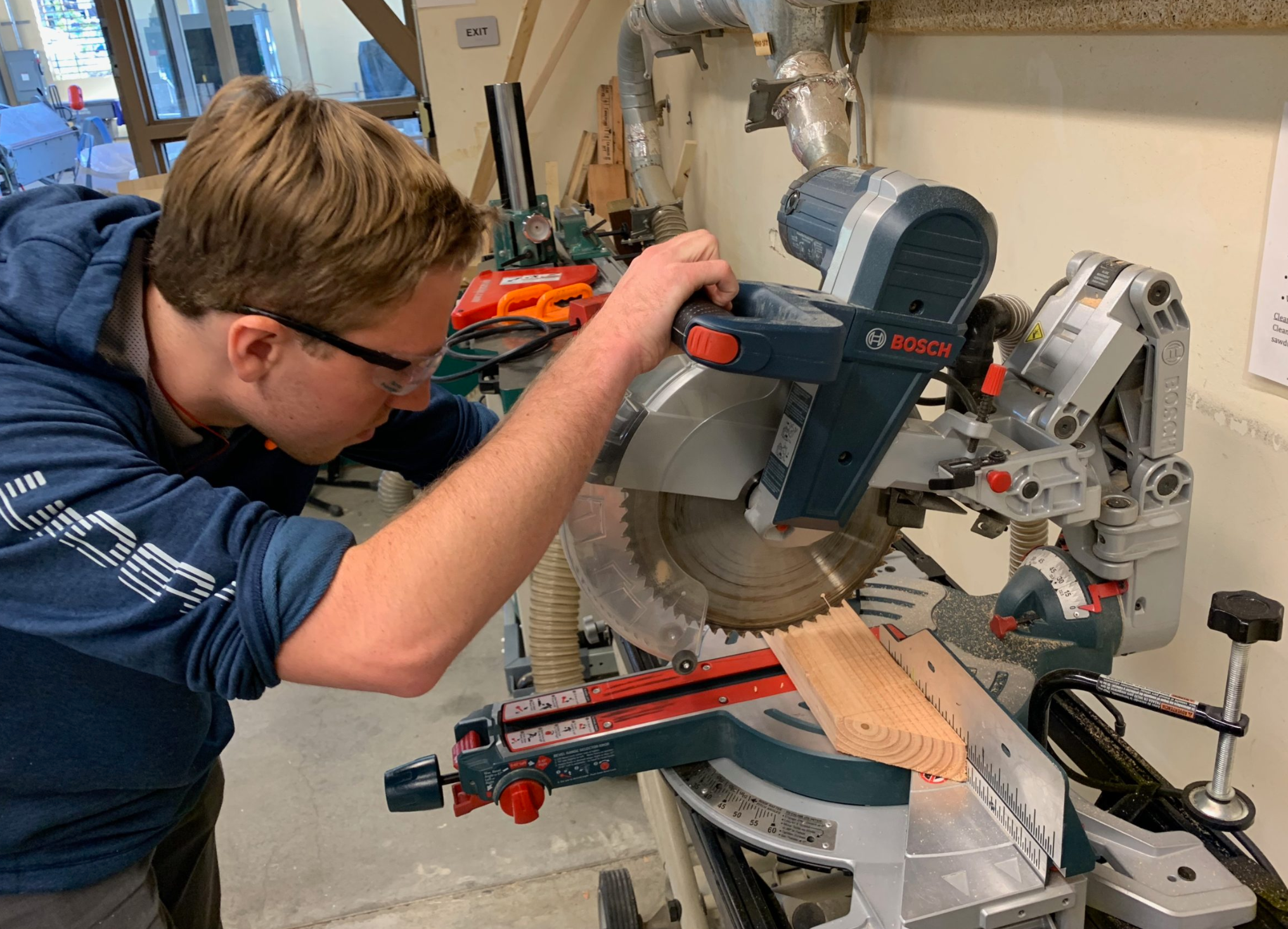
If you’re going for a frame made up pieces with square cross-sections, it is possible to use 2x2” wood boards (which are actually 1.5x1.5”). However, we found that 1x1” square wood dowel was less splintery and much more uniform, making it much nicer to work with.
One of the fastest and easiest way to cut the pieces of the frame is with a miter saw. Most miter saws have the capability of cutting at specific angles with the help of a built-in protractor. If you don’t have access to a miter saw, a hand saw would also work fine. However, this would make cutting much more work and to achieve angles you would need to draw it on the wood with some sort of protractor and straight edge.
Manufacture Panels
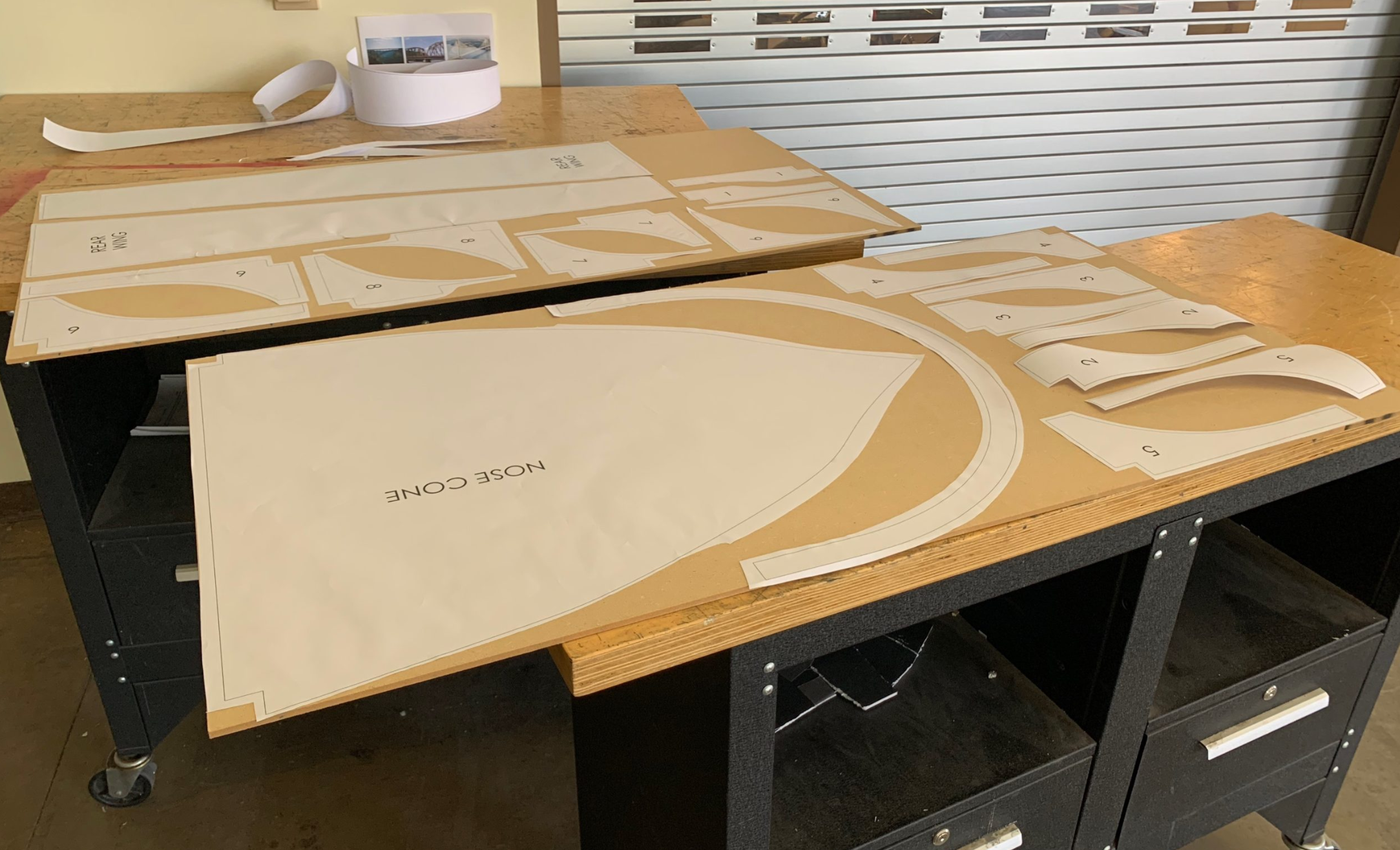
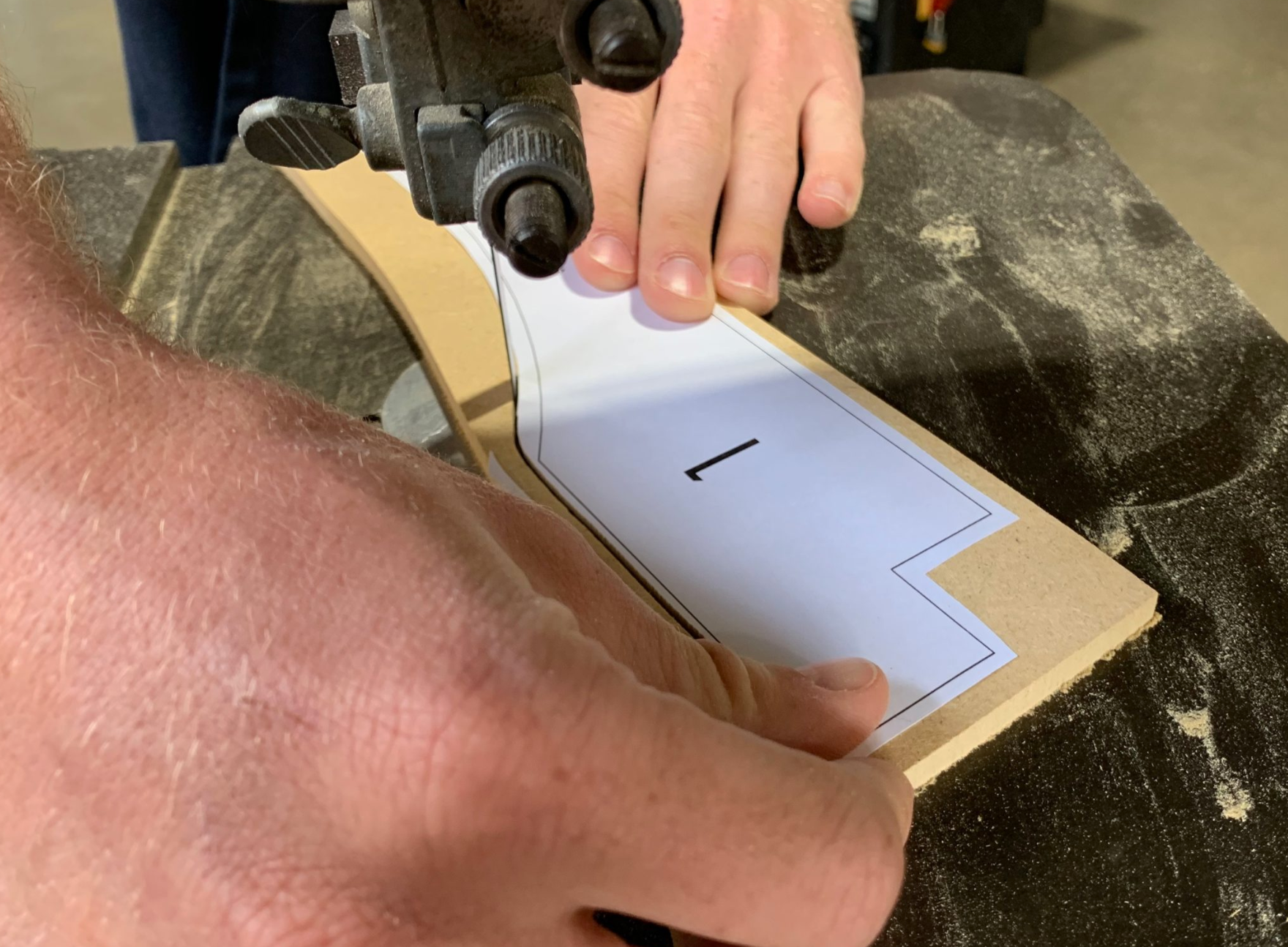
There are plenty of materials which could be
used to make panels, but we considered using either MDF or plywood as they are cheap and easily cuttable. We ended up deciding to use MDF for the purpose of cleaner manufacturing as it doesn’t splinter like plywood.
Before talking about manufacturing techniques, we want to talk a bit about safety. While using any machinery, always were safety glasses and avoid using gloves, especially while sanding! Also, loose hair and clothing should be managed (or removed) so it doesn’t have a chance of getting caught in machinery.
To cut rectangular pieces that aren’t really tiny, it is probably best to use a table saw, as it is able to make quick straight cuts at right angles. For more complicated shapes, there are other options to choose from. One great method is using a laser cutter which is able to accurately cut complex shapes automatically, as long as the piece you’re trying to cut isn’t too big for the laser cutter.
Another method involves printing the shapes of the pieces onto paper and then adhering these onto the panels before cutting with a band saw. This was the method we chose to use because we thought it would be quicker knowing some of our pieces wouldn’t fit in the laser cutter anyway. This process actually turned out to be a bit tricky and quite slow. Also, it is much easier to print shapes larger than standard sheets of paper with a plotter on large sheets. After the shapes were printed, we cut around each individual one, making sure to not cut into the shape. Then, we used double-sided tape to adhere the papers onto the MDF sheet. Then, we used a band saw to cut out each individual piece from the MDF sheet.
Depending how accurate you want to be, you may want to leave a gap between where you’re cutting and the printed shape. It’s worth noting, however, that internal corners are tricky to sand so it’s worth it to carefully cut right on the line with the band saw.
After cutting is complete, the pieces can be sanded by hand or with motorized sanding tools. Straight edges or convex curves can be sanded with belt or disc sanders, while concave curves can be sanded with an oscillating spindle sander.
Assemble the Frame
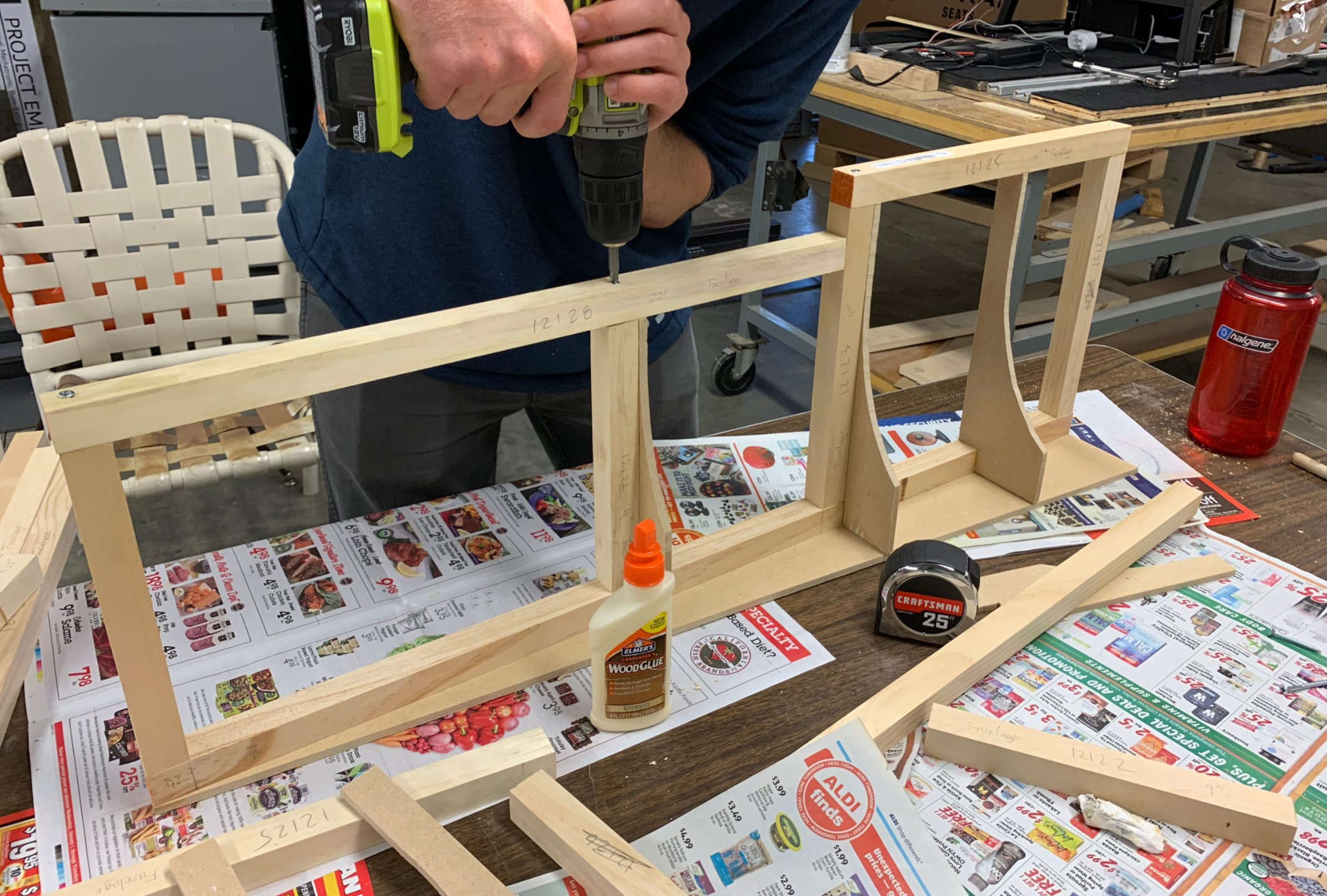
Now that all of the pieces of the frame have been cut, it’s time to put them together. You could just use wood screws to put everything together, however we decided to use wood glue for a few reasons. Ideally, the frame should be as rigid as possible, and to achieve this with only screws would require at least two screws at each junction of the frame to prevent rotation at the joint.
This would have been a real challenge because of the relatively small cross-sections of our frame (1”x1”). Theoretically, L-brackets and T-brackets could be used, but these usually take several screws and they usually don’t result in a very rigid connection. On the other hand, wood glue can be easily applied to even the smallest of joints and the resulting connection is stronger and much more rigid than one using screws.
The one caveat of using wood glue is you need some way to clamp the joint as the glue sets. If you’re dealing with a large frame with many glued joints, as we were, it would be a royal pain, if not impossible, to use actual clamps for every joint.
However, we found a much simpler way which was to use a single screw at the glue joint to clamp the wood pieces together. While this approach requires screws, it requires many fewer than if no glue was used and it makes the assembly process quick and easy. Our end result came out very rigid and seemed very strong.
Lay Up the Thermoplastic Shell
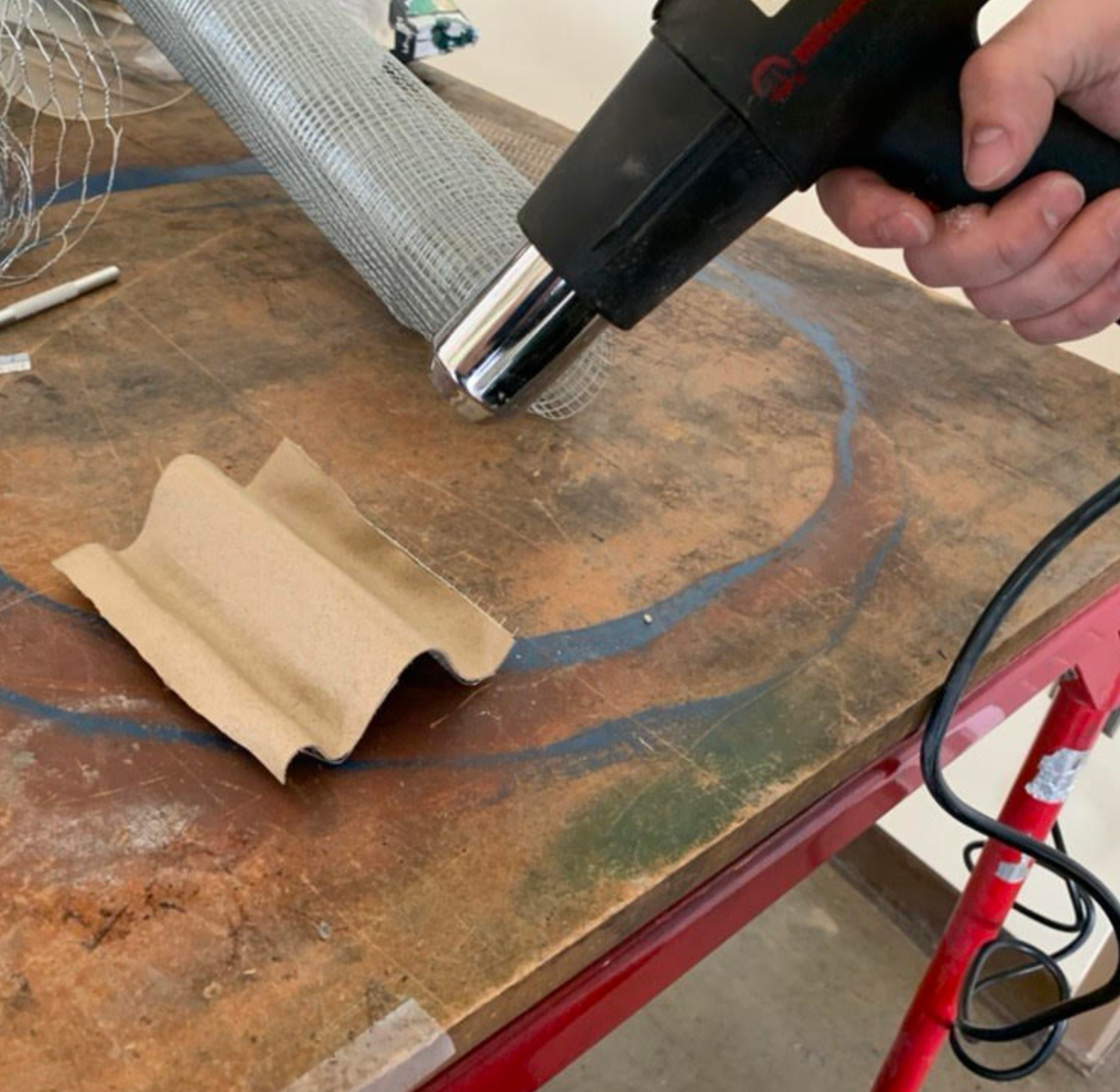
Our team decided that the use of thermoplastics would be a
relatively inexpensive way to achieve a smooth external finish. Although we never actually got to put it to the test, we wanted to give you a few pointers from what we did learn about the material in testing.
Thermoplastic materials are easy to work with using common household tools and without much experience, making them a popular choice for DIY projects like making cosplay props and costumes.
Thermoplastic requires heating to a modest temperature before it can be easily molded to its intended shape. To achieve it’s intended shape, it’s important to create a mold for the thermoplastic to form to.
We used chicken wire with a ¼” square mesh. We found that a fine mesh is important to achieve a smooth finish of the plastic. The chicken wire can be cut with wire cutters and bent into shape by hand. Though, you should be careful of sharp, pointy edges created after cutting, and you may want to use gloves to protect your hands.
After bending the chicken wire to the desired shape, we covered the chicken wire with cotton batting to achieve an even smoother finish. Once the mold is ready, you should cut out a piece of thermoplastic to a desirable size, then place it over the mold and apply even heating with a heat gun. After the thermoplastic is molded to its final shape you can paint it with spray paint.
If you’re using transparent thermoplastic and you want it to be tinted, there are a few options to do this. One way is to use tinting film which is typically used to tint car windows. However, we found that this film adhered poorly, so we wouldn’t recommend it. Another way is using spray-on tinting, which should be much easier but it may be difficult to achieve an even coat. Finally, there’s submersion tinting which involves soaking the clear thermoplastic in a mixture of water and tinting dye. This method should result in a nice, permanent, even tinting effect.
The thermoplastic vendor, Worbla, we sourced our material from had so many great resources, and we've linked their website here!
Test Your Final Design
It is very important to verify the efficacy of your design by testing it. If the prop must fit in a tight location, one simple test to do is to measure it with a measuring tape. Other tests which may be applicable include emergency egress testing, noise level testing, and structural testing. Emergency egress testing can be done simply by having someone inside the prop and another person timing them to see how long it takes them to exit the prop via the emergency exit. Noise testing can be done by ear or by a decibel meter (a smartphone app should work fine). Our design was at no risk of breaking due to the relatively small loading, but we still could run structural deflection tests by applying loads and measuring the deflection with a dial indicator.
Wrap Up
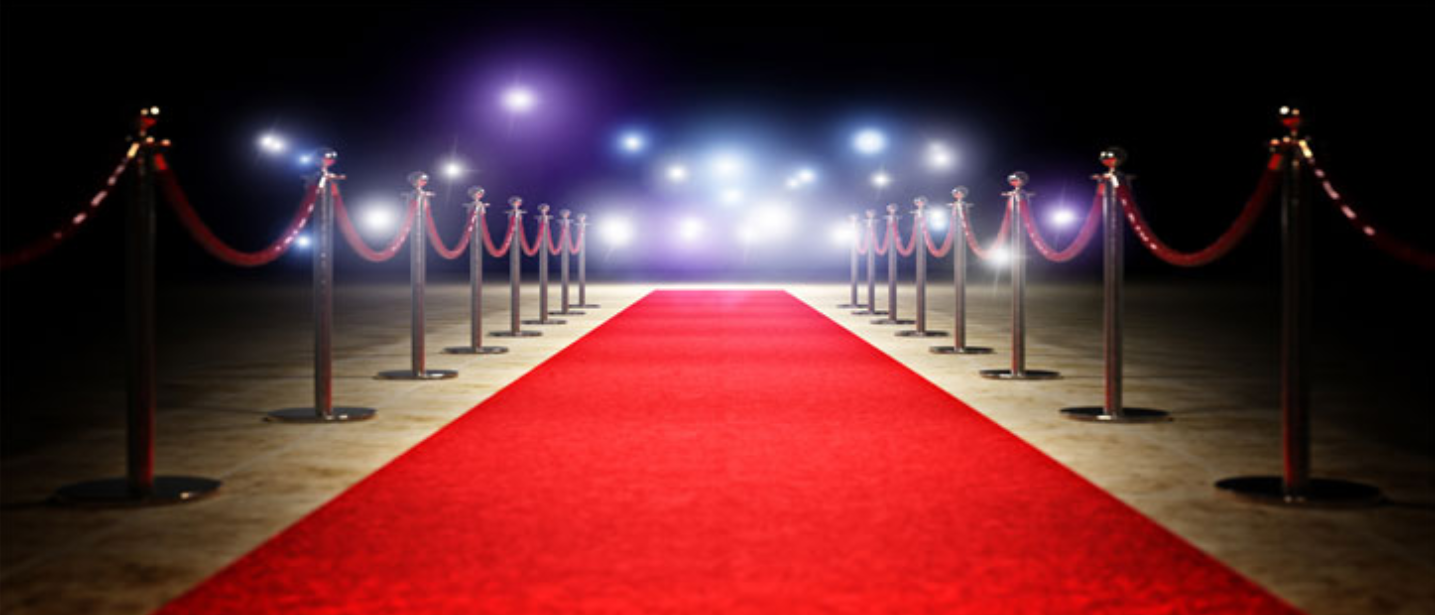
Once your prop is complete and you have done all of the appropriate testing, make sure to draft some sort of Operator’s Manual for all those who might be using your prop, but aren’t as familiar with the inner workings of it as you are. This will help to minimize safety risks. Additionally, if any long term maintenance is required, be sure to develop a maintenance plan and schedule. You’ll likely want to do some work to familiarize the actors with the prop before or during rehearsals, so your performance can go off without a hitch! Finally, be sure to enjoy your project and all your hard work!