3D Printed Portable Heater
by 3DCreation in Workshop > 3D Printing
5178 Views, 59 Favorites, 0 Comments
3D Printed Portable Heater
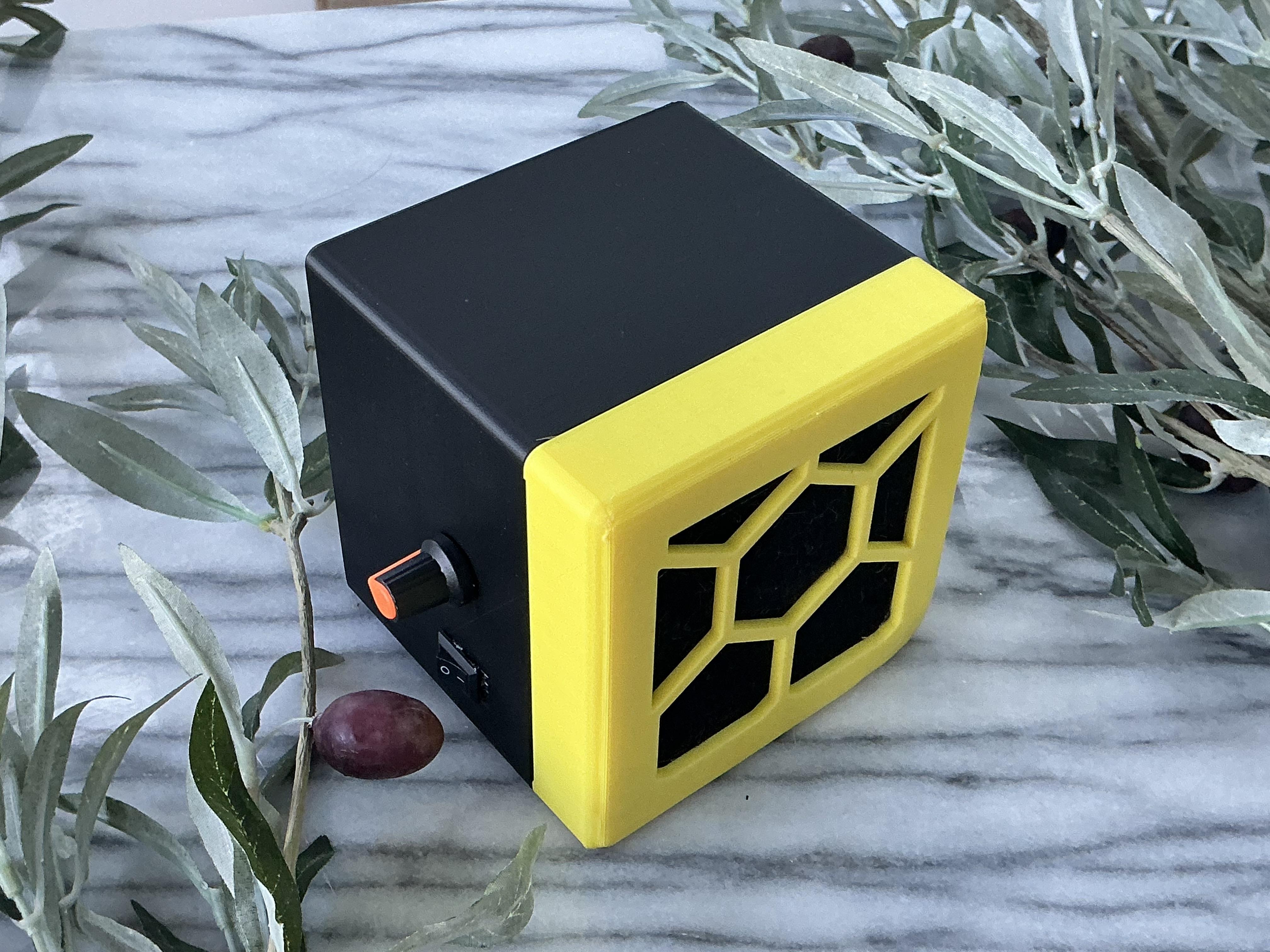
As the cold weather sets in, there’s nothing quite like having a portable heater that you can carry with you anywhere to stay warm. Whether you’re working at your desk, studying, camping outdoors, or just want a cozy spot in a chilly room, a small and portable heater can make all the difference. But why settle for off-the-shelf models when you can create your own custom mini heater? In this Instructables, we’re going to show you how to build a compact portable heater that not only provides heat but lets you adjust the temperature to your exact preferences.
This DIY project is perfect for those who enjoy working with electronics, love hands-on projects, or simply want a functional solution to stay warm during the colder months. With just a few basic tools and materials, you’ll be able to craft a heater that fits your lifestyle—small, efficient, and customizable.
What sets this mini portable heater apart from typical heating gadgets is its adjustable heat feature. Many portable heaters either have one fixed heat setting or are too bulky to carry around easily. By building your own, you get the flexibility of controlling the heat output—whether you need a gentle warmth to take the edge off or a higher temperature to really feel the heat. Plus, because it’s powered by a battery, you don’t have to worry about finding an outlet or dealing with tangled cords.
In this Instructables, we’ll walk you through the process of designing and assembling the heater. You’ll learn how to integrate a heating element, a simple temperature control system, and a battery-powered solution—all while ensuring your project is safe to use. By the end, you’ll have your very own portable heater that can go wherever you do, providing warmth exactly when and where you need it most.
Whether you're a beginner or have experience with electronics, this project is approachable and rewarding. Plus, it’s a great way to gain hands-on experience with key concepts like circuit building, temperature regulation, and power management. So, if you’re ready to stay warm in style, let’s get started on creating your very own adjustable mini portable heater!
Supplies
Materials:
- Yellow PLA Filament
- Black PLA Filament
- PTC Heating Module (Click Here)
- Motor Speed Controller (Click Here)
- Switch
- 12V Battery Holder
- 12V Battery
- Black Felt
Software:
- Tinkercad
- 3D Printing Slicer
Tools:
- 3D Printer
- Electric Screw Driver
Designing the Enclosure in Tinkercad
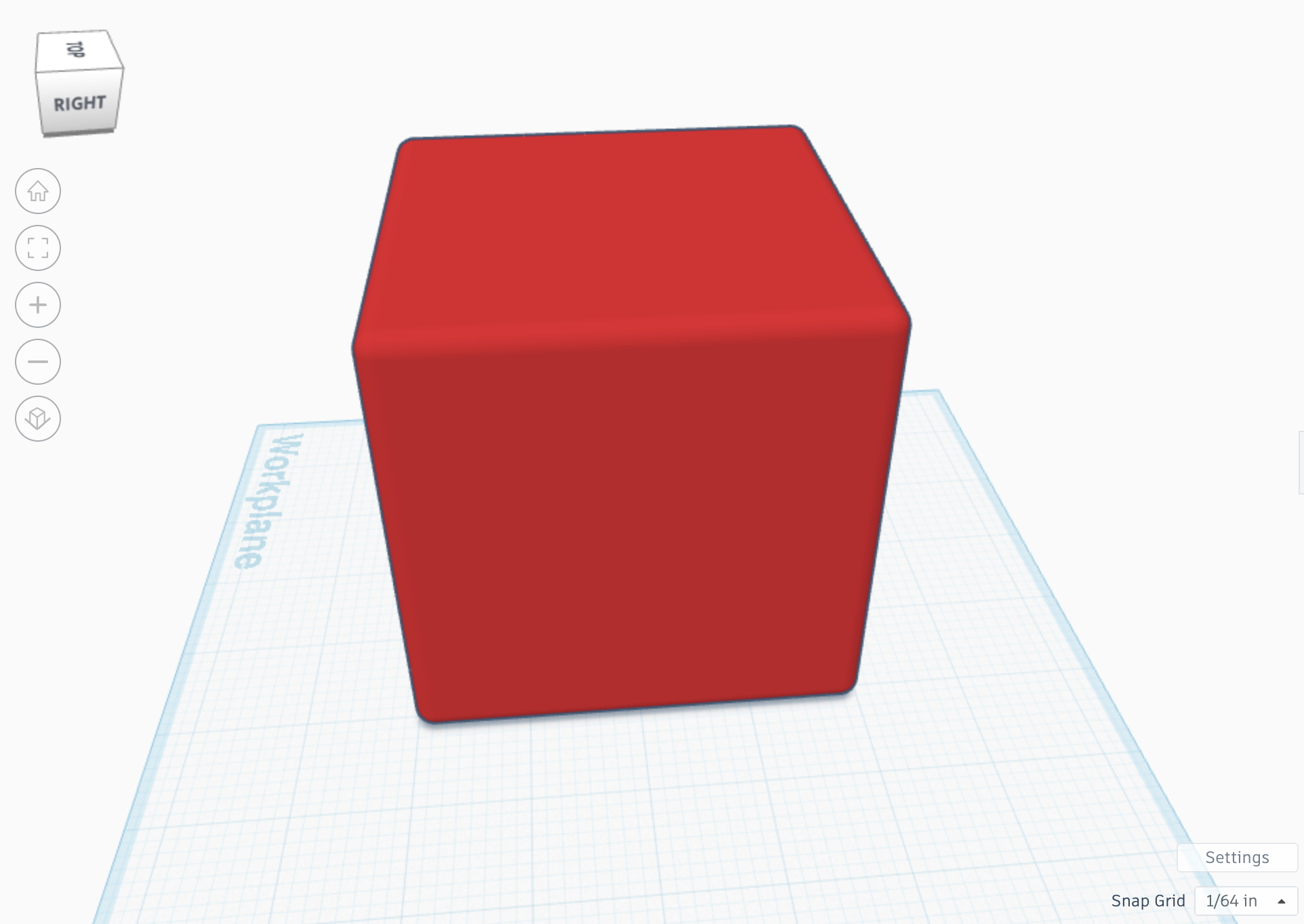
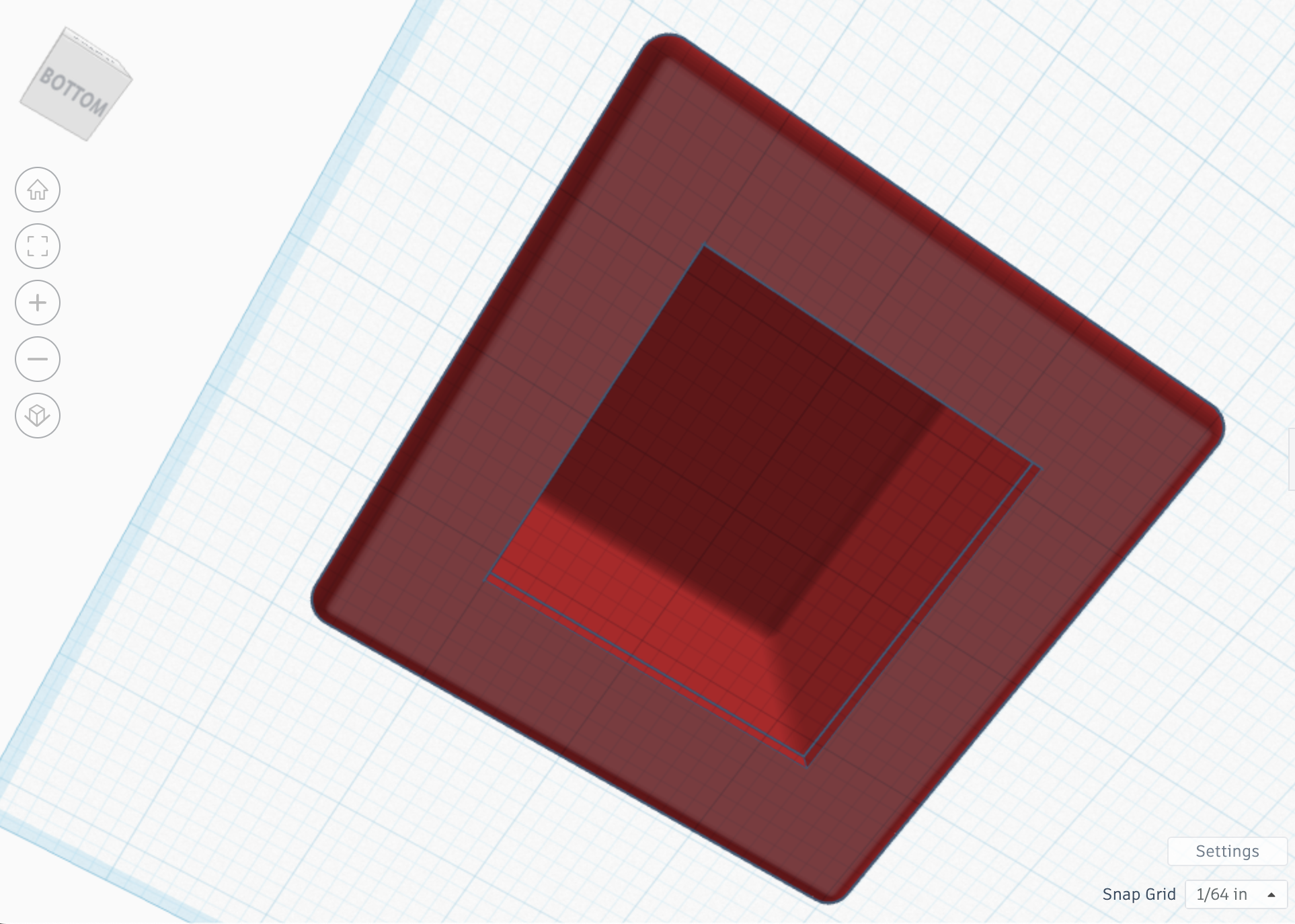
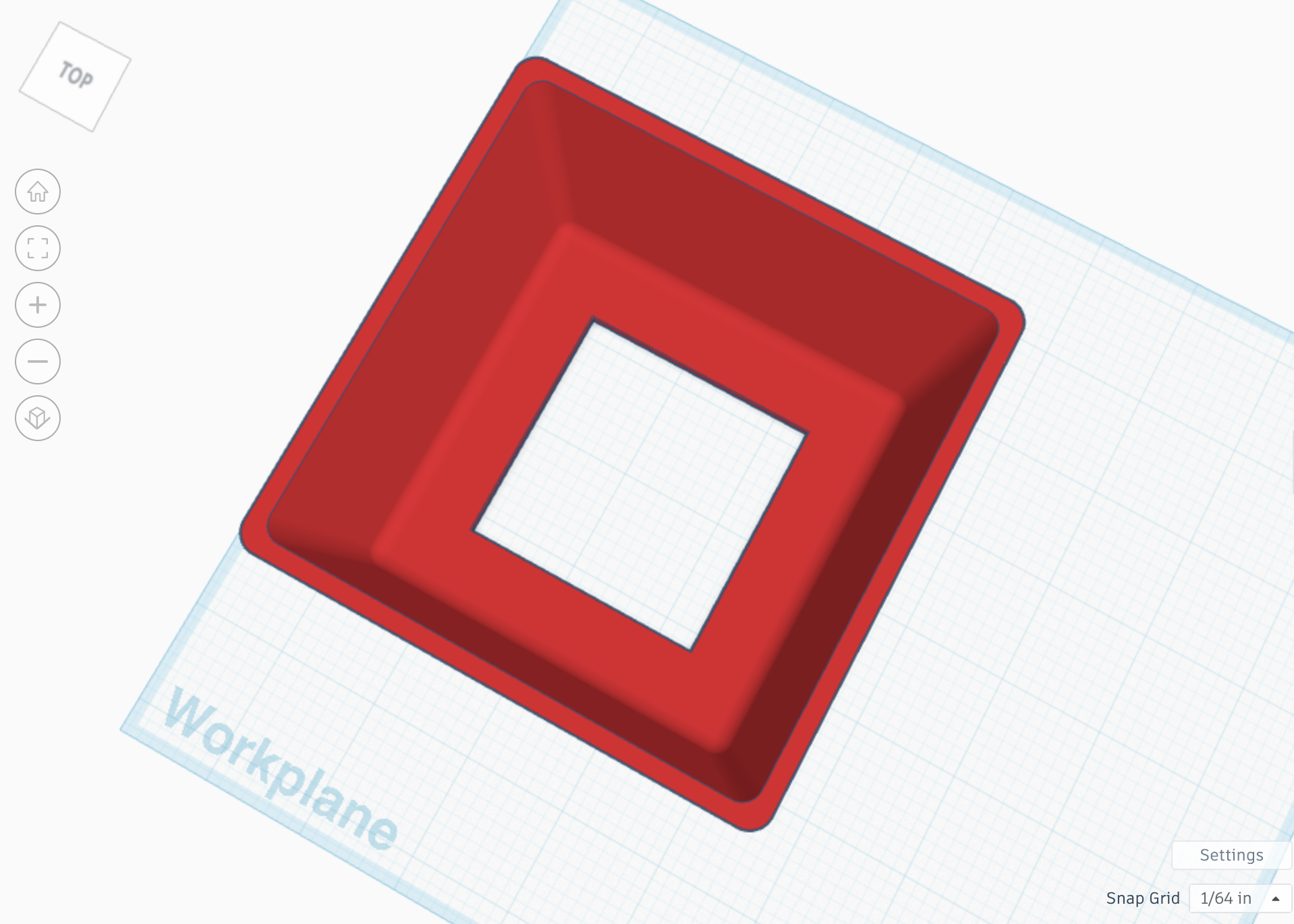
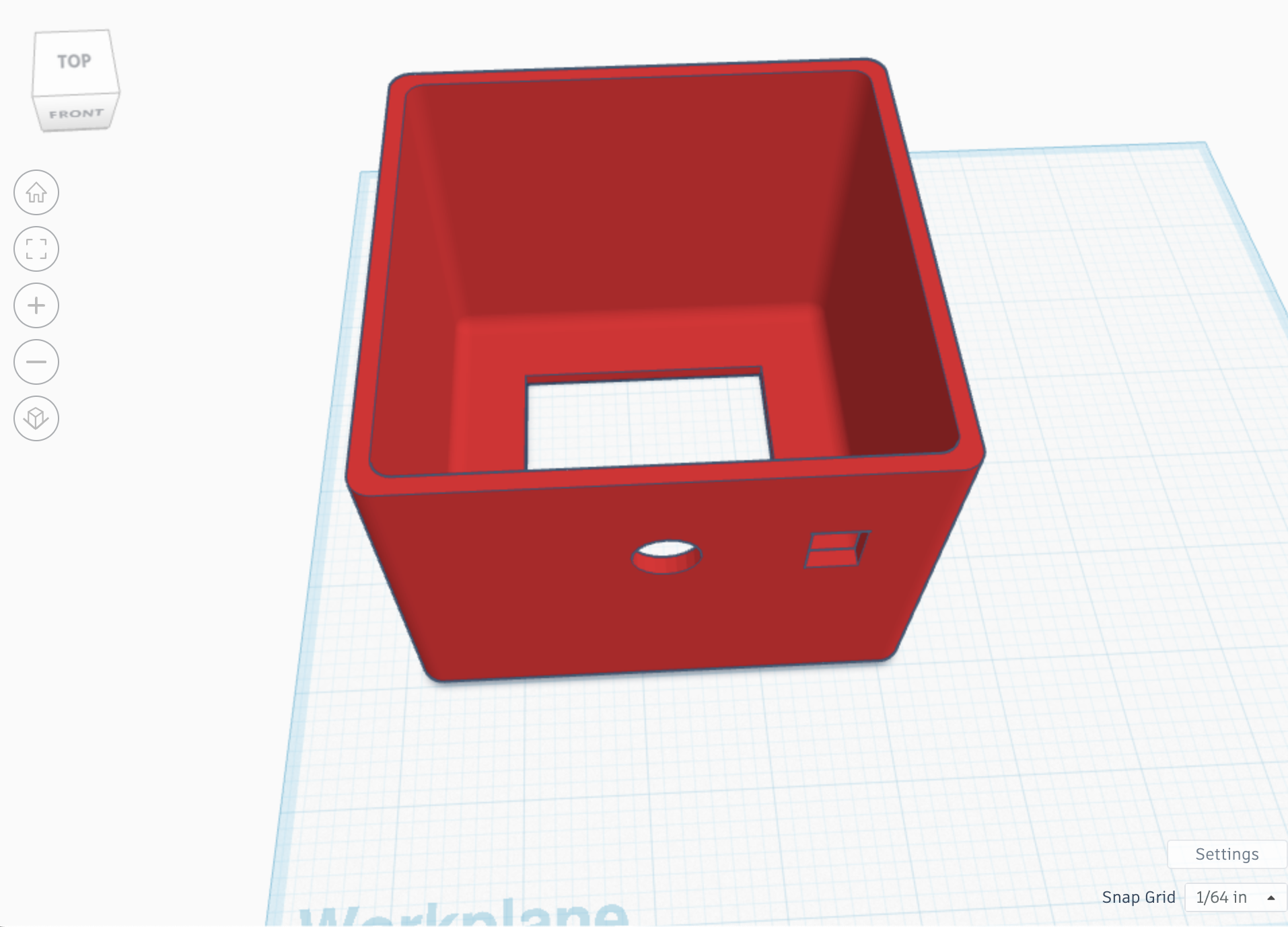
The design begins with the creation of a cube-shaped box that serves as the outer casing for the mini portable heater. This cube is the central structure, providing the physical boundaries that will house all the necessary components of the heater. The choice of a cube as the base shape gives the design a compact, easily manufacturable form while ensuring the internal components fit together snugly and efficiently.
The first task is to create a cutout in the cube for the fan and heating element unit. This unit is typically a single, integrated component that both generates heat and circulates air. The cutout needs to be carefully sized to accommodate the specific dimensions of the fan and heating element unit. It's important that the cutout allows the unit to sit securely within the casing, providing enough clearance for the fan to draw in air and direct it over the heating element. This ensures the heater works efficiently, circulating warm air while maintaining a compact form.
Next, the interior of the cube must be hollowed out. By subtracting a smaller, inner shape from the cube, you create a hollow space that can house the fan, heating element, and other internal components, like wiring and any potential support structures. The hollowing process must ensure that the walls of the cube remain thick enough to be structurally sound, providing support while still allowing enough room for the components to fit comfortably. The interior space will also help in managing heat dissipation, ensuring the components don’t overheat by providing enough airflow around them.
In addition to the internal space for the fan and heating element, the cube casing needs holes for user controls. These typically include a temperature adjustment knob to regulate the heat output and an on/off switch for powering the heater on and off. The holes for the controls must be sized appropriately to fit the controls you plan to use, ensuring they can be easily operated by the user. The position of these holes is important, as they should be accessible and convenient for use, typically located on the front or side of the casing.
Once the basic structure of the casing is complete, with cutouts for the fan and heating element unit, hollowed interior space, and holes for the controls, the design of the cube-shaped box begins to take shape. This structure serves as the foundation for the portable heater, holding all the necessary components in place and ensuring they are properly aligned and functional.
The next stage of design would involve refining the dimensions, ensuring everything fits together securely and making any adjustments needed to optimize performance. Additional features could be added, such as ventilation openings or airflow channels, to further enhance the heater’s functionality by allowing better circulation of air. You could also consider adding additional support elements or reinforcements inside the casing to ensure that the components are securely mounted and insulated for safety and efficiency.
Designing the Lid in Tinkercad
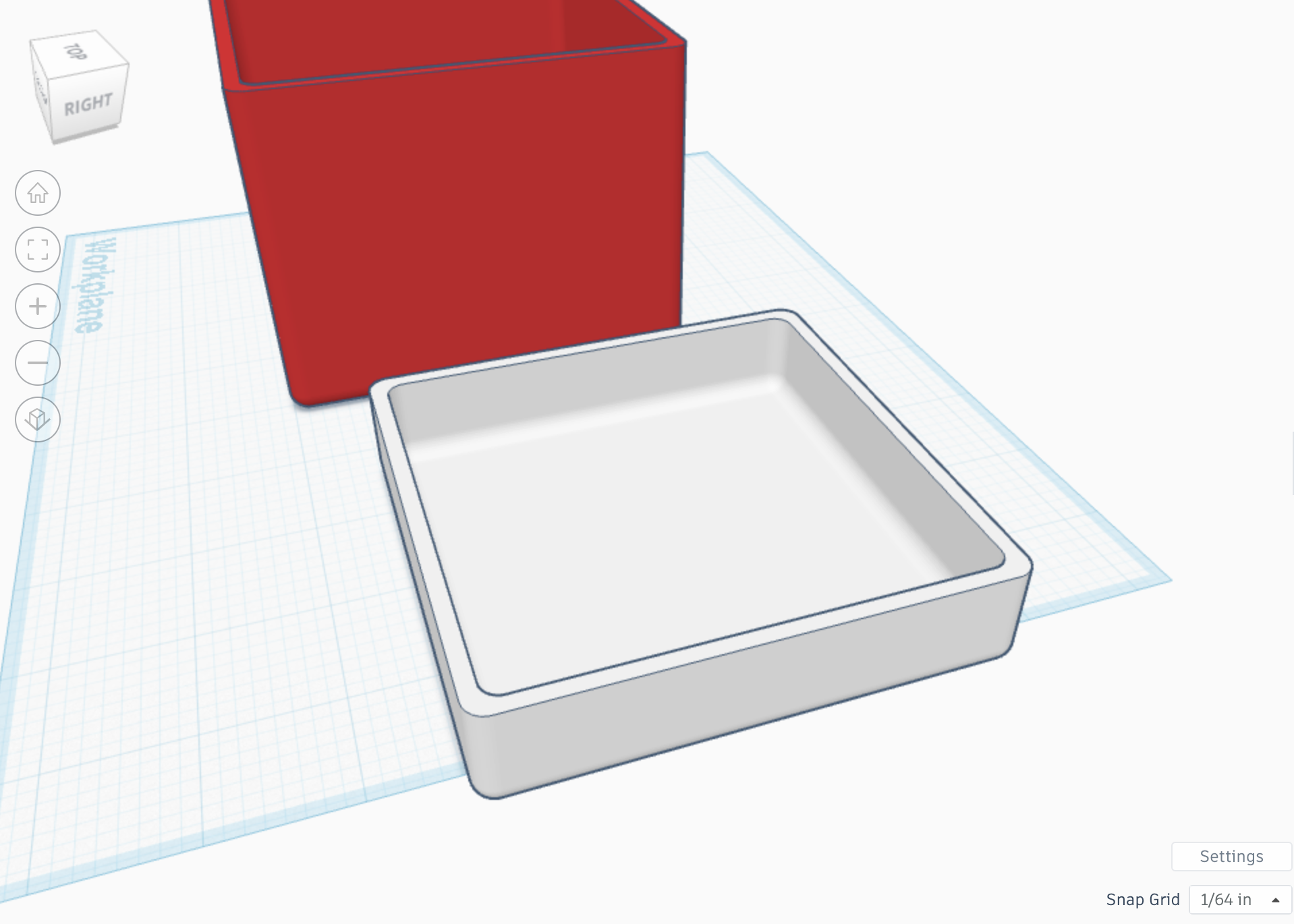
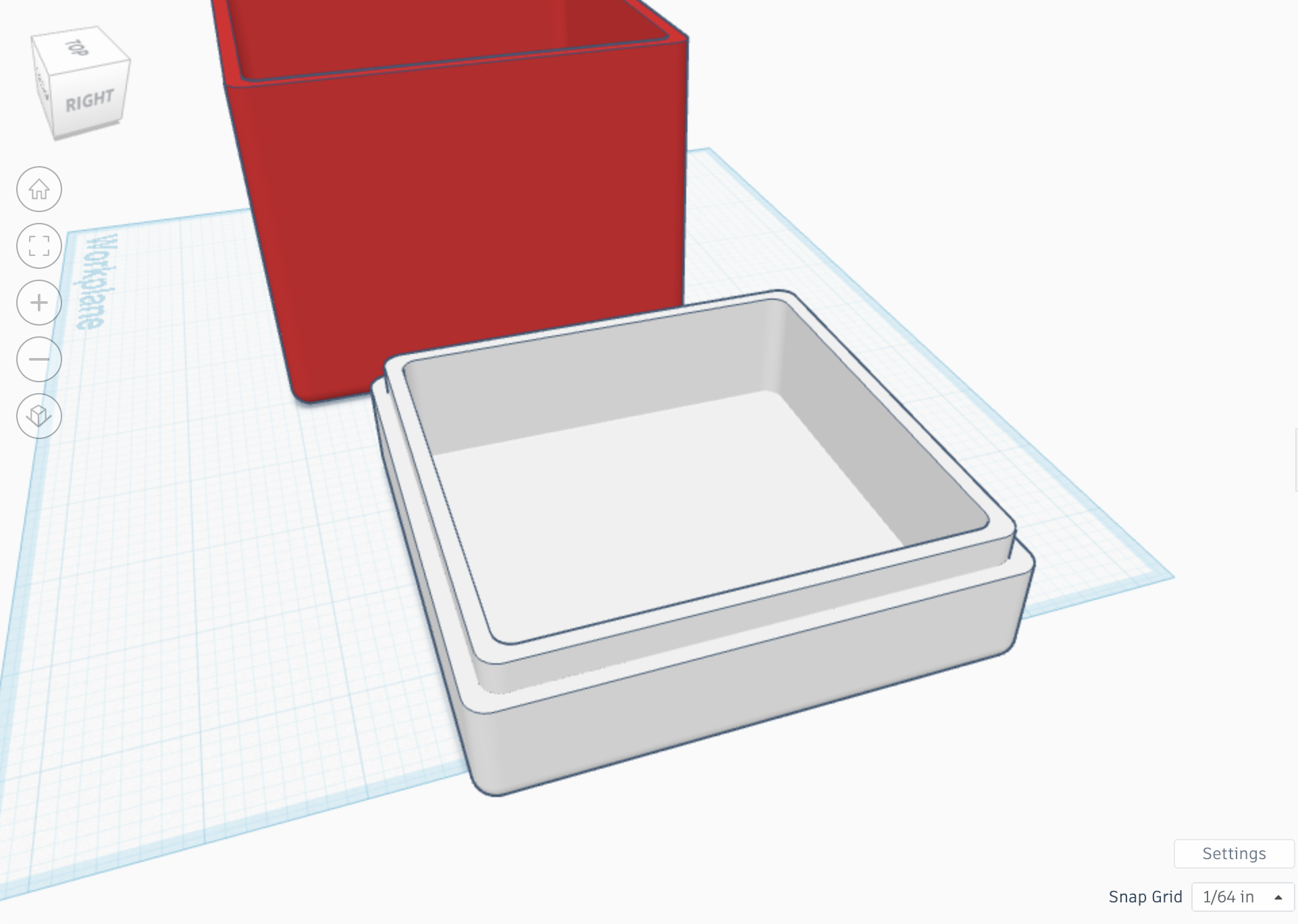
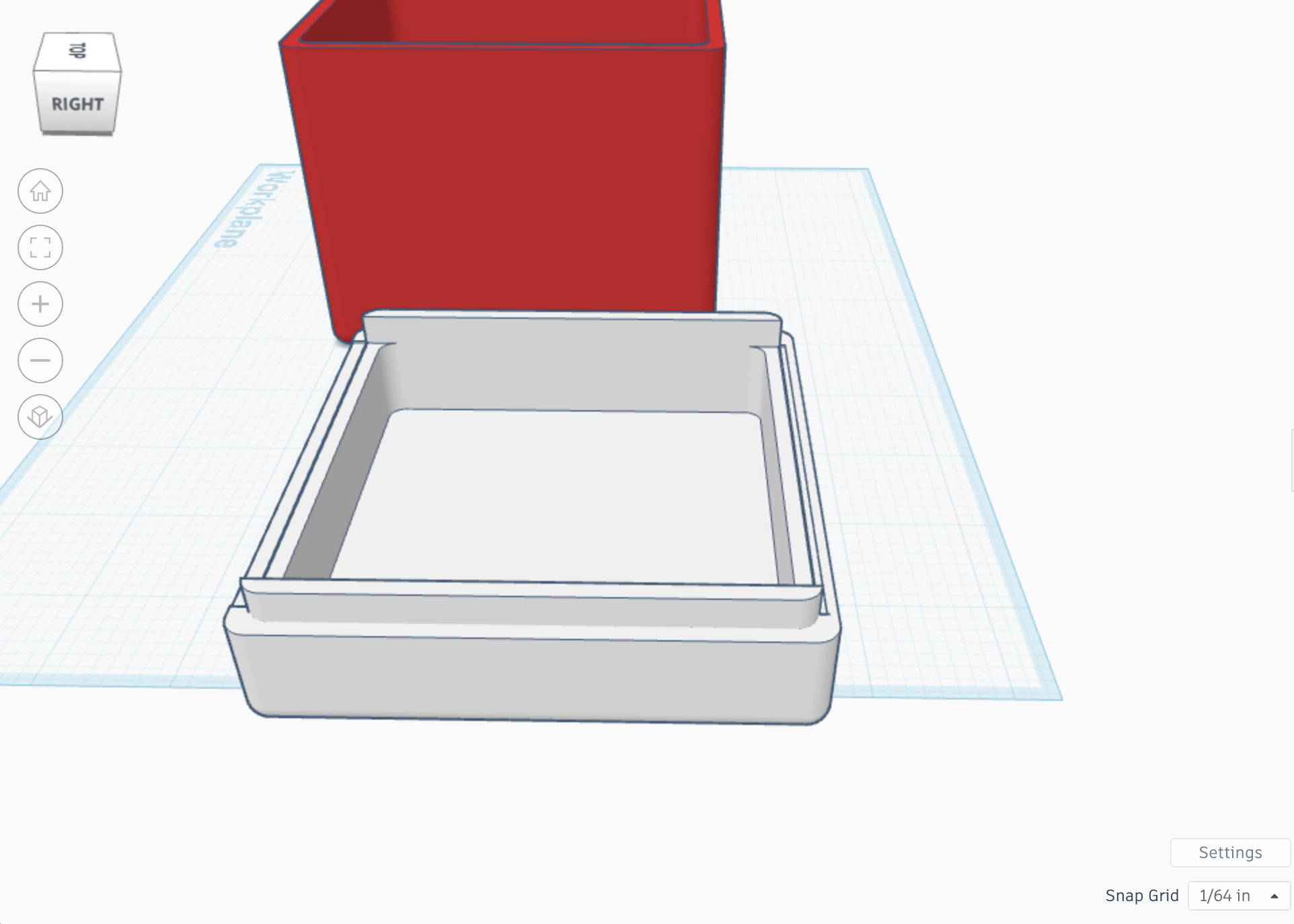
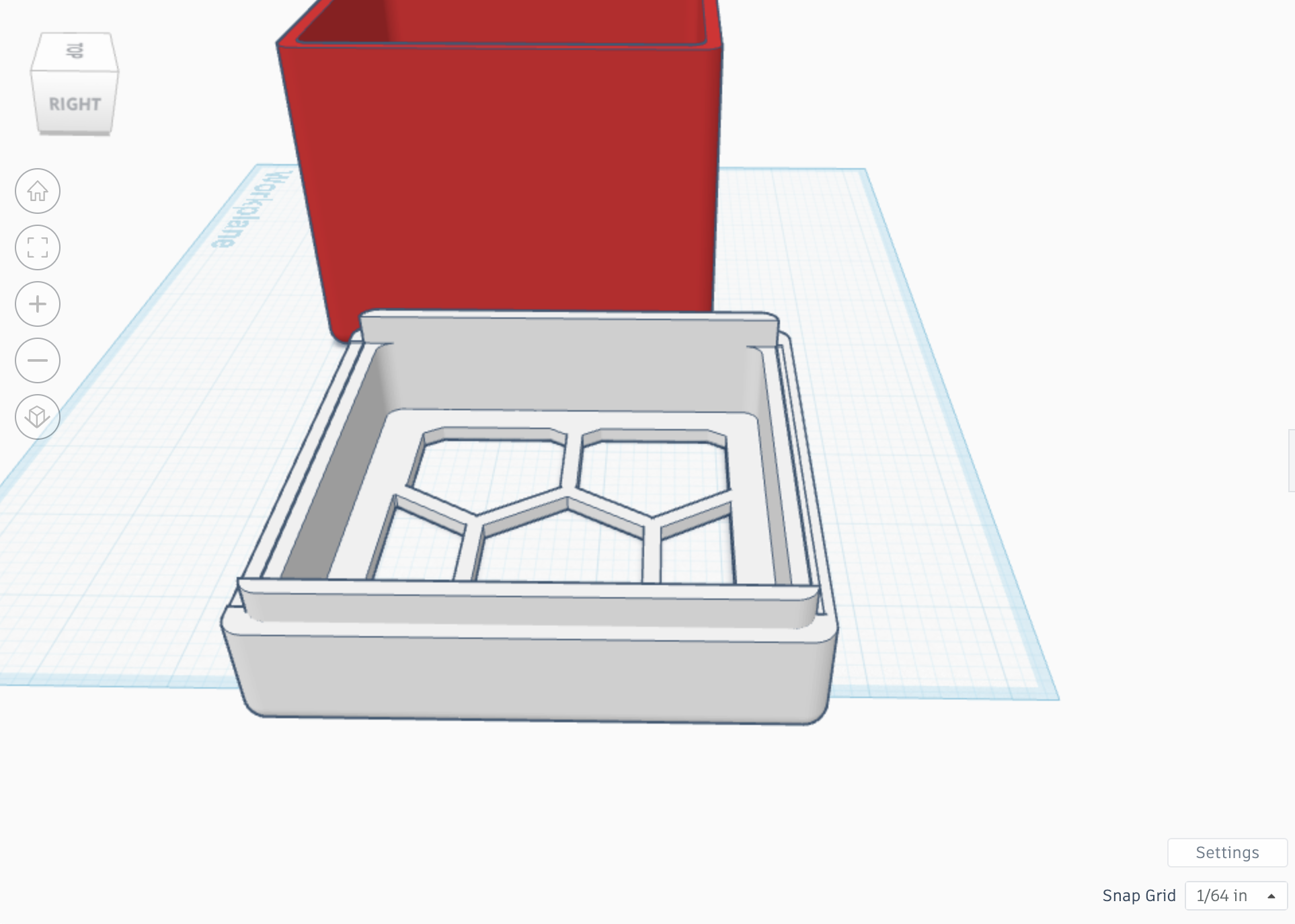
To create the lid for your 3D printed portable mini heater, start by placing a cube onto the workplane in Tinkercad and resizing it to match the size of your heater’s main enclosure. The cube should form the basic structure of the lid, with its dimensions matching the external size of the enclosure.
To bevel the cube, select it and then go to the shape options at the top of the screen. In the shape settings, you’ll find a "Bevel" slider. Use this slider to adjust the corner bevels of the cube. The slider controls how sharp or smooth the bevel will be—sliding it lower creates a more pronounced, angled edge, while a higher setting makes rounded edges. This beveling process will give the lid a clean, sloped edge without needing to manually cut the corners using wedges.
Once you’ve applied the bevel to the cube, create a duplicate of the cube and scale the duplicate down slightly to hollow out the lid. Align the smaller cube inside the larger one, ensuring it’s centered. Group the two cubes together to subtract the inner cube, leaving you with a hollowed-out lid that will be lightweight and sturdy.
After that, create a larger cube and align it with the beveled one. Set it to hole and then group it with the other cudbe
Now, to add the friction-fit rails, drag a Box shape from the Tinkercad toolbar and resize it to create narrow rails that will fit along the inner edges of the lid. These rails are designed to fit into grooves on the main enclosure of the heater, creating a secure, friction-based fit. Position these rails about 3-5mm in from the edge of the lid, and duplicate them as needed to cover all four sides. Once all the rails are in place, group them together to form the friction-fit structure.
For the air intake, use a Polygon shape and change the number of sides to 6 to create a hexagon. Resize this hexagon to the appropriate size for the air intake area of the lid. Arrange multiple hexagons in a grid pattern across the lid to create a honeycomb structure. This pattern will allow the heater to intake air through the lid for proper ventilation.
3D Printing
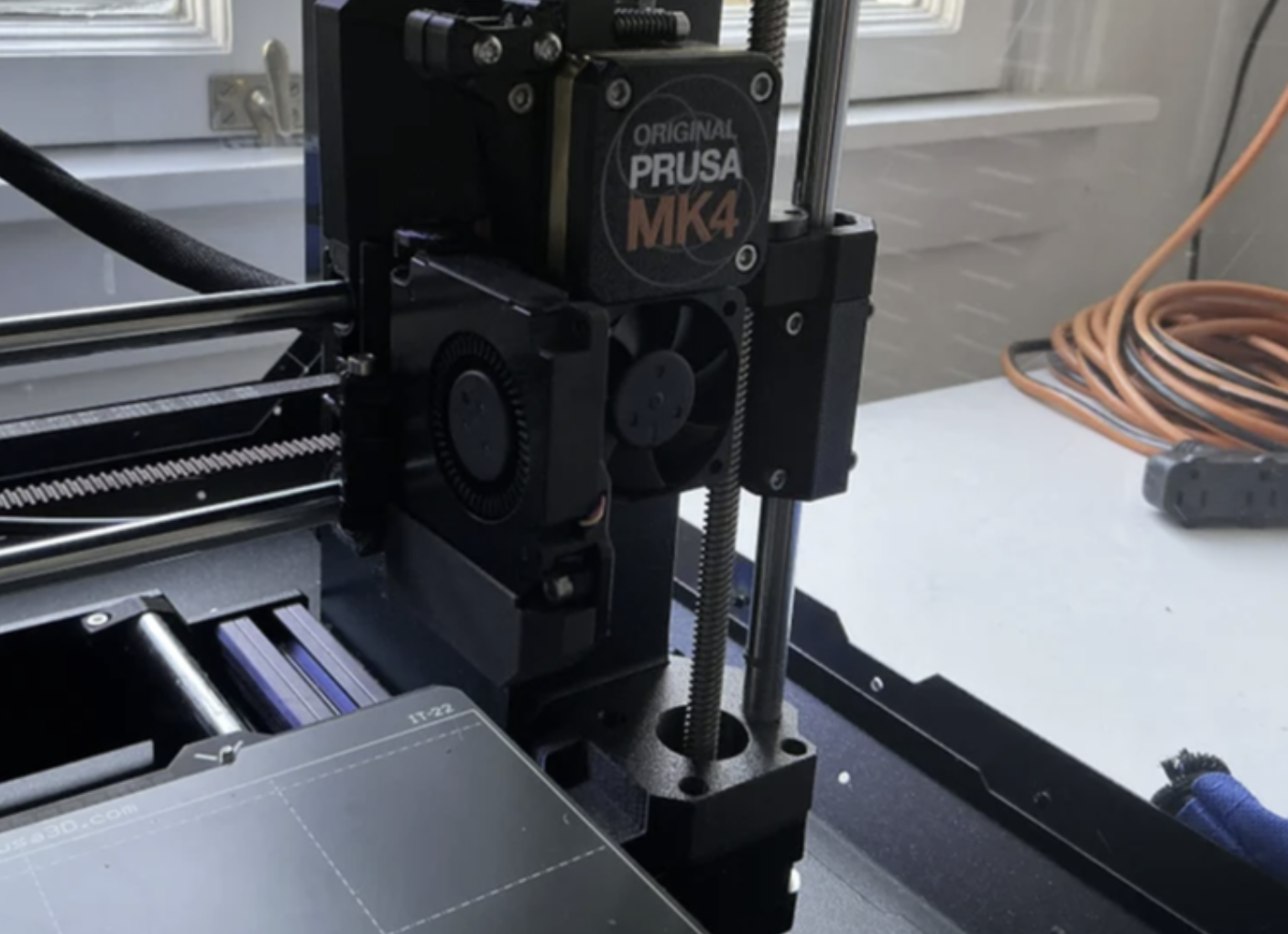
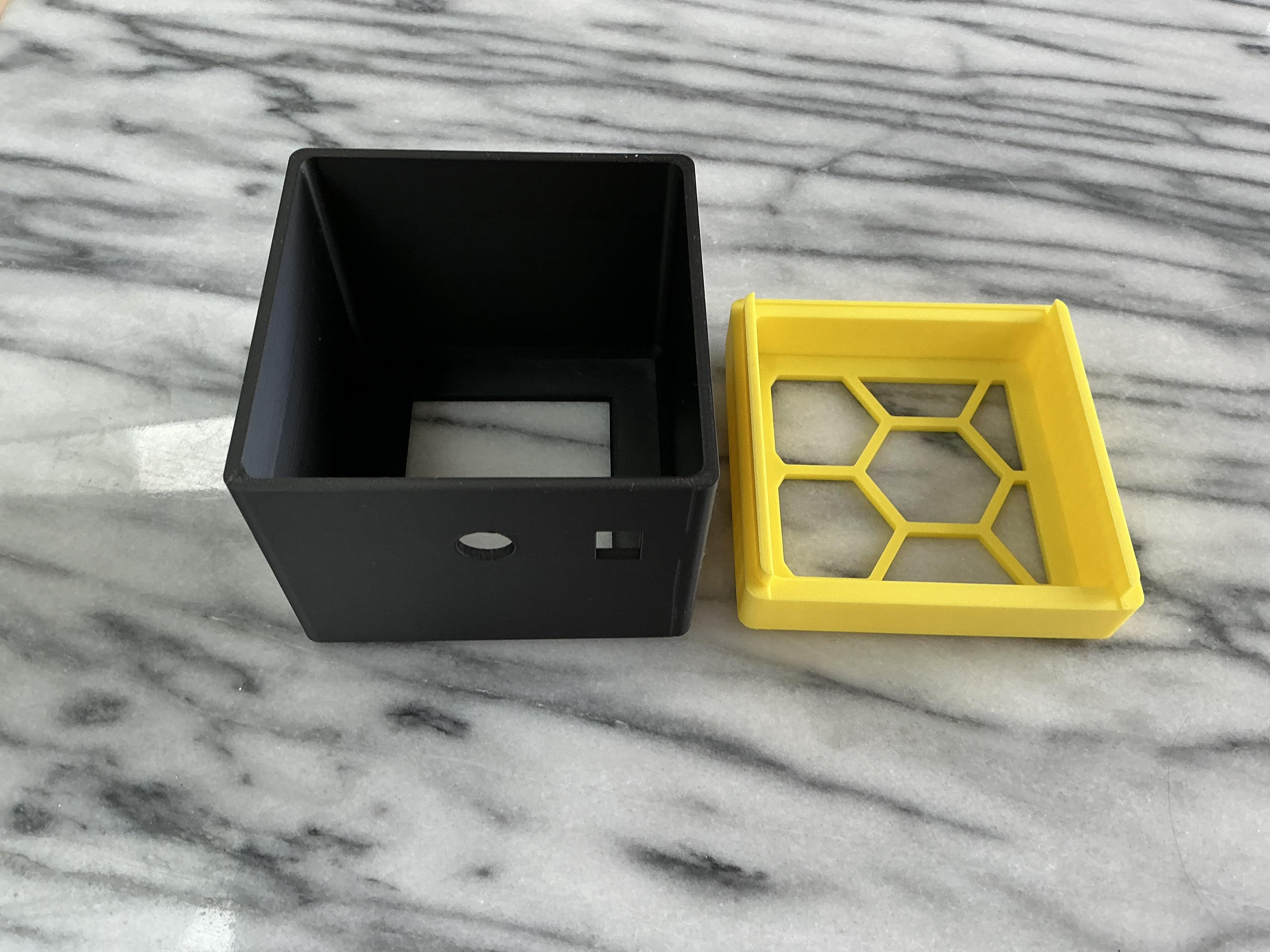
To 3D print the lid in yellow PLA and the main enclosure in black PLA, begin by slicing the STL files in your preferred slicing software, such as PrusaSlicer, Cura, or another slicer that suits your printer. Open the STL files for the lid and main enclosure in the slicer software, and position them correctly on the virtual print bed. Ensure the parts are oriented in a way that minimizes support material and optimizes print quality.
For the lid, load yellow PLA filament into your 3D printer and set the nozzle temperature to 215°C and the heated bed temperature to 60°C. These are standard settings for PLA to ensure smooth extrusion and good adhesion to the print bed. Adjust other settings in the slicer, such as print speed (usually around 50mm/s), and set infill density to about 20%, which is sufficient for most non-structural parts like a lid. If the design includes overhangs, you can enable support structures in your slicer software.
Once you're satisfied with the settings, slice the model and save the G-code file to an SD card, USB stick, or whichever physical medium your printer uses for file transfer. Insert the card into your 3D printer, and start the print. Monitor the first few layers to ensure the filament adheres well to the heated bed and the print is progressing smoothly. After the lid finishes printing, allow it to cool before removing it from the print bed.
Once the lid is complete, switch to black PLA filament for the main enclosure. Unload the yellow PLA filament and load the black PLA into your printer. Again, set the nozzle temperature to 215°C and the heated bed temperature to 60°C, as these settings will work well for the black PLA as well. Reconfigure the slicer settings for the main enclosure, making sure the infill density is suitable for the size and function of the part (you may want to increase it to 30% for more durability). Enable supports if there are overhangs or complex geometry in the design.
Slice the model again and save the new G-code file to your SD card or USB stick. Once the G-code is ready, transfer it to your 3D printer, and begin printing the main enclosure. As with the lid, monitor the print’s progress, especially the first few layers, to ensure good adhesion and print quality. Once the main enclosure has finished printing, allow it to cool completely before carefully removing it from the bed.
With both parts printed—the yellow lid and the black main enclosure—you’ll be ready to assemble your 3D printed portable mini heater. The combination of yellow PLA for the lid and black PLA for the enclosure will give your project a sleek, professional look, with the parts ready for final assembly.
Downloads
Covering the Vent
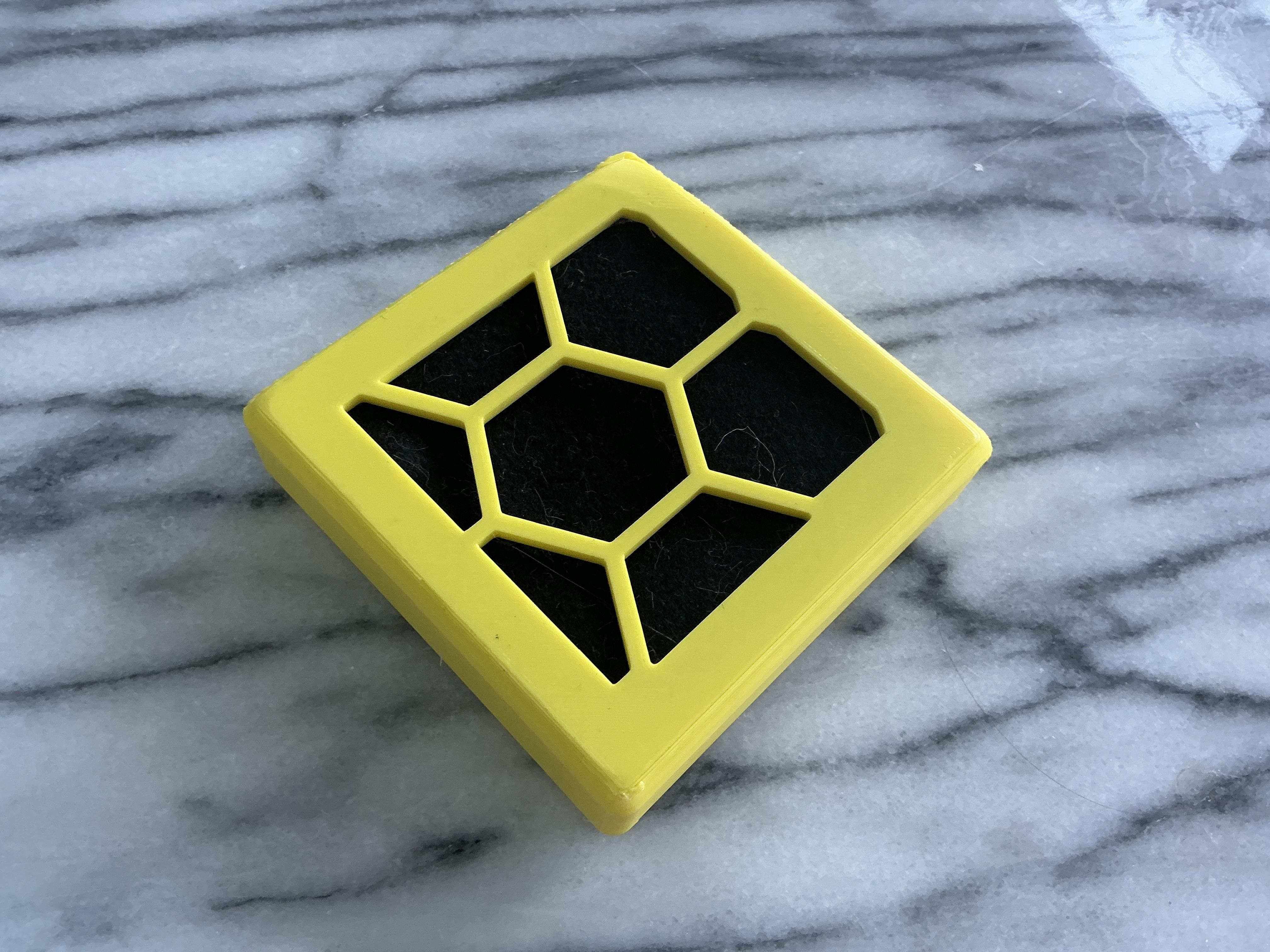
To glue black felt onto the air vent of your portable heater's 3D-printed yellow lid using hot glue, start by cutting the felt to a size slightly larger than the vent opening. You want it to cover the entire vent area with a little extra around the edges for a secure attachment. The felt should be breathable enough to allow air to flow but thick enough to block dust particles.
Next, heat up your hot glue gun. Once it’s ready, flip the lid over to expose the inside of the vent area. Apply a thin, even layer of hot glue around the edges of the vent on the inside of the lid. The glue should be applied to the plastic surface where the felt will attach.
Immediately after applying the glue, press the felt onto the glued area, ensuring it is centered and fully covers the vent. Gently press it into place along the edges to secure it without obstructing the airflow openings. Hold the felt in place for a few seconds to allow the hot glue to cool and set.
Once the glue has set, check around the edges to ensure the felt is firmly attached and that no air passages are blocked. The hot glue will create a strong bond that holds the felt in place, preventing dust from entering while maintaining airflow through the vent.
With the felt securely glued to the inside of the lid, the heater will be better protected from dust without reducing its ability to ventilate properly.
Inserting the Heating Module
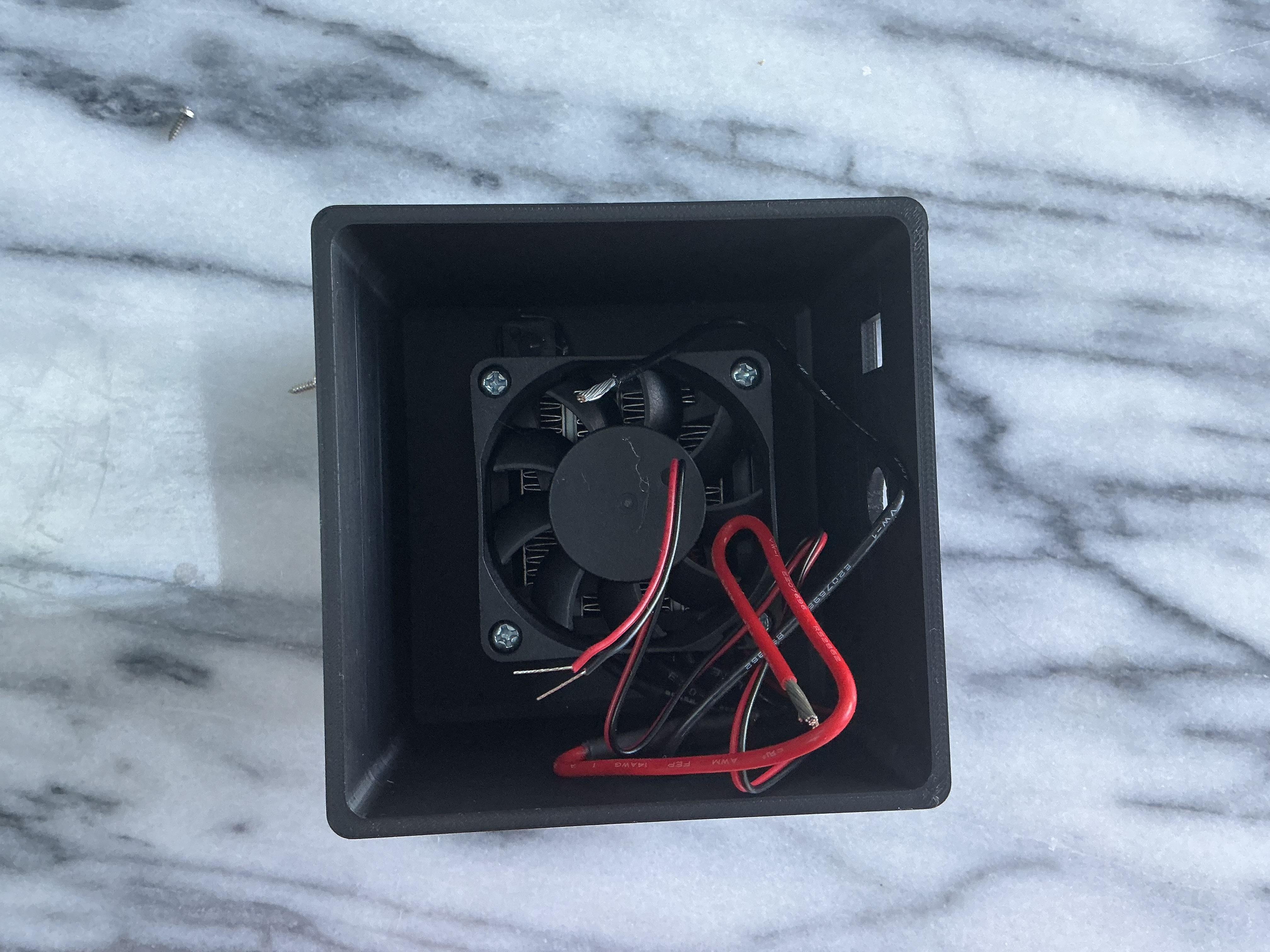
To attach the heating module to the front of your 3D printed enclosure using self-tapping screws, align the module so that it sits flush with the edge of the cutout in the enclosure. Since there are no mounting tabs, position the module directly against the edge of the cutout where you want it to be mounted.
With the module in place, carefully drive the self-tapping screws directly into the 3D printed plastic around the edge of the cutout. As you screw them in, the self-tapping screws will create their own threads in the material, securing the module to the enclosure. Be sure to keep the screws straight to avoid damaging the plastic.
Tighten the screws just enough to hold the module firmly in place, but be careful not to overtighten, as this could crack or deform the plastic. Once both screws are securely in, check that the module is firmly attached and properly aligned with the cutout. The heating module should now be securely mounted to the front of the enclosure, held in place by the self-tapping screws.
Inserting the Fan Speed Controller
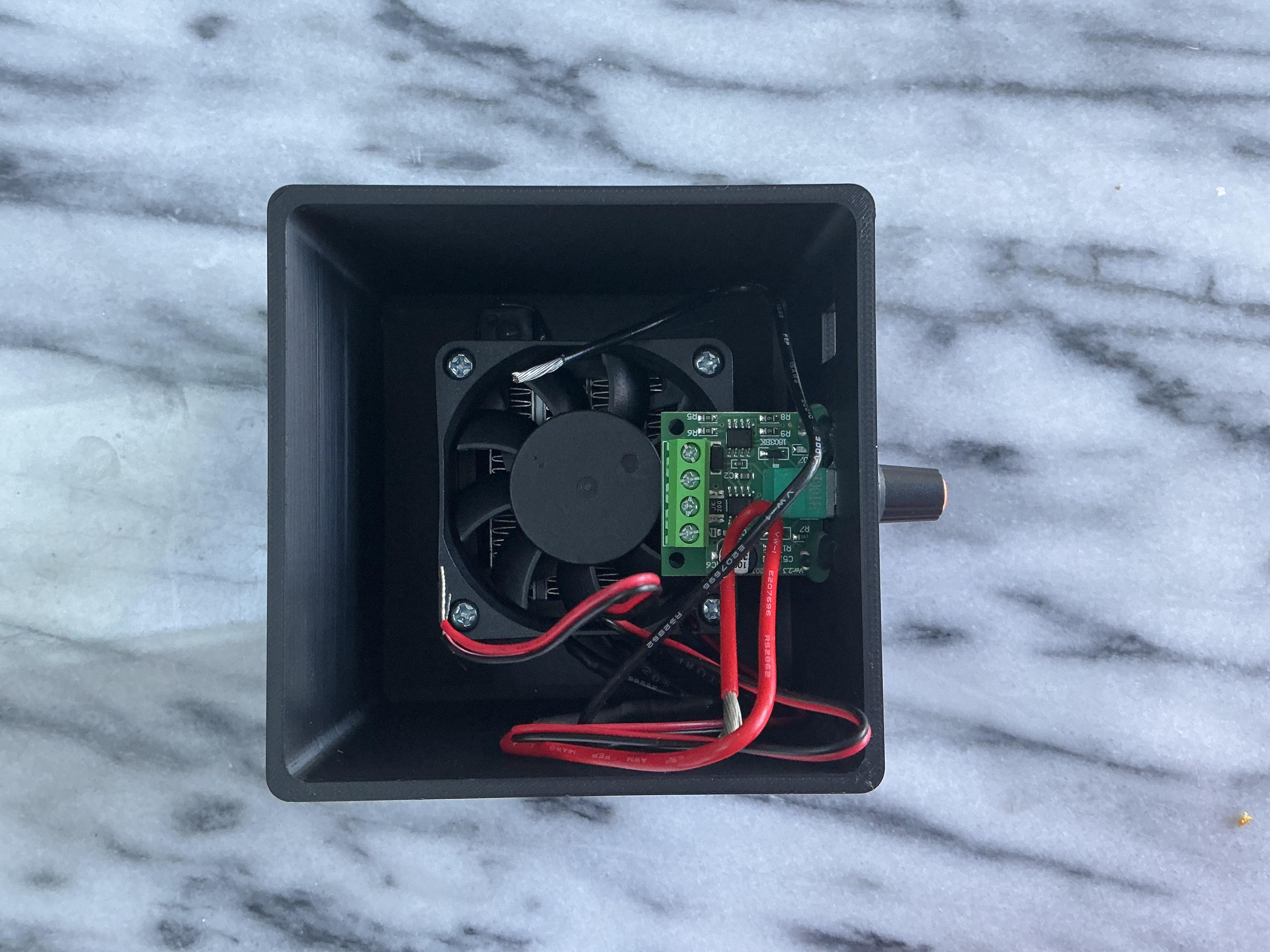
First, remove the knob from the motor speed controller. Since it's a friction fit, simply pull the knob off by applying even pressure and sliding it off the shaft. If there is any resistance, gently wiggle it off to avoid damaging the knob or shaft.
Next, prepare the motor speed controller for installation. Align the controller's shaft with the hole in the side of the enclosure where the shaft will come through. Position the controller inside the enclosure, ensuring the shaft lines up with the side opening.
Insert the shaft through the opening in the side of the enclosure from the inside. You may need to guide the module so that the shaft aligns perfectly with the hole in the enclosure. Once the shaft is through the opening, push the module into position, seating it securely inside the enclosure with the shaft protruding out of the side opening.
After the shaft is through the opening, reattach the knob. Slide the knob back onto the shaft, pressing it down firmly until it fits snugly. Since the knob is a friction fit, it should stay in place tightly without any screws or additional fasteners.
To secure the motor speed controller module inside the enclosure, apply small dots of hot glue around the edges of the module where it meets the enclosure’s inner surface. This will help keep the module firmly in place. Be careful not to apply too much glue, as it could block the movement of the shaft or interfere with the knob's rotation.
Allow the hot glue to cool and harden. Once set, check that the knob turns smoothly and that the motor speed controller is securely held inside the enclosure, with no movement. The friction fit of the knob and the hot glue securing the module will ensure a stable installation.
Soldering the Wires to the Switch
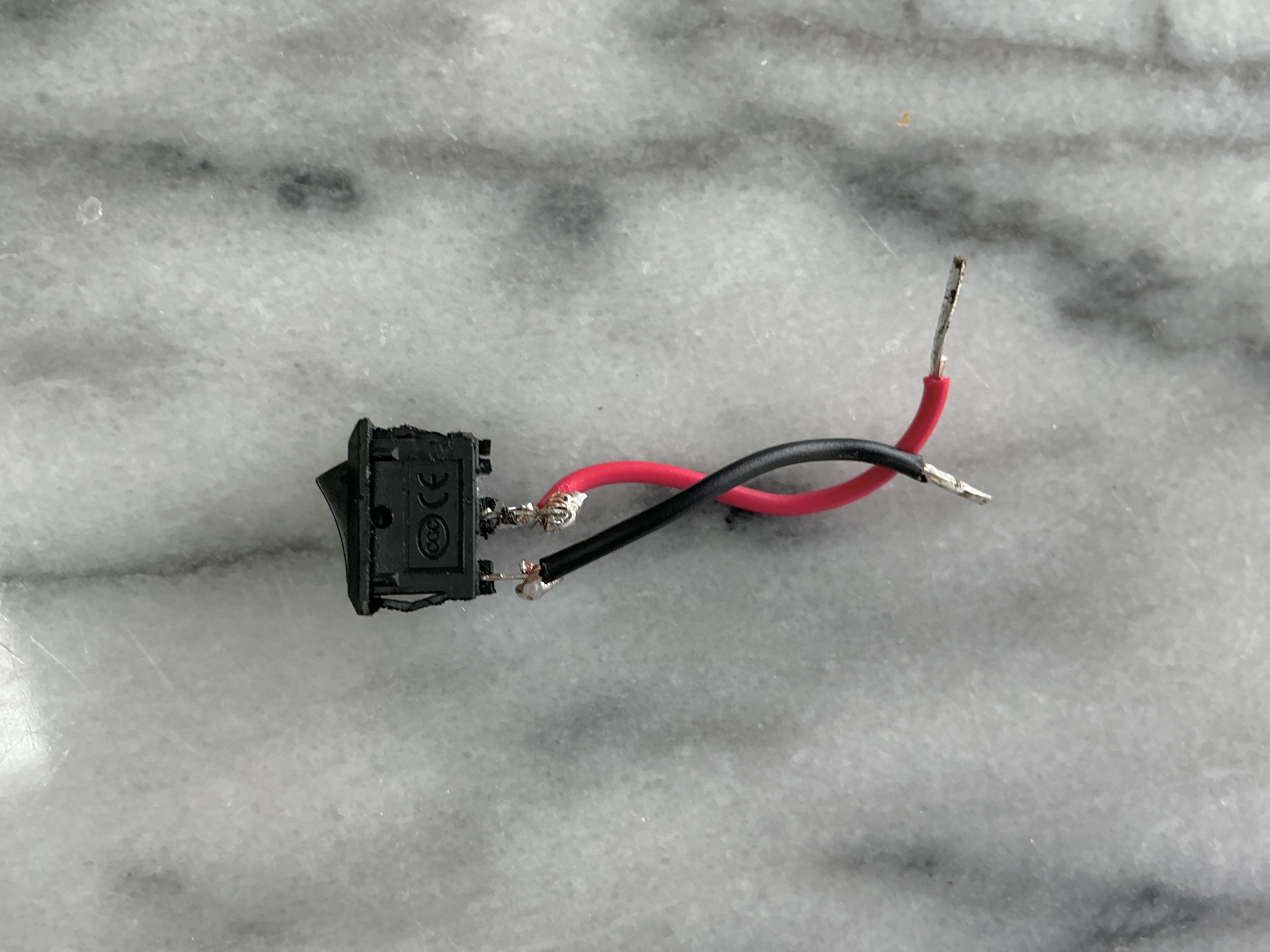
To solder wires to each pole of the switch, begin by preparing your wires. Strip about 3-5mm of insulation off the ends of the wires using wire strippers. Next, heat your soldering iron to around 350°C (660°F), and clean the tip by wiping it on a damp sponge or brass cleaning pad. Apply a small amount of solder to the tip of the soldering iron to help with heat transfer.
Place one wire against a pole (terminal) of the switch, and heat the pole and the wire simultaneously with the soldering iron for 1-2 seconds. Once the pole is hot, feed solder into the joint, then quickly remove the soldering iron. Allow the joint to cool, making sure the connection is smooth and shiny. Repeat the process for the second wire and pole, ensuring both wires are securely attached.
After soldering, inspect the joints to ensure they are solid and shiny, with no gaps or cracks. Trim any excess wire close to the joint, and if necessary, insulate the exposed connections using heat shrink tubing or electrical tape.
The result should be a solid, secure electrical connection between the wires and the switch, ready for use.
Inserting the Switch
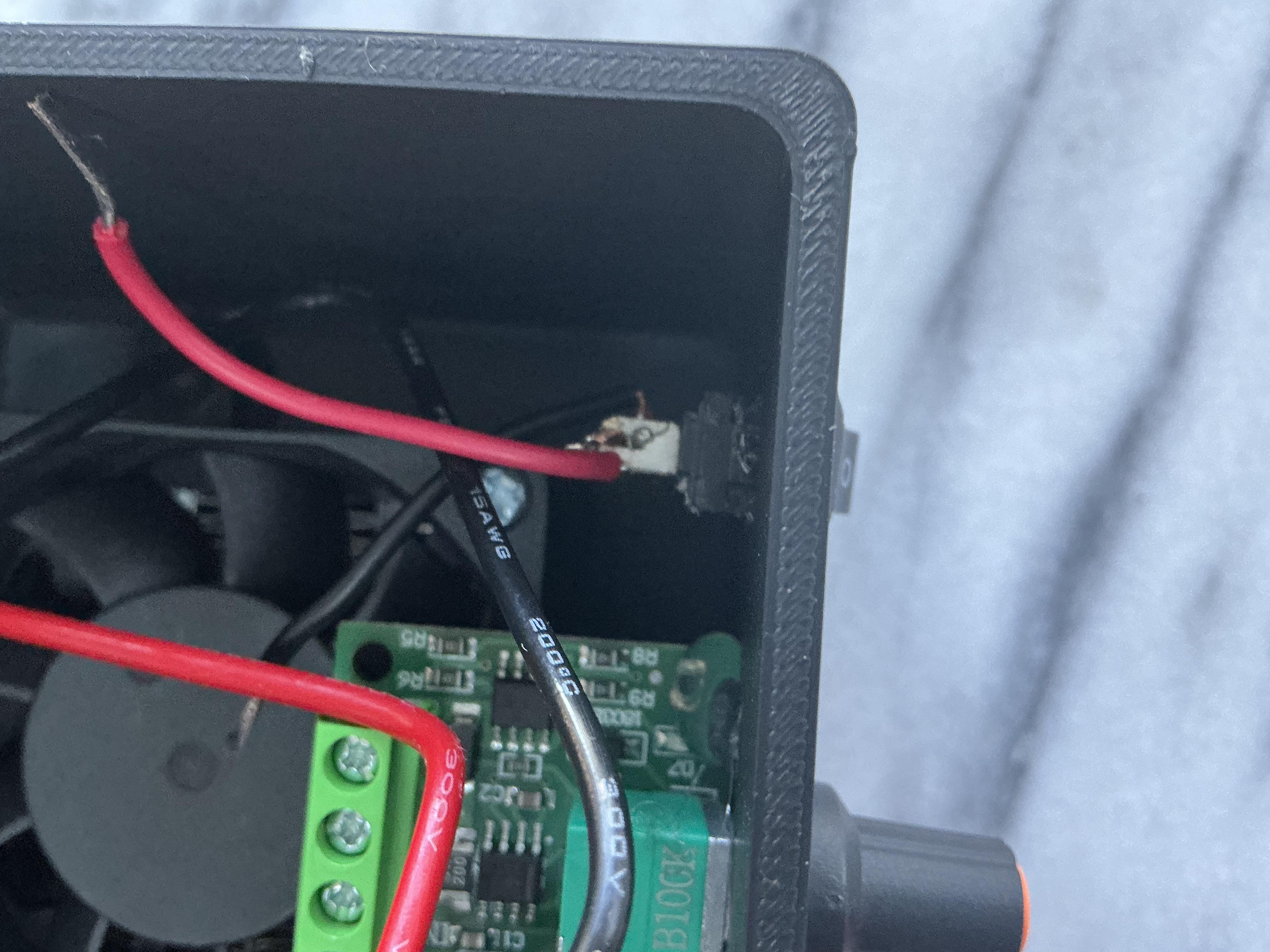
To insert the switch with the two soldered wires into its designated slot on the side of the enclosure, align the switch with the opening. The slot is designed to be the same size as the switch, ensuring that the switch fits snugly inside without any extra space around it. This means there will be no movement once the switch is in place.
Carefully insert the switch into the slot, applying gentle pressure until it is fully seated. Since the slot is the same size as the switch, the fit will be tight, ensuring the switch remains secure without any need for screws or adhesive. Be cautious as you push the switch in to avoid damaging the wires or bending them excessively.
Once the switch is inserted, check that it sits flush against the surface of the enclosure. The wires should be free to move without being pinched, allowing you to easily route them to their connection points. With the switch fully inserted, it will stay firmly in place, providing stability and reliability for the rest of the assembly.
Inserting the Battery Holder
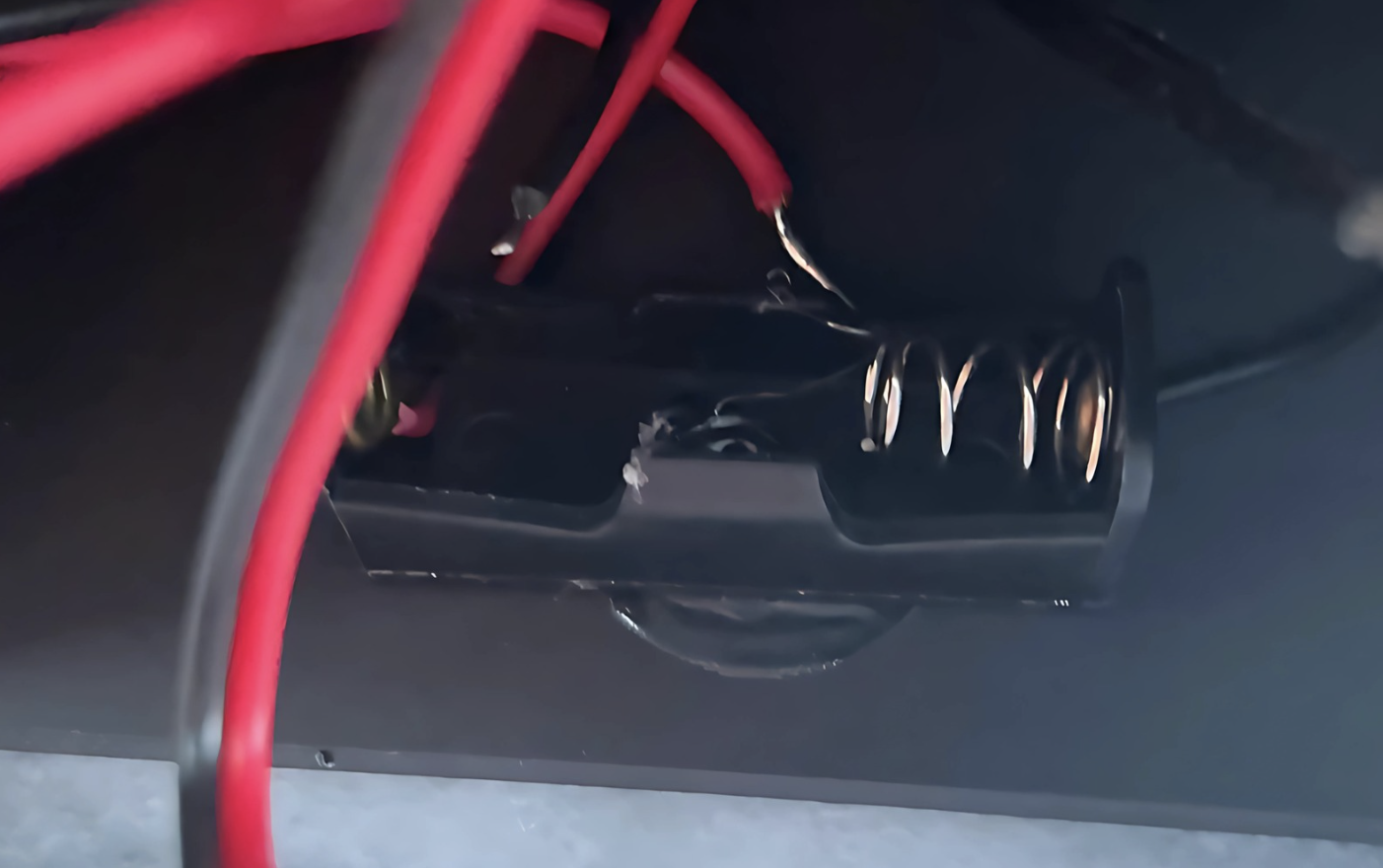
To secure the battery holder to the bottom of the enclosure using a self-tapping screw, first position the holder near the rear opening of the enclosure. Align it carefully so that the screw hole on the battery holder lines up with the spot on the plastic where you want to attach it. This screw hole on the holder will be used to fasten it directly into the plastic of the enclosure.
Once the battery holder is properly aligned and sitting flat against the bottom of the enclosure, take a self-tapping screw and insert it into the hole on the holder. Using a screwdriver or a drill, slowly drive the self-tapping screw into the plastic. The screw will bite into the plastic, creating its own thread as it goes in, so there's no need for a pre-drilled hole in the enclosure.
Be careful not to over-tighten the screw as you drive it in. The self-tapping screw should pull the holder firmly against the bottom of the enclosure, but over-tightening could damage the plastic or crack the enclosure. Once the screw is snug and the holder is secure, check that the battery holder is stable and doesn’t move. The tight fit from the self-tapping screw will keep the holder firmly in place, ensuring it doesn’t shift during use.
With the battery holder securely fastened, the rear opening remains open for the lid to cover it later, keeping the battery in place while leaving access to it when necessary. The single screw provides a solid, secure attachment, ensuring the holder stays exactly where you need it without additional fasteners or complicated mounting.
The Circuit
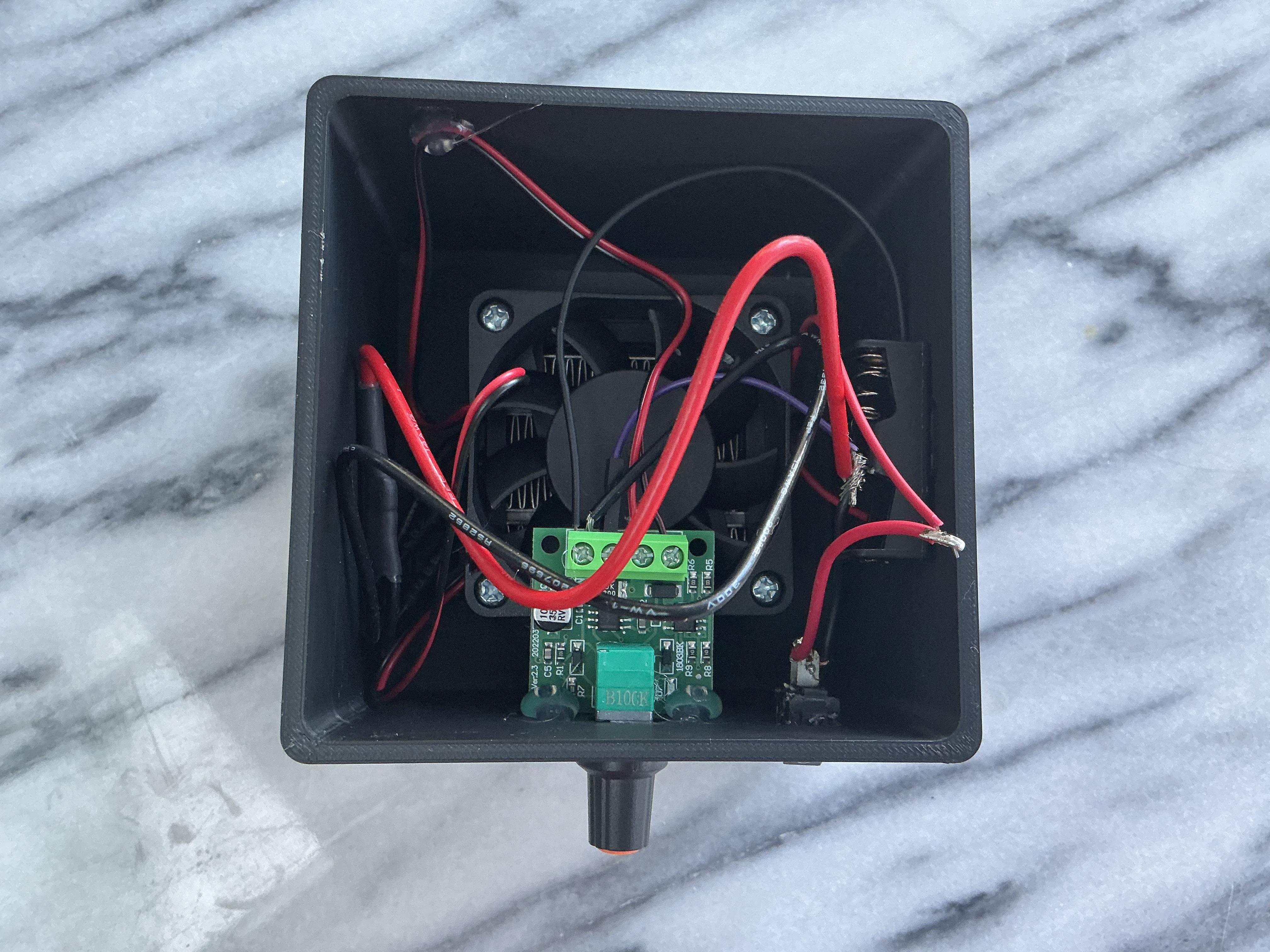
To create the circuit, begin by connecting the positive battery wire to the red wire that is connected to the switch. This ensures that the power from the battery is routed through the switch, allowing you to control the flow of electricity to the rest of the components.
Next, take the black wire that’s attached to the switch and connect it to the positive battery terminal on the motor speed controller. This wire will carry the current from the switch to the motor speed controller, which will regulate the power distribution to the motor.
Then, connect the black wire of the battery to the negative terminal on the motor speed controller. This wire will provide the return path for the current, completing the circuit and allowing the motor speed controller to function properly.
Following this, connect the heating element wires to the positive and negative terminals of the motor speed controller. It doesn't matter which wire connects to which, as long as each of them are connected to a separate battery terminal.
Next, take the positive wire of the fan and connect it to the positive motor terminal of the motor speed controller. This will provide power to the fan when the motor speed controller is activated, allowing the fan to operate in conjunction with the heating element.
Finally, connect the negative wire of the fan to the negative motor terminal on the motor speed controller. This completes the circuit for the fan, ensuring that it operates properly alongside the heating element when the motor speed controller is powered on.
Once all these connections are made, you will have created the full circuit, linking the battery, switch, motor speed controller, heating element, and fan together. This setup allows you to control both the fan and the heating element, with the motor speed controller managing the power distribution to each component.
The Lid
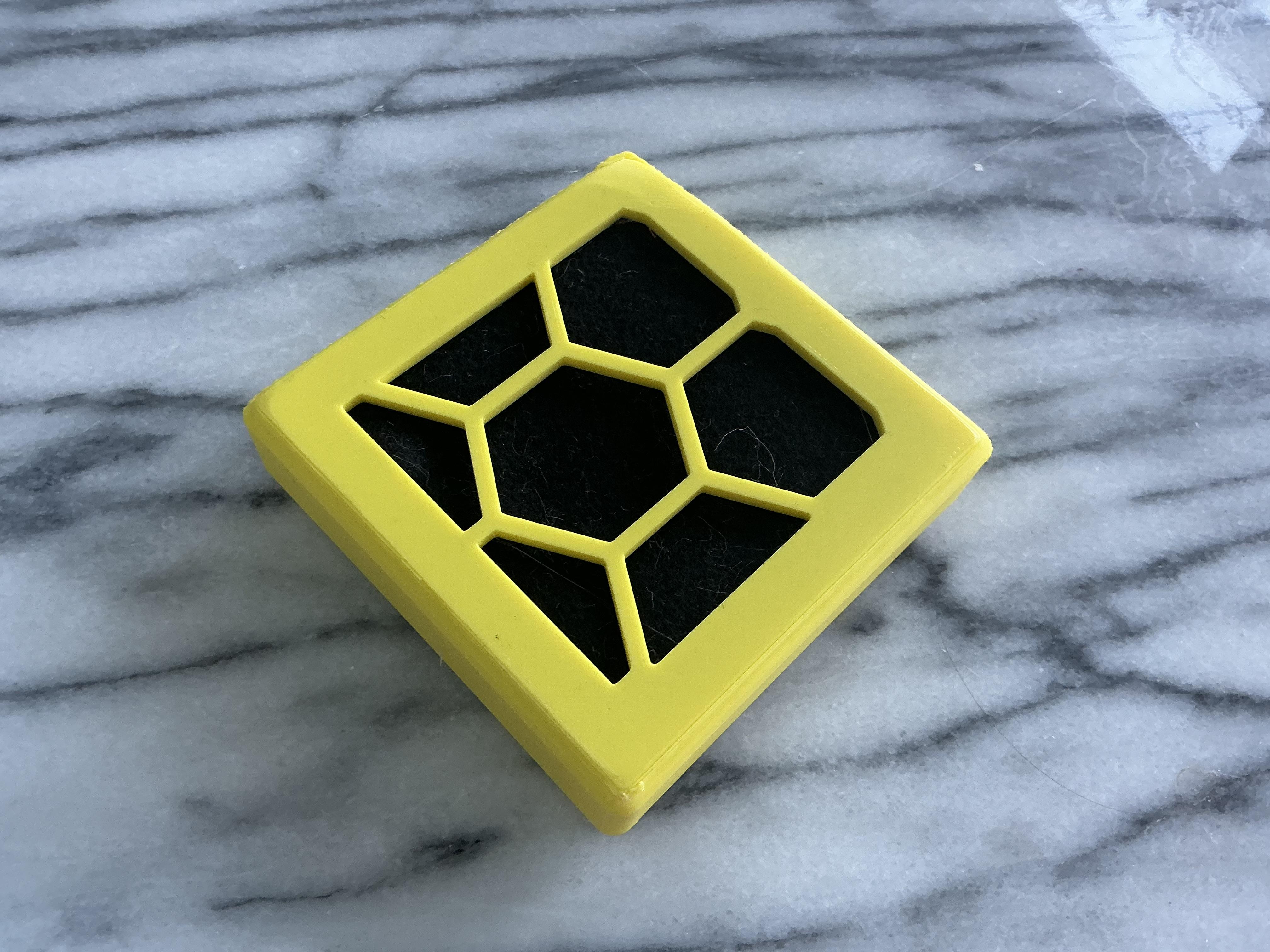
To secure the yellow lid to the back of the heater using a friction fit, begin by aligning the lid with the back of the enclosure, ensuring it fits into place snugly. The design of the lid and the opening on the enclosure should be such that the edges of the lid press tightly against the internal structure of the enclosure, creating a secure seal without the need for screws or adhesive.
Gently press the lid onto the back of the heater, making sure it is oriented correctly. As you push the lid into place, the edges will press against the walls of the enclosure, creating a tight fit. The friction between the lid and the enclosure will hold it securely in place. You may need to apply a little extra pressure to ensure the lid clicks or settles fully into position.
Once the lid is in place, check that it is evenly aligned and flush against the back of the heater. The friction fit should prevent the lid from moving or coming loose during use. If necessary, gently wiggle the lid to ensure it is seated properly.
With the yellow lid securely fitted through friction, the heater is now fully enclosed, and the internal components are protected, ready for use. The friction fit will provide a simple, secure attachment that can be easily removed or adjusted when necessary.
The Final Product
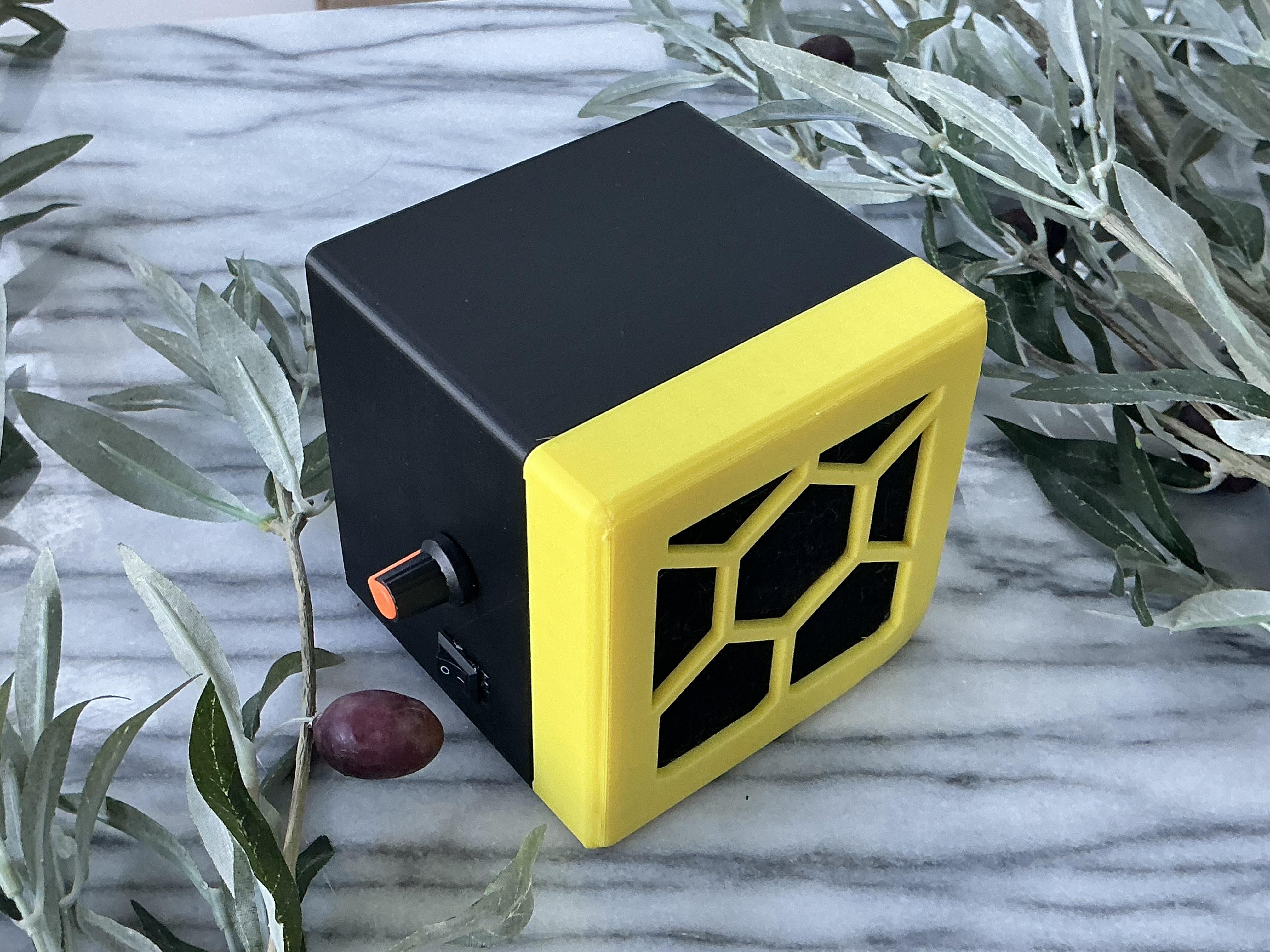
The final product is a sleek, portable mini heater that blends functionality with convenience. It features a compact black enclosure with a bright yellow lid that fits securely thanks to its friction-fit design. This design ensures that the heater is easy to assemble and maintain while keeping the internal components safely housed and protected. The yellow lid, with its snug fit, adds a touch of visual appeal, giving the heater a modern, clean look.
Once assembled, the heater is lightweight and easy to handle, making it ideal for use in a variety of settings. Whether it's keeping you warm during a chilly day in the workshop, providing comfort in a small room, or serving as a portable solution for outdoor activities, the mini heater offers reliable warmth wherever you need it. The user-friendly design means you can take it with you on the go or place it in different spots around your home without hassle.
The overall look is polished and minimalistic, making it an unobtrusive yet practical addition to your space. Its compact size doesn’t sacrifice performance, delivering just the right amount of heat in a portable form. The friction-fit lid makes the device simple to close up when not in use, while still allowing easy access to the internal parts when necessary.
In summary, the portable mini heater stands out not only for its efficient heating capabilities but also for its thoughtful design and portability. It’s an excellent choice for anyone who needs a convenient, reliable source of warmth that can be easily moved, stored, and maintained.